检测指标含义24页文档资料.docx
《检测指标含义24页文档资料.docx》由会员分享,可在线阅读,更多相关《检测指标含义24页文档资料.docx(14页珍藏版)》请在冰豆网上搜索。
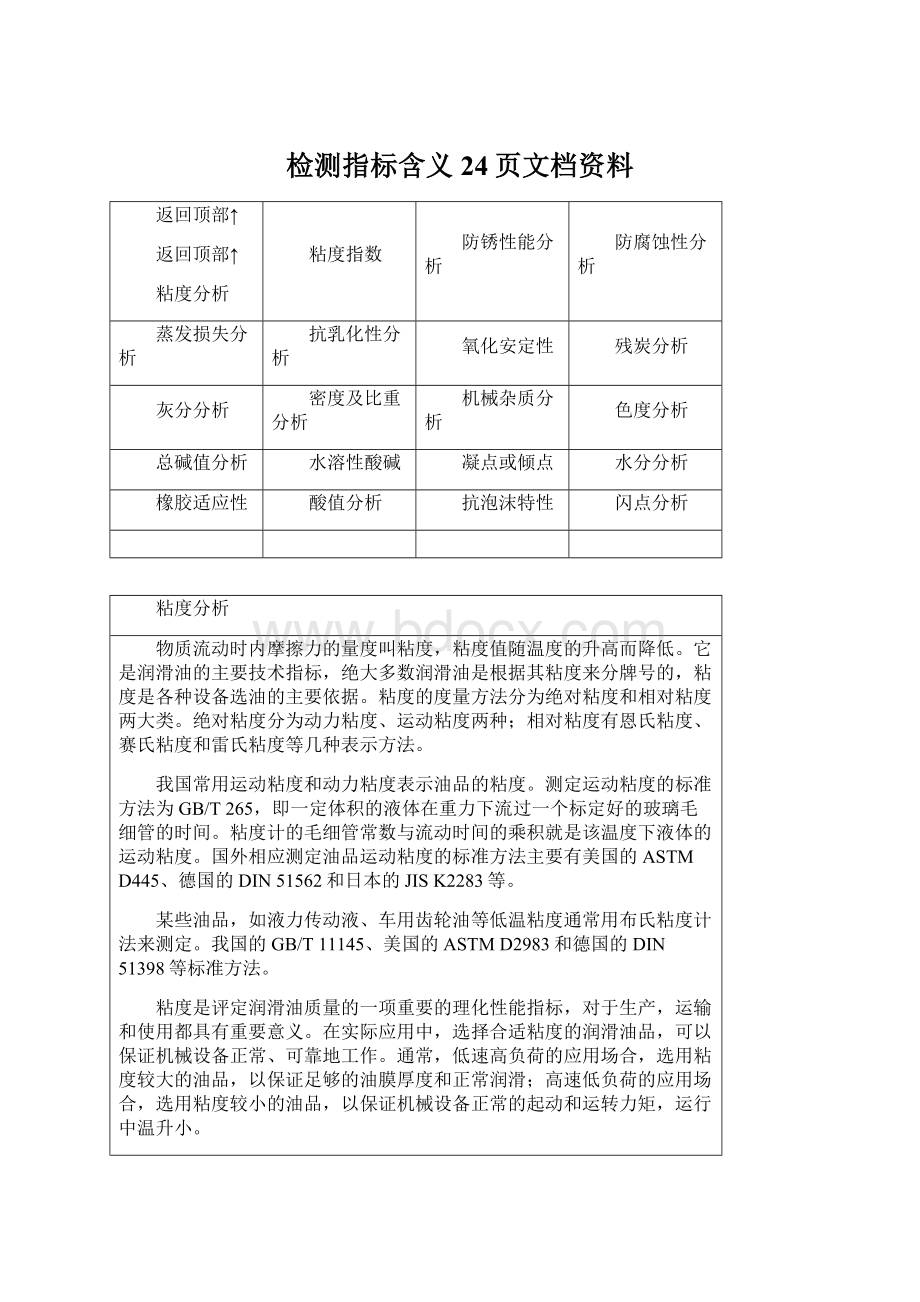
检测指标含义24页文档资料
返回顶部↑
返回顶部↑
粘度分析
粘度指数
防锈性能分析
防腐蚀性分析
蒸发损失分析
抗乳化性分析
氧化安定性
残炭分析
灰分分析
密度及比重分析
机械杂质分析
色度分析
总碱值分析
水溶性酸碱
凝点或倾点
水分分析
橡胶适应性
酸值分析
抗泡沫特性
闪点分析
粘度分析
物质流动时内摩擦力的量度叫粘度,粘度值随温度的升高而降低。
它是润滑油的主要技术指标,绝大多数润滑油是根据其粘度来分牌号的,粘度是各种设备选油的主要依据。
粘度的度量方法分为绝对粘度和相对粘度两大类。
绝对粘度分为动力粘度、运动粘度两种;相对粘度有恩氏粘度、赛氏粘度和雷氏粘度等几种表示方法。
我国常用运动粘度和动力粘度表示油品的粘度。
测定运动粘度的标准方法为GB/T265,即一定体积的液体在重力下流过一个标定好的玻璃毛细管的时间。
粘度计的毛细管常数与流动时间的乘积就是该温度下液体的运动粘度。
国外相应测定油品运动粘度的标准方法主要有美国的ASTMD445、德国的DIN51562和日本的JISK2283等。
某些油品,如液力传动液、车用齿轮油等低温粘度通常用布氏粘度计法来测定。
我国的GB/T11145、美国的ASTMD2983和德国的DIN51398等标准方法。
粘度是评定润滑油质量的一项重要的理化性能指标,对于生产,运输和使用都具有重要意义。
在实际应用中,选择合适粘度的润滑油品,可以保证机械设备正常、可靠地工作。
通常,低速高负荷的应用场合,选用粘度较大的油品,以保证足够的油膜厚度和正常润滑;高速低负荷的应用场合,选用粘度较小的油品,以保证机械设备正常的起动和运转力矩,运行中温升小。
返回顶部↑
粘度指数
滑油的粘度随温度的变化而变化:
温度升高,粘度减小;温度降低,粘度增大。
这种粘度随温度变化的性质,叫做粘温性能。
粘度指数(VI)是表示油品粘温性能的一个约定量值。
粘度指数高,表示油品的粘度随温度变化小,油的粘温性能好。
反之亦然。
石油产品的粘度指数可通过计算得到。
计算方法在我国的GB/T1995或美国的ASTMD2270、德国的DIN51564、ISO2902、日本的JISK2284等标准中有详细的说明。
通常粘度指数均用查表法得到。
粘温性能对润滑油的使用有重要意义,如发动机润滑油的粘温性能不好,当温度低时粘度过大,就会启动困难,而且启动后润滑油不易流到摩擦表面上,造成机械零件的磨损。
如果温度过高,粘度变小,则不易在摩擦表面上产生适当的油膜,失去润滑作用,使机械零件的摩擦面产生擦伤和胶合等故障。
闪点分析
在规定条件下,加热油品所逸出的蒸汽和空气组成的混合物与火焰接触发生瞬间闪火时的最低温度称为闪点,以℃表示。
润滑油闪点的高低,取决于润滑油质量的轻重,或润滑油中是否混入轻质组分和轻质组分的含量多少,轻质润滑油或含轻质组分多的润滑油,其闪点就较低。
相反,重质润滑油的闪点或含轻质组分少的润滑油,其闪点就较高。
润滑油的闪点是润滑油的贮存、运输和使用的一个安全指标,同时也是润滑油的挥发性指标。
闪点低的润滑油,挥发性高,容易着火,安全性差,润滑油挥发性高,在工作过程中容易蒸发损失,严重时甚至引起润滑油粘度增大,影响润滑油的使用。
重质润滑油的闪点如突然降低,可能发生轻油混入事故。
从安全角度考虑,石油产品的安全性是根据其闪点的高低而分类的:
闪点在45℃以下的为易燃品,闪点在45℃以上的产品为可燃品。
闪点的测定方法分为开口杯法和闭口杯法。
开口杯法用以测定重质润滑油和深色润滑油的闪点,方法是GB/T267-88。
闭口杯法用以测定闪点在150℃以下的轻质润滑油的闪点,方法为GB/T2641-83。
同一种润滑油,开口闪点总比闭口闪点高,因为开口闪点测定器所产生的油蒸汽能自由地扩散到空气中,相对不易达到可闪火的温度。
通常开口闪点要比闭口闪点高20-30℃。
国外测定润滑油闪点(开口)的标准有美国的ASTMD92,德国的DIN51376和日本的JISK2274等,闭口闪点有ASTMD93、DIN51758和JISK2265等。
凝点或倾点
润滑油试样在规定的试验条件下冷却至停止流动时的最高温度称为凝点。
而试样在规定的试验条件下,被冷却的试样能够流动的最低温度称为倾点。
凝点和倾点都是表示油品低温流动性的指标,二者无原则差别,只是测定方法有所不同。
同一试样测得的凝点和倾点并不是完全相等,一般倾点都高于凝点2-3℃,但也有两者相等或倾点低于凝点的情况。
国外常用倾点(流动点),我国也一般采用倾点这个标准。
温度很低时,粘度变大,甚至变成无定型的玻璃状物质,失去流动性。
因此在生产、运输和使用润滑油时因根据环境条件和工况选用相适应的倾点(或倾点)。
(1)润滑油凝点测定法(GB/T510)测定的基本过程是:
将试样装入试管中,按规定的预处理步骤和冷却速度进行试验。
当试样温度冷却到预期的凝点时,将浸在冷剂中的仪器倾斜45度保持1min后,取出观察试管里面的液面是否有过移动的迹象。
如有移动时,从套管中取出试管,并将试管重新预热,然后用比上次试验温度低4℃或其它更低的温度重新进行测定,直至某试验温度时液面位置停止移动为止。
如没有移动,从套管中取出试管,并将试管重新预热,然后用比上次试验温度高4℃或其它更高的温度重新进行测定,直至某试验温度时液面位置有了移动为止。
找出凝点的温度范围(即液面位置从移动到不移动或从不移动到移动的温度范围)之后,采用比移动的温度低2℃或采用比不移动的温度高2℃,重新进行试验,直至确定某试验温度能使试样的液面停留不动而提高2℃又能使液面移动时,就取使液面不动的温度作为试样的凝点。
(2)润滑油倾点测定法(GB/T3535)试验的基本过程是:
将清洁的试样注入试管中,按方法所规定的步骤进行试验。
对倾点高于33℃的试样,试验从高于预期的倾点9℃开始,对其它的倾点试样则从高于其倾点12℃开始。
每当温度计读数为3℃的倍数时,要小心地把试管从套管中取出,倾斜试管到刚好能观察到试管内试样是否流动,取出试管到放回试管的全部操作要求不超过3s。
当倾斜试管,发现试样不流动时,就立即将试管放在水平位置上,仔细观察试样的表面,如果在5s内还有流动,则立即将试管放回套管,待温度降低3℃时,重复进行流动试验,直到试管保持水平位置5s而试样无流动时,纪录观察到的试验温度计读数,再加3℃作为试样的倾点。
返回顶部↑
抗泡沫特性
常规分析项目
泡沫特性指油品生成泡沫的倾向及泡沫的稳定性。
润滑油在实际使用中,由于受到振荡、搅动等作用,使空气进入润滑油中,以至形成气泡。
因此要求评定油品生成泡沫的倾向性(ml)和泡沫稳定性(ml)。
这个项目主要用于评定内燃机油和循环用油(如液压油、压缩机油等)的起泡性。
润滑油产生泡沫具有以下危害:
1.大量而稳定的泡沫,会使体积增大,易使油品从油箱中溢出;2.增大润滑油的压缩性,使油压降低。
如液压油是靠静压力传递功的,油中一旦产生泡沫,就会使系统中的油压降低,从而破坏系统中传递功的作用。
3.增大润滑油与空气接触面积,加速油品的老化。
这个问题对空压机油来说,尤为严重。
4.带有气泡的润滑油被压缩时,气泡一旦在高压下破裂,产生的能量会对金属表面产生冲击,使金属表面产生穴蚀。
有些内燃机油的轴瓦就出现这种穴蚀现象。
润滑油容易受到配方中的活性物质如清净剂、极压添加剂和腐蚀抑制剂的影响,这些添加剂大大地增加了油的起泡倾向。
润滑油的泡沫稳定性随粘度和表面张力而变化,泡沫的稳定性与油的粘度成反比,同时随着温度的上升,泡沫的稳定性下降,粘度较小的油形成大而容易消失的气泡,高粘度油中产生分散的和稳定的小气泡。
为了消除润滑油中的泡沫,通常在润滑油中加入表面张力小的消泡剂如甲基硅油和非硅消泡剂等。
在我国,润滑油的泡沫特性可按GB/T12579-90润滑油泡沫特性测定标准方法进行试验,先恒温至规定温度,再向装有试油的量筒中通过一定流量和压力的空气,记下通气5分钟后产生的泡沫体积(ml)和停气静止10分钟后泡沫的体积(ml)。
泡沫越少,润滑油的抗(消)泡性越好。
美国和日本分别用ASTMD892、JISK2518标准方法评定。
航空润滑油可按GJB498-88航空涡轮发动机油泡沫特性测定法(静态泡沫试验),其方法概要是:
向在24±0.5℃和93±0.5℃下恒温的两个泡沫试验量筒中的润滑油通入规定量的净化空气,通气5分钟后记下泡沫的体积,静置10分钟后再记录泡沫体积,93℃通气试验完毕后的试样在室温下冷却至43℃,再放入24±0.5℃恒温浴中,测其在该温度下的泡沫倾向和泡沫稳定性,整个试验必须在3小时内完成。
返回顶部↑
抗乳化性分析
(1)概述
乳化是一种液体在另一种液体中紧密分散形成乳状液的现象,它是两种液体的混合而并非相互溶解。
抗乳化则是从乳状物质中把两种液体分离开的过程。
润滑油的抗乳化性是指油品遇水不乳化,或虽是乳化但经过静置,油-水能迅速分离的性能。
两种液体能否形成稳定的乳状液取决于两种液体之间的界面张力。
由于界面张力的存在,分散相总是倾向于缩小两种液体之间的接触面积以降低系统的表面能,即分散相总是倾向于由小液滴合并大液滴以减少液滴的总面积,乳化状态也就是随之而被破坏。
界面张力越大,这一倾向就越强烈,也就越不易形成稳定的乳状液。
润滑油与水之间的界面张力随润滑油的组成不同而不同。
深度精制的基础油以及某些成品油与水之间的界面张力相当大,因此,不会生成稳定的乳状液。
但是如果润滑油基础油的精制深度不够,其抗乳化性也就较差,尤其是当润滑油中含有一些表面活性物质时,如清净分散剂、油性剂、极压剂、胶质、沥青质及尘土粒等,它们都是一些亲油剂和亲水基物质,它们吸附在油水表面上,使油品与水之间的界面张力降低,形成稳定的乳状液。
因此在选用这些添加剂时必须对其性能作用作全面的考虑,以取得最佳的综合平衡。
对于用于循环系统中的工业润滑油,如液压油、齿轮油、汽轮机油、,油膜轴承油等,在使用中不可避免地和冷却水或蒸汽甚至乳化液等接触,这就是要求这些油品在油箱中能迅速油-水分离,(按油箱容量,一般要求6-30min分离),从油箱底部排出混入的水分,便于油品的循环使用,并保持良好的润滑。
通常润滑油在60℃左右有空气存在并与水混合搅拌的情况下,不仅易发生氧化和乳化而降低润滑性能,而且还会生成可溶性油泥,受热作用则生成不溶性油泥,并剧烈增加流体粘度,造成堵塞润滑系统、发生机械故障。
因此,一定要处理好基础油的精制深度和所用添加剂与其抗乳化剂的关系,在调合、使用、保管和贮运过程中亦要避免杂质的混入和污染,否则若形成了乳化液,则不仅会降低润滑性能,损坏机件,而且易形成油泥。
另外,随着时间的增长,油品的氧化、酸性的增加、杂质的混入都会使抗乳化性的变差,用户必须及时处理或者更换。
(2)润滑油抗乳化性能测定法
目前被广泛采用的抗乳化性测定方法有两个。
其一是油和合成液抗乳化性能测定法(GB/T7305-87),本方法与ASTMD1401-67(77)等效。
本方法适用于测定油、合成液与水分离的能力。
它适用于测定40℃时运动粘度为30-100mm2/s的油品,试验温度为(54±1)℃。
它可用于粘度大于100mm2/s油品,但试验温度为(82±1)℃。
其他试验温度也可以采用,例如25℃。
当所测试的合成液的密度大于水时,试验步骤不变,但这时水可能浮在乳化层或合成液上面。
其二是润滑油抗乳性测定法(GB/T8022-87)本方法与ASTMD2711-74(79)方法等同采用。
本方法是用于测定中、高粘度润滑油与水互相分离的能力。
本方法对易受水污染和可能遇到泵送及循环湍流而产生油包水型乳化液的润滑油抗乳化性能的测定具有指导意义。
汽轮机油的抗乳化能力通常按SH/T34009-87方法进行,将20ml试样在90℃左右与水蒸汽乳化,然后把乳化液置于约94℃的浴中,测定分离出20ml油所需的时间。
这个方法是完全模拟汽轮机油的工作条件,是测定汽轮机油抗乳化性的专用方法。
返回顶部↑
防腐蚀性分析
(1)概述
金属表面受周围介质的化学或电化学的作用而被破坏称为金属的腐蚀。
润滑油的各类烃本身对金属是没有腐蚀作用的,引起油品对金属腐蚀的主要物质是油中的活性硫化物(如元素硫、硫醇、硫化氢和二硫化物等。
注意,不是所有的含硫化合物均是腐蚀性物质)和低分子有机酸类,以及基础油中一些无机酸和碱等。
这些腐蚀性物质又可能是基础油和添加剂生产过程中所残留的,也有可能源于油品的氧化产物或油品储运和使用过程中的污染。
(2)腐蚀性测定法
1)GB/T5096石油产品铜片腐蚀试验,这是目前工业润滑油最主要的腐蚀性测定法,本方法与ASTM
D130-83方法等效。
试验方法概要是:
把一块已磨光好的铜片浸没在一定量的试样中,并按产品标准要求加热到指定的温度,保持一定的时间。
待试验周期结束时,取出铜片,在洗涤后与标准色板进行比较,确定腐蚀级别。
工业润滑油常用的试验条件为100℃(或120℃),3h。
2)SH/T1095润滑油腐蚀试验方法,本方法用于试验润滑油对金属片的腐蚀性。
除非另行规定,金属片材料为铜或钢。
其试验原理与GB/T5096方法基本相同,其主要的差别在于:
一、试验结果只根据试片的颜色变化,判断合格或不合格;二、试验金属片不限于铜片。
3)GB/T391-88发动机润滑油腐蚀度测定法,测定内燃机油对轴瓦(铅铜合金等)的腐蚀度。
该方法是模拟粘附在金属片表面上的热润滑油薄膜与周围空气中氧定期接触时,所引起的金属腐蚀现象。
铅片在热到140℃的试油中,经50小时的试验后,依金属片的重量变化确定油的腐蚀程度,以g/cm3表示。
4)航空润滑油对金属腐蚀的测定方法有:
GJB497-88航空润滑油铅腐蚀度测定方法。
测定的是在铜催化剂存在的条件下,163±1℃的温度下,1小时后测定铅片单位面积的重量变化。
高温航空润滑油还要求按GJB496-88进行试验,将铜片和银片分别浸入试样中,置于232℃下50小时后,测定其重量损失。
航空发动机油对金属的腐蚀性,除了进行上述腐蚀试验外,还要结合氧化试验,测定润滑油在强氧化条件对铅、铜、镁、铝、银等金属的腐蚀性能。
5)汽车制动液对金属的腐蚀性,除了应按GB/T5096进行100℃、3h的铜腐蚀试验外,还须进行叠片腐蚀试验,用马口铁、10号钢、LY12铝、HT200铸铁、H62黄铜、T2紫铜等六种金属试片按一定顺序联接在一起,在100℃下试验120小时,试验结束后测定试片的重量的变化。
返回顶部↑
防锈性能分析
所谓防锈性,是指润滑油品阻止与其接触的金属部件生锈的能力。
评定防锈性的方法很多,在工业润滑油规格中最常见的方法是GB/T11143加抑制剂矿物油在水存在下防锈性能试验法,该方法与ASTMD665方法等效。
GB/T1143方法概要是:
将一支一端呈圆锥形的标准钢棒浸入300ml试油与30ml(A)蒸馏水或(B)合成海水混合液中,在60℃和以100r/min搅拌的条件下,经过24h后将钢棒取出,用石油醚冲洗,晾干,并立即在正常光线下用目测评定试棒的锈蚀程度。
锈蚀程度分如下几级:
无锈:
钢棒上没有锈斑。
轻微锈蚀:
钢棒上锈点不多于6个点,每个点的直径等于或小于1mm。
中等锈蚀:
锈蚀点超过6点,但小于试验钢棒表面积的5%。
严重锈蚀:
生锈面积大于5%。
水和氧的存在是生锈不可缺少的条件。
汽车齿轮中,由于空气中湿气在齿轮箱中冷凝而有水存在,工业润滑装置如齿轮装置、液压系统和涡轮装置等由于使用环境的关系,也不可避免的有水浸入。
其次,油中酸性物质的存在也会促进锈蚀,为提高油品的防锈性能,常常加入一些极性有机物,即防锈剂。
返回顶部↑
酸值分析
中和1克油品中的酸性物质所需要的氢氧化钾毫克数称为酸值,用mgKOH/g油表示。
酸值表示润滑油品中酸性物质的总量。
这些酸性物质对机械都有一定程度的腐蚀性。
特别是在有水分存在的条件下,其腐蚀性更大。
另外,润滑油在贮存和使用过程中被氧化变质,酸值也会逐渐变大,因此常用酸值变化大小来衡量润滑油的氧化安定性。
故酸值是油品质量中应严格控制的指标之一。
对于在用油品,当酸值增大到一定数值时,就必须换掉。
测定酸值的方法分为两大类,一类是颜色指示剂法,即根据指示剂的颜色来确定滴定的终点,如我国的GB/T264-83或SH/T0163-92、美国的ASTMD974和德国的DIN51558等。
另一类为电位滴定法,即根据电位变化来确定滴定终点,主要用于深色油品的酸值测定。
这类方法有我国的GB/T7304-87和美国的ASTMD664等。
返回顶部↑
总碱值分析
在规定的条件下滴定时,中和1g试样中全部碱性组分所需高氯酸的量,以当量氢氧化钾毫克数表示,称为润滑油或添加剂的总碱值。
总碱值表示试样中含有有机和无机碱、胺基化合物、弱酸盐如皂类、多元酸的碱性盐和重金属的盐类。
内燃机油的总碱值则可间接表示其所含清净分散剂的多少。
因而总碱值为内燃机油的重要质量指标。
在内燃机油的使用过程中,分析其总碱值的变化,可以反映出润滑油中添加剂的消耗情况。
石油产品总碱值测定可按SH/T0251-92标准方法进行。
该方法是以石油醚-冰乙酸为溶剂,用0.1N高氯酸标准溶液进行非水滴定来测定石油产品和添加剂中碱性组分的含量。
返回顶部↑
水溶性酸碱
用一定体积的中性的蒸馏水和润滑油在一定温度下相混合、振荡,使蒸馏水将润滑油中的水溶性酸和碱抽出来,然后测定蒸馏水溶液的酸性和碱性,称为润滑油的水溶性酸和碱,按GB/T
259-88标准方法进行测定。
润滑油的水溶性酸是润滑油中溶于水的低分子有机酸和无机酸(硫酸及其衍生物如磺酸及酸性硫酸酯等)。
润滑油中的水溶性碱,是指润滑油中溶于水的碱和碱性化合物,如氢氧化钠及碳酸钠等。
新油中如有水溶性酸或碱,则可能是润滑油精制过程中酸碱分离不好的结果;贮存和使用过程中的润滑油如含有水溶性酸或碱,则表明润滑油被污染或氧化分解。
因此,润滑油的水溶性酸和碱也是一项质量指标。
润滑油的水溶性酸和碱不合格,将腐蚀机械设备。
对于汽轮机油,水溶性酸和碱的存在,使汽轮机油的抗乳化度降低。
对于变压器油,水溶性酸碱不合格时,不仅会腐蚀设备,而且使变压器的耐电压下降。
返回顶部↑
氧化安定性
石油产品抵抗由于空气(或氧气)的作用而引起其性质发生永久性改变的能力,叫做油品的氧化安定性。
润滑油的抗氧化安定性是反映润滑油在实际使用、贮存和运输中氧化变质或老化倾向的重要特性。
油品在贮存和使用过程中,经常与空气接触而起氧化作用,温度的升高和金属的催化会加深油品的氧化。
润滑油品氧化的结果,使油品颜色变深,粘度增大,酸性物质增多,并产生沉淀。
这些无疑对润滑油的使用会带来一系列不良影响,如腐蚀金属,堵塞油路等。
对内燃机油来说,还会在活塞表面生成漆膜,粘结活塞环,导致汽缸的磨损或活塞的损坏。
因此,这个项目是润滑油品必控质量指标之一,对长期循环使用的汽轮机油、变压器油、内燃机油以及与大量压缩空气接触的空气压缩机油等,更具重要意义。
通常油品中均加有一定数量的抗氧剂,以增加其抗氧化能力,延长使用寿命。
润滑油氧化安定性测定方法有多种,其原理基本相同,一般都是向试样中直接通入氧气或净化干燥的空气。
在金属等催化剂的作用下,在规定温度下经历规定的时间观察试样的沉淀或测定沉淀值、测定试样的酸值、粘度等指标的变化。
试验条件因油品而异,氧化设备也因油品而不同,尽量模拟油品使用的状况。
我国对航空涡轮发动机润滑油的抗氧化安定性按两种方法GJB499-88和SH/T0450-92进行氧化试验,前者称为大氧化管法,后者称为小氧化管法;对内燃机油的测定方法有SH/T0299-92和SH/T0192-92标准进行;汽轮机油SH/T0193-92旋转氧弹法来测定其抗氧化性能;变压器油的氧化特性按SH/T0206-92即国际电工委员会标准IEC74-1974标准方法进行;中高档润滑油氧化安定性测定主要有GB/T12581加抑制剂矿物油氧化特性测定法、GB/T12709润滑油老化特性测定法(康氏残炭法)、SH/T0123极压润滑油氧化安定性测定法进行。
返回顶部↑
机械杂质分析
机械杂质就是指存在于润滑油中不溶于汽油、乙醇和苯等溶剂的沉淀物或胶状悬浮物。
机械杂质来源于润滑油的生产、贮存和使用中的外界污染或机械本身磨损,大部分是砂石和积碳类,以及由添加剂带来的一些难溶于溶剂的有机金属盐。
机械杂质的测定按GB/T511-83石油产品和添加剂机械杂质测定法(重量法)进行。
其过程是:
称取100g的试油加热到70℃到80℃,加入2-4倍的溶剂,在已衡重的空瓶中的纸上过滤,用热溶剂洗净滤纸瓶再称重,定量滤纸的前后重量之差就是机械杂质的重量,由此求出机械杂质的质量分数。
机械杂质和水分、灰分、残炭都是反映油品纯洁性的质量指标,反映油品精制的程度。
一般来讲润滑油基础油的机械杂质的质量分数都应该控制在0.005%以下(机械杂质在此以下认为是无),加剂后成品油的机械杂质一般都是增大,这是正常的。
对用户来讲,测定机械杂质也是必要的,因为润滑油在使用、存储、运输中混入灰尘、泥沙、金属碎屑、铁锈及金属氧化物等,这些杂质的存在,将加速机械设备的磨损,严重时堵塞油路、油嘴和滤油器,破坏正常润滑。
另外金属碎屑在一定的温度下,对油起催化作用,应该进行必要的过滤。
但是,对于一些加有大量添加剂油品的用户来讲,机械杂质的指标表面上看是大了一些(如一些高档的内燃机油),但其杂质主要是加入了多种添加剂后所引入的溶剂不溶物,这些胶状的金属有机物,并不影响使用效果,用户不应简单地用“机械杂质”的大小去判断油品的好坏,而是应分析“机械杂质”的内容,否则,就会带来不必要的损失和浪费。
返回顶部↑
橡胶适应性
所有润滑系统和液压系统,特别是航空发动机润滑系统和液压系统,差不多所有的密封件和衬垫都是合成或天然橡胶制成的。
因此要求润滑油和橡胶要有较好的适应性,避免引起橡胶密封件变形。
一般说来,烷烃对橡胶的溶胀或收缩作用不大;而芳烃则能使橡胶溶胀,含硫元素较多的油品则易使橡胶收缩;此外,许多合成润滑油对普通橡胶有较大的溶胀或收缩性,使用时应加以注意,选用特种橡胶(如硅橡胶、氟橡胶)作密封件。
液压油规格中所用的测定方法是SH/T0305-92石油产品密封适应性指数测定法是测定石油产品和丁腈橡胶密封材料的适应性,用体积膨胀百分数表示。
方法概述:
用量规测定橡胶圈的内径,然后将橡胶圈浸在100℃的试样中24h,在1h内将橡胶圈冷却后,用量规测量内径的变化。
SH/T0436-92合成航空润滑油与橡胶的相容性试验方法,是将规定的丁腈标准橡胶BD-L、BD-G及氟标准橡胶BF等标准试片,浸泡在一定温度的合成润滑油中在规定的时间后测定橡胶试片浸泡前后的性能变化(体积变化、拉伸应力应变性能变化和硬度变化)。
汽车制动液的橡胶相容性能是制动液的一项重要指标,GB12981-91合成制动液规格中规定了制动液与橡胶皮碗适应性检验方法,将标准橡胶件(汽车制动系统用分泵皮碗)浸入制动液中,在规定温度(70℃和120℃)下70保持小时,对皮碗的外观、根部直径增值、硬度下降值等进行测定。
返回顶部↑
蒸发损失分析
油品的蒸发损失,即油品在一定条件下通过蒸发而损失的量,用质量百分比表示。
蒸发损失与油品的挥发度成正比。
蒸发损失越大,实际应用中的油耗就越大,故对油品在一定条件下的蒸发损失量要有限制。
润滑油在使用过程中蒸发,造成润滑系统中润滑油量逐渐减少,需要补充,粘度增大,影响供油。
液压液体在使用中蒸发,还会产生气穴现象和效率下降,可能给液压泵造成损害。
蒸馏方法得到的数据只是粗略的结果,润滑油品的蒸发损失需专门方法测定。
目前,我国测定润滑油蒸发损失的方法为GB/T7325润滑油和润滑脂蒸发损失测定法。
该方