连铸用结晶器保护渣的最新动向.docx
《连铸用结晶器保护渣的最新动向.docx》由会员分享,可在线阅读,更多相关《连铸用结晶器保护渣的最新动向.docx(6页珍藏版)》请在冰豆网上搜索。
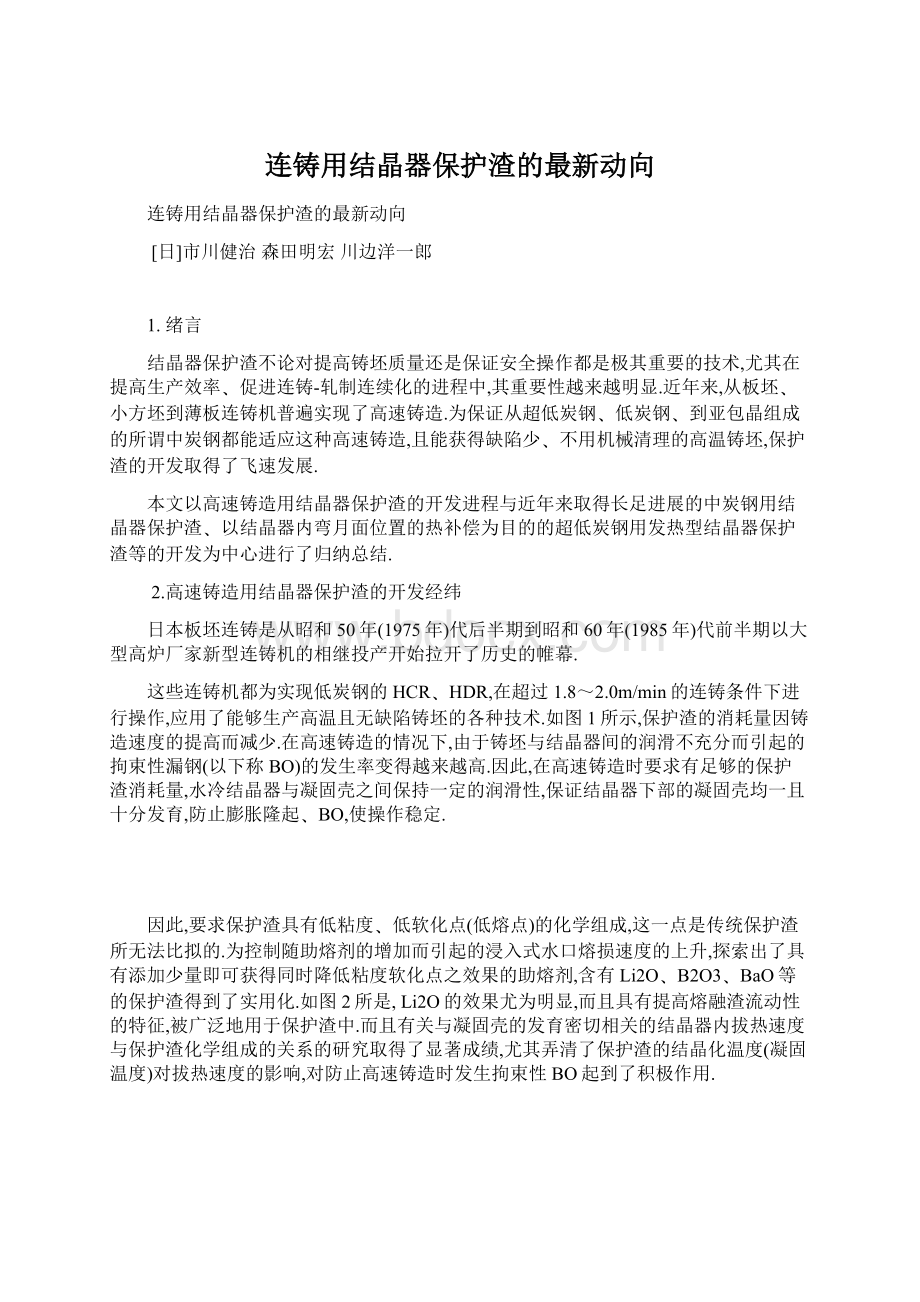
连铸用结晶器保护渣的最新动向
连铸用结晶器保护渣的最新动向
[日]市川健治森田明宏川边洋一郎
1.绪言
结晶器保护渣不论对提高铸坯质量还是保证安全操作都是极其重要的技术,尤其在提高生产效率﹑促进连铸-轧制连续化的进程中,其重要性越来越明显.近年来,从板坯﹑小方坯到薄板连铸机普遍实现了高速铸造.为保证从超低炭钢﹑低炭钢﹑到亚包晶组成的所谓中炭钢都能适应这种高速铸造,且能获得缺陷少﹑不用机械清理的高温铸坯,保护渣的开发取得了飞速发展.
本文以高速铸造用结晶器保护渣的开发进程与近年来取得长足进展的中炭钢用结晶器保护渣﹑以结晶器内弯月面位置的热补偿为目的的超低炭钢用发热型结晶器保护渣等的开发为中心进行了归纳总结.
2.高速铸造用结晶器保护渣的开发经纬
日本板坯连铸是从昭和50年(1975年)代后半期到昭和60年(1985年)代前半期以大型高炉厂家新型连铸机的相继投产开始拉开了历史的帷幕.
这些连铸机都为实现低炭钢的HCR﹑HDR,在超过1.8~2.0m/min的连铸条件下进行操作,应用了能够生产高温且无缺陷铸坯的各种技术.如图1所示,保护渣的消耗量因铸造速度的提高而减少.在高速铸造的情况下,由于铸坯与结晶器间的润滑不充分而引起的拘束性漏钢(以下称BO)的发生率变得越来越高.因此,在高速铸造时要求有足够的保护渣消耗量,水冷结晶器与凝固壳之间保持一定的润滑性,保证结晶器下部的凝固壳均一且十分发育,防止膨胀隆起﹑BO,使操作稳定.
因此,要求保护渣具有低粘度﹑低软化点(低熔点)的化学组成,这一点是传统保护渣所无法比拟的.为控制随助熔剂的增加而引起的浸入式水口熔损速度的上升,探索出了具有添加少量即可获得同时降低粘度软化点之效果的助熔剂,含有Li2O﹑B2O3﹑BaO等的保护渣得到了实用化.如图2所是,Li2O的效果尤为明显,而且具有提高熔融渣流动性的特征,被广泛地用于保护渣中.而且有关与凝固壳的发育密切相关的结晶器内拔热速度与保护渣化学组成的关系的研究取得了显著成绩,尤其弄清了保护渣的结晶化温度(凝固温度)对拔热速度的影响,对防止高速铸造时发生拘束性BO起到了积极作用.
与低炭钢相比,由于中炭钢的断裂敏感性强,所以其高速铸造化的进程相对迟缓,但对保护渣渣膜的行为结晶器拔热速度影响的研究也在推进.充分考虑拔热速度的质量设计已成为可能,无断裂缺陷铸坯的高速铸造已经实现.
目前,厚板钢种也采用了高速铸造技术,而且也出现了最高铸造速度达到2.0m/min的连铸机.
为减少渗炭分层等超低炭钢特有的铸坯缺陷,以发热型为中心对超低炭钢用保护渣进行了多方面的改良和开发.在铸造速度方面,由于各钢铁公司均采用几乎与低炭钢相同的速度进行铸造,所以采用的保护渣也与低炭钢同样是低粘度低软化点化学组成的保护渣.
但是,由于近年来用户对超低炭钢的要求越来越严格,加之近1~2年间新增设的连铸机都是以超过2.0m/min的高速铸造为方向,以往设计的低拈度保护渣在铸造过程中容易被卷入钢中,造成保护渣性铸坯缺陷.为解决这一新的问题,以低炭钢及超低炭钢为对象的新的适应高速铸造的保护渣目前正在锐意开发.其最终质量的确立虽尚需一定时间,但为防止保护渣在铸造过程中被卷入钢中,其基本开发方向应该是高粘度高表面张力的保护渣。
3.低炭钢用结晶器保护渣
在以C=~0.04%的低炭钢高速铸造为方向的昭和50年(1975年)代后半期,能够适应铸造速度超过2.0m/min的保护渣尚未开发出来,当时普遍担心因消耗量不足﹑发生拘束性BO。
因此,作为高速铸造用保护渣,为确保其消耗量,低粘度、低软化点(低熔点)的化学组成是必需的,而且,考虑到因脱氧生成物Al2O3的增加等产生的化学组成变化、随化学组成变化而产生的粘度等特性变化以及确保结晶器下端的凝固壳具有充分的厚度等,低C/S、低结晶化温度的高速铸造用保护渣得到了开发。
随着各种操作条件的改善,即使铸造速度超过2.0m/min,也能保证足够的消耗量与润滑性,没有拘束性BO的稳定操作得以实现。
图3表示的是连连浇时保护渣中Al2O3的变化情况。
由于低C/S、低Al2O3、低Fe2O3的保护渣N随着Al2O3的增加粘度上升幅度变小,随着连连浇的进行,Al2O3的浓度不再提高,能够确保稳定的消耗量,所以稳定的操作得以实现。
图4表示的是低炭钢铸造时粘度、结晶器温度对结晶器内拔热速度的影响。
粘度、结晶化温度均对结晶器内拔热速度产生影响。
图5表示的是低炭钢铸造时铸坯单位表面积的结晶器内拔热速度与铸坯断裂的关系。
低炭钢断裂敏感性小,从确保结晶器下端凝固壳的观点来看,保持结晶器内的高拔热应该是一个方向,但过剩的拔热有时也造成铸坯断裂。
所以设计保护渣时必须保证获得足够的拔热速度。
表1所示的是具有代表性的保护渣品质。
其特征是低粘度、低软化点、低C/S、低Al2O3组成、低结晶化温度。
4.中炭钢用结晶器保护渣
所谓的亚包晶领域(C=0.09~0.16wt%)中炭钢的高速铸造、无机械清理化的最大障碍是拘束性BO、铸坯断裂(纵裂、角裂)。
毋庸置疑,操作方面需要采取相应的措施。
与此同时,结晶器保护渣的品质设计也相当重要。
尤其是通过保护渣特性的调整,控制形成于结晶器与凝固壳之间的保护渣渣膜更为重要。
在前期文集中曾发表过题为“保护渣渣膜的行为与对结晶器内拔热速度的影响”的报告,阐述了为确保低粘度化下的玻璃层落下速度、高结晶化温度下的结晶层厚、防止粘结性漏钢,在充分保证保护渣消耗量的基础上,使结晶器内均匀且缓冷却化、降低纵裂等断裂性缺陷的品质设计思想。
这种设计思想最初是在板坯连铸上确立的,其后扩展到异型坯连铸、大方坯连铸、小方坯连铸,目前已广泛应用于从0.4m/min左右的低速连铸到2.0m/min以上高速铸造的中炭钢保护渣浇铸。
图6表示的是CaO/SiO2对结晶化温度的影响。
保护渣结晶化时的初晶是枪晶石(3CaO·2SiO2·CaF2),F、Al2O3等也有影响,但C/S的影响最大。
图7表示粘度与结晶化温度对中炭钢铸造时保护渣消耗量的影响。
粘度、结晶化粘度对保护渣的影响很大,越是高粘度、高结晶化温度的保护渣,其消耗量越少,特别是粘度的影响尤为显著。
图8表示粘度、结晶化温度对结晶器内拔热速度的影响。
越是高结晶化温度、低消耗量的保护渣,结晶器内的拔热速度越小,结晶化温度对拔热速度的影响尤为显著。
如果结晶化温度特别高,即使消耗量多,拔热速度也小。
即通过低粘度、高结晶化温度,在充分保证消耗量的状态下,可实现结晶器内的缓冷却化。
其结果可使断裂性缺陷锐减,不仅板坯连铸如此,异型坯连铸、大方坯连铸也能获得同样效果。
表2表示的是具有代表性的品质。
由于结晶化温度高,所以C/S在1.2以上。
如图9所示,与以同一铸造速度为对象的低炭钢用保护渣相比较粘度设定得低。
大方坯、小方坯连铸不象板坯、异型坯连铸那样容易出现断裂问题,所以结晶化温度低的品质大多都能适用。
5.超低炭钢用结晶器保护渣
C=30ppm以下的超低炭钢的高速铸造、无机械清理化的障碍与低炭钢同样是以拘束性BO、夹渣、气孔为代表的表面缺陷与渗炭。
另外,由于钢水粘度高,所以操作中要求弯月面钢水流速大,从而导致容易出现因保护渣卷入钢水中而引起的缺陷。
该钢种除了在操作方面应采取相应措施外,结晶器保护渣的品质设计也至关重要。
铸坯表层出现的气体、氧化物缺陷是因为脱氧生成物、保护渣、Ar等吹入气体在结晶器内弯月面部爪状初期凝固壳被捕捉所造成的。
因此,为减少这些表面缺陷,弯月面的热补偿至关重要。
于是,超越传统的保温概念,赋予其热供给源机能的发热型保护渣开始应用。
发热型保护渣如图10所示具有发热组成(作为发热剂的金属与特殊氧化剂),可获得巨大发热反应。
另外显示出与传统产品具有同样的良好的熔化效果。
图11表示的是从下面加热,在保持1200℃的熔融渣上投入发热成分量不同的保护渣时的熔融渣温度变化情况。
通过添加发热成分,发现不仅渣温度的下降减少,在短时间内温度还能恢复。
这种发热成分量根据使用条件、使用目的设计。
作为防止渗炭的对策,减少游离炭量、使用难以渗炭的原料、保证炭原料顺利燃烧、确保足够的熔渣层厚度等均有良好效果。
图12表示的是炭原料对渗炭速度的影响。
不同种类的炭原料渗炭速度也不同。
渗炭的主要原因是保护渣未熔层中的炭与钢水的接触,控制渗炭的最有效方法是使用渗炭速度慢的炭原料。
作为减少因保护渣卷入引起的铸坯缺陷的对策,采用适当形状的浸入式水后、灵活运用电磁力以控制结晶器内钢水流动等措施已被广泛运用。
另一方面,关于保护渣的开发也取得了一定进展。
这种保护渣的开发方向是高粘度化、高表面张力化,其目的在于控制保护渣液滴进入钢水中。
只是由于高粘度化与消耗量减少相伴,所以需要重新认识以往被定为下限值的0.3kg/m2,针对低消耗量采取相应的措施。
关于粘结性漏钢的防止已在灵活运用BO警报装置等改善操作技术方面作了有益的探讨。
表3表示的是具有代表性的保护渣品质
开浇渣为确保熔渣层、防止渗炭而不使用炭原料。
另外,为了给钢水温度最易下降的头坯弯月面位置进行热补偿,发热成分的添加量也设计得高达30%。
该品质的保护渣在保证初期凝固壳的健全方面起到了重要作用。
不仅减少了夹渣、气泡,而且减少了断裂。
这种开浇渣也被用于超低炭钢以外的钢种。
本体渣则在最小限度内使用1%的渗炭速度慢的炭原料以调整熔化速度,并根据使用条件将发热成分的添加量设定在10~30%。
在连铸过程中,使用不同的保护渣对最终产品质量的影响也不同。
图13表示的是使用发热型保护渣生产的卷材与使用传统保护渣生产的卷材不合格率的调查结果。
通过使用发热型保护渣,分层等缺陷大幅度减少,不合格率也减少了一半。
6.今后的课题
作为今后研究的课题有如下几个:
1)提高汽车用表面处理钢板等所谓高级冷轧钢种质量的措施
提高以高级冷轧钢种为核心的钢种质量,当务之急是要确立高粘度、高表面张力等难
以卷入结晶器内钢水中的保护渣质量。
尤其是要确立具有发热性品质的保护渣。
2)包括薄板坯连铸在内,如何适应高速铸造钢种的多样化
今后,包括薄板坯连铸在内,世界范围内的连铸都将朝着高速铸造的方向发展。
尤其
是适应高速铸造的钢种越来越多,必须开发适应各种连铸机特性、连铸条件的保护渣。
3)控制保护渣对浸入式水口的熔损、延长其使用寿命的措施。
已经明确,作为保护渣控制浸入式水口熔损的最有效方法是提高其C/S、降低F成分。
只是F成分降低后需要有其它助熔剂替代,而且随着F成分的降低,保护渣的结晶化行为变化很大。
因此,就目前而言,高C/S、低F保护渣的用途还受到一定的限制。
即首先实现在铸坯断裂问题少、能够控制浸入式水口熔损主要因素的条件下实用化。
板坯连铸用保护渣品质设计的原则是铸坯质量第一。
但今后为提高生产效率,必须提高连连浇的炉次,那末在设计保护渣品质时也要充分考虑控制浸入式水口的熔损。
4)减少连铸机受腐蚀的措施
F对连铸机的腐蚀影响很大,主要原因是保护渣中的F溶解于2次冷却水中造成PH
值下降。
作为防止连铸机受腐蚀的措施,降低保护渣中的F成分是必需的,采用高C/S的保护渣也是一种好方法。
目前,这种保护渣正在大方坯连铸中进行试验。
如何将其推广到板坯及其它连铸方面是今后研究的重要课题。
5)自动供渣、改善操作环境的措施
作为节省人力、改善作业环境的措施就是采用机械自动供渣,开发适应高速铸造的颗
粒保护渣。
保护渣的各种行为是一种复杂的现象,又不能直接观察,因此目前还不能完全解释清楚。
最近,对熔融、熔化行为、渣膜行为、结晶器内的拔热行为、与钢水反应等的研究很活跃,利用数据分析的理论探讨也在进行。
相信今后这种研究将取得更大进展。
7.结束语
本文以高速铸造用结晶器保护渣的开发过程与近年来取得长足进步的保护渣开发为中心进行了归纳总结。
今后,连铸操作技术将朝着高质量、高效率的方向发展。
保护渣的熔融、流入、拔热等各种行为通过更深一步的研究也将逐渐被解释清楚。
在此基础上,将有望开发出适应高级冷轧钢种等的高质量化、包括薄板连铸在内的适应高速铸造钢种的多样化、通过控制保护渣对浸入式水口造成的熔损而延长其使用寿命、减少连铸机的腐蚀、自动供渣、改善作业环境等要求的保护渣。