无刻蚀镀铁电沉积机理及综合性能.docx
《无刻蚀镀铁电沉积机理及综合性能.docx》由会员分享,可在线阅读,更多相关《无刻蚀镀铁电沉积机理及综合性能.docx(11页珍藏版)》请在冰豆网上搜索。
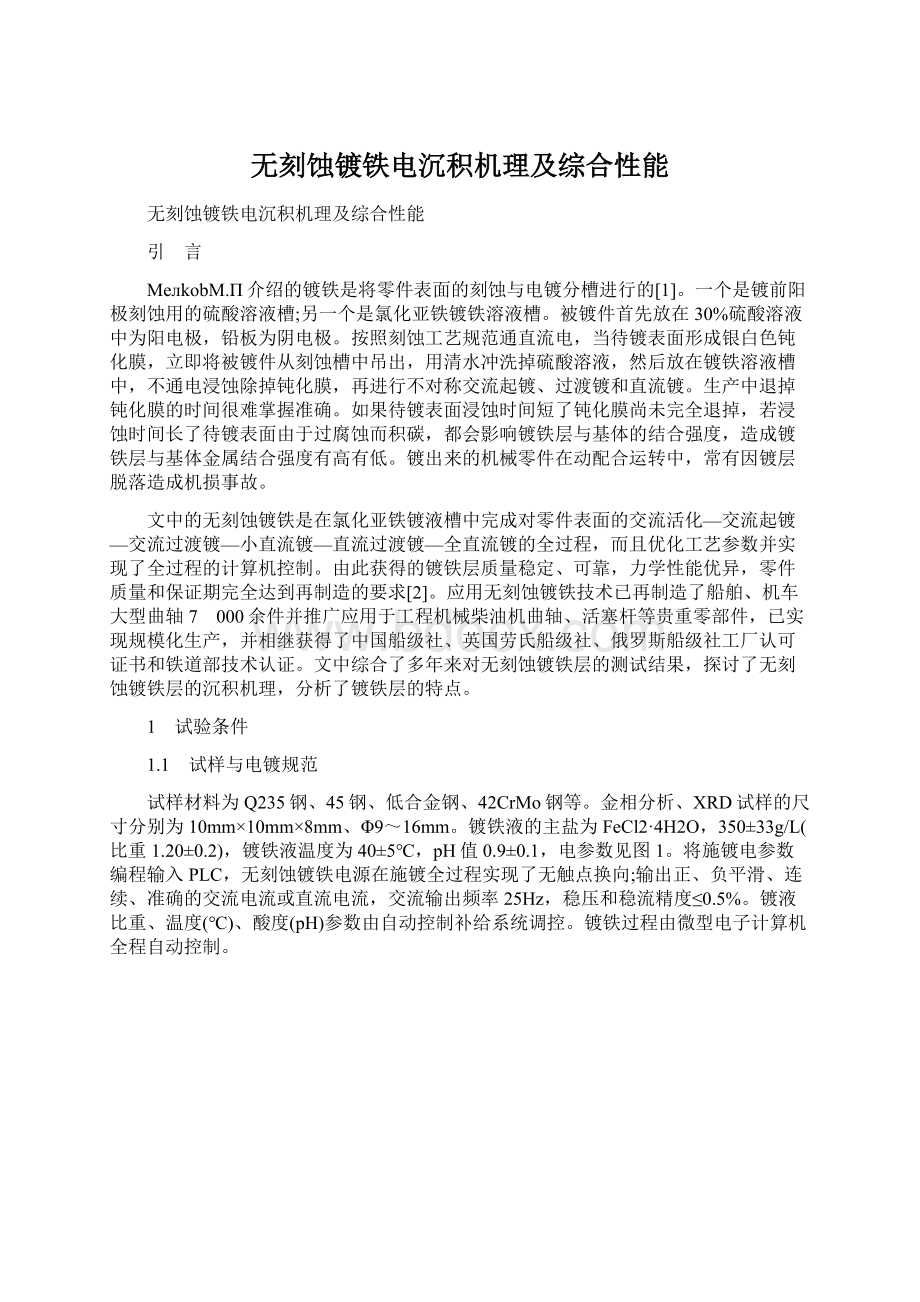
无刻蚀镀铁电沉积机理及综合性能
无刻蚀镀铁电沉积机理及综合性能
引 言
MeлkobM.П介绍的镀铁是将零件表面的刻蚀与电镀分槽进行的[1]。
一个是镀前阳极刻蚀用的硫酸溶液槽;另一个是氯化亚铁镀铁溶液槽。
被镀件首先放在30%硫酸溶液中为阳电极,铅板为阴电极。
按照刻蚀工艺规范通直流电,当待镀表面形成银白色钝化膜,立即将被镀件从刻蚀槽中吊出,用清水冲洗掉硫酸溶液,然后放在镀铁溶液槽中,不通电浸蚀除掉钝化膜,再进行不对称交流起镀、过渡镀和直流镀。
生产中退掉钝化膜的时间很难掌握准确。
如果待镀表面浸蚀时间短了钝化膜尚未完全退掉,若浸蚀时间长了待镀表面由于过腐蚀而积碳,都会影响镀铁层与基体的结合强度,造成镀铁层与基体金属结合强度有高有低。
镀出来的机械零件在动配合运转中,常有因镀层脱落造成机损事故。
文中的无刻蚀镀铁是在氯化亚铁镀液槽中完成对零件表面的交流活化—交流起镀—交流过渡镀—小直流镀—直流过渡镀—全直流镀的全过程,而且优化工艺参数并实现了全过程的计算机控制。
由此获得的镀铁层质量稳定、可靠,力学性能优异,零件质量和保证期完全达到再制造的要求[2]。
应用无刻蚀镀铁技术已再制造了船舶、机车大型曲轴7 000余件并推广应用于工程机械柴油机曲轴、活塞杆等贵重零部件,已实现规模化生产,并相继获得了中国船级社、英国劳氏船级社、俄罗斯船级社工厂认可证书和铁道部技术认证。
文中综合了多年来对无刻蚀镀铁层的测试结果,探讨了无刻蚀镀铁层的沉积机理,分析了镀铁层的特点。
1 试验条件
1.1 试样与电镀规范
试样材料为Q235钢、45钢、低合金钢、42CrMo钢等。
金相分析、XRD试样的尺寸分别为10mm×10mm×8mm、Φ9~16mm。
镀铁液的主盐为FeCl2·4H2O,350±33g/L(比重1.20±0.2),镀铁液温度为40±5℃,pH值0.9±0.1,电参数见图1。
将施镀电参数编程输入PLC,无刻蚀镀铁电源在施镀全过程实现了无触点换向;输出正、负平滑、连续、准确的交流电流或直流电流,交流输出频率25Hz,稳压和稳流精度≤0.5%。
镀液比重、温度(℃)、酸度(pH)参数由自动控制补给系统调控。
镀铁过程由微型电子计算机全程自动控制。
1.2 测试方法
镀铁层的结构、组织应用光学显微镜(OM)、扫描电子显微镜(SEM)、透射电子显微镜(TEM)和X射线衍射(XRD)进行分析;镀铁层的内应力、晶粒度及交流活化后的晶面极密度测定都应用了XRD;镀铁层的硬度梯度分布采用显微硬度计测定,镀铁层的结合强度采用改进的奥拉(Ollard)法测定[3-4],镀铁层的耐磨性采用环—块磨损机测定[3],镀铁试验弯曲疲劳性能按GB4337-84测试。
2 无刻蚀镀铁层的沉积机理研究
2.1 零件经交流活化后的表面状态
按图1施镀时先将零件放入镀铁液槽进行交流活化处理。
交流活化电压为±5V,时间5min。
然后按图1(b)规范交流起镀。
为证明形成微融活化态界面,扈心坦等分析了交流活化前、后及起镀后的试样在扫描电镜上拍摄的表面形貌[5],见图2。
由图2(a)知,低碳钢试件放入氯化亚铁溶液镀槽前由于经过酸化水清洗,表面产生了少许蚀点,分析是氢离子作用的结果。
图2(b)示出了对称交流活化后的低碳钢表面形貌,其特点是微观凹凸不平,而且凹坑是有选择性的。
由低碳钢的组织(F+P)在氯化亚铁电解液中的电化学作用规律可知:
铁素体(F)比珠光体(P)融解得快,所以图2(b)中的凹坑是铁素体被融解的记录,使该处处于高度的活化状态,这种状态称为微融活化态。
当施加阴极有效电压进行不对称交流起镀(见图1中的b段)时,阴极与镀铁液界面中的Fe2+将优先在高活化区获得电子放电沉积,使原凹凸不平的微区变得不甚清晰并形成新的较浅的凹凸表面,其特征见图2(c)。
当起镀45s后,镀铁层已完全覆盖了施镀表面(见图2(d))。
试验显示,无刻蚀镀铁工艺中的对称交流活化的目的是获得适合于Fe2+选择还原沉积的微融活化态界面,这是获得镀铁层与基体高结合强度的基础条件。
2.2 镀铁层沉积中的择优取向
择优取向是多晶体物质中晶粒取向呈现某种程度的规律排列的组织状态。
镀铁层的择优取向可应用X射线衍射仪测定并计算。
试验采用D/MAX-Ⅲ-A衍射仪,测试条件为CoKα,加石墨单色器,测定镀铁层的(110)、(200)和(211)3个晶面的衍射强度并按式
(1)求出各晶面的极密度:
式中,ρhkl是(hkl)晶面的极密度;Ihkl是测得的(hkl)晶面衍射峰的相对强度;I0hkl是JCPDS卡片经修正为CoKα的值再经石墨单色器修正的值;n是被测衍射线的个数。
经XRD测试结果见表1[5]。
由表1可知,在镀铁层形成过程中,铁素体3个主要晶面的极密度是变化的:
低碳钢在对称交流活化后,(110)晶面的极密度最高,也即最初不对称交流起镀时,Fe2+将沿(110)晶面择优放电沉积;但是在起镀5min后,(110)的极密度下降至1.15,而(211)晶面的极密度急剧上升至1.10,这就意味着Fe2+得电子沉积将开始由沿(110)晶面向(211)晶面转化;经直流镀1h后,(211)晶面的极密度升高至1.60并超过(110)晶面的极密度,也即Fe2+得电子放电沉积的择优取向更明显。
以上规律与镀铁层的金相照片的结果相一致。
图3(a)(b)是在基体表面上形成的起镀镀层和过渡镀层的透射电镜(TEM)照片。
该组照片有2个特征:
①图3(a)基体与起镀层在结合部位看不见交界,说明了在呈微融活化状态的界面起镀时的互融特征;②图3(b)是起镀完成后的过渡镀铁层由细小的等轴晶到柱状成长。
图4是在45钢基体表面镀铁层的扫描电镜(SEM)二次电子像,它充分反映了镀铁层主要是沿一定晶向的柱状晶特征。
2.3 镀铁层的晶粒度和物相
由X射线衍射学的基础知识可知,当晶粒(或亚晶粒)细化到0.1μm或更小时,由于每个晶粒中产生X射线衍射的晶面数目减少而使衍射线条显著宽化与漫散,因此可根据衍射线条的真实宽化程度来测定细晶粒的大小。
P.Scher-rer公式反映了衍射线的半高宽与晶粒尺寸的关系:
β=kλ/Dcosθ
(2)
式中,β是衍射线的半高宽(弧度);k为常数,通常k=1;λ为射线波长;D为晶面法线方向的尺寸;θ为衍射角2θ的一半。
图5示出了纯镀铁层的X射线衍射曲线。
它的测试条件是CoKα特征射线。
由图5可知,镀铁层α-Fe的(110)晶面衍射峰明显宽化(2θ=52.267°),测得该衍射峰的半高宽为0.71°,即0.0124弧度,则由式
(2)计算可得镀铁层的晶粒直径为16.1nm。
根据作者提供的镀铁层样品,1980年经鞍钢钢研所测定,晶粒直径为45.7nm;1987年大连海运学院金属材料工艺研究所测定的晶粒直径为32.9nm。
因此可以认为,无刻蚀镀铁层属纳米晶。
多年来的研究积累了一些镀铁层TEM分析时得到的微区电子衍射花样照片,如图6所示。
它们是研究镀铁层物相的依据。
图6(a)显示了镀铁层呈非晶态,说明镀铁层中的某些微区是非晶态,但该衍射花样出现的几率较少,经常出现的衍射花样是图6(b)和6(d)。
图6(b)是晶体的衍射花样,经指数化后可确认是α-Fe(体心立方晶格),见图6(c)。
图6(d)衍射花样是典型的多晶体衍射环,经指数标定:
离衍射中心最近的第1环是α-Fe的(110)晶面的衍射环,第2、3环分别为α-Fe的(200)和(211)晶面的衍射环。
图6(b)和6(d)都显示镀铁层的物相是具有体心立方晶格的α-Fe。
综合无刻蚀镀铁层形成过程中相关问题的研究资料可以认为:
无刻蚀镀铁技术中的关键是零件表面经过对称交流活化使待镀表面处于微融活化态,有利于不对称交流起镀时镀铁液中的Fe2+在零件表面获得电子而还原沉积,而且是沿着被活化的基体晶面择优沉积,沉积形成的镀铁层可能呈微区非晶体,也可能(且是大都)是体心立方晶格的α-Fe晶体,随着镀铁层的增厚,镀铁层先是纳米等轴晶,后是纳米柱状晶。
无刻蚀镀铁层的这种沉积机制直接影响镀层的特殊性能。
3 无刻蚀镀铁层的性能特点
3.1 镀铁层的结合强度
应用改进后的奥拉[3-4](Ollard)试验法测定镀铁层与基体的结合强度,经测定,纯铁镀铁层的结合强度为356.0~398.0MPa;含Ni、Co合金镀铁层的结合强度为435.0~490.0MPa。
3.2 镀铁层的残余应力
镀铁层的残余应力是指镀铁工艺完成和清理后,在镀铁层、起镀层及局部基体系统中存在并自身保持着平衡的应力,也称为内应力。
应用X射线衍射仪可以测定镀铁层系统的内应力[6],其测定结果如图7所示。
由图7可知,在镀铁层系统(含镀铁层、起镀层和基体表层)中都存在呈拉应力的残余内应力,但各个部位的拉应力大小不均匀。
其中,原基体表层的拉应力较大(约100MPa左右),存在范围为160μm;起镀层的拉应力最小(约30MPa),存在范围为基体表面以上65μm内;镀铁层80μm范围内的拉应力居中,约45MPa。
形成上述内应力分布的主要原因是镀铁层、起镀层、基体三者的成分、组织不相同所致。
在相同的镀铁工艺环境中,由于各种原因在镀铁层系统中产生的应力应该相同,但由于成分、组织不同而在相同应力场中的行为不同而达到了上述的最终平衡状态。
基体是45钢,组织为铁素体+珠光体,起镀层是纯铁,组织为铁素体单相,镀铁层也是纯铁,组织为铁素体单相,三者比较,起镀层的塑性最好,其次是镀铁层,最后是基体,而屈服强度相反;在相同的应力作用下,起镀层变形最大,其次是镀铁层,最后是基体;因此,通过应变来松弛应力的效果以起镀层最好,其次是镀铁层和基体,直到最终平衡时即为上述规律。
镀铁层系统呈现拉应力的内应力存在,将会产生较高密度的位错以使镀铁层硬度增高,从而提高了镀铁层的实用力学性能。
3.3 镀铁层的硬度分布
应用显微硬度计沿镀铁层横截面测定硬度,载荷为100g,保持时间为15s,结果见图8。
图8反映了无刻蚀镀铁层的硬度很高(580~630HV0.1),并且在镀铁层系统中呈梯度分布。
在镀铁层系统中,以镀铁层硬度较均匀且最高,在起镀层中存在硬度陡降过渡(约0.15~0.10mm)直至基体硬度。
硬度过渡梯度的存在既保证了镀铁层与基体的结合,又保证了镀铁层系统的安全服役。
镀铁层的高硬度与它的细晶粒强化、位错强化等密切相关,并为镀铁层抗磨料磨损性能的提高创造了条件。
3.4 镀铁试样的旋转弯曲疲劳性能
按GB/T 4337-84标准,设计并加工了3组各15根Φ=9.48±0.01mm标准试样。
第1组是45钢调质试样,称“基材”;第2组为45钢调质+镀铁基合金镀层,直径方向厚度为0.20mm;第3组是45钢调质喷丸处理后再镀铁基合金镀层,直径方向厚度为0.20mm。
试验机为PQI-6型弯曲疲劳试验机,转速为5000r/min,弯矩精度≤1%,试样试验时的径向跳动量≤3mm。
试验目的是测定各组试样的疲劳极限和S-N曲线。
3.4.1 疲劳极限
采用“升降法”[4]确定疲劳试验中的应力水平,测得了3组试验的试验值见图9。
图中,在某应力时的循环周次达到107者即判为“通过”,若循环周次在未达107次时就断裂,则判为“失效”。
由图9并按GB/T 4337-84的方法计算得到3组试样的疲劳极限如表2所示。
由表2可知,在45钢调质处理试样的基础上,表面镀铁基合金镀层并不降低试样的疲劳强度,且略有增高,在45钢调质后喷丸处理,再镀铁基合金镀层时,使体系疲劳极限有很大的提高,比不喷丸的提高了17%,比45钢调质时提高了17.4%。
3.4.2 S-N曲线
测定S-N曲线时,将应力水平定为4级,用升降法测得的疲劳极限作为S-N曲线的低应力水平点,另外3级较高应力水平下的试验,则用成组试验法,根据数据的分散度,每一组定为3根试样。
以应力幅为纵坐标,以对数疲劳寿命(循环次数)为横坐标,将试验数据一一输入计算机,经程序处理得3条曲线,如图10所示。
图10清楚地说明了以下规律:
45钢调质件经镀铁基合金后的旋转弯曲疲劳性能(包括σ-1和S-N关系)比原件略高;45钢调质后喷丸再镀铁基合金则显著地提高了原件的旋转弯曲疲劳性能。
这些特点都说明,无刻蚀镀铁基合金技术特别适用于传递扭矩轴类零件的表面成形再制造。
4 结 论
(1)对称交流活化使待镀件表面形成“微融活化态”界面,是实现无刻蚀镀铁层与基体金属以金属键形式融合为一体的基础;是保证镀铁再制造机械零件装机使用安全可靠的关键。
(2)不对称交流起镀时,微融活化态表面前镀液中的Fe2+在界面获得电子而沿(110)晶面择优放电沉积以形成纳米等轴晶的α-Fe镀层,随后Fe2+因铁素体(211)晶面极密度的提高而转向沿(211)晶面放电沉积,并由纳米等轴转而形成纳米柱状晶,最终形成具有结合强度高、超精细、硬度高、耐疲劳性和耐磨性好的镀铁层,使再制造零部件达到或超过新品标准。
(3)微型电子计算机全自动镀铁电源,实现了无刻蚀镀铁全过程的自动化控制,避免了人为的操作误差,为镀铁生产提供了稳定可靠的电能转为化学能的动力源。