数控铣削正六方形凸台编程及加工工艺探索.docx
《数控铣削正六方形凸台编程及加工工艺探索.docx》由会员分享,可在线阅读,更多相关《数控铣削正六方形凸台编程及加工工艺探索.docx(28页珍藏版)》请在冰豆网上搜索。
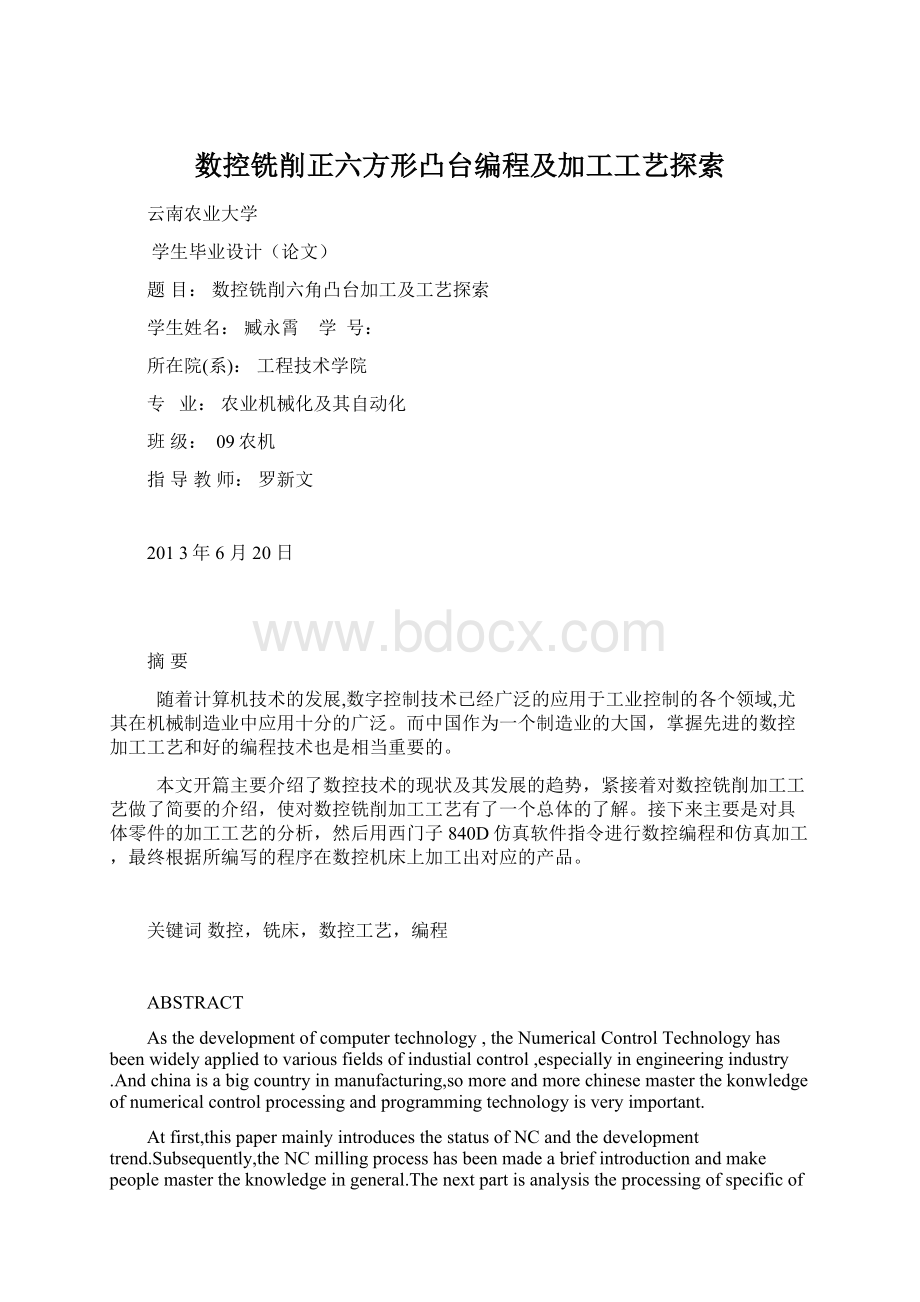
数控铣削正六方形凸台编程及加工工艺探索
云南农业大学
学生毕业设计(论文)
题目:
数控铣削六角凸台加工及工艺探索
学生姓名:
臧永霄学号:
所在院(系):
工程技术学院
专业:
农业机械化及其自动化
班级:
09农机
指导教师:
罗新文
2013年6月20日
摘要
随着计算机技术的发展,数字控制技术已经广泛的应用于工业控制的各个领域,尤其在机械制造业中应用十分的广泛。
而中国作为一个制造业的大国,掌握先进的数控加工工艺和好的编程技术也是相当重要的。
本文开篇主要介绍了数控技术的现状及其发展的趋势,紧接着对数控铣削加工工艺做了简要的介绍,使对数控铣削加工工艺有了一个总体的了解。
接下来主要是对具体零件的加工工艺的分析,然后用西门子840D仿真软件指令进行数控编程和仿真加工,最终根据所编写的程序在数控机床上加工出对应的产品。
关键词数控,铣床,数控工艺,编程
ABSTRACT
Asthedevelopmentofcomputertechnology,theNumericalControlTechnologyhasbeenwidelyappliedtovariousfieldsofindustialcontrol,especiallyinengineeringindustry.Andchinaisabigcountryinmanufacturing,somoreandmorechinesemasterthekonwledgeofnumericalcontrolprocessingandprogrammingtechnologyisveryimportant.
Atfirst,thispapermainlyintroducesthestatusofNCandthedevelopmenttrend.Subsequently,theNCmillingprocesshasbeenmadeabriefintroductionandmakepeoplemastertheknowledgeingeneral.Thenextpartisanalysistheprocessingofspecificofspecificparts,thenusetheSimens840DCNCsimunationsoftwareinstructionsforprogramminganfsimulationprocessing。
Finally,accrodingtotheprogram,machiningthecorrespondingproducts.
KeywordsNC,millingmachine,NCprocessing,programme
1绪论
1.1数控机床的产生和发展
数控机床(NumericalControlMachineTools)是用数字代码形式的信息(程序指令),控制刀具按给定的工作程序、运动速度和轨迹进行自动加工的机床,简称数控机床。
数控机床是在机械制造技术和控制技术的基础上发展起来的,其过程大致如下:
随着电子技术的发展,1946年世界上第一台电子计算机问世,由此掀开了信息自动化的新篇章。
1948年,美国帕森斯公司接受美国空军委托,研制直升飞机螺旋桨叶片轮廓检验用样板的加工设备。
由于样板形状复杂多样,精度要求高,一般加工设备难以适应,于是提出采用数字脉冲控制机床的设想。
1949年,该公司与美国麻省理工学院(MIT)开始共同研究,并于1952年试制成功第一台三坐标数控铣床,当时的数控装置采用电子管元件。
1959年,数控装置采用了晶体管元件和印刷电路板,出现带自动换刀装置的数控机床,称为加工中心(MCMachiningCenter),使数控装置进入了第二代。
1965年,出现了第三代的集成电路数控装置,不仅体积小,功率消耗少,且可靠性提高,价格进一步下降,促进了数控机床品种和产量的发展。
60年代末,先后出现了由一台计算机直接控制多台机床的直接数控系统(简称DNC),又称群控系统;采用小型计算机控制的计算机数控系统(简称CNC),使数控装置进入了以小型计算机化为特征的第四代。
1974年,研制成功使用微处理器和半导体存贮器的微型计算机数控装置(简称MNC),这是第五代数控系统。
20世纪80年代初,随着计算机软、硬件技术的发展,出现了能进行人机对话式自动编制程序的数控装置;数控装置愈趋小型化,可以直接安装在机床上;数控机床的自动化程度进一步提高,具有自动监控刀具破损和自动检测工件等功能。
20世纪90年代后期,出现了PC+CNC智能数控系统,即以PC机为控制系统的硬件部分,在PC机上安装NC软件系统,此种方式系统维护方便,易于实现网络化制造。
目前,世界主要工业发达国家的数控机床已经进入批量生产阶段,如美国、德国、法国、日本等,其中日本发展最快。
我国1958年试制成功第一台电子管数控机床,从1965年开始研制晶体管数控系统,到20世纪70年代初曾研究出数控臂锥铣床、非圆插齿机、数控立铣床、数控车床、数控镗床、数控磨床和加工中心等。
20世纪80年代随着改革开放政策的实施,我国从国外引进了先进技术,并在消化、吸收国外先进技术的基础上,进行了大量的开发工作,进而推动了我国数控机床新的发展高潮,使我国数控机床在品种上、性能上以及水平上均有了新的飞跃。
1.2数控机床的加工特点
(1)自动化程度高,具有很高的生产效率。
除手工装夹毛坯外,其余全部加工过程都可由数控机床自动完成。
若配合自动装卸手段,则是无人控制工厂的基本组成环节。
数控加工减轻了操作者的劳动强度,改善了劳动条件;省去了划线、多次装夹定位、检测等工序及其辅助操作,有效地提高了生产效率。
(2)对加工对象的适应性强。
改变加工对象时,除了更换刀具和解决毛坯装夹方式外,只需重新编程即可,不需要作其他任何复杂的调整,从而缩短了生产准备周期。
(3)加工精度高,质量稳定。
加工尺寸精度在0.005~0.01mm之间,不受零件复杂程度的影响。
由于大部分操作都由机器自动完成,因而消除了人为误差,提高了批量零件尺寸的一致性,同时精密控制的机床上还采用了位置检测装置,更加提高了数控加工的精度。
(4)易于建立与计算机间的通信联络,容易实现群控。
由于机床采用数字信息控制,易于与计算机辅助设计系统连接,形成CAD/CAM一体化系统,并且可以建立各机床间的联系,容易实现群控。
1.3数控机床的发展趋势
随着计算机、微电子、信息、自动控制、精密检测及机械制造技术的高速发展,机床的数控技术有了长足的发展。
近几年一些相关技术的发展,如刀具及新材料的发展,主轴伺服和进给系统、超高速切削等技术的发展。
目前数控机床正朝着高速度、高精度、高工序集中度、高复合化和高可靠性等方向发展。
世界数控技术及其装备的发展趋势主要体现在以下的方面。
1)高速高效高精度
高生产率。
通过数控装置及伺服系统功能的改进,主轴的速度和进给速度大大提高,减小了切削的时间和非切削时间。
高加工精度。
随着精密产品的出现,对精度的要求提高到了0.1微米,有的零件甚至已经达到了0.01微米,高精密零件要求提高了机床的加工的精度,包括采用温度补偿法等。
2)柔性化
柔性化包括两个方面的柔性:
一是数控系统本身的柔性,数控系统采用模块化的设计,功能覆盖面广,便于不同用户的要求;二是DNC系统的柔性,同一DNC系统能够依据不同生产流程的要求,使物料流和信息流自动进行动态调整,从而最大限度的发挥DNC系统的效能。
3)工艺复合化和多轴化
数控机床的工艺复合化,是指工件在一台机床上装夹后,通过自动换刀、旋转主轴头、旋转工作台等给种措施,完成多工序、多表面的复合加工。
此外,数控技术的进步也提供了多轴控制和多轴联动控制功能。
4)实时智能化
在数控技术领域,实时智能控制的研究和应用正沿着几个主要的分支发展,如自适应控制、模糊控制、神经网络控制、专家控制、学习控制、前馈控制等。
5)结构新型化
采用新型结构,实现多坐标联动加工,其控制系统结构复杂,加工精度、加工效率较普通机床高2--10倍
6)编程技术自动化
为了弥补手工编程和NC语言编程的不足,近年来开发出多种自动编程系统,如图形交互式系统、数字化自动编程系统、会话式自动编程系统、语言数控编程系统等。
其中图形交互式系统应用的最为广泛,图形交互式编程系统是以计算机辅助设计(CAD)软件为基础,首先形成零件的图形文件,然后再调用数控编程模块,自动编制加工程序,同时可动态显示刀具的加工轨迹。
目前的图形交互式软件有MasterCAD、Cimatron、pro/E、UG、CAXA、CATIA等。
7)集成化
数控系统采用高度集成化的芯片,可提高数控系统的集成度和软、硬件运行速度,应用平板显示技术可提高显示器的性能。
平板显示器应用先进封装和互连技术,将半导体和表面安装技术融于一体,通过提高集成电路的密度,减小互联长度和数量来降低产品的价格、改进性能、减小组件的尺寸、提高系统的可靠性。
8)开放式闭环控制模式
采用通用计算机组成的总线式、模块化、开放、嵌入式体系结构,便于裁减、扩展和升级,可以组成不同档次、不同类型、不同集成程度的数控系统。
闭环控制模式是针对传统数控系统仅有的专用型封闭式开环控制模式提出的。
由于制造过程是一个多变量控制和加工工艺综合作用的复杂过程,包括诸如加工尺寸、形状、振动、噪音、温度和热变形等各种变化因素,因此,要实现加工过程的多目标优化,必须采用多变量的闭环控制,在实现加工过程中动态调整加工过程变。
在加工过程中采用开放式通用型实时动态全闭环控制模式,易于将计算机实时智能技术、多媒体技术、网络技术、CAD/CAM、伺服系统、自适应控制、动态数据管理、动态刀具补偿、动态仿真等高新技术溶于一体,构成严密的制造过程闭环控制系统体系,从而实现集成化、智能化、网络化。
2数控铣削加工工艺
2.1零件的工艺性分析
(1)零件图的尺寸标注应符合编程方便的原则
零件图的尺寸标注方法应适应数控加工的特点。
在数控加工的零件图上,应该以同一基准标注尺寸或直接给出坐标尺寸。
这样的标注方法既便于编程,也便于尺寸之间的相互协调,在保证设计基准、工艺基准、检查基准与编程原点设置的一致性方面带来很大的方便。
构成零件轮廓的几何元素的条件应充分。
对零件进行手工编程时,要计算每个节点的坐标。
因此在分析零件图时,要充分分析几何元素的给定条件是否充分。
(2)要彻底读懂零件图样
零件图样的尺寸是否标注全,有无漏、多尺寸的情况,有无封闭尺寸,尺寸的标注方法是否方便编程,零件的结构是否表示清楚了,视图是否完整,各几何元素间的相互关系(如相切、相交、垂直、平行等)是否明确。
(3)要分析透零件的加工工艺性
研究零件的被加工表面是否适合于数控铣床加工,被加工表面是否太厚,内转接圆弧R是否太小。
如图2.1所示,当R小于0.2H(H为被加工内轮廓面的最大高度)时,其加工的工艺性不好。
即刀具被迫采用小直径的使其刚性变差,需要采用多次分层切削加工。
当被加工表面的凹圆弧尺寸较多时,应该尽量统一,以减小使用的铣刀的数量,保证零件表面光滑。
否则,在进行切削的时候,在接刀处会留下较多的刀痕,最终影响了表面的加工质量。
零件被加工的底面与侧面相交处的圆角半径是否太大,如图2.2所示,当刀具圆角半径r越大时,铣刀端刃铣削平面的能力就越差,效率也就越低,应该尽量的避免。
图2.1内轮廓圆弧对铣削工艺性的影响
图2.2零件底面圆弧对铣削工艺性的影响
(4)要研究分析零件的精度。
零件的精度(尺寸、形状、位置)是否能够保证,表面质量是否保证。
根据精度、表面质量来决定是否采用粗铣,还是精铣,以及是否要多次进给。
(5)要研究分析零件的刚性。
零件的厚度如果太薄会引起加工变形。
当加工薄壁而且面积较大的零件时,在其加工完后也易引起加工变形,很难保证精度。
(6)要研究分析零件的定位精度。
零件上如果有统一的定位基准,便可保证零件在多次装夹定位后各加工表面之间的位置精度。
其定位基准能够保证零件定位稳定可靠,便没有基准不重合的误差。
(7)要研究分析零件的毛坯和材料。
材料是否具有较好的加工工艺性能,硬度、热处理状态是怎样的,毛坯的余量是否足够,是否均匀,毛坯的安装定位平面是否方便可靠。
2.2、装夹方案的确定
(1)定位基准的选择
在选择定位基准时,应该减小装夹的次数,尽量做到在一次安装中能够把零件上所有要加工的表面都加工出来。
一般选择零件上不需要铣削加工的表面或者孔作为定位基准。
对于薄壁的零件,选择的定位基准应该有利于提高加工的刚性,以减小切削变形。
并且定位基准应该和设计基准重合以减小定位误差对尺寸精度的影响。
(2)夹具的选择
在选择夹具的时候有两个基本的要求。
一是:
要保证夹具的坐标方向与机床的坐标方向相对的固定;二是:
要协调零件和机床坐标系的尺寸关系。
当零件加工批量不大时,应尽量采用组合夹具、可调试夹具及其它通用夹具,来缩短生产准备时间、节省生产费用。
在成批量生产时,采用专用夹具,来提高效率。
在选择夹具时还要保证零件的装卸要快速、方便、可靠。
夹具上各部件应不妨碍机床对零件各表面的加工。
2.3、数控加工刀具
刀具的选择是数控加工工艺中的主要内容之一,不仅影响机床的加工效率,而且直接影响加工的质量。
数控机床在选用刀具时,通常要考虑机床的加工能力、工序内容、工件材料等因素。
数控机床对刀具的要求比普通机床要高、除了要求较好的刚性和尺寸稳定性、较长的寿命、良好的切削性能外,还要求安装调整方便。
选择刀具时,还要使刀具的尺寸与被加工工件的表面尺寸和形状相适应,即选择的刀具的几何形状应依据加工曲面的具体情况而定
(1)刀具选择的基本要求
刀具的刚性要好。
为提高生产效率而采用大切削用量时,需要刚性好的刀具,刚性差的刀具在大切削用量时很容易断刀。
要保证被加工表面的形状精度,用刚性差的刀具在大切削力的作用下,会产生变形而形成让刀,使加工的型面出现斜面。
当被加工的零件表面的加工的余量不一样的时候,若采用刚性好的刀具就可以不必换刀,从而减少了换刀次数。
刀具的耐用度要高。
由于数控铣床靠程序来控制精度,刀具如果磨损很快,则被加工零件的尺寸精度和型面精度就很难保证,故要用耐用度高的刀具。
同时,刀具参数、几何角度、排屑性能等因素也要综合的考虑。
(2)数控加工刀具材料
高速钢。
又称白钢,它含有W、Cr、Mo、V、Co等元素。
它不仅可以用来制造钻头、铣刀,还可以用量制造齿轮刀具、成形铣刀等复杂刀具。
但由于其允许的切削速度较低(50m/min),所以大多用于数控机床的低速加工。
硬质合金。
硬质合金是有硬度和熔点都很高的碳化物(WCTiC等),用comoni做粘结剂制成的粉末冶金产品。
在中速和大切削中发挥出优良的切削性能。
常用的硬质合金有钨钴合金、钨钛合金等。
陶瓷材料。
陶瓷是含有金属氧化物和氮化物的无机非金属材料。
陶瓷材料具有高硬度、高强度、耐磨性好、化学性能稳定性好、摩擦因素低、价格低廉等优点。
立方氮化硼(CBN)。
CBN是人工合成的高硬度材料,其硬度和耐磨性仅次于金刚石,有极好的高温硬度,与陶瓷材料相比,其耐热性和化学稳定性稍差,但冲击韧度和抗破坏性能较好。
聚晶金刚石(PCD)。
PCD作为最硬的刀具材料,硬度很高,具有很好的耐磨性,它能够以高硬度和高精度加工软的有色金属材料,但它对冲击敏感,容易破裂,而且对黑色金属中的铁的亲和力强,容易引起化学反应,一般只能用于加工非铁零件。
(3)铣削加工刀具
在选择铣刀时,要使刀具的尺寸与被加工工件的表面尺寸和形状相适应。
在加工时,对于平面零件的周边轮廓常采用立铣刀。
铣削平面时常采用面铣刀。
在选择铣刀时应该注意以下几点:
刀具半径r应该小于零件内轮廓面的最小曲率半径(一般为其0.8~0.9左右);零件的加工高度H小于等于(1/4~1/6)r,以保证刀具具有足够的刚度;对不通孔或深槽,选取L=H+(5~10)mm,其中L为刀具切削部分的长度,H为零件的高度;加工外型及通槽时,选取L=H+R+(5~10)mm,其中R为刀尖角半径。
在用面铣刀铣削表面时,粗铣时,铣刀直径要小些,因为粗铣切削时切削力大,选择小直径的铣刀可以减小切削力矩。
精铣时,铣刀直径要大些,尽量包容工件的整个表面加工宽度,以提高加工精度和效率,并减小相邻两次进给之间的接刀伤痕。
在铣削立体型面和变斜角轮廓外形时,常用球头铣刀、环形刀、鼓形刀和盘铣刀等。
球头铣刀和环形刀用于加工立体面,鼓形刀和锥形刀用于加工一些变斜角的零件。
曲面加工常采用球头铣刀,但加工曲面较平坦的部分时,刀具以球头顶端刃切削,切削条件较差,因而应该采用环铣刀。
在内轮廓加工时,要注意刀具的半径小于轮廓曲线的最小曲率半径,在自动换刀机床中要预先测好刀具的结构尺寸和调整尺寸,以便在加工时进行刀具的补偿。
(4)孔加工刀具
数控孔加工的刀具常用的有钻头、镗刀、铰刀和丝锥等。
钻头。
一般钻孔的深度约为直径的5倍,细长孔的加工易于折断,要注意排削和冷却,在钻孔前最好先钻中心孔。
镗刀。
镗刀按切削刃数量可以分为单刃镗刀和双刃镗刀。
铰刀。
数控机床上所用的铰刀大多是通用标准铰刀。
除此之外,还有机夹硬质合金刀片单刃铰刀和浮动铰刀等。
2.4、切削用量的确定
合理的选择切削用量,对零件的表面质量、精度、加工效率影响很大。
切削用量包括主轴的转速、背吃刀量、进给量。
合理选择切削用量的原则:
粗加工时,一般以提高效率为主,并考虑经济性和加工成本;半精加工和精加工时,应该在保证加工质量的前提下,兼顾切削效率、经济性、加工成本。
背吃刀量。
选择背吃刀量的主要依据是机床、夹具、刀具和工件的刚度。
在刚度允许的情况下,尽量选择较大的背吃刀量来减少进给次数,提高生产效率。
但在工艺系统刚性不足或毛坯余量很大,或余量不均匀时,粗加工要分几次进给,并且应该把第一、二次进给的背吃刀量尽量取得大一些。
在加工铸、锻件时应该尽量使背吃刀量大于硬皮层的厚度,以保护刀尖。
主轴转速。
主轴转速主要根据允许的切削速度选取。
而刀具的切削速度主要根据已经选定的背吃刀量、进给量、刀具的耐用度来、工件材料的强度和硬度以及切削加工性来选取。
而切削速度与主轴转速的关系如下公式所示:
式中:
-切削刃选定点处所对应的工件或刀具的最大回转直径,单位为mm
n-主轴转速,单位为r/min
-切削速度,单位为m/min
进给量(mm/min或mm/r)。
进给量的选取主要根据零件的加工精度和表面的粗糙度以及刀具、工件材料性质来选取。
当零件的加工精度、表面粗糙度要求高时,进给量应该取小值。
最大进给量受机床刚度和进给系统的性能限制,并与脉冲当量有关。
2.5切削液的选择
在金属切削过程中合理的选择切削液,可以改善切屑、工件、与刀具间的摩擦状况,抑制积屑瘤和鳞刺的生长,从而降低切削力和切削温度,减少刀具的磨损和工件的热变形,提高刀具的耐用度,提高加工效率和加工质量。
切削液在加工过程中的作用很大,它主要具有冷却作用、润滑作用、清洗作用、防锈作用。
常用的切削液主要有水溶液、乳化液、切削油。
在选用切削液时,应该注意以下几点:
在粗加工时,加工的余量大,所选的进给量和背吃刀量也较大,所以会产生大量的切削热,所以选择切削液的主要目的是为了散热;在精加工时,对零件加工表面的质量要求高且要尽量的减少刀具的磨损,所以选择切削液的主要的目的是为了提高加工表面的质量和提高刀具的耐用度;当工件的材料不同时,选择切削液的主要目和种类也有所不同。
当在加工铸铁、黄铜等脆性材料时,一般不用切削液,以免崩脆的切屑粘附在机床的运动部件上。
在加工高强度刚和高温合金等难加工的材料时,对冷却液的冷却、润滑作用都有较高的要求,应尽可能采用积压切削液或积压乳化液。
在切削有色金属和铜、铝合金时,为了得到较高的表面质量和精度,可以采用10%-20%的乳化液、煤油或煤油与矿物油的混合物。
在切削镁合金时,不能用水溶液,以免燃烧。
2.6加工阶段的划分
当零件的加工质量要求较高时,往往不可能在一道工序内就完成一个或者几个表面的全部加工阶段.必须把整个加工过程按工序性质不同划分为几个阶段:
(1)粗加工阶段.在这一阶段中要切除大量的加工余量,使毛坯的形状和尺寸接近零件成品,因此主要的目标是提高生产率。
(2)半精加工阶段。
在这一阶段应该为主要表面的精加工做好准备(达到一定加工精度,保证一定的加工余量),并完成一些次要表面的加工(如钻孔、攻螺纹等),一般在热处理之前进行。
(3)精加工阶段。
保证各主要表面达到图样规定的尺寸精度和表面粗糙度要求,主要的目的是全面的保证精加工质量。
(4)光整加工阶段。
对于零件上精度要求很高,表面粗糙度值要求很小的表面,还需要进行光整加工。
主要目标是以提高尺寸精度和减小表面的粗糙度为主,一般不用来纠正形状精度和位置精度。
(5)超精密加工阶段。
该阶段是按照超稳定,超微量切除等原则,实现加工尺寸误差和形状误差在0.1微米以下的加工技术。
2.7工序的划分
2.7.1工序划分原则
工序的划分可以采用两种不同的原则:
工序集中原则和工序分散原则。
工序集中的原则就是指每道工序包括可能多的加工内容。
将工件的加工集中在少数几道工序内容内完成。
工序集中一般使用结构复杂,机械化,自动化程度高的机床。
因此工序集中的特点是:
1)减少了设备的数量,减少了操作工人和生产面积。
2)减少工序数目,减少运输工作量,简化了生产计划工作,缩短了生产周期。
3)减少了工件的装夹次数,不仅有利于提高生产率,而且由于一次装夹下加工了许多的表面,也易于保证这些表面的加工精度。
4)
工序分散原则就是将工件的加工分散在较多的工序内进行。
每道工序的加工内容很少,最小时即每道工序仅完成一个简单的工步。
其特点是:
1)采用了比较简单的机床和工艺设备。
2)对工人的技术要求低。
3)生产设备工作量小,容易变换产品。
4)设备数量少,工人数量多,生产面积大。
2.7.2工序划分的方法
(1)按所用的刀具划分。
即在一次安装过程中尽可能用一把刀具加工出可能加工的所有部分,然后再换另一把刀加工其他的部位。
即以同一把刀具完成的那一部分工艺过程为一道工序。
(2)按安装次数划分。
即以每一次装夹完成的那一部分工艺过程为一道工序。
这种方法适应于加工内容不多的工件。
(3)按粗、精加工划分。
即以粗加工中完成的那一部分工艺过程为一道工序,精加工中完成的那一部分工艺过程为一道工序。
这种方法使用于加工后变形较大,需要粗、精加工分开的零件。
(4)按加工部位划分。
即以完成相同型面的那一部分工艺过程为一道工序。
对于加工表面多而复杂的零件,可以按结构特点分为几个加工部分,每一部分为一道工序。
2.8工艺文件的制定
零件的加工工艺设计完成以后,就应该将有关的内容填入各种相应的表格或者卡片中,以便贯彻执行并将其作为编程和生产技术准备的依据。
这些表格或者卡片被称为工艺文件。
数控加工的工艺文件除了包括机械加工工艺过程卡、机械加工工艺卡、数控加工工序卡外,还包括数控加工刀具卡。
其中,数控加工工序卡是用来编制程序的依据,以及用来指导操作者进行生产的一种工艺文件。
它的内容包括工序及各工步的加工内容;本工序完成后工件的形状、尺寸和公差;各工步切削参数;本工序所用的机床、刀具和工艺安装等。
数控加工刀具卡主要包括刀具的详细资料,有刀具号、刀具名称及规格、刀辅具等。
它也是用来编制零件加工程序和指导生产的重要工艺文件。
3零件铣削加工工艺分析
3.1分析零件图,