冲压项目说明书赵欢.docx
《冲压项目说明书赵欢.docx》由会员分享,可在线阅读,更多相关《冲压项目说明书赵欢.docx(15页珍藏版)》请在冰豆网上搜索。
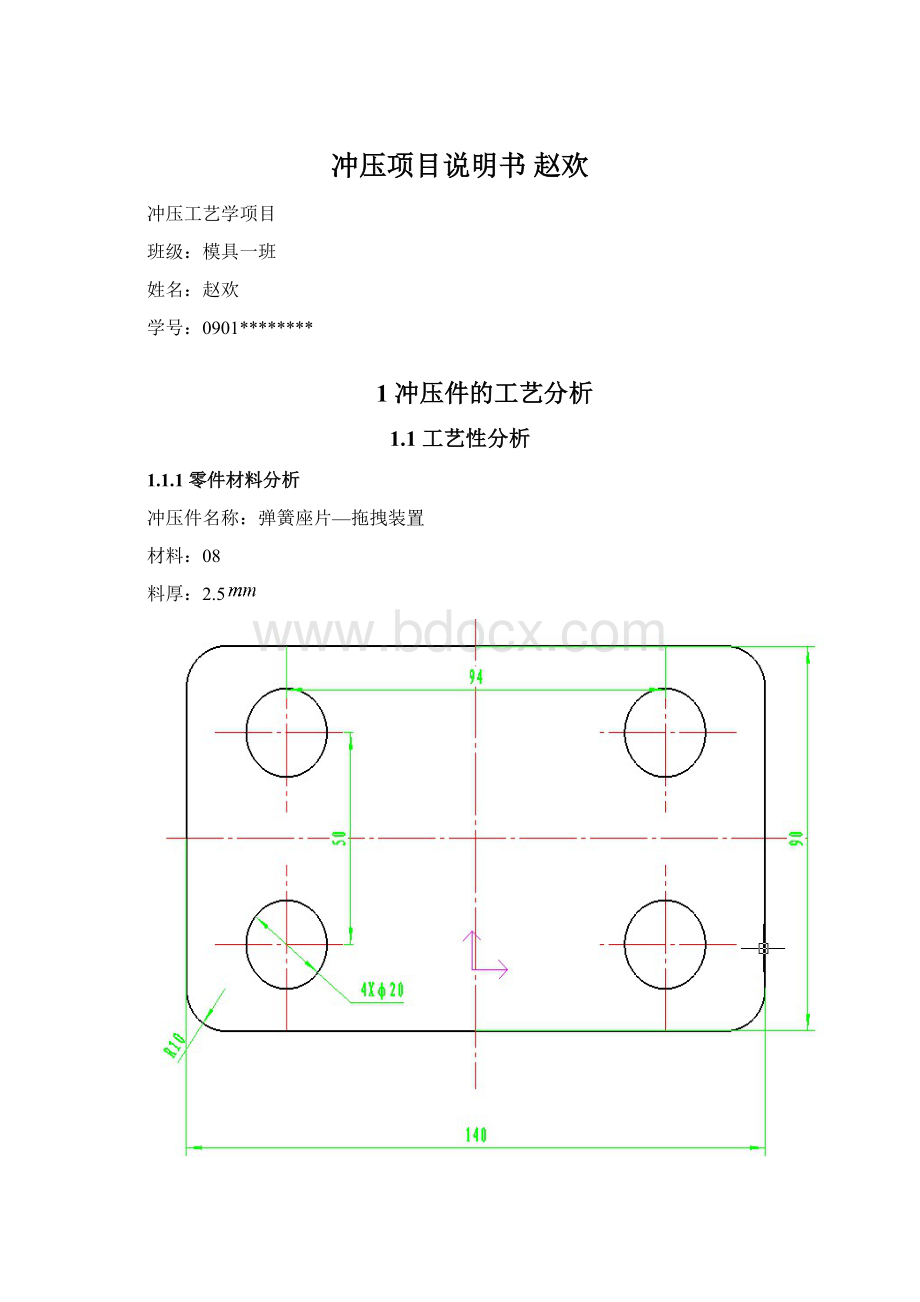
冲压项目说明书赵欢
冲压工艺学项目
班级:
模具一班
姓名:
赵欢
学号:
0901********
1冲压件的工艺分析
1.1工艺性分析
1.1.1零件材料分析
冲压件名称:
弹簧座片—拖拽装置
材料:
08
料厚:
2.5
图1.1零件图
08钢
1.材料名称:
优质碳素结构钢
2.特性及适用范围:
为极软的碳素钢,强度、硬度很低,而韧性和塑性极高,具有良好的深冲、拉延、弯曲和镦粗等冷加工性能、焊接性能。
但存在时效敏感性,淬硬性及淬透性极低。
大多轧制成高精度的薄板或冷轧钢带用以制造易加工成形,强度低的深冲压或深拉延的覆盖零件和焊接构件。
3.化学成份:
碳C:
0.05~0.12硅Si:
0.17~0.37锰Mn:
0.35~0.65硫S:
≤0.035磷P:
≤0.035铬Cr:
≤0.10镍Ni:
≤0.25铜Cu:
≤0.25
4.力学性能:
抗拉强度σb(MPa):
≥325(33)屈服强度σs(MPa):
≥195(20)伸长率δ5(%):
≥33断面收缩率ψ(%):
≥60硬度:
未热处理,≤131HB试样尺寸:
试样尺寸为25mm
1.1.2零件形状与尺寸分析
1.形状分析
冲压件的外轮廓是由四个直径相等的圆弧和四条直线组合而成的,所以曲线不多,形状规则,是简单的外部轮廓。
内部有圆孔,是规则的形状。
所以该件的冲压模具的落料模稍复杂,而冲孔模则简单.。
另外,冲裁件轮廓图形上,直线与直线用圆弧过渡。
这样不仅使模具制造简单,模具磨损慢,而且减少了模具制作工序,提高了生产效率。
2.尺寸精度
冲裁尺寸精度主要与模具的制造精度、材料的力学性能、制件的相对厚度和冲裁件的尺寸和形状有关。
一般冲裁件的尺寸精度可达IT10~IT12级,高精度可达IT8~IT10级。
但因为冲裁件的尺寸精度受模具制造精度的影响,所以冲裁件的公差等级不能太高,一般来说不高于IT11级,本次零件图上的尺寸未标注公差,查表7-3,冲裁件的精度按IT13确定,冲模制造精度按IT6~IT7确定。
1.1.3冲裁件的成型性分析
1.冲裁件的圆角
冲裁件的最小允许圆角半径与材料的厚度及种类等因素有关。
一般情况下,应使
式中R——圆角半径(
);
t——材料厚度(
)。
将冲压件厚度t=2
代入计算得知
R>(0.5~1)×2.5=1.25~2.5mm
工件的最小圆角半径为R10,满足要求。
2.最小孔直径
冲孔工件孔的尺寸不能过小,否则冲孔凸模会很快损坏或折断。
孔的极限尺寸与材料性质、料厚及孔的形状等因素有关。
一般无护套的凸模冲孔时,根据冲孔形状、材料及料厚查得,该垫片的最小凸模尺寸应满足
d≥t
d——冲孔件的孔径(mm);
t——材料厚度(mm)。
代入数据得
d≥t=2.5
工件的孔径为20,满足要求,可以冲孔。
3.冲裁件的孔间距与孔边距
冲裁件孔与孔、或孔与边缘的间距b、b1,与模具强度和寿命以及冲裁件的质量有关,其值不宜过小,一般取b≥1.5t,b1≥t本次需要冲裁的工件有四个孔,孔到边缘的距离为10,孔与孔之间的距离为15,所以满足要求。
1.2工艺方案
1.2.1工序分析
从冲件形状来看,该件需要的工序有落料、冲孔。
1.2.2方案分析
1.分析冲件外形,可以采用的模具加工方案有:
(1)单工序加工,即落料与冲孔,在两套模具上完成。
(2)复合模加工,即落料、冲孔在同一模具中进行加工,两个工序在压力机压下时一步完成。
(3)连续模加工,即落料、冲孔在一套模具中加工,但两个工序在压力机两次行程中分步进行
2.方案分析
单工序模在压力机一次行程中只能完成一道工序,若采用方案
(1),则需要做两套模具,虽然模具加工形状简单,但在很大程度上提高了成本,增长了生产周期,降低生产率,所以不采用该方案。
复合模中落料、冲孔在压力机一次行程中完成,模具结构比单工序模具稍复杂,但生产率可显著提高。
由于连续模需要导正销定位,且直径应大于2~5
,条料厚度一般不小于0.3
,否则孔的边缘可能被导正销压弯而起不到导正和定位作用,有要冲压的零件材料厚度为0.35
,属于薄料类。
另外,对于窄长形零件或落料凸模尺寸不大是,为了避免凸模强度过渡减弱,一般都不使用导正销,而改用侧刃来定距。
但若采用侧刃的话,与尺寸相对较小的冲压件来说,在很大程度上降低了材料利用率。
所以方案(3)不宜采用。
3.确定方案
经过上述分析,确定模具方案为落料、冲孔复合模。
1.4工艺计算
1.4.1材料排样与裁板宽计算
1.排样
由于冲件轮廓呈规则形式,适合采用少废料排样,所以用直排形式进行排样。
,具体方案有两种,如图
(1)
(2)
排样方法
由手册查得搭边值:
工件间a1=2.5mm;沿边a=2.8
计算材料利用率:
方案一:
η=72%
方案二:
η=74%
选用方案二
2.条料宽度的确定
由于冲裁件材料厚度为2.5
,属于较薄材料,且冲裁件尺寸不大,用导正销定位时不易保证凸模强度,所以定位零件不宜用定位销。
若采用侧刃定位,在工件尺寸不大的情况下又会极大地降低材料利用率,考虑到工件的尺寸精度要求不是太高,且落料—冲孔复合模已经可以在一定程度上保证精度要求。
所以,可直接用挡料销对料进行定位和导向,不用导正销和侧刃装置。
条料宽度的计算公式可用
B=(Dmax+2a)0-△
式中Dmax—条料宽度方向冲裁件的最大尺寸;
a—冲裁件之间的搭边值;
△—板料剪裁下的偏差;
B=90+2×2.8
=95.60-0.9mm
故条料宽度为95.6mm。
冲压工艺计算
1.冲压力的计算
考虑到模具刃部被磨损,凸模与凹模间隙不均匀和波动材料的力学性能的波动几材料的厚度偏差等各种因素的影响,实际计算冲裁力时按以下公式:
(1.6)
式中P——冲裁力(N);
L——冲裁剪切周边长度(
);
——冲裁件材料厚度(
);
——被冲材料的抗剪强度(
);
K——系数,一般取1.3。
查表得08钢的抗剪强度τ=260MPa
通过计算得到L=442.8mm;L=251.2mm
代入数据得落料力:
F落=1.3×442.8×2.5×260=374166N
F冲=1.3×251.2×2.5×260=212264N
2.卸料力、顶件力和推件力
冲裁件在冲裁过程完成后,材料会沿径向产生弹性回复,使处于凸模周边材料紧箍在凸模上。
而冲断后落如凹模的材料则因弹性回复而梗塞在凹模内。
从凸模上将工件(或废料)卸下来的力称为卸料力
;从凹模内向冲裁反方向将工件(或废料)顶出的力称为顶件力
;从凹模内顺冲裁方向将工件(或废料)推出的力称为推件力
;
卸料力、顶件力和推件力用以下经验公式进行计算:
式中——F卸、F顶、F推分别为斜料力、顶件力和推件力系数。
可由表2-10,查出K卸=0.03~0.04,取K卸=0.04;K顶=0.05;K推=0.045
代入数据得:
F卸=0.04×586430=23457.2N
F顶=0.05×586430=29321.5N
F推=5×0.045×586430=131946.75N
(1)由以上数据求和即可得出
采用弹性卸料装置和上出料方式的总冲裁力为:
F总=F+F顶+F卸=639280.7N
(2)采用刚性卸料方式和下出料方式的总冲裁力为:
F总=F+F推=718376.75N
(3)采用弹性卸料装置和上出料方式的总冲裁力为:
F总=F+F推+F卸=741833.95N
平刃冲裁时,冲裁功按以下公式计算:
(1.10)
式中
——平刃冲裁功
;
——平刃冲裁时的总冲裁力(
);
——冲裁件的材料厚度
;
——系数,取0.63。
代入数据得
⏹A=mpt/1000=0.63×586430×2.5/1000=490.77N·m
压力中心计算
冲裁合力的作用点称为冲模的压力中心。
设计冲裁模时应该使冲模的压力中心与压力机滑块的中心相重合,即冲模的模柄中心应该与冲模的压力中心一致,以保证冲裁模在压力机上正常、平衡地进行冲制工作。
由于本冲件是关于原点对称的,圆孔的压力中心就在圆心处,所以该冲裁模的压力中心就是圆心,即对称中心。
冲模工作零件计算
1.刃口部分尺寸计算
由表查得,该冲裁模初使用间隙为:
,Zmin=0.33mm
Zmax=0.39mm
计算前需要将冲压件的尺寸换算成标准的标注形式。
冲压件外轮廓形状较复杂,标注尺寸家谱多,且零件材料较薄,所以落料模采用凸凹模配制加工的方法。
冲孔模用分开加工的方法。
故:
(1)落料
Cd=(Cmin+0.5
)±
/8
式中
Cd——凹模刃口尺寸(
);
A,C——工件基本尺寸(
);
——工件公差(
);
——凹模制造公差(
)。
由表查得:
x=0.5。
①圆角半径10
凹模刃口尺寸:
A1d=(A1-x△)0+
=(10-0.5×0.33)0+
=9.8350+0.036mm
凸模刃口尺寸:
②长度140
凹模刃口尺寸:
A2d=(A2-x△)0+
=(140-0.5×0.63)0+
=139.6850+0.036mm
凸模刃口尺寸:
=
③宽度90
凹模刃口尺寸:
A3d=(A3-x△)0+
=(90-0.5×0.54)0+
=89.730+0.036mm
凸模刃口尺寸:
落料凸模各部分尺寸保证模具间隙进行加工。
(2)冲孔直径20
凸模刃口尺寸:
dp=(dmin+x△)
=(20+0.5×0.33)0-0.024=20.1650-0.024mm
凹模刃口尺寸:
dd=(dp+Zmin)
=(20.165+0.33)0+0.036=20.4950+0.036mm
(3)空心距
2.外形尺寸
冲裁模的外形尺寸主要是厚度与高度方向的尺寸。
其高度尺寸在保证强度要求的情况下可以根据标准模架上各板厚来确定,厚度则通过强度计算确定。
(1)凹模尺寸
凹模厚度:
H=kb=140
0.28=39.2mm。
凹模壁厚:
c≥(1.5~2)H=(58.8~78.4)mm。
取c=60mm
凹模板边长:
L=b+2c=140+60
2=260mm
查标准JB/T—6743.1—94:
凹模板宽度为240mm。
凹模外形为:
。
经调整,凹模各部分尺寸见图1.4。
凹模
(2)凸模尺寸
凸模长度根据模架确定,具体尺寸如图1.5。
凸模
(3)凸凹模尺寸
高度方向尺寸标准模架中已经给出,其余部分尺寸如图1.6。
凸凹模
2确定模具总体结构
2.1确定模具结构形式
2.1.1模具类型选择
本设计选用落料-冲孔复合模。
复合模分有顺装和倒装两种形式,其中顺装模是将凸凹模装在上模部分,卸料板装在下模。
倒装模是将凸凹模装在下模部分,卸料板装在下模,这种结构不必特别清除废料,操作方便。
由于本冲压件较小,采用的是自动操作方式,所以选用倒装式复合模。
2.1.2操作方式选择
由于本冲压件料薄且窄,所以为提高生产率采用自动化操作方式,自动从右侧送料。
2.1.3定位方式选择
定位零件的作用是使毛坯或半成品在模具冲裁时
保证正确的位置。
定位包括纵向定位和横向定位。
纵
向定位是确定条料送进的距离,称为挡料;横向定位
是为了保持条料正确的送进方向,称为导料。
常见的
定位零件有:
定位钉、定位板、挡料销、导正销、侧
刃、导尺等。
本套模具中选择较为简单的固定挡料销
进行挡料和导向(图2.1)。
图2.1固定挡料
2.1.4卸料装置和推件装置
1.卸料装置
卸料分固定卸料、弹性卸料和废料切刀形式。
固定卸料板一般用于卸料力大或冲裁厚度较大的零件。
这里选用弹性卸料方式,弹性卸料板具有卸料和压料的双重作用
2.推件装置
推件装置可把工件从凹模口中推出。
2.1.5导向装置
模具采用导柱导套进行导向,零件尺寸可采用标准模架中所给尺寸。
2.2确定压力中心位置
从模具结构选择与零件形状分析可知,模具是对称的结构,所以其压力中心就是模块中心。
4模具结构分析
4.1模具结构特点
本套模具采用倒装式复合模结构,冲孔废料可以直接从模具写的废料口掉出,模具周围清洁,更重要的是避免了人手工取出废料带来的安全隐患。
卸料板在下模上,选择应用广泛的橡胶作为弹性元件。
另外,卡在凹模口中的成型零件通过顶件装置被推出。
4.2注意事项
在模具制造与装模过程中需要注意的有:
1.落料的凸凹模采用配合加工,最大与最小间隙分别为Zmax=0.39mm,Zmin=0.33mm。
2.冲孔的凸凹模分开加工,间隙值为0.33mm。
3.上下模座平行度不大于0.8mm。
4.模柄中心线对上模板垂直度小于1mm。
5.导柱距下模板底面的距离小于1mm,导套距上模板上顶面距离小于1mm。
6.橡胶的预压缩量为1mm。