汽轮机叶片加工方法.docx
《汽轮机叶片加工方法.docx》由会员分享,可在线阅读,更多相关《汽轮机叶片加工方法.docx(11页珍藏版)》请在冰豆网上搜索。
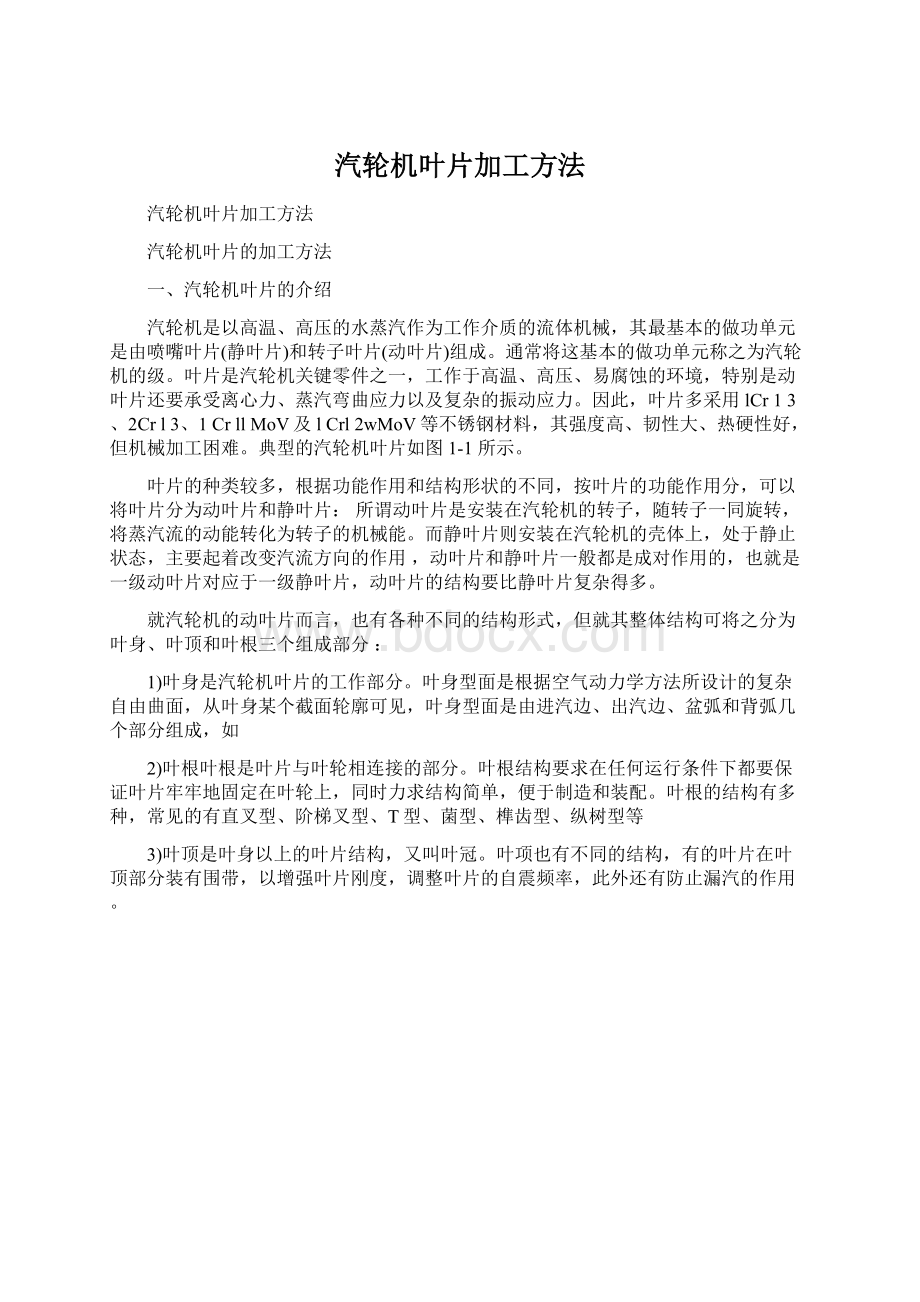
汽轮机叶片加工方法
汽轮机叶片加工方法
汽轮机叶片的加工方法
一、汽轮机叶片的介绍
汽轮机是以高温、高压的水蒸汽作为工作介质的流体机械,其最基本的做功单元是由喷嘴叶片(静叶片)和转子叶片(动叶片)组成。
通常将这基本的做功单元称之为汽轮机的级。
叶片是汽轮机关键零件之一,工作于高温、高压、易腐蚀的环境,特别是动叶片还要承受离心力、蒸汽弯曲应力以及复杂的振动应力。
因此,叶片多采用lCr13、2Crl3、1CrllMoV及lCrl2wMoV等不锈钢材料,其强度高、韧性大、热硬性好,但机械加工困难。
典型的汽轮机叶片如图1-1所示。
叶片的种类较多,根据功能作用和结构形状的不同,按叶片的功能作用分,可以将叶片分为动叶片和静叶片:
所谓动叶片是安装在汽轮机的转子,随转子一同旋转,将蒸汽流的动能转化为转子的机械能。
而静叶片则安装在汽轮机的壳体上,处于静止状态,主要起着改变汽流方向的作用,动叶片和静叶片一般都是成对作用的,也就是一级动叶片对应于一级静叶片,动叶片的结构要比静叶片复杂得多。
就汽轮机的动叶片而言,也有各种不同的结构形式,但就其整体结构可将之分为叶身、叶顶和叶根三个组成部分:
1)叶身是汽轮机叶片的工作部分。
叶身型面是根据空气动力学方法所设计的复杂自由曲面,从叶身某个截面轮廓可见,叶身型面是由进汽边、出汽边、盆弧和背弧几个部分组成,如
2)叶根叶根是叶片与叶轮相连接的部分。
叶根结构要求在任何运行条件下都要保证叶片牢牢地固定在叶轮上,同时力求结构简单,便于制造和装配。
叶根的结构有多种,常见的有直叉型、阶梯叉型、T型、菌型、榫齿型、纵树型等
3)叶顶是叶身以上的叶片结构,又叫叶冠。
叶项也有不同的结构,有的叶片在叶顶部分装有围带,以增强叶片刚度,调整叶片的自震频率,此外还有防止漏汽的作用。
图1-1典型的汽轮机叶片
二、精锻的优点
锻造是叶片制造的主要成形加工工艺,汽轮机中相当一部分叶片几乎全部采用锻造方法生产。
精密模锻是在一般模锻基础上逐步发展起来的一种少无切削加工新工艺,与一般模锻相比,它能获得表面质量好,机械加工余量少和尺寸精度高的锻件,取消或部分取消了切削加工工序,从而提高材料利用率。
可以使金属流线沿零件轮廓合理分布提高零件的承载能力,降低零件生产成本,叶片锻造工艺有精锻、半精锻和模锻三种方式。
在现行叶片生产中目前尚无严格区分精锻和模锻的标准。
一般而言,所谓精锻是指锻件叶身部分余量小少于0.3mm,公差小约为1/3模锻公差,叶身表面不再需要切削加工,而只需要进行精抛光或化学铣削。
而叶片模锻则锻件具有较大的加工余量两者相比,精锻有如下优点:
(1)可以提高叶片的性能和使用寿命,叶片精锻由于采用了合理的模具设计和先进工艺技术,能够保证金属具有良好的成形条件和合适的变形程度,获得沿叶身形状分布的流线和均匀细小的晶粒,增加了强度。
同时由于金属沿着模具的形状流动叶身型面和缘板内侧面及其与型面转接部分不需要机械加工,使外露出来的端向晶粒最少流线不被破坏,减少了应力腐蚀和裂纹,提高了疲劳强度冲击强度和抗腐蚀性能力。
(2)与普通模锻叶片相比,可以节省20%—25%左右的金属材料,在各种类型的叶片生产中,由于叶片形状复杂,材料的利用率都比较低,用方钢铣削汽轮机叶片材料利用率只有7%—15%,普通模锻叶片材料利用率只有25%—40%,这些叶片的材料除了锻造过程中较大的毛边消耗外,大量消耗于为机械加工所留的余量,精锻叶片的材料利用率可以达到50%以上。
(3)简化机械加工过程,精锻叶片型面和缘板内侧不需要机械加工,可以减少大量金属切削机床和机械加工工时,缩短机械加工过程。
(4)解决了难加工材料和型面薄的叶片机械加工的困难,汽轮机叶片材料一般为不锈钢甚至钛合金材料。
加工性能差,叶片型面薄而复杂,加工极易变形,采用精锻可以解决这些问题。
(5)叶片制造的总成本大大降低,采用叶片精锻技术其所用的模具费用和锻造费用较普通锻造提高约5倍左右,增加了锻件的成本但是对整个制造过程而言由于节省了材料,缩短了生产周期,大大减少了机械加工费用。
而且精锻叶片的使用寿命长。
所以其总成本比普通的大余量锻造要低的多。
三、叶片精锻件设计及工艺参数计算
1、叶片锻造平衡角的确定
工艺分析中,叶片锻造转角又称平衡角的确定是叶片锻造成形的关键,也是锻造模具型腔设计时首先考虑的问题。
扭角是叶身各型面弦长线与发电机转子中心线的夹角如图2-1所示
图2-1叶片锻造转角的确定
汽轮机上绝大多数叶片都具有变化的曲面,其各截面的扭角大小不同,靠近叶冠部分的扭角最大,靠近叶根部位的扭角最小,甚至是负值。
扭角大的叶片会给锻造带来如变形、水平错移力大、尺寸精度不稳定等各种困难。
如果把发电机中心线平面当作分模面必然导致模锻过程中产生较大的单向水平推力,使压力机滑块导轨和模具导柱急剧磨损并造成模具错移。
在进行叶片锻件设计时为了克服这一水平力,应将叶片设计基准沿发电机中心线旋转一定合适的角度,放置于锻模上。
锻件图上所示的状态也就是叶片在锻模上放置的状态。
叶片所需旋转的角度称为平衡角。
确定锻造转角应遵循如下准则:
(1)力求使叶身型面平坦。
叶身平坦可以减小锻造载荷和侧向力,防止过大的侧向力产生错模现象。
(2)有利于叶片锻件各部位的充足成形。
叶身不同的部位成形难度各不相同,必须全局考虑成形的过程以做到完好充模。
(3)配合锻坯形状的确定和锻坯在模具型腔中定位的考虑。
确定平衡角有计算法和作图法两种,两种方法各有特点。
以下介绍计算法
计算法确定平衡角
计算法分三种分别如下:
(1)将靠近叶根的截面和靠近叶冠的截面的夹角相加求其平均值
(2)将靠近叶根的截面和靠近叶冠的截面以及叶身中部的夹角相加求其平均值
(3)将叶身各个截面的扭角相加求其平均值
工程上一般采用第2种方法它具有简捷明了的特点,而且考虑到靠近叶冠的截面出气边最薄,一般加上一个验证过程即图2-1中角度α要求:
48º≤a≤52º以保证出气边能够充满。
2、叶身型面余量的加放
叶片的余量与材料性质尺寸大小、加热方法、锻造设备加工方法有关。
精锻叶片叶身虽然无机械加工余量,但考虑到金属在加热过程中存在表面氧化脱碳污染和元素烧损现象,还得留出适当的化铣量或抛光量。
生产实践表明无论是钢或耐热合金,当加热没有采取防护措施时在锻件表面不可避免的产生缺陷层,有时厚度可能达到1mm以上若采取了防护措施可减少缺陷层的厚度,但缺陷层总是不可避免的,叶片毛坯终锻变形时,叶身型面可能出现压坑划伤等缺陷。
如工序周转过程中难免有碰伤,因此必须留有余量。
常用加放余量的方法有两种:
(1)加锻造方向余量,在叶身型面曲率半径较大,扭角较小的情况下叶身余量可以用模锻时的欠压量来保证,即加放y向余量,在给定的坐标点y,坐标上加放余量∆其公式为:
y=y+∆1(∆为欠压量)但当曲率半径较小,扭角较大时将会出现不均匀的余量。
当取∆=0.25mm,型面的弯曲角度a<36º时,才能直接向y向加余量,另外,叶盆和叶背的y向余量不尽相同,因此叶盆和叶背应分别加余量。
(2)加法向余量,为了得到均匀的余量,可以沿法向加放余量,但叶片的型面特征用离散点表示,各坐标点之间没有固定的数学描述,为了加放法向余量,可以采用直接作图法,也可以找出型面曲线的数学描述,在型面点的法向加放余量,然后确定加放余量后的新坐标如图2-3所示的解析法加放余量中,在叶片某一型面上一系列点中取一点m。
(x,y)。
在m。
的法线方向N—N上加余量∆得到m(x,y)由图2-3中几何关系可知
图2-3余量加放(包络)示意图图2-4靠近叶根进气边的修整方法
3、叶身型线的修整
由于叶片叶身形状的扭曲,用普通的画法几何方法不能很好的表达叶片的特征,所以通常叶片的产品图是通过给出叶身一系列截面的离散坐标点来精确的表示叶身,而叶根叶冠则用普通的几何方法表示。
无论是精锻叶片还是普通模锻叶片叶身部分的进出气边都很薄,锻后要向外形成飞边,在这些部位容易出现充不满折叠以及划痕裂纹等各种缺陷。
因此要做一定的延伸和加厚修整,以使可能的缺陷产生在叶身之外。
另外,由于叶片锻造时的水平力使锻件产生水平错移会导致进气边的背弧减薄,所以设计汽轮机叶片锻件时,一定要首先对叶身进出气边进行修整。
精锻叶片的型线修整方法,通过对叶片厂工程技术人员长期经验积累总结有以下四种叶身型线修整方法:
(1)靠近叶根型面进气边型线修整方法图2-4为靠近叶根型面进气边型线修整方法示意图。
靠近叶根部分,由于叶片扭曲翘起很高,为了防止出现倒勾影响出模,必须设置一定的拔模斜度一般取为7º,具体修整过程如下:
(1)作背弧13的偏移(offset)线1,距离d1=1.5—3mm
(2)作进气边小圆12的(offset)线2,距离d2=25—30mm
(3)作进气边小圆12的(offset)线3,距离d3=5—8mm
(4)作内弧偏移线的进气边的延伸线4;与线3相交;
(5)过线3和线4的交点作水平线5
(6)作5线的(offset)线6,距离d4=2—5mm
(7)作线1的7º的相切线与线6相交于b点(背弧端点),过b点作垂线与线5相交于a(内弧端点)
(8)作背弧的45º切线8
(9)以45º切线的切点为起始点,以7º线与线1的切点为终点作线性包络线9
(10)作线4、5的转接R3—R5
(2)叶身中部型面进气边型线修整方法图2-5为叶身中部型面进气边型线的修整示意图,叶片叶身中部随着扭曲逐渐变得较为平坦,这个时候一般不需要考虑拔模的问题,修整过程也相应变得略为简单,但是要考虑叶身最大厚度在这个过程中的影响,当叶身最大厚度处于修整范围以内时,要考虑从最大厚度处进行修整,当最大厚度处于这个范围以外则忽略它的影响,具体修整过程如下:
(1)作背弧13的偏移(offset)线1距离d1=1.5--3mm
(2)作内弧偏移线的进气边的延伸线4与线3相交
(3)过线3和线4的交点作水平线5
(4)作5线的offset线6,距离d4=2—5mm
(5)作进气边小圆12的offset线2,距离d2=25—30mm
(6)作进气边小圆12的offset线3,距离d3=5—8mm
图2-6靠近叶冠进气边的修整方法图2-7型线出气边的修整方法
(7)线3与线6的交点,在a点的里端(即坐标x值较小)时,过a点作铅垂线与6线交于b点,该b点为背弧端点(8)过进气边小圆的外切点作线1的垂线得到e点
(9)作(8)垂线的距离为3—4mm的平行线与线1相交得到交点f
(10)型线的最大厚度处在修整圆2范围内时,背弧修整线起始点在最大厚度处,作线性偏移线9,连接e点和f点
(3)型面出气边的型线修整方法图2-7为型线出气边的修整方法示意图具体修整过程如下:
(1)作出气边小圆的offset线2,距离d1=25—30mm截得尺寸S
(2)作出气边小圆的外切线11,并与背弧型线垂直,截得尺寸T得到交点e
(3)作背弧的offset线1
(4)作进气边小圆的offset线3,距离d258mm
(5)作内弧的进气边的延伸线5
(6)作过线4和线3的交点的水平线5
(7)作线5的offset线6,偏移d3=2—5mm,与线3相交得交点b
(8)过b点作垂线与线5,相交于a点
(9)作线4和线5的圆角,圆角半径R=3—5mm
(10)以c点为起点,以e点为终点,作线性包络线9
4、叶根实体的设计计算
设计叶片锻件图时,把叶根与叶身分开处理,因为叶根需进行机械加工,叶身在精锻情况下,除进排气边缘外,不需机械加工,所以对设计的要求有所区别,叶根的安装及简化图如图2-9和图2-10所示
图2-9叶片安装示意图图2-10叶根简化示意图
叶根机械加工比较方便,没有必要进行精锻,但是叶根内侧面和叶身紧密相连机械加工比较困难,而且由于和叶身加工方法不同,容易造成表面质量下降,所以锻件的叶根内侧面应采用精锻成形,叶根内侧面余量的大小和精锻叶片叶身型面余量的去除方法有关,当采用化铣时内侧面余量,等于叶身型面的余量,如果用手工抛光内侧面,可加余量1.0—1.5mm。
锻件的叶根其它侧面余量大小仍采用普通锻造的余量设计,叶根的机械加工余量主要取决于尺寸和材料,叶片尺寸越大材料愈难加工,则要求的余量愈大。
为了防止内侧面在边缘转角处充不满,与内侧面相邻的面取余量2.5—3mm,其余的面可取余量2—2.5mm。
叶片产品图和锻件图的尺寸标准方向是有区别的。
锻件图上要给出叶根中心线方向和其垂直方向的。
叶根尺寸叶片叶根中心线往往与叶轮中心线有个夹角。
产品图上标注的叶根尺寸要按图样上的投影关系换算成锻件图所需要的叶根尺寸。
即在加余量之前必须先推算出叶根的长宽高的尺寸。
根据这些尺寸加放相应的余量。
即为锻件叶根尺寸。
这里以常用的燕尾型为例,介绍叶根的设计计算
(1)叶根厚度尺寸计算,转子叶片在轮盘上安装位置如图2-9所示,叶根简化形状如图2-10,叶根厚度尺寸关系见图2-11关系式为:
B=b+2(h-h)⋅tgv12
图2-11叶根的F向视图
(2)叶根长度尺寸计算长度L应当从叶片零件图上的俯视图有关尺
寸进行推算如图2-12及图2-13所示
当叶片有斜角时叶根的长度应按下式计算
(3)叶根高度尺寸计算,从图2-12可看出对于普通叶片模锻高度尺寸,可用a代替,但在精锻情况下,由于叶根内侧为无余量,表面应根据叶片在轮盘上的安装位置图,推算其最大高度。
从图2-11可知叶根中心线与轮盘端面呈b角,而叶根纵向中心线与轮盘轴线的夹角为j=90o-b,叶根端面高度方向与中心线偏离轮盘y轴的距离为x0,尺寸关系如下:
图2-12叶根的K向视图图2-13叶根的M图
四、汽轮机叶片表面淬火
在凝汽式汽糟机中,汽流中的水滴会对叶片产生严重的水蚀为了抵御末级动叶片的水蚀,除了从汽轮机结构设计上考虑减少水蚀作用之外,另一种防水蚀的方法是强化末级叶片的水蚀区为提高叶片的抗水蚀能力,目前主要有以下几种工艺方法:
(I)火焰淬火强化:
在叶片进汽边火焰加热淬火,该方法工艺较简单但温度不易控制,易产生变
形、裂纹、硬度不均匀等问题;
(2)高频感应加热淬火:
该工艺采用感应加热后低温回火,产生2~6—砌厚回火马氏体,可提高
效率,但感应加热设备复杂,尤其使感应圈设计和制作复杂;
(3)局部加覆盖层:
在进气边的局部位置覆盖一层新合金,采用的工艺方法有:
钎焊司太立合金
片、热喷吐、堆焊、电镀、化学转化膜、涂料与涂装、激光熔覆等。
该类方法存在工艺复杂、残余应力大、覆盖层易脱落等问题。
(4)叶片进汽边水蚀区经高频淬火获得细晶粒的回火马氏体和较大的残余压应力并提高了硬度,从而提高抗水蚀性和运行安全性.