长江大学级ERP实验报告.docx
《长江大学级ERP实验报告.docx》由会员分享,可在线阅读,更多相关《长江大学级ERP实验报告.docx(18页珍藏版)》请在冰豆网上搜索。
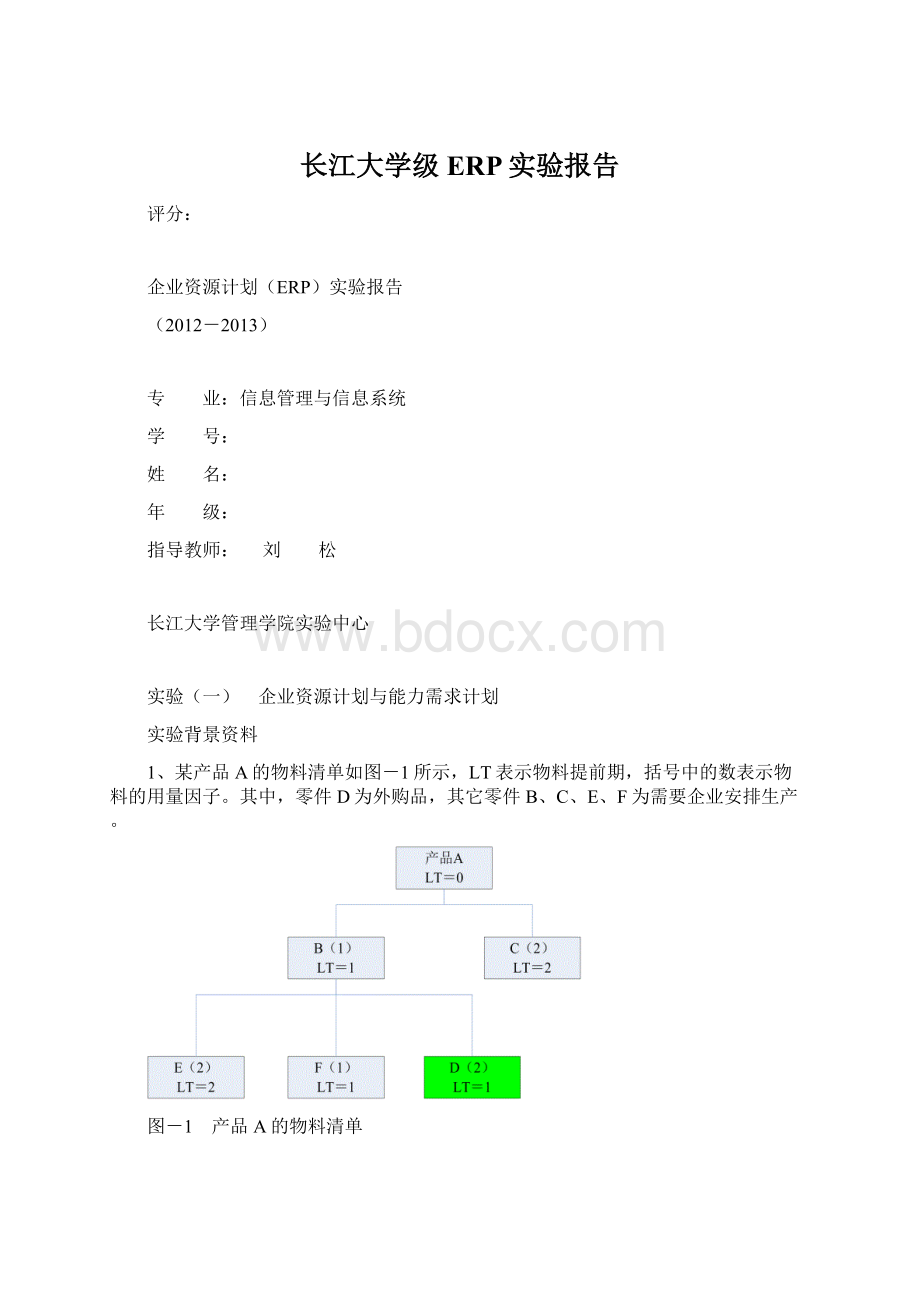
长江大学级ERP实验报告
评分:
企业资源计划(ERP)实验报告
(2012-2013)
专 业:
信息管理与信息系统
学 号:
姓 名:
年 级:
指导教师:
刘 松
长江大学管理学院实验中心
实验
(一) 企业资源计划与能力需求计划
实验背景资料
1、某产品A的物料清单如图-1所示,LT表示物料提前期,括号中的数表示物料的用量因子。
其中,零件D为外购品,其它零件B、C、E、F为需要企业安排生产。
图-1 产品A的物料清单
2、产品A的需求数据、零件的库存信息、工艺路线,以及工作中心工时定额信息和工序间隔时间分别见以下各表。
表-1 计划展望期内产品A的需求
产品A
需求时区
计划时区
预测时区
周期
1
2
3
4
5
6
7
8
9
10
11
12
实际需求
24
25
20
25
18
20
0
8
0
10
0
0
表-2 产品A上一年度的实际需求数据
周期
1
2
3
4
5
6
7
8
9
10
11
12
实际需求量
18
18
19
21
23
20
21
22
22
23
24
24
表-3 产品A各加工工序的时间间隔
工作中心
工序间隔时间
等待时间
运输时间
30
2
1
25
1
1
20
1
1
15
1
1
10
1
1
库房
1
表-4 产品A的工艺路线及工时定额
项目
工序号
关键工作中心
单件加工时间
生产准备时间
平均批量
单件准备时间
单件总时间
A
10
30
0.09
0.4
20
0.02
0.11
B
10
25
0.06
0.28
40
0.007
0.067
C
10
15
0.14
1.6
80
0.02
0.16
20
20
0.07
1.1
80
0.01375
0.08375
E
10
10
0.11
0.85
100
0.0085
0.1185
20
15
0.26
0.96
100
0.0096
0.2696
F
10
10
0.11
0.85
80
0.010625
0.120625
3、产品A的批量规则是净需求量法;零件B、C的批量规则均是:
2周期净需求量,零件E的批量规则是:
3周净需求,零件F的批量规则是:
固定批量60。
表-5 各零部件的批量规则
项目
计划收到量
现有库存
已分配量
提前期
固定批量
1
2
3
4
5
6
7
8
A
B
38
14
1
2周
E
80
140
2
3周
F
22
1
60
C
72
33
2
2周
4、各个工作中心的工时定额数据。
企业每周工作5天,每天工作8小时,每个工作中心只有一个操作工,所有的工作中心利用率和效率均为95%。
假设第2周接收到的80件零件E的第一道工10已经完成,其第二道工序20还需要在第一周占用工作中心15的能力。
试根据以上数据编制生产物料的需求计划、能力需求计划,并分析其能力负荷情况,以及外购物料D的采购计划。
实验过程
1根据上一年度产品A的实际需求数据利用某种预测方法,得到本年度各个周期产品A的预测量。
表-1 移动平均法预测
周期
上一年度实际需求
一次平滑指数
二次平滑指数
1
18
2
18
3
19
18.33
4
21
19.33
5
23
21
19.55
6
20
21.33
20.55
7
21
21.33
21.22
8
22
21
21.22
9
22
21.66
21.33
10
23
22.33
21.33
11
24
23
22.33
12
24
23.66
22.99
根据上表中的数据,得到的预测公式为:
Y=24.34+0.67T
根据上式,可以预测该年度各个月份的需求量如下表所示:
表 计划展望期内产品A的预测需求
产品A
需求时区
计划时区
预测时区
周期
1
2
3
4
5
6
7
8
9
10
11
12
预测需求
25
26
26
27
28
28
29
30
30
31
32
32
2、编制产品A的主生产计划(MPS)
表-2 产品A的主生产计划
计划周期
1
2
3
4
5
6
7
8
9
10
11
12
实际需求
24
25
20
25
18
20
0
8
0
10
0
0
预测需求
25
26
26
27
28
28
29
30
30
31
32
32
主生产计划
24
25
26
27
28
28
29
30
30
31
32
32
3 制定各个物料的物料需求计划
表-3 各零部件的物料需求计划
项目
计划周期
1
2
3
4
5
6
7
8
9
10
11
12
B
毛需求量
24
25
26
27
28
28
29
30
30
31
32
32
计划接收量
38
库存
14
28
3
27
0
28
0
30
0
31
0
32
0
净需求量
23
28
29
31
32
计划入库
50
56
59
61
64
计划下达
50
56
59
61
64
C
LT=2
毛需求量
48
50
52
54
56
56
58
60
60
62
64
64
计划接收量
72
库存
33
57
7
54
0
56
0
60
0
62
0
64
0
净需求量
45
56
58
60
64
计划入库
99
112
118
122
128
计划下达
99
112
118
122
128
E
LT=2
毛需求量
100
112
118
122
128
计划接收量
80
库存
140
140
120
120
8
8
122
122
0
0
0
0
0
净需求量
110
128
计划入库
232
128
计划下达
232
128
F
LT=1
毛需求量
50
56
59
61
64
计划接收量
库存
22
22
32
32
36
36
37
37
36
36
32
32
32
净需求量
28
24
23
24
28
计划入库
60
60
60
60
60
计划下达
60
60
60
60
60
D
LT=1
毛需求量
100
112
118
122
128
计划接收量
库存
0
净需求量
100
112
118
122
128
计划入库
100
112
118
122
128
采购下达
100
112
118
122
128
4编制每道工序的能力需求计划
1、计算每道工序在每个工作中心上的负荷
(1)工作中心30
从工艺路线可以看出,工作中心30只与物料A有关,根据12批次的A物料可以算出各周期内工作中心30的能力需求如下:
第一批次24个单位A需要的能力:
24*0.09+0.4=2.56
第二批次25个单位A需要的能力:
25*0.09+0.4=2.65
第三批次26个单位A需要的能力:
26*0.09+0.4=2.74
第四批次27个单位A需要的能力:
27*0.09+0.4=2.83
第五批次28个单位A需要的能力:
28*0.09+0.4=2.92
第六批次28个单位A需要的能力:
28*0.09+0.4=2.92
第七批次29个单位A需要的能力:
29*0.09+0.4=3.01
第八批次30个单位A需要的能力:
30*0.09+0.4=3.1
第九批次30个单位A需要的能力:
30*0.09+0.4=3.1
第十批次31个单位A需要的能力:
31*0.09+0.4=3.19
第十一,十二批次32个单位A需要的能力:
32*0.09+0.4=3.28
(2)工作中心25
从工艺路线可以看出,工作中心25只与物料B有关,根据5批次的B物料可以算出各周期内工作中心25的能力需求如下:
第二批次50个单位B需要的能力:
24*0.06+0.28=3.28
第四批次56个单位B需要的能力:
25*0.06+0.28=3.64
第六批次59个单位B需要的能力:
26*0.06+0.28=3.82
第八批次61个单位B需要的能力:
27*0.06+0.28=3.94
第十批次64个单位B需要的能力:
28*0.06+0.28=4.12
(3)工作中心20
从工艺路线可以看出,工作中心20只与物料C有关,根据5批次的C物料可以算出各周期内工作中心20的能力需求如下:
第一批次99个单位C需要的能力:
99*0.07+1.1=8.03
第三批次112个单位C需要的能力:
112*0.07+1.1=8.94
第五批次118个单位C需要的能力:
118*0.07+1.1=9.36
第七批次122个单位C需要的能力:
122*0.07+1.1=9.64
第九批次128个单位C需要的能力:
128*0.07+1.1=10.06
(4)工作中心15
从工艺路线可以看出,工作中心15与物料C,E有关,根据5批次的C物料2批次的E物料及E占用工作中心15的能力可以算出各周期内工作中心15的能力需求如下:
第一批次99个单位C需要的能力:
99*0.14+1.6=15.46
第三批次112个单位C需要的能力:
112*0.14+1.6=17.28
第五批次118个单位C需要的能力:
118*0.14+1.6=18.12
第七批次122个单位C需要的能力:
122*0.14+1.6=18.68
第九批次128个单位C需要的能力:
128*0.14+1.6=19.52
第四批次232个单位E需要的能力:
232*0.26+0.96=61.28
第八批次128个单位E需要的能力:
128*0.26+0.96=34.24
第2周接收到的80件零件E占用工作中心15的能力:
80*0.26+0.96=21.76
(5)工作中心10
从工艺路线可以看出,工作中心10与物料E.F有关,根据2批次的E物料5批次的F物料可以算出各周期内工作中心10的能力需求如下:
第四批次232个单位E需要的能力:
232*0.11+0.85=26.37
第八批次128个单位E需要的能力:
128*0.11+0.85=14.93
第一,三,五,七,九批次60个单位F需要的能力:
(60*0.11+0.85)*5=37.25
2、计算每个工作中心的可用能力
小时/天
3、计算每个工作中心对各个负荷的加工天数(必要时取整)
(1)工作中心30
第一批次24个单位A需要的天数:
2.56/7.22≈1天
第二批次25个单位A需要2.65/7.22≈1天
第三批次26个单位A需要2.74/7.22≈1天
第四批次27个单位A需要2.83/7.22≈1天
第五批次28个单位A需要2.92/7.22≈1天
第六批次28个单位A需要2.92/7.22≈1天
第七批次29个单位A需要3.01/7.22≈1天
第八批次30个单位A需要3.1/7.22≈1天
第九批次30个单位A需要3.1/7.22≈1天
第十批次31个单位A需要3.19/7.22≈1天
第十一,十二批次32个单位A需要3.28/7.22≈1天
(2)工作中心25
第三批次50个单位B需要3.28/7.22≈1天
第五批次56个单位B需要3.64/7.22≈1天
第七批次59个单位B需要3.82/7.22≈1天
第九批次61个单位B需要3.94/7.22≈1天
第十一批次64个单位B需要4.12/7.22≈1天
(3)工作中心20
第三批次99个单位C需要8.03/7.22≈1天
第五批次112个单位C需要8.94/7.22≈1天
第七批次118个单位C需要9.36/7.22≈1天
第九批次122个单位C需要9.64/7.22≈1天
第十一批次128个单位C需要10.06/7.22≈1天
(4)工作中心15
第三批次99个单位C需要15.46/7.22≈2天
第五批次112个单位C需要17.28/7.22≈2天
第七批次118个单位C需要18.12/7.22≈3天
第九批次122个单位C需要18.68/7.22≈3天
第十一批次128个单位C需要19.52/7.22≈3天
第六批次232个单位E需要61.28/7.22≈8天
第十批次128个单位E需要34.2/7.22≈5天
第2周接收到的80件零件E占用工作中心15的能力21.76/7.22≈3天
(5)工作中心10
第六批次232个单位E需要26.37/7.22≈4天
第十批次128个单位E需要14.93/7.22≈2天
第二,四,六,八,十各批次60个单位F需要7.45/7.22≈1天
4、用倒排序法计算每道工序的开工日期和完工日期
(1)每种零件各批次所对应的工序开完工时间
零件A
⏹第一批次
⏹第二批次
⏹第三批次
零件B
⏹第一批次50
第二批次56
第三批次59
⏹第四批次61
⏹第五批次64
零件C
⏹第一批次99
第二批次112
⏹第三批次118
⏹第四批次122
⏹第五批次128
零件E
⏹第一批次232
⏹第二批次128
零件F
零件D
(2)能力需求计划汇总表
表-4 各道工序的能力需求汇总表
零件
工作
中心
拖期
计划周期
1
2
3
4
5
6
7
8
9
10
11
12
A
30
0
2.56
2.65
2.74
2.83
2.92
2.92
3.01
3.1
3.1
3.19
3.28
3.28
小计
0
2.56
2.65
2.74
2.83
2.92
2.92
3.01
3.1
3.1
3.19
3.28
3.28
B
25
0
0
3.28
0
3.64
0
3.82
0
3.94
0
4.12
0
0
小计
0
0
3.28
0
3.64
0
3.82
0
3.94
0
4.12
0
0
C
20
0
8.03
8.94
9.36
9.64
10.06
小计
0
15
0
15.46
17.28
18.12
18.68
19.52
E
15
0
21.76
61.28
34.24
小计
0
37.22
17.28
79.4
18.68
53.76
10
0
26.37
14.93
F
10
0
7.45
7.45
7.45
7.45
7.45
小计
0
7.45
7.45
26.37
7.45
7.45
14.93
7.45
5 编制能力负荷图(对比实际能力需求与能力定额之差)
(1)工作中心30
(2)工作中心25
(3)工作中心20
(4)工作中心15
(5)工作中心10
6、请选择某个批次的产品制定对应的车间作业计划(PAC,要求对该批次产品的生产过程所涉及的各个关键工作中心制定“派工单”)
项目
工序号
关键工作中心
需求数量
最早开工时间
最晚开工时间
最晚完工时间
A
10
30
24
5月26日
5月28日
6月1日
B
10
25
0
7月2日
7月3日
7月6日
C
10
15
99
5月28日
5月30日
6月5日
C
20
20
99
6月5日
6月7日
6月8日
E
10
10
0
6月7日
6月11日
6月15日
E
20
15
0
6月19日
6月19日
6月29日
F
10
10
60
5月28日
5月29日
6月4日
7 心得体会与经验总结.
实验过程
<1>用到的工具
<2>犯过的错误
<3>没弄懂的东西
<4>掌握的东西