催化裂化设计书.docx
《催化裂化设计书.docx》由会员分享,可在线阅读,更多相关《催化裂化设计书.docx(36页珍藏版)》请在冰豆网上搜索。
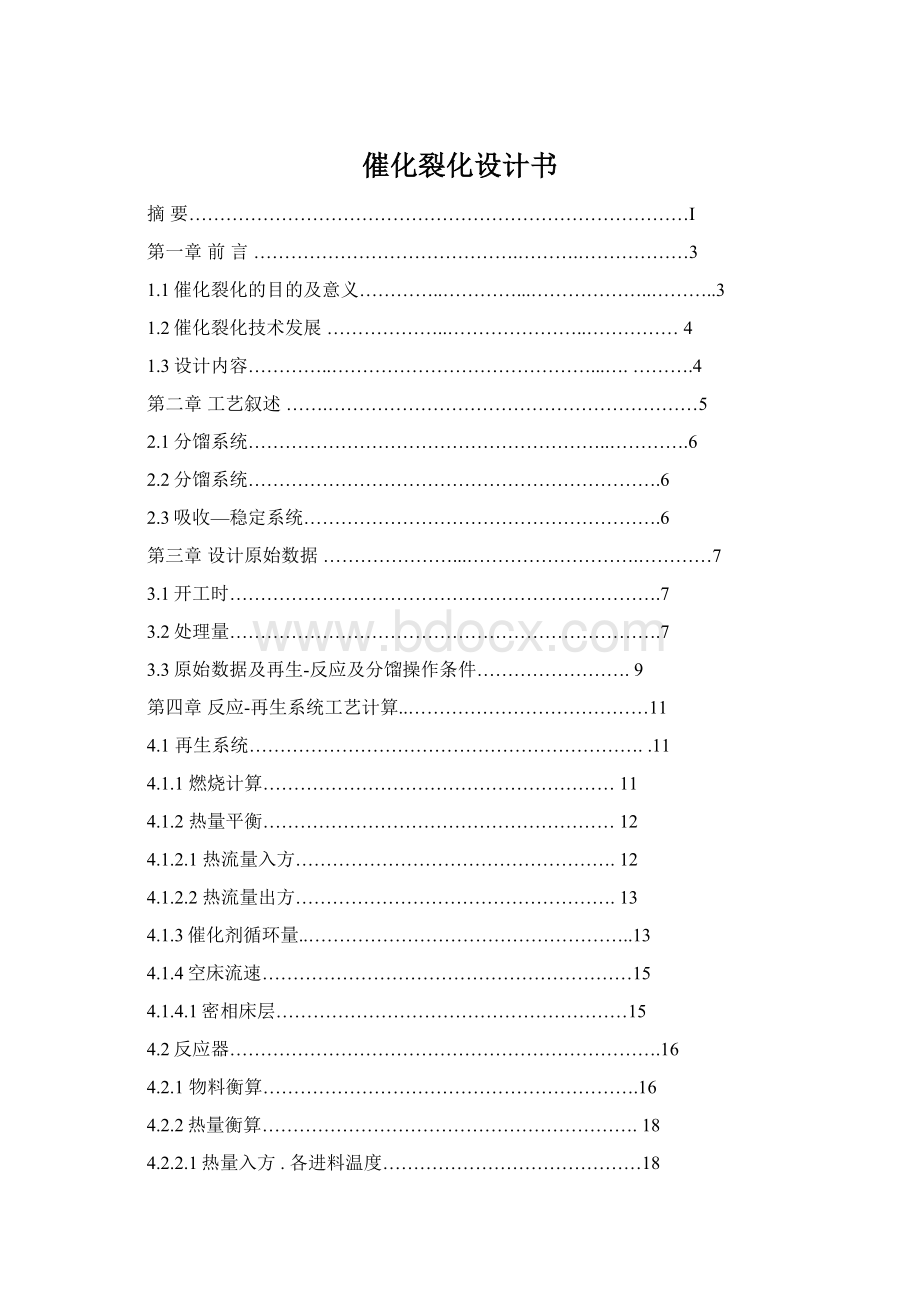
催化裂化设计书
摘要………………………………………………………………………I
第一章前言…………………………………….……….………………3
1.1催化裂化的目的及意义…………..…………...………………..………..3
1.2催化裂化技术发展………………..…………………..……………4
1.3设计内容…………..……………………………………...….……….4
第二章工艺叙述…….……………………………………………………5
2.1分馏系统…………………………………………………..………….6
2.2分馏系统………………………………………………………….6
2.3吸收—稳定系统………………………………………………….6
第三章设计原始数据…………………...……………………….…………7
3.1开工时…………………………………………………………….7
3.2处理量…………………………………………………………….7
3.3原始数据及再生-反应及分馏操作条件…………………….9
第四章反应-再生系统工艺计算..…………………………………11
4.1再生系统………………………………………………………..11
4.1.1燃烧计算…………………………………………………11
4.1.2热量平衡…………………………………………………12
4.1.2.1热流量入方…………………………………………….12
4.1.2.2热流量出方…………………………………………….13
4.1.3催化剂循环量..……………………………………………..13
4.1.4空床流速……………………………………………………15
4.1.4.1密相床层…………………………………………………15
4.2反应器…………………………………………………………….16
4.2.1物料衡算…………………………………………………….16
4.2.2热量衡算…………………………………………………….18
4.2.2.1热量入方.各进料温度……………………………………18
4.2.2.2热量出方…………………………………………………19
4.2.3提升管工艺计算…………………………………………….21
4.2.3.1提升管进料处的压力和温度……………………………….21
4.2.3.2提升管直径……………………………………………….21
4.2.3.3预提升段的直径和高度…………………………………….23
4.2.4旋风分离器工艺计算……………………………………….24
4.2.4.1筒体直径………………………………………………….24
4.2.2.2一级入口截面积……………………………………………25
4.2.2.3二级入口截面积………………………………………….25
4.2.2.4算旋风分离器组数…………………………………………254.2.2.5一级腿负荷及管径…………………………………………25
第五章分馏塔能量平衡计算…………………………………………….27
第六章计算结果汇总…………………………………………………….29
结束语………………………………………………………………………30
参考文献……………………………………………………………………31
致谢……………………………………………………………………….32
第一章前言
1.1催化裂化的目的及意义
我国原油偏重,轻质油品含量低,为增加汽油、柴油、乙烯用裂解原料等轻质油品产量。
我过炼油工业走深度加工的道路,形成了以催化裂化(FCC)为主体,延迟焦化、加氢裂化等配套的工艺路线。
2001年底全国有147套催化裂化装置,总加工能力超过100.0Mt/a,比1991年增加58.4Mt/a,增长137.16%,可以说是世界上催化裂化能力增长最迅速的国家。
催化裂化是重要的重质油轻质化过程之一,在汽油和柴油等轻质油品的生产占有很重要的地位。
催化裂化过程在炼油工业,以至国民经济中只有重要的地位。
在我国,由于多数原油偏重,而H/C相对较高且金属含量相对较低,催化裂化过程,尤其是重油催化过程的地位显得更为重要。
随着工业、农业、交通运输业以及国防工业等部门的迅速发展,对轻质油品的需求量日益增多,对质量的要求也越来越高。
以汽油为例,据1988年统计,全世界每年汽油总消费量约为6.64亿吨以上,我国汽油总量为1750万吨,从质量上看,目前各国普通级汽油一般为91~92(RON),优质汽油为96~98(RON)。
为了满足日益严格的市场需求,催化裂化工艺技术也在进一步发展和改进.本设计是对催化裂化反应-再生及分馏系统进行工艺上的设计与分析。
1.2催化裂化技术发展状况
80年代以来,催化裂化技术的进展主要体现在两个方面:
①开发成功掺炼渣油(常压渣油或减压渣油)的渣油催化裂化技术(称为渣油FCC,简写为RFCC);②催化裂化家族技术,包括多产低碳烯烃的DCC技术,多产异构烯烃的MIO技术和最大量生产汽油、液化气的MGG技术。
目前国外新开发的重油催化裂化技术有:
渣油加氢处理(VRDS)一催化裂化(FCC)组合工艺”、毫秒催化裂化工艺(MSCC)双台组合循环裂化床工艺、剂油短接触工艺(SCT)、双提升管工艺、两段渣油改质技术等等。
国内灵活双效催化裂化工艺(FDFCC)、VRFCC技术、催化裂化(MIP)新技术等等。
下面以两个技术说明一下:
(1)渣油加氢处理一催化裂化组合工艺基础研究的应用—— 它是在对加氢处理和催化裂化两种工艺过程的特点、原料产品性质及加工方案进行深入研究的基础上,经过理论分析,实验室及工业试验后开发出的一种新的石油加工工艺——“渣油加氢处理(VRDS)一催化裂化(FCC)组合工艺”。
流化催化裂化(FCC)是现代化炼油厂用来改质重质瓦斯油和渣油的核心技术,是炼厂获取经济效益的一种重要方法。
据统计,截止到1999年1月1日,全球原油加工能力为4015.48Mt/a,其中催化裂化装置的加工能力为668.37Mt/a,约占一次加工能力的16.6%,居二次加工能力的首位。
美国原油加工能力为821.13Mt/a,催化裂化能力为271Mt/a,居界第一,催化裂化占一次加工能力的比例为33.0%。
我国催化裂化能力达66.08Mt/a,约占一次加工能力的38.1%,居世界第二位。
世界RFCC装置原料中渣油的平均量为15%~20%。
从国外各大公司对原料的要求来看,残炭与金属两个指标已分别达到8%和20μg/g。
而国内渣油催化裂化原料的残炭一般达到6%,金属15μg/g,与国外水平相比,尚有潜力。
中国石化集团公司FCC装置中约80%都掺炼不同比例的渣油,平均掺渣比约为26%,1989-1997年,掺炼重质油的比例从18.52%增至43.64%。
我国大庆石蜡基原油具有残炭低、金属含量低的特点,其减压渣油的残炭为8.95%,金属为7μg/g,所以大庆减压渣油可以直接进行催化裂化。
前郭炼油厂已进行了大庆全减压渣油催化裂化的尝试,但未见国外全减压渣油催化裂化的报道
(2)两段提升管催化裂化(TSRFCC)新技术——TSRFCC可大幅度提高原料的转化深度,同比加工能力增加20~30%;显著改善产品分布,轻油收率提高2~3个百分点,液收率提高3~4个百分点,干气和焦炭产率大大降低;产品质量得到明显改善,汽油烯烃含量下降20个百分点以上,柴油密度减小、十六烷值提高,汽油和柴油的硫含量都明显降低。
采用两段提升管催化裂化技术可使企业获得巨大的经济效益。
1.3设计的主要内容
1.设计专题的经济、技术背景分析
2.工艺流程的选择
3.主要设备物料、能量衡算
4.主要设备工艺尺寸计算
5.装置工艺流程、再生器、反应器提升管工艺流程图的绘制
6.再生器、反应器提升管、分馏塔能量衡算
第二章工艺叙述
工艺流程说明
该装置工艺流程分四个系统如图2-1
2.1反应-再生系统
原料油经过加热汽化后进入提升管反应器进行裂化。
提升管中催化剂处于稀相流化输送状态,反应产物和催化剂进入沉降器,并经汽提段用过热水蒸气汽提,再经旋风分离器分离后,反应产物从反应系统进入分馏系统,催化剂沉降到再生器。
在再生器中用空气使催化剂流化,并且烧去催化剂表面的焦炭。
烟气经旋风分离器和催化剂分离后离开装置,使催化剂在装置中循环使用。
反应系统主要由反应器和再生器组成。
原料油在装有催化剂的反应器中裂化,催化剂表面有焦炭沉积。
沉积的焦炭的催化剂在再生器中烧焦进行再生,再生后的催化剂返回反应器重新使用。
反应器主要为提升管,再生器为流化床。
再生器的主要作用是:
烧去催化剂上因反应而生成的积炭,使催化剂的活性得以恢复。
再生用空气由主风机供给,空气通过再生器下面的辅助燃烧室及分布管进入。
在反应系统中加入水蒸汽其作用为:
(1)雾化——从提升管底部进入使油气雾化,分散,与催化剂充分接触;
(2)预提升——在提升管中输送油气;
(3)汽提——从沉降器底部汽提段进入,使催化剂颗粒间和颗粒内的油气汽提,减少油气损失和焦炭生成量,从而减少再生器负荷。
汽提水蒸气占总水蒸气量的大部分。
(4)吹扫、松动——反应器、再生器某些部位加入少量水蒸气防止催化剂堆积、堵塞。
2.2分馏系统
由反应器来的反应产物油气从底部进入分馏塔,经塔底部的脱过热段后在分馏段分割成几个中间产品:
塔顶为富气,汽油,侧线有轻柴油,重柴油和回炼油,塔底产品为油浆。
轻、重柴油分别经汽提后,再经换热,冷却后出装置。
分馏系统主要设备是分馏塔,裂化产物在分馏塔中分馏成各种馏分的油品。
塔顶汽在粗汽油分离罐中分成粗汽油和富气。
分馏塔具有的特点有:
(1)分馏塔底部设有脱过热段,用经过冷却的油浆把油气冷却到饱和状态并洗下夹带的粉尘以便进行分馏和避免堵塞塔盘。
(2)设有多个循环回流:
塔顶循环回流、一至两个中段回流、油浆回流。
(3)塔顶回流采用循环回流而不用冷回流。
2.3吸收—稳定系统
该系统主要由吸收塔,再吸收塔,解吸塔及稳定塔组成。
从分馏塔顶油气分离器出来的富气中带有汽油部分,而粗汽油中则溶解有C3,C4组分。
吸收—稳定系统的作用就是利用吸收和精馏方法,将富气和粗汽油分离成干气(C2),液化气(C3、C4)和蒸汽压合格的稳定汽油。
第三章设计原始数据
3.1处理量
100万吨/年+学号×2万吨/年即:
100+2×2=104万吨/年
3.2开工时8000小时每年
则处理量为:
104×103×104÷8000=130000kg/h
3.3原始数据及再生-反应及分馏操作条件
原料油及产品性质分别见表3-1、表3-2
产品的收率及性质见表3-3再生器操作及反应条件见表3-4、
提升管反应器操作条件表3-5催化裂化分馏塔回流取热分配见表3-6
分馏塔板形式及层数见表3-7分馏塔操作条件表见3-8
表3-1原料油及产品性质
物料,性质
稳定汽油
轻柴油
回炼油
回炼油浆
原料油
密度
0.7423
0.8707
0.8800
0.9985
0.8995
恩氏蒸馏℃
初馏点
54
199
288
224
10%
78
221
347
380
377
30%
106
257
360
425
438
50%
123
268
399
450
510
70%
137
300
431
470
550
90%
163
324
440
490
700
终馏点
183
339
465
平均相对分子量
表3-2原料油的主要性质
项目
数据
项目
数据
密度
0.8995
族组成分析/W%
馏程℃
饱和烃
62.27
初馏点
224
芳烃
25
10%
377
胶质
11.88
30%
438
沥青质
0.85
350℃馏出率/v%
7.5
重金属含量/μg×g-1
500℃馏出率/v%
49
Ni
5.99
元素组成/w%
V
4.77
C
84.81
Na
0.32
H
12.85
Fe
5.91
硫/w%
0.77
残炭,W%
5.38
表3-3产品产率(质量分数)
产品
产率%
流量,t/h
干气
5.0
液化气
11.0
稳定汽油
48.0
轻柴油
21.2
油浆
6.0
焦炭
8.0
损失
0.8
原料油
100.0
表3-4再生器操作条件
项目
数据
备注
再生器顶部压力/MPa
0.200
主风入再生器温度/℃
162
再生器密相温度/℃
700
待生剂温度/℃
大气温度/℃
25
大气压力/MPa
0.1013
空气相对湿度/%
70
烟气组成(体)/%
CO2
14.2
CO
0.2
O2
4.0
焦碳组成/H/C,质
待生剂含碳量/%
1.10
再生剂含碳量/%
0.02
烧焦碳量/t/h
表3-5提升管反应器操作条件
项目
数据
备注
提升管出口温度/℃
505
沉降器顶部压力/MPa
0.200
原料预热温度/℃
235
回炼油进反应器温度/℃
265
回炼油浆进反应器温度/℃
350
催化剂活性/%
60.0
剂油比
6.0
反应时间/S
3.0
回炼比
0.5
催化剂循环量/t×h-1
原料进料量/t×h-1
回炼油/回炼油浆
1:
0.25
表3-6催化裂化分馏塔回流取热分配(参考)
物料
顶循环回流
一中循环回流
二中循环回流
油浆循环回流
取热比例%
15~20
15~20
15~20
40~50
备注
表3-7分馏塔塔板形式及层数(参考)
序号
塔段
塔板形式
层数
1
油浆换热段
人字挡板或园型挡板
6~8
2
回炼油抽出以下
固舌形
2
3
回炼油抽出口上至
一中回流抽出下口下
固舌形,条形浮阀,填料
10~12
4
一中回流
固舌形,条形浮阀,填料
3~4
5
轻柴油抽出以上至
顶循环回流段抽出下
固舌形,筛孔,条形浮阀,填料
8~9
6
循环回流段
固舌形,条形浮阀,填料
3~4
分馏塔总塔板数
28~32
表3-8催化裂化分馏塔操作条件(参考)
序号
物料
温度/
℃
压力/
MPa
塔板位置
塔板类型
1
分馏塔塔顶油气
125
0.255
30
浮阀
2
顶循环回流
100
30
浮阀
3
顶循环回流出塔
160
27
浮阀
4
富吸收油(再吸收油,视为轻柴油)返分馏塔
120
20
浮阀
5
轻柴油抽出
220
19
浮阀
6
一中回流返回
160
18
浮阀
7
一中回流抽出
275
16
固舌形
8
回炼油返回
210
5
固舌形
9
回炼油抽出
265
2
固舌形
10
油浆循环回流返回
270
1
固舌形
11
回炼油浆抽出
350
塔底
12
循环/外排油浆抽出
350
塔底
13
轻柴油汽提蒸汽温度
250
1.0
14
反应油气进分馏塔
500
塔底
第四章反应-再生系统工艺计算
4.1再生系统
4.1.1燃烧计算
再生器物料平衡是计算待再生催化剂进入再生器后焦炭燃的产物,焦炭量按新鲜原料油的8%计算:
焦炭产量=130000×8%=10400Kg/h=866.67kmol/h
H/C=[8.93–0.425×(CO2+O2)-0.257C0]/(CO2+CO)
=1.1436/14.4
=0.0794
烧碳量=10400×92.66%=9634.98kg/h
烧氢量=10400–9634.98=765.02kg/h
已知烟气组成(体):
CO2:
CO=14.2:
0.2=71:
1
根据:
C+O2=CO22C+O2=2CO2H2+O2=2H2O
生成CO2的碳为9634.98×71/(71+1)=9501.80kg/h=791.76kmol/h
生成CO的碳为:
9634.98–9501.16=133.82kg/g=11.15kmol/h
生成CO2的耗氧量为:
791.76×1=791.76kmol/h
生成CO的耗氧量为:
11.15×1/2=5.575kmol/h
生成H2O的耗氧量为:
765.02×1/2×1/2=191.26kmol/h
则理论的耗氧量为:
791.76+5.575+191.26=988.59kmol/h
理论氮为:
988.59×79/21=3718.98kmol/h
所以,可知燃料产物为791.76kmol/hCO2,11.15kmol/hCO,
191.26×2=382.52kmol/hH2O。
理论干烟气包括燃烧生成CO2和CO和理论氮则总量:
791.76+11.15+3718.98=4521.89kmol/h
已知烟气中过剩氧为4%所以过剩空气摩尔百分数:
(4×100/21)×100%=19%
过剩空气:
(过剩空气百分数/1-过剩空气百分数)×理论干烟气气量
=0.19/(1–0.19)×4521.89=1060.69kmol/h
过剩氧气:
1060.69×0.21=222.74kmol/h
过剩空气含氮:
1060.69–222.89=837.95kmol/h
实际干烟气为理论生成干烟气和过剩空气组成:
4521.69+1060.69=5582.67kmol/h
理论干空气用量:
988.59+3718.98+1060.69=5768.26kmol/h
已知空气的相对湿度为70%,温度为25ºC,根据
《石油加工工艺》中册图6-29查得:
水蒸气/干空气=0.016(摩尔)
空气中含水蒸气为:
0.016×5768.26=92.29kmol/h
湿空气:
5768.26+92.29=5860.55kmol/h
已知回炼比0.5,剂油比为6.0
回炼油浆:
130000×0.5=65000kg/h
剂/油=剂/(130000+26000)=6.0
所以催化剂循环量为:
6.0×(130000+26000)=1170000kg/h
依据每吨催化剂带入1kg水汽,则催化剂循环量为1170t/h则带入
1170kg/h=65kmol/h
吹扫松动水蒸气量:
500kg/h=27.78kmol/h
水蒸气为湿度与生成水及本身带入和吹扫的水蒸气之和
烟气中水蒸气为:
92.29+27.78+65+382.52=567.59kmol/h
综上所述可以得出再生器烟气流量及组成如表4-1。
表4-1再生器烟气流量及组成
组分
分子量
流量(kmo/h)
摩尔百分数
湿烟气
干烟气
O2
32
222.74
3.62
3.99
CO
28
11.15
0.18
0.20
CO2
44
791.76
12.88
14.18
N2
28
4556.93
74.13
81.23
干烟气
30
5582.67
100
总水蒸气
18
567.59
9.19
湿烟气
29
6150.16
100
4.1.2热量平衡
根据Qi=NiCPit
式中:
Qi:
热流量KJ/hNi:
物流Ni的流量kmol/h
CPi:
物流i的热容kJ/(kmol·ºC)t:
温度ºC
4.1.2.1热流量入方
(1)干空气t=162ºCCP=44.6814kJ/kmol·ºC
Q1=5768.26×44.681×162=41.75×106kJ/h
(2)湿空气中水蒸气C水=34.542kJ/kmol·ºC
Q2=92.29×34.542×162=0.52×106kJ/h
(3)催化剂带入水蒸气Q3=65×35.6×505=1.17×106kJ/h
(4)吹扫、松动水蒸气Q4=27.78×34.6×280=0.27×106kJ/h
(5)烧焦炭Q5=866.67×15.6×505=6.83×106kJ/h
(6)催化剂Q6
(7)燃烧热Q7,j=NjΔH查石油馏分焓图得
CO2Q7,1=791.76×407.0×103=322×106kJ/h
COQ7,2=11.15×122.7×103=1.37×106kJ/h
H2OQ7,3=382.52×239.4×103=91.58×106kJ/h
∑Q7=(322+1.37+91.58)×106=414.98×106kJ/h
共计Q=∑Qi=(41.75+0.52+1.17+0.27+6.83+414.95)×106+Q6
=465.49×106+Q6
4.1.2.3热流量出方
干烟气Q,1=5582.67×32.58×700=127.32×106kJ/h
(1)水蒸气Q,2=564.81×39.877×700=15.77×106kJ/h
(2)催化剂带出水蒸气Q,3=65×39.877×700=1.81×106kJ/h
(3)脱附热,脱附热为燃烧热的11.5%
Q,4=414.98×106×0.115=47.72×106kJ/h
(4)热损失=582×烧碳量
Q,5=582×9634.98=5.6×106kJ/h
(5)催化剂Q,6
出方的能量:
∑Q,=(15.77+47.72+5.6+127.32)×106+Q,6
=196.41×106+Q,6
根据热量平衡式:
465.46×106+Q6=196.41×106+Q,6
催化剂升温所需的热量:
Q=Q6ˊ-Q6=269.05×106kJ/h
4.1.3催化剂循环量
催化剂平均比热为1.086kJ/(kg·ºC)。
设催化剂循环量为W㎏/h
1.086W×(700-505)=269.05×106W=1.27×106kg/h
因为回炼比0.5,所以剂油比为:
1.27×106/[130000×(1+0.5)]=6.5
综上所述可得再生器物料平衡如表4-2、热平衡