铝行业发展现状分析.docx
《铝行业发展现状分析.docx》由会员分享,可在线阅读,更多相关《铝行业发展现状分析.docx(4页珍藏版)》请在冰豆网上搜索。
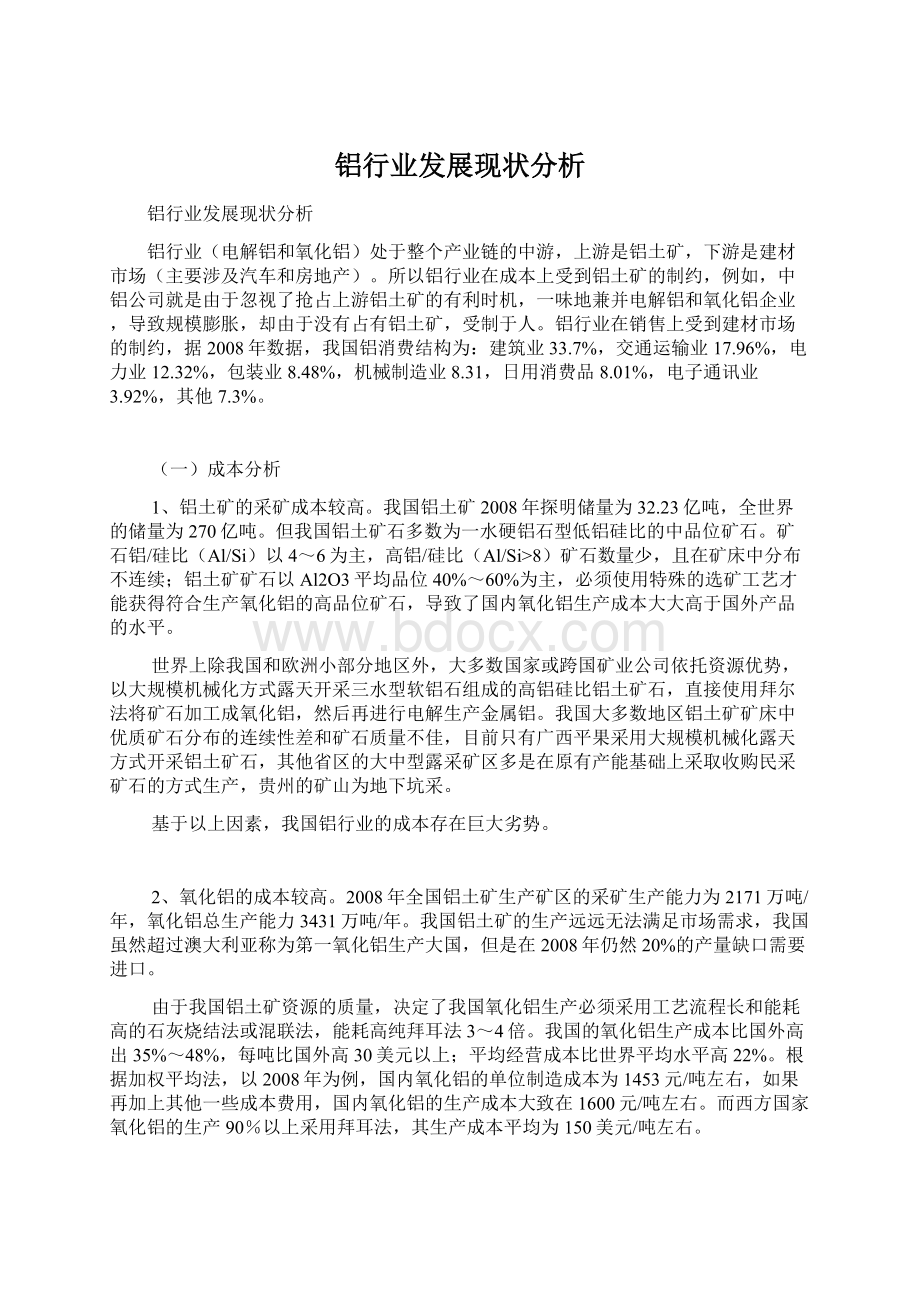
铝行业发展现状分析
铝行业发展现状分析
铝行业(电解铝和氧化铝)处于整个产业链的中游,上游是铝土矿,下游是建材市场(主要涉及汽车和房地产)。
所以铝行业在成本上受到铝土矿的制约,例如,中铝公司就是由于忽视了抢占上游铝土矿的有利时机,一味地兼并电解铝和氧化铝企业,导致规模膨胀,却由于没有占有铝土矿,受制于人。
铝行业在销售上受到建材市场的制约,据2008年数据,我国铝消费结构为:
建筑业33.7%,交通运输业17.96%,电力业12.32%,包装业8.48%,机械制造业8.31,日用消费品8.01%,电子通讯业3.92%,其他7.3%。
(一)成本分析
1、铝土矿的采矿成本较高。
我国铝土矿2008年探明储量为32.23亿吨,全世界的储量为270亿吨。
但我国铝土矿石多数为一水硬铝石型低铝硅比的中品位矿石。
矿石铝/硅比(Al/Si)以4~6为主,高铝/硅比(Al/Si>8)矿石数量少,且在矿床中分布不连续;铝土矿矿石以Al2O3平均品位40%~60%为主,必须使用特殊的选矿工艺才能获得符合生产氧化铝的高品位矿石,导致了国内氧化铝生产成本大大高于国外产品的水平。
世界上除我国和欧洲小部分地区外,大多数国家或跨国矿业公司依托资源优势,以大规模机械化方式露天开采三水型软铝石组成的高铝硅比铝土矿石,直接使用拜尔法将矿石加工成氧化铝,然后再进行电解生产金属铝。
我国大多数地区铝土矿矿床中优质矿石分布的连续性差和矿石质量不佳,目前只有广西平果采用大规模机械化露天方式开采铝土矿石,其他省区的大中型露采矿区多是在原有产能基础上采取收购民采矿石的方式生产,贵州的矿山为地下坑采。
基于以上因素,我国铝行业的成本存在巨大劣势。
2、氧化铝的成本较高。
2008年全国铝土矿生产矿区的采矿生产能力为2171万吨/年,氧化铝总生产能力3431万吨/年。
我国铝土矿的生产远远无法满足市场需求,我国虽然超过澳大利亚称为第一氧化铝生产大国,但是在2008年仍然20%的产量缺口需要进口。
由于我国铝土矿资源的质量,决定了我国氧化铝生产必须采用工艺流程长和能耗高的石灰烧结法或混联法,能耗高纯拜耳法3~4倍。
我国的氧化铝生产成本比国外高出35%~48%,每吨比国外高30美元以上;平均经营成本比世界平均水平高22%。
根据加权平均法,以2008年为例,国内氧化铝的单位制造成本为1453元/吨左右,如果再加上其他一些成本费用,国内氧化铝的生产成本大致在1600元/吨左右。
而西方国家氧化铝的生产90%以上采用拜耳法,其生产成本平均为150美元/吨左右。
氧化铝成本约占铝锭生产成本的28%-34%。
一般来讲,每生产一吨铝锭需耗费2吨氧化铝,随着越来越多的生产厂家采用先进技术和加强技术改造,目前大多数厂家生产一吨铝锭耗费氧化铝约在1.93吨~1.98吨之间,虽然这一比例随着各个厂家的努力还会有下降的趋势,但下降的幅度会很小,我们可理解为常量。
这样,氧化铝的价格变化就决定了这方面的成本。
目前,氧化铝的市场价格维持在2100元上下,我们取每生产一吨铝锭耗费1.95吨铝锭为常数,可以计算出目前氧化铝所耗的费用为4100元左右。
(资料补充:
由于国际氧化铝市场高度集中,全球大部分氧化铝(80%~90%)都通过长期合约的方式进行销售,因此可供现货市场买卖的氧化铝少之又少。
以中国为例,1997年以前,中国氧化铝缺口部分主要在国际现货市场上购买,没有长期合约。
到了1997年,中国有色与美铝签订了30年长期供货合约,每年40万吨,价格根据LME原铝价格的一定比例定价。
近年来,中国电解铝生产规模的不断扩大,导致了国内对氧化铝需求也在不断增长,目前约有三分之二的进口氧化铝需要从现货市场购买。
中国在国际市场上大量采购氧化铝,直接推动了国际氧化铝价格的大幅上涨,据统计,2004年中国共进口氧化铝587万吨,同比增长4.8%,平均进口价为340美元(国外氧化铝生产的现金成本不到120美元),简单测算,仅2004年氧化铝直接进口就多支付国外氧化铝供应商的成本高达数10亿人民币。
不断上涨的氧化铝价格使电解铝生产企业生产成本大幅上升,经济效益大幅下滑,多数企业陷入微利或亏损。
)
3、用电成本较高。
电解铝产业又称“电老虎”行业,占全国用电量的10%左右,这一部分的成本涉及到两个变量,一个是每一度电的电价高低;另外一个变量为每生产出一吨铝锭所耗费的电量的多少。
电解铝行业耗电量很大,由于生产技术装备水平的差异,各生产企业每生产一吨铝锭所耗费的电量差异较大,目前国内大体在14000kwh-16000kwh之间,我们取大多数厂家耗电量的中间值15000kwh,而近两年国内电解铝生产厂家的平均电价为0.34元左右,则每吨铝锭的电费成本为5100元左右。
西方国家铝锭生产的经验显示,当电费超过铝生产成本的30%时被认为是危险的生产。
我国电费成本占铝锭生产成本的40%左右,和西方国家电费成本占25%相比相差较远。
(资料补充:
以2004年为例,2004年中国铝厂吨铝平均耗电为14683kwh/t,比2003年减少了347kwh/t,是中国电解铝行业平均综合交流电耗降幅最大的一年。
尽管如此,由于中国属能源短缺国家,数次上调的电价使铝企业的平均电价上升至0.355元/KWh以上,比2003年上升了近4分/KWh,这意味着铝企业吨铝的生产成本增加了600元。
目前电解铝行业要求降低电价的呼声很高,但这涉及到电力部门,需要国家统筹安排。
在希望电力部门降低电价的同时,许多电解铝生产企业积极进行铝电合营,全行业呈现一种铝厂办小电厂、大电厂办小铝厂、电解铝厂和电厂相互参股的趋势。
降低电费成本的另一个途径是降低单位铝锭的耗电量。
电解铝的电解槽型分为自焙槽和预焙槽,两者相比较,自焙槽具有工艺成熟、投资省、见效快的特点,老企业和新上马的中小企业一般都采用这种电解槽,目前我国铝锭产量中的一半是由这种工艺较为落后的自焙槽生产的,但这种工艺存在较明显的缺陷:
首先是烟气敞开排放,严重危害生态环境和工人的身心健康;其次是技术指标落后、电耗高;第三是产量小、自动化程度低。
预焙槽则刚好相反,具有环境污染小、技术指标高、电耗较低、自动化程度高等特点。
仅耗电量一项,每生产一吨铝锭预焙槽比自焙槽少耗电1000度以上。
)
4、阳极碳块(阳极糊)成本。
目前世界上的电解槽的槽型分为自焙槽和预焙槽。
相对应地,自焙槽所用的碳素阳极称为阳极糊,预焙槽所用的碳素阳极称为阳极碳块,由于阳极碳块要先经过焙烧,多了些工序,因此阳极碳块的价格相对较高。
目前,一吨阳极糊的市场价格在1400元左右,而一吨阳极碳块的价格则在3000元左右,每生产一吨铝锭自焙槽耗阳极糊0。
54吨,预焙槽耗碳块0。
6吨,据此得出一吨铝锭所耗费的阳极糊成本为770元,阳极碳块为1800元,我们取两者的平均值,这方面的成本为1280元。
综合分析:
目前国内每生产一吨铝锭所耗费的社会平均原材料成本为250(氟化盐等)+4100(氧化铝成本)+5100(电费成本)+1280(阳极糊成本)=10730元。
这仅仅是制造成本当中最基本的直接材料费用,而一个企业要维持简单的社会再生产必须得支付企业人员的工资、管理费用、财务费用和销售费用、摊销机器厂房折旧费用、银行贷款利息及税金等,这些都应该计入企业的生产成本。
目前国内企业这方面的成本占整个铝锭生产成本的20%左右。
与国际市场铝锭的成本进行比较,俄罗斯的铝锭平均成本为1700美元/吨,而我国的铝锭的平均成本为2100美元/吨。
我国的电解铝生产成本竞争上非常吃亏。
(二)市场分析
1、市场需求的周期循环。
2000年以前,不论是国际市场,还是国内市场铝行业的市场都比较低迷,价格长期低位徘徊。
2000年以后,我国随着房地产、汽车市场的不断发展,对铝的需要日益增加,铝价上扬,铝行业快速膨胀扩张,这种发展趋势到2008年达到高潮。
2008年末次债危机的爆发,包括房地产市场内的铝行业下游行业陷入低迷,需求萎缩,铝价暴跌,电解铝的暴利期结束。
2009年,随着政府4万亿投资,市场需求有所恢复。
但是世界经济存在二次探底的隐忧,2010年全球铝市场萎缩300万吨,加上我国产业调整以“调结构”为主的政策导向,铝行业的下游行业不存在快速膨胀发展的预期,发展的态势将会比较稳健,市场需求的增长会比较稳定,铝行业将继上个世纪90年代后,再次进入瓶颈发展期。
2、产能过剩的沉重压力。
由于铝行业产业特点,从建厂到投产需要2-3年,受2007年、2008年电解铝市场繁荣刺激,具有能源优势的煤矿开采和发电企业延长产业链涉足电解铝行业以及具有铝矿和能源双重优势的地方政府急于依靠氧化铝和电解铝项目拉动投资,陆续建厂、扩容的电解铝厂将在近两年投产,在市场不旺、需求增长缓慢的情况下,产能过剩将长期存在。
《有色金属调整和振兴规划》中曾提出,截至2008年底,电解铝产能已建和在建产能超过1800万吨,当年消费1260万吨。
但是来自工信部的最新数据显示,目前电解铝产能已达到2000万吨左右,超过需求700万吨左右,产能严重过剩。
由于产能过剩,铝产品产销率下降,库存增加,成本上升(在销量降低情况下,固定成本较为稳定,从而固定成本分摊到单位产品的成本相对增加)。
因高库存制约产品价格上涨,造成企业效益直线下滑,最终陷入恶性循环,影响铝行业发展。
3、国家针对产能过剩采取的措施。
国家不断加大宏观调控力度,主要通过产业政策,规划布局,环境影响评价,提高了进入铝行业的准入门槛,为严格控制总量,国务院颁布实施的《有色金属产业调整和振兴规划》(国发[2009]14号)明确提出,要严格执行国家产业政策,今后三年内原则上不再核准新建、改扩建电解铝项目。
同时,国家加大了节能减排的管理力度,淘汰落后产能、加强技术改造、推进企业重组、充分利用境内外两种资源,发展高精尖深加工项目,发展循环经济,搞好再生利用,以推进铝产业结构调整和优化升级。
如果按照淘汰100KA的标准,2010年、2011年,有将近160万吨/年的产能淘汰。
2009年,国家推进的家电下乡、汽车下乡措施,仅仅是短期有较大效力,对铝行业的后期拉动不大。
2010年,国家对房地产行业进行打压,房地产商从利益最大化的角度考虑,将惜售房屋,多占地,晚开发。
铝行业的市场需求增加受到了较大制约。
(资料补充:
经国务院批准,自2007年8月1日起,以暂定税率形式,将电解铝的进口关税由5%下调至0%;对非铝合金制铝条、杆开征出口暂定关税,暂定税率为15%。
财政部明确表示,此举为进一步限制高耗能、高污染、资源性产品出口,促进节能降耗,鼓励原材料进口。
一位分析人士指出,取消电解铝进口税符合政府抑制国内铝产能扩张的意图。
)
(三)分析小结
1、铝行业的降成本面临着很大的挑战。
氧化铝成本受我国资源制约,降成本的技术难度较大;随着国家2010年调高电价,铝行业的成本压力增加。
这些因素将进一步压缩铝行业的利润空间。
2、铝行业的产能过剩需要逐步消化。
未来三年内,随着国家对铝行业进入门槛的抬高,淘汰落后产能力度加大,产业重组加强,铝业行业有望逐步走出产能过剩。
3、在我国加入WTO后,我国面临着国际市场强有力的竞争,现在国内铝厂没有感受到竞争的压力,是由于现在国际铝价比国内高,一旦国际市场饱和,外国厂商压价进入中国市场,中国铝行业的前景堪忧,这也就是为什么中国铝业等企业开展海外并购,积极利用海外的廉价资源。