测控技术与仪器专业设计论文高炉炼铁炉腹温度控制系统计.docx
《测控技术与仪器专业设计论文高炉炼铁炉腹温度控制系统计.docx》由会员分享,可在线阅读,更多相关《测控技术与仪器专业设计论文高炉炼铁炉腹温度控制系统计.docx(13页珍藏版)》请在冰豆网上搜索。
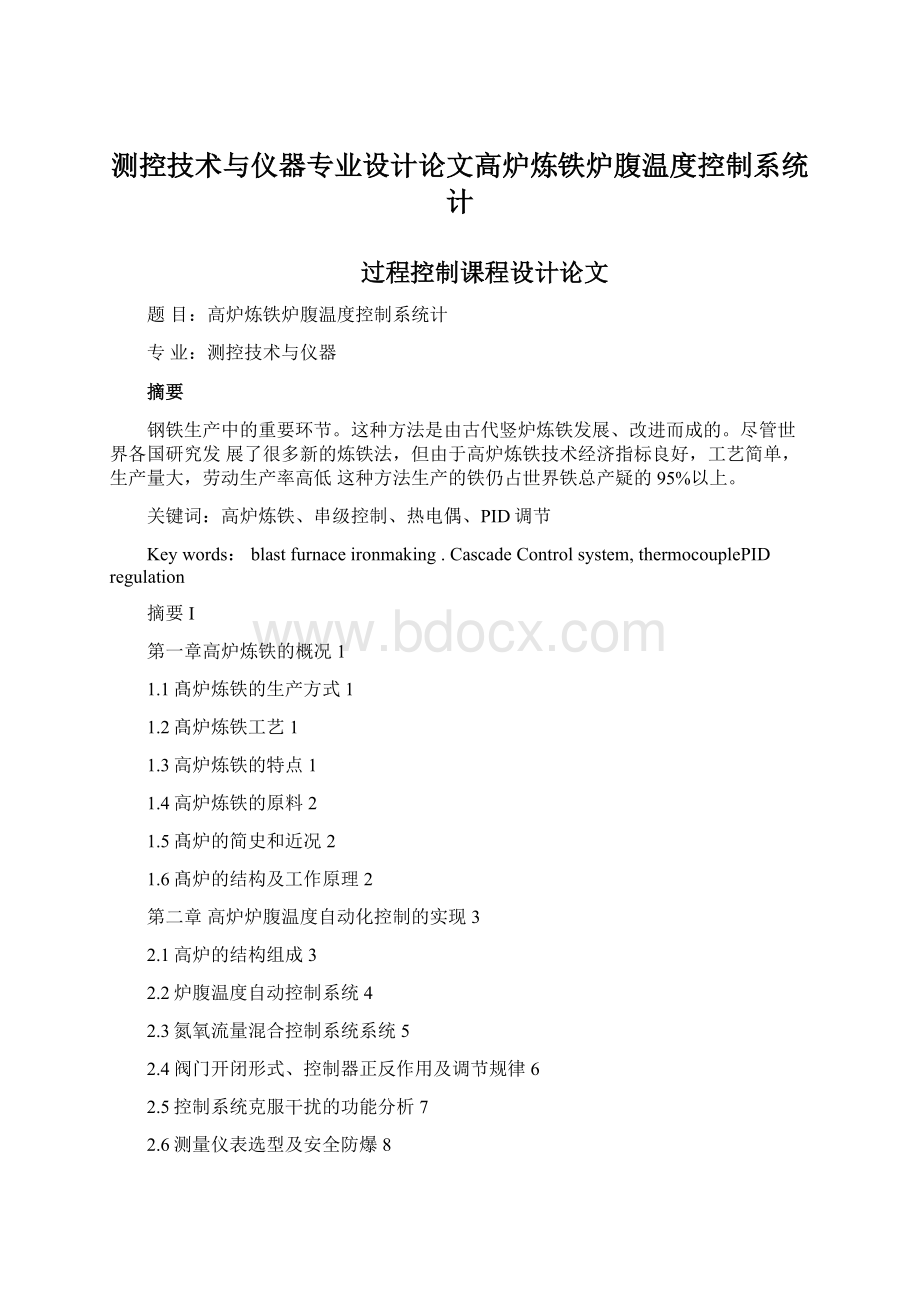
测控技术与仪器专业设计论文高炉炼铁炉腹温度控制系统计
过程控制课程设计论文
题目:
高炉炼铁炉腹温度控制系统计
专业:
测控技术与仪器
摘要
钢铁生产中的重要环节。
这种方法是由古代竖炉炼铁发展、改进而成的。
尽管世界各国研究发展了很多新的炼铁法,但由于高炉炼铁技术经济指标良好,工艺简单,生产量大,劳动生产率高低这种方法生产的铁仍占世界铁总产疑的95%以上。
关键词:
高炉炼铁、串级控制、热电偶、PID调节
Keywords:
blastfurnaceironmaking.CascadeControlsystem,thermocouplePIDregulation
摘要I
第一章高炉炼铁的概况1
1.1髙炉炼铁的生产方式1
1.2髙炉炼铁工艺1
1.3高炉炼铁的特点1
1.4高炉炼铁的原料2
1.5髙炉的简史和近况2
1.6髙炉的结构及工作原理2
第二章高炉炉腹温度自动化控制的实现3
2.1高炉的结构组成3
2.2炉腹温度自动控制系统4
2.3氮氧流量混合控制系统系统5
2.4阀门开闭形式、控制器正反作用及调节规律6
2.5控制系统克服干扰的功能分析7
2.6测量仪表选型及安全防爆8
第三章:
设计体会与心得13
第四章:
参考文献13
第一章高炉炼铁的概况
1.1高炉炼铁的生产方式
高炉生产时从炉顶装入铁矿石、焦炭、造渣用熔剂(石灰石),从位于炉子下部沿炉周的风口吹入经预热的空气。
在高温下焦炭(有的高炉也喷吹煤粉、重油、天然气等辅助燃料)中的碳同鼓入空气中的氧燃烧生成的一氧化碳和氢气,在炉内上升过程中除去铁矿石中的氧,从而还原得到铁。
炼出的铁水从铁口放出。
铁矿石中不还原的杂质和石灰石等熔剂结合生成炉渣,从渣口排出。
产生的煤气从炉顶导出,经除尘后,作为热风炉、加热炉、焦炉、锅炉等的燃料。
1.2高炉炼铁工艺
生铁的冶炼虽原理相同,但由于方法不同、冶炼设备不同,所以工艺流程也不同。
下而分别简单予以介绍。
高炉生产是连续进行的。
一代髙炉(从开炉到大修停炉为一代)能连续生产几年到十几年。
生产时,从炉顶(一般炉顶是由料种与料斗组成,现代化髙炉是钟阀炉顶和无料钟炉顶)不断地装入铁矿石、焦炭、熔剂,从髙炉下部的风口吹进热风(1000-1300摄氏度),喷入油、煤或天然气等燃料。
装入高炉中的铁矿石,主要是铁和氧的化合物。
在髙温下,焦炭中和喷吹物中的碳及碳燃饶生成的一氧化碳将铁矿石中的氧夺取出来,得到铁,这个过程叫做还原。
铁矿石通过还原反应炼出生铁,铁水从出铁口放岀。
铁矿石中的脉石、焦炭及喷吹物中的灰分与加入炉内的石灰石等熔剂结合生成炉渣,从岀铁口和岀渣口分别排出。
煤气从炉顶导出,经除尘后,作为工业用煤气。
现代化髙炉还可以利用炉顶的髙压,用导岀的部分煤气发电。
生铁是髙炉产品(指高炉冶炼生铁),而髙炉的产品不只是生铁,还有锚铁等,属于铁合金产品。
镭铁高炉不参加炼铁高炉各种指标的计算。
高炉炼铁过程中还产生副产品水渣、矿渣棉和髙炉煤气等。
1.3高炉炼铁的特点
规模大,不论是世界其它国家还是中国,髙炉的容积在不断扩大,如我国大型钢铁厂的髙炉已达到4063立方米,日产生铁超过10000吨,炉渣4000多吨,日耗焦4000多吨。
目前国内单一性生铁厂家,髙炉容积也已达到500左右立方米,但多数仍维持在100-300
立方米之间,甚至仍存在100立方米以下的高耗能高污染的小高炉,英产品质量参差不齐,公布分散,不具有期规模性,更不能与国际上的钢铁厂相比。
1.4高炉炼铁的原料
高炉炼铁用的原料主要由铁矿石、燃料(焦炭)和熔剂(石灰石)三部分组成。
通常,冶炼1吨生铁需要1.5-2.0吨铁矿石,0.4-0.6吨焦炭,0.2-0.4吨熔剂,总计需要2-3吨原料。
为了保证髙炉生产的连续性,要求有足够数量的原料供应。
1.5高炉的简史和近况
早期高炉使用木炭或煤作燃料,18世纪改用焦炭,19世纪中叶改冷风为热风(见冶金史)。
20世纪初高炉使用煤气内姻机式和蒸汽涡轮式鼓风机后,高炉炼铁得到迅速发展。
20世纪初美国的大型高炉日产生铁量达450吨,焦比1000公斤/吨生铁左右。
70年代初,日本建成4197立方米高炉,日产生铁超过1万吨,燃料比低于500公斤腕生铁。
中国在淸朝末年开始发展现代钢铁工业。
1890年开始筹建汉阳铁厂,1号髙炉(248米,日产铁100吨)于1894年5月投产。
1908年组成包括大冶铁矿和萍乡煤矿的汉冶萍公司。
1980年,中国髙炉总容积约8万立方米,英中1000米以上的26座。
1980年全国产铁3802万吨,居世界第四位。
1-6高炉的结构及工作原理
横断面为圆形的炼铁竖炉。
用钢板作炉壳,壳内砌耐火砖内衬。
高炉本体自上而下分为炉喉、炉身、炉腰、炉腹、炉缸5部分。
由于高炉炼铁技术经济指标良好,工艺简单,生产量大,劳动生产效率高,能耗低等优点,故这种方法生产的铁占世界铁总产量的绝大部分。
高炉生产时从炉顶装入铁矿石、焦炭、造渣用熔剂(石灰石),从位于炉子下部沿炉周的风口吹入经预热的空气。
在高温下焦炭(有的高炉也喷吹煤粉、重油、天然气等辅助燃料)中的碳同鼓入空气中的氧燃烧生成的一氧化碳,在炉内上升过程中除去铁矿石中的氧、硫、磷,还原得到铁。
炼出的铁水从铁口放出。
铁矿石中未还原的杂质(主要为脉石SiO2)和石灰石等熔剂结合生成炉渣(主要为CaSiO3等),从渣口排出。
产生的煤气从炉顶排出,经除尘后,作为热风炉、加热炉、焦炉、锅炉等的燃料。
高炉冶炼的主要产品是生铁,还有副产高炉渣和高炉煤气。
第二章高炉炉腹温度自动化控制的实现.
2.1高炉的结构组成
现代化高炉广泛使用焊接的钢板炉壳,只有极少数最小的土高炉才用钢箍加固的砖壳。
炉壳的作用是固定冷却设备,保证高炉砌体牢固,密封炉体,有的还承受炉顶载荷。
炉壳除承受巨大的重力外,还要承受热应力和内部的煤气压力,有时要抵抗崩料、坐料其至可能发生的煤气爆炸的突然冲击,因此要有足够的强度。
炉壳外形尺寸应与高炉内型、炉体各部厚度、冷却设备结构形式相适应。
图2.1温度与空气燃料构成的串级比值控制系统工艺管道图(visi。
绘制)
(燃空比为K1/K2)
(1)炉喉:
高炉本体的最上部分,呈圆筒形。
炉喉既是炉料的加入口,也是煤气的导出口。
它对炉料和煤气的上部分布起控制和调节作用。
(2)炉身:
高炉铁矿石间接还原的主要区域,呈圆锥台简称圆台形,曲上向下逐渐扩大,用以使炉料在遇热发生体积膨胀后不致形成料拱,并减小炉料下降阻找力。
炉身角的大小对炉料下降和煤气流分布有很大影响。
(3)炉腰:
高炉直径最大的部位。
它使炉身和炉腹得以合理过渡。
山于在炉腰部位有炉渣形成,并且粘稠的初成渣会使炉料透气性恶化,为减小煤气流的阻力,在渣量大时可适当扩大炉腰直径,但仍要使它和其他部位尺寸保持合适的比例关系,比值以取上限为宜。
炉腰高度对高炉冶炼过程影响不很显著,一般只在很小范围内变动。
(4)炉腹:
高炉熔化和造渣的主要区段,呈倒锥台形。
为适应炉料熔化后体积收缩的特点,其直径自上而下逐渐缩小,形成一定的炉腹角。
炉腹的存在,使燃烧带处于合适位置,有利于气流均匀分布。
炉腹高度随高炉容积大小而定,但不能过高或过低,一般为3.0~3.6m。
炉腹角一般为7旷82;过大,不利于煤气流分布;过小,则不利于炉料顺行。
2.2炉腹温度自动控制系统
炉腹温度自动控制系统是一个炉腹温度与冷风流量够成的一个串级控制系统,其实现思想是,通过热电偶测量炉膛内温度作为炉温控制器的输入参数并与冷风流量参数通过计算机求偏差、再经过PID调节后将其信号输出作为t调节阀执行机构的控制信号。
系统中尽管有两个调节器,但他们作用各不相同。
主调节器具有自己独立的设定值,一般由工艺设定,它是一个定值,因此,主环是一个定制控制系统。
而副调节器设定值是山主调节器的输出提供的,它随主调节器输出变化而变化,因此副调节器是一个随动控制。
图2.2」炉膛温度与燃气流量构成的一个串级控制系统框图(visio绘制)
2.3氮氧流量混合控制系统系统
氮氧双闭环控制系统是山氮气流量和氧气流量构成的双闭环比值控制系统,双闭环比值控制系统中的两个控制回路是通过比值器发生联系的。
这种系统调整负荷比较方便,只需缓慢改变祝流量控制回路的给定值,从流量就可以自动跟踪变化,从而保持系
氧气
2.3.1氮气与氧气流量构成的一个双闭环控制系统工艺图(visio绘制)
2.3.2氮气与氧气流量构成的一个双闭环控制系统框图(visio绘制)
2・4阀门开闭形式、控制器正反作用及调节规律
为了确保生产安全,燃料和助燃空气应选用气开阀,即保证在出现安全故障时燃料和助燃空气调节阀阀门处于关闭状态。
山过程控制原理框图可知,温度和燃料控制器均选用反作用调节。
工艺上对串级控制系统要求比较高,主变量不允许存在余差,而对副变量的要求一般不是很严格,允许存在波动和余差。
因为维持副变量的稳定并不是LI的,设置副变量只是在于保证和提高主变量的控制作用。
而从审级控系统的结构上,主环是一个定值系统,主控制器起着定值控制作用,而本设计主控制器控制的是温度这一通道容积滞后较大的对象,所以主控制器采取PID调节方式。
副环是一个随动控制系统,为了快速跟踪干扰信号,控制器不需要带积分作用,因为积分滞后会使跟踪变缓,所以副控制器选
用比例(P)调节规律即可。
值得注意的是,在实际生产过程中为了保护调节阀门,保证其使用寿命,应该避免控制器的输出过大或过于频繁,希望被测参数在一定范围变化时,输出不变,只有在偏离了这个范围时才按PID规律调节,即温度控制器的给定值不是一个定值,而是一个范围值,当温度差值处于某个范圉时控制器不会发出调节信号,调节阀不动作,这种调节方式就是带死区的PID算法。
♦调节阀:
单座直通阀气开型
采样周期:
15〜20s
♦主控制器:
反作用PID调节
2.5控制系统克服干扰的功能分析
当燃料突然增大,必然将使炉膛温度升高,但是由于炉膛具有一定的容量,干扰的影响滞后,也就是说燃料流量的变化导致炉膛温度改变需要一定的时间,温度控制器的偏差信号仍然为零,这样温度变送器的输出暂时也不会变化。
可是当燃料流量变化的同时流量变送器马上就会检测到,并将其放大后送给流量控制器,但是流量控制器所接收到的给定信号没有变化,测量信号的增大将使它产生正偏差,山于流量控制器釆用反作用的,它的输出将减小,乂由于调节阀是气开式的,就会使燃料阀门关小一些,这样就减小了燃料的输出,山于调节阀动作需要一定的时间,温度变化将会在炉膛内反应出来,被热电偶检测到,随着温度上升,温度控制器将产生一个正偏差,控制器的反作用同样会使输出减小,流量控制器将进一步对调节阀进行控制,直至温度值重新返回到设定值。
可见副回路起到“粗调”而主回路起到“精调”的作用。
2.6测量仪表选型及安全防爆
山于炉膛温度较高,预热段工作温度为780°C>加热段工作温度为1320°C°、均热段工作温度为1280。
。
所以测温元件应选取S型热电偶进行温度检测,原理图可知预热段、加热段、均热锻共需8个S型热电偶。
1热电偶参数:
型号:
钳链10—釦型
分度号:
S型
测温范围:
长期:
0—1300°C短期1600°C
等级:
III
允许温差:
±0.25%t
偶丝直径:
0.5mm
传送信号:
4-20mA电信号(配显示仪表)
补偿导线:
SC型铜一铜線0.6型补偿导线
图2.4釦链型热电偶
燃气总管流量的检测采用涡轮流量讣,助燃空气流量检测釆用节流孔板+变送器的检测方式。
2涡轮流量计参数:
公称口径:
DN4—DN200
精度等级:
±0.5级
防爆等级:
ExdIIBT4
连接方式:
法兰连接
远传显示:
4—20mA电流(配显示仪表)
图2.5涡轮流量汁
3节流式流量讣参数:
节流元件:
孔板
取压方式:
法兰取压
公称直径:
15—2000mm
公称压力:
W40Mpa
工作温度:
-50°CWtW550°C
量程比:
1:
10
精度等级:
0.5
图2.6节流孔板流量计
因为加热炉现场采用煤气这一极易爆炸性危险气体作为燃料,所以防爆控制仪表应选择本质安全型仪表,电路中的电压和电流被限制在一个允许的范围,保证仪表在正常
工作或发生短接和元器件损坏等故障作用时产生的电火花和热效应不至于引起气体混
合物爆炸。
表2・1主要控制回路及现场设备选型和功能表
项
II
位号
川途
硬件
软件功能
名称
数量
1
TI101〜104
均热段炉温检测、调节
S型热电偶
4
显/Js、记录、调节、报警
2
TI201〜204
加热段炉温检测、调节
S型热电偶
4
显刀£、记录、调节、报警
3
TI401〜402
预热段炉温检测
S型热电偶
2
显示、记录
4
TI501〜502
空气预热器前、后烟温检测
K型热电偶
2
显示、记录、控制、报警
5
TICOO1
热风温度控制(放散)
PT100/调节器
1/1
显示、记录、
控制、报警
6
TI601〜604
风机轴承温度
PT100
4
显/Js、记录、
报警
7
HC1O1〜
104
均热段天然气流量调节
孔板/差压变送器/
调节切断阀
2/2/2
显示、记录、调节、切断
8
HC201、
202
加热段天然气流量调节
孔板/差压变送器/
调节切断阀
2/2/2
显示、记录、
调节、切断
9
HC111、
112
均热段天然气流量调节
孔板/差压变送器/调节阀
2/2/2
显示、记录、
调节
10
HC211、
212
加热段空气流量调节
孔板/差压变送器/
调盯阀
2/2/2
显示、记录、调节
11
PIA401
天然气节点压力检测/快
速切断
压力变送器/快速切断阀/调节阀
2/1/1
显不、记录、天然气切断、压力调节
12
PIC5O1、
502
冷热风总管压力检测,调节
压力变送器/执行器
2/2
显示、记录
13
PICO10
炉膛压力调节
微差压变送器/执行器
1/1
显示、记录、
调节、
14
PI601
冷却水总管压力检测
圧力变送器
1
显刀£、记录、
报警
15
PI602
冷却水总管流量
孔板/差压变送器
1/1
显示、记录、
报警
16
PI701
氮气总管压力检测
压力变速器
1
显刀£、记录、
17
PI702
仪表气源压力检测1
压力变送器
1
显示、报警
18
PGA703
仪表气源压力检测2
电接点压力表
1
显示、报警
UVCPV)-01L
里~I畐I
>010PE-011
图2.7燃气流量检测、控制点分布
第三章:
设计体会与心得
本次课程设讣选题选取了上海宝钢集团有限公司钢坯加热生产中使用的高炉炼铁作为研究对象,分析设讣了高炉的温度控制系统这一课题。
从确定选题到初步完稿,我花了两个星期复习所学知识,查阅图书馆资料以及上网搜索有关资料,对于自己亲手完成的设讣感触很多,我不仅将所学过的关于检测仪表和过程控制的知识运用到了工业设计中,还通过自己主动积极的查阅图书馆资源培养了自己勇于面对问题、分析问题和解决问题的能力。
为期两周的课程设计所用到的知识确是两年所学,有的其至是我们自己主动去学习的关于自己相关专业的知识,同时,我还是面临着一些暂时无法解决的,超出自己知识和能力范圉之内的问题,比如过程控制在讣算机完成自动控制这一方面的知识我仅仅知道一些简单的工作原则,不能做到深入的分析和设计,这也将成为我下阶段学习的一个方向,我想只有真正掌握了计算机的自动化控制方面的知识才能在以后的工作中胜任复朵的工作环境,也才能在以后的职场中有晋升的余地。
第四章:
参考文献
【1】孙洪程,翁维勤,魏杰•过程控制系统及工程(第三版)•北京:
化学工业出版社,
2010.7
[2]戚翠芬,张树海•加热炉基础知识与操作•北京:
冶金工业出版社,2005.3
【3】王大克•仪表自动化系统设备选型及维护•上海:
上海宝钢特殊钢事业部,2011.3
[4]戚翠芬•加热炉•北京:
冶金工业出版社,2004.2
【5】王树青,乐嘉谦•自动化与仪表工程师手册•北京:
化学工业出版社,2010.
[6]吴勤勤•控制仪表及装置(第三版)北京:
化学工业出版社,2009.5
【7】武文斐,陈伟鹏,刘中强•冶金加热炉设计与实例•北京:
化学工业出版社,2008.4
【8】李忠虎,李希胜•过程参数检测技术及仪表•北京:
中国计量出版社,2009.1
【9】吴坚,赵英凯,黃玉清•计算机控制系统•武汉:
武汉理工大学出版社,2010年