天然气液化装置标准版.docx
《天然气液化装置标准版.docx》由会员分享,可在线阅读,更多相关《天然气液化装置标准版.docx(11页珍藏版)》请在冰豆网上搜索。
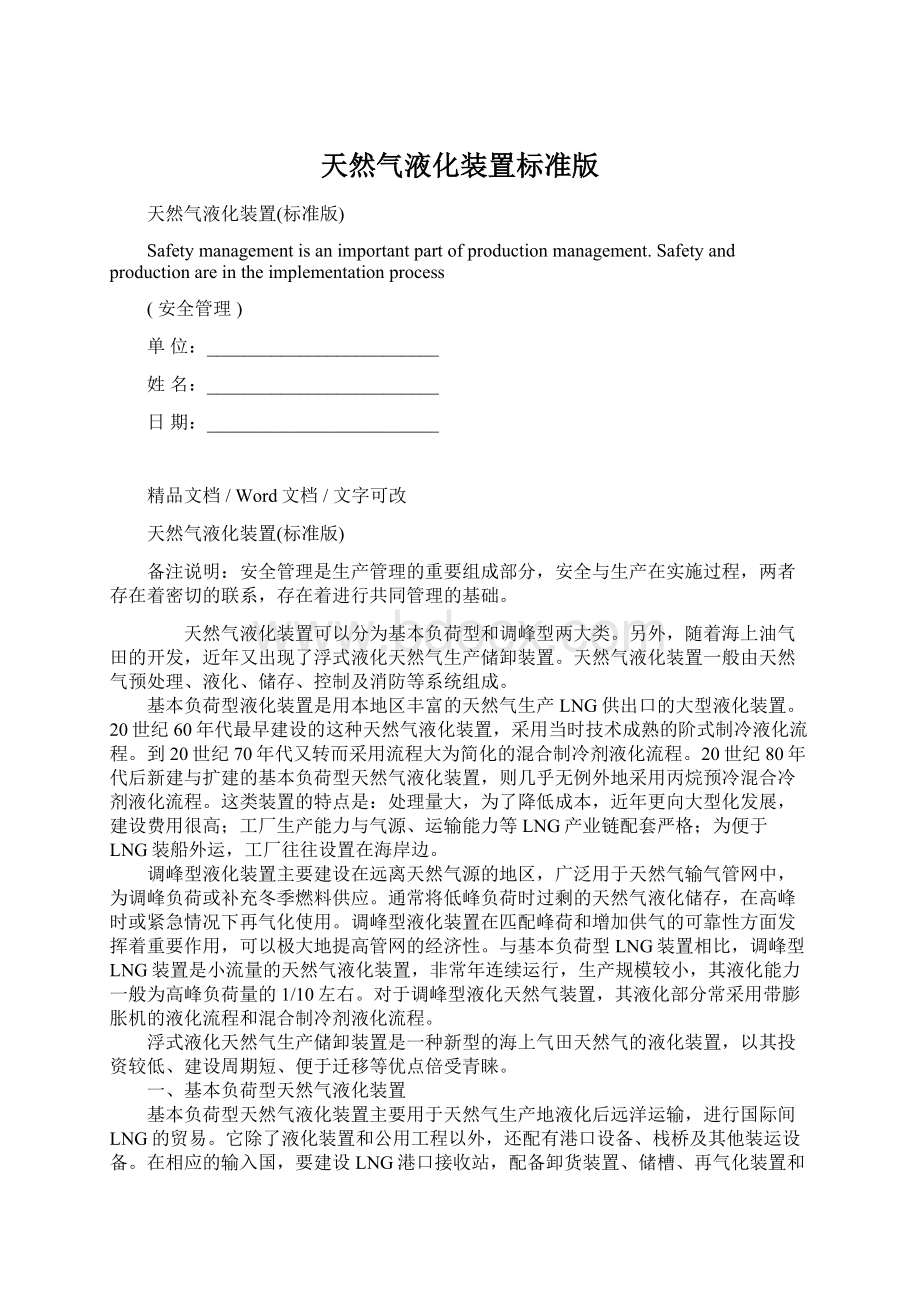
天然气液化装置标准版
天然气液化装置(标准版)
Safetymanagementisanimportantpartofproductionmanagement.Safetyandproductionareintheimplementationprocess
(安全管理)
单位:
_________________________
姓名:
_________________________
日期:
_________________________
精品文档/Word文档/文字可改
天然气液化装置(标准版)
备注说明:
安全管理是生产管理的重要组成部分,安全与生产在实施过程,两者存在着密切的联系,存在着进行共同管理的基础。
天然气液化装置可以分为基本负荷型和调峰型两大类。
另外,随着海上油气田的开发,近年又出现了浮式液化天然气生产储卸装置。
天然气液化装置一般由天然气预处理、液化、储存、控制及消防等系统组成。
基本负荷型液化装置是用本地区丰富的天然气生产LNG供出口的大型液化装置。
20世纪60年代最早建设的这种天然气液化装置,采用当时技术成熟的阶式制冷液化流程。
到20世纪70年代又转而采用流程大为简化的混合制冷剂液化流程。
20世纪80年代后新建与扩建的基本负荷型天然气液化装置,则几乎无例外地采用丙烷预冷混合冷剂液化流程。
这类装置的特点是:
处理量大,为了降低成本,近年更向大型化发展,建设费用很高;工厂生产能力与气源、运输能力等LNG产业链配套严格;为便于LNG装船外运,工厂往往设置在海岸边。
调峰型液化装置主要建设在远离天然气源的地区,广泛用于天然气输气管网中,为调峰负荷或补充冬季燃料供应。
通常将低峰负荷时过剩的天然气液化储存,在高峰时或紧急情况下再气化使用。
调峰型液化装置在匹配峰荷和增加供气的可靠性方面发挥着重要作用,可以极大地提高管网的经济性。
与基本负荷型LNG装置相比,调峰型LNG装置是小流量的天然气液化装置,非常年连续运行,生产规模较小,其液化能力一般为高峰负荷量的1/10左右。
对于调峰型液化天然气装置,其液化部分常采用带膨胀机的液化流程和混合制冷剂液化流程。
浮式液化天然气生产储卸装置是一种新型的海上气田天然气的液化装置,以其投资较低、建设周期短、便于迁移等优点倍受青睐。
一、基本负荷型天然气液化装置
基本负荷型天然气液化装置主要用于天然气生产地液化后远洋运输,进行国际间LNG的贸易。
它除了液化装置和公用工程以外,还配有港口设备、栈桥及其他装运设备。
在相应的输入国,要建设LNG港口接收站,配备卸货装置、储槽、再气化装置和送气设备等。
基本负荷型天然气液化装置的液化和储存连续进行,装置的液化能力一般在106
m3
/d以上。
全部设施由天然气预处理流程、液化流程、储存系统、控制系统、装卸设施和消防系统等组成,是一个复杂庞大的系统工程,投资高达数十亿美元。
如年产600×104
t的LNG项目,从天然气生产、液化到LNG运输,不包括LNG接收和下游用户,投资约需60~80亿美元。
项目建设一般需以20~25年的长期供货合同为前提。
由于项目投资巨大,LNG项目大多由大型跨国石油公司与资源拥有国政府合资建设。
(一)阶式制冷的基本负荷型天然气液化装置
1961年,在阿尔及利亚建造的世界上第一座大型基本负荷型天然气液化装置(CAMEL),采用丙烷、乙烯和甲烷组成的阶式制冷液化流程,见图3-13[7]
。
于1964年在阿尔及利亚Arzew交付使用。
该液化工厂共有三套相同的液化装置。
每套装置液化能力为1.42×106
m3
/d。
进厂的天然气压力为3.24MPa;温度37.8℃;组分的摩尔分数是:
83%甲烷、10%C2
+
以上的烷烃、7%氮。
原料气先经离心压缩机压缩到4.1MPa,用海水进行冷却;此后用单乙醇胺溶液脱除二氧化碳,用乙二醇及铝胶清除水分,将露点降到-73℃以下。
净化后的原料气进入液化装置。
每套装置用三台离心式制冷压缩机,它们在各自的封闭循环系统中作为制冷剂压缩机。
其中丙烷制冷循环在换热器15和19中,为天然气提供两个温度级的冷量,用于冷却天然气;乙烯制冷循环在乙烯冷却器22中,为天然气提供三个温度级的冷量,用于液化天然气;甲烷制冷循环在换热器23、24、25中,为天然气提供三个温度级的冷量,用于过冷液化天然气。
过冷后的液化天然气闪蒸到大气压,用泵送至储罐。
液化后的天然气组分的摩尔分数大致为:
86.98%甲烷、0.71%氮、其余为C2
+
以上的烷烃。
制冷循环所用的甲烷和丙烷直接取自天然气;乙烯则由乙醇脱水制得,每天补充量约需5t。
采用阶式制冷液化流程的优点是能耗低,且各制冷循环及天然气液化系统各自独立,相互牵制少,操作稳定。
它的缺点是流程复杂、机组多,要有生产和储存各种制冷剂的设备,各制冷循环系统间不能有任何渗漏,维修也不方便。
(二)混合冷剂制冷的基本负荷型天然气液化装置
混合制冷剂液化流程有开式和闭式两种。
闭式混合制冷剂液化流程是指制冷剂循环与天然气液化过程彼此分开的液化流程。
图3-14[7]
为采用闭式混合制冷剂液化循环的天然气液化装置示意图。
这套装置是1970年恢复运转的利比亚伊索工厂的液化装置。
该厂共有四条液化生产线,每两条液化线组成一套装置。
每套装置设有单独的原料气预处理、压缩机及换热器等。
总液化能力为1075×104
m3
/d。
两台并联布置的压缩机将原料气从起始压力2.84MPa压缩到4.64MPa。
压缩后的原料气用热钾碱法脱除二氧化碳与硫化氢;用分子筛脱水干燥,并借助吸附过程脱除高碳氢化合物。
净化后的天然气进入低温换热器冷却和液化,其液化压力为3.94MPa。
每套液化装置由四台离心式制冷压缩机及两台绕管式铝制换热器组成。
因此整个液化系统共有八台制冷压缩机,均用蒸汽透平驱动;四台低温绕管式换热器,每台直径4.5m,高61m,换热器面积93000m2
。
液化天然气产品在大气压下,储存在两个容量为47700m3
的地面双层隔热合金钢储槽中,储槽直径42.7m、高36.6m,内壳采用含9%Ni的钢板,蒸发率为0.1%。
与级联式液化流程相比,采用混合制冷剂液化流程的液化装置具有机组设备少、流程简单、投资较少、操作管理方便等优点。
同时,混合制冷剂中各组分一般可部分或全部从天然气本身提取和补充,因而没有提供纯制冷剂的困难,且纯度要求也没有级联式液化流程那样严格。
其缺点是能耗比级联式液化流程高出15%~20%;对混合制冷剂各组分的配比要求严格,流程计算困难。
(三)丙烷预冷混合冷剂制冷的基本负荷型液化装置
为了降低混合制冷剂液化流程的能耗,20世纪60年代末出现了许多改进型的混合制冷剂液化流程。
70年代,APCI(美国空气液化公司)发展了丙烷预冷混合制冷剂液化流程,于1973年获得专利,并在大型LNG工厂得到了广泛应用。
它是级联式循环和混合制冷剂循环的结合,用丙烷将天然气从40℃预冷至-30℃;混合制冷剂循环再把天然气从-30℃过冷到-160℃。
图3-15[7]
是首次采用这种液化流程的天然气液化装置的流程简图,于1973年建于北加里曼丹的文莱。
该厂共有五套这样的装置,每套液化能力为424.5×104
m3
/d。
原料气经脱除水分及重烃后,通过两条直径为710mm的输气管送入厂内。
采用环丁砜法吸收脱除原料气中的二氧化碳及硫化氢;处理后的原料气含有的饱和水经两步脱除,即先将原料气冷却至21℃左右,使约70%的水分被冷凝分离出来,而后再用分子筛深度脱水。
净化后天然气组分的摩尔分数为:
88.2%甲烷、50%乙烷、4.9%丙烷、1.8%丁烷及0.1%C3
+
。
此后,天然气经重烃回收塔分离重烃,并用丙烷预冷到-34℃,在4MPa压力下进入混合制冷剂循环的低温换热器,在其中被冷却、液化和过冷。
过冷后的液化天然气送入储槽。
该厂有液化天然气地面储槽三个,每个容量60000m3
。
槽内压力维持在29.4kPa,槽内蒸发气返回工厂作燃料。
(四)基本负荷型液化装置中液化流程的比较
基本负荷型天然气液化装置主要采用上述三种液化流程,其主要指标的比较见表3-5。
表3-6列出世界上一些基本负荷型装置所使用的液化流程及其性能指标。
表3-5液化流程主要技术经济指标比较
比较项目
阶式液化流程
闭式混合冷剂液化流程
丙烷预冷混合冷剂液化流程
处理气量/104
m3
①
1087
1087
1087
燃料气量/104
m3
①
168
191
176
进厂气总量/104
m3
①
1255
1287
1263
制冷压缩机功率/kw
丙烷压缩机
58971
—
45921
乙烯压缩机
72607
—
—
甲烷压缩机
42810
—
—
混合制冷剂压缩机
—
200342
149886
总功率
175288
200342
195870
换热器总面积/m2
翅片式换热器
175063
302332
144257
绕管式换热器
64141
32340
52153
钢材及合金耗量/t
15022
14502
14856
总投资/104
美元
9980
10070
10050
①为标准状态下的气体体积。
表3-6基本负荷型液化装置性能指标
项目名称
投产时间/年
液化流程
产量/(104
t/a)
压缩机功率/kw
功率③
/kW
阿尔及利亚Arzew,CAMEL
1963
阶式
36
22800
141
阿拉斯加Kenai
1969
阶式
115
63100
122
利比亚MarsaelBrega
1970
MRC①
69
45300
147
文莱LNG
1973
C3
/MRC②
108
61500
127
阿尔及利亚Skikda1,2,3
1974
MRC
103
78300
169
卡塔尔Gas
1996
C3
/MRC
230
107500
104
马来西亚MLNGDua
1995
C3
/MRC
250
102500
91
马来西亚MLNGTiga
2002
C3
/MRC
375
14D000
83
①MRC为混合制冷剂液化流程。
②C3
/MRC为丙烷预冷混合制冷剂液化流程。
③功率为生产1kg的LNG所消耗的功。
从表中可以看出,丙烷预冷混合制冷剂液化流程在基本负荷型装置中得到了广泛的应用。
大多数运行中的基本负荷型LNG装置都采用这种液化流程。
在过去的几年里,对这类工艺流程进行了进一步的改进,从而几个新建LNG工厂都采用了这种液化流程,如马来西亚的MLNGTiga,澳大利亚西北大陆架第4条生产线和尼13利亚扩建的LNG项目。
现其单线生产能力已达到400×104
t/a的数量级。
当前日趋激烈的市场竞争对天然气液化装置提出了能耗低、投资少、设备运行可靠、易于维护的要求。
这些要求促进了天然气液化技术的进步。
目前除了上述广泛采用的三种液化天然气的液化流程外,近年来在工业上还发展了一些改进型的混合制冷剂液化流程,如壳牌公司设计的双混合制冷剂液化流程(DMR),且已在阿尔及利亚Skikda天然气液化工厂的I型液化装置(共3套)上采用。
另外,特立尼达和多巴哥的LNG项目,安装了菲利浦的优化级联液化流程。
壳牌公司的双混合制冷剂液化流程,主要用于中高生产量的LNG生产线,其产量范围为(200~500)×104
t/a。
这一液化流程包括两个混合制冷剂循环,一个用于预冷,另一个用于液化。
壳牌公司通过优化设计DMR液化流程,从而可充分利用预冷循环和液化循环中的压缩机驱动装置的动力。
对于DMR液化流程,可通过调节两个循环中混合制冷剂的组分,使压缩机在很宽的进气条件和大气环境下工作。
DMR液化流程在投资方面比丙烷预冷混合制冷剂液化流程更有竞争力。
这已在阿尔及利亚Skikda天然气液化工厂中得到证实。
DMR液化流程若用在热带地区,则投资将会进一步降低。
(五)发展趋势
天然气液化工厂是LNG产业链中技术密集、投资额大的重要一环。
在全球天然气利用快速增长的今天,寻求天然气液化工厂经济有效的建设方案也越发受到关注,特别是工艺技术、经济规模、优化设计等方面的进步,提高了天然气液化工厂的经济性。
1.工艺技术
天然气液化工厂的工艺技术主要是天然气预处理工艺和液化工艺。
工艺流程的先进、合理是减少投资、方便操作、降低成本的基础。
随着各种类型气田的开发,液化工厂的原料气组成变化不断增大。
天然气预处理工艺要适应各种气质的处理要求,特别是高酸气含量的原料气的处理。
目前,醇胺法、Sulfinol法和Benfield法是使用较多的酸气脱除方法。
而分子筛法是使用较多的天然气脱水方法。
对于液化工艺,。
由于液化设备的投资要占工厂总投资的近三分之一,因此工艺的先进性直接影响到工厂建设和运行的经济性。
液化工艺的选择应使流程简单、适应性强、操作弹性大、设备标准化程度高、污染排放少。
目前,丙烷预冷混合制冷剂液化工艺被认为是高效的。
在此基础上,发展的一些流程各具特色,需按项目情况选择。
如澳大利亚采用的优化级联流程,AP-X流程等。
2.装置规模
与大多数工厂相同,在一定的产量下,装置规模大,有利于降低建设投资和运行成本。
LNG工厂也是如此。
随着生产规模的扩大,投资费用的增加并不显著,如工艺相同的装置,年产量800×104
t的工厂总投资仅比年产量600×104
t的工厂多10%~15%,但是单位产品的投资要降低15%,生产运行费用也低。
因而增加单套生产规模可以得到好的规模效益。
单套装置的年生产能力已达到300×104
t。
但是,由于LNG产业链的特点,LNG工厂的生产能力受上游气田天然气供应能力和下游LNG运输能力的制约,生产规模不宜太大。
对于一座年产量800×104
t的LNG工厂,按合同期25年计,其原料气需求量多达3×1012
m3
,必须要有资源量足够的天然气田的支持。
另外,天然气资源产地往往远离市场,生产能力的安排必须考虑工厂附近地区市场需求之外的产品的运输问题。
对LNG产业链来说,这两方面的问题比其他产业更为突出。
3.设计优化
工厂的设计优化对降低造价作用明显。
近年来,LNG工厂设计,从厂址选择、总图布置、管路安装到设备选型,都着重于设计优化。
如厂址选择不仅考虑厂址内部工程地质条件、地貌情况、水电等公用系统的供应,而且对工厂与气源地、产品外运条件做充分的比选。
在LNG工厂设计中越来越重视集成优化。
二、调峰型天然气液化装置
调峰型液化装置指为调峰负荷、补充冬季燃料供应或事故调峰用的天然气液化装置,通常将低峰负荷时过剩的天然气液化储存,在高峰时或紧急情况下再气化使用。
此类装置的液化能力较小,储存容量和再气化能力较大,生产的LNG一般不作为产品外售。
调峰型LNG装置通常远离天然气的产地,常处在城市管网附近。
调峰型LNG工厂年开工200~250天,以保证充满储罐,再气化供调峰使用。
调峰型天然气液化装置中主要采用以下三种类型的液化流程:
①阶式液化流程,曾被广泛采用,现在基本上不用;②混合制冷剂液化流程;③膨胀机液化流程,这类装置充分利用原料气与管网气之间的压力差,达到节能的目的。
(一)天然气直接膨胀调峰型液化装置
天然气直接膨胀液化流程,是直接利用气田来的有压力的天然气,在膨胀机中绝热膨胀到输送管道的压力,而使天然气液化的流程。
美国西北天然气公司1968年建立的一座调峰型液化装置就是采用此液化流程,其流程简图见图3-12。
该装置以压力为2.67MPa,经粗净化后含CO2
(900~4000)×10-6
m3
/m3
、H2
S0.7~4.5mg/m3
、硫化物约6~70mg/m3
的天然气为原料气,经天然气膨胀机绝热膨胀到约490kPa的压力,循环的液化率为10%左右。
每日处理原料气量为56.6×104
m3
,装置液化能力约为5.7×104
m3
/d。
储槽容积约1700×104
m3
,全年的液化气量都储入储槽。
气化器气化能力为170×104
m3
/d,并有100%的备用量。
在高峰负荷时,即在10天内将全年储存量全部进行气化。
进入膨胀机的天然气不需要脱除CO2
,而只对液化部分的原料气进行CO2
的脱除,因此预处理气量大为减少。
装置正常运转时,储槽蒸发的天然气经返回气压缩机压缩后,回到系统进行液化。
装置的主要工艺参数见表3-7。
表3-7装置主要工艺参数
工艺参数
物流名称
原料气
返回气
换热器5的膨胀气①
过冷器8的原料气①
出膨胀机气体
尾气
温度/℃
压力/kPa
流量/(104
m3
/d)
15.6
2670
56.6
26.7
241
14.2
—
480
—
-143
—
—
-112
—
—
37.8
—
36.8
①所列的设备见图3-12天然气膨胀液化流程图所示。
这种流程特别适用于管线压力高,实际使用压力较低,中间需要降压的地方。
其突出的优点是能充分利用天然气在输气管道的压力差膨胀制冷,做到几乎不需要消耗电。
此外还具有流程简单、设备少、操作及维护方便等优点。
因此,它是目前发展很快的一种流程。
在这种液化装置中,天然气膨胀机是个关键设备,因为在膨胀过程中,天然气中一些沸点高的组分将会冷凝析出,致使膨胀机在带液工况下运行,这要求膨胀机有特殊的结构。
目前国外多家公司已制造天然气带液膨胀机。
美国在1972年已出现了膨胀量为53×104
m3
/h的犬型天然气透平膨胀机,天然气从16.7MPa膨胀到4.7MPa,膨胀机出口含湿量为15%,制动压缩机可将天然气从4.7MPa增压到9.4MPa,从而使这种流程的应用范围日益广泛。
膨胀机液化流程的液化率,相对于其他类型的流程来说要低一些,且主要取决于膨胀前后的压力比。
压比越大,液化率也越大,液化率一般在7%~15%左右。
(二)氨膨胀液化调蜂型液化装置
氮膨胀液化流程是天然气直接膨胀液化流程的一种变型。
在流程中,氮气制冷循环回路与天然气液化回路分开,氮气制冷循环为天然气提供冷量。
该流程对含氮稍多的原料天然气,只要设置氮一甲烷分离塔,就可制取纯氮以补充氮制冷循环中氮的损耗,并可同时副产少量的液氮及纯液甲烷。
装置中的膨胀机和压缩机均采用离心式,体积小,操作方便;对原料气组分变化有较大的适应性;整个系统较简单。
但这种流程能耗较高,约为0.5kW·h/m3
,比混合制冷剂液化流程高40%左右。
氮-甲烷膨胀液化流程是氮膨胀液化流程的一种改进,其制冷循环中采用的工质是氮气和天然气的混合物,而不是纯氮。
(三)混合冷剂制冷调峰型液化装置
随着混合制冷剂液化流程的广泛应用,在调峰型装置中也越来越多地应用这类流程。
我国建造的第一座调峰装置(上海浦东LNG调峰站)就是采用混合制冷剂液化流程。
该调峰装置用于东海天然气开发中,当上游生产因人力不可抗拒的因素(如台风等)停产时,确保安全供气。
装置采用整体结合式级联型液化流程(CII液化流程)。
液化能力为165m3
LNG/d。
气化能力为120m3
LNG/h。
三、浮式液化天然气生产储卸装置
由于海洋环境特殊,海上天然气的开发技术难度大、投资高,建设周期和资金回收期长,因此风险较大j目前开发的都是一些大型的商业性天然气田。
边际气田一般为地处偏远的海上小型气田,若采用常规的固定式平台进行,则收益较低,开发的经济性很差。
20世纪90年代以来,随着发现的海上大型气田数量减少,边际气田的开发日益受到重视。
同时海洋工程的不断进步,也使边际气田曲勺开发成为可能。
浮式液化天然气生产储卸装置(FloatingProduction,StorageandOffloadingsystem,简称FPSO)作为一种新型的边际气田开发技术,以其投资较低、建设周期短、便于迁移等优点倍受青睐。
常规海上天然气开发,包括海上平台的建设、铺设海底天然气输送管道、岸上天然气液化工厂的建设、公路建造、LNG外输港口等基础设施,其投资大、建造周期长、现金回收迟。
针对以上不足,浮式LNG生产储卸装置的设计着眼于低投资、投产快和高效益,集液化天然气的生产、储存与卸载于一身,简化了边际气田的开发过程,优点颇多。
浮式LNG装置可分为在驳船、油船基础上改装的LNG生产储卸装置和新型混凝土浮式生产储卸装置。
整个装置可看作一座浮动的LNG生产接收终端,直接泊于气田上方进行作业,不需要先期进行海底输气管道、LNG工厂和码头的建设,降低了气田的开发成本。
同时减少了原料天然气输送的压力损失,可以有效回收天然气资源。
浮式LNG装置采用了生产工艺流程模块化技术,各工艺模块可根据质优、价廉的原则,在全球范围内选择厂家同时进行加工建造,然后在保护水域进行总体组装,可缩短建造安装周期,加快气田的开发速度。
另外,浮式LNG装置远离人口密集区,对环境的影响较小,有效避免了陆上LNG工厂建设可能对环境造成的污染问题。
该装置便于迁移,可重复使用,当开采的气田气源衰竭后,可由拖船拖曳至新的气田投入生产,尤其适合于海上边际气田的开发。
海上作业的特殊环境对液化流程提出了如下要求:
①流程简单、设备紧凑、占地少、满足海上的安装需要;②液化流程有制取制冷剂的能力,对不同产地的天然气适应性强,热效率较高;③安全可靠,船体的运动不会显著地影响其性能。
美孚石油公司浮式LNG装置的液化流程如图3-16所示[8]
。
设计采用了单一混合制冷剂液化流程,可处理CO2
的体积分数高达15%,H2
S体积浓度含量为10-4m3
/m3
的天然气。
由于取消了丙烷预冷,彻底消除了丙烷储存可能带来的危害。
该流程以板翅式换热器组成的冷箱为主换热器,结构紧凑,性能稳定。
出于安全性的考虑,BHP石油公司采用改进的氮膨胀液化循环作为浮式LNG装置的液化流程。
氮膨胀循环以氮气取代了常用的烃混合物作为制冷剂,安全可靠,流程简单,设备安装的空间要求低,缺点是能耗较高。
浮式LNG装置的液化流程在设计时,要充分考虑波浪引起的船体运动对设备性能可能产生的不良影响。
由于填料塔工作性能稳定,酸气脱除模块中的吸收塔和再生塔应优先选择填料塔,分配器的类型和塔径也要合理选择,以保证工质在填料中的合理分配。
当天然气中CO2
体积分数高于2%时,可考虑采用胺洗和膜吸附相结合的酸气脱除系统。
液化及分馏模块中的蒸馏塔的直径和高度,由于远小于吸收塔和再生塔,对塔盘、堰板进行改进后