压铸技术.docx
《压铸技术.docx》由会员分享,可在线阅读,更多相关《压铸技术.docx(30页珍藏版)》请在冰豆网上搜索。
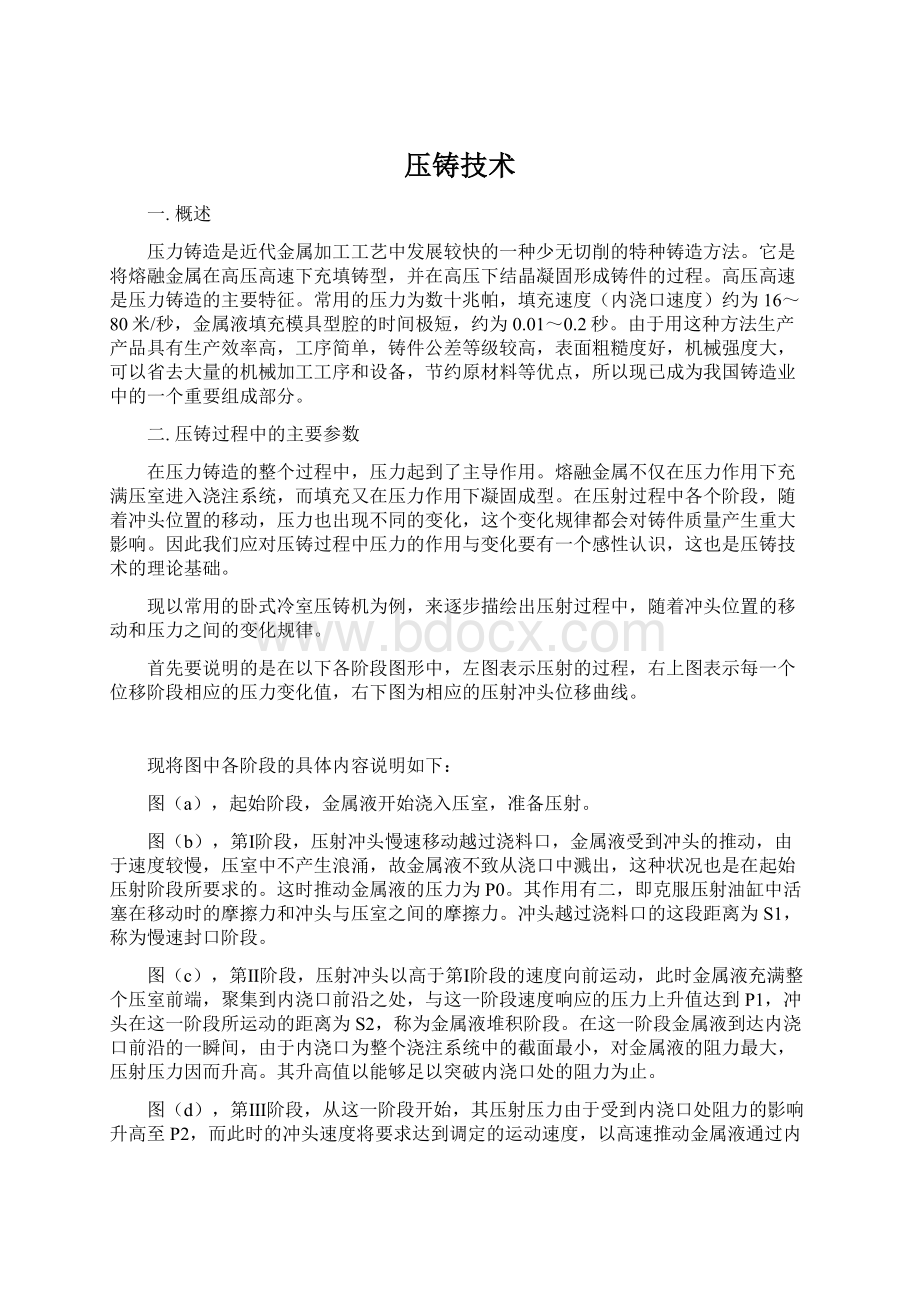
压铸技术
一.概述
压力铸造是近代金属加工工艺中发展较快的一种少无切削的特种铸造方法。
它是将熔融金属在高压高速下充填铸型,并在高压下结晶凝固形成铸件的过程。
高压高速是压力铸造的主要特征。
常用的压力为数十兆帕,填充速度(内浇口速度)约为16~80米/秒,金属液填充模具型腔的时间极短,约为0.01~0.2秒。
由于用这种方法生产产品具有生产效率高,工序简单,铸件公差等级较高,表面粗糙度好,机械强度大,可以省去大量的机械加工工序和设备,节约原材料等优点,所以现已成为我国铸造业中的一个重要组成部分。
二.压铸过程中的主要参数
在压力铸造的整个过程中,压力起到了主导作用。
熔融金属不仅在压力作用下充满压室进入浇注系统,而填充又在压力作用下凝固成型。
在压射过程中各个阶段,随着冲头位置的移动,压力也出现不同的变化,这个变化规律都会对铸件质量产生重大影响。
因此我们应对压铸过程中压力的作用与变化要有一个感性认识,这也是压铸技术的理论基础。
现以常用的卧式冷室压铸机为例,来逐步描绘出压射过程中,随着冲头位置的移动和压力之间的变化规律。
首先要说明的是在以下各阶段图形中,左图表示压射的过程,右上图表示每一个位移阶段相应的压力变化值,右下图为相应的压射冲头位移曲线。
现将图中各阶段的具体内容说明如下:
图(a),起始阶段,金属液开始浇入压室,准备压射。
图(b),第Ⅰ阶段,压射冲头慢速移动越过浇料口,金属液受到冲头的推动,由于速度较慢,压室中不产生浪涌,故金属液不致从浇口中溅出,这种状况也是在起始压射阶段所要求的。
这时推动金属液的压力为P0。
其作用有二,即克服压射油缸中活塞在移动时的摩擦力和冲头与压室之间的摩擦力。
冲头越过浇料口的这段距离为S1,称为慢速封口阶段。
图(c),第Ⅱ阶段,压射冲头以高于第Ⅰ阶段的速度向前运动,此时金属液充满整个压室前端,聚集到内浇口前沿之处,与这一阶段速度响应的压力上升值达到P1,冲头在这一阶段所运动的距离为S2,称为金属液堆积阶段。
在这一阶段金属液到达内浇口前沿的一瞬间,由于内浇口为整个浇注系统中的截面最小,对金属液的阻力最大,压射压力因而升高。
其升高值以能够足以突破内浇口处的阻力为止。
图(d),第Ⅲ阶段,从这一阶段开始,其压射压力由于受到内浇口处阻力的影响升高至P2,而此时的冲头速度将要求达到调定的运动速度,以高速推动金属液通过内浇口进入型腔,这种冲头速度通称为压射速度,而这一阶段冲头的运动距离为S3,称为填充阶段。
图(e),第Ⅳ阶段,这一阶段是按照压射缸所调定的压力,使铸件在凝固阶段进一步致密的最终加压。
其最终压力的大小,取决于压铸机压射系统的性能。
有两种情况可以解释,当压射系统无增压机构时,其最终压力的上升为P3,但当压射系统中带有增压机构时,其最终的增压压力可以从P3上升至P4,这一阶段压射冲头只前移一段极短的距离S4,从上图中可清楚地看到。
这一阶段称为增压压实阶段。
以上所述,如果按照压射各个阶段来划分的话,可以称作为四级压射系统,对于现代化的压铸机而言,多数按以上要求进行设计。
各阶段速度的变化,可以根据铸件的种类和要求进行调节,并可在监视设备上进行显示、储存和记录各阶段最合理的变化,以达到稳定生产的目的。
至于通常所称的三级压射系统,则是将四级压射系统中的第Ⅱ阶段和第Ⅲ阶段合并为一个阶段而加以命名的。
三.压铸工艺压铸工艺是将压铸机、压铸模和合金三大要素有机地组合而加以综合运用的过程。
而压铸时金属按填充型腔的过程,是将压力、速度、温度以及时间等工艺因素得到统一的过程。
同时,这些工艺因素又相互影响,相互制约,并且相辅相成
只有正确选择和调整这些因素,使之协调一致,才能获得预期的结果。
因此,在压铸过程中不仅要重视铸件结构的工艺性,压铸模的先进性,压铸机性能和结构优良性,压铸合金选用的适应性和熔炼工艺的规范性;更应重视压力、温度和时间等工艺参数对铸件质量的重要作用。
在压铸过程中应重视对这些参数进行有效的控制。
(一)压力
压力的存在是压铸工艺区别其他铸造方法的主要特点。
1.压射力
压射力是压铸机压射机构中推动压射活塞运动的力。
它是反映压铸机功能的一个主要参数。
压射力的大小,由压射缸的截面积和工作液的压力所决定。
压射力的计算公式如下:
P压射力=P压射油缸×π×D2/4
式中:
P压射力-压射力(N-牛)
P压射油缸-压射油缸内工作液的压力(Pa-帕)
D-压射缸的直径(m-米)
π=3.1416
2.比压
压室内熔融金属在单位面积上所受的压力称为比压。
比压也是压射力与压室截面积的比值关系换算的结果。
其计算公式如下:
P比压=P压射力/F压室截面积
式中:
P比压-比压(Pa-帕)
P压射力-压射力(N-牛)
F压室截面积-压室截面积(m2-米2)
即F压室截面积=πD2/4式中D(m-米)为压室直径
π=3.1416
3.压力的作用
(1)比压对铸件机械性能的影响
比压(可通过调整压射力和冲头截面积控制)增大,结晶细,细晶层增厚,由于填充特性改善,表面质量提高,气孔影响减轻,从而抗拉强度提高,但延伸率有所降低。
(2)对填充条件的影响
合金熔液在高比压作用下填充型腔,合金温度升高,流动性改善,有利于铸件质量的提高。
.比压的选择
(1)根据铸件的强度要求考虑
将铸件分为有强度要求的和一般要求的两类,对于有强度要求的,应该具有良好的致密度。
这是应该采用高的增压比压。
(2)根据铸件壁厚考虑
在一般情况下,压铸薄壁铸件时,型腔中的流动阻力较大,内浇口也采用较薄的厚度,因此具有大的阻力,故要有较大的填充比压,才能保证达到需要的内浇口速度。
对于厚壁铸件,一方面选定的内浇口速度较低,并且金属的凝固时间较长,可以采用较小的填充比压;另一方面,为了使铸件具有一定的致密度,还需要有足够的增压比压才能满足要求。
(填充比压,增压比压)
对于形状复杂的铸件,填充比压应选用高一些。
此外,如合金的类别,内浇口速度的大小,压铸机合模能力的功率及模具的强度等,都应作适当考虑。
填充比压的大小,主要根据选定的内浇口速度计算得到。
至于增压比压的大小,根据合金类别,可参考下表数值选用。
当型腔中排气条件良好,内浇口厚度与铸件壁厚的比值适当的情况下,可选用低的增压比压。
而排气条件愈差,内浇口厚度与铸件壁厚比值愈小时,则增压比压应愈高。
推荐选用增压比压范围表
零件类型
铝合金
锌合金
黄铜
承受轻负荷的零件
30~40MPa
13~20MPa
30~40MPa
承受较大负荷的零件
40~80MPa
20~30MPa
40~60MPa
气密性面大壁薄零件
80~120MPa
25~40MPa
80~100MPa
锌合金以热室压铸机为主
5.胀型力和锁模力
(一) 压铸过程中,填充结束并转为增压阶段时(关键阶段),作用于正在凝固的金属上的比压(增压比压),通过金属(铸件浇注系统、排溢系统)传递型腔壁面,此压力称为胀型力(又称反压力)。
当胀型力作用在分型面上时,便为分型面胀型力,而作用在型腔各个侧壁方向时,则称为侧面胀型力。
胀型力可用下式表示:
P胀型力=P比压×A投影面积
式中:
P胀型力-胀型力(N-牛)
P比压-增压比压(Pa-帕)A投影面积-承受胀型力的投影面积(m2-米2)
通常情况下必须使锁模力大于计算得到的胀型力。
否则,在金属液压射时,模具分型面会胀开,从而产生金属飞溅,并使型腔中的压力无法建立,造成铸件尺寸公差难以保证,甚至难以成型。
(可见飞料不是一个小case)
锁模力(即合模力)是选用压铸机时首先要确定的重要参数。
一般应满足下面公式的要求:
P锁模力≥K×P胀型力
式中:
P锁模力-压铸机的锁模力(N-牛)
K-安全系数(一般取K=1.3)
P胀型力-胀型力(N-牛)
(二)压射速度
压射过程中,压射速度受压力的直接影响,又与压力共同对铸件内部质量、表面质量和轮廓清晰程度起着重要的作用。
生产中,速度的表示通常为冲头速度(压射速度)和内浇口速度两种。
1.压射速度
压室内的压射冲头推动金属移动时的速度称为压射速度(又称为冲头速度)。
而压射速度分为两级,Ⅰ级压射速度亦称为慢压射速度,这级速度是指冲头起始动作直至冲头将室内的金属送入内浇口之前的运动速度,在这一阶段中要求将压室中的金属液充满压室,在既不过多地降低合金液温度又有利于排除压室中的气体的原则下,该阶段速度应尽量低,一般为0.3米/秒。
Ⅱ级压射速度又称快压射速度。
这个速度由压铸机的特性所决定。
压铸机所给定的最高压射速度一般在4~5米/秒范围内,旧式的压铸机压射速度较低,而近代的压铸机则较高,甚至达到9米/秒。
(1)快压射速度的作用和影响
提高压射速度,动能转化为热能,提高了合金熔液的流动性,有利于消除流痕、冷隔等缺陷,提高了机械性能和表面质量;但速度过快时,合金熔液雾状与气体混合,产生严重涡流包气,机械性能下降。
(2)快压射速度的选择考虑因素
①压铸合金的特性:
熔化潜热、合金的比热、导热性和凝固温度范围。
②模具温度高时,压射速度可适当减低,在考虑到模具热传导状况,模具设计结构和制造质量,以及提高模具寿命,亦可适当限制压射速度。
③铸件质量要求:
表面质量要求高和薄壁复杂件,采用较高的压射速度。
2.内浇口速度
熔融金属在冲头移动作用下,经过横浇道到达内浇口,然后填充型腔,当机器的压射系统性能优良时,熔融金属通过内浇口的速度可以认为不变(或变化很小),
这个不变的速度,即熔融金属通过内浇口导入型腔的线速度,便称为内浇口速度,通常采用的内浇口速度范围为15~70米/秒。
熔融金属在通过内浇口后,进入型腔各部分流动(填充)时,由于型腔的形状和厚度(铸件的壁厚),模具热状态(温度场分布)等各种因素的影响,流动的速度随时在发生变化,这种变化的速度称为填充速度。
通常在工艺参数上只选定不变的速度来衡量,所以内浇口速度就是重要的工艺参数之一。
内浇口速度的高低与铸件机械性能的影响极大,内浇口速度太低,铸件强度下降;速度提高,强度上升;速度过高强度又下降。
3.冲头速度(压射速度)与内浇口速度(填充速度)的关系
根据连续性原理,内浇口速度和压射速度的关系可由下式表示:
流入的金属量=进入的金属量
V内浇口=F压射室×V压射/F内浇口
式中:
V内浇口-内浇口速度(m/s-米/秒)
F压射室-压射室截面积(cm2-厘米2)
V压射-压射速度(m/s-米/秒)
F内浇口-内浇口截面积(cm2-厘米2)
因此,冲头压射速度越高,则金属流经内浇口速度越高。
4.速度的选择
在压铸生产中,速度与压力共同对铸件内在质量,表面要求和轮廓清晰度起着重要作用。
综上所述,如果对压铸件的机械性能,如抗拉强度和致密性提出了高的要求,则不应选用过大的内浇口速度,这样能降低由于紊流动所造成的涡流,这个涡流含有空气和由涂料挥发的气体。
随着卷入涡流内的空气和蒸汽的增多,压铸件组织内部呈多孔性,机械性能明显变坏。
(速度高,表面質量好,但容易出現氣孔,影響机械性能)
如果压铸件结构是复杂的薄壁零件,并对其表面质量提出了较高的要求,应选用较高的压射速度和内浇口速度,完全是必要的。
根据铸件的不同情况,可按下表的推荐值选用,核算出压射速度,进行试压修正。
浇注系统各个部位填充速度推荐值表
部位
直浇道
横浇道
内浇口
填充速度(m/s)
15~25
20~35
30~60
推荐的铸件平均壁厚与内浇口速度的关系表
铸件平均壁厚(mm)
内浇口速度(m/s)
铸件平均壁厚(mm)
内浇口速度(m/s)
1
46~55
5
32~40
1.5
44~53
6
30~37
2
42~50
7
28~34
2.5
40~48
8
26~32
3
38~46
9
24~29
3.5
36~44
10
24~27
4
34~42
内浇口速度与压射速度、压室直径和内浇口截面积有关,可通过以下方面调整:
(1)调整压射冲头速度
(2)更换压射室直径
(3)改变内浇口截面积
(三)压射行程
根据压铸填充过程各个阶段的冲头位移-压力曲线图可知,压射冲头移动总共分为五个阶段。
其中第Ⅰ阶段(慢速封口阶段)加上第Ⅱ阶段(金属液堆积阶段)的压射冲头的位移量通常称为慢压射行程。
第Ⅲ阶段(填充阶段)的压射冲头的位移量通常称为快压射行程。
第Ⅳ阶段(增压压实阶段)的压射冲头位移量通常称为增压压实行程。
特别要提及的是,铸件气孔中的气体来源于合金液、模具型腔、压射室及涂料。
但在正常规范的生产中铸件气孔中的气体主要来源于模具型腔和压射室,模具型腔主要靠合理的浇注系统和溢流排气系统来最大程度地减少气体进入铸件并使之排出模外,而压射室中的气体是靠调整压射行程来控制压射冲头快速填充位移的起点,也就是慢压射行程的终点,使合金液以慢速充满压室前端堆积于内浇口前沿,从而最大程度地减少气体被合金液卷入而带入模具型腔,达到最大程度地减少铸件中的气孔,提高铸件的内部质量。
而在正常生产中铸件气孔中的气体主要来源于压射室。
所以,在压铸过程中对压射行程的控制是非常必要的。
压射行程的计算:
L快=体积/面积
L快=G/γ/F压室
式中:
L快-快压射行程(cm-厘米)
G-进入内浇口所有合金的重量(铸件重量+溢渣包重量)(g-克)
γ-合金的液态密度(g/cm3-克/厘米3)
铝合金的液态密度γ=2.4g/cm3
F压室-压射室截面积(cm2-厘米2)
压铸机快压行程的调整位置的计算:
L快压起点=L冲头伸出+L料饼厚+L快
式中:
L快压起点-快压行程开关距冲头跟随终点行程开关的距离(cm-厘米)
L冲头伸出-冲头跟随伸出模具分型面的距离(cm-厘米)
L料饼厚-铸件浇注系统中余料饼的厚度(cm-厘米)
L快-快压射行程(cm-厘米)
(四)温度
压铸过程中,温度对填充过程的热状态,以及操作的效率等方面起着重要的作用。
压铸中所指的温度是指浇注温度和模具温度。
温度控制是获得优良铸件的重要因素。
1.浇注温度
熔融金属的浇注温度是指它自压室进入型腔时的平均温度。
由于对压室内的金属液的温度测量不方便,一般以保温炉的温度表示。
(1)浇注温度的作用和影响
①气体在合金中溶解度,随温度的升高而增大,其熔解金属中的气体,在压铸过程中难以析出,对塑性是有影响的。
②含铁量随合金温度升高而增加,使流动性降低,结晶粗大,性能恶化。
③铝合金随温度升高氧化加剧,氧化夹杂物增多,使合金性能恶化。
因此合金过热,易产生缩孔、裂纹、气孔、氧化夹杂物,故机械性能降低。
合金温度过低,也会产生成分不均匀,流动性差,影响填充条件,产生缺陷。
④合金温度对填充流态有直接影响。
浇注温度过高,又高速的作用下,易产生紊流、涡流包气。
溫度升高也會不飽料。
因為。
。
。
(1)含鐵量升高,流動性不佳,粗大結晶;
(2)氣體融解度上升,析出後,產生不飽料現象;
(2)合金浇注温度选择
通常在保证“成型”和所要求表面质量的前提下,尽可能采用低的温度。
浇注温度一般高于压铸合金的液相线温度20~30℃。
推荐压铸合金的浇注温度如下表。
第8页共25页2004年9月·压铸工艺培训讲义
压铸合金浇注温度推荐值表
合金类别
锌合金
铝合金
镁合金
铜合金
浇注温度℃
410~450
610~700
640~700
900~980
2.模具温度
在压铸过程中,模具需要一定的温度,模具的温度是压铸工艺中又一重要的因素,它对提高生产效率和获得优质铸件有着重要的作用。
(1)模具温度的作用和影响
①在填充过程中,模温对液流温度、粘度、流动性、填充时间和填充流态等均有较大影响。
模温过低时,表层冷凝后又被高速液流破碎(澆口處容易出現氣孔),产生表层缺陷,甚至不能“成型”,模温过高时,虽有利于获得光洁的铸件表面,但易出现收缩凹陷。
②模温对合金液冷却速度、结晶状态、收缩应力均有明显影响。
模温过低时,收缩应力增大,铸件易产生裂纹。
③模温对模具寿命影响甚大,激烈的温度变化,形成复杂的应力状态,频繁的应力交变导致模具龟裂。
(熱應力導致龜裂)
④模温对铸件尺寸公差的影响,模温稳定,则铸件尺寸收缩率也相应稳定,尺寸公差等级也得以提高。
(2)影响模具温度的主要因素
①合金浇注温度、浇注量、热容量和导热性。
②浇注系统和溢流槽的设计,用以调整热平衡状态。
?
③压射比压和压射速度。
④模具设计,模具体积大,热容量大,模温波动较小。
模具材料导热性愈好,温度分布较均匀有利于改善热平衡。
⑤模具合理预热,提高初温,有利于改善热平衡,提高模具寿命。
⑥生产频率越快,模温升高,在一定范围内对铸件和模具寿命都是有利的。
⑦模具润滑起到隔热和散热作用。
(3)模具温度对机械性能的影响
模具温度提高,改善了填充条件,使机械性能得到提高。
模温过高,合金冷却温度降低,细晶层厚减薄,晶粒较粗大,故强度有所下降。
为此,要获得质量稳定的优质铸件,必须将模具温度严格控制在最佳的工艺范围内。
这就必须应用模具冷却加热装置,以保证模具在恒定温度范围内工作。
第9页共25页2004年9月·压铸工艺培训讲义
(4)模具温度的选择与控制
①模具温度的选择
模具温度的选择,应根据铸件的形状大小和结构特点,合金的性质与浇注条件等各个方面的因素综合考虑。
推荐的模具的预热温度及工作温度如下表所示。
推荐的模具工作温度表
合金类别
模具预热温度(℃)
模具工作温度(℃)
锌合金
120~160
160~200
镁合金
150~180
180~250
铝合金
150~180
180~260
铜合金
200~250
250~300
②模具温度的控制
为了保证压铸生产过程的正常连续进行,模具工作温度应保持在一定的范围内,就必须使模具处于热平衡的状态下。
模具热平衡指的是,在每一个压铸循环中,熔融金属传给模具的热量,应等于模具传走的热量和冷却及加热装置所传走的热量。
模具温度控制可采用专制的,采用不燃油作介质的模具加热冷却装置系统。
但大多数目前还是采用在模具上开设水冷却和电加热装置来进行模具的温度控制。
(五)时间
压铸工艺上的“时间”是填充时间,增压建压时间,持压时间及留模时间。
这些“时间”都是压力、速度、温度这三个因素,再加上熔融金属的物理特性,铸件结构(特别是壁厚),模具结构(尤其是浇注系统和溢流系统)等各方面的综合结果。
时间是一个多元复合的因素,但它与上述各因素有着密切的关系。
因此,“时间”在压铸工艺上是至关重要的。
1.填充时间
熔融金属在压力作用下开始进入型腔直到充满的过程所需的时间称为填充时间。
填充时间是压力、速度、温度、模具的浇注与溢流系统的特点,合金的性质,以及铸件结构(壁厚)等多种因素结合以后所产生的结果。
因而,也是填充过程中各种因素相互协调程度的综合反映。
填充时间以熔融金属尚未凝固而填充完成为原则,填充时间的选择按下表:
第10页共25页2004年9月·压铸工艺培训讲义
铸件的平均壁厚与填充时间的推荐值表
铸件平均壁厚(mm)
填充时间(s)
铸件平均壁厚(mm)
填充时间(s)
1
0.010~0.014
5
0.048~0.072
1.5
0.014~0.020
6
0.056~0.084
2
0.018~0.026
7
0.066~0.100
2.5
0.022~0.032
8
0.076~0.116
3
0.028~0.040
9
0.088~0.138
3.5
0.034~0.050
10
0.100~0.160
4
0.040~0.060
按表选用时还应考虑下列情况:
①合金浇注温度高时,填充时间可选长些。
②模具温度高时,填充时间可选长些。
③铸件厚壁部分离内浇口远时,填充时间可选长些。
④熔化潜热和比热高的合金,填充时间可选长些。
2.增压建压时间
增压建压时间是指熔融金属在充型过程中的增压阶段,从充满型腔的瞬时开始,直至增压压力达到预定值所需建立起来的时间。
也就是压射比压上升到增压比压建立起来所需的时间。
3.持压时间
熔融金属充满型腔后,使熔融金属在增压比压作用下凝固的这段时间,称为持压时间。
持压作用是使压射冲头将压力通过还未凝固的余料、浇口部分的金属传递到型腔,使正在凝固的金属在高压下结晶,从而获得致密的铸件。
持压时间的选择,按下列因素考虑:
①压铸合金的特性:
压铸合金结晶范围大,持压时间应选得长些。
②铸件壁厚:
铸件平均壁厚厚度大,持压时间可选得长些。
③浇注系统:
内浇口厚,持压时间可选得长些。
第11页共25页2004年9月·压铸工艺培训讲义
推荐常用的比压时间表(s)
合金
铸件壁厚(mm)
<2.5
2.5~6
锌合金
1~2
3~4
铝合金
1~2
3~5
镁合金
1~2
3~5
铜合金
2~3
5~7
4.留模时间
留模时间是压铸过程中,从持压终了至开模顶出铸件的这段时间。
足够的留模时间,是使铸件在模具内得到充分凝固和适度的冷却使之具有一定的强度,在开模和顶出时,铸件不致产生变形或拉裂。
留模时间的选择,通常以顶出铸件不变形、不开裂的最短时间为宜。
然而,过长的留模时间不仅降低了生产效率,而且会带来不良的后果。
例如:
不易脱模,因合金的热脆性而引起裂纹,改变了预定的收缩量。
推荐常用的留模时间表(s)
合金
壁厚<3mm
壁厚3~6mm
壁厚>6mm
锌合金
5~10
7~12
20~25
铝合金
7~12
10~15
25~30
镁合金
7~12
10~15
25~30
铜合金
8~15
15~20
25~30
综上所述,压铸生产中的工艺参数压力、速度、温度、时间选择可按下列原则:
①铸件壁越厚,结构越复杂,压射力越大。
②铸件壁越薄,结构越复杂,压铸速度越快。
③铸件壁越厚,持压留模时间需越长。
④铸件壁越薄,结构越复杂,模温浇温需越高。
(六)压室的充满度
通过对各种工艺因素的分析,并根据机器提供的规格,初步选定了压室直径后,还应考虑压室的容量,而浇入压室的金属液量占压室总容量的程度称为压室的充满度,通常以百分率计。
第12页共25页2004年9月·压铸工艺培训讲义
充满度对于卧式冷室压铸机有着特殊的意义。
因为,卧式冷室压铸机的压室在浇入金属液后,并不是完全充满而只在金属液上方留有一定的空间。
这个空间占有的体积越大,存有空气越