浴室柜涂装过程的问题及分析解决.docx
《浴室柜涂装过程的问题及分析解决.docx》由会员分享,可在线阅读,更多相关《浴室柜涂装过程的问题及分析解决.docx(41页珍藏版)》请在冰豆网上搜索。
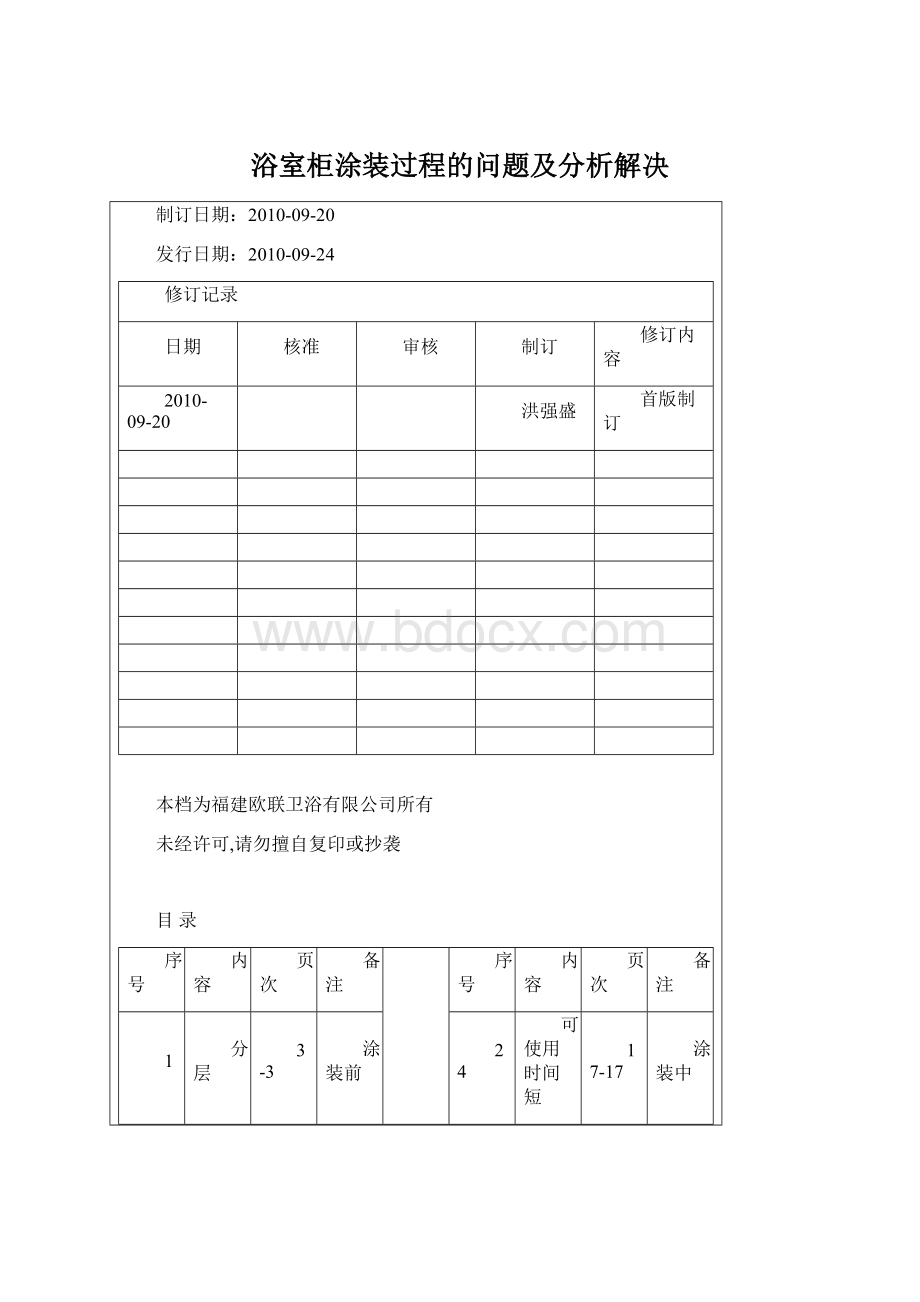
浴室柜涂装过程的问题及分析解决
制订日期:
2010-09-20
发行日期:
2010-09-24
修订记录
日期
核准
审核
制订
修订内容
2010-09-20
洪强盛
首版制订
本档为福建欧联卫浴有限公司所有
未经许可,请勿擅自复印或抄袭
目录
序号
内容
页次
备注
序号
内容
页次
备注
1
分层
3-3
涂装前
24
可使用时间短
17-17
涂装中
2
结皮
3-3
涂装前
25
出枪不爽
17-18
涂装中
3
结块
3-4
涂装前
26
配好油后分层
18-18
涂装中
4
固化
4-4
涂装前
27
露底
18-18
涂装中
5
流动性差
4-5
涂装前
28
颜色不一样
18-19
涂装中
6
变稠
5-5
涂装前
29
透明度差
19-19
涂装后
7
沉淀
5-6
涂装前
30
干燥不良
19-20
涂装后
8
变黄
6-6
涂装前
31
耐划痕性差
20-20
涂装后
9
多泡
6-7
涂装前
32
附着力差
20-21
涂装后
10
混浊
7-7
涂装前
33
耐划痕性差
21-22
涂装后
11
走油(缩孔)
7-8
涂装中
34
起雾
22-22
涂装后
12
起泡
8-9
涂装中
35
六裂
22-23
涂装后
13
针孔
9-10
涂装中
36
返白
23-23
涂装后
14
桔皮
10-11
涂装中
37
光泽不匀
23-24
涂装后
15
起皱
11-12
涂装中
38
粗糙手感差
24-25
涂装后
16
流挂
12-12
涂装中
39
变黄
25-25
涂装后
17
咬底
12-13
涂装中
40
丰满度差
25-26
涂装后
18
回粘
13-14
涂装中
41
底漆不好打磨
26-26
涂装后
19
起粒
14-15
涂装中
42
PE底不干
26-27
涂装后
20
发白
15-15
涂装中
43
变脆
27-27
涂装后
21
发花和浮色、渗色
15-15
涂装中
44
漆膜塌陷
27-28
涂装后
22
刷痕
15-16
涂装中
45
失光
28-28
涂装后
23
相溶性差
16-17
施工中
46
气味
28-29
涂装后
一、分层
现象
油漆分成明显的的上下层,上层为清液,下层为粉状物,用器具搅动底层无结块现象,此现象多出现在亚光漆系列.
原因分析:
a)亚光漆出现此现象多为亚光漆及相关粉料比重偏大,而防沉剂的量有些不够;
b)防沉剂搭配不合理;
c)生产过程中防沉剂没有分散好,防沉剂没有起到应有的作用;
d)溶剂的溶解力不够;
e)亮光清漆出现分层是由于树脂体系不相溶。
解决方法:
a)亚光漆使用前要充分搅拌均匀;
b)改善防沉体系,增加防沉剂的用量;
c)加入防沉剂后要高速分散;
d)增加溶剂或稀释的溶解力;
e)亮光清漆出现这种情况,先不要使用、搅拌均匀后,按正常配比配好漆。
若无异常,可小面积喷涂试验,若正常,则可使用;若出现异常情况,比如产生混浊、呈豆腐脑状或喷涂后起桔皮、失光、起泡等,请立即停止施工。
二、结皮
现象
油漆表现出现一层胶状漆膜,用手摸不粘手,此层漆皮厚度可以从几毫米到几厘米不等。
原因分析:
1)桶盖密封不严,空气进入后对其表面进行氧化形成结皮;
2)包装时油漆温度过高,盖上桶盖后,里面的热空气冷后形成水珠浮在油漆表面与油漆反应而结成;
3)油漆粘度过高,颜填料含量较多,催干剂过多而结皮,且放置时间越长皮膜越厚;
4)油漆中混合了气干型树脂,比如说PU漆中混入了PE漆,经过存放后会形成很硬的结块。
解决方法:
1)漆桶应盖严,油漆应存放在阴凉干燥处,避免暴晒;
2)油漆包装时温度不宜过高,应控制在60度以下;
3)粘度和含粉量高的产品尽量先用,贮存时间不要太长。
在生产过程中增加分散剂的用量;
4)严禁PU与PE系列混用;
5)使用时去掉皮块,然后在漆面上倒一层同类型稀料,盖紧桶盖。
三、结块
现象
油漆中出现不均匀的或大或小的块状物,有的如棉絮状。
原因分析:
1)分散过程中没有分散均匀;
2)包装过滤时过滤袋破裂;
3)包装时将缸底和缸沿的沉积油漆铲入了包装桶内;
4)油漆中混入了硝化棉之的东西,由于溶解力不够而形成结块。
解决方法:
1)分散过程中一定要注意分散均匀,严格按工艺操作,必要时补加分散剂;
2)包装时注意过滤袋是否破裂。
3)缸底和缸沿的沉积油漆不能直接铲入包装桶内,要过滤后包装或铲进分散缸中等下次生产时加入;
4)生产时不要混入加硝化棉之类的产品;
5)若出现结块情况,可以先搅匀,然后配漆,用120-200目过滤布过滤后进行喷涂。
四、固化
现象:
多指固化剂,其在桶内己成固态,完全不能使用。
原因分析:
1)桶子密封不好,空气进入使其固化;
2)桶内有水、油之类,与固化剂反应而固化;
3)溶剂的溶解力不够;
4)固含太低;
5)固化剂中混入了含羟基的物质,与其发生反应;
6)固化剂包装太少,放置时间长,与桶内空气反应固化。
解决方法:
1)桶子要密封好,存放在阴凉干燥的地方,避免暴晒和受潮;
2)包装前检查桶内是否干净;
3)增加强溶剂的用量;
4)不要使用固含低的固化剂;
5)使用的所有村料中不能有含羟基的物质;
6)包装时不要包得太少。
五、流动性差
现象
油漆基本不流动,表面又未结皮,搅拌后恢复正常,但停止搅拌一段时间后又恢复原样。
原因分析:
1)油漆含粉料量太高,树脂含量少,不易流动;
2)触变剂加量比较大,油漆触变性大,正因为触变性大,才起到了很好的防沉和防流挂效果;
3)油漆中溶剂溶解力不够;
4)气温太低。
解决方法:
1)使用含粉量少的产品,或要生产中加入分散剂以降低粘度来提高流动性;
2)使用时多搅拌一下即可正常使用;
3)增加油漆中强溶剂的含量;
4)提高施工环境的温度。
六、变稠
现象
油漆在贮存过程中出现稠度明显增加的现象、严重时会出现固化或胶化状态,
此现象主要出现在固化剂、PE漆和PE稀释剂。
原因分析:
1)包装桶密封不严,有空气进入;
2)包装桶内含有水油之类物质或配料所用的溶剂含水量太高;
3)放置时间太长,超过了保质期;
4)贮存过程中温度太高,油漆产生自聚而增稠。
解决方法:
1)检查包装桶的密封性能;
2)控制配料所用溶剂的含水量,检查包装桶内是否有水、油之类物质;
3)产品到货后不要放置太长时间,尽早用掉、不要超过保质期;
4)不要将油漆贮存在高温环境中,尽量贮存在阴凉通风干燥的室内;
5)若出现油漆增稠情况,请立即停止使用该产品,并通知本公司技术部进行调查处理。
七、沉淀
现象
油漆开桶后外观状态基本正常,但是器具搅动时能够感觉到底层有结块现象,或
是底层含粉量明显比上层多,严重时结块部分无法搅动。
此现象多出现在亚光面
漆和底漆方面,也有部分色漆会出现这种情况。
原因分析:
①亚光漆和底漆出现这种情况主要是油漆含粉量高,粉的比重偏大而沉淀;
②防沉剂加量太少;
③防沉体系搭配不合理;
④防沉剂和粉料冒雨分散好,没有起到应有的效果;
⑤油漆中溶剂的溶解力不够,不能使基料完全的溶解而形成稳定均匀的状态;
⑥油漆存放时间太长,超过保质期,防沉体系失去效果。
解决方法:
①尽量选用防沉性好的粉料;
②加大防沉剂的用量;
③重新选择防沉体系;
④注意分散过程,严格按照生产工艺操作,必要时加大分散剂的用量;
⑤合理选择溶剂,加强溶剂溶解力。
八、变黄
现象
油漆外观呈明显的黄色,严重时会变成黑色,这种情况主要出现在硝基漆、腻
子和含硝化棉的油漆中。
原因分析:
①硝化棉质量太差,易变黄;
②包装罐密封不好,遇空气氧化而变黄;
③所用溶剂含水量太高、造成变质;
④油漆中混入了酸性物质,与硝化棉反应而变黄;
⑤氨类催干剂加的太多;
⑥包装罐生锈,导致油漆变黄;
⑦存放时间太长,超过了保质期。
解决方法:
①选用好的硝化棉,生产过程中补加抗氧剂;
②检查包装罐的密封情况;
③控制溶剂的含水量;
④生产或贮存过程中应避免混入其它杂质;
⑤硝化棉体系中尽量不要使用氨类催干剂;
⑥生锈的包装罐不得用来装成品;
⑦油漆要尽快用完,不要超过保质期,油漆应存放在阴凉干燥通风的地方;
⑧出现变黄情况,若较轻微,请根据您的要求选择是否继续使用,若颜色较深,
请立即停止使用该产品。
九、多泡
油漆开盖后表面有气泡,少则几个,多则厚厚的一层,直接影响油漆的外观。
原因分析:
①消泡体系搭配不好;
②消泡剂加量不够;
③油气粘度太高;
④分散时间太长。
解决方法:
①调整消泡体系;
②增加消泡剂的用量;
③降低油漆的粘度;
④注意分散工艺,分散后期采用低速分散;
⑤在包装过程中采用过滤包装,然后在表面洒上溶剂以助消泡;
⑥如果表面气泡太多,可以将上层刮掉,调漆后过滤喷涂。
十、混浊
现象
多出现在亮光清面漆中,油漆呈不透明状或半透明,也有的亚光清面
漆呈乳白状。
原因分析:
①油漆中的树脂与树脂之间相溶性差,比如书醇酸树脂中混入了丙烯树脂,就
会形成混浊情况;
②油漆中的助剂搭配不合理,助剂与树脂的相溶性不好;
③油漆了混入了水分导致混浊或是温度太低,部分助剂和树脂析出;
④油漆中混入了含粉料的物质;
⑤溶剂体系搭配不好,溶解力太差。
解决方法:
①树脂在使用前先要试验其相溶性;
②选用相溶性好的助剂;
③生产中控制溶剂的含水量,包装中检查包装是否进水,运输与贮存过
程中避免进水,油漆应存放在不低于5℃之通风干燥的地方;
④生产与包装中要严格按工艺操作;
⑤选择溶解力好的溶剂;
⑥出现此类情况,请立即停止使用该产品,与本公司技术部联系,确认处理措施。
十一、走油(缩孔)
现象
⒈涂料施工后,漆膜在流平过程中出现回缩,成小圆形地裸露出底材或底层;
⒉涂料施工后表面形成凹坑状如火山口,能明显看到在凹穴的中央有异物粒子存
在,象鱼眼,一般不显露底材;
⒊涂料施工后,漆膜回缩,使较大面积的底材裸露出来,亦称为“抽缩”;
⒋施涂后的涂膜,边角处特别厚,涂成样板看上去犹如镜框;
⒌涂料施工后,在底材的边角处涂膜回缩,导致该处涂膜较薄,甚至露底;
⒍同一种油漆修色,用另一种油漆碰湿罩面,出现油窝。
原因分析:
⒈湿膜上下部分表面张力不同,在成膜过程中,当上层湿膜的表面张力低于下层
湿膜的表面张力时就会发生缩孔;
⒉底材冒雨处理好,底漆冒雨打磨或打磨得太光滑;
⒊底材被油污、蜡、皂类、酸、碱之类污染,涂膜对底材润湿不良;
⒋湿膜中沾附了异物粒子,把周围的涂料排斥而形成凹坑;
⒌油水分离器中水分太多;
⒍施工环境被污染,或周围有重大污染源,如加油站、废弃物焚烧点、其它类
型化工厂等;
⒎油漆本身有问题,如溶剂搭配不当,硅油类逐级加量大等;
⒏稀释剂使用不当,由于边角处的湿膜溶剂挥发得比别处快,使该处成膜物的
浓度高于别处,温度低于别处,形成高表面张力区,迫使邻近的涂料流向边
角,加厚了该处涂膜,形成镜框效果;
⒐喷房或晾干房中风速太大,湿膜被风带动形成走油;
⒑油漆相溶性不好,两种油漆之间存在相排斥成分;涂料的粘度过高或过低;
⒒空气压力太大,喷枪于工件距离太近;
⒓施工时温度太低。
解决方法:
⒈配方设计时尽量选用表面张力接近的树脂与溶剂搭配;
⒉底材要处理好,层与层之间一定要打磨,但不能打磨得太光滑;
⒊如果底材被油污和蜡之类污染,要彻底用水磨,必要时用稀释剂擦洗干净;
⒋喷涂前放掉油水分离器中的水分;
⒌油漆配好后用200目左右的滤布过滤喷涂;
⒍检查是否有污染源,清理施工环境,喷涂前可洒部分水于地面和墙面,必要时
要远离污染源;
⒎配方设计时合理使用溶剂和助剂,可加大润湿剂的用量,以降低涂膜的表面张力;
⒏使用配套稀释剂;
⒐油漆施工后,不要放于空气流通太快的地方;
⒑若用一种油漆修色,采用湿碰湿工艺,最好用同系列油漆罩面。
让给采用不
同的两种油漆,最好等到色漆完全干透后再打磨罩面漆;
⒒调配好涂料的粘度;
⒓调整空气压力,以及喷枪和工件之间的距离;喷涂距离一般为15cm-30cm、
⒔温度过低时停止施工。
十二、起泡
现象
⒈油漆在刷涂时所产生的气泡,在涂膜干后也无法消除,打磨后再喷漆会形成一
个个的凹坑;
⒉油漆在表干过程中产生饿气泡,此现象相对于刷涂时产生的气泡要小,干后成
痱子状态;
⒊油漆喷好后,在使用过程中,涂膜与底层脱离,形成气泡。
原因分析:
⒈油漆本身消泡性太差;
⒉底材目眼不深,气泡很难逸出;
⒊底材含水量太高,不经干燥处理就施工;
⒋油漆是个粘度太高,气泡无法逸出;
⒌贴皮或贴纸用的胶水太差,与油漆反应生成气泡;
⒍稀释剂选用不合理,挥发太快;
⒎被涂物表面有油污,水分;
⒏涂层过厚,溶剂挥发困难;
⒐固化剂加量太大;
⒑稀释剂加量太少,施工粘度高,反应生成的气泡难挥发出;
⒒调漆时搅拌太长;
⒓稀释剂挥发速度太快;
⒔油漆喷涂时,每遍之间的间隔时间不合理;
⒕施工工具含有水油之类物质;
⒖被涂物表面温度太高;
⒗在高温高湿的环境西施工;
⒘调好油后静止时间不够就施工;
⒙干燥后放在高温,高湿中太久。
解决方法:
⒈增加消泡剂,以提高油漆本身的消泡性能;
⒉对底材进行打磨处理,然后刷涂一遍封闭底,让其渗透到木眼中;
⒊控制木材的含水率,要求木材含水率与当地平衡含水率相当;
⒋适当的增加稀释剂的用量;
⒌选用质量好一点的胶水和木皮;
⒍调整稀释剂的干速,可以适当添加慢干水;
⒎使被涂物表面保持干爽洁净;
⒏不要一次性喷涂太厚,一次涂层不超过30um;
⒐按正常配比添加固化剂;
⒑适当的增加稀释剂的用量;
⒒调漆时搅拌时间不要太长;
⒓在稀释剂中补加慢干水,一般加量为稀物的3%-15%;
⒔油漆每半个“十”字之间的间隔时间应控制在10分钟以内,或者等底层完全干
透后再喷上面一层;
⒕检查施工设备是否含有水油之类物质,并彻底清洗;
十三、针孔
现象
涂膜干燥后,在涂膜表面形成针的状小孔,严重时针孔大小似皮革的毛孔状表面,
还有一种现象是打磨后出现白色小点,喷完面漆后形成针孔。
原因分析:
⒈涂料粘度过高,搅拌时间过长,空气进入涂料中释放不出来;
⒉被涂工件表面有油污、水分;
⒊喷枪压力大、口径小、喷涂距离太远;
⒋涂层太厚,溶剂挥发困难;
⒌在高温高湿的环境中施工;
⒍固化剂加量太大;
⒎稀释剂挥发速度太快,涂膜中有气泡逸出;
⒏底层产生气泡后,经打磨形成针孔,再喷面漆时面漆往下渗,而针孔中的空气
要往外逸,形成针孔;
⒐PE漆的兰、白水加量太大;
⒑油漆配好后放置时间太长,已产生絮凝状,喷涂后极易产生针孔;
⒒涂料或稀释剂中含水量过高.
解决方法:
⒈涂料粘度调配适当,调好油后静止5-10分钟左右再使用;
⒉将工件表面处理干净后再施工,必要时用稀释剂清洗一遍;
⒊调整空气压力,掌握好喷涂的距离,一般距离被涂物件表面15-30cm左右;
⒋不要一次性喷涂太厚,一次涂层不超过30um;
⒌在高温高湿的环境中施工时,应补加慢干水,慢干水的加量为稀物的3%-15%
之间,若情况严重,请停止施工;
⒍按正常配比添加固化剂;
⒎若底层打磨时出现白点状,则将其表面清洗干净,如何用腻子或水灰
刮涂一遍,打磨后再喷底漆,或者是清洗干净后用含粉量多一点的底漆喷涂一遍,
干后轻磨,再喷面漆;
⒏PE漆根据施工配比表添加兰白水,若冬天出现慢干时,可适当加大兰、白水的
用量,但最多不能超过正常配比的1.5倍;
⒐一次性不要配太多的油漆,配好的油漆尽快用完,底漆一般在2小时左右,面漆
在3小时作用用完不包括PE底、PE底配好后在20分钟内就要用完、;
⒑选用配套稀释剂,生产过程中严格控制溶剂的含水量。
十四、桔皮
现象
1.漆膜未能充分流动形成的似桔皮的痕迹:
2.漆膜流平性不好,干后形成似桔皮状的痕迹,此现象在亮光漆中尤其明显。
原因分析:
1.溶剂挥发太快,涂料流平不好:
2.涂料自身流平差;
3.喷抢嘴口径太大或太小;
4.喷涂距离不当,空气压力不足,涂料雾化不好;
5.被涂物件的温度过高;
6.施工场所风速过快,将湿膜吹动形成桔皮,如湿膜放在排风扇下吹干等;
7.油漆配好后放置时间太长,已接近絮凝状;
8.油漆施工粘度太高;
9.被涂物件表面处理不平整,影响涂料的流平性;
10.油漆本省的流平助剂加量太大,影响最终流平;
11.底漆的硬度不够,干后有点塌陷;
解决方法:
1.合理选用稀释剂,必要时补加适量慢干水,慢干水的加量一般为稀释剂的3%-15%;
2.改进涂料本省的流平性,可增加流平剂等;
3.选择合适口径的喷抢;
4.调整喷抢的空气压力和雾化效果,调整好喷涂距离,一般距被涂物表面的距离为15-30cm;
5.降低被涂物表面的温度;
6.施工场所控制通风,以不影响漆膜的流平为宜;
7.配好的油漆要及时用完,底漆一般在2小时以内,面漆在3小时以内用完;
8.适当调低涂料的施工粘度。
十五、起皱
现象
施涂喻底层上的涂膜,在干燥过程中会形成局部或全部的皱纹状涂膜,此病态称之为起皱,
也有的会出现如砂纸状表面,此现象多出现在亚光漆系列。
原因分析:
1.底面干速不一致,面干底不干,即易起皱。
2.涂料粘度过大,涂层过厚;
3.涂料配方有问题,所选用的亚粉为表面经过蜡处理的亚粉,与树脂相溶性不好;
4.采取不易挥发性稀料,残留溶剂太多,或者是稀释剂搭配不当,挥发速度没有调整好,
前期挥发的是强溶解力溶剂,造成后阶段树脂析出;
5.漆膜干燥时间不够,骤然高温加速干燥所致;
6.催干剂加量太大。
解决方法:
1.注意使用底层快干、面层干速稍慢的涂料;
2.施工涂料粘度要适中,且控制好涂层厚度,一次性不要喷涂太厚;
3.选用合适的涂料,喷涂时可采用间隔法,若出现起皱现象,可先喷涂一遍,待其基本表干时再碰一枪,
以此方法层层施工,既能达到想要的涂膜厚度又不会出现起皱;
4.选用配套稀料,防止树脂析出;
5.选用少量高沸点溶剂,并让湿膜在常温下风干时间稍长些,防止湿膜温度过高而引起涂膜起皱;
6.合理选用催干剂,且加量不能超过千分之五。
十六、流挂
现象
油漆涂饰垂直物体表面,在涂膜形成过程中,湿膜受到重力的影响朝下流动。
形成不均匀的涂膜,称为流挂。
原因:
1.涂料粘度底,涂层过厚;
2.喷抢口径太大,出油量调得太大;
3.喷涂空气压力不均;
4.涂料中含有密度大的颜料搅拌不均;
5.被涂物表面过于光滑;
6.油漆干速太慢;
7.稀料选用不合理,比如冬季施工时用稀释剂;
8.空气温度太低也会造成流挂。
解决方法:
1.调配好涂料施工粘度,涂层厚度一次不能超过30um;
2.调整喷涂距离,喷涂距离为15-30cm,并控制好适当的喷抢移动速度;
3.根据实际情况选用适当口径的喷抢,一般喷底漆的口径为1.5-2mm,喷面漆的口径为1.2-1.5mm,且调节好喷抢出油量;
4.施工中保持稳定的空气压力;
5.施工过程中涂料要多次充分搅拌均匀;
6.应保证被涂物表面适当的粗糙度,各层之间应仔细打磨;
7.调整油漆的干速,可增加一些防流挂的触变助剂;
8.选用配套稀释剂;
9.提高施工场所温度。
十七、咬底
现象
当涂装施工第一道面漆于底漆表面时,会发现底层涂膜过分变软以至起皱,此种现象俗称咬底。
原因分析:
1.底层与面层不配套,如硝基底漆上涂聚酯面漆;
2.底层未干就涂面层涂料;
3.油漆涂的太厚,面干底不干;
4.腻子涂的太厚,面层溶剂太强将腻子溶解;
5.固化剂配比不够,漆膜交联反应不完全;
6.油漆配好后放置时间太长,有时甚至增调后再往里面加稀料,然后再喷;
7.所用稀释剂不配套,含有大量的醇类溶剂,而醇与固化剂反应的速度特别快,
会消耗部分固化剂,造成固化剂量不够,形成慢干而导致咬底;
8.有谢咬底现象出现在边角和沟槽的边沿上,以及上面的部分地方。
这种现象主要原因是底材没有处理好,底漆漆膜太薄,
当贴纸后有些地方由于凹陷,纸张无法贴实,当喷完底漆后,没有贴牢的纸张部分往外鼓,然后打磨极易打穿或只剩下极
薄的漆膜,当再喷面漆时,溶剂将纸张咬起,形成咬底现象,特别是边角与沟槽边线易打穿而咬底,所以打磨时应特别注意;
9.冬天施工由于气温低,干速慢,易出现咬底现象;而在每年的3、4、5月份,由于北方已到换季时节,已停止供暖,而
配套固化剂也由快干固化剂改为普通固化剂,很多家具厂还按以前的施工方法和间隔时间去做,所以这一段
时间极易出现咬底现象;
解决方法:
1.底层与面层涂料注意配套使用;
2.同一类型的涂料,底层实干后再涂面层涂料;
3.涂膜不宜太厚,一次涂层不超过30um;
4.若底层为腻子,请不要刮涂太厚,以填平木眼为宜,且将木材表面腻子打磨干净后再喷底漆;
5.按正常配比添加固化剂,不要担心因起泡而少加固化剂;
6.油漆配好后请尽快用完,底漆一般2小时内用完,面漆3小时以内用完;
7.选用配套稀释剂;
8.贴纸前最好对底材进行封闭处理,可以刮灰、刮腻子或喷底漆等,将底材填平后再打磨贴纸,在极易出现咬底的边角与
沟槽线上,尽量多喷些油漆,打膜时注意不要打的太透;
9.冬季施工时可适当提高室内温度,改用快干固化剂,而在换季过程中,请最好准备快干固化剂和普通固化剂两种,
以适应天气变化,且适当的延长施工时间;
十八、回粘
现象
涂料施工后,在干燥成膜的短时间内又会出现漆膜手感不爽、指触有发粘现象。
原因分析:
1.涂层未干就重叠或包装;
2.固化剂加量不够或没加固化剂,导致反应不完全或完全不反应;
3.慢干溶剂太多,溶剂挥发不完全;
4.被涂物表面被油污和蜡之类污染,没有进行有效处理;
5.底漆未干透就喷漆,造成面干底不干,里面溶剂无法挥发而使漆膜发软;
6.施工场所通风不好,空气中溶剂溶度太高,漆膜中的溶剂无法挥发出来;
7.施工场所湿度过高;
8.气温太底,普通固化剂和催干剂起不了作用;
9.涂料品质不好,如NC漆中硝化棉加量太少;
10.油漆或板材存放在低温下,调油施工后因温度底而不能正常反应。
解决方法:
1.待漆膜完全干透后方可重叠或包装出货;
2.按正常配比施工;
3.选用合适的稀料,慢干溶剂不要添加过量;
4.清理被涂物表面,必要时用稀释剂擦洗一遍;
5.等底漆干透以后再喷面漆;
6.改善喷房和晾板房中的通风设施,定期对密封好的晾板房进行抽风;
7.延长干燥时间或适当加温;
8.气温太底时选用快干固化剂或提高室内温度;
9.使用优质涂料;
10.油漆应存放在10-30C之通风干燥处,板材也尽量放在温度高点的地方。
十九、起粒
现象
漆膜表