制动系统设计手册NEW.docx
《制动系统设计手册NEW.docx》由会员分享,可在线阅读,更多相关《制动系统设计手册NEW.docx(13页珍藏版)》请在冰豆网上搜索。
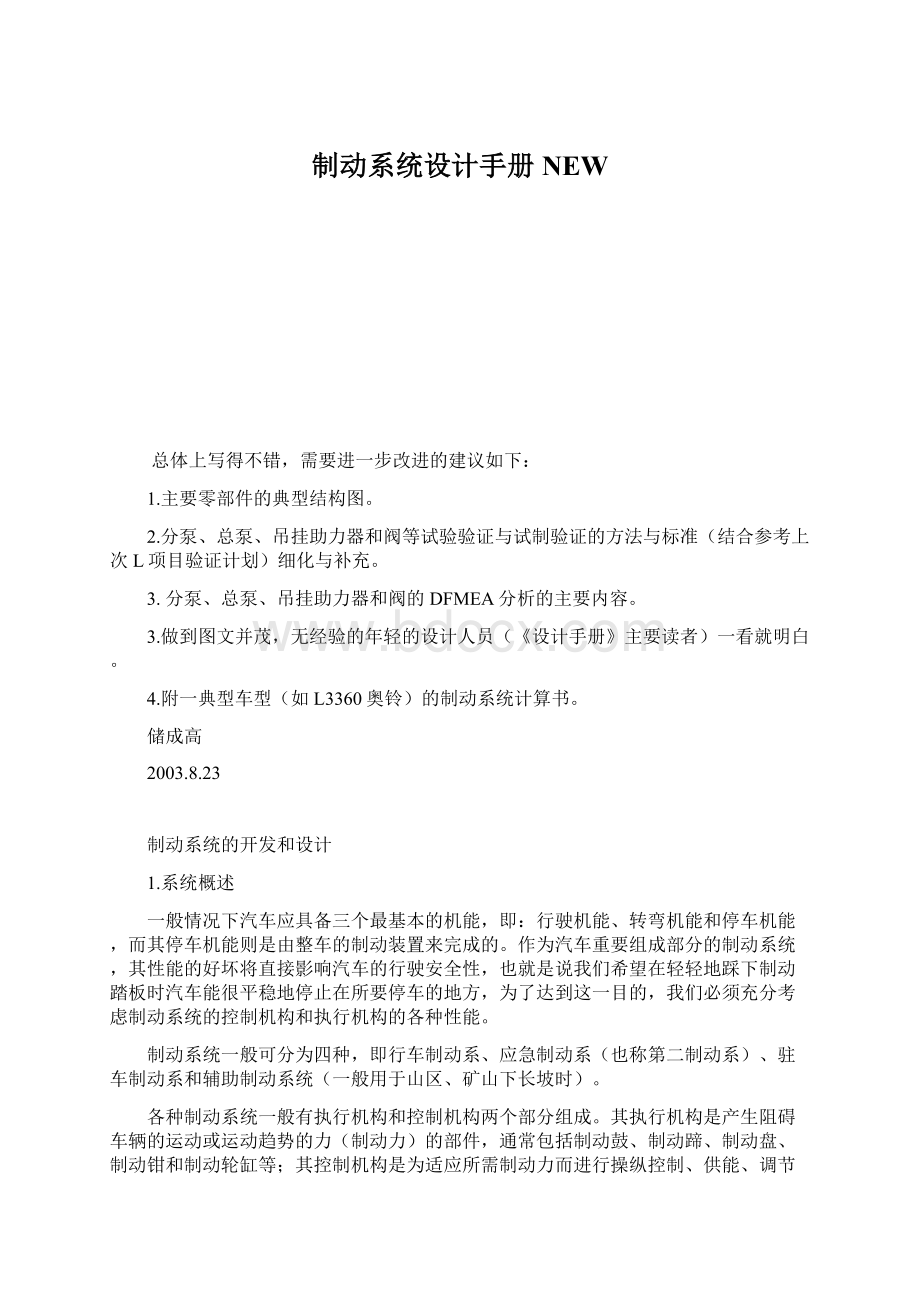
制动系统设计手册NEW
总体上写得不错,需要进一步改进的建议如下:
1.主要零部件的典型结构图。
2.分泵、总泵、吊挂助力器和阀等试验验证与试制验证的方法与标准(结合参考上次L项目验证计划)细化与补充。
3.分泵、总泵、吊挂助力器和阀的DFMEA分析的主要内容。
3.做到图文并茂,无经验的年轻的设计人员(《设计手册》主要读者)一看就明白。
4.附一典型车型(如L3360奥铃)的制动系统计算书。
储成高
2003.8.23
制动系统的开发和设计
1.系统概述
一般情况下汽车应具备三个最基本的机能,即:
行驶机能、转弯机能和停车机能,而其停车机能则是由整车的制动装置来完成的。
作为汽车重要组成部分的制动系统,其性能的好坏将直接影响汽车的行驶安全性,也就是说我们希望在轻轻地踩下制动踏板时汽车能很平稳地停止在所要停车的地方,为了达到这一目的,我们必须充分考虑制动系统的控制机构和执行机构的各种性能。
制动系统一般可分为四种,即行车制动系、应急制动系(也称第二制动系)、驻车制动系和辅助制动系统(一般用于山区、矿山下长坡时)。
各种制动系统一般有执行机构和控制机构两个部分组成。
其执行机构是产生阻碍车辆的运动或运动趋势的力(制动力)的部件,通常包括制动鼓、制动蹄、制动盘、制动钳和制动轮缸等;其控制机构是为适应所需制动力而进行操纵控制、供能、调节制动力、传递制动能量的部件,一般包括助力器、踏板、制动主缸、储油杯、真空泵、真空罐、比例阀、ABS、制动管路和报警装置等,有的还包括具有压力保护和故障诊断功能的部件。
在其控制机构中如果按其制动能量的传输方式制动系统又可分为:
机械式、液压式、气压式和电磁式(同时采用两种以上传能方式的制动系统可称为组合式制动系统,如气顶油等)。
制动系统是影响汽车行驶安全性的重要部分,通常其应具备以下功能:
可以降低行驶汽车的车速,必要时可以在预定的短距离内停车,且维持行驶方向的稳定性;下长坡时能维持一定的车速;驻车制动的功能等。
2.设计依据和原则
2.1根据产品信函(或项目描述书)所描述的整车的使用情况(含道路状况、使用条件及用户群体等)确定制动系统的总体方案,为系统各零部件的选型提供依据;
2.2根据车型提供的整车参数,结合各项强制法规的要求,初步分析各所选制动零部件与整车匹配的合理性;
2.3根据强制法规的要求,制定试验方案进一步验证整车制动系统匹配和各制动元件选型的合理性。
3.设计方案初步规划
3.1各主要零部件的选型及相关注意事项:
3.1.1制动器总成
3.1.1.1通过对所开发车型与已开发同类车型(或标杆车)的比较,初步确定系统各零部件的型式、结构和相关参数,而单纯从整车对制动力的需求方面来说,制动器的制动力越大越好,但由于制动器所产生的制动力与制动器的结构型式、制动器直径、制动器的分泵直径、制动器摩擦副的相对摩擦系数、制动管路压力等等因素有关,故在选取时应遵循以下原则;
3.1.1.2制动器结构型式的选型原则:
根据整车档次、使用地区、用户群体等确定制动器的结构型式;
系统类型
制动器结构型式
制动器特点
适用整车工作情况
备注
液压制动系统
盘式
具有优良的热稳定性和水稳定性,适应于高速的需求,但由于其制动效能低(需要输入较高的液压),制动液的工作温度较高,且价格也较高
广泛用于中高档车上
对制动液的要求高,否则制动液会气化形成气阻
双向自增力式
价格低廉、制动效能高但制动过程较粗暴、稳定性较差,且效能太高易发生制动器自锁
在国外尤其是美国、澳大利亚等较多地用于大型高速轿车中,但由于国内在制造工艺、生产水平等方面存在一定的问题,该类制动器不适合高速车辆配置;普遍用于农村或城乡结合带且超载较为频繁的车辆上
领从蹄式
制动过程较稳定,构造简单,价格也比较低,但制动效能较低
适用范围较广,一般用于后制动器,与盘式或双领蹄式制动器配合。
双领蹄式/双向双领蹄式
制动过程较稳定,价格适中,但制动效能也比较适中
广泛应用于各类中高档汽车中,尤其是轻卡新产品
双从蹄式
虽然其结构简单、稳定性好,但其制动效能太低
在汽车产品中较少应用
气压制动系统
领从蹄式
冲压底板,渐开线凸轮,价格低廉,但制动底板的刚性相对较弱,且凸轮与制动蹄铁之间为滑动摩擦,时间久了或润滑不良的情况下在接触面易形成沟槽或浊点,引起制动蹄回位不良等问题
现主要用于经济型汽车或农用车中
铸造底板,S凸轮,价格较高,制动底板的刚性较强,凸轮与制动蹄铁之间为滚动摩擦,整个制动过程相对较为稳定
广泛用于各类气制动系统的车型中
3.1.1.3制动器直径的选型原则:
由于制动器的直径与轮辋直径有关,在选型时应根据整车布置及轮辋的要求,考虑制动鼓的散热问题,一般制动鼓与轮辋的间隙应不小于10mm,否则会导致制动器散热不良,引起制动鼓早期龟裂、制动衬片烧结、炭化,大大降低制动器的制动效能;另外,制动器与轮辋的间隙太小,制动过程所产生的热量也将大量传导至轮辋上,对轮胎不利。
3.1.1.4制动器衬片摩擦系数的确定:
由于制动器衬片的摩擦系数是决定制动器制动力的主要原因之一,在同型、同规格的制动器中,制动衬片的摩擦系数越高,制动器所产生的制动力越大,但对于不同结构的制动器来说,并不是摩擦系数越高越好,摩擦系数太高对制动鼓(或盘)的磨损也越大,且对于双向自增力式制动器,摩擦系数越高,制动过程越粗暴,对制动底板、制动蹄铁、制动鼓的刚性要求越高,否则在制动过程中越易产生制动器颤动、整车发抖的现象,故对于摩擦系数的选取根据本人的经验建议:
双向自增力式制动器的取0.38左右,其它结构型式的制动器取0.45~0.5左右,盘式制动器取0.35左右。
3.1.1.5制动器分泵直径的选型和确定:
在上述参数选定以后,根据整车所需的各轴制动力来确定制动器分泵的直径。
对于单个制动器而言,制动器所产生的制动力与制动分泵活塞的有效面积(直径的平方——液压制动器)成正比,在选取过程中应兼顾国家标准规格(为提高零部件资源的通用性,国家对制动总、分泵的直径的规格制定了相关标准)和社会成熟资源,液压制动器的分泵直径最大不超过32mm。
3.1.1.6前后制动器制动分泵的选取、分配原则:
从各方面的调查分析,对于一般的驾驶员来说,在正常行车的过程中实施制动的概率分布如下:
制动强度在0.25以下的约占95%左右,在0.5以上的仅占0.1%。
这一统计数据表明通常的制动都是在小制动减速度下进行,且此时各轴的车轮均未出现抱死现象,即制动衬片与制动鼓之间一直处于滑动摩擦阶段,而此时整个制动系统的管路压力一样,对于同样结构的制动器,如果分泵活塞直径大,则制动器产生的制动力就大,从而导致制动衬片的磨损加大,因此,在确定前后制动分泵直径时,最佳原则时前后制动器分泵直径相等或后分泵比前分泵稍小,以确保前后制动器在正常情况下同步磨损。
当然,当前后制动分泵直径相等或相差不大时,在实施较大制动强度的制动时易出现后轮先抱死甩尾,故在采取此种分配方式时必须增加阀类元件调节后管路的压力,以防止后轮先抱死。
3.1.2真空助力器带制动总泵总成
3.1.2.1制动总泵的选取原则:
制动总泵的选取主要取决于制动分泵,在制动器间隙合适的情况下,其直径的选取将直接引响制动踏板的行程,对于单分泵制动器的系统,一般以总泵的直径与后制动器直径相当为宜,而对于双分泵制动器的系统其总泵的直径以与前制动分泵直径相当为好。
3.1.2.2真空助力器的选用原则:
真空助力器的直接作用在于降低制动踏板力,当制动踏板力太大时,仅依靠人的输入力(按照标准要求人的最大输入力不得大于700N)可能不足以使整车完全制动,而利用真空对助力器内橡胶膜片及反馈盘的作用可以成数倍(取决于真空助力器的助力比)地放大制动踏板的输入力,即增大制动总泵活塞的输入力,从而增大制动管路的压力。
当然真空助力器助力比的选取应合适,助力比太大易使驾驶员失去踏板感,而太小又使人在制动过程中感到吃力,且对于一定规格的助力器来说,助力器的助力比越大,其最大输出拐点越低,这就容易造成整个制动过程在初期省力,但在后期特废力,严重时也会刹不住车,故真空助力器助力比的选取以使制动踏板力调整适当为宜。
另当某一规格的助力器对整车制动踏板力的调整不能满足要求且适当调整助力比仍不能达到要求时应更换助力器的规格。
3.1.3制动踏板吊挂总成:
制动踏板吊挂总成的设计和选用一般根据驾驶室布置的需要而确定,其杠杆比的确定以总行程不大于180mm、踏板面至地板的高度160mm左右、与前面配置的分泵、总泵的分配原则(制动踏板的行程以不大于总行程的75%为宜)等因素进行确定,一般取4.5~5左右;
3.2初步分析计算:
3.2.1根据以上对制动系统的初步规划和主要零部件的选型后需要对整个制动系统的匹配进行初步分析计算,考察所选配置与整车、所选配置在整车上的应用与相关法规的符合性,必要时重新调整配置;
3.2.2分析计算过程中的相关注意事项:
3.2.2.1整车基本参数应尽可能地准确,尤其是空、满(超)载质心的位置;
3.2.2.2制动踏板的行程:
根据制动系统各部分总的杠杆比情况一般不得大于制动踏板总行程的75%;
3.2.2.3制动踏板力:
一般情况下制动踏板力不宜过大,在0.8制动强度下整车的制动踏板力轻卡以不大于250N、小卡、微卡以不大于200N为宜;
3.2.2.4制动距离:
根据相关标准的要求应与其符合,必要时按法规要求在规定的制动踏板下进行部分管路失效计算;
3.2.2.5制动器的磨损容量和热容量:
一般用磨擦片的比能量耗散率[每单位衬片(衬块)磨擦面积的每单位时间耗散的能量]、比磨擦力[每单位衬片(衬块)磨擦面积的制动器的磨擦力]来衡量制动器的热容量和磨损容量。
鼓式制动器的热容量以不大于1.8w/mm2,盘式制动器不大于6w/mm2,磨损容量不大于0.48N/mm2为宜。
3.3制动系统各总成零部件在设计和布置过程中的注意事项:
3.3.1制动器总成:
优先采用社会成熟资源,但在与整车实际应用时应考察制动器的效能、制动底板、制动蹄铁、制动鼓的刚性与整车的符合性。
3.3.2制动总泵:
应严格控制总泵的空行程、建压行程和建压曲线,一般总泵每腔的空行程以不大于1.5mm,在输出口输出压力达0.4Mpa时总泵活塞推杆的行程不得大于4mm(一般0.4Mpa的管路压力可以消除制动蹄与制动鼓之间的间隙),总泵的建压曲线越陡越好,不能过于平坦,否则会造成制动踏板感发绵、发软。
3.3.3真空助力器:
应严格控制真空助力器总成的空行程,一般以不大于1.5mm为宜。
3.3.4真空助力器带总泵总成:
助力器推杆与总泵活塞窝的间隙以不大于0.5mm为宜,整个总成的建压行程应不大于6mm。
3.3.5制动踏板吊挂总成:
为确保制动过程中对踏板行程的消耗,在设计和制造过程中应严格控制各铰接(连接)处的配合间隙。
一般以输出端不动的情况下,输入端(踏板面)的行程不大于3mm为宜。
3.3.6制动管路的布置:
首先以不与其它零部件干涉为前提,应尽量理顺;其次各管路的结构应合理,尤其是管路两端在整车行驶过程中有相对运动的件应考虑吸震方案,必要时采用软管连接;另外,在进行管路布置时应考虑管子的卡固,在空间允许的前提下管卡子的间隔以500~600mm为佳,当然在局部障碍部位可能要密一些。
4.试验验证
4.1试验目的:
通过性能试验验证系统的配置与整车及法规的符合性;通过可靠性试验以验证系统各零部件的工作可靠性。
4.2试验前提:
在试验前一定要将整个系统按规范进行调整完毕,即:
管路系统无空气、踏板的自由行程(一般不大于15mm)符合要求、制动器的间隙合适等。
4.3