200KA预焙槽控制效应系数实践.docx
《200KA预焙槽控制效应系数实践.docx》由会员分享,可在线阅读,更多相关《200KA预焙槽控制效应系数实践.docx(20页珍藏版)》请在冰豆网上搜索。
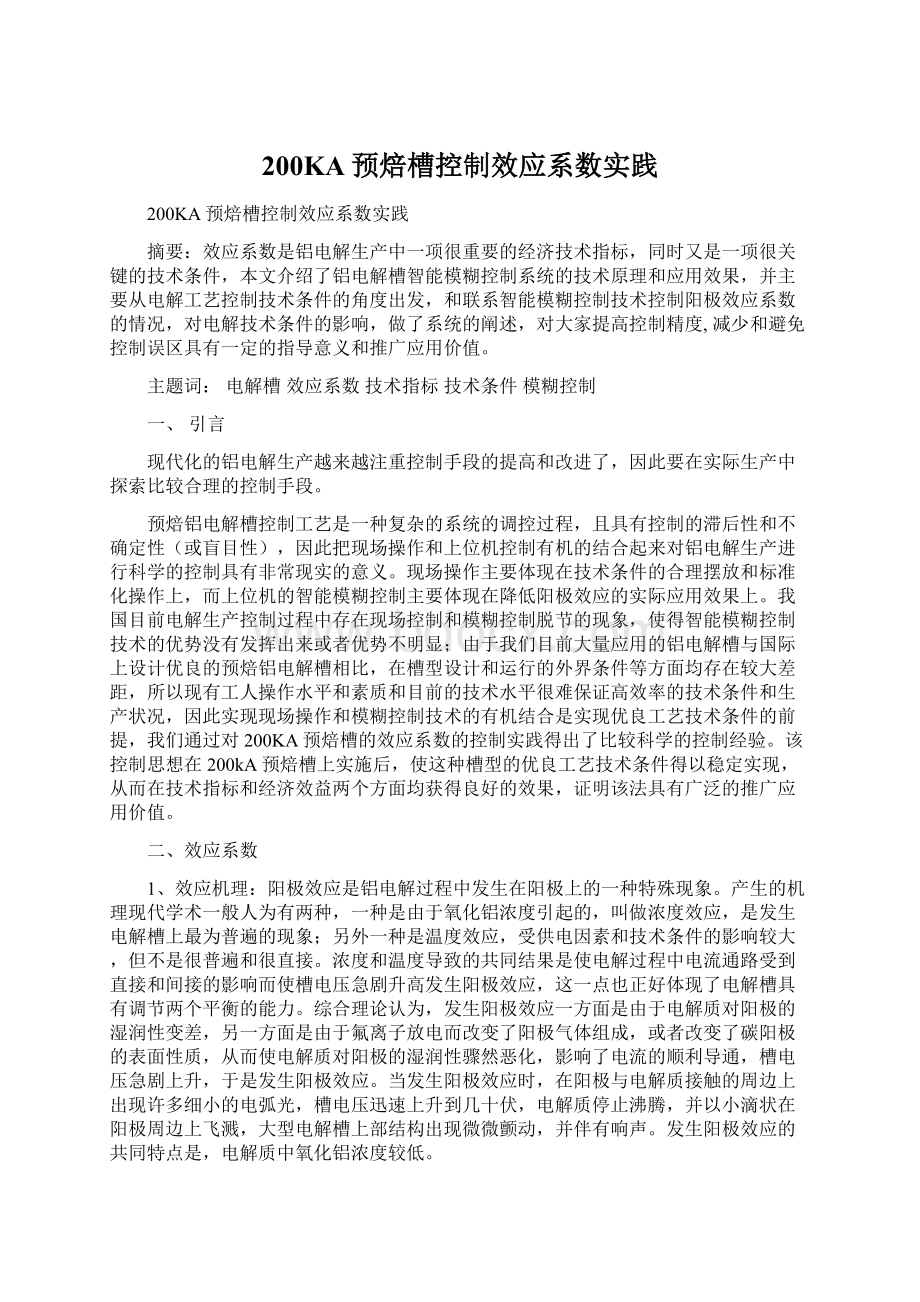
200KA预焙槽控制效应系数实践
200KA预焙槽控制效应系数实践
摘要:
效应系数是铝电解生产中一项很重要的经济技术指标,同时又是一项很关键的技术条件,本文介绍了铝电解槽智能模糊控制系统的技术原理和应用效果,并主要从电解工艺控制技术条件的角度出发,和联系智能模糊控制技术控制阳极效应系数的情况,对电解技术条件的影响,做了系统的阐述,对大家提高控制精度,减少和避免控制误区具有一定的指导意义和推广应用价值。
主题词:
电解槽效应系数技术指标技术条件模糊控制
一、引言
现代化的铝电解生产越来越注重控制手段的提高和改进了,因此要在实际生产中探索比较合理的控制手段。
预焙铝电解槽控制工艺是一种复杂的系统的调控过程,且具有控制的滞后性和不确定性(或盲目性),因此把现场操作和上位机控制有机的结合起来对铝电解生产进行科学的控制具有非常现实的意义。
现场操作主要体现在技术条件的合理摆放和标准化操作上,而上位机的智能模糊控制主要体现在降低阳极效应的实际应用效果上。
我国目前电解生产控制过程中存在现场控制和模糊控制脱节的现象,使得智能模糊控制技术的优势没有发挥出来或者优势不明显;由于我们目前大量应用的铝电解槽与国际上设计优良的预焙铝电解槽相比,在槽型设计和运行的外界条件等方面均存在较大差距,所以现有工人操作水平和素质和目前的技术水平很难保证高效率的技术条件和生产状况,因此实现现场操作和模糊控制技术的有机结合是实现优良工艺技术条件的前提,我们通过对200KA预焙槽的效应系数的控制实践得出了比较科学的控制经验。
该控制思想在200kA预焙槽上实施后,使这种槽型的优良工艺技术条件得以稳定实现,从而在技术指标和经济效益两个方面均获得良好的效果,证明该法具有广泛的推广应用价值。
二、效应系数
1、效应机理:
阳极效应是铝电解过程中发生在阳极上的一种特殊现象。
产生的机理现代学术一般人为有两种,一种是由于氧化铝浓度引起的,叫做浓度效应,是发生电解槽上最为普遍的现象;另外一种是温度效应,受供电因素和技术条件的影响较大,但不是很普遍和很直接。
浓度和温度导致的共同结果是使电解过程中电流通路受到直接和间接的影响而使槽电压急剧升高发生阳极效应,这一点也正好体现了电解槽具有调节两个平衡的能力。
综合理论认为,发生阳极效应一方面是由于电解质对阳极的湿润性变差,另一方面是由于氟离子放电而改变了阳极气体组成,或者改变了碳阳极的表面性质,从而使电解质对阳极的湿润性骤然恶化,影响了电流的顺利导通,槽电压急剧上升,于是发生阳极效应。
当发生阳极效应时,在阳极与电解质接触的周边上出现许多细小的电弧光,槽电压迅速上升到几十伏,电解质停止沸腾,并以小滴状在阳极周边上飞溅,大型电解槽上部结构出现微微颤动,并伴有响声。
发生阳极效应的共同特点是,电解质中氧化铝浓度较低。
2、阳极效应对生产的影响及当前阳极效应系数
阳极效应对铝电解生产过程的稳定性破坏很大。
当电解槽发生阳极效应后,电解质温度从正常生产的920℃~940℃上升到950℃~970℃,短时间内热能急剧增加,破坏了热平衡状态,导致炉帮熔化而减薄,槽温和炉帮将近一小时后才能恢复正常。
阳极效应系数太高,不仅易破坏侧部炉帮,恶化生产,影响电流效率,而且使电耗大幅度增加,不利于电解槽稳定生产。
我分厂目前阳极效应系数为0.3~0.35次/槽·日,阳极效应持续时间为5~8分钟。
3、控制目的和目标
通过氧化铝浓度控制,调整和改善电解液对阳极的湿润性,从而降低阳极效应系数。
由此可以优化和合理保持各项技术条件,稳定生产,保护炉膛,降低电耗,提高电流效率。
电解槽阳极效应系数主要与阳极炭块、槽温、电流稳定情况、氧化铝特性及氧化铝浓度有着密切的关系。
对于我们电解厂来说,阳极炭块质量和氧化铝特性无法直接控制,唯有氧化铝浓度可以实现在线控制。
因此,我们利用智能模糊控制系统通过氧化铝浓度的控制,和合理摆放工艺技术条件优化操作将效应系数控制在0.1~0.3次/槽·日。
三、控制模型简介
该模型主要通过现场技术条件和操作的控制及智能模糊控制技术来保证控制的有效性和科学性,如图所示:
该模型要通过技术部门的协调和指挥统一进行,技术部门还要负责试验数据的测量、整理、统计,分析、总结试验结果。
各生产单位的专门负责人:
主要负责检查试验槽的技术条件和标准化作业情况。
四、控制实施步骤
(一)工艺技术条件控制模型及控制
(1)电解车间技术条件按标准要求保持如下:
a、槽温:
范围940-950℃,目标945。
b、两水平:
电解质水平20-22cm,铝水平18-20cm(铝水平的保持要根据具体技术条件及槽况而定)。
c、工作电压:
范围4.10-4.20v,目标4.18。
d、分子比:
范围2.3-2.5,目标2.4。
e、出铝量:
1480-1490kg。
f、加工间隔:
95-105s。
g、效应时间:
4-6分钟。
h、效应电压:
20-30v。
i、辅助条件:
阳极卡具压降平均达到15mv以下。
其它:
保温料添加保证厚度均匀,炉堂规整,炉底压降符合要求。
(2)技术科统计数据并组织对试验数据的整理,对过程中发生的技术条件的异常波动进行具体的研究和分析,及时采取正确的措施,指导现场操作和调整,以保证试验数据的科学性。
(二)、现场操作控制模糊模型
(1)、电解车间具体操作人员对本试验的目的和要求做到心中有数。
(2)、试验曹技术条件严格按照技术标准调整到合适范围,并保证槽况良好后,开始进行试验。
(3)、电解小组、大组、电解横班、车间在技术部门的统一指挥协调下积极配合计算机站完成本试验的操作要求及取得准确的试验数据。
具体要求如下:
a、按技术科要求一步一步进行,本试验方案执行前一周下发到各车间。
b、本试验周期定为三个月。
c、试验控制开始技术科对试验槽的技术条件进行重点跟踪检查和记录。
d、槽控机操作严格按有关技术标准和作业标准进行,严禁手动控料、私自关料阀或不按标准给信号,杜绝人为干扰对本试验控制的影响。
e、效应熄灭要按槽控机效应处理程序自动处理,严禁人工手动下料,杜绝长重效应。
表1:
《控制效应系数试验》数据统计表
时间:
年 月 日 时 分 记录人:
槽号
电压(v)
针振
(mv)
摆动
(mv)
加工间隔
(s)
两水平
(cm)
分子比
产量
(kg)
槽温
℃
换极
炉底压降(mv)
效应情况
备注
设定
工作
铝
质
任务量
吸出量
(三)、智能模糊控制模型
1、软件、实施步骤
(1)实施“柔性等待”机制。
(2)实施“效应智能预报”功能。
(3)调整参数。
2、硬件实施步骤
(1)对220V电源装置进行改造。
(2)对效应报警装置进行改进。
3、模糊控制
特殊作业要进行必要的物料补偿和能量补偿,能量补偿主要是抬高极距,而物料补偿主要是进行物料的平衡。
物料平衡的控制主要是指如何控制氧化铝浓度。
计算机控制任何对象必须具有如下条件。
a.基准:
必须给计算机设定一个控制参数的基准,在铝电解控制系统中同样也要设定两个基准:
(1)基准下料间隔;
(2)设定电压。
b.关系:
必须存在输入信息跟被控参数间的某种对应关系,对氧化铝浓度控制来说就是要找到电压V、电流I与浓度α之间的关系,这个对应关系就是所谓的“U”型曲线(图
所示)。
R平经过如下处理:
电阻R由电压V和电流I可以推出R=(V-V反)/I,经过一次滤波求出R滤,再经过二次滤波求出R平。
整个“U”型曲线分为四个区域
效应区;
低浓度区;
中浓度区;
高浓度区。
图
电解槽“U”型曲线图
在低浓度区有如下特征(图
A点):
浓度降低,R平上升;浓度增大,R平下降;在中等浓度区,浓度的变化对R平的影响不大,也就是说在中等浓度区R平变化不敏感;在高浓度区有如下特征(图
B点):
浓度降低,R平下降;浓度增大,R平上升。
控制系统在控制电解槽的氧化铝浓度时是采取“激励——反馈”机制来实现,所谓激励就是通过对电解槽下料采取欠量或过量方法来刺激电解槽,反馈就是电解槽R平的变化;而欠量或过量对应的是让电解槽的氧化铝浓度减小或增加。
图
电解槽氧化铝浓度控制示意图
a、在A、B、C、D四个阶段,由“U“型曲线各个区间的对应关系可以看出,在这个过程中,电解槽氧化铝处于高浓度区。
b、从D到E这个阶段,控制系统发现电解槽浓度偏高后,采取一种阶梯式的“拉升”,即不断增加欠量的程度来逐步将电解槽的浓度从高浓度区拉到低浓度区。
到达E点后R平与下料间隔的对应关系满足低浓度区的特征。
这种“阶梯式”的拉升比大幅度欠量或长时间欠量要好,可以减少电解槽化炉膛的机会。
而且这种台阶的变化内含一种“优先机制”,即对不敏感的电解槽台阶变化快,对敏感的电解槽台阶变化慢,这样进一步保证了敏感槽炉膛的稳定。
台阶的高度每次变化5%~10%,台阶的宽度是以30分钟为单位。
如果氧化铝浓度和R的关系走偏,则及时将浓度调整到低浓度范围,上述这种拉升机制保证了电解槽氧化铝浓度能长期处在低浓度区,以获得较高的电流效率。
经改进后,特殊作业时物料补偿为出铝后小过,换极和边加工后大欠,出铝后小过量为了抑制突发效应,而换极和边加工后大欠量考虑到停料对电解槽影响很大。
另外,现在出铝后改为自动降阳极,具体过程如图
所示。
出铝后自动降阳极的条件:
图
出铝、换极电压上升示意图
触摸了出铝按钮,准备出铝。
检测到连续5次爬升。
当前电压>(设定电压+200mv+出铝附加电压量),自动降阳极时每隔60秒降一次。
2、效应处理机制的改进
2.1效应处理改进及突发效应的控制
控制系统对效应的处理采用分阶段的方式来进行,如图
所示从上一次效应结束开始(A点),如果在指定的效应等待间隔内没来效应则进入效应第一次等待阶段,如果没有等来效应则进入第二次正常处理阶段,如果仍然没来效应就进入效应第二次等待阶段,如果仍不来效应就从头再来(即从E点转入A点)。
以前的控制方法是到达B点后立即无条件停料等效应,这种方法比较“死”,效应等来
图
效应处理示意图
的几率不高,等待时间也比较长,现在改成了所谓的“柔性等待”机制,即时间到达B点后要视电解槽的浓度而定,如果浓度比较低,电阻爬升的高度合适就立即停料;否则继续拉升直至满足条件再停料等效应,这种办法能有效的提高效应等待率,同时等待的时间也不长,对炉膛的破坏也小。
现在控制系统将电解槽氧化铝浓度控制的比较低,出现突发效应的可能性增大,为了有效的抑制突发效应应该从如下几个方面来处理。
、通过调整基准NB间隔来调整电解槽的浓度。
、检查下料系统是否有问题。
、注意温度效应,效应从原理上来说分为浓度效应和温度效应。
浓度效应是缺料造成的,而温度效应产生的原因比较复杂,一般跟槽况有关,则需要调整相关的工艺技术条件。
控制好系列电流,电流波动是引起突发效应的主要原因之一。
2.2、槽况的判断及处理
现在的控制程序中,只要阳极一动作下料控制就会从初始化开始,这样就干扰了下料的控制过程。
目前流行的一种看法认为,阳极的消耗跟铝液的增长是几乎相等的。
因此应尽量少的进行阳极升降,如果电压超出了电压上限,首先通过过量来压制电压,如果物料不能压
图
电解槽针摆处理示意图
回电压再考虑让计算机来自动调整电压,这种方法能减少压极距的机会,进一步提高电流效率。
控制系统通过针振、摆动这两个参数来判断槽况。
针振是频率波动信号,一般产生的原因是阳极附近局部故障造成的,比如阳极长包、阳极附近碳渣过多、阳极电流偏流等。
而摆动是低频率波动信号,一般产生的原因是整体炉膛不好造成的。
控制系统处理波动电解槽的办法只有附加电压,即把电压抬起来。
具体的处理过程如下(图
所示)。
这种分两步降的方法对抑制重复发生的针摆有一定的好处。
2.3效应智能预报
效应智能预报以槽电阻斜率和累积斜率为主要判据、物料平衡估算值以及电阻针振强度为辅助判据的阳极效应智能预报方法。
该方法首先获取用于阳极效应预报的信息,内容包括槽电阻采样、槽电阻低通滤波、槽电阻斜率与累积斜率计算、槽电阻针振强度计算以及物料平衡估算(即估算一定时间内累计加入电解槽内的氧化铝量与该时间内理论消耗量之差,简称物料累计偏差)。
然后,该方法利用上述信息进行阳极效应预报,基本做法是:
首先利用当前解析周期内的电阻斜率与累积斜率推理确定当前预报阳极效应的可信度有多大,然后依据近期槽电阻针振强度的变化趋势以及物料累计偏差的取值情况对可信度进行调整,最后依据可信度值对阳极效应预报的进程标志作出处理。
测试结果表明,该方法的阳极效应预报成功率高达90%以上。
众所周知,铝电解过程中阳极效应(以下记为AE)的发生是以槽电压骤然从正常值(4~4.5V)升高至30~50V甚至更高为主要特征。
因其导致电能额外消耗、电解质挥发损失增加、产生对大气层有极大破坏作用的氟化物气体、并干扰铝电解槽的正常运行过程,所以现代铝电解工艺希望尽可能地减少AE的发生,即降低AE系数。
因为一般情况下,导致AE发生的主要原因是氧化铝浓度过低,所以AE系数的控制与氧化铝浓度的控制是紧密相关的。
尤其是现代铝电解生产正普遍采用“低温、低分子比、低氧化铝浓度、低AE系数、高极距”这种既临近AE发生又追求低AE系数的工艺技术条件,所以AE预报显得十分重要。
跟踪槽电阻的变化是当今被普遍采用的AE预报方法,基本做法是:
对依据槽电压和系列电流的同步采样值所计算出的(表观)槽电阻序列进行滤波(或平滑)处理,并求其斜率(即变化速率),然后将滤波电阻值及其斜率(或累积斜率)值分别与限定值比较,作出判断。
这种传统方法对AE预报的成功率一般在60%~70%之间。
1.3槽电阻斜率和累积斜率计算
电阻斜率定义为最近2分钟内滤波电阻的平均变化速率(mV/min)。
电阻累积斜率定义为近期(最近约8分钟内)滤波电阻的累积增量。
1.4电阻针振强度计算
由于当有发生AE的趋势时,阳极底掌会逐步形成不稳定的气膜层,因此常会在AE发生前出现电阻的高频噪声(本文定义为电阻针振)明显增大的现象。
1.5物料累计偏差的计算
通常AE的发生是氧化铝浓度过低所至,因此基于物料平衡估算所计算出的近期(约2小时内)累计加入槽中的氧化铝量与该时间内理论消耗量之差(简称为物料累计偏差)这一信息对AE预报也有一定的价值。
2AE预报的算法
利用上述的信息进行AE预报推理的基本思路是:
首先利用当前解析周期内的电阻斜率和累积斜率推理确定,当前预报AE的可信度有多大;然后依据近期电阻针振强度的变化趋势以及物料累计偏差的取值情况对可信度进行调整;最后,根据可信度值对AE预报的进程标志作出处理。
2.1AE预报可信度的确定
为了便于利用电阻斜率和累积斜率来确定AE预报的可信度,先将两变量的取值均映射到区间[0,5]。
这种映射处理类似于模糊控制中的变量“模糊化”(或称“量化”)的处理。
以电阻斜率(S)为例,映射后的取值在0附近则表示电阻斜率很小,取值在5附近则代表电阻斜率很大。
同样方式处理累积斜率(T),得到映射后的取值记为T'。
然后按下式计算出一个具有[0,1]之间取值的数值,并将其视为可信度:
A=(S'+T')/10
2.2AE预报可信度的调整
同样,借鉴模糊控制中变量模糊化的思想,将物料累计偏差(W)、电阻针振强度(H)以及低通滤波电阻(Rw)均量化(模糊化)为具有5个档级值的模糊语言变量来描述,5个档级值定义为:
“负大”、“负小”、“零”、“正小”、“正大”。
然后,采用下列原则建立起一组用于可信度调整的推理规则:
(a)如果W为“负大”,则增大A值,反之如果W为“正大”,则缩小A值;
(b)如果近期H在增大,且当前为“正大”,则增大A值,反之如果近期H在减小,且当前为“负大”,则缩小A值;
(c)如果Rw为“正大”,则增大A值,反之如果Rw为“负大”,则缩小A值。
2.3AE预报的作出
以1分钟为预报周期,若当前周期内的可信度值大于设定值(如:
0.5),则认为当前有AE趋势,否则没有。
据此再对AE预报的进程标志进行处理,即作出AE预报“起始”、“维持”、“暂消失”、“重现”、“无”等结论。
4、效应参数的改进
在对效应分析报表数据及热平衡状态进行挖掘后,得到对效应受控率影响最大的因素,然后进行智能决策,具体决策过程如下:
1.如果效应发生时状态是主要影响因素,则应按如下规则进行决策:
a.如果正/过、欠/过居多,表明欠过量的程度不合理,应对控制系统的欠过量千分数进行调整。
b.如果欠/正、正/欠居多,表明欠量的程度过大,应对控制系统的欠量千分数、基准欠量周期及过量判定标准进行调整。
c.如果过/欠、过/正居多,表明过量的程度不够,应对控制系统的基准过量周期、过量千分数进行调整。
d.如果停/…、…/停居多,表明人工作业的影响太大,一方面应从管理上强化人工操作的工序,提高操作质量;另一方面,可以适当缩短控制系统在人工作业时自动停料的时间。
2.如果效应前8下料平衡态是主要影响因素,则应按如下规则进行决策:
a.如果欠量百分比是主要影响因素,应对控制系统的欠量千分数、基准欠量周期进行调整。
b.如果过量百分比是主要影响因素,应对控制系统的过量千分数、基准过量周期及系统下料器故障进行调整。
c.如果正常百分比是主要影响因素,应对控制系统的欠过量欠分数、基准欠过量周期作适当的调整。
3.如果效应周期内的统计时间值是主要影响因素,则应按如下规则进行决策:
a.如果停料时间是主要影响因素,应对人工操作过程进行强化管理,提高人工作业的质量和效率,同时可适当调整控制系统人工作业时的停料时间。
b.如果等效应时间是主要影响因素,应对控制系统整体欠过量基准进行适当调整,尽量使等效应时间缩短。
4.如果效应预报统计是主要影响因素,则应按如下规则进行决策:
a.如果效应预报次数是主要影响因素,应对控制系统的效应预报基准进行适当调整,尽量使保持在适当的水平。
b.如果效应预报距AE时间是主要影响因素,应对控制系统的效应预报基准及基准过2周期进行适当的调整。
5.如果热平衡状态是主要影响因素,则应按如下规则进行决策:
a.如果热平衡状态是热趋势,应根据专家诊断输出规则对设定电压、出铝量及氟盐添加量提出调整建议,同时应对控制系统的下料量进行调整,适当增加过量的比例。
b.如果热平衡状态是冷趋势,除根据专家诊断输出规则对设定电压、出铝量及氟盐添加量提出调整建议,同时应对控制系统的下料量进行调整,适当增加欠量的比例。
上述决策过程的调整是动态进行的,调整过程中可按类似专家决策系统的线性输出规则进行。
由于对系统的跟踪是比较实时的,因此应对调整范围进行严格限制,调整系数不要过大,以免控制系统走偏。
硬件步骤概要:
槽控机动力电源主要为电解槽的打壳、下料、阳极升降、效应灯、效应报警等提供电源,是电解槽正常运行的根本,2005年我们对槽控机动作板12V电源跳闸信号回路进行了改进,保证槽控机安全、可靠的运行,以保证对铝电解槽的正常模糊控制,解决生产中的实际问题。
一、槽控机动力电源供电简述
图1动力电源原线路
槽控机动力电源AC220V由AC380V电源通过降压隔离变压器(BY4)降压输出AC220V电压。
它在槽控机系统中主要控制的是:
1、主电源跳闸(U9-1TLP521-2)、2、保护电路中的三相电源缺相保护(A、B、C三相)、3、主未合、4、主粘连(U7TLPS21-2)、5、辅未合、6、辅粘连(U8-1、U8-2)、7、动力电源220v的通断(S1)。
AC220V电源一路接接触器的线圈、电磁阀的线包、效应继电器和效应灯;另一路接光偶U9-1(主要是给动作板提供AC220v电源通断的信号)。
如图1所示。
二、存在的问题
在实际工作中,动作板上的0.75A保险丝经常因发生故障而熔断。
在这种情况下槽控机没有任何故障提示,主控室监控机上也没有故障提示信息,维修人员、监控机操作者及现场人员都很难及时发现槽控机电源跳闸故障。
这样就会造成:
1)无法进行正常的打壳、下料。
2)无法进行正常的阳极升降调整。
3)无法及时报告效应及异常情况。
4)实际下料量与报表下料量不符。
5)无法正常切断AC220V动力电源信号。
现电解槽采用模糊控制,其效应采用临界控制,因而缺少一个正常加工过程,则会影响槽控机对电解槽的正常控制,破坏电解槽工艺技术条件,甚至会发生效应,如果处理不及时,会造成长效应,甚至造成红炉帮,更甚者会破坏工艺技术条件,从而发生病槽,因此,只有保证槽控机电源的正常运行,才能保证槽控机模糊系统的正常、可靠运行。
才能更好地保证电解槽的工艺技术条件。
图2改进后动力电源线路
三、改进方法
通过以上分析,经过认真的讨论,现将原电源跳闸信号控制中U9-1的电源直接由变压器输出控制其电源,由操作板上的接线端子T8中的第5根电源线输入,它控制U9-1、U7、U8-1、U8-2等光偶所提供给PSD211、GMS90C32的保护信号。
现将光偶U9-1的ACCOM共用输入线切断,切断其由变压器直接提供的电源,将光偶U9-1的AC公用线ACCOM改为保险丝FUSE的输出端。
通过改进后,如保险故障时U9-1没有输入电源而不工作,槽控机立刻显示电源跳闸信号。
这样就解决了动作板保险丝熔断后,槽控机面板无显示和上位机系统无法检测到跳闸信号。
便于维修人员、监控机操作者及现场工作人员能够及时发现故障,及时进行维修。
避免造成智能模糊控制系统无法打壳、下料、阳极升降,破坏了工艺技术条件,降低电流效率的情况。
四、改进后解决的问题及可实施性验证
经过改进后可以有效地防止无法进行正常的打壳、下料;无法进行正常的阳极升降调整;无法及时报告效应及异常情况;实际下料量与报表下料量不符;无法切断AC220V动力电源信号等情况的发生,保证了铝电解智能模糊控制系统的正常运行,为电解的正常生产提供了保障。
为了验证此项改进的可实施性,我们在实验室、生产现场进行了一定测量。
测量数据如下:
项目
IN4742(DC12V)
电压值
R11(1K)电压值
U9-1
光耦
TLP521-2
实验室(不带载)
现场(带载)
无动作时回路电流
有动作时回路电流
无动作时回路电流
动作时回路电流
改线前
(原有线路)
12.03V
6.355V
1.13V
6.355mA
10.2mA
6.33mA
10.2mA
改线后
12.085V
6.380V
1.13V
6.355mA
10.2mA
6.35mA
10.3mA
通过此表可知,改动前与改动后相比,这个回路中的电流与各元气件上的电压前后变化不大。
考虑到测量手段、工具等客观因素的存在,这