上机指导书质量管理概述.docx
《上机指导书质量管理概述.docx》由会员分享,可在线阅读,更多相关《上机指导书质量管理概述.docx(26页珍藏版)》请在冰豆网上搜索。
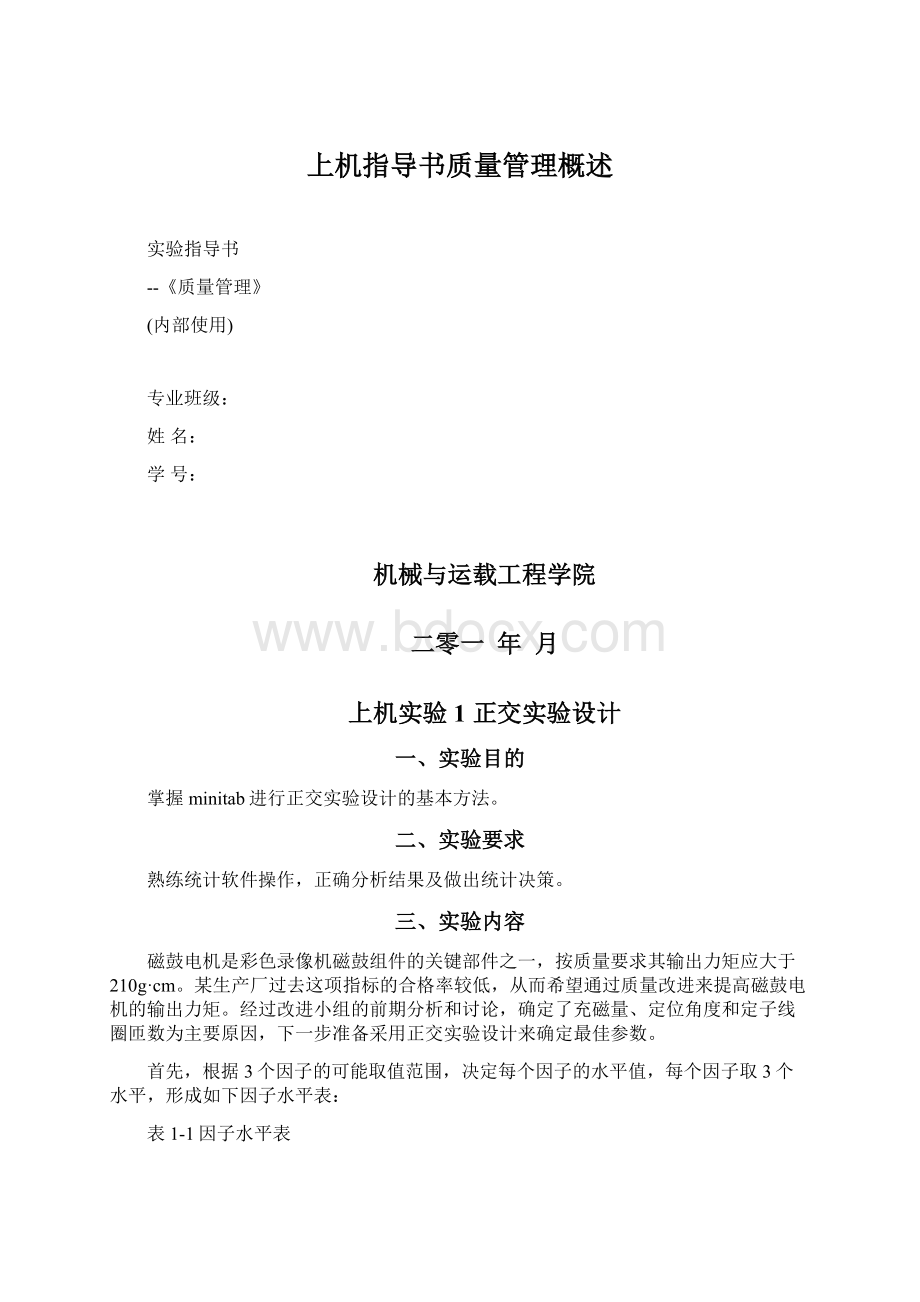
上机指导书质量管理概述
实验指导书
--《质量管理》
(内部使用)
专业班级:
姓名:
学号:
机械与运载工程学院
二零一年月
上机实验1正交实验设计
一、实验目的
掌握minitab进行正交实验设计的基本方法。
二、实验要求
熟练统计软件操作,正确分析结果及做出统计决策。
三、实验内容
磁鼓电机是彩色录像机磁鼓组件的关键部件之一,按质量要求其输出力矩应大于210g·cm。
某生产厂过去这项指标的合格率较低,从而希望通过质量改进来提高磁鼓电机的输出力矩。
经过改进小组的前期分析和讨论,确定了充磁量、定位角度和定子线圈匝数为主要原因,下一步准备采用正交实验设计来确定最佳参数。
首先,根据3个因子的可能取值范围,决定每个因子的水平值,每个因子取3个水平,形成如下因子水平表:
表1-1因子水平表
因子
水平
1
2
3
A:
充磁量
900
1100
1300
B:
定位角度
10
11
12
C:
定子线圈匝数
70
80
90
四、实验步骤思考及习题
1.创建正交实验计划
(1)选择菜单“统计-〉DOE-〉创建田口设计”:
(2)点击“创建田口设计”后,弹出如下对话框:
(3)在对话框“设计类型”中选择“3水平设计”,“因子数”选择“3”,再按下“设计”按钮,弹出如下对话框:
(4)选择“L9”正交表,按下“确定”返回上级对话框:
(5)按下“因子”按钮,进行因子水平表设计:
(6)根据“表1-1因子水平表”,将相应的内容修改到上面对话框中,修改后的对话框如图:
(7)点击“确定”按钮,返回上级对话框。
(8)点击“确定”按钮,Minitab将自动生成正交表,如图:
(9)在上图C4下面的标题框中输入“实验结果y”,完成实验计划的创建:
2.实施实验
有了实验计划后就可以按其进行实验,为了避免事先某些考虑不周而产生系统误差,因此实验的次序最后要随机化,然后将实验结果记录在对应的“实验结果y”列中。
获得的实验数据输入Minitab中,如图:
3.数据分析
(1)数据的直观分析:
按下“分析田口设计”,进入“分析田口设计”
将“实验结果y”选中到“响应数据位于”文本框中,按下“确定”按钮,进行分析:
根据Minitab所给出的均值响应表和均值主效应图可以看出:
对输出力矩影响最大的因子是定位角度,其次是充磁量,最后是定子线圈匝数
使指标达到最大的条件是A2B2C3,即充磁量取1100,定位角度取11,定子线圈取90,可以使输出力矩达到最大。
在数据的直观分析中是通过极差的大小来评价各个因子对指标影响的大小,那么极差要小到什么程度可以认为该因子对指标值已经没有显著的差别了呢?
为回答这一问题,需要对数据进行方差分析。
(2)数据的方差分析
按下“统计-〉方差分析-〉一般线形模型”进入如下对话框:
将“实验结果y”选中到“响应”框中,“充磁量、定位角度、定子线圈匝数”选入“模型”框内,点击“确定”,可得如下分析结果。
由于因子定位角度对应的P值为0.020小于0.05,所以在显著性水平0.05上,因子B是显著的;因子充磁量的P值为0.076小于0.10,所以因子在显著性水平0.10上是显著的。
因子C的P值为0.214大于0.10,所以在显著性水平0.10上因子C是不显著的。
4.最佳条件的选择
对显著因子应该选择其最好的水平,因为其水平变化会造成指标的显著不同,而对不显著因子可以任意选择水平。
实际中常可根据降低成本、操作方便等来考虑其水平的选择。
在显著性水平0.10上,因子A与B是显著的,所以要选择其最好的水平,按前所述,应取A2B2C3,对因子C可以选任意水平,譬如为了节约材料可选C1。
因此最佳条件为A2B2C1。
5.验证实验
在实验中找到的最佳条件是A2B2C3,即实验中的第5号实验,其实验结果确为9次实验中指标最高的。
但在实际问题中分析所得的最佳条件不一定在实验中出现,为此通常需要进行验证实验,譬如选择条件A2B2C1,该条件就不在所进行的9次实验中,它是否真的符合要求?
对于最终确定的实验结果,我们可以采用Minitab进行模拟验证:
点击“统计-〉DOE-〉田口-〉预测田口结果”菜单进入“预测田口结果”对话框,如图:
选中“均值”复选框,点击“水平”按钮进入“预测田口结果-水平”对话框,如图:
根据A2B2C1,对每个因子选择相应的水平数,然后点击“确定”按钮,返回“预测田口结果”对话框,如图:
点击“确定”按钮,由Minitab完成指定实验的模拟分析,结果如下:
由上面的数据可知模拟的结果为234.778。
对于预测的模拟结果,可在实际实验中进一步核实。
五、思考题
1.对于本实验,若显著性水平为0.05,则最佳条件该如何选定?
2.若要考虑因子之间的交互作用,如何进行数据分析?
上机实验2控制图
一、实验目的
掌握minitab软件用于绘制控制图的基本方法。
二、实验要求
熟练统计软件操作,正确分析结果及做出统计决策。
三、实验内容
某汽车发动机组装厂的部件之一的凸轮轴的长度必须为600mm+2mm以满足工程规格。
凸轮轴长度不符合规格是一个长期以来的问题,它引起装配时配合不良,导致废品率和返工率都居高不下。
部门主管要求绘制Xbar-R控制图以监控此特征,于是在一个月中从工厂使用的所有凸轮轴收集共100个观测值(20个样本,每个样本中5个凸轮轴),并从每个供应商处收集100个测量值。
其中一家供应商A的数据见表2-1,请绘制Xbar-R控制图。
表2-1供应商A凸轮轴长度测量值
样本1
样本2
样本3
样本4
样本5
样本6
样本7
样本8
样本9
样本10
1
601.6
602.8
598.4
598.2
600.8
600.8
600.4
598.2
599.4
601.2
2
600.4
600.8
599.6
602.0
598.6
597.2
598.2
599.4
598.0
599.0
3
598.4
603.6
603.4
599.4
600.0
600.4
598.6
599.4
597.6
600.4
4
600.0
604.2
600.6
599.4
600.4
599.8
599.6
600.2
598.0
600.6
5
596.8
602.4
598.4
600.8
600.8
596.4
599.0
599.0
597.6
599.0
样本11
样本12
样本13
样本14
样本15
样本16
样本17
样本18
样本19
样本20
1
602.2
601.6
599.8
603.8
600.8
598.0
601.6
602.4
601.4
601.2
2
599.8
600.2
602.8
603.6
600.2
598.4
603.4
602.2
599.2
604.2
3
599.8
601.8
600.0
601.8
600.4
600.8
597.0
600.6
601.6
600.2
4
601.0
601.2
599.6
602.0
600.2
602.8
599.8
596.2
600.4
600.0
5
601.6
597.6
602.2
603.6
602.2
597.6
597.8
602.4
598.0
596.8
四、实验步骤
(1)将上述按照表格形式数据输入到Minitab表格中,
(2)选择菜单“数据-〉堆叠列-〉列”,对数据堆叠成一列,弹出的对话框如图:
(3)按照上述内容进行设置,则可将所有的样本组数据堆叠成一列,如图:
(4)由于Xbar-R是计量型控制图,为保证结论的有效性,首先需要对数据的正态性进行检验。
(5)选择菜单“统计-〉基本统计量-〉正态性检验”,弹出对话框,如图:
将“C22样本数据”选中“变量”后面的文本框中;正态性检验规则,选中“Anderson-Darling”。
注:
正态性检验的三种方法选择依据:
①Anderson-Darling:
根据观测数据的累积分布函数ECDF来计算的,是系统的默认项,该方法是目前所有正态性检验中功效最高的;
②Ryan-Joiner:
该方法是ISO组织和我国标准化组织采用的方法,优点是可以对很小的样本进行正态性检验;
③Kolmogorov-Smirnov:
可适用于多种分布的检验,因此单独针对正态性检验的功效比前两种方法要低一些。
(6)点击上图的“确定”按钮后,弹出概率图,如图:
软件会生成正态概率图并进行假设检验,以检查观测值是否服从正态分布。
对于正态性检验,假设为:
H0:
数据服从正态分布与H1:
数据不服从正态分布
查看上图中的“P值”可知数据是否满足正态分布。
若P≤0.05,表示数据服从正态分布的概率小于或等于5%,属于小概率事件,则拒绝H0,反之,则没有足够证据拒绝H0,即在目前的情况下,接受数据服从正态分布的原假设。
有图上可得到P=0.615,也就是说本次的测量数据满足正态分布,可以进行下一步的工作;若本次得到的P值小于或等于0.05,则应该分析数据为什么非正态,找出原因,进行改进,再进行下一步的分析工作。
(7)选择菜单“统计->控制图->子组的变量控制图->Xbar-R”。
(8)在弹出的“Xbar-R”对话框的下拉框中选择“图表的所有观测值均在一列中”,双击鼠标左键将左边列表框中的“C22样本数据”选中到“图表的所有观测值均在一列中”下面的文本框中,“子组大小”后面的文本框中输入“5”,如图:
(9)点击“Xbar-R”对话框中的“Xbar-R选项”按钮,弹出“Xbar-R控制图-选项”对话框,点击“检验”标签,在标签页面中,选择“对特殊原因进行所有检验”。
(10)完成上述设置后,点击各级“确定”按钮,则系统自动弹出所绘制完成的控制图和分析结果,如图:
若控制图有异常,软件会在控制图上把存在异常的点,用红色进行标记。
从上图可看出,在Xbar图上有3处出现了异常情况,具体原因在“会话”窗口显示,如图:
从上面信息可看出过程处于非稳定状态,具体原因:
①第2、14样本的均值不符合检验规则1,即距离中心线超过3个标准差;
②从第5到第9样本的均值分布不符合检验规则6,即5点中有4点距离中心线超过了1个标准差(注意:
样本9出现异常,不是因为在控制限上,单点出现在控制限上,属于合格)。
(11)根据控制图所提供的信息,针对不合格情况,分析不合格原因,实施改进。
(12)再次收集数据,制作控制图,对过程的稳定性进行判定。
若过程稳定了,且工序能力满足要求,则延长此控制限,成为控制用控制图。
五、思考题
1、作为石灰石采石场的渠道经理,您要监视每周向重要客户运送的45批石灰石的重量(kg)和变异。
每一批的重量应近似为422kg。
表2-2是某一批次石灰石的重量,请选用适当的控制图来进行监控。
表2-2石灰石重量数据表
批
重量
批
重量
批
重量
批
重量
批
重量
1
905
10
910
19
915
28
975
37
900
2
930
11
920
20
930
29
1000
38
920
3
865
12
915
21
890
30
1035
39
980
4
895
13
925
22
940
31
1020
40
950
5
905
14
860
23
860
32
985
41
955
6
885
15
905
24
875
33
960
42
970
7
890
16
925
25
985
34
945
43
970
8
930
17
925
26
970
35
965
44
1035
9
915
18
905
27
940
36
940
45
1040
2、为调查一日产1800件的PCBA试产车间的质量状态,质量人员对其35天内每天出现的不良品数量进行了统计,数据见表2-3,如何了解其过程是否受控?
表2-3不良品数量统计表
天
1
2
3
4
5
6
7
缺陷数
5
0
6
4
6
3
4
天
8
9
10
11
12
13
14
缺陷数
3
3
4
3
4
1
3
天
15
16
17
18
19
20
21
缺陷数
6
8
2
5
2
4
3
天
22
23
24
25
26
27
28
缺陷数
2
5
2
7
5
3
4
天
29
30
31
32
33
34
35
缺陷数
9
5
3
4
1
3
2
上机实验3过程能力指数Cpk评估
一、实验目的
掌握minitab计算过程能力指数Cpk的基本方法。
二、实验内容
某六西格玛小组的改进课题是提高机电式电能表磁系统装配的合格率。
在需界定阶段对现场进行了调查研究,以了解当前的实际工序能力。
小组每天到装配工序抽取5个样品,进行测量并记录数据(测量系统已经过验证,符合要求),共记录了20天,数据如表3-1。
表3-1
第1天
第2天
第3天
第4天
第5天
第6天
第7天
第8天
第9天
第10天
1
2.41
2.37
2.36
2.47
2.46
2.33
2.38
2.41
2.44
2.45
2
2.48
2.51
2.37
2.5
2.37
2.29
2.28
2.49
2.28
2.39
3
2.44
2.54
2.45
2.4
2.5
2.43
2.3
2.38
2.45
2.41
4
2.26
2.43
2.38
2.38
2.41
2.45
2.41
2.42
2.45
2.35
5
2.41
2.39
2.42
2.32
2.46
2.49
2.46
2.36
2.51
2.4
第11天
第12天
第13天
第14天
第15天
第16天
第17天
第18天
第19天
第20天
1
2.38
2.45
2.33
2.44
2.41
2.36
2.46
2.41
2.37
2.47
2
2.28
2.39
2.29
2.35
2.49
2.37
2.37
2.48
2.45
2.5
3
2.3
2.41
2.43
2.45
2.38
2.45
2.5
2.44
2.55
2.4
4
2.41
2.35
2.45
2.45
2.42
2.3
2.41
2.26
2.55
2.38
5
2.46
2.4
2.49
2.51
2.36
2.42
2.46
2.41
2.39
2.32
过程的技术要求是2.50mm
0.25mm,请分析过程能力指数Cpk。
三、实验步骤
1.方法一:
单步分析法
(1)将上述按照表格形式数据输入到Minitab表格中。
(2)通过数据堆叠,将上述20天的数据堆叠到C21一列当中,并给C21列命名为“数据”,如图:
(3)由于MSA已经做过,是满足要求的,因此,在这里我们首先要进行数据的正态性检验。
选择菜单命令“统计->基本统计量->正态性检验”,如图:
从上图可看出,P值=0.129>0.05,数据满足正态分布。
(4)接着进行过程的稳定性分析,选择Xbar-R控制图来进行稳定性的判断。
如图:
从图中可看出,图中未出现红色异常点,表示过程处于稳定状态。
(5)选择菜单命令“统计->质量工具->能力分析->正态”。
(6)在弹出的“能力分布(正态分布)”对话框中,“数据排列为”选中“单列”,双击左边列表框中的“C21数据”将其选中到“单列”后面的文本框中,将数字“5”输入到“子组大小”后面的文本框中;规格下限设定为“2.25”,规格上限设定为“2.75”,如图:
(7)点击上面“能力分布(正态分布)”对话框中的“估计”按钮,则弹出“能力分布(正态分布)-标准差估计”对话框。
将框中的“估计子组内标准差的方法”选中为“Rbar”。
因为我们前面在对过程进行稳定性评判的时候,所采用的控制图是Xbar-R型的,如图:
(8)点击“确定”按钮,返回“能力分布(正态分布)”对话框中,点击对话框的“选项”按钮,则弹出“能力分布(正态分布)-选项”对话框。
将“2.5”输入到“目标(添加Cpm到表格)”后面的文本框中;选择“子组内分析”复选框。
如图:
(9)点击“确定”按钮,返回“能力分布(正态分布)”对话框中,点击对话框的“确定”按钮,完成设置,软件则弹出“数据的过程能力”图,如图:
从上图可看出Cpk=0.76,产品的合格率为10959.97×10-6,存在着较大的改进空间。
由于样本均值=2.41和目标值2.50存在较大的偏移,说明尺寸偏负,我们可以从现场管理方面入手,找出原因,将偏移进行修正,由于Cp=1.19,即使纠偏为0,Cpk也只能达到1.19,因此,若仍达不到我们改进目前的目标,说明过程波动过大,就要从5M1E等技术因素入手,优化参数,降低波动。
2。
方法一:
集成分析法
为了简化计算过程,Minitab提供了一种集成化的六合一Cpk分析图形,下面我们按照这种方法来进行操作。
(1)将上述数据按照表格形式输入到Minitab表格中。
(2)通过数据堆叠,将上述20天的数据堆叠到C21一列当中,并给C21列命名为“数据”。
(3)选择菜单命令“统计->质量工具->CapabilitySixpack->正态”。
(4)在弹出的“CapabilitySixpack(正态分布)”对话框中,“数据排列为”选中“单列”,双击左边列表框中的“C21数据”将其选中到“单列”后面的文本框中,将数字“5”输入到“子组大小”后面的文本框中,规格下限设定为“2.25”,规格上限设定为“2.75”,如图:
(5)点击“CapabilitySixpack(正态分布)”对话框中的“检验”按钮,在弹出的“检验”对话框中,将“进行所以8项检验”选中,以便完成控制图判异准则的设置,如图:
(6)点击“确定”按钮,返回“CapabilitySixpack(正态分布)”对话框。
点击对话框中的“估计”按钮,则弹出“CapabilitySixpack(正态分布)-标准差估计”对话框。
将框中的“估计子组内标准差的方法”选中为“Rbar”。
也就是说在对过程进行稳定性评判的时候,所采用的控制图将是Xbar-R型的,如图:
(7)点击“确定”按钮,返回“CapabilitySixpack(正态分布)”对话框。
点击对话框中的“选项”按钮,则弹出“CapabilitySixpack(正态分布)-选项”对话框。
将“2.50”输入到“目标(添加Cpm到表格)”后面的文本框中,如图:
(8)点击“确定”按钮,返回“CapabilitySixpack(正态分布)”对话框。
点击对话框中的“确定”按钮,完成设置,软件则弹出“数据的ProcessCapabilitySixpack”图,如图:
我们可以按照Cpk的分析流程,对上图中的图表逐一分析:
①首先看右中图“正态概率图”:
从图中可看出P=0.129,说明数据是状态的;
②然后看左上图和左中图所表示的Xbar-R控制图,未发现红色异常点,因此过程是稳定的;
③上述两个图都通过了,说明了我们具备计算Cpk的前提和基础了,然后看右下图“能力图”中所显示的Cpk值,从图中看知Cpk=0.76。
④若需要改进,则可通过右上图“能力直方图”来寻找改进的方向。
四、思考及习题
某型号钢珠直径的技术要求为(10.9~11.0)mm,质量状况欠佳,车间欲了解当前的实际工序能力指数情况,以便实施改进。
车间工艺人员每1000个作为一批,在钢珠加工工序抽取5个样品,进行测量并记录数据(测量系统已经过验证,符合要求),共记录了20天,数据如表3-2:
表3-2
批次
样品编号
1
2
3
4
5
1
10.95
10.90
10.95
10.96
10.98
2
10.91
10.97
10.95
10.98
10.94
3
10.97
10.91
10.94
10.95
10.93
4
10.92
10.94
10.95
10.95
10.93
5
11.02
10.96
10.92
10.98
10.99
6
10.92
10.94
10.93
10.98
10.95
7
10.98
10.91
10.96
10.90
10.93
8
10.96
10.93
10.94
10.93
10.96
9
10.94
10.93
10.97
10.96
10.95
10
10.91
10.95
10.93
10.96
10.92
11
10.94
10.94
10.98
10.94
10.97
12
10.97
10.95
10.93
10.92
10.98
13
10.99
10.95
10.95
10.95
10.96
14
10.93
10.97
10.94
10.92
10.93
15
11.02
10.98
10.97
10.96
10.91
16
10.95
10.95
10.93
10.94
10.93
17
10.96
10.95
10.97
10.99
10.95
18
10.97
10.97
10.93
10.95
11.01
19
11.00
10.93
10.95
10.96
10.96
20
10.95
10.92
10.92
10.98
10.93
21
10.95
10.94
10.95
10.96
10.97
22
10.92
10.97
11.0
10.94
10.94
23
10.95
10.94
10.93
10.96
10.95
24
11.00
10.99
10.90
10.94
10.98
25
10.94
10.92
10.96
10.93
10.96
请进行Cpk分析。