回转窑轴线测量及调整secret.docx
《回转窑轴线测量及调整secret.docx》由会员分享,可在线阅读,更多相关《回转窑轴线测量及调整secret.docx(11页珍藏版)》请在冰豆网上搜索。
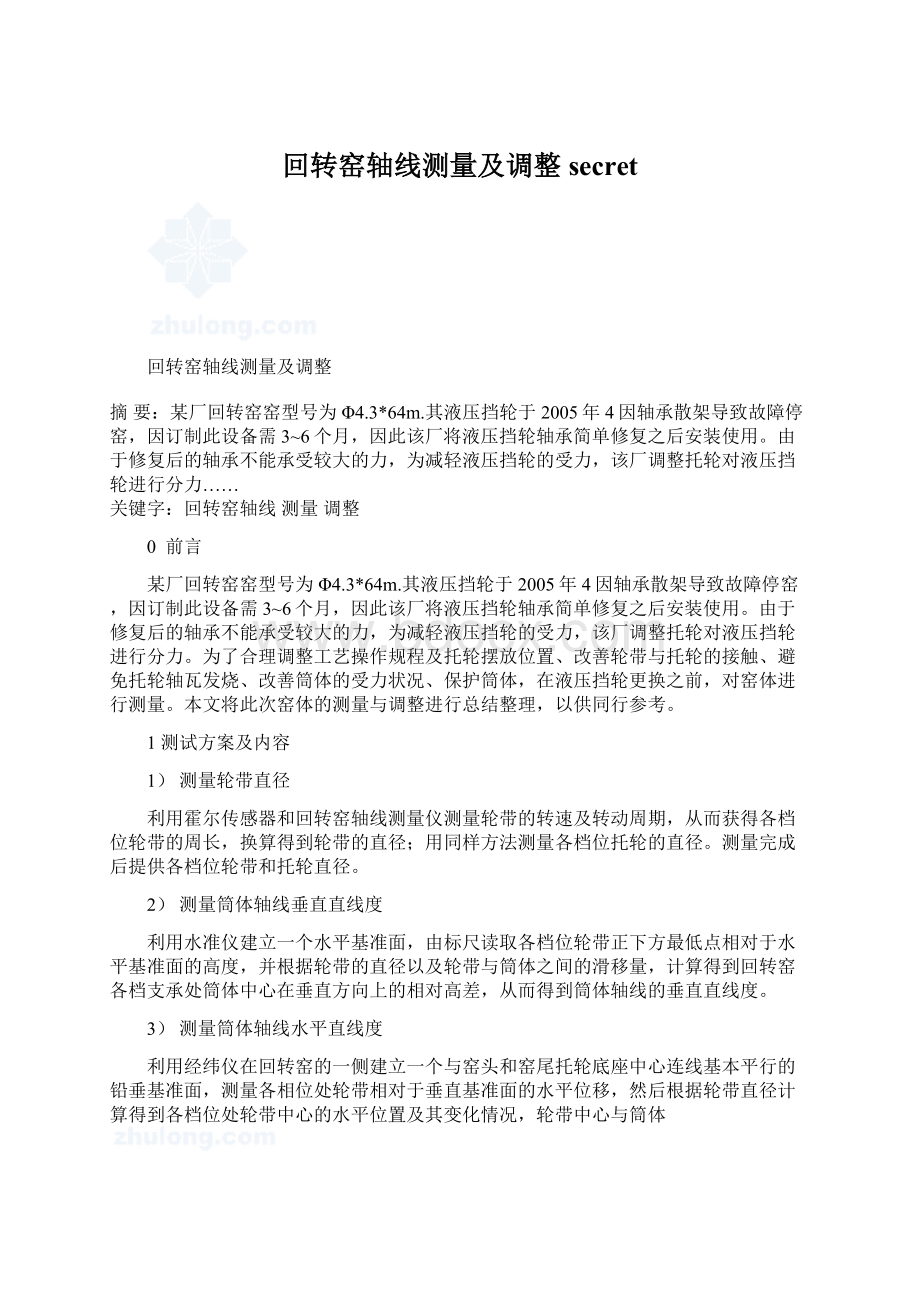
回转窑轴线测量及调整secret
回转窑轴线测量及调整
摘要:
某厂回转窑窑型号为Φ4.3*64m.其液压挡轮于2005年4因轴承散架导致故障停窑,因订制此设备需3~6个月,因此该厂将液压挡轮轴承简单修复之后安装使用。
由于修复后的轴承不能承受较大的力,为减轻液压挡轮的受力,该厂调整托轮对液压挡轮进行分力……
关键字:
回转窑轴线测量调整
0 前言
某厂回转窑窑型号为Φ4.3*64m.其液压挡轮于2005年4因轴承散架导致故障停窑,因订制此设备需3~6个月,因此该厂将液压挡轮轴承简单修复之后安装使用。
由于修复后的轴承不能承受较大的力,为减轻液压挡轮的受力,该厂调整托轮对液压挡轮进行分力。
为了合理调整工艺操作规程及托轮摆放位置、改善轮带与托轮的接触、避免托轮轴瓦发烧、改善筒体的受力状况、保护筒体,在液压挡轮更换之前,对窑体进行测量。
本文将此次窑体的测量与调整进行总结整理,以供同行参考。
1测试方案及内容
1)测量轮带直径
利用霍尔传感器和回转窑轴线测量仪测量轮带的转速及转动周期,从而获得各档位轮带的周长,换算得到轮带的直径;用同样方法测量各档位托轮的直径。
测量完成后提供各档位轮带和托轮直径。
2)测量筒体轴线垂直直线度
利用水准仪建立一个水平基准面,由标尺读取各档位轮带正下方最低点相对于水平基准面的高度,并根据轮带的直径以及轮带与筒体之间的滑移量,计算得到回转窑各档支承处筒体中心在垂直方向上的相对高差,从而得到筒体轴线的垂直直线度。
3)测量筒体轴线水平直线度
利用经纬仪在回转窑的一侧建立一个与窑头和窑尾托轮底座中心连线基本平行的铅垂基准面,测量各相位处轮带相对于垂直基准面的水平位移,然后根据轮带直径计算得到各档位处轮带中心的水平位置及其变化情况,轮带中心与筒体
中心在同一铅垂面内,从而得到筒体轴线的水平直线度。
测量完成后算出筒体轴线垂直直线度和水平直线度。
4)根据测量得到的筒体轴线直线度和筒体的安装情况,制定以轴线准直为目的托轮位置调整方案。
2 轮带和托轮直径测量
2.1 测量原理
轮带直径的测量原理如图1所示。
在轮带侧面吸附一磁片,在轮带下方安装一个霍尔传感器,霍尔传感器在磁片经过时输出一个脉冲信号,用回转窑轴线测量仪测量这些脉冲的时间间隔,可以得到轮带的转动周期。
速度传感器与测量仪配合可以测量轮带表面的线速度。
根据轮带表面线速度和转动周期可以计算出轮带周长,进而计算得到轮带直径。
托轮直径用同样方法测量。
2.2测量数据
测量各轮带和托轮左、中、右三个位置的直径,轮带、托轮及其上面测量截面的选取及编号如图2所示。
轮带上测量截面的编号为1、2、3,托轮上的为1′、2′、3′,1(1′)、3(3′)号测量截面一般距侧面150mm,截面选择原则为尽量靠近外侧且没有油污和大的剥落斑点,2号截面位于中部,选择原则为尽量没有大的剥落斑点。
表1和表2为测量结果。
表1托轮直径测量数据(单位:
mm)
截面
A
B
C
D
E
F
1
1599
1600
1798.7
1786.7
1598.7
1597.7
2
1599
1598
1800.3
1798.5
1599.7
1596.7
3
1600
1599
1798.7
1794.0
1594.7
1596.0
表2轮带直径测量数据(单位:
mm)
截面
I
II
III
1
5258.7
5258.3
5252.5
2
5257.7
5254.0
5254.5
3
5255.0
5243
5248.0
表中数据没有小数点的数据为轮带或托轮转动4周过程中测量的最大值,有小数点的数据为轮带或托轮转动4周,4个测量数据中剔除最小值后三个值的平均值。
2.3测量数据分析
根据测量数据绘制的托轮和轮带形状示意图如图3所示。
从图3中可以看出:
I、II档东侧托轮磨损较严重,同时I档西侧托轮南端磨损较严重,II档轮带南端磨损较多。
据此,可以大致判断其受力情况,磨损较多主要与长期受力相对较大有关。
除III档西侧托轮A以外,各档轮带和托轮南端磨损都相对较多,其原因可能是安装时托轮摆放斜度与筒体斜度不一致;或者运行过程中I、II档轮带特别是I档轮带向南端移动较多,导致筒体实际斜度变小,而托轮斜度未变,故托轮和轮带南端普遍受力较大。
需在停窑检修期间对托轮及轮带直径进行测量,或用压铅丝法测量各档不同位置受力情况,以验证以上分析并进行相应处理。
3 筒体轴线垂直直线度和水平直线度的测量与分析
3.1垂直直线度测量及分析
3.1.1测量原理及有关数据
图4为测量原理图及各档轮带最低点到水平基准面的测量数据。
S1、S2为回转窑安装图纸中各档轮带中心的水平距离。
根据轮带直径测量截面布置及垂直位移测量情况,取各轮带1号截面直径用于计算回转窑轴线垂直直线度,轮带直径数据见表2。
表3为轮带转动3周过程中的滑移量。
表3各档滑移量数据
档位
I
II
III
滑移量δC(mm)
50.5
23.25
40
(表3中的数据如何得来?
是计算还是测量?
)
设轮带直径为D,筒体加垫板后直径为d,轮带与筒体中心高差为δh,δh=(D-d)/2,滑移量δC=3π(D-d),则δh、δC关系为:
δh=δC/(6π)
(公式δC=π×(D-d)×3的出处?
)
3.1.2 垂直直线度计算
1)各档轮带最低点相对于水平基准面的高度
H1=h1=498.1mm
H2=h2+h2′=252.8+1088.2=1341mm
H3=h3+h3′+h2′=531.0+500.0+1088.2=2119.2mm
2)各档轮带中心与筒体中心的高度差
δh=δC/(6π)
δh1=50.5/(6π)=2.7mm
δh2=23.25/(6π)=1.2mm
δh3=40/(6π)=2.1mm
3)II、III档筒体中心相对于I档筒体中心的实测高度
h21=(H2+D2/2-δh2)-(H1+D1/2-δh1)=847.2mm
h31=(H3+D3/2―δh3)―(H1+D1/2-δh1)=1624.8mm
4)II、III档筒体中心相对于I档筒体中心的设计高度
h21'=825.6mm
h31'=1650mm
此数据由建筑图纸各档轮带中心标高换算得到。
5)II、III档筒体中心实测高度与设计高度偏差
EY2=h21-h21'=21.6mm
EY3=h31-h31'=-25.2mm (负值表示偏低)
6)II档筒体中心相对于I、III档筒体中心连线的偏差
EY2'=h21-h31×S1/(S1+S2)=34.4mm
3.1.3垂直直线度分析
图5为根据计算结果绘制的回转窑垂直直线度分析图。
从图5可以看出,II档筒体中心比设计值偏高21.6mm,III档比设计值偏低25.2mm。
测量过程中观察到I档基础有明显轴向振动,而且轮带侧面焊接的供中控室测量轮带与筒体间滑移量用的角铁已低于与之配合的传感器。
结合轮带及托轮磨损数据和垂直直线度分析结果,初步判断III档基础有一定下沉,同时I档轮带向南移动距离较大。
由上判断结果需对各档轮带中心之间轴向水平距离,即图4中S1、S2,进行准确测量,并根据计算过程中步骤6)所示公式校核II档与I、III中心连线之间偏差EY2',根据校核情况对托轮位置进行适当调整。
轮带中心测量有一定困难,实际测量图4中S1、S2时可以测量各档轮带侧面最低点之间距离,即图4中测量各档轮带最低点高度的位置。
3.2水平直线度测量及分析
3.2.1 测量原理及有关数据
测量原理图及主要数据如图6和图7所示。
由于III档托轮底座中心标记已不存在,现以I、II档托轮底座中心标记连线作为理想轴线,并以此为参照物建立铅垂基准面:
将I、II档托轮底座中心标记分别向东侧平移2676mm和3600mm,标记为C1、C2,用经纬仪建立过C1、C2的铅垂面作为水平位移测量的基准面。
C2与II档底座上的轮带中心标记沿轴线方向的距离为DS2=1873mm。
由于基准面与I档轮带北侧外圆相切,如图6所示,故不再用位移传感器测量此档位水平位移,直接用轮带直径计算即可,这样可以减小支架安装和振动等造成的测量误差。
基准面在II、III档处与位移传感器上标尺的交点分别标记为C2'、C3',基准面与I档轮带北侧外圆的切点记为C1'。
C2'、C3'之间轴向距离为S2,C1'、C2'之间为DS-DS2。
基准面与轴线之间夹角记为θ。
δL为轮带转动一周过程中位移传感器读数平均值。
δL测量值及平均值见表4。
回转窑轴线测量仪记录位移数据时将轮带等分为36份,轮带每转过10°时测量仪记录一个位移值,按轮带标称直径5250mm计算,表4中各相位在轮带表面大约相距458mm,表中相位编号从轮带上焊接角铁的位置开始,逆着轮带转动方向编号增大。
表4中加括号的位移数据为较大误差的原始数据,实际计算时取前后两个相位位移的平均值作为此相位位移值。
括号中数值比外面数值小的说明此点是一个凹陷的剥落斑点,比外面数值大则是即将产生剥落的鼓起点。
根据传感器布置情况,I档取北侧的1号截面直径用于计算水平位移,II、III档取位于中间的2号截面直径用于计算,轮带直径数据见表2。
水平直线度计算结果为各档位筒体中心与理想轴线的偏差。
计算过程为:
首先根据基准面与理想轴线之间夹角及各档之间距离计算出基准面在各档位处与理想轴线的距离Lzi,然后根据传感器零点与基准面之间距离L及传感器读数平均值δL计算出各档轮带外圆到理想轴线的距离Ri'=Lzi-Li-δLi,最后根据各档轮带直径计算出轮带中心与理想轴线的偏差EXi=Ri'-Di/2,i=1,2,3。
基准面与轴线夹角θ的正切值为:
tanθ=(E2-E1)/DS=0.03904。
I档轮带宽度B1=750mm。
表4II、III档轮带位移数据
相位
Ⅱ
Ⅲ
相位
Ⅱ
Ⅲ
1
6.3
2.2
21
5.1
3.9
2
5.8
2.6
22
5.2
3.7
3
5.0
2.7
23
5.2
3.5
4
5.0
3.0
24
5.2
3.2
5
4.6
3.1
25
5.3(1.8)
2.9
6
4.4(1.8)
3.2
26
5.3
2.6
7
4.1
3.2
27
5.3
2.2
8
3.9
3.4
28
5.3
2.0
9
-0.2
2.7
29
5.4
2.1
10
-0.2(5.1)
-0.5
30
5.4(-2.3)
2.1
11
-0.2
-1.0
31
5.4
2.1(5.5)
12
0.0
-1.4
32
2.0
2.1
13
0.0
-1.9
33
1.5
2.2
14
-0.1
3.7
34
5.3
2.2
15
0.2
3.7
35
5.3
2.3
16
5.5
3.7
36
5.3
2.3(-3.3)
17
5.5
3.2
平均值δL
4.0
2.4
18
5.5
3.1
最大值
-0.2
-1.9
19
5.1
3.9
最小值
6.3
3.9
20
5.1
3.4
晃动幅度
6.5
5.8
3.2.2水平直线度的计算
1)基准面在各档位处与理想轴线的距离Lzi
Lz1=E1-(S1+DS2-DS-B1/2)×tanθ=2621.2mm
Lz2=E1+(DS-DS2)×tanθ=3526.9mm
Lz3=E1+(DS-DS2+S2)×tanθ=4446.2mm
2)各档轮带外圆到理想轴线的距离Ri'
R1'=Lz1=2621.2mm
R2'=Lz2-L2-(-δL2)=3526.87-895+4.0=2633.9mm
R3'=Lz3-L3-(-δL3)=4445.7-1792.5+2.4=2647.6mm
3)各档轮带中心与理想轴线的距离EXi
EX1=R1'-D1/2=-8.2
EX2=R2'-D2/2=2633.87-5254÷2=6.9mm
EX3=R3'-D3/2=2647.6-5254.5÷2=20.3mm
4)II档轮带中心相对于I、III档轮带中心连线的偏差EX2'
EX2'=(EX2-EX1)-(EX3-EX1)÷(S2+S2-B1/2)×(S1-B1/2)=0.9mm
3.2.3水平直线度分析
根据计算结果绘制的各档轮带中心水平偏差情况如图8所示。
计算数据及图示表明,II、III档轮带中心均偏向基准面所在侧,即东侧,I档偏向西侧,但三个档位轮带中心仍基本位于同一直线。
II档轮带中心相对于I、III档轮带中心连线的偏差EX2'仅为0.9mm。
根据轴线偏斜情况分析,I档西侧托轮应受力较大,这与托轮和轮带直径测量结果相符合。
同时,由于轴线歪斜较多,由托轮位置调整所致的可能性不大,有可能是基础移动所致。
若III档整体向东侧移动而II档托轮位置无变化,则II档轮带将有所升高I档轮带将向西偏移,同时导致II档东侧托轮受力较大,这和轮带及托轮直径测量结果相符合,也和垂直直线度测量结果一致。
4 托轮位置调整方案
4.1回转窑存在问题及原因分析
1)III档筒体中心比设计高度有较大程度降低,达25mm,向东偏移达20mm;
2)II档轮带比设计高度有一定程度降低,但目前II档筒体中心高出I、III档筒体中心连线达34mm,结合II档托轮调整记录,以确定轮带降低原因及数值,筒体中心向东偏移6.9mm;
3)I档轮带向南端移动较多,同时有较大程度降低,轮带降低可能为托轮调整所致,但轮带沿托轮沿轴向移动也会影响水平高度,结合计算结果和查找I档托轮调整记录,以确定轮带降低原因及具体数值,筒体中心有向西偏移8.2mm。
根据回转窑存在问题及现场观察情况,认为导致回转窑轴向变化原因有以下几个方面:
1)III档基础东侧有较大下沉,导致筒体中心高度降低,同时向东歪斜;
2)由于液压挡轮损坏,导致各档轮带长期在托轮南端运行,I档基础有较大轴向振动,可能与此有关;
3)I档托轮底座或基础由于长期受轴向振动影响,可能有一定程度向南移动,
注:
C1为I档基础地面上测量时用水泥钉所做的标记。
4.2托轮调整方案
根据当前回转窑轴线实际情况,结合实际调整的可能性,将III档托轮和大齿轮底座东侧同时升高,托轮和大齿轮底座不能同时调整,则仅调整I、II档托轮,降低II档轮带高度,并适当调整I、II档托轮斜度,调整方法及计算过程如下。
为减小托轮调整工作量,直线度调整只调整中间II档托轮,使II档轮带降低,此时,由于筒体在水平方向存在歪斜,I、II档托轮中心线也应做适当调整,使其与筒体轴线偏转方向一致。
因为II档轮带升高与筒体轴线水平方向偏斜有关,所以应首先将此档托轮底座轴线调至I、III档筒体中心连线上,即两侧托轮均向东平移6mm,使托轮底座中心在水平方向与图8中的筒体中心重合。
这样调整之后会使II档轮带大幅度降低。
为使轴线准直,还需降低的高度约为III档筒体中心高度降低量的一半,具体数值为:
Δh=EY3×S1/(S1+S2)=25.2×23572.46÷(23545.65+23572.46)=12.6mm。
在图10所示的三角形O1O2O3中,底边为设计值,两侧边为II档轮带和托轮中间位置半径之和。
O1O2=3527.15mm,O2O3=3525mm,O1O3=3526.25mm,此时,轮带中心距托轮中心连线高度为h=3054.7mm。
保持两侧边长度不变,高度降低Δh=12.6mm,则两托轮中心距应变为:
=3568.3
两托轮分别向外移动的距离为(3568.3-3525)/2=21.6mm。
综合以上计算结果,II档东侧托轮需向外移动21.6+6=27.6mm,西侧托轮需向外移动21.6-6=15.6mm。
筒体向东偏转角度正切值为tanγ=(EX3-EX1)/(S1+S2)=0.0006,为使托轮与轮带良好接触,各托轮轴线也应具有相同斜度。
即I、II档各托轮南端应向西调,北端向东调整,且移动距离应相同,设移动距离均为x,托轮宽为W,tanγ=2x/W,则调整量为x=W/2tanγ。
托轮宽约1000mm左右,即x应为0.3mm左右。
此调整量虽小,但对改善托轮与轮带接触情况有显著影响。