年产170万吨焦炭焦化厂COG净化工艺及设备初步设计.docx
《年产170万吨焦炭焦化厂COG净化工艺及设备初步设计.docx》由会员分享,可在线阅读,更多相关《年产170万吨焦炭焦化厂COG净化工艺及设备初步设计.docx(58页珍藏版)》请在冰豆网上搜索。
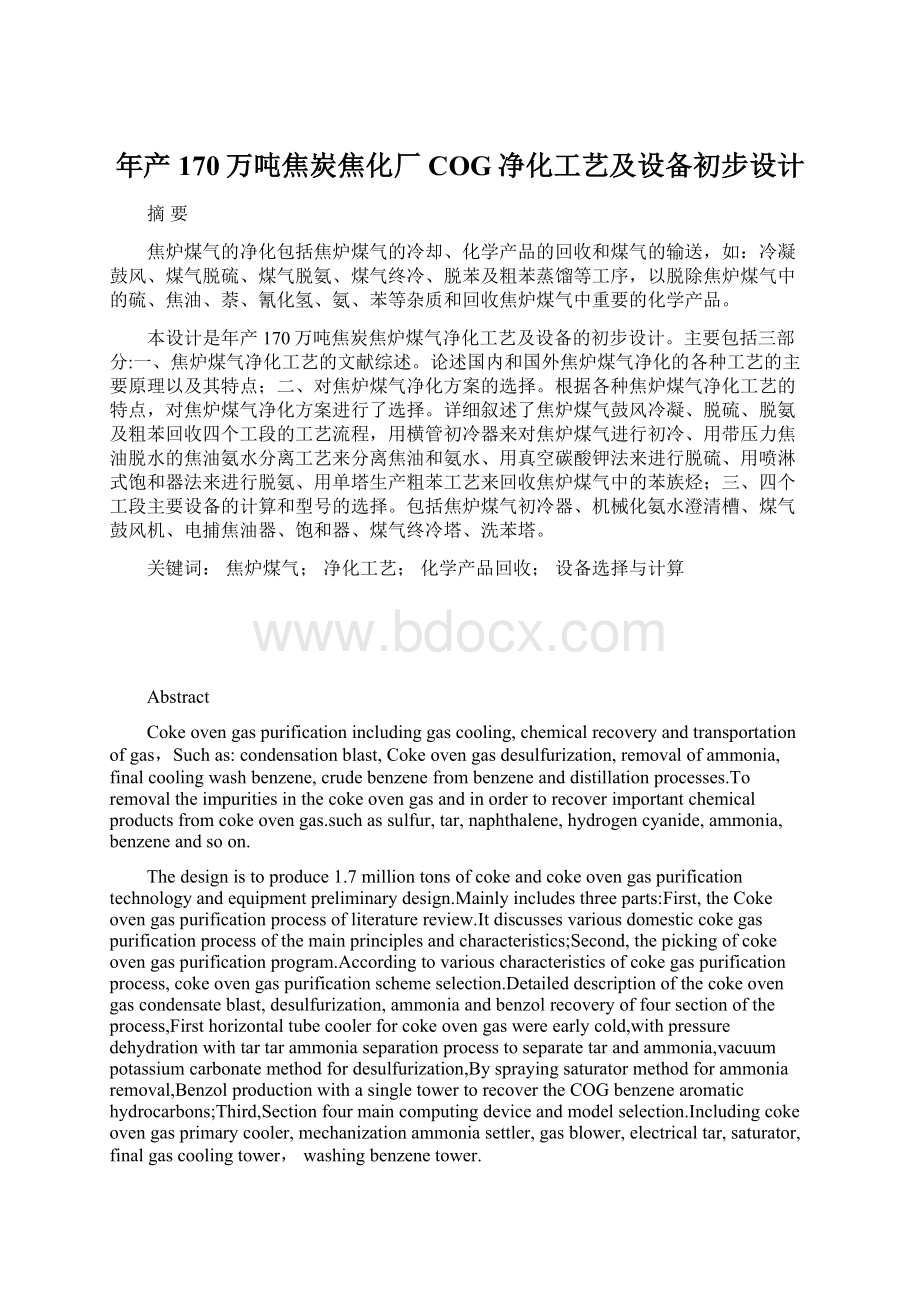
年产170万吨焦炭焦化厂COG净化工艺及设备初步设计
摘要
焦炉煤气的净化包括焦炉煤气的冷却、化学产品的回收和煤气的输送,如:
冷凝鼓风、煤气脱硫、煤气脱氨、煤气终冷、脱苯及粗苯蒸馏等工序,以脱除焦炉煤气中的硫、焦油、萘、氰化氢、氨、苯等杂质和回收焦炉煤气中重要的化学产品。
本设计是年产170万吨焦炭焦炉煤气净化工艺及设备的初步设计。
主要包括三部分:
一、焦炉煤气净化工艺的文献综述。
论述国内和国外焦炉煤气净化的各种工艺的主要原理以及其特点;二、对焦炉煤气净化方案的选择。
根据各种焦炉煤气净化工艺的特点,对焦炉煤气净化方案进行了选择。
详细叙述了焦炉煤气鼓风冷凝、脱硫、脱氨及粗苯回收四个工段的工艺流程,用横管初冷器来对焦炉煤气进行初冷、用带压力焦油脱水的焦油氨水分离工艺来分离焦油和氨水、用真空碳酸钾法来进行脱硫、用喷淋式饱和器法来进行脱氨、用单塔生产粗苯工艺来回收焦炉煤气中的苯族烃;三、四个工段主要设备的计算和型号的选择。
包括焦炉煤气初冷器、机械化氨水澄清槽、煤气鼓风机、电捕焦油器、饱和器、煤气终冷塔、洗苯塔。
关键词:
焦炉煤气;净化工艺;化学产品回收;设备选择与计算
Abstract
Cokeovengaspurificationincludinggascooling,chemicalrecoveryandtransportationofgas,Suchas:
condensationblast,Cokeovengasdesulfurization,removalofammonia,finalcoolingwashbenzene,crudebenzenefrombenzeneanddistillationprocesses.Toremovaltheimpuritiesinthecokeovengasandinordertorecoverimportantchemicalproductsfromcokeovengas.suchassulfur,tar,naphthalene,hydrogencyanide,ammonia,benzeneandsoon.
Thedesignistoproduce1.7milliontonsofcokeandcokeovengaspurificationtechnologyandequipmentpreliminarydesign.Mainlyincludesthreeparts:
First,theCokeovengaspurificationprocessofliteraturereview.Itdiscussesvariousdomesticcokegaspurificationprocessofthemainprinciplesandcharacteristics;Second,thepickingofcokeovengaspurificationprogram.Accordingtovariouscharacteristicsofcokegaspurificationprocess,cokeovengaspurificationschemeselection.Detaileddescriptionofthecokeovengascondensateblast,desulfurization,ammoniaandbenzolrecoveryoffoursectionoftheprocess,Firsthorizontaltubecoolerforcokeovengaswereearlycold,withpressuredehydrationwithtartarammoniaseparationprocesstoseparatetarandammonia,vacuumpotassiumcarbonatemethodfordesulfurization,Bysprayingsaturatormethodforammoniaremoval,BenzolproductionwithasingletowertorecovertheCOGbenzenearomatichydrocarbons;Third,Sectionfourmaincomputingdeviceandmodelselection.Includingcokeovengasprimarycooler,mechanizationammoniasettler,gasblower,electricaltar,saturator,finalgascoolingtower,washingbenzenetower.
Keywords:
Cokeovengas;Thepurificationprocess;Chemicalproductsrecycling;Equipmentselectionandcalculation
1绪论
1.1焦炉煤气净化意义
我国是一个储煤量的大国,也是一个炼焦产业的大国,炼焦过程会产生大量的焦炉煤气,如果焦炉煤气没有经过净化利用而燃烧掉放空的话,不仅会造成资源的浪费,而且还会严重污染大气环境和生态环境,这是非常不可取的。
根据统计数据显示,我国的焦化企业将近有200多家,主要分布于冶金、化工、城建、煤炭等各个部门,其中每年焦炭产量超过l000kt的焦化企业约占l0%。
在炼焦过程中,除有75%左右的原料煤变成焦炭外,还有25%左右的原料煤生成多种化学产品以及焦炉煤气。
煤气净化回收系统回收的炼焦化学产品在国民经济中占有非常重要的地位。
煤在炼焦时,从焦炉的上升管出来的荒煤气,经高压氨水喷洒冷却和用各种吸收剂以及净化工序处理后,可以提取焦炉煤气中的焦油、氨、萘、硫化氢、氰化氢以及粗苯等变为比较纯的化学产品,并得到纯净的焦炉煤气。
焦炉煤气的净化对于煤气输送过程及回收化学产品的设备正常运行来说都是十分必要的。
焦炉煤气中含有的萘和焦油在煤气中的最大危害就是堵塞设备和管路;焦炉煤气中的硫化氢和氨等酸性气体的最大危害就是严重腐蚀焦炉煤气净化的设备和焦炉煤气输送的管路;而且NH3和HCN等气体的危害是在煤气燃烧时转变为含氮的氧化物和含硫的氧化物,将会形成酸雾、酸雨、光化学烟雾等环境污染物,这将会严重污染大气环境。
原料煤在焦炉中炼焦的过程中,原料煤中约有30%~35%的硫将会转化成H2S和HCN等含有毒有害的化合物,与NH3和HCN等气体一起形成焦炉煤气中的杂质,其中焦炉煤气中H2S的质量浓度大约为5~8g/m3,氰化氢(HCN)的质量浓度大约为l~2.5g/m3[l~2]。
另外H2S和HCN具有非常强的腐蚀性和毒性,不仅会带来严重的腐蚀问题和环境污染问题,而且当空气中H2S的体积分数达到为0.l%时就能使人致命[3]。
在焦炉煤气没有经过净化就作为燃料使用时,焦炉煤气中H2S和HCN等气体及其燃烧的产物SO2和含氮氧化物均有毒性,这将会严重污染大气环境和水资源,因此必须通过焦炉煤气净化系统除去这些有危害的杂质,同时转化为有用的化工原料和化学产品,这样既充分利用了资源,又保护了环境,减少了大气污染,所以焦炉煤气净化在国民经济中具有非常重要的现实意义和战略意义。
1.2设计规模
本设计是焦化厂的一部分,是焦化厂的化学产品回收车间,回收焦炉煤气中的化学产品,以净化焦炉煤气,再将净化后的焦炉煤气用于其他用途。
设计规模是年产170万吨焦炭的焦化厂的焦炉煤气净化,新建投产,一次建成。
本设计主要为化产车间的鼓风冷凝工段、硫冷工段、硫铵工段和粗苯回收工段,一共四个工段。
1.3焦炉煤气净化主要技术方案
焦炉煤气鼓风冷凝工段:
焦炉煤气的冷却工艺方案首先是煤气在桥管中被循环氨水冷却到80—90℃后进入到煤气初冷器,初冷器选择间接冷却的橫管式初冷器,橫管初冷器应将煤气尽可能冷却到21—22℃,才能使煤气里75%的焦油和焦油雾,80%的萘除去;选择沉降除渣和静置分离工艺,将焦油氨水和焦油渣分离;选择蜂窝式电捕焦油器在鼓风机前的负压工艺来捕集煤气中的焦油雾;选择变频调速器的离心式鼓风机为煤气输送提供动力。
焦炉煤气脱硫工段:
选择真空碳酸钾法来煤气脱硫,这种工艺是利用碳酸钾溶液来吸收煤气中的硫化氢和氰化氢等酸性气体,从而净化焦炉煤气。
焦炉煤气脱氨工段:
选择喷淋式饱和器法硫铵工艺方案来脱氨。
焦炉煤气终冷和粗苯工段:
焦炉煤气的终冷工艺选择间接冷却的橫管初冷器工艺方案;在装有填料的填料塔中,用焦油洗油做吸收剂来吸收煤气中的粗苯;采用单塔生产粗苯工艺来进行粗苯蒸馏。
1.4本设计的主要设备
焦炉煤气初冷:
一段选F=4000m2横管式初冷器;二段选F=1600m2的横管式初冷器。
一、二段各选用3台,第一段和第二段叠放使用,另外备用1台,共计4台横管式初冷器。
焦油捕集:
选择两台沉淀极孔数为276孔,直径为5200mm的蜂窝式电捕焦油器,一开一备;
鼓风机类型和调速技术:
离心式鼓风机;用液力偶合器来调速。
焦油氨水的分离设备:
选择四台机械化氨水澄清槽,三用一备,其规格为V=300m3;
焦炉煤气输送设备:
两台Q=1200m3/min,扬程为30000Pa离心鼓风机。
另外备用一台,共计三台。
焦炉煤气脱硫:
真空碳酸钾脱硫塔。
焦炉煤气脱氨设备选择:
选择喷淋式饱和器的内径D=5.4m,饱和器的内环直径D=1.73m,中央煤气出口管的直径为1.28m。
焦炉煤气终冷:
选用F=6000m2的横管式终冷器2台,另外备用1台,共计3台横管式终冷器,其总传热面积为F=6000m2。
焦炉煤气洗苯塔:
选择1台直径为6m的洗苯塔,每台洗苯塔充5段SM-125Y型波纹板填料,每段高4.2m,故洗苯塔高43.7m。
2文献综述
2.1焦炉煤气鼓风冷凝工艺
2.1.1焦炉煤气的冷却工艺
焦炉煤气离开焦炉时,通过上升管以650~750℃的温度进入集气主管,在桥管中用高压氨水对焦炉煤气进行喷洒,焦炉煤气被冷却到80~90℃,焦炉煤气的热量变为氨气的气化潜热和焦炉煤气一起进入集气管,形成的气液混合物从集气管进入气液分离器,气体进入煤气初步冷却器,煤气通过不同的冷却设备,并按不同的净化工艺要求,冷却到21~23℃或25~30℃后进入后续工序。
煤气冷却过程不仅要对焦炉煤气进行冷却,还要尽最大可能地去除焦油雾、萘和腐蚀性杂质,以达到最大限度地净化煤气的目的[4~5]。
(1)间接冷却工艺
A、立管式初冷器
立管式初冷器由筒体、上下水箱组成。
多根传热管垂直地配置在冷却器的筒体内,用隔板将上下水箱分隔成六格。
上部水箱为敞开的型式,这样就方便清扫管内的污垢,煤气与水室对应分格,煤气被冷却的同时,产生的冷凝液沉积在煤气室的下部,用管道引入到初冷器的水封槽。
由于立管式初冷器的上部水箱为敞开式,因此水在管内流速低,大约为0.1m/s。
而且传热效率低,并且冷凝液分别从各个分格中引出,煤气中的大部分萘是在50℃以后才开始析出,因而造成初冷器后段的堵塞严重,煤气的阻力增大,清扫频繁,出口煤气中的萘含量高,将会使使煤气的净化效果变差。
在实际操作中,出现上部水温反而比下部水温高的情况,致使煤气入口侧这一格起不到冷却传热的作用。
B、横管式初冷器
横管式初冷器是由多个箱体组成的,在高为1m的长方形箱体内水平配置多根传热管。
煤气从上向下流动,冷却水由下向上流动,整个设备可按需要分为三段或二段(上面的是循环水段、下部的是低温水段)。
在低温水段可以采用断塔板与上部隔开,这样有较好的节能效果。
用焦油氨水混合液横管式初冷器的中段、下段进行连续喷洒,一方面可以在传热管的外部壁面形成液膜,形成膜状冷凝,可以提高液膜的传质效率;另一方面煤气和冷凝液并行流动自上而下冲洗可防止萘和焦油等杂质的堵塞。
由于横管初冷器提高了水流速度,一般为0.6~0.7m/s,煤气流向又于冷凝液流向一致,因此,其除萘效果要比立管式初冷器好得多,可最大限度地提高煤气的净化效率,总传热系数比立管式初冷提高了一倍多。
对于相同的煤气量,横管初冷器的传热面积可大为减少,其工艺流程如图2.1所示。
图2.1横管初冷器的煤气冷却工艺流程
煤气的初步冷却是煤气净化工艺的基础。
在初冷器中最大限度地将煤气冷却至21~22℃,就可以去除煤气中75%以上的焦油和焦油雾,还可去除煤气中80%的萘,使出口煤气的含萘量降低到0.4g/m3以下,即可达到相当于出口煤气的露点。
这样,就可以实现整个工艺过程不需要另外建单独的煤气脱萘装置。
(2)直接冷却工艺
煤气流向为从下向上流动、氨水从上方向下进行喷淋与煤气进行逆流接触。
采用直接式初冷器时,由于水与煤气直接接触,因此在冷却煤气的同时还可以对煤气起到洗涤的效果,煤气中的H2S、NH3、HCN等腐蚀性介质以及焦油雾等可以得到较好的净化。
冷却过程中,为了防止设备的腐蚀,因此不能让腐蚀性的介质积累在循环液中,便需要经常换新鲜水,生成的废水送往焦油氨水澄清槽中对污水进行处理,补充的新鲜水可用送往焦炉的循环氨水,整个过程的换水量为整个循环量的5%~10%。
对于直接式初冷器来说,由于存在先用冷却水冷却循环洗涤氨水,再用洗涤氨水冷却煤气这样的两个温差,在同样温度的冷却水下,直接冷却器冷却后的煤气温度要比间接初冷器的高。
此外,由于直接式初冷器的液气比大,导致泵的电能耗用量也大,换热器的换热面积及换热器的台数将会增多,而且换热器占用地的面积大,我国有的设计中已不再采用这种初冷器。
(3)间直冷工艺
煤气在高温段由80~90℃冷却到50~55℃时采用间接冷却器,这时由于冷却的传热温差比较大,冷凝液的量比较大,但冷凝下来的萘的量相对较少,但是这种工艺的传热系数比较高,因此需要的传热面积比较少,则换热器的占地面积将会比较少;在煤气温度达到50~55℃时采用直接式冷却器,可充分发挥直接冷却净化煤气效果好的优点。
但此工艺相对比较复杂,设备比较多、能源消耗大、占地空间面积大,我国只在宝钢一期和三期工程中采用此工艺。
2.1.2焦炉煤气脱萘
根据装入焦炉的煤料和焦炉的操作条件的不一样,焦炉出来的焦炉煤气中一般含萘量为5~10g/m3,其中萘呈气态。
焦炉煤气脱萘的工艺流程:
70℃的补充氨水在第一冷却器中冷却到35~36℃后,进入洗萘塔底部的循环氨水槽。
然后用氨水循环泵抽出,经过第二冷却器将氨水冷却到35℃后再送至洗萘塔上段的煤气终冷段喷洒。
氨水从终冷段的底部自流到下面的煤气预冷段喷洒,氨水则流入底部的循环氨水槽。
焦炉煤气脱萘的主要设备是油洗萘塔,为空喷塔,塔体用钢板焊制而成,预冷段和终冷段内村环氧玻璃钢,捕雾层有丝网和旋流板两种形式。
2.1.3焦油氨水分离
送入焦炉煤气集气管的循环氨水进入到焦炉煤气集气管,气液混合物从集气管送到气液分离器中将焦炉煤气和液态混合物进行分离,液体混合物经气液分离器自流到焦油氨水分离装置。
此外,从煤气初冷器、电捕焦油器和鼓风机等设备冷凝下来的冷凝液也送往焦油氨水分离装置,在此将焦油氨水和焦油渣分离。
循环氨水送回焦炉集气管喷洒,剩余氨水送往下道工序,焦油作为产品送油库外销。
国内经常采用的焦油氨水分离工艺有三种方式[6],现分述如下:
A、带有二段脱渣的焦油氨水分离工艺
机械化焦油氨水澄清槽内各层的密度如下:
上层为1.01~1.02g/cm3;中层为1.17~1.18g/cm3;底层焦油渣为1.25g/cm3。
在焦油分离器内的主要作用是再次分出焦油中少量的氨水和焦油渣,用泵将焦油从焦油分离器中送入到焦油槽。
带有二段脱渣的焦油氨水分离工艺具有以下特点:
①二段脱渣的效率高。
经三段脱渣后可使焦油含渣量降低到0.3%(100μm以上),脱除焦油渣的效率可以达到97%。
②焦油氨水分离器的容积要比传统的机械化焦油氨水澄清槽大,并且各槽只有一格,操作检修时的劳动条件好。
B、沉降除渣和静置分离工艺
焦油氨水的分离采用常压、沉降除渣、静置分离工艺,其主要设备是焦油渣分离箱和焦油氨水分离槽两种,除渣和焦油氨水分离工序在不同设备内进行。
焦油氨水分离槽的结构里面是锥形,外面为圆柱形的双层结构,这样可以巧妙地将油水分离槽、循环氨水槽和焦油脱水槽三者组合成为一体结构。
另外,在油和水的界面处设置有乳化液的采出口。
焦油氨水分离槽具有很多的优点,例如:
操作简单、能耗低、分离效果好等。
因沉降除渣和静置分离工艺的转动设备少,主要靠静置分离,实际操作表明,可使焦油的含水量降低到2%以下,其分离效果极为良好。
沉降除渣和静置分离工艺的流程如图2.2所示。
图2.2焦油氨水的沉降除渣和静置分离工艺流程
C、带压力焦油脱水的焦油氨水分离工艺
经过气液分离器分离后得到的焦油氨水首先送入到焦油氨水澄清槽中,氨水从澄清槽的顶部自流入循环氨水槽。
带刮板的焦油氨水澄清槽中的刮刀将焦油渣刮出并连续排至手推车内,槽底上方的含水焦油用泵抽送至压力焦油分离器,以保证焦油中尽可能少含固体颗粒。
在压力焦油分离器中,可以将焦油和水进行高度分离,槽底的焦油渣由螺旋输送机沿焦油流动方向输送,并间歇排入焦油氨水澄清槽。
上层的氨水在满流槽中,当氨水满了之后会自动地排至焦油氨水澄清槽,经过脱水后的焦油将会自流至焦油储槽。
这种流程最大的优点就是是占地面积小;缺点是传动设备比较多,因此维修工作量大,操作的工作量比较大,而且操作也比较复杂。
2.1.4煤气中焦油雾的分离
焦炉煤气经过初步冷却器初步冷却后,还含有0.1~100μm的颗粒悬浮焦油雾,其含量为3~5g/m3,可通过高效率的电捕焦油器加以脱除,电捕焦油器的捕集效率在99%以上,捕集器后煤气中的焦油含量为20~50mg/cm3。
在电捕焦油器沉淀极和电晕极之间的高压直流电场作用下,焦油雾被捕集在沉淀极上。
以前,由于对电捕焦油器的重要性认识不足,再加上电捕焦油器本身存在不少问题,故国内不少焦化厂的电捕焦油器大多搁置不用,造成后续工序设备和管道的严重堵塞和腐蚀,甚至直接影响焦化产品的质量等不良后果[7]。
根据电捕焦油器在焦炉煤气净化流程中不同位置的配置情况,一般可分为两种流程,即配置在鼓风机后的正压操作流程和配置在鼓风机前的负压操作流程。
电捕焦油器的负压操作流程:
、煤气所含的3~5g/m3焦油雾可在鼓风机前充分脱除,减轻鼓风机冷凝液排出管的堵塞并减少吹扫次数;
由于鼓风机的绝热压缩后的煤气升温在15℃左右,焦油雾中的萘会将会升华而使煤气中的含萘量增加。
因此,经初冷后存在于煤气中的焦油雾在鼓风机前脱除是极其重要的。
电捕焦油器的正压操作流程:
优点是煤气体积小,设备容量小。
电捕焦油器沉淀极的形式有三种,即同心圆式、圆管列管式以及蜂窝式。
同心圆式电捕焦油器的应用比较少,一般只在小型焦化厂中使用。
列管式电捕焦油器是传统形式。
只要瓷瓶等附件及馈电形式适宜,设备尺寸选择正确,其捕雾效率是可以保证的。
蜂窝式电捕焦油器可以很好地利用材料,占用占用的空间少,设备布置紧凑,制造安装比较方便,而且操作管理容易。
避免了列管式为了固定电晕极而存在无效空间的弊端。
2.2焦炉煤气脱硫工艺
焦炉煤气中的硫化氢含量主要取决于炼焦用煤料中所含硫分,而氰化氢则是煤煤在焦炉中炭化时,煤气中的氨与红焦发生反应而生成的产物,即:
C+NH3HCN+H2
焦炉煤气中硫化氢和氰化氢主要分布在初冷器后的焦炉煤气和初冷过程中形成的剩余氨水中。
焦炉煤气脱硫脱氢的方法可以分为干法脱硫工艺和湿法脱硫工艺两种工艺。
现代化的大型焦化厂均采用湿法脱硫脱氢工艺。
表2.1脱硫脱氰方法
方法类型
名称
脱硫效率/%
脱氰效率/%
吸收剂、催化剂
湿式吸收法
代亚毛克斯法
约98
约30
氨
AS循环洗涤法
90~98
50~75
氨
真空碳酸盐法
90~98
约85
碳酸钾
湿式催化氧化法
改良蒽醌法
约99
约90
碳酸钠、蒽醌二磺酸
萘醌法
约99
约90
氨、萘醌磺酸
苦味酸法
约99
约90
氨、苦味酸
栲胶法
约99
约90
碳酸钠、栲胶
PDS法
约99
约90
碳酸钠、酞氰钴磺酸盐
HPF法
约99
约90
氨、对苯二酚、双核酞菁钴六磺酸铵
2.2.1HPF法煤气脱硫脱氰
HPF法是湿式催化氧化法脱硫,其催化剂是HPF催化剂。
用HPF催化剂脱硫脱氰是一种液相催化氧化反应,具有在脱硫和再生全过程中催化剂活性比较高和流动性比较好等突出优点[8]。
(1)HPF法煤气脱硫脱氰的工艺流程
HPF法煤气脱硫可分为正压流程(脱硫装置位于鼓风机后)和负压流程(脱硫装置位于鼓风机前)。
在正压流程中,鼓风机后的煤气首先进入预冷塔,与塔顶喷洒液逆流接触,煤气被冷却到30℃后进入脱硫塔。
为了提高脱硫系统的氨硫比,剩余氨水蒸馏后的氨气兑入预冷塔前的煤气中,或将氨气冷凝成浓氨水后兑入脱硫液中。
吸收硫化氢和氰化氢后的脱硫富液从脱硫塔底自流入到反应槽,然后用泵将脱硫富液抽送至再生塔进行再生。
再生后就得到脱硫贫液,再将脱硫贫液通过液位调节器自流到脱硫塔中。
硫磺泡沫再经过浓缩后装入到熔硫釜,再经过加热脱水、熔融后制得硫磺产品。
脱硫废液经添加装置回兑入炼焦煤中,其工艺流程图如图2.3所示。
图2.3HPF法煤气脱硫脱氰装置的工艺流程
(2)对HPF法脱硫工艺的评价
优点:
①HPF法脱硫工艺的整个过程中,催化剂的催化活性和流动性比较好;
②脱硫效率可满足《焦化企业准入条件》的要求;
缺点:
①煤气脱硫过程中会产生富含硫氰酸铵和硫代硫酸铵等副盐的脱硫废液,且该废液难以处理。
②从再生塔顶排出的再生尾气带有大量的氨,如果将这部分尾气直接排放便会造成严重的二次污染。
③脱硫装置的产品硫磺纯度低,质量差,销路不畅。
④因脱硫塔的空塔速度低、液气比大和再生强度高,从而使脱硫装置的设备庞大,能耗高。
2.2.2真空碳酸钾法煤气脱硫
真空碳酸钾法煤气脱硫是利用碳酸钾溶液来吸收焦炉煤气中的硫化氢和氰化氢。
由于硫酸钾的溶解度高于碳酸钠,即真空碳酸钾法煤气脱硫工艺脱硫液的碱度大于真空碳酸钠法,故脱硫效率略高于真空碳酸钠法。
在脱硫塔上部设置碱洗段的情况下,真空碳酸钾法出口煤气的硫化氢含量可达到200mg/m3,可满足焦化企业准入条件的要求[9~10]。
(1)真空碳酸钾法煤气脱硫的基本原理
吸收反应
K2CO3+H2S=KHCO3+KHS
K2CO3+HCN=KHCO3+KCN
K2CO3+CO2+H2O=2KHCO3
解析反应
KHCO3+KHS=K2CO3+H2S
KHCO3+KCN=K2CO3+HCN
2KHCO3=K2CO3+CO2+H2O
副反应
2KHS+2O2=K2S2O3+H2O
K2CO3+H2S+0.5O2+HCN=KSCN+KHCO3+H2O
(2)真空碳酸钾法煤气脱硫的工艺流程
真空碳酸钾法煤气脱硫的工艺流程如图2.4所示。
图2.4真空碳酸钾法煤气脱硫的工艺流程
从图2.4中可以看出,焦炉煤气从脱硫塔下部进入到脱硫塔中,脱硫和脱氰后的煤气从脱硫塔顶离开,再经除雾器除去夹带的液滴后送后续工序处理。
由真空泵抽送并加压送往克劳斯装置或湿接触法制酸装置,回收硫磺或制取硫酸。
为了提高脱硫效率,脱硫塔和再生塔均采用分段操作。
脱硫液在循环过程中因氧的存在而生成KSCN和K2S2O3等盐类,为了保证脱硫效率,必须外排少量的脱硫废液,该废液可送机械化焦油氨水澄清槽处理。