设施规划实验讲解学习.docx
《设施规划实验讲解学习.docx》由会员分享,可在线阅读,更多相关《设施规划实验讲解学习.docx(22页珍藏版)》请在冰豆网上搜索。
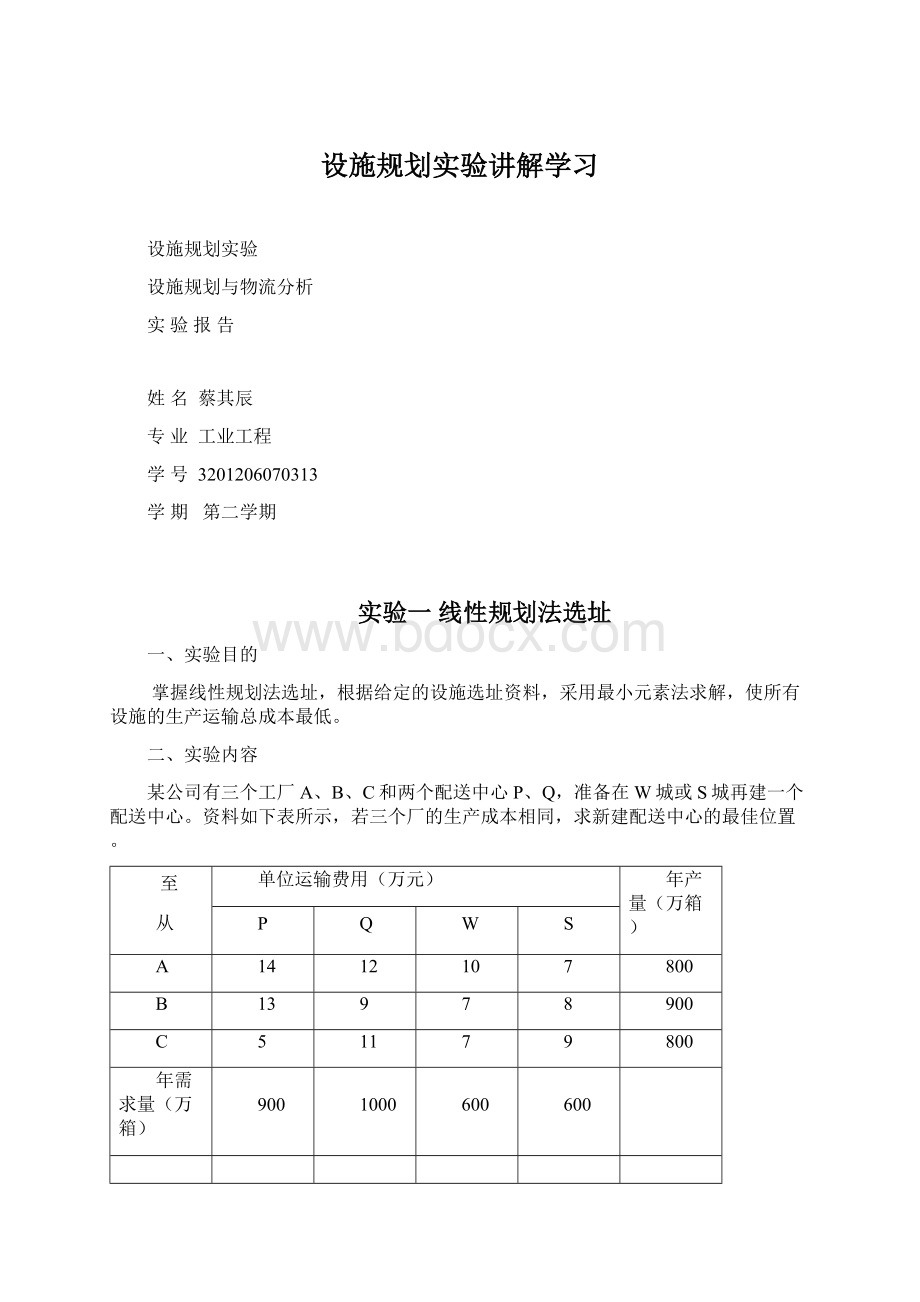
设施规划实验讲解学习
设施规划实验
设施规划与物流分析
实验报告
姓名蔡其辰
专业工业工程
学号3201206070313
学期第二学期
实验一线性规划法选址
一、实验目的
掌握线性规划法选址,根据给定的设施选址资料,采用最小元素法求解,使所有设施的生产运输总成本最低。
二、实验内容
某公司有三个工厂A、B、C和两个配送中心P、Q,准备在W城或S城再建一个配送中心。
资料如下表所示,若三个厂的生产成本相同,求新建配送中心的最佳位置。
至
从
单位运输费用(万元)
年产量(万箱)
P
Q
W
S
A
14
12
10
7
800
B
13
9
7
8
900
C
5
11
7
9
800
年需求量(万箱)
900
1000
600
600
三、实验步骤
1.将W城和S城的资料数据分解为两个表。
选址W城的单位运输费用(万元)
从至
P
Q
W
年产量(万箱)
A
B
C
年需求量(万箱)
选址S城的单位运输费用(万元)
从至
P
Q
S
年产量(万箱)
A
B
C
年需求量(万箱)
2.采用最小元素法,按照费用最少的点优先供应的原则来进行分配,在表中列出分配的顺序及数据。
从运价最小的格开始,在格内标上允许分配的最大数。
然后按运价从小到大顺序填数。
若某行(列)的产量(销量)已满足,则该行(列)的其他格不再分配。
如此进行下去,直至分配完成。
选址W城的运量分配(万箱)
从至
P
Q
W
年产量(万箱)
A
B
C
年需求量(万箱)
选址S城的运量分配(万箱)
从至
P
Q
S
年产量(万箱)
A
B
C
年需求量(万箱)
3.分别计算出选址W城和S城的运输成本,选择成本低的作为新建配送中心的位置。
选址W城的运输成本:
选址S城的运输成本:
选址结果:
实验二布置设计
一、实验目的
1.掌握物流分析的基本方法,掌握系统布置设计的基本方法与步骤。
2.掌握用ExstrategyFIE布局与物流规划软件进行建模仿真分析的方法。
二、实验内容
3
1
8
9
7
4
5
2
6
1.根据如下相关表将9个作业单位布置在3×3的网格中,其中5号作业单位在左下角。
2.已知某企业各部门的物流相关表、非物流相关表以及各部门所需面积,物流与非物流相互关系相对重要性的比值m:
n=2:
1,试建立综合相关表,并将5个部门布置在30mx30m的正方形内。
部门1
部门2
部门3
部门4
部门5
面积(m2)
100
300
300
100
100
物流相关表非物流相关表
3.某车间生产五种零件,各零件的工艺路线和日产量如下表所示。
A为入口,H为出口,B、C、D、E、F、G为生产设备。
要求作出物流量从至表,划分物流强度等级,作出物流相关表,画出位置相关图。
零件
工艺路线
日产量(托盘)
1
A→B→C→E→D→G→H
2
2
A→C→E→D→B→H
20
3
A→F→G→C→B→D→E→H
5
4
A→G→B→D→E→H
30
5
A→D→B→E→H
10
三、实验步骤
实验1:
(1)根据相关表作出关系工作表,每行列出一个作业单位,AEIOUX各成一列,将与之形成AEIOUX各级关系的其他单位分列在各列之中。
A
E
I
O
U
X
作业单位1
3、7、8
4、9
5
2、6
作业单位2
5、6
9
4
8
1、3
作业单位3
1、9
7
5
2、4、6、8
作业单位4
6、7
1、8
2
3、5、9
作业单位5
2、7、9
3、1
4、6、8
作业单位6
4、2
7
8
6、3、1、9
作业单位7
1、2、4、5、8、9
3、6
作业单位8
1、7
4
2、6
3、5、9
作业单位9
5、7、3
1、2
8、6、4
(2)找出关系最重要的,即A最多的,若A级数量相同,再比较E的,将该作业单位放于中央位置。
(3)根据其他作业单位与该作业单位的相互关系进行布置,主要考虑A、E、X级关系。
布置规则:
A级关系要边靠边放,E级关系至少角靠角,X级关系不能边靠边也不能角靠角。
(4)接着考虑新布置的作业单位,按照同样方法继续布置,直到完成。
(5)按照以上原则可得到多种布置方案。
对这些方案可按以下方法评分:
如果A级的既未边靠边也未角靠角,罚2分;X级的边靠边也罚2分;A级的只角靠角,罚1分;X级角靠角,E级未角靠角也罚1分。
(6)选择罚分最少的布置方案。
3
1
8
9
7
4
5
2
6
罚分:
-1、-1、2
原因:
5和7A级罚一分
7和8A级罚一分
实验2:
(1)计算综合相互关系
物流关系(权值:
2)
非物流关系(权值:
1)
综合关系
部门
等级
分值
等级
分值
分值
等级
1-2
I
2
A
4
8
E
1-3
U
0
U
0
0
U
1-4
A
4
A
4
12
A
1-5
O
1
O
1
3
U
2-3
E
3
O
1
7
I
2-4
I
2
I
2
6
I
2-5
U
0
U
0
0
U
3-4
E
3
E
3
9
E
3-5
E
3
U
0
6
I
4-5
I
2
U
0
4
0
(2)作综合相关表
(3)计算综合接近程度
部门
1
2
3
4
5
分值
8
7
7
10
4
(4)画出布置图
2
1
3
2
4
3
2
5
3
实验3:
(1)作物流量从至表
从至
A
F
G
C
B
D
E
H
A
5
30
20
2
10
F
5
5
G
30
5
5
30
2
2
C
20
5
7
22
B
2
30
7
65
10
20
D
10
2
65
57
50
E
22
10
57
45
H
2
20
45
(2)划分物流强度等级
单位-单位
物流量
等级
单位-单位
物流量
等级
A-F
10
U
G-H
4
U
A-G
60
E
C-B
14
O
A-C
40
I
C-E
44
I
A-B
4
U
B-D
130
A
A-D
20
O
B-E
20
O
F-G
10
U
B-H
40
I
G-C
10
U
D-E
114
A
G-B
60
E
E-H
90
E
G-D
4
U
(3)作物流相关表
(4)计算综合接近程度
单位
A
F
G
C
B
D
E
H
分值
1
0
2
0
5
7
5
2
(5)画出位置相关图
(6)根据位置相关图,结合给定的车间面积,利用ExStrateFIE布局物流规划软件建立不知模型,进行仿真分析,确定车间布置方案.
实验二步骤设计
一实验目的
掌握用ExStrategyFIE布局与物流规划软件对设施布置进行建模仿真的方法。
二、实验内容
某车间生产五种零件,各零件的工艺路线和日产量如下表所示。
A为入口,H为出口,B、C、D、E、F、G为生产设备。
要求利用ExStrategyFIE布局与物流规划软件根据下图建立车间布置模型,进行仿真分析,调整各生产设备的位置,尽量降低物流成本,确定优化方案。
零件
工艺路线
日产量(托盘)
1
A→B→C→E→D→G→H
2
2
A→C→E→D→B→H
20
3
A→F→G→C→B→D→E→H
5
4
A→G→B→D→E→H
30
5
A→D→B→E→H
10
三、实验步骤
1.打开软件ExStrategyFIE布局与物流规划软件,新建项目3201206070313蔡其辰。
2.打开文件选项,选中项目属性,对项目属性进行设置,如下图
3.设置车间围墙及设备。
如下图
图3
4.对项目入口、出口、和设施分别进行设置,并分别命名A、B、C、D、E、F设备。
如下图。
5.设置零件1的加工流程.选中
,根据原题中所给加工条件,在下面添加七个结点,并对每一个结点的性质进行设置,如下图所示零件1加工过程.
6.用鼠标点击
选中一个结点后不放鼠标,直至托至下一个链接结点,然后在选中另外一个结点继续链接,就这样一次进行完。
如下图完成后的零件5加工流程。
7.双击两个结点之间的连线,然后按要求选中起点和结束点。
一次进行对所有的结点之间的连线进行设置,操作如下图
8.将所有零件按照工艺路线设置好,确定无误后输入路线,得到如之后所示完整的设施规划初步示意图。
9.设置完成以后,调整各设施位置,对其总运输成本进行优化及调整,如下图所示。
10.选择总运输成本最小的设备规划安排作为最优安排,最优安排根据粗略计算总运输成本不会高于1600。
实验四自动化立体仓库作业
一、实验目的
了解自动化立体仓库的入库、移库、出库作业和电子标签货架系统;根据产品生产线规划设计AGV小车的运行轨迹。
二、实验内容
结合减速器装配生产线进行入库、移库、出库作业和电子标签辅助拣选,规划设计AGV小车的运行轨迹,用其为装配线各工作站运送零件,完成减速器的装配。
三、实验步骤
说明:
先画出立体仓库布置图,然后详细写出具体的实验步骤(以下只是简要步骤,给大家做个提示而已,你就这么写来交给我是没分的哈)。
1.将减速器底座入库到立体仓库托盘货架。
2.将其余零件入库到电子标签货架。
3.规划AGV小车领取零件运送至各工作站的运行轨迹。
4.运行AGV小车至电子标签货架,并进行零件出库作业。
5.用AGV小车将零件运送至各工作站。
6.制定生产计划,启动流水线,进行减速器装配作业。
7.对减速器成品进行移库作业。
8.将减速器成品出库。
四、实验过程:
了解立体仓库的布置:
(如下图所示)
1、首先用AGV小车把减速器的底座运输至(如图中23)处,在FLE软件中,输入入库指令。
首先输入减速器零件入库口令:
1)、创建物料
分别设置——物料编码(001,002,003,004)、物料名称(减速器)、所属仓位(1~18仓位中任意4个)——确定创建物料。
2)、设置物料管理
物料入库:
、
按照下表设置
物料编码选择
物料名称设置
001
JSQ1
002
JSQ2
003
JSQ3
004
JSQ4
之后分别选择所属仓位,入库量后,分别确定入库。
物料出库:
选择物料编码→确定物料名称→确定所属仓位→选择出库量→确定出库。
3)、AGV小车路线:
选择连接AGV小车——初始位置——设置路线11→12→13→14→15→16→17→18→19→20→21→22→23→24→25
增加停靠站18号,选择停靠模式采用手动离站添加20~25号执行路线表。
选择执行
4)、具体操作:
(1)新建入库申请,输入入库货物条码和数量,点击“添加入库请求按钮”
(2)选择入库仓位,点击“指定仓位”按钮确定。
如下图
入库单作业
(3)所有入库请求添加完毕,点击“生成入库单”按钮。
生成入库单。
生成入库单示图
(5)选择“新建入库单”清空所有入库申请,然后在下拉列表中选择入库货物的条码,在点击“添加入库请求”按钮。
,执行入库作业。
(6)如果想删除某条入库申请,则输入货物条码,并选择“删除入库请求”。
所有入库申请建立后,点击“生成入库单”,保存在选定电脑储存路径下。
如果要导入一份旧有的入库单,则选择“导入入库单”(选择前可先更新,选择“刷新入库单”)。
2、拆解减速器,分别放于四个托盘中,区分减速器大轴,小轴,螺纹,端盖四部分,将零部件分别由仓库中调配放入电子标签货架上,然后在主控台上输入指令:
设置需要运用的货架001,002,003,004,再依次调用零件运输。
3、规划AGV小车领取零件运送至各对应工作站的运行轨迹:
(1)电子货架001的托盘运送至20号位所在的操作台上;
(2)电子货架002的托盘运送至21号位所在的操作台上;
(3)电子货架003的托盘运送至22号位所在的操作台上;
(4)电子货架004的托盘运送至23号位所在的操作台上;
4、运行AGV小车至电子标签货架,并进行零件出库作业:
(1)仓储中心→库存管理→库位明细查询→点击(占料库位)找‘减速器’打头的是电子标签库房查看库存数量(库存数量大于10可以进行货物拣选操作,小于10应进行补货操作) →退出
(2)按照出库方式操作:
客户(订单合同—订单录入—订单发送—制造商—委托商—委托单确认—物流中心—委托单确认—仓储中心—出库校验)—确认—摘取式分炼出库—点击启动(等待连接成功)—刷新。
5、用AGV小车将零件运送至各个工作站:
(1)AGV小车把电子货架001的托盘里的零件运送至(如图20)所在的操作台上;
(2)AGV小车把电子货架002的托盘里的零件运送至(如图21)所在的操作台上;
(3)AGV小车把电子货架003的托盘里的零件运送至(如图22)所在的操作台上;
(4)AGV小车把电子货架004的托盘里的零件运送至(如图23)所在的操作台上;
6、制作生产计划,启动流水线,进行减速器装配作业:
操作方法:
依次选择制定生产计划→计划管理→增加计划→计划生产日期→完成生产日期→选择交货日期→选择成品→选择路线组→完成。
新建计划:
选择作业调度——工单管理点击查询计划(增加)输入计划编号选择生成工单,然后进行工单执行,选择控制系统——生成计划——生产作业点击启动工位脚踏开关控制
启动作业:
选择的工位脚踏开关控制点分别为:
流简线02——工位01处脚踏;
流简线02——工位02处脚踏;
流简线02——工位03处脚踏;
倍速线01——工位01处脚踏。
7、对减速器成品进行移库作业:
操作方法:
选择移库管理:
输入原仓库名称,点击查询,选择目标仓位名称,开始查询目标输入移库计划并配置移库作业选择更新,点击确定移库。
8、将减速器成品出库:
操作方法:
选择出库管理:
输入出库类型(成品),选择成品,点击查询(库位)(选择目标受体、选择详细目标受体)。
点击加入数据,确定出库。
选择出库单号,进行校验信息出库单号,进行确认,选择其他作业——打印出库清单,点击确认(启动堆垛机开始出库),选择退出。
自动立体仓库开始工作(电子看板显示堆垛机出入库信息)如果是散出件,出库后还需在出货口处按回库按钮,货物会自动回到原来的仓位。
学生学习心得
在本次试验中,我们完成了立体仓库自动化的入库、出库、移动、调节等环节。
在整个实际操纵环节中,我们发现,虽然较之人工操作极大地提高了便利程度与工作效率,但是任然存在着诸如:
操作系统仓储情况反映不实际;出仓实验中出现未按照正确出仓口出仓等问题。
虽然其中有部分问题是由于操作人员失误或者多余操作,经验不足等问题造成的,但是也有诸如受到扫描器位置影响无法正常出仓等情况发生,并且,全自动化的工厂带来的后果是相较人工操作,其容错性太低,且员工与机器所受压力都极大,日常维护等相较繁重。
个人认为:
在完善系统,加强平日调试与维护外,员工的培训,以及重要工段部分采用人工机器合作模式也是不可避免的。
虽然相较纯人工会有部分效率的流失,但是也是在相较全自动环境下的低容错率的比较平衡经济的方式。
学生(签名):
年月日
诚信承诺
本人郑重声明所呈交的课程报告是本人在指导教师指导下进行的研究工作及取得的研究成果。
据我所知,除了文中特别加以标注的地方外,论文中不包含其他人已经发表或撰写过的研究成果。
与我一同工作的同学对本文研究所做的贡献均已在报告中作了明确的说明并表示谢意。
学生(签名):
任课
教师
评语
成绩评定:
任课教师(签名):
年月日