某大桥钢箱梁制造方案.docx
《某大桥钢箱梁制造方案.docx》由会员分享,可在线阅读,更多相关《某大桥钢箱梁制造方案.docx(77页珍藏版)》请在冰豆网上搜索。
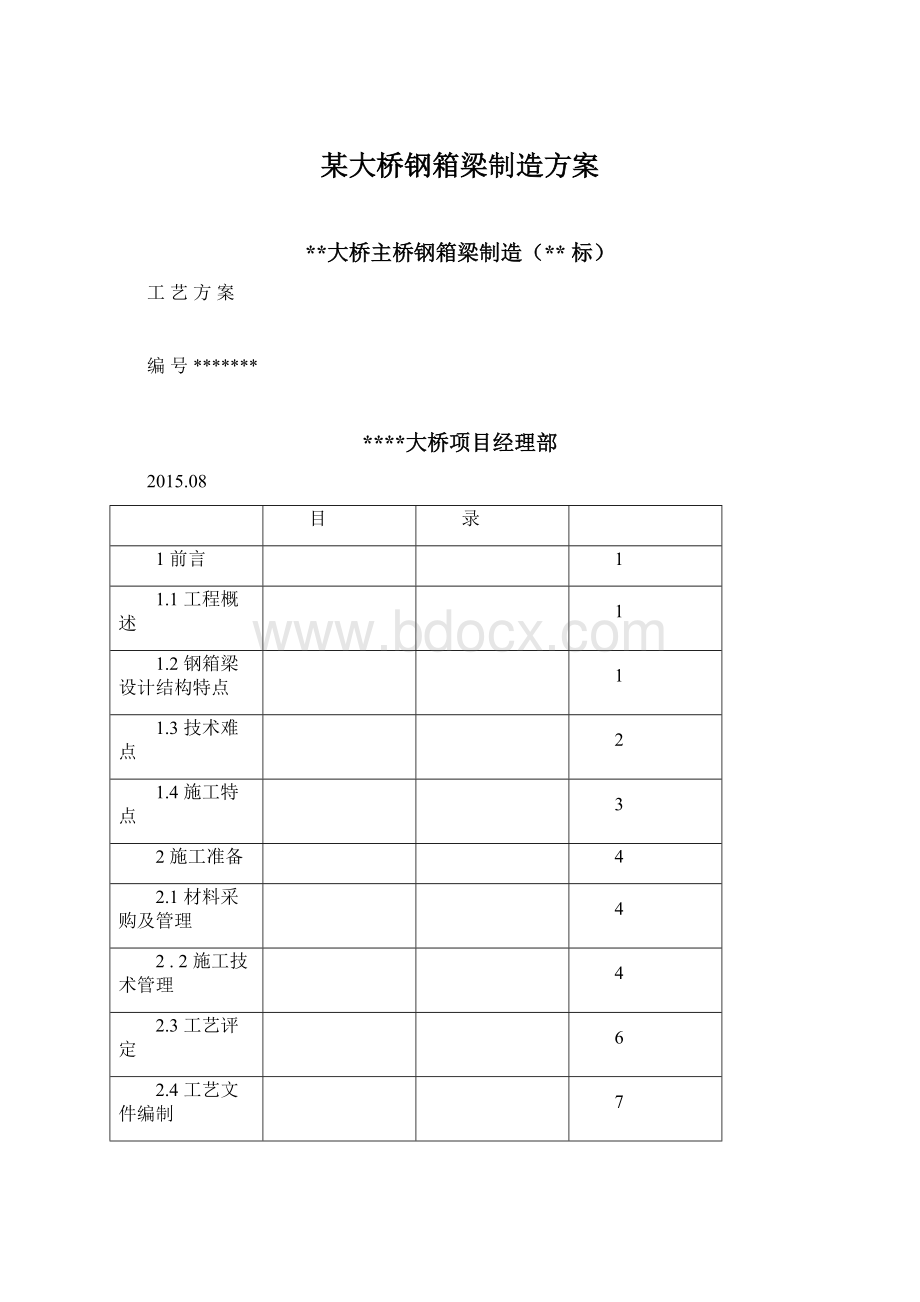
某大桥钢箱梁制造方案
**大桥主桥钢箱梁制造(**标)
工艺方案
编号*******
****大桥项目经理部
2015.08
目
录
1前言
1
1.1工程概述
1
1.2钢箱梁设计结构特点
1
1.3技术难点
2
1.4施工特点
3
2施工准备
4
2.1材料采购及管理
4
2.2施工技术管理
4
2.3工艺评定
6
2.4工艺文件编制
7
3板单元制造
8
3.1板单元划分
8
3.2关键工艺
9
3.3板单元制造工艺
10
3.4板单元制造工艺说明
21
3.5梁段、大块件制造方法
23
3.5.1总拼装胎架
23
3.5.2梁段制造
24
3.5.3预拼装
28
3.5.4大块件制造
31
4焊接
39
4.1焊接工艺评定
39
4.2焊接接头性能检验
40
4.3焊缝外观检验
40
4.4焊缝内部质量无损检验
40
5钢箱梁涂装方案
40
1.前言
1.1工程概况
****公路大桥跨江大桥工程主桥为100+100+300+1088+300+100+100m的双塔双索面斜拉桥,主桥全长2088m(见图1-1)。
图1-1***大桥主桥跨布置图
桥面纵坡为1.5%,其中主跨处于R=36300m的圆弧竖曲线上。
主桥钢箱梁为扁平流线形结构。
全桥钢箱梁分为17种类型141个梁段,标准段长度16m,边跨尾索区梁段标准长度为12m。
主跨和边跨标准梁段最大起吊重量约450t;钢箱梁含风嘴全宽41m,不含风嘴顶板宽35.4m,中心线处高4m.
C5标段工程主要工作内容包括:
1)材料的采购;
2)板单元制作和节段预拼;
3)箱梁运输、梁段现场临时连接、现场焊接和螺栓连接;
4)防撞护栏、检修道护栏、中央分隔带栏杆制作、运输和安装;
5)箱外检修小车的制作、运输、协助和指导安装;
6)箱内运输小车和轨道的设计和制作、协助和指导安装;
7)钢箱梁及检修小车、护栏等附属结构的涂装,包括涂料采购;
8)交通工程的预留,并为交通工程和桥面铺装施工、桥梁动静载试验提供协助和便利条件等。
1.2钢箱梁设计结构特点
钢箱梁梁段由顶板、底板(包括斜底板)、腹板、横隔板、纵隔板、锚箱、风嘴等组成,见图1-2。
图1-2***大桥主桥钢箱梁梁段图
钢箱梁梁高4.0m,全桥重约5万吨。
顶板、底板、腹板的厚度为12~36mm;顶、底板采用U形肋加劲,U形肋厚度为6~10mm。
锚箱安装在箱梁腹板外侧,并与其焊成一体。
根据索力大小的不同,锚箱构造分成了M1~M5五种类型。
横隔板采用整体式,由上、下两块板组成,上板先与顶板单元组焊,梁段组装时上、下板横位对接熔透焊。
标准梁段内设4道整体式横隔板,间距为4.0m。
根据受力、施工构造要求,横隔板采用10~36mm厚钢板,共分为18种类型。
横桥向设置两道纵隔板,其构造采用实腹板式和桁架式两种,共分为16种类型。
辅助跨、边跨及索塔区梁段将几个梁段焊接成一体,成为21.9m、60m、36m、56m、32m、
24m、48m、22.2m的大块件(由两个及两个以上梁段焊接成一体的吊装单元),利用浮吊进行整体吊装,大块件最长60m,最大重量约1300t。
梁段间工地连接除顶板U形肋采用高强度螺栓连接外,其它部分均为焊接。
NA34~NA11、SA34~SA11、JH、NA1、NA2、SA1、SA2梁段上的风嘴及部分梁段尾部3.2m
(斜拉索牵引、张拉施工区域)风嘴待桥上梁段吊装就位后安装焊接,其它风嘴与梁段在拼装场组焊。
1.3技术难点
1)钢箱梁结构复杂,钢板厚度较大,熔透焊缝和坡口焊缝较多,所产生的焊接变形和残余应力较大,制造过程中控制难度较大;
2)横隔板设计为整体式,下部直接插入底板U形肋,上部和预先焊在顶板的上接板横位熔透对接,因此在横隔板单元制作过程中控制尺寸精度是一个难点;
3)锚箱与腹板的熔透焊缝是全桥最关键的传力焊缝,其焊缝质量控制尤为关键;
4)顶板采用了14mm、16mm、18mm、20mm、24mm五种厚度,底板采用了12mm、
16mm、18mm、20mm、24mm五种厚度,厚度之多在钢箱梁中属于首次,不同厚度之间的
对接需要加工过渡坡,而且使得板单元的种类大大增加,制造难度增大;
5)U形肋的板厚和高度随着顶、底板的厚度不同而变化,这就给U形肋的加工制作、钻孔胎型及组装胎型的设计带来较大难度;
6)由于大块件吊装就位后不能及时安装斜拉索,在自身重力作用下,钢箱梁出现中间下挠,两边上翘,使两相邻梁段对接口出现转角,因此,在大块件梁段组拼时,需根据大块件梁段的长度、重量参数,设置相应的预拱度;
7)参与大块件组装的板单元有的不宜留长度配切量,这就要求板单元的长度要准确预留焊接收缩量、索力水平压缩量、线形调解量等;
8)部分梁段的风嘴在桥上安装,增加了桥上的工作量和难度;
1.4施工特点
钢箱梁制造与安装划分为三个阶段:
即板单元制造,梁段(含大块件)制造,桥上拼装焊接。
根据钢箱梁的结构特点,综合考虑“联合体”两公司的现状和运输等因素,确定顶板单元、部分底板单元、锚腹板单元等在中铁山桥的车间内完成;横、纵隔板单元、风嘴单元、部分底板单元等在金泰公司的车间内完成。
以便发挥两公司各自的设备优势,避免运输给一些较薄板件带来的损伤,保证板单元的质量。
梁段制造在金泰公司拼装场完成;桥上拼装焊接在架设现场梁段吊装就位后完成。
根据我们对本桥钢箱梁设计文件的理解,确定本桥钢箱梁制造与安装采用“板单元制造→板单元运输→板块拼接→梁段组焊及预拼装→涂装→大块件拼焊→称重→梁段运输→桥上连接→最终涂装”的程序。
板单元制造完成后,在****公司拼装场进行梁段(含大块件)的制造(由***桥制造的板单元及零件,在****港装船运抵拼装场)。
根据本桥钢箱梁的结构特点,采用多节段连续匹配组装、焊接和预拼装同时完成的方案。
全桥共85个梁段、20个大块件,为满足架设工期要求,改造两条170m长的梁段总拼装线(每条线每次最多可组装10个标准梁段),按照架梁顺序及工期要求进行匹配制造。
每轮次组拼不少于5个梁段,全桥共分10轮次制造,每轮预拼装合格后,标记梁段号,将最后一个梁段留下,参与下一轮预拼装,其余梁段出胎进入涂装工序。
在梁段制造中,按照底板、斜底板→横、纵隔板→中间顶板→锚腹板→边顶板→风嘴的顺序,实现立体阶梯形推进方式逐段组装与焊接。
组装时,以胎架为外胎,以纵、横隔板为内胎,重点控制桥梁的线形、钢箱梁几何形状和尺寸精度、相邻接口的精确匹配等。
钢箱梁制造检查验收应符合《****大桥主桥钢箱梁制造验收规则》(以下简称《规则》)
的规定。
2.施工准备
2.1材料采购及管理
2.1.1材料采购
用于钢箱梁制造的主要材料均通过招标,并报业主批准后采购。
在材料采购过程中参照《苏通大桥物资采供管理办法》执行。
所有材料的采购应满足钢箱梁设计和生产进度的要求。
2.1.2材料复验
1)材料除必须有生产厂家的出厂质量证明书外,并按现行有关标准进行复验,做好复验检查记录备查。
探伤板按10%进行复检,复检标准为《中厚钢板超声波检验方法》
(GB/T2970-2004),质量等级为Ⅱ级。
复检过程中将根据复检情况,并经监理工程师批准,适当调整复检比例。
2)所有材料复验合格并经监理工程师验收后方可使用。
2.1.3材料管理
1)检验合格,由质检部门在质保书上加盖合格印章,编上序号,作为领料依据;不合格材料反馈给供货单位及时换料。
2)本工程材料专料专用,物资部门必须妥善保管,作明显标记,严格材料领退制度,加强退料管理,杜绝混料。
3)所有材料应妥善存放,避免积水积尘,防止腐蚀和变形。
2.2施工技术管理
2.2.1技术准备
技术部认真研究理解业主提供的钢箱梁技术文件(设计图纸、招标文件、规范等资料),参加设计交底。
在此基础上,编制《钢箱梁制造验收规则》、《钢箱梁制造工艺方案》,完成施工图转化、工装设计、焊接和火焰切割工艺评定、油漆工艺试验、工艺文件编制和质量计划编制等技术准备工作。
2.2.2施工图绘制
施工图全部用CAD绘制。
内容包括:
板单元施工图、梁段施工图、大块件施工图、梁段拼
装顺序图、附属设施施工图、材料明细表等。
苏通大桥主桥钢箱梁施工图清单
序号
编号
工艺文件名称
1
QS-ST-1-
板单元施工图
2
QS-ST-2-
梁段施工图
3
QS-ST-3-
大块件施工图
4
QS-ST-4-
检查车及箱内小车
5
QS-ST-5-
桥面附属设施
施工图绘制程序如下:
2.2.3工装设计
1)为保证各梁段的制造精度,提高生产效率,将设计制造或改制一系列工装,具体见下表:
板单元制造
梁段制造
桥上作业
1.自动定位U形肋旋转钻孔胎
1.工艺拼接板
1.桥上工作车
2.板单元自动定位组装胎
2.板块拼装胎架
2.施工平台
3.顶板单元横接板组装胎
3.多梁段匹配组焊及预拼装胎架
3.防风防雨棚
4.板单元检测平台
4.大块件组焊胎架
5.焊接反变形胎
5.钢箱梁段称重装置
6.锚箱和腹板组焊平台
6.测量坐标系统
7.纵、横隔板单元组焊胎架
7.防风防雨棚
8.风嘴组焊胎架
梁段及大块件组焊胎架等重要的工装设计应报监理工程师审核批准。
2)工装设计流程框图
设计文件
施工图
制作方案
车间状况
2.3
工艺评定
2.3.1焊接工艺评定1)焊接工艺评定是编制焊接工艺的依据,应在钢箱梁制造开工前完成。
2)根据本桥设计图纸和《苏通大桥主桥钢箱梁制造验收规则》的规定,编写《焊接
工艺评定试验方案》,呈报监理工程师审批。
根据批准的焊接工艺评定试验方案,拟定焊接工艺评定指导书(PWPS),逐项进行焊接工艺评定试验。
3)焊接工艺评定试验提供阶段性报告及最终报告,经监理工程师审查、批准生效。
并在生产中跟踪、检查,补充和完善施工工艺。
如在生产过程中按某焊接工艺焊接的焊缝,当质量不稳定或低于标准要求时应立即终止使用此焊接工艺,并查找原因。
4)试验报告按规定程序批准后,根据焊接工艺评定试验报告编写焊接工艺规程和各
种接头的焊接工艺指导书。
经监理工程师批准后,根据焊接工艺规程和焊接工艺指导书的内容组织焊接施工。
2.3.2火焰切割工艺评定
在钢材加工之前,用有代表性的试件进行火焰切割工艺评定。
对于切割前已经过抛丸除锈预处理并喷上车间底漆的钢材,其进行火焰切割工艺评定的试件,必须涂上同样的底漆。
2.4工艺文件编制
按照招标文件中《技术规范》和设计文件的要求,编制《***大桥主桥钢箱梁制造验收规则》作为内控标准来指导和控制钢箱梁制造的全过程,并对制造验收规则进行分解细化,应编制各个工序的工艺文件共47个,用于指导生产,控制施工质量。
苏通大桥主桥钢箱梁制造工艺文件清单
序号
编号
工艺文件名称
1
BZ/STQ-GZ
钢箱梁制造验收规则
2
ZJ/STQ(2005)
钢箱梁制造质量创优规划
3
GY/STQ-FA
钢箱梁制造工艺方案
4
焊接工艺评定试验方案
5
GY/STQ-01
U形肋技术标准
6
GY/STQ-02
材料管理办法
7
GY/STQ-03
材料检验规程
8
GY/STQ-04
板单元编号及打写号规定
9
GY/STQ-05
钢箱梁制造检验规程
10
GY/STQ-06
板件切割、修磨工艺规程
11
GY/STQ-07
钢板焰切缺陷修补工艺规程
12
GY/STQ-08
顶板单元半成品加工工艺细则
13
GY/STQ-09
顶板单元组装工艺规程
14
GY/STQ-10
底板单元半成品加工工艺细则
15
GY/STQ-11
底板单元组装工艺规程
16
GY/STQ-12
锚腹板单元半成品加工工艺细则
17
GY/STQ-13
锚腹板单元组装工艺规程
18
GY/STQ-14
横(纵)隔板板单元半成品加工工艺细则
19
GY/STQ-15
横(纵)隔板单元组装工艺规程
20
GY/STQ-16
风嘴板单元半成品加工工艺细则
序号
编号
工艺文件名称
21
GY/STQ-17
风嘴组装工艺规程
22
GY/STQ-18
顶板单元焊接工艺规程
23
GY/STQ-19
底板单元焊接工艺规程
24
GY/STQ-20
锚腹板单元焊接工艺规程
25
GY/STQ-21
横(纵)隔板单元焊接工艺规程
26
GY/STQ-22
风嘴焊接工艺规程
27
GY/STQ-23
附属部件焊接工艺规程
28
GY/STQ-24
板单元修整工艺规程
29
GY/STQ-25
钢材预处理工艺规程
30
GY/STQ-26
板单元存放、吊装运输规程
31
GY/STQ-27
钢箱梁涂装工艺规程
32
GY/STQ-28
钢箱梁桥上涂装工艺规程
33
GY/STQ-29
焊缝无损检验规程
34
GY/STQ-30
焊缝无损检验记录规定
35
GY/STQ-31
梁段整体组装工艺规程
36
GY/STQ-32
梁段整体焊接工艺规程
37
GY/STQ-33
梁段存放运输规程
38
GY/STQ-34
钢箱梁整体组拼测量工艺规程
39
GY/STQ-35
梁段称重规程
40
GY/STQ-36
桥上焊接工艺规程
41
GY/STQ-37
焊缝编号规定
42
GY/STQ-38
焊缝锤击工艺规程
43
GY/STQ-39
板单元焊缝探伤清册
44
GY/STQ-40
整体拼装焊缝探伤清册
45
GY/STQ-41
高强度螺栓施拧工艺规程
46
GY/STQ-42
员工岗前培训计划
47
GY/STQ-43
焊工考试方案
3.板单元制造
3.1板单元划分
在满足设计要求、保证大桥制造质量的的前提下,综合考虑供料、运输及批量生产等因素,对梁段进行了板单元划分,见图3.1-1。
图3.1-1梁段板单元划分
每个标准梁段划分成55块板单元,其中顶板单元16块,底板和斜底板单元15块,横隔板单元12块,纵隔板单元8块,锚腹板单元2块,风嘴单元2件。
钢箱梁制造中实现板单元化,尽量避免或减少零散部件参与梁段组装。
这样所有板单元可按类型在专用胎架上形成流水作业制造,实现生产规范化,产品标准化,质量稳定化。
3.2关键工艺
板单元制造按照“钢板赶平及预处理→数控精确下料→零件加工(含U形肋制造)→胎型组装→反变形焊接→局部修整”的顺序进行,其关键工艺如下:
●钢板赶平及预处理
●数控精切下料
●U形加劲肋制造
●利用旋转钻孔胎型钻制顶板U形肋螺栓孔
●板件用数控钻床制孔
●用高精度U形肋自动定位板单元组装胎组装顶、底板单元
●锚箱与腹板的组装和焊接
●横隔板单元外形尺寸控制
●对单侧有纵肋的板单元采用反变形焊接
●优先选用自动和半自动CO2焊接方法
3.3板单元制造工艺
3.3.1顶板单元
3.3.2
1)制造工艺
●顶板采用多嘴精切(含坡口),一般情况下在背塔端留配切量。
横隔板接板数控精切下料,U肋下料后经过矫正、机加工、压制成型。
●
顶板精切下料后用赶板机赶平,严格控制
平面度。
●顶板U形肋组装前在专用旋转钻孔胎上钻孔。
于板单元组装前组焊封头
●
采用磁力吊吊钢板,以防产生永久变形。
用板单元组装胎组装,组装胎设有钢板、
U肋栓孔的定位装置。
组装时将纵、横基线返到顶板上,并打上样冲眼。
●
采用反变形胎,用CO2自动焊机施焊,焊后控制松卡温度,并进行适当修整。
●在专用组装胎内组装横隔板接板,横隔板接板位置靠胎型自动定位,避免人为因素造成的误差,确保梁段组装时与横隔板在同一平面内。
●焊后上平台进行修整检验,以保证顶板平面度。
●将顶板单元的纵、横基线返到无U肋面,打样冲眼,以备梁段组装用。
2)制造工艺流程
不合格品N
控制程序复验
Y
赶平
不合格品N
控制程序检查
Y
N
检查
Y
组焊U形肋封头板
不合格品控制程序
检查N
Y
不合格品控制程序
·检查包括检查N
焊缝探伤
Y
不合格品控制程序
3.3.3
底板单元1)制造工艺
●底板采用多嘴精切(含坡口),一般情况下在背塔端留配切量。
U形肋下料后经过矫正、机加工、压制成型。
矫正●底板精切下料后用赶板机赶平,严格控制平面度。
组装U肋
●
采用磁力吊吊钢板,以防产生永久变形。
用板单元组装胎组装,组装时将纵、横基线返到底板上,并打上样冲眼。
焊接●采用反变形胎,用CO2自动焊机施焊,焊后控制松卡温度,并进行适当修整。
修整
●用塑料布将底板U肋端口封闭,防
包装止雨水和杂物进入。
旋转式板单元反变形船位焊接胎板单元修整检测平台
3.3.4锚腹板单元1)制造工艺
●增加对腹板的连接锚箱部位及锚固板、承压板的近熔透焊缝区域进行超声波探伤复检。
●锚固板、承压板及非矩形肋板采用数控精切下
下料
料。
腹板及长条肋板采用多嘴切割机精切下
矫正●精切下料后用赶板机赶平,严格控制平面度。
●在平台上精确划线组装,两锚固板间用专用卡具定位,同时确保锚固板、承压板与腹板连接边在
机加工划线
●
焊接坡口、承压板和锚垫板孔、斜面及排水槽等均采用机加工。
●在平台上精确划出水平肋系统中线(纵基线)、
锚箱处的横隔板中线(横基线)、熔透焊缝探伤系统线,并在线的两端打上样冲眼。
●以所划线为基准组装肋板,肋板在锚箱
同一个平面内,近腹板
侧的两块加劲板和锚箱隔板暂时不组焊。
锚箱加劲板
承压板
组焊锚箱组焊腹板
锚固板
●锚箱和腹板应分别组焊,然后再焊为一体。
部位连接横隔板处留嵌补段工地组焊,以保证对锚箱与腹板的熔透角焊缝进
行充分有效的探伤,保证梁段组装时隔板与腹板熔透角焊缝质量。
腹板内侧竖
向加劲板待梁段组拼时组焊。
腹板
●锚箱组焊修完成后,用立式铣床加工承压板外平面,以保证承压板与锚垫板的密贴。
腹板和锚箱单元组焊
●在平台上以腹板横、纵基线为基准精确划线组装,经检查合格后方可施焊。
●焊前预热,焊接时采用小线能量,防止层状撕裂。
焊后用直探头从腹板内侧检查有无层状撕裂。
锚垫板
腹板
o锚箱隔板
2)锚腹板单元制造工艺流程
(1)腹板
(2)锚箱(3)锚腹板单元
进料
锚箱与腹板组装
不合格品控制程序
N
原材料复验
Y
赶平
预处理
●包括超声波探伤检
N不合格品
检查控制程序
Y
焊接
数控精切下料赶平
机加工
修整
·检查包括检验焊缝探伤
Y
N不合格品控制程序
不合格品N
控制程序检查
Y
N
检查
组装锚箱隔板、加劲板与锚垫
N不合格品
检查控制程序
Y
焊接
Y修整
不合格品控制程序
组锚箱
N
检查
Y
N不合格品
检查控制程序
Y
不合格品检查控制程序N
机加工检验
Y与腹板组装
Y
不合格品N
控制程序
3.3.5
横隔板单元
根据横隔板的结构特点,横隔板可分为无拉索处横隔板和有拉索处横隔板。
1)无拉索处横隔板制造工艺
●上接板采用水下等离子数控精切下料;肋板、人孔和管线孔围板采用多嘴切割机精切下料。
●上接板焊接坡口亦可机加工;人孔和管线孔围板压型。
●划线组装,预留焊接收缩量,在板单元对接处,水平肋留
400mm嵌补段。
板边与胎架固定,在反变形胎架上进行焊接,用CO2半自动焊机对称施焊,严格控制焊接变形,以减小修整量。
●在平台上进行检验,严格控制平面度。
●以上水平肋为基准,用水下等离子数控切割机切割,严格控制上水平肋至底边的尺寸,从而便于顶板在梁段组装时确定标高。
●用CO2半自动焊机对称施焊,严格控制焊接变形。
2)工艺流程
●包括超声波探伤检验
3)有拉索处横隔板制造工艺
●上接板采用水下等离子数控精切下料;肋板、人孔和管线孔围板采用多嘴切割机精切下料;主板边块焰切荒料。
●机加工荒料对接坡口及过渡坡;上接板焊接坡口亦可机加工;人孔和管线孔围板压型。
●采用埋弧自动焊焊接。
●用火焰修整,严格控制平面度。
●划线组装,预留焊接收缩量,在板单元对接处,水平肋留
400mm嵌补段。
板边与胎架固定,在反变形胎架上进行焊接,用CO2半自动焊机对称施焊,严格控制焊接变形,以减小修整量。
●在平台上进行检验,严格控制平面度。
●以上水平肋为基准,用水下等离子数控切割机切割,严格控制上水平肋至底边的尺寸,从而便于顶板在梁段组装时确定标高。
●用CO2半自动焊机对称施焊,严格控制焊接变形。
3.3.6纵隔板单元
纵隔板分为桁架式和实体式两种类型。
桁架式纵隔板上、下弦杆为T形截面,板厚为14mm,斜杆由2根∠160×14mm角钢加缀板组合而成;实体式纵隔板在索塔区板厚一般为
24mm,压重区为14mm。
1)桁架式纵隔板2)实体式纵隔板
●上下弦腹板数控精切下料,盖板用多嘴精切,节点板剪切或用数控精切下料,角钢锯切。
●严格控制直线度和平面度。
●主板用数控精切,其它件采用多嘴精切。
矫正●严格控制平面度和直线度。
加工●刨焊接坡口,人孔围板压型。
●上下弦盖板刨头,严格控制长度公差。
剪切下料的节点板刨焊接边。
T形肋组焊修
●采用CO2半自动焊,焊后修整严格控制直线度。
●上、下弦杆及斜杆分别组焊修。
注意在斜杆组装前必须先将角钢内部进行涂装。
T形肋与主板组焊修
组焊人孔围板和竖肋
●在反变形胎上用CO2半自动焊机施焊,以减小焊接变形和修整量。
●在平台上用CO2半自动焊机按工艺规定的顺序施焊,严格控制焊接变形。
●用胎型控制其外形尺寸和T形腹板与节点板的对中。
采用CO2半自动焊焊接。
修整●焊后在平台上修整检验。
3.3.7风嘴单元
风嘴单元由风嘴顶板单元(检修道板)、风嘴底板单元、导风板单元及风嘴隔板单元组
成。
●
风嘴隔板数控精切,其余多嘴精切
(含坡口),顶、底板和导风板预留焊接收缩量。
●严格控制平面度和直线度。
●顶、底板和导风板用自动定位板单元组装胎组装。
在反变形胎上用CO2自动焊机对称施焊。