套类零件的加工.docx
《套类零件的加工.docx》由会员分享,可在线阅读,更多相关《套类零件的加工.docx(8页珍藏版)》请在冰豆网上搜索。
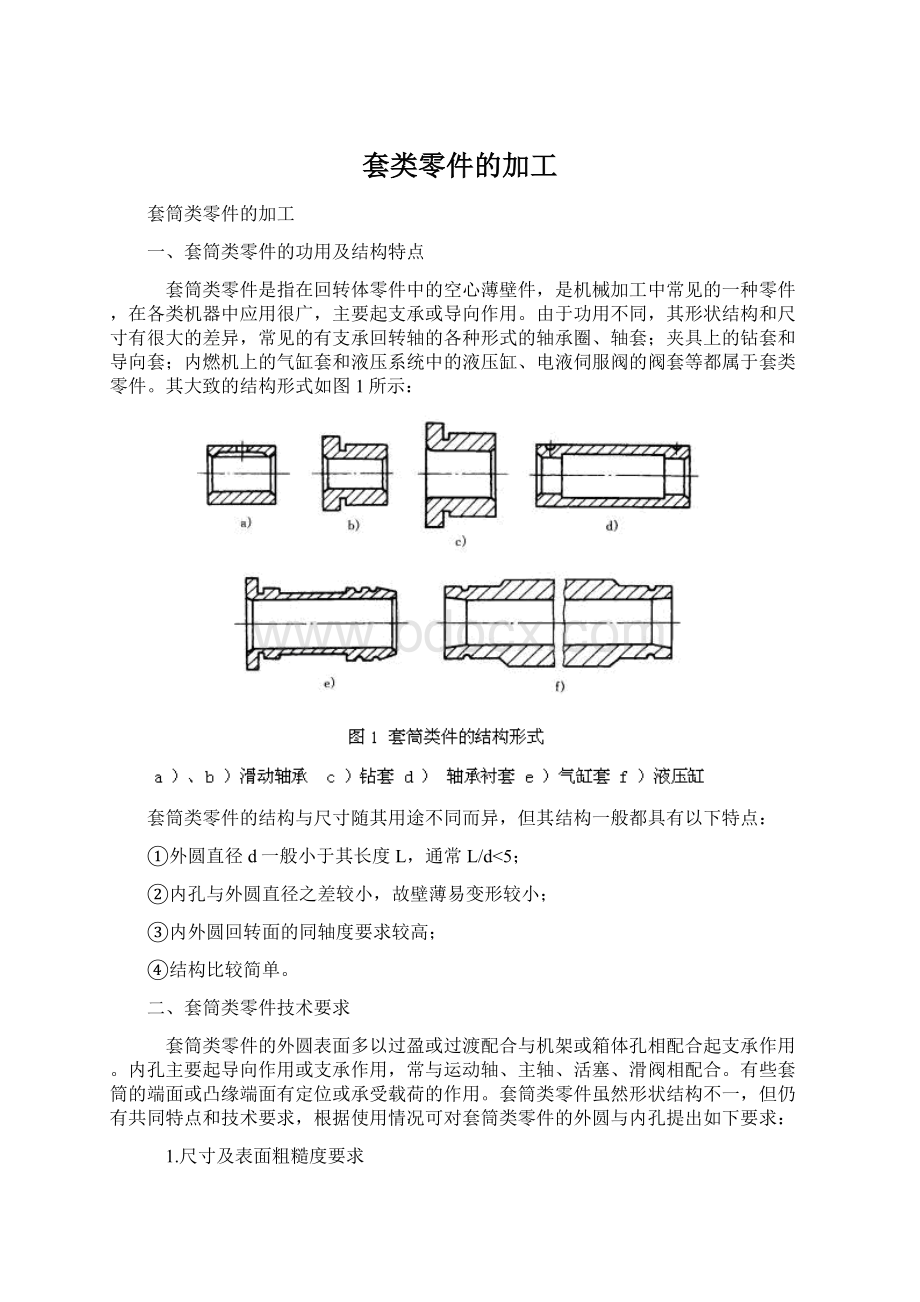
套类零件的加工
套筒类零件的加工
一、套筒类零件的功用及结构特点
套筒类零件是指在回转体零件中的空心薄壁件,是机械加工中常见的一种零件,在各类机器中应用很广,主要起支承或导向作用。
由于功用不同,其形状结构和尺寸有很大的差异,常见的有支承回转轴的各种形式的轴承圈、轴套;夹具上的钻套和导向套;内燃机上的气缸套和液压系统中的液压缸、电液伺服阀的阀套等都属于套类零件。
其大致的结构形式如图1所示:
套筒类零件的结构与尺寸随其用途不同而异,但其结构一般都具有以下特点:
①外圆直径d一般小于其长度L,通常L/d<5;
②内孔与外圆直径之差较小,故壁薄易变形较小;
③内外圆回转面的同轴度要求较高;
④结构比较简单。
二、套筒类零件技术要求
套筒类零件的外圆表面多以过盈或过渡配合与机架或箱体孔相配合起支承作用。
内孔主要起导向作用或支承作用,常与运动轴、主轴、活塞、滑阀相配合。
有些套筒的端面或凸缘端面有定位或承受载荷的作用。
套筒类零件虽然形状结构不一,但仍有共同特点和技术要求,根据使用情况可对套筒类零件的外圆与内孔提出如下要求:
1.尺寸及表面粗糙度要求
外圆直径精度通常为IT5-IT7,表面粗糙度Ra为5-0.63,要求较高的可达0.04。
内孔作为套类零件支承或导向的主要表面,要求内孔尺寸精度一般为IT6-IT7,表面粗糙度要求Ra2.5-0.16,有的精密套筒及阀套的内孔尺寸精度要求为IT4-IT5,也有的套筒(如油缸、气缸缸筒)由于与其相配的活塞上有密封圈,故对尺寸精度要求较低(IT8-IT9),但对表面粗糙度要求较高,一般为Ra2.5-1.6。
2.几何形状精度要求
通常将外圆与内孔的几何形状精度控制在直径公差以内即可,对精密轴套有时控制在孔径公差的1/2-1/3,甚至更严。
对较长套筒,除圆度有要求以外,还应有孔的圆柱度要求。
3.位置精度要求
主要应根据套类零件在机器中功用和要求而定。
如果内孔的最终加工是在套筒装配(如机座或箱体等)之后进行时,可降低对套筒内、外圆表面的同轴度要求;如果内孔的最终加工是在装配之前进行时,则同轴度要求较高,通常同轴度为0.01-0.06mm。
套筒端面(或凸缘端面)常用来定位或承受载荷,对端面与外圆和内孔轴心线的垂直度要求较高,一般为0.05-0.02mm.。
三、套筒类零件的材料、毛坯及热处理
套筒类零件毛坯材料的选择主要取决于零件的功能要求、结构特点及使用时的工作条件。
套筒类零件一般用钢、铸铁、青铜或黄铜和粉末冶金等材料制成。
套筒类零件的毛坯制造方式的选择与毛坯结构尺寸、材料、和生产批量的大小等因素有关。
孔径较大(一般直径大于20mm)时,常采用型材(如无缝钢管)、带孔的锻件或铸件;孔径较小(一般小于20mm)时,一般多选择热轧或冷拉棒料,也可采用实心铸件;大批大量生产时,可采用冷挤压、粉末冶金等先进工艺,不仅节约原材料,而且生产率及毛坯质量精度均可提高。
套筒类零件的功能要求和结构特点决定了套筒类零件的热处理方法有渗碳淬火、表面淬火、调质、高温时效及渗氮。
四、工件的定位装夹
轴向刚性比径向好,用卡爪径向夹紧,工件变形大,若沿轴向施加夹紧力,变形就会小得多:
刚性心轴:
弹性心轴、液性塑料心轴:
五、内孔表面的加工
常用的孔加工方法有:
钻孔、扩孔、铰孔、镗孔、拉孔、磨孔以及光整加工。
铰刀
铰刀是一精度较高的多刃刀具,有6~12条刀齿,其工作部分由引导锥、切部分、校准部分组成。
引导锥是铰刀开始进入孔内时的导向部分:
常用铰刀:
与钻孔、扩孔一样,只要工件与刀具之间有相对的旋转运动和轴向进给运动,就可进行铰削加工。
因此,车床、钻床、镗床和铣床都可完成铰孔作业。
铰削适合于加工钢、铸铁和有色金属材料,但不能加工硬度过高的材料(如淬火钢、冷硬铸铁等)。
拉刀
拉削在工业生产中应用很广泛,可加工不同的内外表面,种类也很多,如按加工表面的不同,可分为内拉刀和外拉刀,内拉刀用于加工内表面。
常见的有圆孔拉刀、花键拉刀、方孔拉刀和键槽拉刀等。
一般内拉刀刀齿的形状都做成被加工孔的形状。
外拉刀用于加工外成形表面。
在我国内拉刀比外拉刀应用更普遍些。
普通圆孔拉刀的结构如图所示:
珩磨
珩磨是磨削加工的一种特殊形式,属于光整加工,需要在磨削或精镗的基础上进行。
珩磨加工范围比较广,特别是大批大量生产中采用专用珩磨机珩磨更为经济合理,对于某些零件,珩磨已成为典型的光整加工方法,如发动机的气缸套,连杆孔和液压缸筒等。
(1)珩磨原理
在一定压力下,珩磨头上的砂条(油石)与工件加工表面之间产生复杂的的相对运动,珩磨头上的磨粒起切削、刮擦和挤压作用,从加工表面上切下极薄的金属层。
(2)珩磨方法
珩磨所用的工具是由若干砂条(油石)组成的珩磨头,四周砂条能作径向张缩,并以一定的压力与孔表面接触。
珩磨头与工件之间的旋转和往复运动,使砂条的磨粒在孔表面上的切削轨迹形成交叉而又不相重复的网纹。
珩磨时磨条便从工件上切去极薄的一层材料,并在孔表面形成交叉而不重复的网纹切痕(如图7.3b),这种交叉而不重复的网纹切痕有利于贮存润滑油,使零件表面之间易形成—层油膜,从而减少零件间的表面磨损。
(3)珩磨加工的特点
1)工件发热少,不易烧伤,而且变形层很薄,从而可获得较高的表面质量。
珩磨时砂条与工件孔壁的接触面积很大,磨粒的垂直负荷仅为磨削的1/50-1/100。
珩磨的切削速度较低,一般在100m/min以下,仅为普通磨削的1/30-1/100。
在珩磨时,注入的大量切削液,可使脱落的磨粒及时冲走,还可使加工表面得到充分冷却,所以
2)珩磨可达较高的尺寸精度和较低的粗糙度,珩磨能获得的孔的精度为IT6-IT7级,表面粗糙度Ra为0.2-0.025
。
3)珩磨加工不能修正孔的相对位置误差,因此,珩磨前在孔精加工工序中必须安排预加工以保证其位置精度。
珩磨头与机床主轴采用浮动联接,珩磨头工作时,由工件孔壁作导向,沿预加工孔的中心线作往复运动——自为基准。
4)珩磨孔的生产率高,机动时间短,加工质量高,加工范围大,可加工铸铁件、淬火和不淬火的钢件以及青铜件等,但不宜加工韧性大的有色金属。
五、典型套筒类零件的加工工艺