模具毕业设计螺钉直角固定铁架模具设计.docx
《模具毕业设计螺钉直角固定铁架模具设计.docx》由会员分享,可在线阅读,更多相关《模具毕业设计螺钉直角固定铁架模具设计.docx(26页珍藏版)》请在冰豆网上搜索。
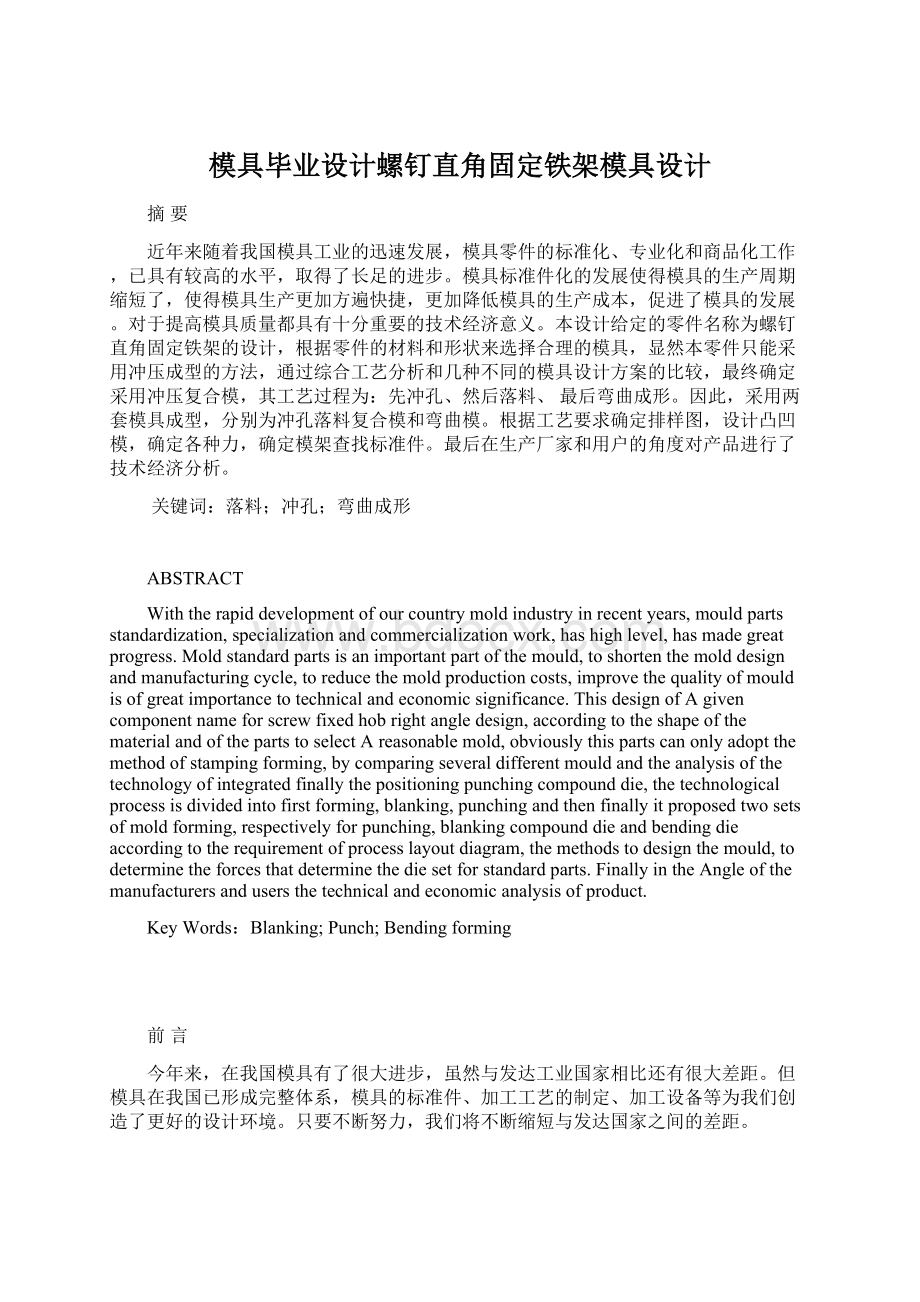
模具毕业设计螺钉直角固定铁架模具设计
摘要
近年来随着我国模具工业的迅速发展,模具零件的标准化、专业化和商品化工作,已具有较高的水平,取得了长足的进步。
模具标准件化的发展使得模具的生产周期缩短了,使得模具生产更加方遍快捷,更加降低模具的生产成本,促进了模具的发展。
对于提高模具质量都具有十分重要的技术经济意义。
本设计给定的零件名称为螺钉直角固定铁架的设计,根据零件的材料和形状来选择合理的模具,显然本零件只能采用冲压成型的方法,通过综合工艺分析和几种不同的模具设计方案的比较,最终确定采用冲压复合模,其工艺过程为:
先冲孔、然后落料、最后弯曲成形。
因此,采用两套模具成型,分别为冲孔落料复合模和弯曲模。
根据工艺要求确定排样图,设计凸凹模,确定各种力,确定模架查找标准件。
最后在生产厂家和用户的角度对产品进行了技术经济分析。
关键词:
落料;冲孔;弯曲成形
ABSTRACT
Withtherapiddevelopmentofourcountrymoldindustryinrecentyears,mouldpartsstandardization,specializationandcommercializationwork,hashighlevel,hasmadegreatprogress.Moldstandardpartsisanimportantpartofthemould,toshortenthemolddesignandmanufacturingcycle,toreducethemoldproductioncosts,improvethequalityofmouldisofgreatimportancetotechnicalandeconomicsignificance.ThisdesignofAgivencomponentnameforscrewfixedhobrightangledesign,accordingtotheshapeofthematerialandofthepartstoselectAreasonablemold,obviouslythispartscanonlyadoptthemethodofstampingforming,bycomparingseveraldifferentmouldandtheanalysisofthetechnologyofintegratedfinallythepositioningpunchingcompounddie,thetechnologicalprocessisdividedintofirstforming,blanking,punchingandthenfinallyitproposedtwosetsofmoldforming,respectivelyforpunching,blankingcompounddieandbendingdieaccordingtotherequirementofprocesslayoutdiagram,themethodstodesignthemould,todeterminetheforcesthatdeterminethediesetforstandardparts.FinallyintheAngleofthemanufacturersandusersthetechnicalandeconomicanalysisofproduct.
KeyWords:
Blanking;Punch;Bendingforming
前言
今年来,在我国模具有了很大进步,虽然与发达工业国家相比还有很大差距。
但模具在我国已形成完整体系,模具的标准件、加工工艺的制定、加工设备等为我们创造了更好的设计环境。
只要不断努力,我们将不断缩短与发达国家之间的差距。
随着工业产品质量的不断提高,冲压产品生产正呈现多品种、少批量,复杂、大型、精密,以及更新换代速度快等特点。
冲压模具正向高效、精密、长寿命、大型化方向发展。
在我国模具的起步较晚,虽然目前不能与国际水平相比较,但已有长足进步,我们正在不断提高产品的质量、降低缩小产品成本同时兼顾模具的开发生产更新换代的新型模具。
今年来,很多模具企业为了生存,引进了CAD、UG、Pro/Engineer、I-DEAS等国际上比较常用的软件设备,并成功应用于冲压模的设计中。
1.1国内冲压模具的现状和发展趋势
1.1.1冲压模具的现状概括
在我国,曾很早的时候就已经出现模具了。
比如活字印刷技术就是很好的例子,只是人们没想到将这些重要技术运用到工业生产,加上封建思想一直未形成产业,改革开放才是我国模具进入飞跃发展的重大时期,虽然中国冲压模具工业发展迅速,但仍有许多需要改进的地方。
近年来我国模具数量已有很大规模,制造水平也有很大提高,但设计制造水平总体上落后许多制造业大国。
当前我国模具制造业存在很多缺点:
(1)总量供不应求
(2)企业的制造结构、零件的结构、生产的条件和进出口的比例均不合理
在我国模具生商业化模式低,企业自产自用比例高达60%左右,而国外商品化模具程度高。
模具复杂,精度高。
2005年,模具的进出口之比例是3.2:
1,进出口相差较大,使得我国浪费大量资金进口模具,是世界模具进口量非常大的国家。
(3)模具生产零件水平远远低于国际产品水平,生产产品制造周期却高于国际生产水平。
我国高精尖模具级技术人员相对较少,对于产品的开发没有投入大量精力,在模具生产市场中处于欠发达的被动地位。
模具人员创造价值远不能与发达国家相比。
(4)工艺装备水平低,且配套性不好,利用率低
我国模具的总体现况不是很好,从各个反面来讲我们都有继续为国家的模具事业多做贡献,环境在不断变化,我们的生产条件越来越好,我国的模具制造说平将不断上涨,中奖超越国际水准。
1.1.2冲压模具的发展趋势
中国冲压模具生产要尽量提高生产能力,更重要的是着重于行业内部结构调整和技术发展水平提高。
结构的调整方向,主要是企业的结构化向专业化方向调整,产品的结构向着更进一步模具制造发展,促进产业升级,发展技术,向高精密模具靠拢,缩短与发达国家之间的差距。
第一章螺钉直角固定铁架产品介绍
1.1螺钉直角固定铁架产品介绍
该产品是为某公司设计的产品,常用于书柜、橱柜、办公桌等处,厂商要求大批量生产,价格便宜,制造精度不高,结构相对简单,如图2.1、2.2所示。
图2.1螺钉直角固定铁架零件图
图2.2螺钉直角固定铁架成品
1.2螺钉直角固定铁架的加工工艺性分析
模具的产品加工工艺性是指冲压件对冲裁加工的适应性,即加工是否有难度。
本产品材料选用Q235,不是很硬,可以使用冲孔落料弯曲等操作,外官为一个矩形和圆孔组成。
从尺寸上看33mm、33mm、3mm在冲压加工范围内,精度要求不高,主要为IT13级,常用的冲压设备完全适应。
第二章冲孔落料复合模的设计
2.1零件图分析
2.1.1零件的外形及精度分析
该零件形状简单、是由平面和圆孔组成,总体结构呈对称特征,制件中心就是模具中心。
零件的制造精度不高,中心距精度较高,其余为IT13级要求,普通的冲压及弯曲均能达到精度要求。
2.1.2零件的加工方案确定
一般冲裁件内外形所能达到的经济精度为IT11~14。
将以上精度与该零件的精度要求相比,我认为此零件的精度要求能够通过冲压加工得到保证,且其他的尺寸标注、生产的批量等情况,也都符合冲裁加工要求,因此采用冲压方式获得冲孔落料件,然后再进行弯曲后得到制件。
由于此工件属于L型弯曲,弯曲模没有固定的结构形式,可以设计很简单,也可以设计很复杂,这需要根据工件的材料性能、形状、精度要求和产量等进行综合考虑,确定模具的具体结构形式。
本工件零件图中所示尺寸公差为未注公差,在处理这类零件公差的等级时均按IT13级要求,故此件形状、尺寸、精度均能满足弯曲工艺要求,可采用弯曲工序加工。
图示零件材料为Q235号钢板,能够进行一般的冲压加工,市场上也容易得到这种材料,价格适中。
由工件图可知:
该工件既有冲孔落料又有弯曲,但工件上的的孔、槽是对称的,总的来说加工起来是容易的。
由以上的分析情况我得到该零件比较适合冲压生产,生产工艺条件不难。
2.2冲压工艺方案的确定
从外形看此零件需要冲孔落料和弯曲三个重要工序,我想到以下三种工艺方案。
第一种方案:
先冲孔,再落料,最后弯曲,采用三道工序模进行生产。
第二种方案:
冲孔、落料,再弯曲。
采用两道工序模具进行生产。
第三种方案:
冲孔、落料、弯曲级进冲压成形。
采用级进模生产。
第一种方案模具结构相对简单,可是这需要三道工序三副模具,成本高而且生产效率不高,不利于满足生产批量的加工要求。
第二种方案共需要两副模具,第一使用一套模具进行冲孔落料生产,第二使用一套模具进行弯曲成形形成零件。
工件的加工精度和生产的效率都比较高,易于批量的生产,模具的强度适中,制造的难度相对小,冲压结束后,在清理模具上的物料上,只需要手动将制造的零件取下,最后的一道弯曲将制件彻底成型使其满足要求。
方案三只需要一副模具,生产效率高,但操作不方便,送料速度较快。
通过对上述三种方案的分析比较,该件选择第二种方案较为合适。
冲压生产采用该方案为最佳。
在此,首先通过使用一套冲孔落料正装复合模对下好的坯料板进行冲孔落料,形成下图2.3所示的半成品坯料,然后将其作为半成品坯料再用一套弯曲模对其进行一次弯曲成形,达到制件要求形状如下图2.4所示。
图2.3半成品坯料图2.4零件成型
2.3必要的工艺计算
2.3.1产品展开尺寸设计与计算
结合制件尺寸可知:
由于弯曲变形时不仅弯曲圆角部分变薄严重,同时影响与边缘相接处的直边部分,使得直边有变薄使得趋势,所以应该按照变形前后中性层长度不变的条件来计算板件的长度。
图2.5中性层长度
1)当R=0,折弯角θ=90°(T<1.2,不含1.2mm)
L=A+B+K式(2.1)
=A+B+0.4T
上式中取:
λ=T/4
K=λ*π/2
=T/4*π/2
=0.4T
2)当R=0,θ=90°(T≧1.2,含1.2mm)
L=A+B+K式(2.2)
=A+B+0.5T
上式中取:
λ=T/3
K=λ*π/2
=T/3*π/2
=0.5T
3)当R≠0θ=90°
L=A+B+(R+λ)*π/2式(2.3)
当R≧5T时λ=T/2
1T≦R<5Tλ=T/3
0(实际展开时除使用尺寸计算方法外,也可在确定中性层位置后,通过偏移再实际测量长度的方法)
经计算:
L=30+30+0.5*3
=62.345
取L=61.5mm
2.3.2排样的设计
设计复合模时,首先要设计条料排样图。
根据工件的形状选择有废料排样,且为直排的形式,虽然材料的利用率低于少废料和无废料排样,但工件的精度高,且易于保证工件外形的圆角。
2.3.3确定搭边值
为了确保冲裁件质量,排样中各工件与料边之间、工件与工件之间留下的余量,称为搭边。
在此处根据课本表2.9最小搭边值,取得工件间a1=2.5mm,a=3.0mm。
2.3.4确定零件的排样方案
对于设计冲孔、落料复合模,开始就要设计零件排样图。
冲压件在条料、带料和板料上的排列方式,称为冲裁件的排样,简称为排样。
合理的排样应是在保证制件质量、有利于简化模具结构的前提下,以最少的材料消耗,冲出最多数量的合格工件。
底座的形状简单,由于零件外形尺寸为自由尺寸对精度要求不高,为了提高材料的利用率减少冲裁力,虽然这时会使零件外形尺寸公差等级降低但是经过等筹兼顾,全面考虑。
这里我们采用有废料排样。
如图2.6所示:
图2.6排样
2.3.5计算送料的步距和条料的宽度
有课本2.33得送料步距A=D+a1
其中D——横向的冲裁件宽度
a1——冲裁件之间的搭边值
故A=D+a1=30+2.5=32.5mm
模具采用无侧压装置的导料方式,条料宽度由课本公式3.36得
条料宽度D=Dmax+2a
其中B——条料宽度
Dmax——冲压件垂直于进给方向最大尺寸
a——侧搭边的最小值
故D=61.5+3×2=67.5mm
图2.7步距
2.3.6计算材料的利用率
式(2.4)
式中S1—一个布距内零件的实际面积;
S2—一个布距内所需毛坯面积;
送料布距为32.5mm
条料宽度为67.5mm
代入已知数据,可得一个步距的材料利用率
:
2.4计算冲压力和初选压力机
2.4.1计算凸、凹模刃口尺寸
冲尺寸为6mm的孔对应凸、凹模刃口尺寸的计算
查表2.4得间隙值Zmin=0.46mm,Zmax=0.64mm。
表2.1冲裁模初始双面间隙Z(mm)
材料厚度
08、10、350
Q345
40、50
65Mn
9Mn、Q235
Cmin
Cmax
Cmin
Cmax
Cmin
Cmax
Cmin
Cmax
小于0.5
极小间隙
0.5
0.04
0.06
0.04
0.06
0.04
0.06
0.04
0.06
1
0.1
0.14
0.1
0.14
0.1
0.14
0.09
0.126
2
0.246
0.36
0.26
0.38
0.26
0.38
2.5
0.36
0.5
0.38
0.54
0.38
0.54
3
0.46
0.64
0.48
0.66
0.48
0.66
3.5
0.27
0.54
0.74
0.58
0.78
0.78
4
0.64
0.88
0.68
0.46
0.34
0.46
因为制件结构简单,加工精度要求不是很高,所以采用凸模、凹模分别加工的方法制造凸、凹模。
其凸、凹模刃口尺寸的计算如下:
查表2.5得凸、凹模制造公差:
δ凸=-0.020mm,δ凹=+0.025mm
校核:
Zmax-Zmin=0.18mm,而δ凸+δ凹=0.0450mm
满足δ凸+δ凹<Zmax-Zmin,故而采用分别法制造模具刃口。
工件图中未标注公差值,查相关文献可得尺寸为6mm的工件公差值分别为△=0.18mm。
查表2.6得IT13级时的磨损系数x=0.75
所以按式(2.5)可得:
式(2.5)
式(2.6)
(2)模具的外形落料凸、凹模刃口尺寸的计算
从冲裁件的外轮廓落料,形状相应也比较简单,当以凹模为基准件时凹模磨损后,刃口部分尺寸都变大,因此属于A类尺寸。
对于外形尺寸分别为61.5mm和30mm,所以通过查相关文献可查得其对应公差分别为:
0.46mm,0.39mm。
按公所以式:
Aj=(Amax-x△)
可求得:
式(2.7)
凸模落料的基本尺寸与凹模相同,分别是61.155mm、29.7075mm,不必标注公差,不过要在技术要求中备注:
凸模的刃口实际尺寸与落料凹模配制,保证凸模与凹模的最小合理间隙值Zmin=0.46mm。
2.4.2冲压力的计算及压力中心的确定
(1)冲压力的计算
该制件首先是采用冲孔落料正装复合模,拟选用弹性卸料上出料。
冲压力的相关计算如下:
冲裁力F:
F=KLt
式(2.8)
式中:
F—冲压力(KN);
L—冲压件的周边长度(mm);
t—冲压件的材料厚度;
—被冲材料的抗剪强度(MPa);
K—系数,一般取1.3.
在一般情况下,材料的抗剪强度
=1.3
,为方便计算,也可按下式进行估算冲裁力F=1.3Lt
≈Lt
式中
—被冲裁材料抗拉强度(MPa)
查手册【3】得Q235钢的
为235Mpa.
F=1.3Lt
=1.3×(183+18.84*6)×3×235=271.32KN
由于此处采用的是弹性卸料装置和下出料的冲孔、落料倒装复合模,所以其冲裁工序总力的计算公式为:
F总=F+FX+FT式(2.9)
查表2.7取KX=0.035KT=0.045
FX=KXF=0.035×271.32KN=9.496KN
FT=nKTF=2×0.045×271.32KN=24.4KN
所以FZ=F+FX+FT=271.32+9.496+24.4=305.23KN
(2)压力中心的确定
对于这个相对称的零件来将,压力中心很好确定。
首先冲压件为矩形,压力中心在对角线上,上面有六个孔,它们三个各在零件的一般,这样看的话也是对称的,因此六个孔的对称中心也在中心,与矩形的压力中心重合。
将两个综合考虑,很好确定压力中心。
此零件是比较简单的对称零件,在这里就不写出找压力中心的具体方法。
压力中心的计算公式如下:
X0=(L1X1+L2X2+……LnXn)/(L1+L2+……Ln)式(2.10)
Y0=(L1Y1+L2Y2+……LnYn)/(L1+L2+……Ln)
式中:
X0-压力中心横坐标值;
Y0-压力中心纵坐标值;
L-各线段的长度值;
X-各线段重心的横坐标位置;
Y-各线段重心的纵坐标位置。
分析本制件图可知,该图基本上关于X轴,Y轴对称,所以压力中心的坐标就取(0,0)。
图2.8压力中心
2.4.4初选压力机
有上述已知计算可知,选择型号为JC23—35型的开式双柱可倾压力机是比较合适的选择,它能满足制件的要求。
主要技术参数如下表所示:
表2.2JC23—35型压力机主要技术参数
公称压力/KN
350
滑块行程/mm
80
滑块行程次数/(次/min)
50
最大封闭高度/mm
280
封闭高度调节量/mm
60
滑块中心线至床身距离/mm
205
立柱距离/mm
300
工作台尺寸/mm(前后×左右)
380×610
工作台孔尺寸/mm(前后×左右×直径)
200×290×φ260
垫板尺寸/mm(厚度)
60
模柄孔尺寸/mm(直径×深度)
φ50×70
床身最大倾斜角(°)
30°
2.5模具的总体设计
2.5.1模具的类型选择
按照复合模工作零件的安装位置不同,分为正装式复合模和倒装式复合模两种,两种的优点、缺点及适用范围见下表:
表2.3正装式复合模和倒装式复合模它们的优点、缺点及适用的具体范围
比较项目
正装(顺装)式复合模
倒装式复合模
结构
凸凹模装在上模,落料凹模和冲孔凸模装在下模
凸凹模装在下模,落料凹模和冲孔凸模装在上模
优点
冲出的冲件相对位置精度较高
结构较简单
缺点
结构复杂,冲件容易被嵌入边料中影响操作
不宜冲制搭边值较小的零件
适用范围
冲制精度较高,相对位置精度要求较高的零件,还主要用于冲压搭边值较小的零件。
倒装式复合模具是我们比较喜欢和常用的装配方式,它的结构特点适用冲压简单零件,卸料容易,精度要求不高,高工效率高
通过对正装式复合模和倒装式复合模两种优点、缺点及适用范围的分析比较,正装式复合模适合于冲制精度较高,位置精度要求较高的零件,还主要用于冲压搭边值较小的零件。
倒装式复合模不宜冲制孔边距离较小的冲压件,倒装式模具结构简单,并且直接利用压力机打杆装置进行卸料,操作方便,并为零件生茶件创造了有利条件,故应用十分广泛是我们最想到和最想使用的模具结构。
综上所述,该制件结构形状简单,精度要求较低,搭边值足够,不会影响制件的质量问题,所以采用倒装式复合模。
倒装模其上模部分由上模座、打料板、垫板、凸模固定板、凸模及落料凹模等零件组成,下模部分由凸凹模、凸凹模固定板、弹性卸料板、垫板、下模座等组成。
2.5.2定位方式的选择
因为是批量生产,采用手动送料方式,从右往左送料;又因为该制件采用的是倒装复合模,所以直接用挡料销和导料销即可。
2.5.3导向方式的选择
为确保零件的质量及稳定性,选用导柱、导套导向。
又根据制件尺寸及精度要求等采用后侧导柱模架。
2.6模具的主要零部件的结构设计
2.6.1凸模、凹模、凸凹模的结构设计
1.对于落料凸、凹模的设计在落料凹模内部,因为要设置推件块,使得制件容易卸下,所以凹模刃口使用直通型刃口,经查表2.21得到刃口高度h=13mm。
根据凹模特点,在这里采用整体式。
又查表2.22,得k=0.35
即凹模高度
H=ks=0.35×61.5mm=21.525mm式(2.11)
取H=35mm
垂直于送料方向的凹模宽度B
B=s+(2.5~4.0)H=117.5~170mm式(2.12)
送料方向上的凹模长度L
L=S1+(2.5~4.0)H=61.5+(2.5~4.0)H=149~201.5mm式(2.13)
参照标准,在此取凹模外形尺寸为:
160mm×130mm×35mm
2.冲尺寸为6mm孔的凸模设计由于该零件内孔是圆形,它的固定方式是P7/h6的靠台固定;我将凸模镶嵌在凹模内,与凹模成间隙配合,再与凹模平面磨平,最后通过垫板将其固定。
其长度计算如下:
L=h凸模固定板+h落料凹模=18mm+35mm=53mm式(2.14)
图2.9凸模
由于此凸模尺寸适中,且长度较短,刚强度足够,所以不需对其进行校核。
冲裁时注意进入凹模刃口2mm。
3.对于凸凹模的结构设计,凸凹模在模具中是主要的成型部件,它既对冲孔起作用,同时也负责落料的形成。
冲孔根据凸模尺寸计算,同时有圆形废料,所以下面孔比成型孔略大些,有利于自动落料。
同时起落料凸模的作用,所以落料根据凹模尺寸计算。
将零件冲入上模,需要保证与凹模的间隙,冲裁件通过打板卸下,凸凹模的结构简图应如图所示。
图2.10凸凹模
2.6.2模架的设计
上模座:
290mm×245mm×40mm
下模座:
2090mm×245mm×50mm
导柱:
28mm×220mm
导套:
28mm×100mm×
38mm
模柄:
44mm×80mm
垫板:
160mm×130mm×8mm
卸料板:
160mm×130mm×18mm
凸模固定板:
160mm×130mm×18mm
模具闭合高度:
H闭=H上模+H垫板×2+H凸凹模+H凹模+H垫板2+H固定板+H下模座-2式(2.15)
=40mm+8×2mm+54mm+35mm+30mm+18mm+50mm-2=241mm
第三章弯曲模的设计
3.1主要计算
3.1.1弯曲件回弹值的计算
由于回弹直接影响了弯曲件的形状和尺寸,因此,在模具设计和制造时,回弹是不可不考虑的因素,它对成型起至关重要的作用,如果计算不当甚至会造成弯曲机的损坏。
通常的方法是先根据经验数值和简单的计算以及制件的材质等,确定模具工作部分的尺寸后再试模修正相应部分的形状和尺寸。
小变形程度(r/t≥10)时,回弹比较大,先计算凸模圆角半径,再计算凸模角度;大变形程度(r/t<5)时,卸载后圆角半径变化小,仅考虑弯曲中心角的回弹变化。
弯曲此工件时,其弯曲中心角为90°,故而结合制件材料为Q235钢以及其相对弯曲半径为r/t=0.5、材