各种加工方法能达到的表面粗糙度.docx
《各种加工方法能达到的表面粗糙度.docx》由会员分享,可在线阅读,更多相关《各种加工方法能达到的表面粗糙度.docx(12页珍藏版)》请在冰豆网上搜索。
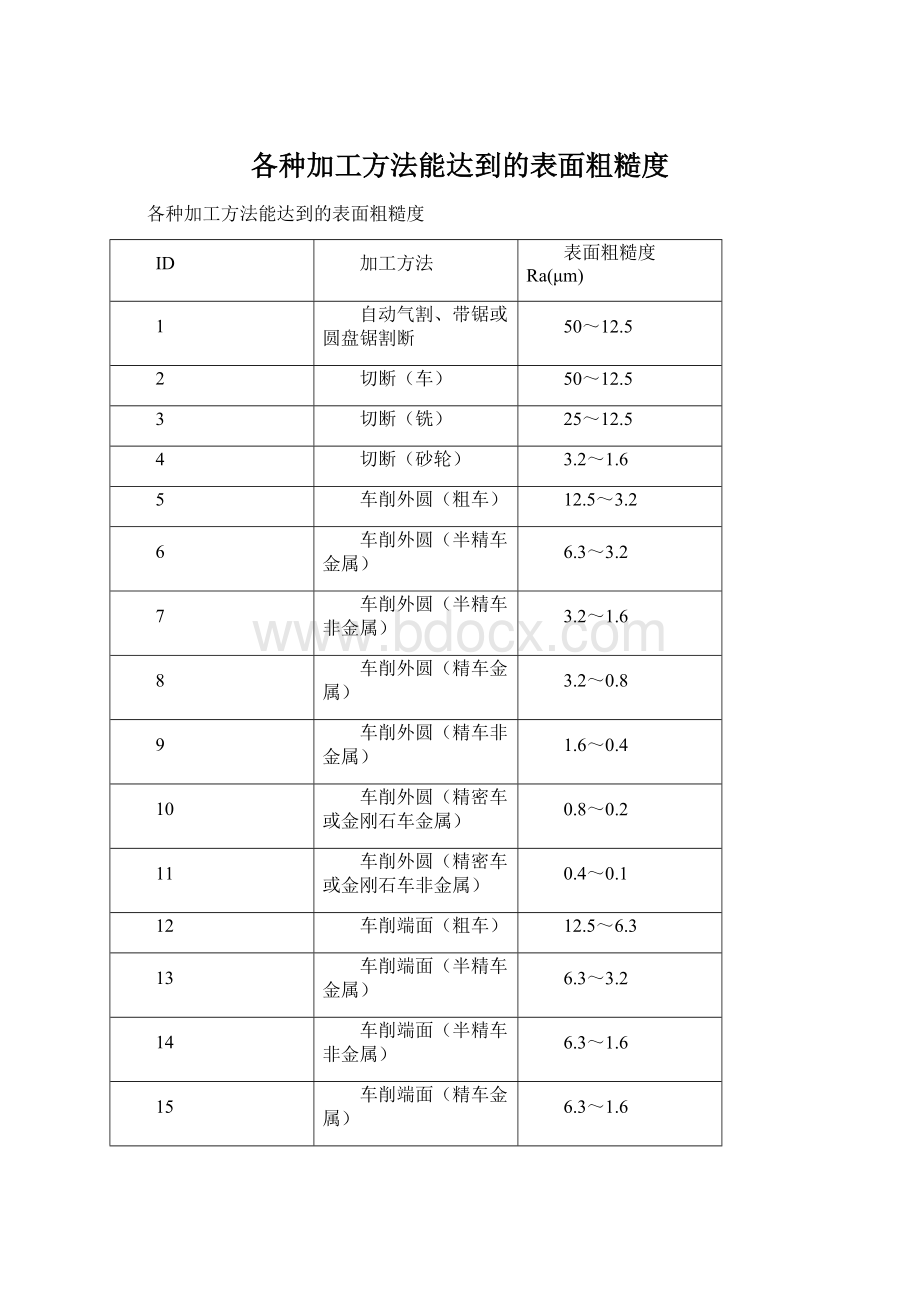
各种加工方法能达到的表面粗糙度
各种加工方法能达到的表面粗糙度
ID
加工方法
表面粗糙度Ra(μm)
1
自动气割、带锯或圆盘锯割断
50~12.5
2
切断(车)
50~12.5
3
切断(铣)
25~12.5
4
切断(砂轮)
3.2~1.6
5
车削外圆(粗车)
12.5~3.2
6
车削外圆(半精车金属)
6.3~3.2
7
车削外圆(半精车非金属)
3.2~1.6
8
车削外圆(精车金属)
3.2~0.8
9
车削外圆(精车非金属)
1.6~0.4
10
车削外圆(精密车或金刚石车金属)
0.8~0.2
11
车削外圆(精密车或金刚石车非金属)
0.4~0.1
12
车削端面(粗车)
12.5~6.3
13
车削端面(半精车金属)
6.3~3.2
14
车削端面(半精车非金属)
6.3~1.6
15
车削端面(精车金属)
6.3~1.6
16
车削端面(精车非金属
6.3~1.6
17
车削端面(精密车金属)
0.8~0.4
18
车削端面(精密车非金属)
0.8~0.2
19
切槽(一次行程)
12.5
20
切槽(二次行程)
6.3~3.2
21
高速车削
0.8~0.2
22
钻(≤φ15mm)
6.3~3.2
23
钻(>φ15mm)
25~6.3
24
扩孔、粗(有表皮)
12.5~6.3
25
扩孔、精
6.3~1.6
26
锪倒角(孔的)
3.2~1.6
27
带导向的锪平面
6.3~3.2
28
镗孔(粗镗)
12.5~6.3
29
镗孔(半精镗金属)
6.3~3.2
30
镗孔(半精镗非金属)
6.3~1.6
31
镗孔(精密镗或金刚石镗金属)
0.8~0.2
32
镗孔(精密镗或金刚石镗非金属)
0.4~0.2
33
高速镗
0.8~0.2
34
铰孔(半精铰一次铰)钢
6.3~3.2
35
铰孔(半精铰一次铰)黄铜
6.3~1.6
36
铰孔(半精铰二次铰)铸铁
3.2~0.8
37
铰孔(半精铰二次铰)钢、轻合金
1.6~0.8
38
铰孔(半精铰二次铰)黄铜、青铜
0.8~0.4
39
铰孔(精密铰)钢
0.8~0.2
40
铰孔(精密铰)轻合金
0.8~0.4
41
铰孔(精密铰)黄铜、青铜
0.2~0.1
42
圆柱铣刀铣削(粗)
12.5~3.2
43
圆柱铣刀铣削(精)
3.2~0.8
44
圆柱铣刀铣削(精密)
0.8~0.4
45
端铣刀铣削(粗)
12.5~3.2
46
端铣刀铣削(精)
3.2~0.4
47
端铣刀铣削(精密)
0.8~0.2
48
高速铣削(粗)
1.6~0.8
49
高速铣削(精)
0.4~0.2
50
刨削(粗)
12.5~6.3
51
刨削(精)
3.2~1.6
52
刨削(精密)
0.8~0.2
53
刨削(槽的表面)
6.3~3.2
54
插削(粗)
25~12.5
55
插削(精)
6.3~1.6
56
拉削(精)
1.6~0.4
57
拉削(精密)
0.2~0.1
58
推削(精)
0.8~0.2
59
推削(精密)
0.4~0.025
60
外圆磨内圆磨(半精、一次加工)
6.3~0.8
61
外圆磨内圆磨(精)
0.8~0.2
62
外圆磨内圆磨(精密)
0.2~0.1
63
外圆磨内圆磨(精密、超精密磨削)
0.050~0.025
64
外圆磨内圆磨(镜面磨削外圆磨)
<0.050
65
平面磨(精)
0.8~0.4
66
平面磨(精密)
0.2~0.05
67
珩磨(粗、一次加工)
0.8~0.2
68
珩磨(精、精密)
0.2~0.025
69
研磨(粗)
0.4~0.2
70
研磨(精)
0.2~0.025
71
研磨(精密)
<0.050
72
超精加工(精)
0.8~0.1
73
超精加工(精密)
0.1~0.05
74
超精加工(镜面加工、两次加工)
<0.025
75
抛光(精)
0.8~0.1
76
抛光(精密)
0.1~0.025
77
抛光(砂带抛光)
0.2~0.1
78
抛光(砂布抛光)
1.6~0.1
79
抛光(电抛光)
1.6~0.012
80
螺纹加工/切削/板牙、丝锥、自开式板牙头
3.2~0.8
81
螺纹加工/切削/车刀或梳刀车、铣
6.3~0.8
82
螺纹加工/切削/磨
0.8~0.2
83
螺纹加工/切削/研磨
0.8~0.050
84
螺纹加工/滚轧/搓丝模
1.6~0.8
85
螺纹加工/滚轧/滚丝模
1.6~0.2
86
齿轮及花键加工/切削/粗滚
3.2~1.6
87
齿轮及花键加工/切削/精滚
1.6~0.8
88
齿轮及花键加工/切削/精插
1.6~0.8
89
齿轮及花键加工/切削/精刨
3.2~0.8
90
齿轮及花键加工/切削/拉
3.2~1.6
91
齿轮及花键加工/切削/剃
0.8~0.2
92
齿轮及花键加工/切削/磨
0.8~0.1
93
齿轮及花键加工/切削/研
0.4~0.2
94
齿轮及花键加工/滚轧/热轧
0.8~0.4
95
齿轮及花键加工/滚轧/冷轧
0.2~0.1
96
刮(粗)
3.2~0.8
97
刮(精)
0.4~0.05
98
滚压加工
0.4~0.05
99
钳工锉削
12.5~0.8
100
砂轮清洗
50~6.3
由于机械加工表面质量对机器零件的使用性能如耐磨性、接触刚度、疲劳强度、配合性质、抗腐蚀性能以及精度的稳定性能有很大的影响,因此对机器零件的重要表面应提出一定的表面质量要求。
加工表面质量包括两个反复面的内容:
(1)已加工表面的几何形状特征,主要指已加工表面的粗糙度、波度和纹理方向。
(2)已加工表面层的物理品质,主要包括表面层的加工硬化程度及冷硬层深度,表面层残余应力的性质、大小及分布状况,加工表面层的金相组织变化。
已加工表面粗糙度
1.表面粗糙度的形成原因及降低措施
(1)切削加工表面粗糙度形成原因
1)几何因素,几何因素所产生的表面粗糙度主要决定于残留面积高度(见图3-1中的H)。
图3-1 车削时的残留面积高度
2) 物理因素,切削加工后表面的实际粗糙度最大值往往高于残留面积高度,这主要是因为在切削加工过程中还存在各种物理因素的影响。
这些物理因素主要是积屑瘤、鳞刺、金属材料的塑性变形,以及工艺系统的振动等。
(2)降低切削加工表面粗糙度的措施
1)刀具方面,增大刀尖圆弧半径rε,减小主偏角kr及副偏角k′r;使用长度比进给量稍大一些的修光刃(k′r=0°);提高刀具刃磨质量,减小刀具前、后到面的粗糙值(抛光至Ra1.25μm以下);采用较大的前角y0加工塑性大的材料;限制副刀刃上的磨损量;选用细粒的硬质合金切削谈素工具钢,用金刚石或矿物陶瓷刀具加工有色金属,高速钢刀具采用TiN涂层等。
2)工件方面,切削低碳钢、低合金钢时,对工件进行调质处理;加工中碳钢及中碳合金钢时,若采用较高切削速度,工件应为珠光体组织,若采用较低切削速度,工件应为片状珠光体加细晶粒的铁素体组织;易切削钢中应含有硫、铅等元素;灰铸铁中石墨的颗粒尺寸应小。
3)切削条件反复面,以较高的切削速度切削塑性材料,减小进给量(见图3-2);采用高效切削液;提高机床运动精度,增强工艺系统刚度等。
图3-2切削速度及进给量对表面粗糙度的影响
工件:
35钢,刀具:
YT15,切削深度ap=0.5mm
(3)磨削表面粗糙形成原因及降低措施磨削表面粗糙度形成原因既有几何因素(残留面积),也有塑性变形、软化、微熔等物理因素,以及工艺系统振动的印象,因此降低磨削表面粗糙度的主要措施是:
1)砂轮特性方面,采用细粒度砂轮(砂轮粒度号一般不超过80号,常用的是46~60号);根据工件材料、磨料等选择适宜的砂轮轮硬度(通常选用中软砂轮);刚玉或氧化铝类砂轮适于磨削各种钢制零件,碳化硅类砂轮适于磨削硬质合金、铸铁、黄铜、铝等,人造金刚石砂轮适于加工光学玻璃、陶瓷,立方氮化硼砂轮可用于磨削高硬度、高强度钢;组织紧密的砂轮适用于精磨、成形磨削,中等组织的砂轮适用于一般磨削,疏松组织的砂轮适用于粗磨、平面磨、内圆磨、以及热敏感性较强的材料、软金属和薄壁工件的磨削;增大砂轮宽度,采用直径较大砂轮等。
2)磨削条件反复面。
降低工件速度,提高砂轮转速;采用较小的纵向进给量、磨削深度(背吃刀量),最后进行无进给光磨;砂轮修整要细,静,动平衡精度要高;正确选用切削液的种类、浓度比、压力、流量和清洁度;提高机床主轴的回转精度、工作台运动的平稳性以及整个工艺系统的刚度。
2. 各种加工方法能达到的表面粗糙度(见表3-31)。
表3-31 各种加工反复法能达到的表面粗糙度
加工方法
表面粗糙度Ra/μm
加工方法
表面粗糙度Ra/μm
自动气割、带锯或圆盘割断
50~12.5
铰孔
精铰(二次铰)
铸铁
3.2~0.8
切断
车
50~12.5
钢、轻合金
1.6~0.8
铣
25~12.5
黄铜、青铜
0.8`0.4
砂轮
3.2~1.6
精密铰
钢
0.81~0.2
车削外圆
组车
12.5~3.2
轻合金
0.8~0.4
半精车
金属
6.3~3.2
黄铜、青铜
0.2`0.1
非金属
3.2~1.6
圆柱铣刀铣削
粗
12.5~3.2
精车
金属
3.2~0.8
精
3.2~0.8
非金属
1.6~0.4
精密
0.8~0.4
车削外圆
精密车(或金刚石车)
金属
0.8~0.2
端铣刀铣削
粗
12.5~3.2
非金属
0.4~0.1
精
3.2~0.4
车削端面
粗车
12.5~6.3
精密
0.8~0.2
半精车
金属
6.3~3.2
高速铣削
粗
1.6~0.8
非金属
6.3~1.6
精
0.4~0.2
精车
金属
6.3~1.6
刨削
粗
12.5~6.3
非金属
6.3~1.6
精
3.2~1.6
精密车
金属
0.8~0.4
精密
0.8~0.2
非金属
0.8~0.2
槽的表面
6.3~3.2
切槽
一次行程
12.5
插削
粗
25~12.5
二次行程
6.3~3.2
精
6.3~1.6
高速车削
0.8~0.2
镗孔
粗镗
12.5~6.3
半精镗
金属
6.3~3.2
钻
<15mm
6.3~3.2
非金属
6.3~1.6
>15mm
25~6.3
精镗
金属
3.2~0.8
扩孔
粗(有表皮)
12.5~6.3
非金属
1.6~0.4
精
6.3~1.6
精密镗(或金刚石镗)
金属
0.8~0.2
锪倒角(孔的)
3.2~1.6
非金属
0.4~0.2
带导向的锪平面
6.3~3.2
高速镗
0.8~0.2
铰孔
半精铰(一西铰)
钢
6.3~3.2
拉削
精
1.6~0.4
黄铜
6.3~1.6
精密
0.2~0.1
推削
精
0.8~0.2
螺纹加工
切削
板牙、丝锥、字开式板牙头
3.2~0.8
精密
0.4~0.025
车刀或梳刀车、铣
6.3~0.8
外圆磨内圆磨
半精(一次加工)
6.3~0.8
磨
0.8~0.2
精
0.8~0.2
研磨
0.8~0.050
精密
0.2~0.1
滚轧
搓丝模
1.6~0.8
精密、超精密磨削
0.050~0.025
滚丝模
1.6~0.2
镜面磨削(外圆磨)
<0.050
齿轮及花键盘加工
切削
粗滚
3.2~1.6
平面镜
精
0.8~0.4
精滚
1.6~0.8
精密
0.2~0.05
精插
1.6~0.8
珩磨
粗(一次加工)
0.8~0.2
精刨
3.2~0.8
精、精密
0.2~0.025
拉
3.2~1.6
研磨
粗
0.4~0.2
剃
0.8~0.2
精
0.2~0.05
磨
0.8~0.1
精密
<0.050
研
0.4~0.2
超精加工
精
0.8~0.1
滚轧
热轧
0.8~0.4
精密
0.1~0.05
冷轧
0.2~0.1
镜面加工(二次加工)
<0.025
刮
粗
3.2~0.8
抛光
精
0.8~0.1
精
0.4~0.05
精密
0.1~0.025
砂带抛光
0.2~0.1
滚压加工
0.4~0.05
砂布抛光
1.6~0.1
钳工锉削
12.5~0.8
电抛光
1.6~0.012
砂轮清理
50~6.3