螺杆式氯气液化机组中常见故障.docx
《螺杆式氯气液化机组中常见故障.docx》由会员分享,可在线阅读,更多相关《螺杆式氯气液化机组中常见故障.docx(7页珍藏版)》请在冰豆网上搜索。
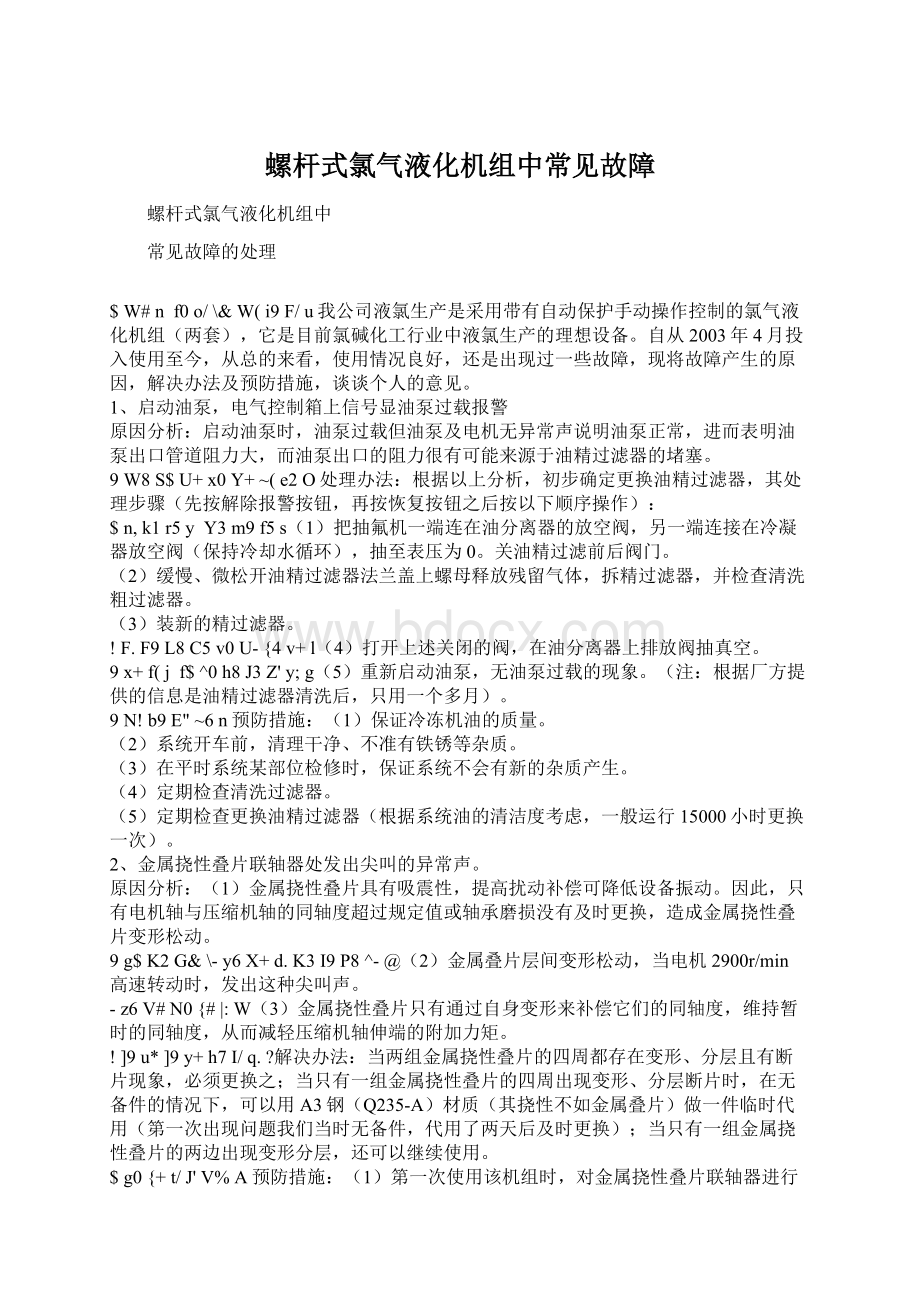
螺杆式氯气液化机组中常见故障
螺杆式氯气液化机组中
常见故障的处理
$W#n f0o/\&W(i9F/u我公司液氯生产是采用带有自动保护手动操作控制的氯气液化机组(两套),它是目前氯碱化工行业中液氯生产的理想设备。
自从2003年4月投入使用至今,从总的来看,使用情况良好,还是出现过一些故障,现将故障产生的原因,解决办法及预防措施,谈谈个人的意见。
1、启动油泵,电气控制箱上信号显油泵过载报警
原因分析:
启动油泵时,油泵过载但油泵及电机无异常声说明油泵正常,进而表明油泵出口管道阻力大,而油泵出口的阻力很有可能来源于油精过滤器的堵塞。
9W8S$U+x0Y+~(e2O处理办法:
根据以上分析,初步确定更换油精过滤器,其处理步骤(先按解除报警按钮,再按恢复按钮之后按以下顺序操作):
$n,k1r5y Y3m9f5s
(1)把抽氟机一端连在油分离器的放空阀,另一端连接在冷凝器放空阀(保持冷却水循环),抽至表压为0。
关油精过滤前后阀门。
(2)缓慢、微松开油精过滤器法兰盖上螺母释放残留气体,拆精过滤器,并检查清洗粗过滤器。
(3)装新的精过滤器。
!
F.F9L8C5v0U-{4v+l(4)打开上述关闭的阀,在油分离器上排放阀抽真空。
9x+f(j f$^0h8J3Z'y;g(5)重新启动油泵,无油泵过载的现象。
(注:
根据厂方提供的信息是油精过滤器清洗后,只用一个多月)。
9N!
b9E"~6n预防措施:
(1)保证冷冻机油的质量。
(2)系统开车前,清理干净、不准有铁锈等杂质。
(3)在平时系统某部位检修时,保证系统不会有新的杂质产生。
(4)定期检查清洗过滤器。
(5)定期检查更换油精过滤器(根据系统油的清洁度考虑,一般运行15000小时更换一次)。
2、金属挠性叠片联轴器处发出尖叫的异常声。
原因分析:
(1)金属挠性叠片具有吸震性,提高扰动补偿可降低设备振动。
因此,只有电机轴与压缩机轴的同轴度超过规定值或轴承磨损没有及时更换,造成金属挠性叠片变形松动。
9g$K2G&\-y6X+d.K3I9P8^-@
(2)金属叠片层间变形松动,当电机2900r/min高速转动时,发出这种尖叫声。
-z6V#N0{#|:
W(3)金属挠性叠片只有通过自身变形来补偿它们的同轴度,维持暂时的同轴度,从而减轻压缩机轴伸端的附加力矩。
!
]9u*]9y+h7I/q.?
解决办法:
当两组金属挠性叠片的四周都存在变形、分层且有断片现象,必须更换之;当只有一组金属挠性叠片的四周出现变形、分层断片时,在无备件的情况下,可以用A3钢(Q235-A)材质(其挠性不如金属叠片)做一件临时代用(第一次出现问题我们当时无备件,代用了两天后及时更换);当只有一组金属挠性叠片的两边出现变形分层,还可以继续使用。
$g0{+t/J'V%A预防措施:
(1)第一次使用该机组时,对金属挠性叠片联轴器进行冷机状态下找正,在机组连续运行4小时后,检查其平行偏差和角偏差,直至偏差值调整至规定尺寸,再运行约一周后,停机立即检查同轴度(角偏差和平行偏差),若不正常,则重新调整直至满足要求为止。
(2)定时检查机组地脚螺栓是否紧固。
(3)随时监听轴承的声音是否异常。
(4)若是一用一备的机组,定期轮换使用,定期检查两轴的同轴度,从而保证偏差值在规定范围内。
3、电机轴伸端的轴承位置有异常声
原因分析:
其轴承坏的原因可能是:
(1)滚动轴承本身质量不佳,寿命短;
*B2J$v6f,K2~0Y*d7g
(2)滚动轴承的润滑脂没有定期更换;
7~!
z8M-u D1Q5j(3)电机轴和压缩机的同轴度偏差的影响。
处理办法:
更换质量好的轴承,调整好电机轴和压缩机轴的同轴度。
预防措施:
(1)定期巡回检查,发现轴承出现问题及时处理。
(2)定期检查轴承的润滑情况(不能出现“干油”现象)。
.}3I"c2u$}%~#Y#J(3)严把轴承、油脂的质量关(买质量好的轴承和油脂)。
(4)记录轴承有效运行时间、轴承厂家,定期更换轴承。
7e&N+l/H$v*T.j5x&`8s4、压缩机运行时,油分离器下视镜看不见油机头噪音大。
%W"J q/J-c2N/s原因分析:
(1)油进入压缩机起到润滑、降噪、降温、密封的作用。
油位降低,机头有噪音,表明油进入压缩机的量不足。
;t.I#o%a5Z处理办法:
(1)利用油蒸馏器,回收液化器的油。
9_,W:
h:
I1x @)I+k
(2)把油分离器另一端的油阀打开、排尽并检查油分离器滤芯处垫片是否密封好。
.\"I-];f9{.Y0T"k2C(3)停车,按加油程序进行补油至规定要求的油位。
(4)油分离器油位从上视镜中心降至正视镜看不见油,表明油进入油分离器另一端,且有一部分油带到液化器(从液化器液位计或液氯的液化温度升高可知);
预防措施:
加强巡检,发现油分离器液位降低,采取以下措施:
+P5v1A4\7R2~0R7t
(1)打开油分离器底部压缩机的回油阀约3~5分钟后关该阀,同时观察油分离器液位是否恢复正常,若油不能到达规定液位,说明有部分油进入液化器。
(2)为了避免油进入液化器,不仅控制最佳油温在40~55℃之间(保证油与R22分离效果),而且控制好压缩机吸气不带液,这需控制液化最高液位在规定范围内(满液式卧式列管换热器的最高静液位为直径的70%,一般在液化器管壳中心位置),液位不能超高,还要根据环境气温降低(意味着热负荷能量减小),适当调小节流阀(或膨胀阀)的开度。
(3)开车时增载不能过快避免吸气带液。
(4)油分离的油位不能超高。
此外,特别注意在停压缩后,必须关闭吸气阀,这是因为停车时,排气压力高于吸气,油分离器的油随R22通过压缩机吸气阀及其管道进入液化(压缩机与油分离器之间无阀门)。
I4v!
K9{$D8N!
c*|3L9|4x$|5、吸气压力逐渐降低,贮氟液器液位逐渐升高。
"z#n0Q/J;{原因分析:
液化机组在运行时,出现这种情况,类似于正常停机时,把液化器里的氟收回贮液器,供液阀处于关闭状态。
因此,怀疑供液电磁阀的滤网出现堵塞,氟里昂才不能正常循环。
8Z,o.e9i3~4N处理办法:
根据以上分析,在不停机的情况下,多次敲打电磁阀滤网部位或反复全开、全闭此阀几次,并对此阀用蒸汽加热处理均无效。
于是决定拆出此阀,其步骤:
0}8J0f2u a.m+s7`
(1)关闭氟贮液器的供液阀,在加氟阀处用抽氟机抽供液阀至节流阀之间的氟至氟贮液器(冷凝器的冷却水保持循环),至绝压为5.33KPa;
4j%K8t$^8W)o&c
(2)此时可卸此阀。
拆开时发现电磁阀前的滤网结冰,经清洗、吹干、复位安装,为了吸收残留水分,在干燥器内放0.5-1kg变色硅胶(用纱布包装,硅胶干燥后呈深蓝色,吸水后呈粉红色)。
(3)再用抽氟机抽系统真空后,重新开机,贮液器内R22逐渐进入液化器。
预防措施:
(1)严格控制氟里昂的质量,不应有水和空气、杂质等异物(氟里昂的含水量一般控制在30ppm以下)。
若制冷剂氟里昂中含水超过规定值,不仅能腐蚀金属,而且使润滑油部分乳化。
这次出现冰堵,恰好是该机组加氟里昂后的第二天下午。
因此,这次出现冰堵很有可能是R22中含水超标。
(2)严格控制冷冻机油的质量
一般规定,每公斤油含水量不超过20~40mg,否则,若油中含有水分和杂质,同样在制冷系统中出现冰堵或脏堵。
(3)注意加强对冷冻机油的密封管理,防止油接触水分空气,否则油会乳化变质。
'O,?
#?
;w-A"?
(4)避免干燥剂在干燥器中时间久了出现破碎的小粒进入制冷系统,再次出现堵塞(因电磁阀前滤网很小),因此在下次停机时,取出干燥剂,剔去被击碎的小颗粒。
+{(J'?
#F$?
9c"\#I'z5U6、氯气系统压力突然升高
#d'n"f6o3N:
?
B氯气系统压力是界定在液化区域内,氯气进口压力、液化器的尾气压力,气液分离器的尾气压力,氯气尾气分配台的压力。
*z0O1X&R;b;o原因分析:
由于吸气压力(液化器的蒸发压力)、油温、排气压力、液化器的液位等到工艺参数均未发生变化,在很短的时间内(约1-2分钟)进液化器氯气管内压力升高约0.025MPa,只能怀疑上工序(氯处理工序)有问题,经氯处理工序检查发现其氯气分配台的压力也比正常时约高0.03MPa,其它条件没有发生变化,当时,备用氯压机正在拆卸,于是怀疑氯气进口阀关不严,而两台氯压机氯气进口并联在一根管上,此时空气通过运行的氯压机被抽进系统所造成。
处理办法:
(1)用盲板密封备用泵氯气进口。
(2)从尾气分配处,打开去废气处理的阀门泄压,同时关闭在正常情况下去合成盐酸的阀门。
经过以上处理,几分钟后,氯系统趋于正常。
'?
%T!
B.i#l8Z%Y+_6r预防措施:
(1)拆备用氯压机检修时,及时封堵氯气进口阀,避免空气进入氯系统。
7?
(~ g9~)m3P6v9h
(2)氯压机进口段负压区阀门保持不漏(以免吸进空气)。
0k2` b;]&Y0@$h#H7、液化器入口氯气压力逐渐升高,氯尾气压力基本不变。
原因分析:
一般情况下,进液化器的压力为0.08MPa左右,液化尾氯气压力在0.05~0.06MPa,经过一个月时间,氯气进液化器的压力由0.08MPa逐渐上升到0.16MPa左右,而液化尾气压力基本不变,诸如吸排气压力、油温、油压、液化温度等工艺参数基本上在规定的范围内变化。
经过反复思考认为,氯气在液化器的列管内流动存在着较大的阻力,流速减慢。
阻力从何而来?
而每天氯处理工序来氯气的纯度,均在98%以上。
但酸捕集器的滤芯曾经常出现过穿孔和盐泥堵塞,从开车以来,每月至少更换一次滤芯。
由此,可推论,由氯气带来的盐,日积月累(2003年4月至2004年1月)沉积在液化器列管内。
处理办法:
根据以上分析,拆开液化器的两端封头,发现液化器内每根列管上富集了白色的盐,因此,采用喷嘴头喷射水冲洗,再用干燥气吹干,盖好两端封头,机组开车,这种现象消除了。
预防措施:
电解的湿氯气先经过氯气洗涤塔处理后再到氯处理工序,并解决好酸捕集器的滤芯,从而避免氯处理后的氯气流入液化器里不带盐或盐量很少。
8、油温升高引起停机,发出报警信号。
4k%`)T&P5x9N(V8K0I机组停车经过:
当班操作者在巡检时,观察油温为40℃,想把温度调到最佳温度范围45~55℃,于是调节油冷却器的进水阀(关小)大约经过10分钟,操作者到螺杆机处发现机组停了,电气控制箱显示油温超高报警。
原因分析:
机组设置了油温超过65℃时,温度控制器动作,停止机组运行。
其原因在于操作者一是没有把握好阀门调节的开度大小。
二是没有想到调整工艺操作会引起其它工艺参数变化(尤其是油温的变化)。
e&[2E.D2H'Y:
Z.f n;t处理办法:
发生油温超高故障停机后,可先按下报警解除按钮,停止电铃报警,此时故障指示灯仍亮,再按复位按钮。
这时,根据油温情况,调整冷却水量,启动压缩机,启动油泵,减载运行,把能量降至零后,按正常开车顺序重新开机。
预防措施:
一是在其它参数在正常范围内只要油温在40℃,一般情况下,不要调小冷却器进水量;二是调整阀门要缓慢,注意把握阀门开度大小调节的经验;三是调整工况时最好不离开现场,注意观察相关参数的变化,以便及时作出适当调整。
)E1X)I&d(i:
D1Z8n9、液化温度升高(最高的一次为-15.8℃)
原因分析:
引起液化温度升高是制冷剂与气氯热交换效果差,即表现为制冷剂的制冷能力不足的原因。
'T+h:
J"c%[(H3e$P,]*W0u
(1)在热负荷不变的情况下,液化器里的制冷剂不够,造成制冷量不足。
2@5~#z&J7w(O-m"~5n
(2)制冷剂中有较多的空气,使冷凝压力升高,排气温度升高制冷剂不能变成过冷液体,减少制冷能力;
1h(v*J3S e(a(3)机组所用的冷却水是循环水,在夏天,冷却水温度高(特别是冷却塔风机的电机出现故障风机不转动时)或循环冷却水量不足,引起油温高和排气温度高,导致制冷量不足。
(4)在系统制冷剂够的情况下,节流阀(或膨胀阀)的开度过小。
5q#v"C9A#u4}4D(C)V$q(5)电磁阀的滤网出现冰堵或脏堵,致使制冷剂逐渐减少。
&U/d T%h"Z*F+l(6)当吸气带液、油温低于30℃、加油过多、热负荷减少、机组开车增载过快等原因影响油与R22分离效果,使大量油进入氟冷凝器和液化器,至使液化器换热效果差。
8}._6r*x'M处理办法:
针对以上原因处理办法如下:
(1)在制冷系统的加氟阀处,补充氟里昂;
(2)停机后在制冷设备的最高点放空处用抽氟机抽空至绝对压力为5.33MPa(40mmHg)左右(油分离器、冷凝器);
(3)及时修理或更换电机,若有可能补充冷却水量或添加直流水;
(4)适当加大节流阀的开度;
B4z+h.u#v&h5R1I,}+N(5)停车经抽空处后,拆除滤网进行清洗,吹干;
"W2X'K5`(X(6)从液化器上放油阀处缓慢开启阀门,利用液化器内的R22气体吹出液化器内的润滑油至油馏器内或停车时之前,关闭供液阀逐渐把液化器内的R22用抽氟机抽至贮氟器内,然后,从液化器底部排净阀处放油,并用干燥的空气或氮气(在压力表处接头)吹扫液化器。
预防措施:
针对以上情况,相应的预防措施如下:
(1)根据贮氟器和液化器的液位计液位减少时,作适当的补充R22;
(2)在设备管道阀门检修完毕,进行抽空处理后再开车,另外在加氟、加油时,先排净其管内的空气,最后在加油后在油分离器的放空阀处抽空至绝压5.33KPa(40mmHg)再开机;
)} o-d"e%q"q(}:
b(3)提高电机的绝缘能力,计划检查、检修冷却塔设备、预留添加直流水的接头,一旦水量不够或温度高,及时补充。
6?
~-]7R$W-a"e!
j(4)加强巡回检查频次,把各工艺参数控制在规定范围内,适当调整相应阀门的开度。
-I-{#d,o3M"s8{+K%n(5)定期在干燥处放变色的硅胶干燥剂(用两层纱布包好)并定期检查干燥剂(变色或破碎后及时更换);并严格控制冷冻机油和氟里昂含水分不超标。
(6)一是油分离器里的油不能加过量(在规定范围内);二控制好油温,通过调节水温或水量,保证在35~65℃,最佳范围为45~55℃,从而保证油与R22的分离效果;三是开机时,增载不能过快,增载过快,吸气带液。
一般情况下,5分钟把能量增至100%,夏天,环境温度高,经过2~3次在2~3分钟把能量增至100%。
四是停车时,必须立即关吸气阀,以免排气高压进入低压系统时带走油分离器内的油(因油分离器与压缩机之间没有阀门);五是当环境温度低时(特别是夜班)进液化器的负荷(氯气)管道没有保温(相当于热负荷能量减少),液化氯气所需的冷量减少,适当调小节流阀的开度,避免吸气带液。
2R7t6o8D%k+a3v10、液化机组漏氟里昂
:
|7u+b6j9W"Y#\氯气液化机组漏R22不存在大漏,平时在系统运行时,用肥皂水检查各个密封点,每次检查的漏点主要是螺纹连接处,漏量较大的是吸气阀和液化器上R22出口截止阀的填料部位,每次一套系统漏点只有2-3个,由于生产任务紧,不能停几天来检查,一年来,两套系统损失R22近两万元。
为了减少漏氟损失,只有系统停车,整个系统做气密性试验,气密性试验的介质最好是氮气,可以不考虑由温差引起压力变化,其次是干燥空气,千万不能用氧气介质来做试验,这是因为用氧气作试验完毕,在排放时,与机组内残余油(出厂前机组试过车),因气流摩擦,发生爆炸事故(八十年代原武汉冷冻机厂在山东某企业调试时,出现了机毁人亡的爆炸事故)。
;K7h2w$w!
O7o氯气液化机组做气密性试验是操作调试的重点,也是难点,做气密性试验时,要考虑由于环境温度的变化引起的误差(压缩干燥空气)。
还要注意一点,整个系统在做气密试验时,在24小时压力稳不住始终往下降,而又检查不出漏点。
在这种情况下,就要重点检查液化器、冷凝器、油冷器内,管板与筒体间的焊缝以及管板与列管间的焊缝是否漏(打开容器两个封头)。
11、压缩机内滑阀托瓦脱离排气端座(出现两次)。
该机组的故障记录(从2003年4月开车至2005年10月):
2003.6.9出现机组振动(紧固了机组地脚螺栓);
*L,O;@-X:
F2003.7.25波纹管式机封漏油10滴/分(更换了O形圈);
2003.11.20出现大的异常声(更换了金属挠时叠片2组);
6{.d7`8}2D2004.3.26供液电磁阀前滤网出现冰堵(停机处理);
2004.10.10电机轴承噪音大(联轴器一侧,更换);
0z6i7M4n4n5u&M1z/N-P2004.11.1更换联轴器出现大的异响(更换了金属挠性叠片);
/j8Q"V5Q'i*q.Q2005.1.10停车减载能量显示30%;
5B8x3C!
k;C*P#g$k;i2005.3.3由于交流接触器故障引起压缩机无法启动(更换);
2005.4.7停车时不能减载(拆机检查托瓦掉了,恢复);
2005.8.17~24机头间断出现不明显的异常声(误认为是机内气流声);
2005.8.25机头发出异响,伴有振动(拆机检查托瓦掉)。
原因分析:
造成滑阀托瓦脱落原因,一是压缩机长期的轻微振动,引起托瓦与排气端座之间的两个定位销松动,以及连接的四颗螺栓抖松;
二是柱销与瓦配合以及螺栓与机座内螺纹的配合尺寸偏小。
#m6r*L8V$Q1s.^0^6^8o)k0[!
]0x三是这四颗螺栓出厂装配时没有拧紧。
2A-f1w"p7H*p压缩机的振动从何而来?
根据机组正常运行时,用手摸机头,存在轻微的振动。
我们从其故障记录得知:
机组地脚螺栓、机封漏油或更换联轴器的金属挠性叠片可以推论,压缩机轴与电机轴的同心度可能存在偏差,从而导致机组的振动。
此外,如果压缩机的滑动轴承磨损,电机的滚动轴承磨损,不仅带来异常声,也会引起机头振动甚至机组振动。
拆机检查发现,第一次滑阀托瓦脱落(至2005.4.7机组总的运行时间为15598小时)的前兆是停车时减载操作无法进行,只好按紧急停车按钮,能量显示为100%。
由于启动机组时,能量显示应为0,不允许有负荷启动。
因此,要拆机检查,造成机组不能减载的可疑原因还有:
四通阀堵塞,油活塞的“O”形环磨损失去密封性以及吸气端座与吸气盖之间的垫片窜油。
处理办法:
(拆机检查,厂家派了一名技术工人)
7R*j4?
6B5N&F2m0W7D&o/v1、用氮气检查四通阀及油管,未见堵塞现象;
2、检查吸气端座与吸气盖之间垫片无窜油痕迹;
3、检查活塞的“O”形环磨损很轻微;
)w"m0Q(T%D;R4、发现托瓦脱离,两个定位销及四颗螺栓均掉了,更换园柱销和螺栓,并恢复了止退垫。
*t+~"~%[$t;O#w&p)P:
Y第二次出现滑阀托瓦脱落的前兆是压缩机内有异常声,伴有振动出现(2005.8.25晚20:
30左右;至此总的有效时间为19980小时),操作者经调度通知维修人员到现场,初步判断机内有异物,滑动轴承坏成为可疑原因。
停车第二天,拆机检查,滑动轴承磨损很小,再次出现了滑阀托瓦脱落,定位销剪断一颗,螺栓剪断两颗,阴转子出现三处轻微损伤。
金属挠性叠片变形分层并有2—3片断裂。
3p4Z/b)@;w&e"g'V其处理办法:
对压缩机进行解体,全面清洗检查,注意以下几点:
1、修复阴转子损伤部位;
2、更换相应的易损零件(O形图等);
3、各零部件在安装前后保证清洁度;
&A3}+x7D }4、各部件组装完毕检查其灵活性;
5、机体与转子配合轴承孔表面,不准有拉伤现象;
"m7Q.M%y+z*h0f.w.i/?
6、阴阳转子与排气端座贴合面间隙控制在0.08~0.12mm。
预防措施:
'L$J,m+O8R3m$L+T1、加强巡回检查、发现问题(特别是压缩机内有异常声,及时停车检查),及时处理;
2、定期检查校对机轴与压缩机轴的同轴度;
3、定期清洗油粗、精过滤器和吸气过滤器;
4、发现油变质(呈黑色),立即更换;
)L%~-D)r!
}$Q5、定期对电机轴承清洗加油(约5000小时左右),并定期更换(1.2万小时)
+],L)j0A!
p7Q2_$R4R结束语
.W-z8O4}:
g9?
4}-P&h0W氯气液化机组是一个密闭压力容器系统,制冷剂在系统中状态要变化,如果我们不去很好地研究掌握其变化规律(物质状态变化、能量变化、热负荷变化等),一旦出现故障,要查明原因,比较困难。
为了正确地判断故障,解决故障,必须以“正常运行标志为基础,用我们的眼、耳、手去观察、倾听、感觉各部分的运转情况,依据压力表、温度计、控制器测定的各种数据,以及故障显示进行综合分析,判断故障的原因所在,“对症下药”。
因此,只有熟悉机组设备结构原理、系统介质(R22、油、水)的流程及系统内制冷剂的状态变化,以及操作调试,就能很容易地掌握排出故障的技能;更能很好地指导操作,预防故障的发生;从而保证设备长周期、安全稳定地运行。
我们公司采用的是武冷的氟利昂螺杆制冷机组,最近,机组的能耗特别高并且液化量老上不去,请问一下可能的原因有哪些?
一个一个慢慢排查吧:
(1) 吸气过滤器阻塞
(2) 压缩机轴承磨损后间隙过大
9J$c8_'J$_2o)@,|1@'^(3) 冷却水量不足或水温过高
:
x8J$|!
p4z6y3N(4) 蒸发器配用过小
!
h-S1}8|.D1z(5) 蒸发器结霜过厚
(6) 膨胀阀开得过小
%N#U-G7^#u(7) 干燥过滤器阻塞
(8) 节流阀胀堵或冰堵
(9) 系统内有较多空气
(10) 制冷剂充灌量不足
(11) 蒸发器内有大量润滑油
(12) 电磁阀损坏
(13) 膨胀阀感温包内充灌剂泄漏
(14) 冷凝器或贮液器的出液阀开启过小
9N!
|9P3H#} z+f(15) 制冷剂泄漏过多
1o!
s-^1R/}3H#F(16) 能量调节指示不正确