模具毕业设计基于UG的齿轮注塑模设计.docx
《模具毕业设计基于UG的齿轮注塑模设计.docx》由会员分享,可在线阅读,更多相关《模具毕业设计基于UG的齿轮注塑模设计.docx(21页珍藏版)》请在冰豆网上搜索。
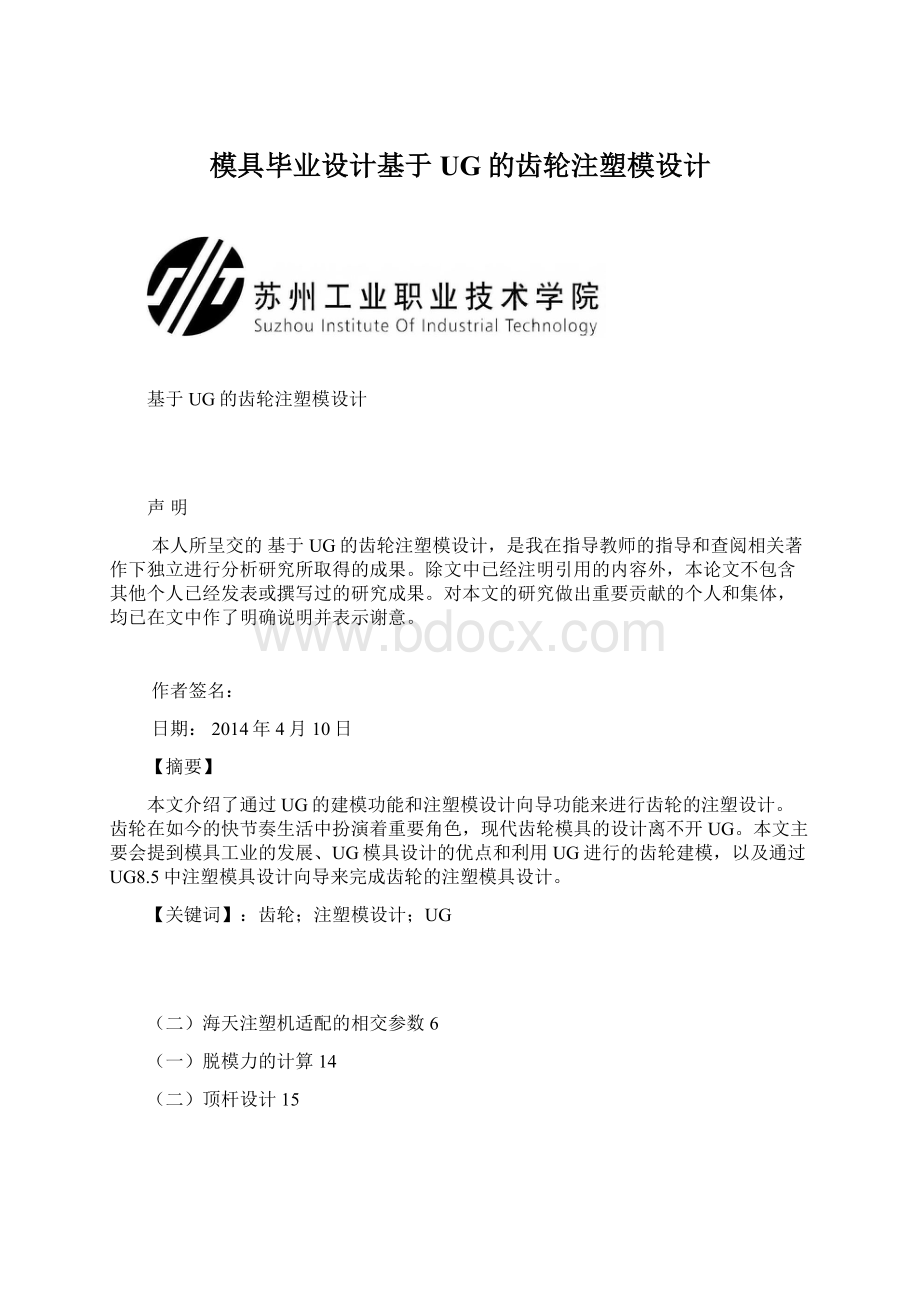
模具毕业设计基于UG的齿轮注塑模设计
基于UG的齿轮注塑模设计
声明
本人所呈交的基于UG的齿轮注塑模设计,是我在指导教师的指导和查阅相关著作下独立进行分析研究所取得的成果。
除文中已经注明引用的内容外,本论文不包含其他个人已经发表或撰写过的研究成果。
对本文的研究做出重要贡献的个人和集体,均已在文中作了明确说明并表示谢意。
作者签名:
日期:
2014年4月10日
【摘要】
本文介绍了通过UG的建模功能和注塑模设计向导功能来进行齿轮的注塑设计。
齿轮在如今的快节奏生活中扮演着重要角色,现代齿轮模具的设计离不开UG。
本文主要会提到模具工业的发展、UG模具设计的优点和利用UG进行的齿轮建模,以及通过UG8.5中注塑模具设计向导来完成齿轮的注塑模具设计。
【关键词】:
齿轮;注塑模设计;UG
(二)海天注塑机适配的相交参数6
(一)脱模力的计算14
(二)顶杆设计15
引言
当今世界上,模具工业发挥了它无与伦比的作用,人们生活的方方面面都离不开它。
在模具市场中,注塑模具的需求量相当大。
随着人们低碳生活的提倡,工程塑料成为近些年来模具发展的重点方向。
工程塑料包括聚苯硫醚、聚甲醛、PBT等等。
工程塑料具有优异的耐热性、耐磨性、耐腐蚀性等。
工程塑料比金属材料轻,加工成型容易,可替代一些金属做为结构材料使用。
近年来,工程塑料被广泛应用于电子、汽车、办公、医疗设备等领域。
在这一领域,我们国家相比较发达国家还存在一定差距。
我国面临着相关材料及制造技术的落后、模具产业链推广不够完善、人才培养不足和国家及地方政策的扶持力度不够等诸多问题。
随着信息化社会的不断展,软件的完善和智能化水平的提高,模具制作中3D设计将发挥不可替代的作用。
相比90年代CAD/CAM技术较高的价格与硬件需求,今后的模具造价随之降低。
并且,近些年来在大小企业中得到进一步的推广。
伴随着网络的发展与技术的积累,将改变传统的生产制造方式,解决无法实际分工协作等诸多问题。
目前UG的主要功能在于产品设计、工业设计布局、模具设计、NC编程加工等方面。
随着UG功能的不断完善,UG完成了与众多数控机床的无缝连接。
使得企业在产品设计、开发、制造的时间、成本大大降低,并缩短了产品研发周期。
一、注塑件的材料选择
(一)材料的选择
从塑件的用途出发,考虑到为减速马达齿轮箱内部齿轮,所以需要有较高的强度和硬度、并且不易磨损,容易成型加工等要求,结合考虑其加工性能、物理和化学性能来选取。
本次注塑材料选择为热塑性塑料。
在市场上的众多材料中,分析和比较后,选择PE6(聚酰胺6或者尼龙6)。
其性能分析如下:
1.一般性能
PE6无毒、无味、冲击强度高、表面不易磨损、成型熔点较低。
2.力学性能
优异的强度和耐久性,优良的刚性和耐热性,适用于齿轮及轴承的制造。
3.热学性能
极高的热稳定性,能在高达270度的波峰焊锡中不挂锡。
4.电学性能
电绝缘性很好,几乎不受温度、湿度和频率的影响。
5.化学性能
不易被化学品腐蚀
(二)PE6材料的介绍
PE6又名尼龙6或者聚酰胺6。
性状表现为半透明或者不透明乳白色结晶形聚合物。
其特点包括:
热塑性、轻质、任性好、耐化学品和耐久性好。
具有良好的耐磨性、自润滑性和耐溶剂性。
由于它易于成型及加工,广泛应用于制造轴承、圆齿轮、凸轮、伞齿轮、泵叶轮等。
。
PE6很容易吸收水分,因此加工前的干燥特别需要注意。
PE6工艺性良好,融化温度在230-280℃。
PE6对模具的温度要求在80-90℃,模具温度有益于结晶度的提高,而结晶度又影响着塑件的机械特性。
对于结构部件来说结晶度很重要,因此建议模具温度80-90℃。
成型温度过高,会破坏其成分,导致材料出现分解。
对于薄壁的,流程较长的塑件建议使用较高的模具温度。
增大模具温度可以提高塑件的强度和刚度。
PE6塑料也许多缺点,如不耐高温、易燃、加工过程中容易吸水、成型时凝固时间相对较短等等。
尽管这样,PE6塑料仍然为一种良好的工程材料。
本广泛应用于汽车内饰部件、发动机周边部件、高压油管等建构性领域。
二、注塑件的工艺分析研究
(一)注塑件外形分析
产品为圆形规则零件,其精度和表面粗糙度要求不是很高,但因为整个体积较大,所以需要注射力较大的注射机。
因为零件整体规则且分型面处较厚,所以受力较均匀且顶出时不易损伤产品。
没有复杂的曲面,易加工。
所以选择浇口位
置在零件表面。
图2-1齿轮三维图
图2-2齿轮二维图
(二)注塑件的体积和质量的计算
PE6材料的平均密度为1.36g/cm³,平均收缩率为1%到1.5%。
首先,画出三维图,点击UG分析功能计算体积。
图2-3为UG中的计算结果:
图2-3
通过计算风扇产品的体积V塑=2075439.6012mm³,所以质量为M塑=ρV塑=1.05g/cm³×2075439.6012/1000cm³=2189.711g(式子中ρ塑料密度g/cm³)
浇注系统凝料大体按照塑件体积的0.2-1倍。
如图2-4、图2-5分别为流道侧视和流道俯视,浇注系统凝料为0.5倍塑件体积,所以如下可得:
V浇=V塑×0.5=2075439.6012/1000cm³×0.5=1037.719cm³
可计算出浇注系统质量为:
M浇=ρV浇=1037.719×1.05=1089.604g
因为一模一腔,所以V总=V塑+V浇=3113.158cm³、M总=M塑+M浇=3279.026g。
图2-4流道侧视图2-5流道俯视
三、模架的分析与选用
根据《新编塑料模具设计手册》,对塑件进行分析以及考虑到注塑机规格要求,选用细水口模架,模架各模板以及尺寸如图所示。
模架各板厚度表
综上,模具的总厚度为:
H总=50+35+66+110+120+30=411mm。
四、注塑机的选定与校核
(一)注塑机的选定
以上是海天注塑机参数
目前注塑行业一般选用螺杆卧式注塑机,在设备的考虑上,我们应该主要考虑注射量、顶出行程、锁模力。
根据初步估算出来的注射塑料总质量V总=2075.439cm3,V机=V总/0.8得V机=2075.439/0.8=2594cm3.。
根据以上计算,初步选定注射机注射量为2594cm3。
根据塑件的体积初步选设备为海天HTF3431卧式液压式注塑机。
其主要技术规格见海天注塑机参数。
(二)海天注塑机适配的相交参数
1.模具定位环的尺寸
应随着塑机不同而改变一般情况下,360Ton 以下塑机注塑的模具,定位环尺寸为φ100×20mm,360Ton 以上塑机注塑的模具,定位环尺寸为φ150×20mm
2.模具的顶出孔尺寸
常用国产塑机,K、O孔排布如下图。
此图仅试用于海天注塑机
此图仅试用于海天注塑机
(三)注塑机校核
1.注射压力校核
P公为3000Mpa,P0为60~150Mpa,取P0=1300Mpa,其中P公为注塑机公称注射压力、P0为材料所需注射压力。
K=1.1~1.3,取1.2,其中K为注射压力安全系数。
所以KP0=3300,小于P公,所以合格。
2.最大注塑量校核
制件和浇口凝料总体积需要小于最大注塑量的80%。
通过公式可得:
最大注塑量V+塑件体积V<浇注系统凝料V*80%
故V机=(2075.439+1037.719)/0.8=3891.4475cm³,满足要求。
3.模具型腔内膨胀力F胀
P腔为腔内平均计算压力值。
根据塑料种类、结构复杂度、模温等因素选择腔内熔体平均压力为P=40MPa,所以:
F胀=A总P腔=40
13266.5=530.66KN
F为900KN,其中F为注塑机的公称锁模力,安全系数为K2取1.2,所以可以知道K2F胀=630.792,小于F,所以该注射机锁模力合格。
4.锁模力校核A投=πr²=3.14
65²=45690.5mm2,其中A投为塑件在分型面上的投影面积。
由于浇注方向与分型面平行,所以A浇=0,其中A浇为流道凝料和浇口投影面积。
塑件和浇注系统在分型面上总的投影面积A总,所以:
A总=A投+A浇
5.模具安装尺寸的校核
模具厚度须满足以下条件:
其中
为注射机上最小模具厚度
=400mm
为所选的模具厚度
=600mm
为注射机上最大模具厚度
=1500mm
所选该注射机满足模具的安装尺寸要求。
6.开模行程的校核
因为要去取出注塑件,所以最大开模行程必须大于取件距离。
所以可以得到以下方程:
H1+H2+(5~10)
式中:
S为最大行程;H1为塑件高度;H2为顶出距离
其中H1为25mm,H2为15mm,所以25+15+10=50
所选注射机满足此项要求。
经过多项校核认证该注射机满足要求。
五、齿轮注塑模具部件的设计
(一)型腔数量的确定与分布
注塑机型腔数的确定与现代注塑机的规格、所要求的塑件质量、塑件的几何形状、塑件成本及交货周期等有关。
由于本次制件体积较大,制件最大投影面积达到1875439.6012mm²,整体体积为2075.439cm³,重量较重,考虑到模具整体体积不宜过大,所以选用一模一腔。
如图5-1
图5-1
(二)分型面及排气形式的确定
模具上用以选取塑件和凝料的可分离的接触表面成为分型面,是动模和定模的分界面。
注塑模具有一个或者多个分型面,分型面应该尽可能简单,以便于塑件的脱模和磨具的制造,同时分型面的位置位于塑件的断面轮廓最大处,分型面还应考虑型腔排气顺利、确保塑件质量、无损塑件外观等因素。
选择分型面时,应该遵循以下原则:
1.分型面的方向尽量采用与注塑机开模方向垂直的方向。
2.便于脱模,开模时使制件能够留在动模一侧,利于侧面分型和抽芯。
3.分析面一般开设在产品最大界面处。
4.尽可能使塑件留在动模一侧
所以制件分型面应选择在最大投影面处,塑件型腔留在动模处
排气方式的确定:
由于塑件较小,排气量小,因此采用分型面及推杆和推杆孔间的间隙排气。
(三)型芯和型腔的结构设计
成型塑件外表面或者上表面的零件称为凹模或者型腔。
凹模按结构形式可分为整体式、整体嵌入式、局部镶嵌式、组合式等。
依照制件的造型,采用整体式,简化了复杂成型零件的加工,减少了热处理变形。
其中有以下几点好处:
1.便于各个流程的加工,由于整个注塑件整体体积较大,所对应的需要的型芯和型腔也相应增大。
在加工过程中,不便于电火花、加工中心、磨床等加工制造。
所以分割开来便于加工制造。
2.将整体分开后,各部件之间可开排气槽,便于排气。
使得在生产中不易出现烧伤的情况。
3.减少了后期热处理的变形。
(四)凸凹模的尺寸设计
根据在项目初始化中ABS材料的收缩率和注塑模向导中的工件功能,进行模具凸凹模的尺寸设计。
在UG中具体操作如图5-8、图5-9所示
图5-8图5-9
六、浇注系统的设计
(一)流道设计
1.主流道设计
由于该塑件你用卧式注塑机,因此主流道为锥形流道。
由于主流道要与高温的塑料熔体和喷嘴反复地接触和碰撞,容易随坏,所以模具的主流道通常设计成
可拆卸与更换的衬套结构。
为了节省材料,定位环与主流道衬套分开设计。
如上图所示。
主流道影响制件的填充时间和流速。
太小,相对增加了冷却面积,加大热能消耗和注射压力损失,太大浪费材料。
所以,取值如下:
如图6-1所示,为主流道选择步骤:
图6-1主流道选择步骤图
2.分流道设计
分流道的设计要点:
分流道要短,而且光滑,弯折少,体积小。
使得其流动过程中要少消耗温度,少损失压力。
相对于注塑件产品,要晚固化,从而来使得保压和补缩过程中,压力能够正常传递。
在熔料进入型腔时,能够均匀快速。
分流道的布置:
因为制件为圆形对称结构,三个分流道的长度、截面形状、尺寸都相同。
各个浇口尺寸也相同,从而达到注塑时的同时均衡进料。
所以本塑件的分流道采用了平衡式布置,梯形结构。
如图6-2是在UG中的步骤。
图6-2分流道选择步骤图
(二)浇口设计
因为塑件为圆盘形对称结构,制件整体尺寸较大,考虑到分型需要,所以设计浇口采用点浇口,点浇口锥角一般为
-
,这里取30°,倾斜角取2°,进料口直径d1取1.2,浇口长度为60mm。
下图6-4、图6-5分别为UG中点交口选择截图和点交口三维截图:
图6-4点交口选择图6-5点交口三维图
七、冷却系统的设计
(一)冷却时间计算
通过分析可以得到,沉孔的厚实部分在模具的冷却过程中温度较高,所以此处的冷却管道应特别注意,使该处尽量靠近进水口。
查阅《塑料模具技术手册》可得PE6材料冷却时间与壁厚的关系,即如表7-1所示。
表7-1PE6材料壁厚与冷却时间
材料
PE6
制件壁厚(mm)
0.8
1.0
1.3
1.5
1.8
2.0
2.3
2.5
3.2
冷却时间(s)
1.2
2.4
3.7
4.5
7
8.9
9.8
12.3
21.5
根据上表,本塑件材料为PE6,壁厚为2.5mm,故冷却时间为9.8-21.5s。
(二)冷却回路的设计
本次设计采用并联直通式冷却水管,不会与其他零件产生干涉。
冷却水管之间由外部橡胶水管连接,使之能够形成回路。
在UG中的步骤如图7-1所示:
图7-1冷却回路选择步骤
八、脱模推出机构的设计
(一)脱模力的计算
推出部分的设计计算在很大程度上与塑件的脱模力有关,因此在设计计算之前就必须先设计塑件的脱模力,塑件脱模力属于薄壁(
,其中
为塑件壁厚,d为塑件直径),脱模力公式:
记过计算最终脱模力为1667N
(二)制件采用的是推杆脱模机构
该机构是最简单、最常用的一种脱模形式,制造简单、方便更换、推出效果好等特点。
推杆直接与塑件接触,开模后将塑件推出。
推出行程一般为顶出制件使其能够脱离模具5~10mm,所以模具的推出距离为10mm。
根据模架各板长度,使用长度为182.5mm,直径为5mm的顶杆和长度为167.5mm直径为4mm的顶杆。
采用H8/f7~H8/f8的间隙配合。
(二)推出机构的导向与复位
复位杆上添加弹簧来实现。
推出机构的导向采用在动模座板上固定四个导柱来实现,复位杆的大小为是直径20mm,长度是190mm。
九、合模导向机构设计
导向结构设计
该模具的设计主要采用导柱和导套,然后导柱分布在模具四周,采用对称不等径布置;导柱导套的材料为T8碳素工具钢,热处理方式为淬火,配合面的Ra值要求为4μm,而固定部分的Ra值要求为0.8μm;导柱的滑动配合精度为H7/g6的间隙配合,导柱部分的配合精度按H7/k6过渡配合;并用直径为6mm的紧固螺钉固定。
在凸凹模以及别的零件对插过程中,合模导向机构起到定位作用,避免零件发生碰撞和干涉。
本次设计中采用的是导柱导向,导柱和导套的均采用标准件。
为了推出和复位过程中有较好的稳定性,所以在推板上增加推板导柱和推板导套。
总结
本次毕业设计使我发现我确定个人今后的发展方向。
经过黄洪根老师的指导下,自己的毕业设计完成了,按时完成了学校和老师的任务要求。
本文介绍了通过UG的建模功能和注塑模设计向导功能来进行齿轮的注塑模设计。
在正真开始着手写了之后,才发现,自己需要掌握的知识还相当的多。
通过这次的毕业论文,自己学到了很多,一方面是学会了模具相关方面的很多知识,比如:
模架、流道、浇口等,并且很好得学会了自己动手查阅资料解决问题,另一方面自己熟悉了UG的使用和操作。
通过这次毕业设计,是我更加意识到了自己的不足。
参考文献
[1]齐卫东.塑料模具设计与制造[M].北京:
北京理工大学出版社,2007.
[2]周元康、林昌华、张海兵《机械设计课程设计》重庆大学出版社2004.09
[3]王章忠.材料科学基础[M].北京:
高等教育出版社,2005.1.
[4]吴宗泽、罗圣国《机械设计课程设计手册》高等教育出版社.2006.06
[5]洪慎章.实用注塑模具结构图册[M].上海:
上海交通大学出版社,2006.
[6]申开智《塑料成型模具》(第二版)化学工业出版社2005年
[7]翁其金《塑料模具成型技术》机械工业出版社2005年
致谢
经历了这么久,论文终于完成了。
在此,回顾到自己三年学习期间的日子,感慨万千。
自己即将离开学校,踏上社会。
在此我需要感黄洪根老师。
在毕业设计论文写作时,遇到了种种问题,都是黄老师帮助了我,为我答疑解惑,知道我毕业设计的要点。
季老师工作认真踏实,解决问题时一针见血,绝不拖泥带水,使我学习到了很多做人做事方面的东西。
非常感谢学校的领导,感谢黄洪根老师,他为我做毕业论文提供了条件。
在做论文的过程中,我遇到了许多苦难,但在黄老师的帮助下,我的课题的设计任务得以顺利完成。
他严谨的治学态度和踏实的工作作风给我留下了很深刻的印象,是我学习的榜样。
在以后的工作和学习中自己一定加倍努力,才不会愧对大家的帮助和关心。