表面处理电泳漆.docx
《表面处理电泳漆.docx》由会员分享,可在线阅读,更多相关《表面处理电泳漆.docx(15页珍藏版)》请在冰豆网上搜索。
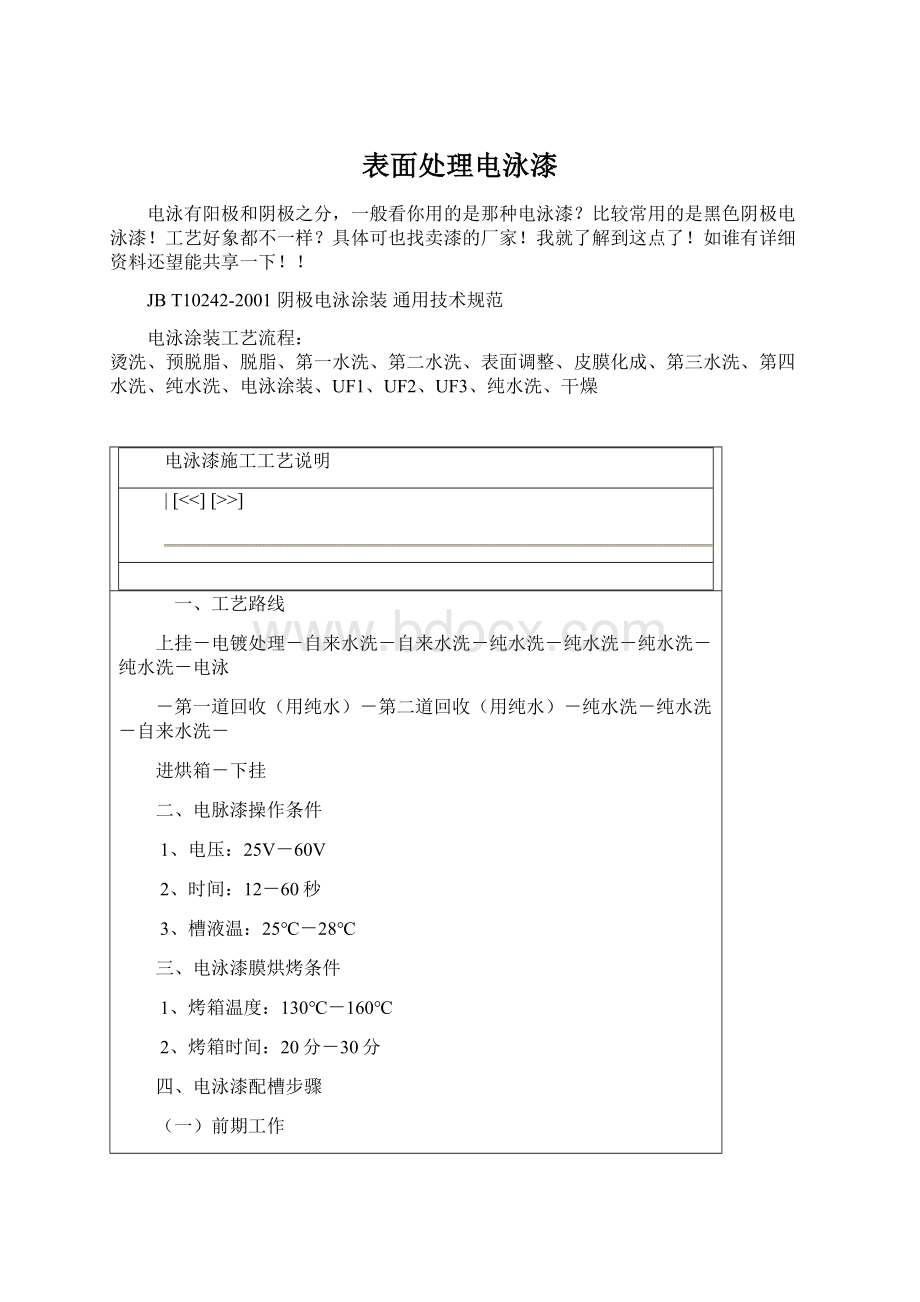
表面处理电泳漆
电泳有阳极和阴极之分,一般看你用的是那种电泳漆?
比较常用的是黑色阴极电泳漆!
工艺好象都不一样?
具体可也找卖漆的厂家!
我就了解到这点了!
如谁有详细资料还望能共享一下!
!
JBT10242-2001阴极电泳涂装通用技术规范
电泳涂装工艺流程:
烫洗、预脱脂、脱脂、第一水洗、第二水洗、表面调整、皮膜化成、第三水洗、第四水洗、纯水洗、电泳涂装、UF1、UF2、UF3、纯水洗、干燥
电泳漆施工工艺说明
|[<<][>>]
一、工艺路线
上挂-电镀处理-自来水洗-自来水洗-纯水洗-纯水洗-纯水洗-纯水洗-电泳
-第一道回收(用纯水)-第二道回收(用纯水)-纯水洗-纯水洗-自来水洗-
进烘箱-下挂
二、电脉漆操作条件
1、电压:
25V-60V
2、时间:
12-60秒
3、槽液温:
25℃-28℃
三、电泳漆膜烘烤条件
1、烤箱温度:
130℃-160℃
2、烤箱时间:
20分-30分
四、电泳漆配槽步骤
(一)前期工作
1、先用自来水将电泳槽稍微清洗,除去一产电泳槽时所产生的PVC及PP碎屑。
2、再用水清洗,加入少许NaOH烧碱,以除去槽内表面之油污,清洗干净,倒
去污水。
3、再用自来水彻底清洗2-3次,并开动过滤泵的检查各管路是否漏液。
检查
电机正转还是反转。
4、再用纯水清洗两次、干净、开动搅拌机。
5、盖上盖子,等待开缸。
(二)配制有色电脉步骤(以配100升槽各色浆及漆比例)
1、取调色漆0.5升或开一小桶内。
2、取1升色浆边搅拌边缓慢加入色浆,用电动搅拌机操作搅拌,搅拌充分30分钟。
3、将上述搅拌混合均匀之色浆移动至易一大塑料桶中。
4、取20升032#漆在大搅拌机搅拌下,加入上述之塑料桶中,充分搅拌1小时后,
移入电泳槽。
5、重复1-4步骤。
6、将所配有色电泳漆全部混合液都在电泳槽后。
7、再将大搅拌机移至电泳槽中,充分搅拌电泳电泳漆半小时。
8、在强力搅拌下,缓慢加适应症纯水<要求电导率<5μs>加时要注意缓慢,
间歇性。
9、性水位加至溢流槽位时,开支过滤泵循环。
10、性水位加至溢流槽位时,开支过滤泵循环。
11、第二试泳。
12、再配第二槽重复1-10工序。
五、电泳补加
(一)漆补加
1、准备一专用加料桶(20公升)
2、用电泳漆浓缩液2升置入加料桶中,开动小搅拌机。
3、从电泳槽内取工作液若10升,在边搅拌情况下加入上述浓缩液中,充分搅拌
30分钟,混合均匀。
4、将调配好加料补加入电泳槽内溢流槽。
(二)色浆之被加
1、取0.5升调色漆于配料桶,开动小搅拌机。
2、取色浆所需量,边搅拌边加入上述调色漆中,充分搅拌30分钟。
3、取工作槽中工作液10升,在边搅拌加补加入中,充分混合后,加入工作槽中,
溢流槽。
六、注意事项
(一)设备方面
1、注意管路接是否漏
2、阴、阳极是否接反
3、电机不要空转
(二)工艺方面
1、纯水水质要求<5μs以下
2、槽液液温控制在25℃-26℃之内(用冰或冷动机)
3、进槽要清洗干净,不要将酸、碱带入槽中。
4、电泳漆要晾干然后时烘箱,烤温不要升温太快。
电泳涂装设备及涂装方法
电泳涂装(electro-coating)是利用外加电场使悬浮于电泳液中的颜料和树脂等微粒定向迁移并沉积于电极之一的基底表面的涂装方法。
电泳涂装的原理发明于是20世纪30年代末,但开发这一技术并获得工业应用是在1963年以后,电泳涂装是近30年来发展起来的一种特殊涂膜形成方法,是对水性涂料最具有实际意义的施工工艺。
具有水溶性、无毒、易于自动化控制等特点,迅速在汽车、建材、五金、家电等行业得到广泛的应用。
电泳涂装是把工件和对应的电极放入水溶性涂料中,接上电源后,依靠电场所产生的物理化学作用,使涂料中的树脂、颜填料在以被涂物为电极的表面上均匀析出沉积形成不溶于水的漆膜的一种涂装方法。
电泳涂装是一个极为复杂的电化学反应过程,其中至少包括电泳、电沉积、电渗、电解四个过程。
电泳涂装按沉积性能可分为阳极电泳(工件是阳极,涂料是阴离子型)和阴极电泳(工件是阴极,涂料是阳离子型);按电源可分为直流电泳和交流电泳;按工艺方法又有定电压和定电流法。
目前在工业上较为广泛采用的是直流电源定电压法的阳极电泳。
1-经表面处理后的工件;2-电源;3-工件;4-喷水冲洗;5-槽液过滤;6-沉积槽;7-循环泵
电泳涂装与其他涂装方法相比较,具有下述特点:
(1)采用水溶性涂料,以水为溶解介质,节省了大量有机溶剂,大大降低了大气污染和环境危害,安全卫生,同时避免了火灾的隐患;
(2)涂装效率高,涂料损失小,涂料的利用率可达90%~95%;
(3)涂膜厚度均匀,附着力强,涂装质量好,工件各个部位如内层、凹陷、焊缝等处都能获得均匀、平滑的漆膜,解决了其他涂装方法对复杂形状工件的涂装难题;
(4)生产效率高,施工可实现自动化连续生产,大大提高劳动效率;
(5)设备复杂,投资费用高,耗电量大,其烘干固化要求的温度较高,涂料、涂装的管理复杂,施工条件严格,并需进行废水处理;
(6)只能采用水溶性涂料,在涂装过程中不能改变颜色,涂料贮存过久稳定性不易控制。
一、电泳涂装的设备
电泳涂装的设备是由电泳槽、搅拌装置、涂料过滤装置、温度调节装置、涂料管理装置、直流电源装置、电泳涂装后的水洗装置、超滤装置、烘烤装置、备用罐等组成。
电泳槽槽体的大小及形状需根据工件大小、形状和施工工艺确定。
在保证一定的极间距离条件下,应尽可能设计小些。
槽内装有过滤装置及温度调节装置,以保证漆液一定的温度和除去循环漆液中的杂质和气泡。
搅拌装置可使工作漆液保持均匀一致,多采用循环泵,漆液的循环一般每小时4~6次,当循环泵开动时,槽内漆液液面应均匀翻动。
涂料管理装置的作用在于补充调整涂料成分,控制槽液的PH值,用隔膜电极除去中和剂和用超滤装置排除低分子量成分等。
电泳电源的选择,一般采用直流电源。
整流设备可采用硅整流器或可控硅。
电流的大小与涂料的性质、温度、工作面积、通电方式等有关,一般为30~50A/m2。
水洗装置用于电泳涂装前后工件的冲洗,一般用去离子水,但需加压设备,常用的是一种带螺旋体的淋洗喷嘴。
烘烤装置用来促进电泳涂料的干燥成膜,可采用电阻炉、感应电热炉和红外线烘烤设备。
烘房设计要有预热、加热和后热三段,应根据涂料的品种和工件的情况制订。
二、影响电泳涂装的主要工艺参数
1、电压
电泳涂装采用的是定电压法,设备相对简单,易于控制。
电压对漆膜的影响很大;电压越高,电泳漆膜越厚,对于难以涂装的部位可相应提高涂装能力,缩短施工时间。
但电压过高,会引起漆膜表面粗糙,烘干后易产生“橘皮”现象。
电压过低,电解反应慢,漆膜薄而均匀,泳透力差。
电压的选择由涂料种类和施工要求等确定。
一般情况下,电压与涂料的固体分及漆温成反比,与两极间距成正比。
钢铁表面为40~70V,铝和铝合金表面可采用60~100V,镀锌件采用70~85V。
2、电泳时间
漆膜厚度随着电泳时间的延长而增加,但当漆膜达到一定厚度时,继续延长时间,也不能增加厚度,反而会加剧副反应;反之,电泳时间过短,涂层过薄。
电泳时间应根据所用的电压,在保证涂层质量的条件下,越短越好。
一般工件电泳时间为1至3分钟,大型工件为3至4分钟。
如果被涂物件表面几何形状复杂,可适当提高电压和延长时间。
3、涂料温度
涂料温度高,成膜速率快,但漆膜外观粗糙,还会引起涂料变质;温度低,电沉积量少,成膜慢,涂膜薄而致密。
施工过程中,由于电沉积时部分电能转化成热能,循环系统内机械摩擦产生热量,将导致涂料温度上升。
一般漆液温度控制在某些方面15~30℃。
4、涂料的固体分和颜基比
市售的电泳涂料的固体分一般为50%左右,施工时,需用蒸馏水将涂料固体分控制在10%~15%。
固体含量太低,漆膜的遮盖力不好,颜料易沉淀,涂料的稳定性差。
固体分过高,粘度提高,会造成漆膜粗糙疏松,附着力差。
一般颜基比为1比2左右,高光泽电泳涂料的颜基比可控制在1比4。
由于实际操作中,涂料的颜料量会逐渐下降,必须随时添加颜料分高的涂料来调节。
5、涂料的PH值
电泳涂料的PH值直接影响槽液的稳定性。
PH值过高,新沉积的涂膜会再溶解,漆膜变薄,电泳后冲洗会脱膜。
PH值过低,工件表面光泽不一致,漆液的稳定性不好,已溶解的树脂会析出,漆膜表面粗糙,附着力降低。
一般要求施工过程中,PH值控制在7.5~8.5之间。
在施工工程中,由于连续进行电泳,阳离子的铵化合物在涂料中积蓄,导致PH值的上升。
可采用补加低PH值的原液,更换阴极罩蒸馏水,用离子交换树脂除去铵离子,采用阳极罩等方法降低PH值。
若PH值过低时,可加入乙醇铵来调节。
6、涂料电阻
被涂物件从前一道工序带入电泳槽的杂质离子等引起涂料电阻值的下降,从而导致漆膜出现粗糙不均和针孔等弊病。
在涂装施工中,需对涂料进行净化处理。
为了得到高质量涂膜,可采用阴极罩设备,以除去铵及钙、镁等杂质正离子。
7、工件与阴极间距离
距离近,沉积效率高。
但距离过近,会使漆膜太厚而产生流挂、橘皮等弊病。
一般距离不低于20cm。
对大型而形状复杂的工件,当出现外部已沉积很厚涂膜,而内部涂膜仍较薄时,应在距离阴极较远的部位,增加辅助阴极。
三、电泳涂装的方法及技巧
(1)一般金属表面的电泳涂装,其工艺流程为:
预清理→上线→除油→水洗→除锈→水洗→中和→水洗→磷化→水洗→钝化→电泳涂装→槽上清洗→超滤水洗→烘干→下线。
(2)被涂物的底材及前处理对电泳涂膜有极大影响。
铸件一般采用喷砂或喷丸进行除锈,用棉纱清除工件表面的浮尘,用80#~120#砂纸清除表面残留的钢丸等杂物。
钢铁表面采用除油和除锈处理,对表面要求过高时,进行磷化和钝化表面处理。
黑色金属工件在阳极电泳前必须进行磷化处理,否则漆膜的耐腐蚀性能较差。
磷化处理时,一般选用锌盐磷化膜,厚度约1~2μm,要求磷化膜结晶细而均匀。
(3)在过滤系统中,一般采用一级过滤,过滤器为网袋式结构,孔径为25~75μm。
电泳涂料通过立式泵输送到过滤器进行过滤。
从综合更换周期和漆膜质量等因素考虑,孔径50μm的过滤袋最佳,它不但能满足漆膜的质量要求,而且解决了过滤袋的堵塞问题。
(4)电泳涂装的循环系统循环量的大小,直接影响着槽液的稳定性和漆膜的质量。
加大循环量,槽液的沉淀和气泡减少;但槽液老化加快,能源消耗增加,槽液的稳定性变差。
将槽液的循环次数控制6~8次/h较为理想,不但保证漆膜质量,而且确保槽液的稳定运行。
(5)随着生产时间的延长,阳极隔膜的阻抗会增加,有效的工作电压下降。
因此,生产中应根据电压的损失情况,逐步调高电源的工作电压,以补偿阳极隔膜的电压降。
(6)超滤系统控制工件带入的杂质离子的浓度,保证涂装质量。
在此系统的运行中应注意,系统一经运行后应连续运行,严禁间断运行,以防超滤膜干枯。
干枯后的树脂和颜料附着在超滤膜上,无法彻底清洗,将严重影响超滤膜的透水率和使用寿命。
超滤膜的出水率随运行时间而呈下降趋势,连续工作30~40天应清洗一次,以保证超滤浸洗和冲洗所需的超滤水。
(7)电泳涂装法适用于大量流水线的生产工艺。
电泳槽液的更新周期应在3个月以内。
以一个年产30万份钢圈的电泳生产线为例,对槽液的科学管理极为重要,对槽液的各种参数定期进行检测,并根据检测结果对槽液进行调整和更换。
一般按如下频率测量槽液的参数:
电泳液、超滤液及超滤清洗液、阴(阳)极液、循环洗液、去离子清洗液的PH值、固体含量和电导率 每天一次;
颜基比、有机溶剂含量、试验室小槽试验 每周2次。
(8)对漆膜质量的管理,应经常检查涂膜的均一性和膜厚,外观不应有针孔、流挂、橘皮、皱纹等现象,定期检查涂膜的附着力、耐腐蚀性能等物理化学指标。
检验周期按生产厂家的检验标准,一般每个批次都需检测。
顶端Posted:
2008-02-0308:
38|11楼
yoyo1981
级别:
学徒工
精华:
0
发帖:
83
威望:
2点
金钱:
744机械币
贡献值:
0点
在线时间:
39(小时)
注册时间:
2006-12-14
最后登录:
2008-09-05
小中大引用推荐编辑只看复制
钢模板电泳涂装技术原理与工艺流程
一、前言
钢模板,又称盒子板、模板。
钢模板是建筑行业普遍使用的一种工具材料。
以钢模板替代木质跳板进行砼施工,不仅使用方便,施工速度快,质量好,而且成本低,效益高。
由于钢模板与砼直接接触,就会产生所谓电化学腐蚀,降低模板精度,影响工程质量。
以往,钢模板防腐多采用喷涂或刷涂油漆,弊病很多。
例如,模板阴面筋板焊接结合部不易涂装,漆膜外观差,其附着力,耐冲击等技术指标都较低,且工人劳动强度大,施工速度慢,油漆浪费严重。
1979年武钢金属结构厂试制电泳涂装钢模板获得成功。
1980年建成国内第一条钢模板电泳涂装生产流水线。
这条生产线投产以来,不仅产品质量得到极大提高,而且产量也逐年增加,现已达年产5000t,社会效益及经济效益较好。
二、钢模板电泳涂装基本原理
所谓电泳涂装,是将被涂物(钢模板)浸渍在水溶性涂料中作为阳极(阳极电泳),另设一与其相对应的阴极,在两极间通直流电,靠电流所产生的物理化学作用,使涂料均匀涂在被涂物上的一种涂装技术。
电泳涂装必须使用电泳漆,电泳漆通常又称水溶性涂料,电泳漆与蒸馏水必须按一定比例进行稀释,才能使用。
电泳涂装一般包括四个同时进行的过程:
1、电泳:
在直流电场的作用下,正,负带电胶体粒子向负,正方向运动,也称泳动。
2、电解:
电极上分别进行着氧化还原反应,反而在电极上形成氧化与还原现象。
3、电沉积:
由于电泳作用,移至阳极附近的带电胶体粒子在模板表体放出电子,而呈不溶状态沉淀,析出的现象,此时漆膜形成。
4、电渗:
在电场作用下,固相不动,而液相移动的现象。
电渗作用使漆膜内所含水份逐渐被排到涂膜外,最后形成几乎连电流也通不过去,含水率极低,电阻相当高的致密漆膜。
5、铁红环氧电泳漆为例:
该电泳漆系改性环氧树脂,丁醇,乙醇胺,滑石粉,铁红的物质组成,电泳漆与蒸馏水混合后,在直流电场的作用下,即分离成带正电荷的阳离子和带负电荷的阴离子,并进行一系列复杂的物理化学胶体化学,电化学变化过程。
三、工艺过程
1、钢模板电泳涂装工艺流程
除油、除锈→水冲→水洗→干燥→电泳上膝→水冲→烘干→喷商标→包装→出厂
2、对工艺流程的说明
除油、除锈:
采用二合一法,即除油、除锈一步法,溶液本厂自配。
水冲、水洗:
其目的在于去掉模板表面的酸碱残留物。
水洗时,最好采用常流水。
电泳上漆:
这是工艺的目的和核心。
电泳槽内的电流、电压、固成份含量、PH值、电泳温度速度以及电泳槽附加设备的正确使用,是决定电泳上漆成败的关键。
烘干:
钢模板电泳上漆后必须烘干。
烘干箱工作温度为160-180℃,烘烤时间为30min。
电泳涂装所需的主要设备。
各种水槽,电泳槽,通道式烘干箱,机械传动系统,电气控制系统,漆液和漆膜设备,如电导仪,附着力测定仪等。
3、质量检测与控制
(1)漆液浓度
电泳漆与蒸馏水混合后,其浓度应达到10%-15%,浓度过高,漆膜流平性欠佳,易出现桔皮等缺陷。
浓度过低,漆膜变薄,易出现针孔现象。
(2)电压
电泳电压一般应控制在60V左右。
电压升高,沉积量增加,漆膜变的粗糙,形成桔皮,电压过低,漆膜甚簿,甚至泳不上漆。
(3)PH值
一般漆液PH值在8-9时均能得到满意的漆膜。
PH值过低,电泳槽内脉冲电流密度降低,从而造成模板局部无漆,形成花脸,PH值过高,会造成湿膜再溶解,使漆膜变簿,影响涂装质量。
调整槽液的PH值有多种方法,我们选择了阴极罩法。
阴极罩是将阴极板装在一个帆布袋内,袋用钢丝架支撑着,袋内装满蒸馏水。
电泳时,胺的正离子和漆液中带正电荷的杂质离子(如水中的Ca2﹢、Mg2﹢)均可通过帆布进入阴极罩内,并在阴极放电。
更换罩内蒸馏水,就可将杂质除去。
(4)电泳时间
电泳漆膜的厚度一般是随着电泳时间的增加而增加的,但是,当电泳时间到达一定点后,漆膜厚度就不再增加,其原因就是漆膜在达到一定厚度时产生绝缘。
故采用处长电泳时间使漆膜增厚是行不通的,而且由于耗电增加,在经济上是不合算的。
电泳时间一般有3min即可。
(5)电导率
电泳漆工作液的导电能力,通常用电导率表示。
漆液的电导过低,漆膜不易形成;电导过高,造成漆膜外观粗糙。
对同一种涂料而言,对漆液电导影响最大的因素是漆液中杂质离子的存在。
因此,一定要通过控制杂质含量,保持电导率的正常值。
钢模板电泳涂膜的部分性能见表1。
(表1钢模板电泳漆膜的部分性能)
检验项目 指标
(1)漆膜颜色及外观 红色,符合色标标准
(2)柔韧性,mm 1
(3)附着力(划圈法),级 ≤2
(4)冲击强度,公斤,厘米 50
(5)漆膜厚度,μM ≥2
(6)漆膜光度,度 55-7
(7)耐盐水性(25℃=1℃,3%氯化钠溶液中24H)肉眼观察无变化
四、结语
电泳涂装及水性漆的运用,标志着涂装工业的一项重大进步。
电泳涂装施工速度快,可实现机械化和自动化连续作业,减轻劳动强度,漆膜均匀,附着力强,对一般涂装方法不易涂到或涂不好的部位,如前所述的筋板焊缝等处都能获得均匀平整,光滑的漆膜。
涂料利用率高达90%-95%,由于电泳涂料是以水作为溶剂的,具有不燃性,无毒、操作方便等优点。
电泳后经过烘干的漆膜,具有优良的附着力,它的防锈性耐腐蚀性,耐候性等性能均优于普通油漆及一般的施工方法。
金结厂生产的武钢牌电泳模板,畅销国内二十多个省,市,自治区和直辖市。
仅1991年至1993年10月,钢模板电泳就创产值277万元,创利税24万元。
高柔韧性电泳漆工艺流程及技术指标
慧聪网 2006年2月13日9时31分 信息来源:
慧聪网涂料行业频道 网友评论0条 进入论坛
电泳作为表面处理的一部分,凭借其优异的性能,简单的操作,在行业中得到了迅猛的发展和应用,然而在一些有特殊要求的行业中,目前市面上的电泳涂料仍满足不了要求,新一代高性能电泳涂料的发展及应用解决了这方面的难题。
以下介绍的是高柔韧性电泳漆在要求有强的柔性及韧性的工件表面应用工艺,以麦克风及台灯上新用的弹簧支管为例,工件构造:
弹簧及弹簧缝包三角铁组合成形。
工艺流程:
酸洗→水洗→预脱脂→脱脂→水洗→水洗→磷化→水洗→水洗→超声波清洗→纯水洗→电泳→喷淋洗→水洗→纯水洗→风干→烘烤
涂膜性能指标
四、涂膜性能指标
项目
指标
检验方法
外观
平整光滑
目测
膜厚μm
8-12
GB/T1764-79(89)
光泽(60℃)
>90
GB/T9754-88
硬度H
3-5
GB/T6739-1996
附着力(划格法)级
0
GB/9286-88
耐碱性
合格
特殊检验*1
耐酸性
合格
特殊检验*2
耐水性
5
特殊检验*3
磷化与涂装——国家标准一览表
2007/11/14/08:
47 来源:
慧聪网表面处理行业频道
现有网友评论0条 进入论坛
一.表面处理表面准备部分
序号
标准名称
标准号
1
涂装前表面准备—酸洗
JB/T 6978—1993
2
钢铁工件涂漆前磷化处理技术条件
GB/T 6807—1986
3
金属的磷酸盐转化膜
GB/T 11376—1997
4
化学转化膜 铝及铝合金上漂洗和不漂洗铬酸盐转化膜
GB/T 17460—1998
5
金属材料上的转化膜 单位面积上膜层质量的测定 重量法
GB/T 9792—1988
6
钢铁件涂装前除油程度检验方法(验油试纸法)
GB/T 13312—1991
7
涂装前钢材表面锈蚀等级和除锈等级
GB 8923—1988
8
多功能钢铁表面处理液通用技术条件
GB/T 12612—1990
9
涂装前钢材表面粗糙度等级的评定(比较样块法)
GB/T 13288—1991
二.漆膜性能测试部分
序号
标准名称
标准号
1
漆膜附着力测定法
GB/T1720—1979(89)
2
漆膜一般制备法
GB/T1727—1992
3
漆膜硬度测定法 摆杆阻尼试验
GB/T1730—1993
4
漆膜柔韧性测定法
GB/T1731—1993
5
漆膜耐冲击测定法
GB/T1732—1993
6
漆膜耐水性测定法
GB/T1733—1993
7
漆膜耐汽油性测定法
GB/T1734—1993
8
漆膜耐热性测定法
GB/T1735—1979(89)
9
漆膜耐湿热测定法
GB/T1740—1979(89)
10
漆膜光泽测定法
GB/T1743—1979(89)
11
漆膜耐化学试剂性测定法
GB/T1763—1979(89)
12
漆膜厚度测定法
GB/T1764—1979(89)
13
测定耐湿性﹑耐盐雾﹑耐候性(人工加速)的漆膜制备法
GB/T1765—1979(89)
14
色漆和清漆 涂层老化的评级方法
GB/T1766—1995
15
色漆和清漆 耐中性盐雾性能的测定
GB/T1771—1991
16
色漆和清漆 人工气候老化和人工辐射暴露(滤过的氙弧辐射)
GB/T1865—1997
17
漆膜颜色标准
GB/T3181—1995
18
色漆和清漆 耐水性的测定 浸水法
GB/T5209—1985
19
涂层附着力的测定法 拉开法
GB/T5210—1985
20
涂膜硬度铅笔测定法
GB/T6739—1996
21
涂膜弯曲试验(圆柱轴)
GB/T6742—1986
22
色漆和清漆 划痕试验
GB9279—1988
23
色漆和清漆 漆膜的划格试验
GB/T9286—1998
24
色漆和清漆 杯突试验
GB/T9753—1988
25
色漆和清漆 不含金属颜料的色漆漆膜之20