整车常规质量检验标准.docx
《整车常规质量检验标准.docx》由会员分享,可在线阅读,更多相关《整车常规质量检验标准.docx(145页珍藏版)》请在冰豆网上搜索。
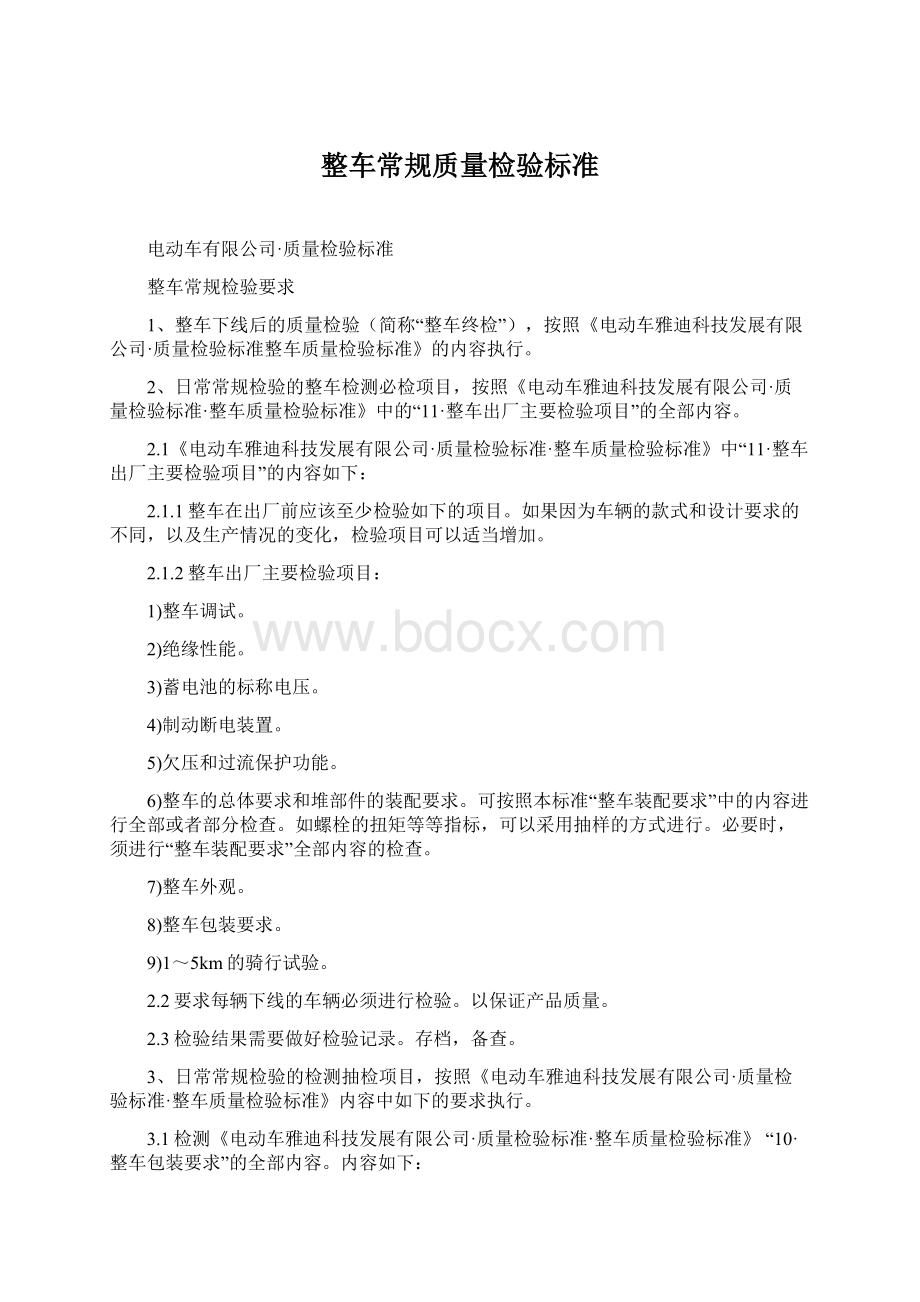
整车常规质量检验标准
电动车有限公司·质量检验标准
整车常规检验要求
1、整车下线后的质量检验(简称“整车终检”),按照《电动车雅迪科技发展有限公司·质量检验标准整车质量检验标准》的内容执行。
2、日常常规检验的整车检测必检项目,按照《电动车雅迪科技发展有限公司·质量检验标准·整车质量检验标准》中的“11·整车出厂主要检验项目”的全部内容。
2.1《电动车雅迪科技发展有限公司·质量检验标准·整车质量检验标准》中“11·整车出厂主要检验项目”的内容如下:
2.1.1整车在出厂前应该至少检验如下的项目。
如果因为车辆的款式和设计要求的不同,以及生产情况的变化,检验项目可以适当增加。
2.1.2整车出厂主要检验项目:
1)整车调试。
2)绝缘性能。
3)蓄电池的标称电压。
4)制动断电装置。
5)欠压和过流保护功能。
6)整车的总体要求和堆部件的装配要求。
可按照本标准“整车装配要求”中的内容进行全部或者部分检查。
如螺栓的扭矩等等指标,可以采用抽样的方式进行。
必要时,须进行“整车装配要求”全部内容的检查。
7)整车外观。
8)整车包装要求。
9)1~5km的骑行试验。
2.2要求每辆下线的车辆必须进行检验。
以保证产品质量。
2.3检验结果需要做好检验记录。
存档,备查。
3、日常常规检验的检测抽检项目,按照《电动车雅迪科技发展有限公司·质量检验标准·整车质量检验标准》内容中如下的要求执行。
3.1检测《电动车雅迪科技发展有限公司·质量检验标准·整车质量检验标准》“10·整车包装要求”的全部内容。
内容如下:
3.1.1整车包装要求“
3.1.2包装应该在检验完全合格后进行。
3.1.3整车在包装时应该继续进行整车外观的检查。
重点检验塑料件的色差。
发现问题及时放置于指定位置,并且上报。
3.1.4包装的操作过程中,必须保证车辆的外观清洁。
如果发现油污和污渍,须立即擦拭。
3.1.5包装箱的内容:
3.1.5.1检验合格的电动车产品一辆。
3.1.5.2电动车产品附件。
其内容根据需要放置。
附件一般装入电动车的后尾中。
附件在一般情况下的装入内容:
1)雨披1件。
2)倒车镜1套(2只)。
3)充电器1只。
4)雅迪车牌1只。
5)气门嘴1只。
6)说明书1本。
7)合格证一张。
8)脚蹬1套(2只)。
(视车型款式的不同,必要时可以卸下放入后尾箱)。
9)曲柄1套(2只)。
(视车型款式的不同,必要时可以卸下放入后尾箱)。
3.1.6说明书使用自封塑料袋。
塑料内同时装有保险丝管1只;扎带4~6根。
3.1.7后尾箱装入零部件后,应该使用废纸填满,以防止运输中碰撞。
3.2检测《电动车雅迪科技发展有限公司·质量检验标准·整车质量检验标准》中的“9·说明书与合格证要求”的全部内容。
说明书与合格证要求内容如下:
3.2.1每辆电动车必须附有说明书。
3.2.2说明书中必须包括《GB17761-1999电动自行车通用技术条件》中5.6所有内容。
3.2.3合格证背面要求填写的内容:
1)车型。
2)整车编号。
3)车架号码。
4)电机号码。
5)电池号码。
6)检验员。
7)出厂日期。
8)打印的合格证编号。
3.2.4合格证填写的整车编号、车架号码、电机号码、电池号码必须和所装入的电动车的相关编号完全一致。
3.2.5合格证的内容应该打印而成。
尽量避免手写。
3.3检测《电动车雅迪科技发展有限公司·质量检验标准·整车质量检验标准》中的“7·整车外观要求”的全部内容。
整车外观要求的内容如下:
3.3.1电动车的各个外露零部件,其表面应该清洁,无污渍、锈蚀、损伤。
3.3.2商标、贴花应全面、完整、清晰。
位置正确。
3.3.3电镀外露件:
3.3.3.1电镀外露件应符合《QB/T1217-1991自行车电镀技术条件》中5.1.1镀铬一类件和镀锌一类件的规定。
3.3.3.2电镀外露件应该色泽均匀,光亮,平整。
不得存在起泡、划伤、剥离、烧黑、露黄等等电镀缺陷。
不得有毛刺、针孔、花斑、麻点等等制造缺陷。
3.3.4外露油漆件:
3.3.4.1外露油漆件应符合《GB/T1218-1991自行车油漆技术条件》中3.1.1油漆一类件的规定。
3.3.4.2外露油漆件表面应该光亮、光滑、色调一致。
不可存在流漆、起泡、漏漆、龟裂、喷涂厚薄不均、脱漆、起皱、杂质诸类喷漆缺陷。
对于需要涂敷底漆、腻子部件的油漆表面,更需要检查是否存在不均和开裂现象。
3.3.5铝合金外露件:
3.3.5.1铝合金外露件应符合《QB/T2184-1995自行车铝合金件阳极氧化技术条件》中4.1外观一类件的规定。
3.3.5.2铝合金外露件其表面应该平整、色泽一致。
不得出现凸凹、疤痕、和设计不符的明显起伏。
铸铝件不得存在缩孔、缩松、表面拉毛和其它压铸缺陷。
3.3.6塑料件和塑料外露件:
3.3.6.1塑料外露件表面应色泽均匀,无飞边、划伤、裂纹和凸凹等等外观缺陷和注塑缺陷。
3.3.6.2批量进货的塑料外露件不应出现眼睛可以观察出来的色差。
3.3.6.3塑料件应该壁厚均匀,表面平整。
配合面符合配合要求。
3.3.6.4塑料件的螺钉安装位置应该符合设计要求;螺钉安装孔的深度、直径符合紧固螺钉的长度要求和攻入要求。
3.3.6.5对于注塑件应无收缩痕迹。
3.3.6.6表面氧化或者其它表面处理的(如发黑、发兰)零部件,应该处理全面,色泽均匀,无锈斑、其它斑点和附着杂质。
3.4检测《电动车雅迪科技发展有限公司·质量检验标准·整车质量检验标准》中的“6·整车装配要求”的全部内容。
整车装配要求的内容如下:
3.4.1总体要求:
1)电动车应该安装款式和型号进行组装。
不得错装和漏装。
2)所有的零部件必须安装到位。
不得出现错位、干涉和错装现象。
3)电动车的各个紧固件应该紧固到位。
各转动件应该运转灵活,不应出现涩滞和振动现象。
4)各个对称部件应该于车架中心面左右对称,不得出现明显的倾斜、偏离现象。
5)调速装置和制动系统应该装配正确,操纵灵活。
6)电动车的固定件应该规定牢固,不应和运动件发生干涉和摩擦。
3.4.2轮辋径向、端面圆跳动量:
应该符合《GB/T3566-1993自行车·装配要求》中13.1的规定。
3.4.2.1装轮缘闸的轮辋,其径向、端面的圆跳动量不大于2mm.
3.4.2.2不装轮缘闸的轮辋,其径向、端面的圆跳动量不大于4mm.
3.4.2.3轮辋的中心面应该位于前、后轴二安装平面的正中央。
二相对偏差不大于的2mm。
3.4.3前、后轴二安装平面是指:
对于普通轴,为两轴挡的外端面。
如果有锁紧电力线的轴挡,则指两锁紧螺母的外端面。
3.4.4前、后轮辋与前叉、车架平叉、立叉两边的相对偏差:
应符合《GB/T3566-1993自行车·装配要求》中15.1规定的要求。
3.4.4.1装轮缘闸的车轮,不大于3mm。
3.4.4.2不装轮缘闸的车轮,不大于6mm。
3.4.4.3前、后轮中心面相对偏差不大于7mm.
3.4.4.4前轮的紧固力矩不小于18N·m
3.4.4.5后轮的紧固力矩不小于30N·m
3.4.4.6前、后轮的装配完毕后,应该转动灵活,并且无松动现象。
3.4.5整车零件装配要求
3.4.5.1前叉,车轮,曲柄等转动零部件应回转灵活,且无松动,不得出现回转时涩滞,松紧不一和明显地松动现象。
3.4.5.2车把立管插入前叉立管的深度应的最小插入深度标记以上;把心丝杆,把接头螺杆的紧固扭距不得小于18N·m;把横管应与前轮中心面保持垂直,不得有明显的偏斜;把套应装配到位。
3.4.5.3中轴锁母的紧固扭距不小于30N·m;右中轴碗应旋紧到底,中轴锁母旋紧后,曲柄装配后中轴应回转灵活且无松动。
3.4.5.4鞍管插入车架立管的深度应的插入深度标记位置以上;鞍座位置装正,不得有明显的偏斜;鞍座要夹紧螺栓,车架后接头螺钉的紧固扭距不小于18N·m。
3.4.5.5两曲柄的安装方向相反,呈180°。
脚蹬轴应和曲柄紧固,不得松动。
3.4.5.6链条应松紧适宜,运转灵活;链条锁紧片应装的外侧,开口侧应与链条运转方向相反;链条应定位良好,不得与链罩,护板,曲柄相摩擦。
3.4.5.7气门嘴孔应于两辐条大拦之间,装胎时气门嘴的外胎商标中央。
3.4.5.8辐条应均匀张紧,辐条螺纹头部不得突出条母外。
3.4.5.9轮胎按350千帕气压充气,内外胎不得有明显的扭曲,褶皱现象,气门嘴不得偏斜。
3.4.5.10前,后轮中心面相对偏差不大于7mm.前,后轮的紧固扭矩应不小于30N·m。
后轮应回转灵活且无松动。
3.4.5.11前闸把应安装的车把右侧,后闸把应安装的车把左侧。
闸把应损伤灵活,并能借助闸簧迅速复位。
制动时闸皮除了轮毂外不得与其它任何零部件相碰,两侧的闸皮能同时与轮毂接触,松闸后能借助弹簧力时闸皮迅速复位。
抱闸的闸皮间隙调节适宜,松闸后能迅速复位。
3.4.5.12前后泥板不得有明显的扭曲。
3.4.5.13衣架应与车轮左右对称,无明显的偏斜。
3.4.5.14双支架应与车轮左右对称,无明显的偏斜,支起成车后能使成车垂直站稳,支架应使用灵活,复位方便。
3.4.6整车性能基本要求
3.4.6.1多功能前灯性能良好,显示器能正常显示,车的技术参数,电喇叭声音响亮,悦耳,前灯亮度明亮。
3.4.6.2调速装置操作灵活,复位良好。
3.4.6.3制动性能良好,制动时应能自动断开电源。
3.4.6.4骑行试验人力,电动,电动助力性能良好。
3.5抽检率暂定为5%.采用随机抽检的方式。
3.6检验结果需要做好检验记录。
存档,备查。
4、合格品的判定:
4.1凡是不符合《电动车雅迪科技发展有限公司·质量检验标准整车质量检验标准》中“11·整车出厂主要检验项目”以及“6”“7”“9”要求的车辆,均属于不合格品。
]
4.2其它不符合《电动车雅迪科技发展有限公司·质量检验标准·整车质量检验标准》的内容,应该视检验经过进行综合判定。
4.3根据车辆不合格的位置,严重程度,可以分为废品;换件品;返修品。
4.4废品:
出现诸如车架断裂,开焊,或者其它零部件严重损坏,以致无法修复的故障。
此类故障一旦出现,必须将检验的车辆专门放置。
并且立即上报。
同时必须组织技术部门共同研究问题出现的原因。
并应通知相应的协作厂家。
4.5换件品:
属于外协塑件以及标准件等等不合格造成的不合格品。
该车虽然出现问题,但是尚能够正常使用。
但是出现的问题将影响车辆的整车质量。
而且无法修复。
这种情况,一般是的出现批量的塑件或者铁件的外观质量上。
如果出现的数量比较大,则应立即上报。
通知上级部门、技术部门和公司领导,以便进行综合判定。
并且根据判定结果,通知外协厂家。
进行相应的处理。
同时,在加强进货检验的同时,应该通知车间加强巡回检验。
4.6返修品:
属于装配不合格的产品。
经过维修或者重新装配,可以达到质量要求。
对于此类产品,应该退回车间,进行重新调试或者装配。
并且做好记录。
如果出现较大的此类故障,应该通知技术部门、上级部门和公司质量小组,以便进行装配过程和装配工艺的问题诊断。
5、发现不合格品的处理:
5.1如果的抽样检验中发现属于不合格的异常问题,则需要增加抽检率。
暂定出现异常问题的补加抽检率为继续抽检10%。
如果仍旧出现异常,则必须逐辆进行检测。
检测的内容为本标准“3”章的全部内容。
5.2所有出现的质量问题,必须记录在案。
5.3凡是出现质量不合格的情况,均应该及时做出质量问题的原因判定。
如果出现当时无法判定的问题,应该会同技术部门进行做好判定。
并且及时上报。
5.4不合格品,不得随意放置。
必须放置在指定位置。
更不得与合格产品一起放置。
6、其它项目的检测:
6.1《电动车雅迪科技发展有限公司·质量检验标准整车质量检验标准》中的与国家要求的检测项目,应该按照相关国家标准的要求到指定的检测的部门进行相关检测。
6.2《电动车雅迪科技发展有限公司·质量检验标准整车质量检验标准》中的其它诸如包装、合格证等等检测,可以随时随机进行抽样。
如果一旦发现问题,即应按照本标准“5.1”的要求,进行10%的抽样检测。
6.3车架、车架前叉组合件的振动强度试验,暂定为每三个月进行一次综合测试。
6.4道路试验暂定为每三个月至半年进行一次全面测试。
6.5其它试验暂定为每三个月至半年进行一次全面测试。
迈赫自动化管理制度
★
产品质量检验标准
MHOF.10101.02.1-2012
2012年1月1日发布2012年1月1日实施
山东迈赫自动化装备股份有限公司
第一章原材料质量检验标准……………………………………………………………………4
1.1普通碳钢板、卷………………………………………………………………………………4
1.2镀锌板、卷……………………………………………………………………………………10
1.3不锈钢板、卷…………………………………………………………………………………12
1.4钢管……………………………………………………………………………………………14
1.5实心钢…………………………………………………………………………………………14
1.6型钢……………………………………………………………………………………………14
1.7铝板……………………………………………………………………………………………15
第二章标准件检验标准…………………………………………………………………………16
2.1紧固件…………………………………………………………………………………………16
2.2销………………………………………………………………………………………………16
2.3键………………………………………………………………………………………………16
2.4螺栓、螺柱……………………………………………………………………………………16
2.5螺母……………………………………………………………………………………………16
2.6螺钉……………………………………………………………………………………………17
2.7垫圈、挡圈……………………………………………………………………………………17
2.8铆钉……………………………………………………………………………………………18
2.9其他常用件……………………………………………………………………………………18
第三章涂装设备加工制作过程检验标准………………………………………………………20
3.1下料工序………………………………………………………………………………………20
3.2冲孔工序………………………………………………………………………………………20
3.3折弯工序………………………………………………………………………………………21
3.4钣金件制作工序………………………………………………………………………………21
3.5装配焊接工序…………………………………………………………………………………21
3.6除锈底漆包装工序……………………………………………………………………………22
第四章机械化输送设备制作安装过程检验标准………………………………………………24
4.1基本要求………………………………………………………………………………………24
4.2滚床……………………………………………………………………………………………24
4.3移行滚床………………………………………………………………………………………24
4.4旋转滚床………………………………………………………………………………………24
4.5举升台…………………………………………………………………………………………24
4.6双联式输送机…………………………………………………………………………………24
4.7单链式输送机…………………………………………………………………………………25
4.8皮带积放输送机………………………………………………………………………………25
4.9提升机…………………………………………………………………………………………25
4.10划撬撬体………………………………………………………………………………………25
4.11气路单元………………………………………………………………………………………25
4.12整机要求………………………………………………………………………………………26
4.13漆及安全要求…………………………………………………………………………………26
4.14制造保证………………………………………………………………………………………26
4.15金属风管的制作质量验收标准………………………………………………………………26
第五章电控柜加工制造过程检验标准…………………………………………………………28
5.1柜体检验………………………………………………………………………………………28
5.2配电柜安装标准(固定件)…………………………………………………………………28
5.3配电柜安装标准(电盘配线)………………………………………………………………28
5.4配电柜安装标准(绝缘测试)………………………………………………………………30
5.5配电柜安装标准(上电调试)………………………………………………………………31
第六章非标设备现场安装检验标准……………………………………………………………32
6.1一般要求………………………………………………………………………………………32
6.2主体安装………………………………………………………………………………………33
6.3管道安装………………………………………………………………………………………33
6.4风机及泵的安装………………………………………………………………………………33
6.5输送设备安装…………………………………………………………………………………34
6.6悬挂输送设备安装……………………………………………………………………………34
6.7除锈、涂装及保温……………………………………………………………………………34
6.8电气控制系统…………………………………………………………………………………35
6.9喷漆室安装调试检验标准……………………………………………………………………36
6.10面漆、底漆、胶烘干、水份烘干室安装调试验收标准……………………………………37
6.11强冷室调试工艺要求及验收标准……………………………………………………………38
6.12流平、打磨、擦净室工艺要求………………………………………………………………38
第七章电气制作安装工艺要求及验收标准……………………………………………………39
7.1配电柜(盘)制作安装………………………………………………………………………39
7.2电气设备配管(槽)及管(槽)穿线工程工艺要求………………………………………40
7.3照明装置安装工艺要求………………………………………………………………………42
7.4接地、避雷装置施工工艺要求………………………………………………………………43
7.5.高温区电气设备安装工艺要求……………………………………………………………44
第一章原材料质量检验标准
序号
名称
质量规范标准
1.1
普通碳钢板、卷检验标准
1.1.1热轧单扎钢板的厚度允许偏差(A类B类C类N类)。
(参照GB/T709-2006)
1.1.2热轧钢带(包括连轧钢板)的厚度允许偏差。
(参照GB/T709-2006)
1.1.3切边热扎钢板的宽度允许偏差。
(参照GB/T709-2006)
1.1.4不切边钢带(包括连轧钢板)的宽度偏差。
(参照GB/T709-2006)
1.1.5切边钢带(包括连轧钢板)的宽度偏差。
(参照GB/T709-2006)
1.1.6纵切钢带的宽度允许偏差。
(参照GB/T709-2006)
1.1.7热轧单扎钢板的长度允许偏差。
(参照GB/T709-2006)
1.1.8热轧连轧钢板长度允许偏差。
(参照GB/T709-2006)
1.1.9不平度:
单扎、连轧钢板不平度偏差。
(参照GB/T709-2006)
不平度测量方法:
将钢板自由地放在地面上,除钢板自身重量外不施加任何压力,用1根长度1000mm或2000mm的直尺,在距离单扎钢板纵边至少25mm和距离横边至少200mm区域内的任何方向,测量钢板上表面与直尺之间的最大距离。
如图1:
不平度测量方法如图2:
1.1.10板材表面平整、厚度均匀,无明显的凹凸及压伤现象,不得有砂眼、结痕及刺边和锈蚀。
彩色钢板无明显的划痕、脱色、擦皮。
同一规格、同一批进货色彩必须一致光亮。
锈蚀标准见下表:
锈蚀等级
内容
考核
A级
钢材表面完全覆盖粘附的氧化皮,几乎无铁锈
良好
B级
钢材表面已经开始锈蚀,氧化皮开始呈片状脱落
合格
C级
钢材表面上的氧化皮已锈蚀,或可刮除,但裸眼可看到轻微锈点
每件考核50元,超过总数20%退货处理
D级
钢材表面的氧化皮已锈蚀剥落,裸眼可看到大量锈点
每件考核100元,超过总数20%退货处理
1.1.11切斜:
钢板的切斜不大于实际宽度的1%,测量方法如下图:
1.1.12镰刀弯:
钢板或钢带的凹形侧边与连接测量部分两端点直线之间的最大距离。
单扎钢板的镰刀弯不大于实际长度的0.2%,如下表:
镰刀弯测量方法如下图:
1.1.13冷轧钢板和钢带的尺寸、外形、重量及允许偏差参照GB/T708-2006.
1.2
镀锌板、卷检验标准
1.2.1钢板及钢带的镀层表面结构符合下表:
镀层种类
镀层表面结构
代号
特征
Z
普通锌花
N
镀层在自然条件下得到肉眼可见的锌花结构
ZF
小锌花
M
通过特殊控制方法得到的肉眼可见的细小锌花结构
无锌花
F
通过特殊控制方法得到的肉眼不可见的细小锌花结构
普通锌花
R
通过对纯锌镀层的热处理后获得的镀层表面结构,该表面结构通常为灰色无光
1.2.2彩色涂层钢板及钢带参照《宝钢彩色涂层钢板及钢带标准》(Q/BQB440-2003)彩色涂层钢板。
定义:
是指彩涂基板经过表面预处理后,以连续辊涂的方式在钢板表面涂敷一层或二层有机涂料,然后进行烘烤固化而成的产品。
1.2.3镀锌板公称厚度偏差如下表:
(参照GB/T2518-1998)
序号
薄板板宽≥1000
序号
薄板板宽1500—1800
1
0.8
±0.10
11
5
±0.3
2
0.9
±0.12
12
6-7
+0.7
―06
3
1
±0.13
13
8-10
﹢0.6
―0.8
4
1.2
±0.14
14
11-25
﹢0.6
―0.8
5
1.5
±0.16
15
26--30
﹢0.6
―0.9
6
2
±0.18
16
32—34
﹢0.6
―1.0
7
2.2
±0.19
17
36--40
﹢0.9
―1.1
8
2.5
±0.2
9
2.8—3.0
±0.22
10
3.8—4.0
±0.3