PVC异型材挤出模具的保养与维修.docx
《PVC异型材挤出模具的保养与维修.docx》由会员分享,可在线阅读,更多相关《PVC异型材挤出模具的保养与维修.docx(26页珍藏版)》请在冰豆网上搜索。
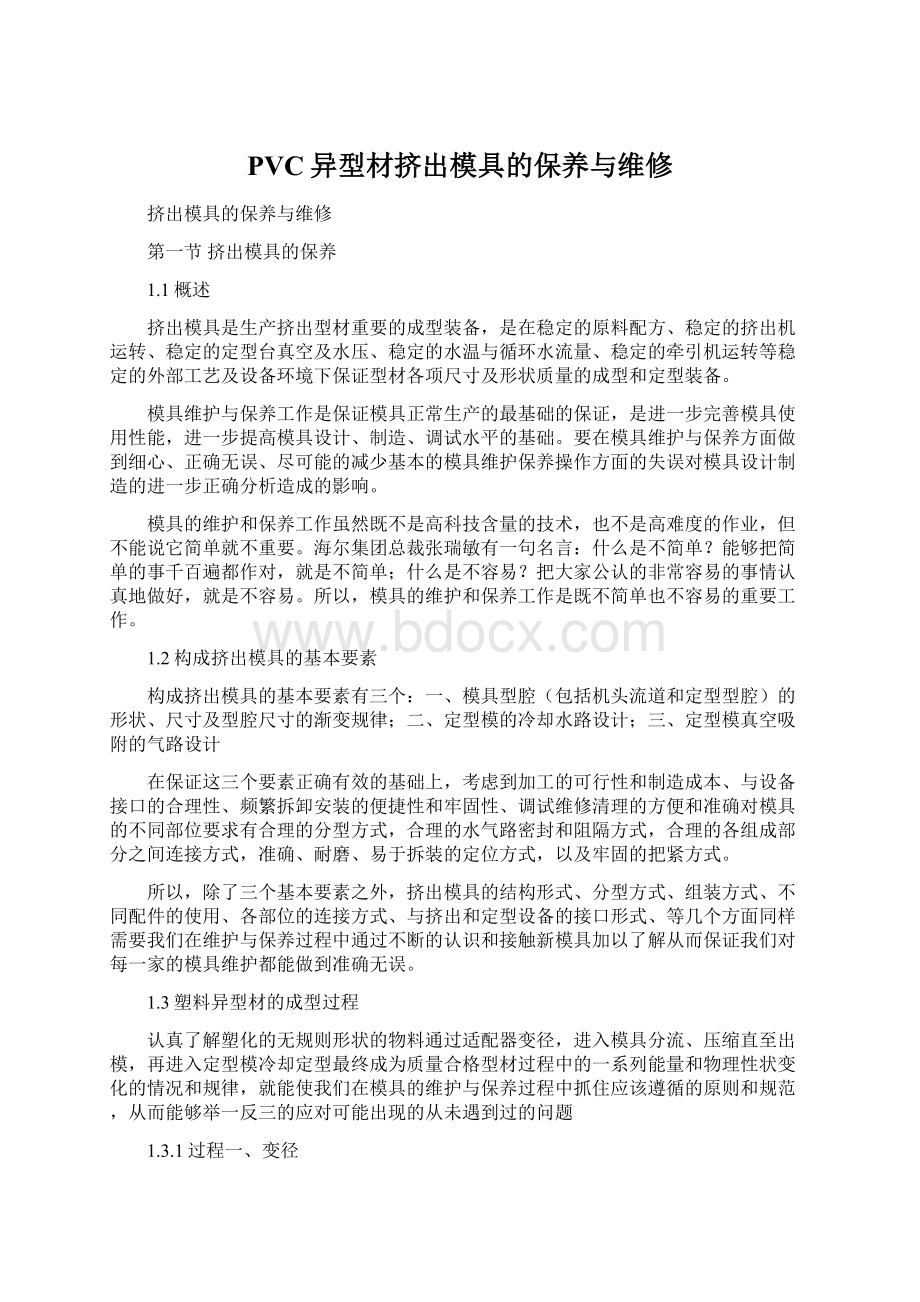
PVC异型材挤出模具的保养与维修
挤出模具的保养与维修
第一节挤出模具的保养
1.1概述
挤出模具是生产挤出型材重要的成型装备,是在稳定的原料配方、稳定的挤出机运转、稳定的定型台真空及水压、稳定的水温与循环水流量、稳定的牵引机运转等稳定的外部工艺及设备环境下保证型材各项尺寸及形状质量的成型和定型装备。
模具维护与保养工作是保证模具正常生产的最基础的保证,是进一步完善模具使用性能,进一步提高模具设计、制造、调试水平的基础。
要在模具维护与保养方面做到细心、正确无误、尽可能的减少基本的模具维护保养操作方面的失误对模具设计制造的进一步正确分析造成的影响。
模具的维护和保养工作虽然既不是高科技含量的技术,也不是高难度的作业,但不能说它简单就不重要。
海尔集团总裁张瑞敏有一句名言:
什么是不简单?
能够把简单的事千百遍都作对,就是不简单;什么是不容易?
把大家公认的非常容易的事情认真地做好,就是不容易。
所以,模具的维护和保养工作是既不简单也不容易的重要工作。
1.2构成挤出模具的基本要素
构成挤出模具的基本要素有三个:
一、模具型腔(包括机头流道和定型型腔)的形状、尺寸及型腔尺寸的渐变规律;二、定型模的冷却水路设计;三、定型模真空吸附的气路设计
在保证这三个要素正确有效的基础上,考虑到加工的可行性和制造成本、与设备接口的合理性、频繁拆卸安装的便捷性和牢固性、调试维修清理的方便和准确对模具的不同部位要求有合理的分型方式,合理的水气路密封和阻隔方式,合理的各组成部分之间连接方式,准确、耐磨、易于拆装的定位方式,以及牢固的把紧方式。
所以,除了三个基本要素之外,挤出模具的结构形式、分型方式、组装方式、不同配件的使用、各部位的连接方式、与挤出和定型设备的接口形式、等几个方面同样需要我们在维护与保养过程中通过不断的认识和接触新模具加以了解从而保证我们对每一家的模具维护都能做到准确无误。
1.3塑料异型材的成型过程
认真了解塑化的无规则形状的物料通过适配器变径,进入模具分流、压缩直至出模,再进入定型模冷却定型最终成为质量合格型材过程中的一系列能量和物理性状变化的情况和规律,就能使我们在模具的维护与保养过程中抓住应该遵循的原则和规范,从而能够举一反三的应对可能出现的从未遇到过的问题
1.3.1过程一、变径
在模具设计过程中,通常模具入口的直径是按照能够达到模具设计挤出量1.25---1.5倍挤出量的挤出机出口直径设计的,所以通常不存在变径的问题。
但是当实际使用的机型过大或过小,亦或当型材的断面尺寸过大或过小导致模具流道设计要求要有过大或过小的入口时,变径的问题就产生了。
知道了变径情况的存在,我们在安装模具时就能够考虑并注意到模具和设备接口之间的匹配性,避免安装过程中造成错误。
1.3.2过程二、分流、压缩、出模
挤出模具机头的主要作用就是把从挤出机挤出的柱状熔体逐渐变成以薄片流体形式互相连接成的型坯流体。
分流和压缩两个过程保证了机头这一主要作用的实现。
熔体在流道由后向前流动的过程中,对流道断面形状的改变具有记忆的特性,这一特性使料坯离模之后与口模的形状存在一定程度上的差异。
差异的大小决定于口模平直段的长度。
平直段越长,差异越小
1.3.3过程三、定型
软化的熔体型坯离开模具挤出以后,其尺寸和形状的最终确定是经过定性模和冷却水箱的逐步冷却作用下最终达到的。
要保证型材具备正确形状和合格尺寸,对于定型模来说要具备以下几个条件:
一、正确的入口形状和尺寸;二、正确的型腔尺寸和尺寸变化规律;三、正确的型腔形状;四、充分的冷却速度;五、充分的吸附能力。
1.4模具的维护和保养的原则
维护是指检查有无损坏,是否需要维修或更换;保养是指清理、除锈、抛光。
最基本的操作是拆卸和安装。
在日常模具维护与保养工作中,如下原则要贯彻始终。
原则一、保证装配以后型腔形状的正确性;
原则二、保证装配以后型腔尺寸的正确性
原则三、保证装配以后挤出方向上型腔的直线度
原则四、保证装配以后挤出方向上各型腔尺寸的正确变化规律
原则五、保证装配以后型腔表面平滑、光亮、不溢料
原则六、保证各装配分形面的水密性、气密性
原则七、保证所有冷却水路畅通
原则八、保证所有气路畅通
原则九、保证机头加热均匀
原则十、保证热电偶测量真实
1.5模具维护与保养的工作范畴
挤出模具维护与保养的范畴包括:
1.5.1模具型腔表面的维护和保养。
●分为机头型腔表面和定型模型腔表面。
主要保证型腔表面无粘附物、平滑、光亮、无尖角、无毛刺、挤出方向上型腔型腔型腔形状的直线度。
●主要操作为抛光。
以能达到清理目的最小材料去除的方式为原则。
具体使用的抛光介质按照去除材料由少到多的顺序包括:
布、600#的纱布、纤维片/棒。
抛光工具以带黄铜棒的平动气动抛光枪为主。
●注意事项:
要绝对避免型腔表面边缘造成倒角、或塌陷等损坏。
1.5.2模具各组成部分装配分型面的保养
●分为机头各板装配表面、定型套各板装配表面、定型套与底座之间的装配表面以及水箱块下表面与水箱底面。
主要保证装配表面无粘附物、平整无突起、边缘无毛刺以及装配表面的平面度要求。
●主要操作:
用油石背平,清理。
在清理过程中,要经常用长刀口尺检测各板装配分型面各个方向上的平面度情况,是否发生弯曲或扭曲等变形。
●注意事项:
要绝对避免型腔表面边缘造成倒角、或塌陷等损坏。
1.5.3模具各组成部件之间定位部件的维护与保养
定位部件主要包括定位销和定位孔。
根据不同的模具组成部分、不同模具制造厂的设计方式,具体形式上又分为柱销、锥销和方键,与之相对应的则是销孔和键槽。
在挤出模具中,定位部件是精度较高且非常重要的组成部分。
●具体的形式如下所示:
格瑞那还对他的定位部件做了偏心的设计,共有5个偏心级别,每个偏心级差为0.1mm。
所以在更换和安装过程中要注意保证其型号和方向与原来一致。
●主要操作:
检查定位部件的定位表面是否清洁,有无损坏或磨损过大,并及时更换型定位部件。
●注意事项:
绝对避免在拆装定位部件过程中损坏定位孔、槽的关键定位表面,一旦损坏很难修复,同时注意在更换前后,定位部件的型号和安装方向都要一致。
1.5.4模具各组成部分之间装配螺栓的维护和保养
●装配螺栓包括机头螺栓和定性模螺栓。
国内外新旧模具均采用内六角普通粗牙型螺栓,区别在于不同的设计方式、不同的部件使用的螺栓长度、公称直径有所不同。
●主要操作:
检查螺栓的规格和型号是否合适,螺纹的工作段是否损坏,内六角沉孔是否损坏,并及时更换新螺栓。
●注意事项:
机头螺栓处于持续高热工作状态下,安装前要在螺纹上涂抹高温润滑油,以保护频繁拆卸的螺纹工作段;安装前要清理螺栓孔无粘附物或杂物;紧固螺栓要力度适当,螺栓孔发生拧入困难时要及时使用丝锥修正(要用三锥)。
1.5.5密封元件的维护和保养
●主要指水路、气路的密封。
●
包括密封圈、密封胶条、密封丝堵和密封闷头。
密封圈主要用于定型套分型面水孔衔接处的水密封。
密封圈的外径和断面圆直径根据所密封的水孔处沉孔的直径和深度相关。
按断面形状分为圆形(大部分的定型套使用)和三角形(TP模具定型套使用)
●注意事项:
密封圈是否合适不只与外径大小有关,与密封圈断面圆的直径也有关系。
如果断面圆直径过大,密封圈与沉孔深度之差δ就会过大,会导致分型面装配不严。
如果断面圆直径过小,与沉孔深度之差δ就会过小甚至出现负值。
保证密封效果但不影响装配的合理δ值应该在0.1~0.2mm之间。
●
密封丝堵主要用于定型套水路和气路端部的密封,型号和规格同密封的气孔和水孔的孔径相关,通常为细牙涂胶螺纹,内六角沉孔,有些带有锥形沉头和密封圈,特殊部位采用分段型丝堵。
●主要操作:
●定期拆卸、清理水路,检查螺纹及内六角沉孔是否损坏并及时更换。
1.5.6冷却水路的维护和保养
不同的模具制造厂设计的冷却水路的供水、排水、和水路的排布方式不同。
但不外乎如下几种形式,
●供水方式上:
◆定型套底座集中供水;
◆个别模板直接供水;
◆小水孔与大水孔同时供水。
●排水方式上:
◆大水孔集中出水;
◆小水孔单独出水。
●水路排布方式上:
◆大的定型表面上的蛇形水路排布方式;
◆直行水路的排布方式。
◆主要操作:
清理水路中的杂物,保证水路走水的畅通。
完整的水路包括供水段、冷却工作段和排水段。
●注意事项:
判断水路是否畅通的标准是:
供水段畅通+冷却工作段畅通+排水段畅=>通水路畅通
●格瑞那的蛇形水路依靠可方便拆卸的水堵串进行分隔,从而实现水路的蛇形排布。
一般各节定型套水堵块的间距有差异,从标识上可分为B1、B2,C1、C2,D1、D2(四节定型套时使用)。
在拆卸、清理、安装时注意水堵串的表示要对应以及安装方向要正确。
●国产模具定型套蛇形水路采用垂直打孔+堵块封死的方式实现,清理时要把侧面的丝堵拆下,用高压气体将水孔中的水垢、锈蚀、及杂物清理干净。
1.5.7真空气路的维护和保养
●虽然各家模具厂的气路设计各有不同,但总体来说气路都由以下几个部分组成:
气室、气孔、气槽。
●虽然气路的主要作用在于使型坯外表面与定型套型腔表面之间形成真空气室已达到型坯外表面与型腔表面密切贴附的作用,但同时也起到了带走高热型坯表面的硬化析出并容纳析出物的作用,所以经过长期生产的模具的气路会被析出物所填满。
●主要操作:
清理干净气路各个部分,包括气室、气孔、气槽内的析出物和杂物。
●注意事项:
经过长期磨损后,原来倒圆的气槽棱边会再次出现尖锐的棱角,为防止刮伤型材表面,需要再一次对它使用纤维片倒角和抛光,但倒角不宜过大,一般以不刮手为宜。
1.5.8冷却水箱的维护与保养
●主要操作:
◆保证水箱底面清洁,
◆检查密封胶条的密封效果并及时更换老化失效的胶条,
◆用胶水稳固脱落的胶条,
◆修复变形的水箱盖板铰链,
◆修复并密封断裂或破碎的有机玻璃板主体,
◆检查水箱配件是否完整并及时更换补充。
1.5.9模具配件的维护与保养
●模具配件主要包括机头加热板、热电偶座、水汽接头、排水接头及导、排水管等。
●机头加热板的安装要做到加热层与模头外形面密切贴实,螺栓要齐全,加热板规格和孔位要与机头一致。
●要保证热电偶孔底部清洁无杂物。
●水汽接头的规格要合适,安装时要确保不干涉、密封性好。
MA共挤模具共挤流道的维护和保养
●
PMMA共挤流道及接口件示意图
共挤模具的维护同样也要遵循维护原则。
只不过由于所成型的材料特性同PVC差异很大(主要表现为黏度更低,流动性更好),所以对流道的表面光洁度要求更高,同时由于供给流道的间隙很小(一般小于0.25mm),所以对杂质以及粘附物的反应也更敏感。
●在实际生产过程中,共挤层厚度不均和共挤层露白是PMMA共挤型材经常出现的质量问题。
一般来讲出现了这类问题都要以清理抛光为主,对流道的尺寸维修为辅,多数情况下经过仔细的检查和清理、抛光都能达到改善问题的效果。
●维修的次数越多,流道的实际尺寸越不规则,对不同材料流动性的差异反应越敏感,进而导致维修的频率加大,最后的结果就是无法恢复。
PMMA共挤型材生产的质量问题可以分为两个方面:
一、青白主体部分:
青白主体部分的问题主要包括壁薄、配合尺寸不好、波浪、内腔小、功能槽尺寸不好、焊接尺寸不好、喘气等问题。
这些问题是随着模具使用延长米的增加导致模腔磨损程度不断加大而产生的,与普通全色型材的磨损规律相近。
当模具的磨损程度没有达到一定量的时候,这些问题对生产的连续稳定性的影响不是致命的;但当模具的磨损程度超过一定量的时候,维修难度会急剧增大。
所以对待这类问题需要通过定期适度维修来解决。
二、PMMA共挤表面部分:
概括来说(个别模具会有具体的情况)共挤表面的问题主要有:
表面划线、表面凹陷、表面亮暗线、色料析出痕、局部露白、覆盖不均匀、共挤层厚度不均匀等等。
这些问题对生产的连续和稳定都是致命的,往往必须要停机进行多次处理才会得到改善。
引起这些问题的因素主要有以下几点:
●共挤层原料颜色的改变
大量的实际经验表明,不同颜色的PMMA共挤原料的流动性是不一样的。
比如从苔绿换为深褐的时候,共挤层的不均匀性加大,局部出料特别快;而换为烟灰色的时候局部出料特别慢。
这种巨大的差异也可以从平衡工艺参数的差别来发现,比如共挤料颜色为烟灰时与共挤料颜色为深褐时辅机的螺杆转数可相差一倍,螺筒区的温度会相差5度,模具区的温度会相差十度。
不同颜色的PMMA共挤原料流动性的差异对于共挤面断面尺寸小的模具的影响相对较小,往往可以通过平衡工艺参数来进行改善;而对共挤面断面尺寸大的型模具影响更大,比如PP150、SF104A、FR104A等,往往很难通过平衡工艺参数来完全改善,必须依靠频繁的修模来解决。
由于大部分PMMA共挤模具经历去年一年的生产后,共挤流道尺寸的损耗已经有了一定程度的累积,流道尺寸和形状一定程度上变得不规则,这就更加加剧了各种颜色PMMA共挤料之间出料速度的差异,使得自2009年度生产以来通过调整工艺参数来平衡各色料之间差异性的难度加大,通过维修手段来调整出料速度变得更加频繁,使得共挤流道尺寸和形状变得更加不规则。
这是一个恶性循环的过程,随着维修频率的增加,共挤流道尺寸和形状的不规则性就会越剧烈,进一步累积的结果就是:
维修难度更大,普通的维修手段最终不能解决共挤出料不均的问题而导致模具报废。
比如SF104A模具的共挤流道经过多次维修之后,流道间隙最大处和最小处的值已经相差150%以上。
●主体青白料流动性的改变
引起主体青白料流动性变化的因素有很多,主要有PVC原料的改变、配方组分的改变、干混料中各组分分散的不均匀性、挤出机控制系统的波动等等。
主体青白料流动性的改变会直接导致共挤断面青白料出料速度不均匀,也就是局部出料会很快或很慢,那么在这一点PMMA共挤料出料速度也会随之变快或变慢,这样在表面覆盖的均匀性上就会出现差异。
●PMMA物料析出
在生产中,由于PMMA析出引起的表面状态问题凸显出来。
PMMA析出含于共挤层内,通过光线反射和折射的差异能清晰的表现出来。
这种析出具有不规则性,在表面上的位置不确定,而且时断时续,非常难解。
●冷却水中的杂质
目前冷却水中存在大量的粒径在0.2mm以下,类似SiO2硬质的杂质,普通的过滤装置不能去除。
这类杂质对于全色PVC型材表面状态的影响很小,但对于表面更光亮的PMMA共挤表面来说就极其明显。
第二节挤出模具维修技术
2.1认识模具
挤出模具的维修不同于挤出模具的调试。
模具的维修是一个大的范畴。
它主要针对产品生产过程中出现的质量问题,在准确详细分析一系列影响因素的基础上,以维护为主,强调保障模具的正常使用寿命的解决问题的方法。
它是建立在确定的模具调试结果基础之上的后续维护手段。
作为挤出模具的使用单位,模具供应的来源是多方面的,各个模具供应商的技术发展情况又是日新月异的。
因此,我们要清楚的了解所使用的模具,知道其设计、制造中有哪些优缺点,搞清楚哪些部位我们可以加以利用、加以修改和调整及其范围,进而达到控制产品质量的目的。
这是得出有效维修方法的重要前提。
接下来,从以下几个方面来说明通过哪些关键要素去清楚地了解模具的特点。
2.1.1机头结构形式
1.流道结构形式
流道结构形式包括以下几个方面:
1)
主腔壁流道各段长度、间隙、分流锥角、压缩角、压缩比。
如图2.1.1。
挤出模具设计技术发展到现在,各制造厂的设计参数已基本趋于一致。
虽然如此还是存在一些细微差别,比如在各段的长度分配上,有的公司偏向于长的
成型段流道,而有的公司倾向于短的成型段流道;有的公司倾向于短的压缩流道和相对较小的压缩比,而有的公司则倾向于长的压缩流道和较小的压缩角。
这些差异对于模具的使用性能有多大的影响很难用直接的统计数据进行分析和证明,但流道的设计者们始终都在致力于设计出更能保证出料稳定的流道结构形式。
2)爪钩体流道的结构形式。
抓钩体是指在型材断面上伸出于型材腔壁主体以外的,在型材使用过程中具有一定功能作用的型材断面结构。
抓钩体流道同样具备分流、过渡、压缩、成型各典型段,只是它的各段长度是在主腔壁流道确定后的基础上设计出来的,某种程度上受到了主体流道的参数的制约。
由于一般爪钩体都具有特定的功能形状,所以讨论爪钩体流道的特点更加侧重于其流道各段的断面形状特点。
例如图2.1.2图一的形式,而有的厂家则设计成图二或图三的形式。
还有2.1.2中例二过渡段流道截面形状也有可能设计成2.1.2中例四过渡段流道截面形状可能设计成
以上所列举的情况只是实际工作中所遇到的部分情况,但仍然具有一定的代表性。
由于熔体具有一定的机械物理特性,所以不同的流道形状对产品成型过程的质量影响是显着的,具体如何影响需要我们在实际工作中不断积累和体会。
3)支撑筋分布
支撑筋是连接型芯和支架板的必要结构。
支撑筋的设计参数包括支撑筋的厚度、长度、分布情况、设置的位置等等。
由于熔体在机头内从后向前流动过程中要被支撑筋分割后再融合,所以,恰当的选择支撑筋的设计参数对于减少产品成型时出现质量问题有关键作用。
下面列举了一些典型的支撑筋排布和设置方式。
4)导流翅设置、长度及厚度。
导流翅是在流道结构中出现的厚度较薄,深入到流体内部,用于分割、导向料流的结构。
具体形式如图2.1.3图一、图四、图六中所示。
在近几年挤出模具设计发展过程中,设计者渐渐认识到恰当的安置导流翅对于提高出料的稳定性、避免出现相关的质量问题有很大作用。
5)融合段长度、宽度、圆角。
融合段流道是指在口模流道中,主腔壁流道之间、内筋流道与主腔壁流道之间、爪钩体流道与主腔壁流道之间的融合连接处的流道。
为了保证两股流道之间有足够的融合强度,融合段的长度、宽度、圆角以及在特殊要求下采用的特殊流道截面形状都是应该合理设定的参数。
2.机头各板之间的定位方式。
机头各板之间主要以成对的柱销或锥销来定位。
如图所示的双头定位柱销、锥形定位销以及与锥形定位销配合使用的锥弹簧垫等。
还有1.5.3节第四种定位形式所示的销套等。
一般来讲从简单的柱销定位到锥弹簧垫—锥销以及柱销柱销套定位方式的过渡,实际上是考虑到了人们在对模具反复拆装使用过程中定位结构的磨损和高定位精度给拆装带来的种种麻烦后采取的一系列改进措施。
这些改进对于提高模具的使用寿命、保证模具使用过程中的性能都是有着重要作用和价值的。
定位结构是保证模具装配后流道各项参数正确的重要部分。
在实际工作中经常遇到由于定位的准确或正确或精度问题而影响机头出料稳定性的情况。
机头各板之间的连接紧固方式。
虽然机头各板的连接紧固方式总体上来说都是采用内六角螺栓紧固连接,但在连接紧固模板的数量分配上的区别还是能体现出设计者对模具使用性能的理解水平的差距。
同时,主紧固螺栓的长度、紧固点设置的不合适还会造成板间溢料等设计事故。
2.1.2定型模的结构形式
定型模的结构形式主要包括:
真空吸附结构、冷却定型结构、连接与把紧结构、定位结构、定型模长度和节数。
1.完整的真空吸附结构包括吸附气路的位置、吸附气路形式、气路与设备的接口等
涉及到的设计参数有:
气槽的深度和宽度、气孔的孔径、气室的深度和宽度、气孔与气槽连接处的伞端口径以及在挤出方向上一组完整吸附结构排布的数量和间距等等。
这些参数对于产品成型的过程和产品质量的稳定程度都有重要的影响。
同时也影响或决定着连续稳定产生质量合格产品的的生产周期的长短。
在维修过程中,有些时候我们面对的可能是解决连续生产的稳定性或周期短的问题,了解了真空吸附结构的特点结合经验上对不同结构形式的优缺点的认识就可能给我们解决这类问题提供依据。
冷却水路结构
完整的冷却水路结构包括供水口(与设备的接口)、供水水路、冷却水路、出水水路、出水口以及密封部件等。
涉及到的设计参数主要包括,各水路段的孔径、第一组冷却水路距离定型模入口端的距离、各组冷却水路间的排布间距、冷却水的流动方式、供水方式、出水方式等方面。
图2.1.5供水端水路结构示意图
供水端冷却水路结构如图2.1.5所示。
随着挤出模具设计技术的发展,越来越多的厂家采用了统一入水口供水的设计形式。
实践表明统一入水口的做法有利于集中优化处理各水孔的位置、排布,让每个冷却水路的入水点均靠前,使冷却效果更好。
出水端冷却水路结构形式如图2.1.6所示
图2.1.6出水端水路结构示意图
由于在出水端采用了统一进水口的形式,为了保证不同孔径的冷却水路中水流速度都能满足产品定型所需要的冷却效率,避免不同水孔之间出水量相互影响,在出水端采用各自独立出水的形式。
有的公司还会在大水孔出水处设计缩小孔径的节流件,从而保证大水孔中的水压足以满足冷却水在水孔中流动时充满孔的截面,保证大水孔冷却效果的同时,也能尽可能提高小水孔的水流压力,提高小水孔的冷却效率。
由于型腔周围的空间有限,冷却水路的设计一经确定,在后续维修过程中便很难改变,任何试图提高冷却效率的改进措施都使人感觉到力不从心。
然而,通过提高定型台冷却水泵的功率,提高供水的压力,从设计基础上可以提高定型模的冷却效率。
2.定型模的连接与把紧形式
定型模的连接与把紧形式包括各模板之间、定型模与底座之间、定型模与定型模之间的连接与把紧形式。
在实际维修工作中注意这些方面的特点能够帮助我们避免在工作中的装配上的失误。
3.定位方式
定型模的定位方式和机头模板之间的定位一样,决定着装配以后的型腔形状、尺寸以及各项设计参数的正确性。
主要包括各模板之间、定型模与底座之间、定型模与定型模之间的定位。
具体形式如1.5.3节介绍的内容。
4.定型模长度、节数
在挤出模具的设计参数中定型模的长度、节数是至关重要的,直接关系到挤出模具的设计产能、冷却效率和使用稳定性。
不同厂家在这一方面的处理上都旨在体现自家的设计特点。
2.1.3水箱的结构形式
冷却水箱的结构形式主要体现在水箱的结构形式对冷却水的流动方式的控制能力上。
主要参数包括入口处的结构形式、水箱板的厚度、水箱板的间距、遮流板间距、抽吸口的数量、抽吸口的位置、进气口的位置、水箱壁上的导流槽等等。
众多参数的设定的目的都是为了保证产品在水箱中得到均匀、充分、高效的冷却。
2.1.4与设备的安装接口结构形式
1.机头与挤出机接口结构形式
机头与挤出机接口的结构形式接近于标准化。
都是靠连接体的内圆面和过渡套的外圆面来保证定位关系的。
值得注意的是,为了改善熔体的塑化情况,个别厂家改变了过渡环或多孔板的结构和构造。
有些形式的多孔板对熔体的流动情况改善作用非常大。
2.定型模与定型台接口结构形式
一般不要求精确定位,采用螺栓进行连接、紧固。
有些厂家将定型模设计成浮动的,即只限制其在挤出单方向上的自由度。
与真空泵和水泵的接口普遍采用快速接头的方式。
值得一提的是,解决实际生产问题时会遇到很多意想不到的情况。
比如定型台的供水管或真空管有些时候数量不能满足定型模接口的需要,有时会遇到一些假水汽管干扰我们等等。
2.2型材的结构及尺寸分析
2.2.1结构分析
型材的结构分析主要是从型材的外形特点、结构元素、主腔壁厚度几个方面进行。
从影响成型的角度来考虑外形特点可分为:
对称型、旋转对称型、单侧对称型、无腔室型、直角三角形、四边形、L型等等。
对称型的型材把持点分布也对称,在维修的过程中要把握住均衡的要点。
比如SE76等中挺型材;旋转对称型的型材把持点的分布也是旋转对称的,容易导致型材的扭曲变形,所以在维修时要注意在把持力矩的相反方向维持反方向的力矩加以平衡防止产品变形;直角三角形的型材容易发生斜边下滑的现象,在维修时要注意持斜边成型的把持点位置以及斜边补偿曲率;L型的型材在成型的过程中一出现直角变锐角的情况,维修时要注意保持相反趋势成对把持点的力矩