旋转机械的振动论文.docx
《旋转机械的振动论文.docx》由会员分享,可在线阅读,更多相关《旋转机械的振动论文.docx(12页珍藏版)》请在冰豆网上搜索。
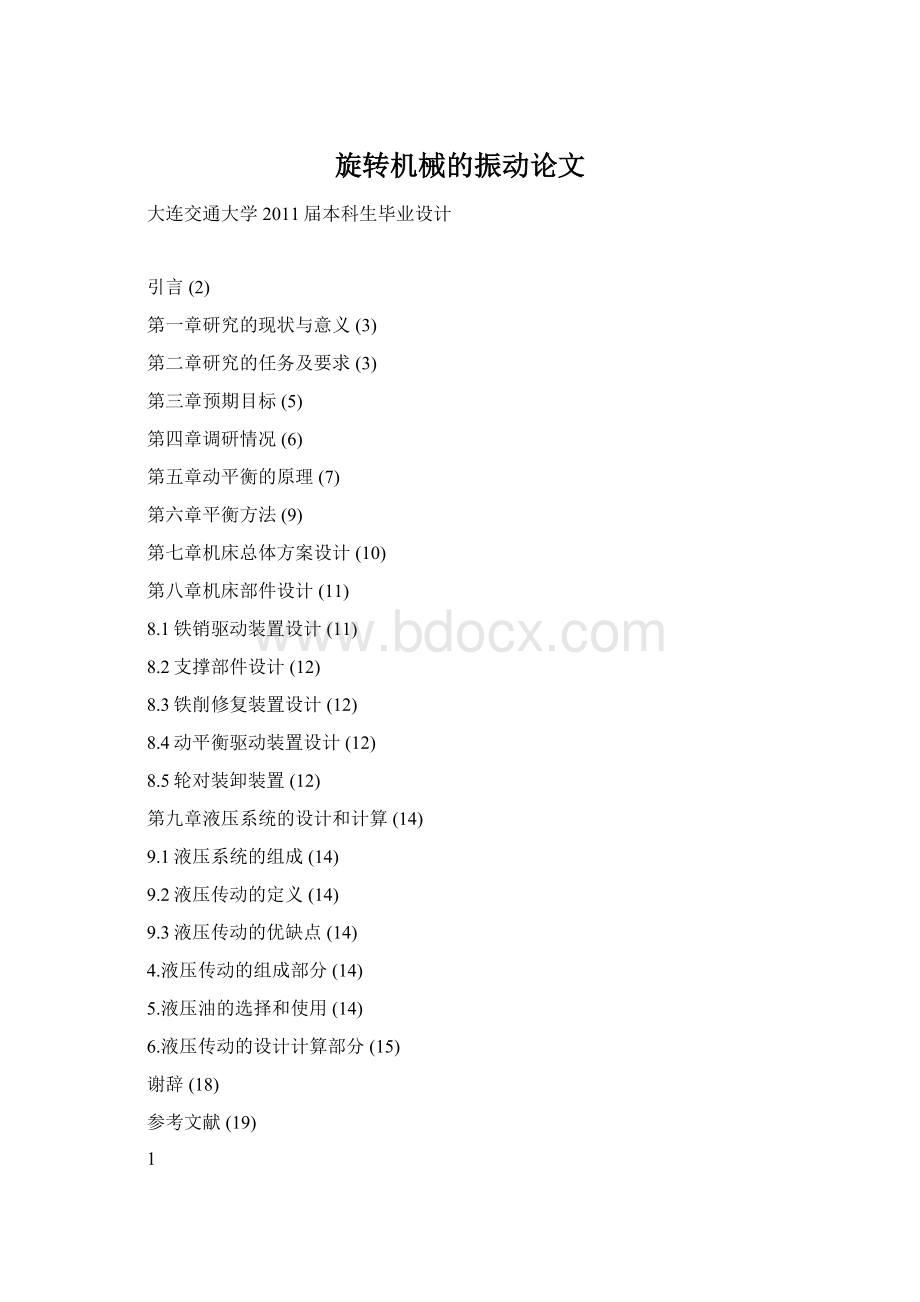
旋转机械的振动论文
大连交通大学2011届本科生毕业设计
引言
(2)
第一章研究的现状与意义(3)
第二章研究的任务及要求(3)
第三章预期目标(5)
第四章调研情况(6)
第五章动平衡的原理(7)
第六章平衡方法(9)
第七章机床总体方案设计(10)
第八章机床部件设计(11)
8.1铁销驱动装置设计(11)
8.2支撑部件设计(12)
8.3铁削修复装置设计(12)
8.4动平衡驱动装置设计(12)
8.5轮对装卸装置(12)
第九章液压系统的设计和计算(14)
9.1液压系统的组成(14)
9.2液压传动的定义(14)
9.3液压传动的优缺点(14)
4.液压传动的组成部分(14)
5.液压油的选择和使用(14)
6.液压传动的设计计算部分(15)
谢辞(18)
参考文献(19)
1
引言
在当今,旋转机械的振动问题有很大一部分是由于转子不平衡引起的,因此,可以以为转子不平衡是引起旋转机械振动的重要原因之一,对于线性系统来说,不平衡引起的振动,其频率等于转子的旋转频率,而当转子有非线性特征时,失衡将引起转子旋转频率为基频,以及带有一系列高阶谐波成为的振动为了消除或减轻由于失衡引起的振动,就必须对转子进行动平衡。
对于实际转子来说,其不平衡质量沿转子轴向和径向的分布是任意的随机的,因此在实际的动平衡中不可能确定不平衡量的具体分布,然后在每一个平面进行平衡,采用的一般方法只能是人为地在转子某个部位加上或者减去一些质量,这些质量成为校正质量,而所谓的动平衡过程就是在平衡面上找出增加或者去校正质量的大小和方位,然后在那个方位加上或者减去矫正质量,从而使校正质量所激发的振动与原始不平衡产生的振动相互抵消,最终达到平衡转子,减小振动的目的。
第一章研究的现状与意义
无论是在客车还是火车上,轮对都是一个非常重要的部分,在轮对的制造以及装配返修中对轮对进行动平衡测试以及根据测试的结果修正轮对使之达到动平衡,因为对于回转机械,在运转过程中如果转子不平衡,将会引起机械的振动,而所谓的转子不平衡是指由于转子的质量分布不均匀而产生的离心惯性力系的不平衡,而这种不平衡的惯性力系,将对支撑和基座产生附加动压力,这使转子产生弯曲变形,附加动压力将会降低轴承的寿命,而明显的弯曲变形将会对转子的结构强度和工作性能产生不好的影响,此外,振动通过支撑传给基座,从而引起震动,振动引起噪声,使工作环境恶化,所以对于大型回转机械,转子的动平衡是保证机械正常运转的重要措施。
目前在国内所采用的动平衡方法普遍存在着检测修复效率低,精度低,劳动强度大,自动化程度低等缺点,针对以上几点铁路部门研制开发了几种新型动平衡机床,一台现代的动平衡机床一般由支撑系统,驱动系统,结算及标定电路,以及幅值相位指示系统组成,而研发和研究制造的这几种动平衡机床的使用效果不是很好,主要是检测装置对检测结果的干扰没有彻底解决,质量很难保证,特别是在需要二次装夹的对中不是很好,在修复时效率也没有大幅度提高,这些都是迫切需要研究开发,设计一种新型的轮对动平衡机床,他需要抗干扰能力强,而且效率高,集中实现高效高质量的计算机控制检测和计算机数控修复切削,以适应铁路现代化和全面提速的要求,对车辆的安全运行,提高劳动生产率和经济效益具有十分重要的意义。
第二章研究的任务及要求
1.实习,调研,阅读有关参考资料,包括外文资料选修相关课程。
2.机床总体方案拟定,包括监测方案,修复切削方案,传动和结构方案。
3.机床部件设计。
4.动力学模型建立和计算,必要的动力学实验,检测试验。
5.检测装置设计。
6.液压系统设计。
7.完成毕业论文以及设计计算说明书。
第三章预期目标
1.轮对组装后需进行动平衡试验,允许不平衡值为0.735N.M,采用去重法对其进行修正。
2.对于一台动平衡机床,它由驱动系统,支撑系统,结算和标定电路和相位系统组成
(1)驱动系统是带动转子以它选定的速度转动,驱动方式有方向节驱动,围带驱动,摩擦轮驱动,气驱动,磁驱动等多种方式
(2)支撑系统是用来支撑转子并在转子不平衡离心力作用下产生振动,并把振动经特定的传感器转换成电讯号传给结算电路
(3)解算和标定电路是将传感器传送来的电讯号加以分析和变换,针对具体转子以及所选平面位置,分立左右两个较正面的相互影响确定指示系统的灵敏度
(4)幅值和相位指示系统,根据解算的结果指示出校正值的大小和方位
3.所研制开发的动平衡机床要能够达到抗干扰能力强切削效率高的要求,对铁路车辆的安全提供有力的支撑。
第四章调研情况
轮对检修
1.退卸内圈,防尘挡圈。
2.外观检查。
3.煮洗,防锈。
4.确定修成检查。
5.车轴磁粉探伤。
6.车轴超声波探伤。
7.踏面旋修。
8.检查测量,选修后踏面与轮缘粗糙度Ra应不大于25um轮缘厚度为2
1
32+-,同一车轮踏面与轴劲面距离在同一直线上测量的两点,相差不大于0.6mm,同一车轮直径差,不大于0.5mm,同一轮对相对车轮直径差不大于1mm。
9.动平衡检测,允许平衡值为0.735N.m,采用去重法对不平衡进行校正10.涂油了解现有动平衡机床的优缺点,包括支撑定义装置,检测装置,切削装置和切削装置等。
第五章动平衡的原理
1.它的测量系统可根据传感器发出的信号判断出转子不平衡量IIMV和
MV∏∏以及它们的相位
2.1.2为拾振器,它采集左右两个支撑的振动信号,此信号加到解算电路上去,解算电路的作用是使来自拾振器1的信号仅仅反应在平衡面I上的不平衡量大小,使来自拾振器2的信号仅仅反应平衡面2上的不平衡量大小。
经过选频放大器4将工作信号放大,最后由经过事先标定的表头与直接读上平衡面上的不平衡量大小,经过选频放大后的信号的频率与转子的转速相同,其相位与不平衡量的位置存在一个相位差,将放大后的信号再经过整形放大器6变成脉冲信号,送到鉴相器7的一端,鉴相器的另一端是是基准信号,他来自光甩头8和整形放大器9,基准信号的频率也与转子的转速相同,其相位与转子的黑白标记相对应,相位差表10的读数指示的是鉴相器两端信号的相位差,因此,以转子上事先做好的黑白标记为基准,根据相位差的读数即可定出不平衡量的位置。
3.在测得了两个平衡面上的不平衡量的大小和相位后,可以减去两个校正量
'
1v'
2v,使'
'
IIIVmrVmr∏∏∏==。
他们与不平衡量之间的相位相同,边测量边校正,
选择平衡面的位置,根据转子的实际结构在设计时就要考虑好,一般选择尽量靠近支撑,这样平衡的效果最好。
对于刚性转子,不平衡力引起的转子绕曲可以忽略,因此我们可以用刚性理学的办法来处理动平衡问题。
对于一个长为L的钻子可以认为是由于无穷多个薄盘组合而或其中任何一个薄盘之如有偏心,Li将产生离心惯性力,根据静力学原理,总可以被等效地分解到左右两个平面A和B上去,通常情况下,都将A,B两个平面选为转子的两个断面,其质量分别为Fcia,Fcib且
Fcia=fal(l-li)/LFcib=fail/L
转子上任何一个具有偏心的薄盘所产生的离心惯性力,均可按这种方法分解到A,B两个平面上,然后若将A,B两平面上各薄盘的分量按照矢量求和,即可得到A,B两平面上的合力Fca和Fcb,这时只要分别在A,B两平面上加上与Fca和Fcb方向相反,大小相等的平衡力,即可使转自达到平衡,其具体做法是,在平面A上Fca的反方向上,距轴心Ra处,加上校正质量Ma,使caAAFwrm=2这样Ma的离心力就与Fca相平衡,同理,在平面B上Fcb的反方向距轴心Vb处加上质量Mb则可平衡掉Fcb。
从原理上看,任一不平衡的刚性转子均可采用在两个校正面上加减校正质量
的方法来使整个转自达到平衡,此处,由于刚性转子本身玩去变形很小,转子的不平衡分布不会因为转速的变换而改变,因此,当刚性转子在某一转速下平衡好之后,则无论在其他什么转速下,要保证转子仍然是刚性的条件,那么转子的平衡也将仍然得到保持。
第六章平衡方法
放行转子的动平衡方法常有平衡机法和现场平衡法两种,他们各有优缺点,平衡机法大概如下
平衡机法德优点是,可以高效精密地进行转自平衡吗,且适用于不平衡较大的转子,以及那些不能在运行转速下进行平衡不能在现场进行无损检测,以及在大修中由于其他原因已经吊出机器的转子。
动平衡机的基本构成如上图所示
1.底座,主要用于安置驱动和支撑系统以及仪表等
2.驱动系统,主要功能是按规定转速驱动转子转动常用驱动方式包括万向节驱动,围带驱动,摩擦轮驱动,气驱动和磁驱动等
3.支撑系统,其功能是支撑轮子并在其不平衡力的激励下做恒定的受迫振动
4.传感器,主要作用是将支撑系统的振动信号,转换为电信号输出,以便进行平衡计算,通常采用速度传感器,电容传感器等
5.测试系统,收集传感器传来的振动信号,并进行处理和分析,然后通过相位,幅值,转速等仪表,指示出在平衡转速下,各校正质量的大小和方位,动平衡机按支撑形式的不同可分为软支撑和硬支撑两种类型,在软支撑动平衡机中每一支撑是一个在水平方向可以自由摆动的摆架,这种支撑在轴向以及垂直方向均有极大的刚度,但水平刚度却很小,其振动固有频率远远低于平衡转速,因此摆架的最大振幅间的相位约为180°,于是根据传感器输出地信号,便可确定不平衡量的大小和方位。
硬支撑动平衡机是近十年发展起来的新行动平衡机,这种支撑的刚度很大,其振动固有频率远远高于平衡转速,因此,其支撑的振幅直接与不平衡离心力成正比,其相位基本一致,于是根据传感器的输出,同样可以确定不平衡量的大小以及方位。
软支撑动平衡机的支撑示意图,应支撑动平衡机的支撑示意图
软支撑动平衡机的优点是:
平衡精度较高,适用于微型以及精密转子,缺点是:
转子在摆架上振幅较大,与转子的实际工作条件差别较大,分析电路需要按测量调整,操作比较复杂。
硬支撑动平衡机的主要优点是:
适应性强,比较符合机器的实际工作条件,起动,停车时间较短,效率高,机械结构支撑坚固,适合于生产车间等一般环境条件,缺点是:
灵敏度相对度较差,进一步提高精度目前有困难。
本设计采用的应支撑动平衡机
第七章机床总体方案设计
本设计利用轮对在转动时的不平衡会引起机床支架的周期性受迫振动,采用检测装置(速度拾振器)采取出来并转换为电信号,并利用解算装置计算出不平衡的幅值和相位
在检测不平衡之前先用动平衡驱动装置(靠背轴)带动轮对转动,当达到一定转速时靠背轮脱离平稳的检测。
当检测出不平衡的幅值和相位后,利用其计算出切削位置及切削量,采用去重法(切重法)对不平衡量进行修复切削使其不平衡量达到小于0.735n.m的要求。
为了提高机床的工作效率,本设计采用了两套相同的切削装置分别对轮对进行切削,节省了切削头施转等工序。
主轴采用蜗轮蜗杆传动结构紧凑简单,主轴箱占有空间小,主轴前端采用三爪液压卡盘且定心效果好,油缸位于主轴后端,主轴箱外侧,随主轴转动,用一杆与液压卡盘相联系,控制卡盘的夹紧或者松开。
第八章机床部件设计
8.1铁销驱动装置设计
1).为提高装夹的精度选用三爪自定心液压卡盘(为了防止划伤轮对轴采用软卡爪),由于装夹位置软对轴端的直径为130mm,所以,选用规格D=400的K51系列锲式动力卡盘,把液压缸设计在主轴后端通过一根比的连杆与动力卡盘连接油缸,选用TP24160高速回转油缸,因为该产品系高速不通孔回转油缸,内部有保压安全措施,可防止因液压系统故障等原因引起油缸输出推拉力的急速下降,可以包加工安全,是数控机床理想的动力源,它的油缸最大使用压力为3.5MPa输出最大推拉力为f600doN,油塞最大行程为35mm,油缸极限转速为500r/min。
主轴旋动采用蜗杆涡轮传动蜗杆转动是用来传递空间垂直交错两轴间运动和动力的传动机构,它具有如下特点:
结构紧凑,传动比大,动力传动一般为8~80,只传递运动由可达1000,传动平衡无噪音,蜗杆传动与螺旋传动一样,在齿合面的相对滑动速度较大,摩擦和磨损严重,传动效率低,一般为0.7~0.8,蜗杆传动可以自锁的,此时传动效率低于0.5,应用广泛,从结构紧凑简单考虑,故选用蜗杆传动。
主要参数和几何尺寸计算
选择标准模数m=8mm,d1=140mm,蜗杆的直径系数q=
d/m=140/8=17.5。
..
1
蜗杆头数
z,蜗杆头数1z可根据传动比和传动效率要求来选择,蜗杆头数小,
1
传动比大,但效率较低,如要求提高效率,则应增加蜗杆头数,但蜗杆头数越多加工越困难,所以蜗杆头数取
z=1~6,考虑两方面的因素,这里选取1z=4。
1
涡轮齿
z为了避免切削蜗轮齿数时产生根切与单头蜗杆搅合的蜗轮齿数应
2
大于17~18,与双头蜗杆搅合的蜗轮,齿数
z应大于27,对于动力传递,2z一
2
般不大于80,这里选取
z=28。
2
蜗杆传动时的传动比
蜗杆传动的通常以蜗杆为主动件,蜗杆与蜗轮之间的传动比
i=2z/1z=28/4=7。
12
蜗杆传动的中心距
a=0.5/(
d+2d)=m/2(17.5+28)=182mm
1
蜗杆驱动:
选用B下系列磁阻式步进电动机型号150B下003
主要性能数据是:
最大静距15.68m/(N.m)外形尺寸150*n8.
8.2支撑部件设计
在调研过程中所见的动平衡机床采用的是顶尖表面上这种方式对中性好,精度高,而实际上,由于制造安装中的误差,两侧同轴度误差较大,而对检测的结果有很大的影响,造成结果失真,所以在这里我们对轮对两侧分别用两对轴承支撑,这样可降低由于设备本身原因对检测结果的影响,提高检测精度,从而使为后来的切削修复过程提供一个好的基础。
检测动平衡用的拾振器安装在支架上靠近轮对支撑的地方,这样动平衡检测的效果最好。
8.3铁削修复装置设计
为了提高铁削修复过程的效率,这里采用双边切削工作方式,它们独立工作,互不干扰,但从其形式结构上来说是一致的。
采用TX20A型铁削头(配置TX20-F41齿轮传动装置,十字滑台),纵向液压传动,横向丝杠传动。
8.4动平衡驱动装置设计
在检测动平衡时,要使轮对自由转动,这里我们选用背靠轮
工作时,电机通过一个带传动把动力传给背靠轮,有摩擦力带动轮对传动,当达到转速平稳时,背靠轮脱离,检测装置开始工作。
背靠轮的背靠或者脱离是通过液压缸来完成的,液压缸与支架相连,为了使液压缸适应工作时可有一定角度的摆动,液压缸选用ZG1系列单作用柱塞式液压油缸型号ZG1-E40X800.
8.5轮对装卸装置
为了方便地将轮对装夹到机床上,在机床前安装了两条导轨,接到外面的铁轨上,使轮对可以直接从外面一直水平移到机床上,当轮对移动到正确的位置后安装在导轨下方向液压缸驱动使导轨下移使轮对两轴头,安放在两轴承之间,使其径向位置得到固定。
轮对径向位置确定之后,在支架上的小液压缸,动作使其前部伸出,它的前部带有一滚动轴承其外圆顶到轮对轴肩凸台上,使轴对的轴向未知得以固定。
当轮对的径向和轴向位置都得到固定之后,支架上部的油缸开始动作,使其下部下移,达到夹紧轮对的目的,该装置有两个导向套筒以保证其位置,另外还有其下部也有两滚动轴承,四个滚动轴承使其径向位置牢牢固定,另外该部有一
燕尾槽有一些间隙,使其可以达到自动定心的目的。
此外为了方便安装,应使主轴箱可以自由的前后移动。
在上面安装了液压滑台,在油缸的驱动下,使主轴箱实现前后移动,使其前部液压卡盘达到或者脱离夹紧位置。
第九章液压系统的设计和计算
9.1液压系统的组成
包括液压站,油缸等
9.2液压传动的定义
液压装置中的油泵将电动机或者其他发动机的机械能转变成流体能量(主要是压力能)由于工作油的流体能量具有压力,流量,方向三个基本参数,这些参数可用控制阀按所定的目的进行调整,之后再借助适当的执行机构(油缸或油马达)重新变成直线运动或回转运动的机械能,这种动力变换和传递的过程主要是以液压油作为传递介质,故称液压传动。
9.3液压传动的优缺点
优点:
①易于在很大范围内实现无极调速。
②易于实现过载保护。
③在同等体积下液压装置能比电气装置产生更多的动力。
④液压系统易于自动化,这是因为它对液体压力流量或者流动方向易于进行调节或者控制的缘故等等。
缺点:
①难于避免的漏油。
②由于油的粘度随温度而变化,造成工作机构运动的不稳定,故难以实现定比传动。
4.液压传动的组成部分
1)能源装置—液压泵。
2)执行装置—液压缸。
3)控制执行装置—各种控制阀。
4)辅助装置—油箱,滤油器,油管等。
根据液压传动的原理,我们应根据自己设计的要求和所能达到的效果,应对液压系统的一些设备作一些要求,如油液油温的确定。
5.液压油的选择和使用
(一)液压油的选择
目前我国在液压系统中仍大量采用机械油和汽轮机油,正确合理地选择液压油,对液压系统适应各种环境的能力,延长系统和元件的寿命,提高系统工作的可靠性都有重要作用。
在众多的考虑因素中,最重要的因素是液压油的粘度,粘度太大,液流的压力损失和发热大,使系统效率下降,粘度太小,泄露增大也影响系统效率,因此我们选择使系统能正常高效可靠工作的油液粘度。
(二)液压油的使用
使用时应注意以下几点
(1)应使液压油液长期处于低于它开始氧化的温度下工作。
(2)在储存搬运以及加注过程中应防止被污染。
(3)对油液定期抽样检验并建立定期换油制度。
6.液压传动的设计计算部分
根据设计可知,其有八组液压缸,分别为
(1)轨道升降液压缸
(2)支架升降液压缸
(3)轴向限位液压缸
(4)驱动靠背轮运动的液压缸
(5)驱动左滑台带动主轴箱进退的液压缸。
(6)控制液压夹具的TP24160高速回转油缸
(7)驱动后面左液压滑台动作的液压缸、
(8)驱动左右液压滑台动作的液压缸
控制轨道升降的液压缸共有两个,他们共同支撑起轨道以及其上面的轮对的重量,轮对重量约为69kg,轨道长约一米,共51.514×2≈103kg,共计1472kg,每个液压缸受力约为736kg。
控制支架升降的液压缸受到支架以及靠背轮对的压力
其余液压缸均为夹紧油缸。
6.1根据液压设计手册查表,选取油缸,内径d=65mm,外径D=120mm,活塞杆
d=35mm。
1
再根据组合机床液压设计手册公式:
油缸的驱动压力
P=2P*2F/1F+1D/1F+G/1F
1
P油缸后腔的压力
2
F油缸前腔的压力
1
2F油缸后腔面积
1D
油缸阻力和管路损失,可取1D/1F=4-5公斤/2cm
G支撑部位重量计算得
1P≈12
公斤/厘米
油缸速度选定V向前=10Q/F(m/min)取向前速度为2m/min
2m/min=10Q/(π/4*6)推得Q=6.62/minL
由于两由腔同时进油,则总的流量Q总=2×6.6L/min=13.2L/min以上是支撑轨液压缸
下面计算驱动铁削头纵向进给液压缸铁削头切削力N=5×50.130.880.7510zDtsBZN已知B=10mmzs=0.15mmZ=10n=500通过计算得到N=0.8079kwf=0.2
V=80×π×500×0.01=125.6m/minN=FVF≈385N
切削力约为385N同理轴向力也为385N计算油缸快进时候的驱动压力
选取油缸d=110mm外径D=150mm杆1d=50mm
1P=2P*2F/1F+1D/1F+G/1Fu2P油缸后腔的压力(组合机床多用差动系统2P=1P)1F油缸前腔面积1F油缸后腔面积
1D
油缸阻力和管路损失可取1D/1F=4~5公斤/2cm
u摩擦系数取0.14~0.15G移动部件(铁削头)计算得1P=5.23公斤/2cm6.2选择液压元件:
系统压力和流量是选择压力控制阀流量控制阀以及方向控制阀的主要依据,我们根据设计要求,选用三位五通换向阀,它使运动部件向前向后控制,或使部件在任意位置停留。
6.3油箱温升计算以及油箱容量的选定
油箱除了用来置油以提供液压系统的油源外,还用来维持液压系统适当的油温,沉淀中的污浊和分离掉油中的气泡。
液压系统中的发热主要有以下几个方面的损失所造成:
1)油泵和油缸中的损失
2)油液从溢流阀中排出时的损失
3)油液通过油管,节流阀和其他元件的损失
谢辞
首先,我要感谢老师对毕业设计的指导。
在毕业设计中,老师花了大量的时间提出了很多的设计问题,并给予了很多的建议,让我知道了在做设计时应多方面考虑问题,同时,老师认真、负责的工作态度,让我在此次设计路上走的更为平坦,衷心的感谢老师,您辛苦了!
同时,我深深感谢在大学四年中教授我知识的老师们。
你们辛苦的付出,让我在学习中收获了很多,在你们的课堂上,我受益匪浅,得到了不少对我论文有帮助的知识和想法。
我也非常感谢我的父母。
在学习和生活上,他们一直都很支持我,使我能全身心地投入到学习中,在此,我想对我的父母说:
你们辛苦了,我会尽最大的努力来让你们过上最幸福的日子,请相信我。
最后,很感谢阅读这篇毕业设计的人们。
感谢您们抽出宝贵的时间来阅读这篇毕业设计。
参考文献
[1]李旦,邵东向,王杰.机床专用夹具图册[M],哈尔滨:
哈尔滨工业大学出版社,
2005。
[2]贵州工学院机械制造工艺教研室.机床夹具结构图册[M],贵阳:
贵州任命出版社,
1983。
[3]陈宏钧.实用金属切削手册[M],北京:
机械工业出版社,2005。
[4]陈宏钧.实用机械加工工艺手册[M],北京:
机械工业出版社,2003。
[5]李洪.机械加工工艺手册[M],北京:
机械工业出版社,1990。
[6]马贤智.机械加工余量与公差手册[M],北京:
中国标准出版社,1994。
[7]强毅.设计图实用标准手册[M],北京:
科学出版社,2000。
[8]杨叔子.机械加工工艺师手册[M],北京:
机械工业出版社,2001。
[9]李益民.机械制造工艺设计简明手册[M],北京:
机械工业出版社,1979。
[10]艾兴肖诗纲.切削用量简明手册[M].广州:
机械工业出版社,2006。
[11]李庆余,张佳.机械制造装备设计[M],北京:
机械工业出版社,2003。
[12]廖念钊,莫雨松,李硕根.互换性与技术测量[M],中国计量出版社,2000:
9-19。
[13]王光斗,王春福.机床夹具设计手册[M],上海科学技术出版社,2000。
[14]何玉林,沈荣辉,贺元成.机械制图[M],北京:
机械工业出版社,2000。
[15]邓文英.金属工艺学[M],北京:
高等教育出版社,2001。
[16]MachineToolsN.chernor1984.
[17]MachineToolMetalworkingJohnL.Feirer1973.
[18]HandbookofMachineToolsManfredweck