航空发动机涡轮叶片的故障分析DOC.docx
《航空发动机涡轮叶片的故障分析DOC.docx》由会员分享,可在线阅读,更多相关《航空发动机涡轮叶片的故障分析DOC.docx(23页珍藏版)》请在冰豆网上搜索。
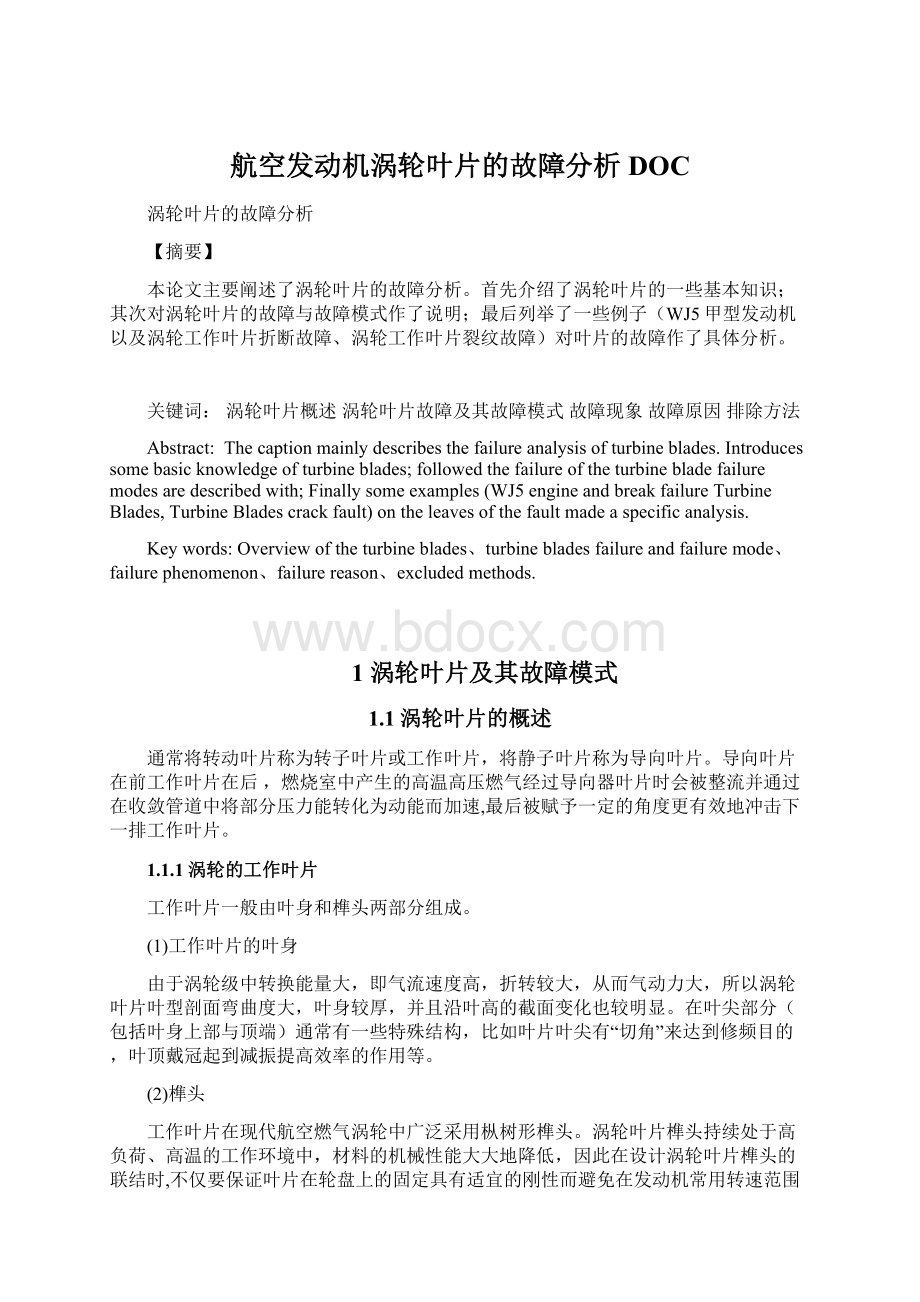
航空发动机涡轮叶片的故障分析DOC
涡轮叶片的故障分析
【摘要】
本论文主要阐述了涡轮叶片的故障分析。
首先介绍了涡轮叶片的一些基本知识;其次对涡轮叶片的故障与故障模式作了说明;最后列举了一些例子(WJ5甲型发动机以及涡轮工作叶片折断故障、涡轮工作叶片裂纹故障)对叶片的故障作了具体分析。
关键词:
涡轮叶片概述涡轮叶片故障及其故障模式故障现象故障原因排除方法
Abstract:
Thecaptionmainlydescribesthefailureanalysisofturbineblades. Introducessomebasicknowledgeofturbineblades;followedthefailureoftheturbinebladefailuremodesaredescribedwith;Finallysomeexamples(WJ5engineandbreakfailureTurbineBlades,TurbineBladescrackfault)ontheleavesofthefault madeaspecificanalysis.
Keywords:
Overviewoftheturbineblades、turbinebladesfailureandfailuremode、failurephenomenon、failurereason、excludedmethods.
1涡轮叶片及其故障模式
1.1涡轮叶片的概述
通常将转动叶片称为转子叶片或工作叶片,将静子叶片称为导向叶片。
导向叶片在前工作叶片在后,燃烧室中产生的高温高压燃气经过导向器叶片时会被整流并通过在收敛管道中将部分压力能转化为动能而加速,最后被赋予一定的角度更有效地冲击下一排工作叶片。
1.1.1涡轮的工作叶片
工作叶片一般由叶身和榫头两部分组成。
(1)工作叶片的叶身
由于涡轮级中转换能量大,即气流速度高,折转较大,从而气动力大,所以涡轮叶片叶型剖面弯曲度大,叶身较厚,并且沿叶高的截面变化也较明显。
在叶尖部分(包括叶身上部与顶端)通常有一些特殊结构,比如叶片叶尖有“切角”来达到修频目的,叶顶戴冠起到减振提高效率的作用等。
(2)榫头
工作叶片在现代航空燃气涡轮中广泛采用枞树形榫头。
涡轮叶片榫头持续处于高负荷、高温的工作环境中,材料的机械性能大大地降低,因此在设计涡轮叶片榫头的联结时,不仅要保证叶片在轮盘上的固定具有适宜的刚性而避免在发动机常用转速范围内出现危险共振。
榫头的形式和尺寸要避免存在过大的应力集中,榫头应便于安装,以保证叶片的修理和更换而且要特别注意允许榫头联结处受热后能自由膨胀,以减少热应力和榫头传热性要好,使叶片上的热量容易散走。
叶片榫头是一种多齿形结构,各隼齿间刚性的相对分布、材料的物理性能以及制造误差等都对各齿载荷的均匀性产生重要影响,一般齿数不宜过多。
1.1.2导向叶片
涡轮导向叶片是涡轮部件中温度最高和承受热冲击最厉害的零件,型面简单,数量多。
在铸造的分机匣内,由于机匣壁较厚,整流叶片可用各种形式的榫头直接固定在机匣内壁机械加工成的特形环槽内。
它与机匣的联接要保证可靠传力、定位和足够刚性,整流叶片与内环的联接要保证良好定位,密封和热补偿。
1.2涡轮叶片的故障模式
1.2.1涡轮叶片常见故障
叶片的故障和故障模式随不同的工作环境有所不同,常见的故障有:
裂纹断裂,强度不足和高低疲劳损伤,其中疲劳损伤较多。
(1)强度不足及其故障模式
叶片的强度不足故障是指工作时叶片某一断面或部位的应力超过材料的断裂应力而导致损伤。
这种故障多数是因叶片设计时裕度不足,受瞬态冲击载荷或者叶片截面内部留有残缺隐患所造成。
如叶片材质不良,工艺缺陷和环境影响等因素。
强度不足的故障模式有:
挠曲,变形,裂纹和断裂等。
(2)高周期疲劳损伤及其故障模式
叶片高周疲劳损伤即通常说的高循环应力疲劳损伤,其疲劳取决于两个因素,即叶片的疲劳应力水平和叶片的应力循环次数。
其还要取决于叶片振动应力水平的高低,应力高,循环次数自然要降低。
叶片的高周疲劳断裂部位多位于叶片的最大应力截面,叶片的最大应力截面与振型有关。
对于一阶弯曲振动,最大应力截面向叶尖上移,其断口走向通常是一条直线。
对于扭转振型与复合振型,其最大应力截面也随振型不同而不同。
对于高阶振型,最大应力截面也随阶次的增高向叶尖上移,其断口走向是先平后翘。
因此研究叶片的断裂部位与断口走向,都可以判断叶片属于何种振型的振动故障。
叶片的高周疲劳大都属于共振疲劳损伤,其排除方法不外乎是避开共振,即一是改变激振频率;二是改变叶片的固有频率(叶片调频)。
高周疲劳故障模式通常表现为裂纹和断裂。
(3)低周疲劳损伤及故障模式
叶片低周疲劳损伤也就是大应变疲劳损伤。
由于应力水平比较高,其损伤的疲劳循环次数比较低,一般循环次数N<103。
低周疲劳损伤多是由于叶片气弹失稳现象或叶片颤振现象所导致,故也称为颤振故障,它主要由气动力特性在特定条件下与叶片弹性耦合所确定。
叶片的低周疲劳损伤,其断口特征往往也有三个区域,裂纹的形成区与扩展区交织在一起,疲劳弧线比较粗糙,疲劳条带间距较大,表面粗糙。
这与高周疲劳断口有较明显的不同。
低周疲劳故障模式通常也表现为裂纹和断裂。
总之,叶片振动故障是发动机中属于多发性的具有极大危险程度的故障,其发作机理有时是比较复杂的,排故的方法也是多种多样的,是从事于发动机研究、设计、生产和维护者们应注意的问题。
2WJ5甲型发动机以及涡轮工作叶片折断故障
2.1故障现象
1991年5月30日,东方航空运七B3476号飞机由厦门返回南昌。
飞机滑入跑道请示起飞是,此时右发转速103﹪,排气温度440-460℃,发动机参数正常,接到起飞命令后,推油门过程中忽听一声闷响,右发转速急剧下降,立即停车。
1991年11月24日,太原航空运七12WJ5AI850086号发动机在太原空域油门从12°向22°推进时发出“咚”的闷响,扭矩压力降为零,振动极大,驾驶人员立即将油门从22°推向30°,扭矩压力不变,温度屑信号灯亮。
当即采取人工顺桨停车,单发着陆成功。
1991年12月10日,吉林局运七B3490号飞机在合肥准备起飞。
机械师将油门推至20°,此时右发(12WJ5AI850077号发动机)的T4温度为270°,振动值为0.6g,发动机工作参数正常。
随后在将油门推至26°的瞬间,右发突然发出“砰”的一声响,接着飞机剧烈振动。
机组迅速解除螺旋桨限动,关闭停车电门。
此时排气温度640℃,飞机单发滑回停机坪。
1992年1月17日,东方航空运七3458号飞机在南京机场起飞滑行过程中,左发12WJ5AI910311号发动机突然剧烈抖动,立即停车。
故障发生后,为保证飞机及人员安全,在没有查清故障原因及落实排故措施的情况下,运七飞机全部停飞。
2.2故障原因分析
2.2.1发动机分解检查
上述四台故障发动机在返厂分解检查时发现,12WJ5AI900248号一级发动机涡轮工作叶片全部折断,另外三台各有1片一级涡轮工作叶片折断(见图2-1),四台发动机的二、三级涡轮工作叶片、各级导向叶片及其他相关零件均受到不同程度损伤。
从故障现象基本可以判定四台发动机故障都是因一级涡轮工作叶片这段引起的。
图2-1折断叶片
2.2.2理化分析
(1)断口分析
为确定首断件,排除受害件,对四台发动机所有的断裂件进行断口分析。
经分析确认,四台发动机中各有1片一级涡轮工作叶片属于疲劳断裂,而其余断裂件均属于瞬间被动破坏。
观察这4片一级涡轮工作叶片的折断面,可以看到断口由形貌不同的两个区域组成(图2-2、3、4),分别为疲劳区和瞬断区,在每个疲劳区都存在严重缺陷,每个叶片缺陷具体情况及工作时间见表2-1。
图2-2断口低倍放大全貌图2-3主疲劳扩散区形貌
表2-1叶片缺陷情况及工作时间表
发动机号
叶片件号
工作时间/h
缺陷性质及状态
12WJ5AI900248
775.04.002
1219
断面上存在严重显微疏松和一个3.2mm×2.0mm的气孔
12WJ5A850086
775.04.001
2338
断面上存在一处2.5mm×2.0mm的氧化皮夹杂
12WJ5A850077
775.04.002
521
加强筋上存在一处2.2mm×1.8mm的夹砂
12WJ5A910311
775.04.002
556
断面上存在三处平坦的脆断区
需要说明的是,12WJ5AI910311号发动机叶片缺陷的形成于工艺过程中采用Sn-Bi合金定位后,叶片表面残留Sn、Bi元素有关。
Sn-Bi合金在叶片的工作温度下为液态,对叶片的材料—K405合金有致脆作用,因此其折断叶片的断口是脆断;而其余均属冶金缺陷,与铸造过程中偶然因素有关,因缺陷在X光检验的盲区而没有被发现。
同时断口上清晰可见疲劳条带,这些疲劳条带均起始于缺陷处。
通过断口分析可以判定,四起故障的肇事者均为带缺陷的一级涡轮工作叶片。
(2)材质分析
一级涡轮工作叶片是由K405合金真空精铸而成,每熔批均进行化学成分及力学性能检查并记录存档。
经检查故障件熔批的理化分析记录,其化学成分及力学性能符合验收技术条件,因此排出了材料力学性能不合格导致故障的因素。
(3)过热分析
经过四台发动机故障叶片金相检查,未发现γ′相聚集、长大、回溶现象,因而派出了金属过热导致故障的因素。
2.2.3台架动应力测试
为查明一级涡轮工作叶片在发动机全转速范围内是否有危险共振发生,进行了台架动应力测试,试验采用电测法进行,试验结果表明:
在发动机全转速范围内未发现一级涡轮工作叶片有危险的共振。
2.2.4结构应力计算分析
一级涡轮工作叶片为对分大圆弧齿带冠、伸根结构、叶身带7个径向冷却孔。
为躲开冷却孔进气口,伸根设计成与中心线成32º50'的夹角,在叶身重心下方设一加强筋。
鉴于四起折断故障的断裂部位均为伸根段,为了查明伸根段结构是否存在强度设计的薄弱区域,应用大型结构应力分析计算程序对伸根段进行了三维有限元弹性应力分析。
计算状态:
取最大载荷状态即起飞Ⅱ状态。
伸根段工作温度:
660℃。
660℃时材料屈服极限:
σ0.2=754MPa。
边界条件:
根据叶片实际工作情况设定三种边界条件,三种边界条件在工作时都可能出现。
计算结果表明,叶片伸根段存在三个大应力区:
Ⅰ区—第一隼齿齿底;
Ⅱ区—伸根与下缘板转接段下部;
Ⅲ区—伸根的加强筋上部。
三个大应力区在各种边界条件下的最大主应力见表2-2。
表2-2三种边界条件下大应力区的最大主应力
大应力区
第一种边界条件
第二种边界条件
第三种边界条件
Ⅰ区
1652
1092.6
1062
Ⅱ区
754.2
723.6
605.7
Ⅲ区
823.5
887.4
814.5
为验证计算的准确性,另外进行了光弹实验。
光弹试验结果与应力计算结果基本吻合,因此证明上述结果是正确的。
可以看出,在三种边界条件下,除Ⅱ去在屈服极限附近外,Ⅰ、Ⅲ区局部应力已超过屈服极限,Ⅰ区弹性应力最大,但根据计算结果,Ⅰ区的应力梯度较大,因而,即使在此区产生疲劳裂纹,其扩展速度也极缓慢,厂内各种试车已经证实了这一点,而Ⅱ区虽然应力水平小于Ⅰ区,但其应力梯度小,所以一旦产生裂纹就会迅速扩展,导致叶片折断,四起故障都是这种模式。
2.3故障分析结论
通过上述分析可得出如下结论:
(1)一级涡轮工作叶片从伸根处疲劳断裂,断裂的叶片飞出后打坏后面的涡轮工作叶片和导向叶片,导致发动机失效。
(2)一级涡轮工作叶片疲劳断裂的原因是伸根处存在大应力区,并且在大应力区存在不应有的冶金铸造缺陷和工艺污染。
正是这些在大应力区内的缺陷和污染成为疲劳源,并萌生裂纹,裂纹迅速扩展导致叶片折断。
2.4质量改进措施与效果
为预防和排除叶片断裂故障,针对故障原因和实际情况,采取三个阶段的方法,对叶片进行质量控制和改进。
第一阶段对已出厂的叶片进行分阶段返厂检查,同时贯彻如下措施:
(1)改进探伤工艺,消除X光检验盲区,更新X光探伤设备,对返厂叶片重新进行X光探伤。
(2)制定加严的叶片伸根段荧光检查标准,按新标准检查叶片。
(3)为彻底消除Sn、Bi污染,在叶片加工工艺中增加水吹砂和酸洗工艺,并用原子吸收法检查叶片上是否残存Sn、Bi元素。
(4)加严的伸根及加强筋的尺寸控制。
为验证以上措施的效果,选用在外场工作1600小时的叶片进行了低循环疲劳对比试验和寿命研究。
按试验数据处理结果:
经过加严检查合格的叶片寿命明显提高。
第二阶段
为了在短时间内提高叶片的使用寿命和寿命期内的可靠性,针对叶片伸根段局部应力过大问题,对叶片进行了局部改进设计,降低了伸根段的应力。
经过试验器试验和长期试车考核,证明改进后的叶片寿命有所提高。
局部改进设计后的叶片寿命为1500小时/1500次循环。
第三阶段
为彻底克服叶片伸根受力不合理的状况,进一步提高叶片质量和可靠性,延长叶片使用寿命,决定研制全新叶片。
新叶片研制的设计原则是:
保证与原叶片能够互换,采用成熟的工艺方法早日实现生产。
新叶片设计时采用大型三维有限元计算程序对叶片进行了应力和振动计算,计算表明,新研制叶片的应力水平较原叶片有较大幅度的降低,彻底消除了原叶片伸根存在大应力区问题。
在试验器上进行的对比试验证明,新设计叶片的伸根寿命比原叶片有大幅提高。
通过台架试车考核验证,新叶片的寿命已达到2000小时/2000次热循环。
1992年后最后一起涡轮叶片故障后,在WJ5AI型发动机涡轮叶片再没出现过同类的故障,证明改进措施是有效的。
3涡轮工作叶片裂纹故障
3.1故障现象
在发动机涡轮叶片故障中,叶片裂纹问题是比较普遍和严重的问题,在某型发动机大修中,其高压涡轮叶片裂纹统计结果中叶片裂纹超标叶片占叶片总数的5%-6%。
表3-1给出了WP7和WP13系列发动机一级涡轮工作叶片裂纹统计表。
表3-1WP7和WP13系列发动机一级涡轮工作叶片裂纹统计表
裂纹类型
发动机号
发动机工作
时间(h:
min)
发现裂
纹时间
裂纹叶片
数量及特征
叶片过热
过烧裂纹
32P7B402087
99:
57/200:
20
1989年4月
94片单片裂纹
32P7B402013
99:
57/195:
25
1990年6月
61片有裂纹
P7830163
34:
02
1988年
87片进气边裂纹
P13AⅡ9043
33:
10
1992年
94片全部有裂纹,单片2-5条裂纹
15ⅡP72087
199:
17
1990年
5、7、29、36、88号叶片有裂纹
叶片冶金缺
陷诱发裂纹
P7850426
98:
:
30
1988年3月
2片叶片有裂纹
P7830175
104:
05
1988年
把号叶片进气边有裂纹,全级报废
P7820103
299:
46
1998年
5号叶片有铸造缺陷
P7840326
95:
57
1987年
83号叶片有裂纹
15ⅡP7872
199:
29
1990年
60号叶片进气边横向裂纹
统计中看出,涡轮工作叶片叶身上的裂纹故障是多发性的,在各种发动机上都出现过,是一种重大质量隐患,故障中主要有:
叶片过热过烧裂纹和叶片冶金缺陷诱发裂纹。
3.2故障原因分析
初步分析,涡轮叶片产生裂纹故障主要是有叶片所处的恶劣工作环境和性质决定的:
(1)叶片在高温、高转速下工作,运转中承受很大的离心力和气动力作用,产生拉伸应力和弯曲应力。
(2)高速然气流的脉冲,使叶片受到振动力。
(3)叶片各处温度分布不同,造成温差应力。
(4)叶片上的温度还因发动机启动或停车而急剧变化,使叶片承受热疲劳。
(5)燃气中的杂质使叶片产生腐蚀。
3.2.1叶片叶尖裂纹状态
(1)叶尖裂纹故障的形貌分析
通过对叶片叶尖裂纹进行着色显示和放大镜在观察和记录,高压涡轮叶片叶尖裂纹的分布是这样的:
叶盆面裂纹条数明显多于叶背,而且叶盆裂纹主要集中在曲率半径嘴大处。
一般情况下,裂纹最长4.5mm,最短0.3mm。
随机抽取一片叶片作为研究对象,将其放入扫描电镜下观察,明显可见在叶尖端面有明暗相间的磨损条带存在(见图2-1),对图3-2中的明暗条带(1、2位置)进行了能谱分析(见图3-3、3-4),结果发现有Cl、O、C元素存在,这表明叶尖遭受复杂的热腐蚀过程。
图3-1叶尖端面磨损形态图3-2磨损带的明暗区
图3-3暗区能谱分析图3-4明区能谱分析
(2)叶尖裂纹的形态分析
依然选取这一片叶片作为研究对象,将其进行解剖分析,肉眼可见在叶尖叶盆一侧有一条裂纹,而在叶背一侧有三条裂纹,为了确定在大裂纹周围是否还有小裂纹存在,用线切割将叶片按图2-5所示部位切下,制成金属试样,最长的裂纹直线距离为3mm,最短的裂纹约为60µm,裂纹间距从250µm-1500µm不等。
最长的裂纹1出现了两次向上分叉,裂纹编号、分布及直线长度如图2-5所示。
图3-5叶片切片部位及裂纹分布示意图
用扫描电镜对裂纹进行观察发现,无论是大裂纹扩展路径都很平直且无分叉(图3-6和图3-7),裂纹的端口比较光滑(图3-8),呈明显的穿晶发展的特征,裂纹超过一定限度,氧化和塑性变形累计损伤很大时,裂纹就会出现分叉(图3-9)。
在裂纹内部存在腐蚀产物(图3-10)
图3-6平直无分叉大裂纹图3-7平直无分叉小裂纹
图3-8主裂纹开口段平直图3-9有两个分叉的主裂纹
图3-10裂纹内部腐蚀产物存在
总的来说,高压涡轮叶片叶尖裂纹状态有如下特点:
①叶盆断裂明显多于叶背;②裂纹多发生曲率半径最大处;③裂纹有长有短,大裂纹旁边有小裂纹存在;④长裂纹分叉,短裂纹不分叉;⑤裂纹起始端平直;⑥裂纹内有腐蚀产物存在。
3.2.2裂纹形成及发展特征
首先,对图3-5所示的叶片切片试验抛光在金相显微镜下观察时发现,试样表面在没有用任何侵蚀剂侵蚀的条件下,明显发现了晶界,这表明叶片尖部有大量的腐蚀坑存在(图3-11,)在裂纹(图3-12)的起始端有明显的腐蚀坑。
经能谱分析裂纹内的腐蚀产物主要为碳化物和氧化物(见下表3-2)将小裂纹在放大镜下观察,发现在腐蚀层中央有裂纹,裂纹在腐蚀层内扩展,但裂纹尖端没有穿过腐蚀层,这表明主裂纹是先腐蚀后开裂的(图3-13、图3-14)。
表3-2裂纹内部腐蚀产物能谱分析
元素含量
C
O
Al
W
Nb
Ti
Cr
Co
Ni
Wt%
20.07
19.09
5.37
10.89
1.67
5.85
17.85
5.12
14.08
At%
42.48
30.34
5.07
1.51
0.46
3.11
8.73
2.21
6.10
图3-11表层腐蚀坑图3-12腐蚀坑引起的裂纹
图3-13钉状裂纹图3-14钉状裂纹
在裂纹扩展过程中,热循环导致材料材料和裂纹表面不断腐蚀氧化,有时材料会出现大块腐蚀氧化脱落现象(图3-15),裂纹增宽。
能谱分析结果如表3-3,从表3-3中得出,裂纹中部仍然以氧化物和碳化物为主,出现了很多Al2O3块。
材料在热循环过程中,虽然破坏主要以穿晶为主,但有时因局部严重晶界氧化而出现沿晶开裂(图3-16、表3-4),裂纹分叉多发生在γ-γˊ共晶处,腐蚀沿晶界择优进行,裂纹主要沿晶界扩展,但也有裂纹穿过晶粒和氧化裂纹相连接而扩展(图3-17、图3-18)。
于应力垂直的裂纹尖端没有腐蚀产物,裂纹是先开裂后腐蚀,而不与应力垂直的裂纹尖端有腐蚀产物,是先腐蚀后开裂。
图3-15主裂纹中部腐蚀产物图3-16分叉裂纹尖端氧化开裂
图3-17主裂纹的第一个分叉沿晶扩展图3-18主裂纹的第二个
分叉裂纹沿晶扩展
表3-3图3-14所示各点能谱分析
各点
元素
1
2
3
4
5
6
Wt%
Wt%
At%
Wt%
At%
Wt%
Wt%
At%
Wt%
At%
Wt%
At%
C
16.44
49.04
14.77
40.82
15.51
37.27
14.08
38.75
27.23
66.69
O
2.30
5.15
10.19
21.13
15.89
28.67
9.43
19.48
32.42
44.72
Al
0.65
0.80
2.75
2.94
4.27
5.25
1.42
1.55
67.58
55.28
W
10.38
2.02
13.57
2.48
11.87
1.86
12.24
2.20
12.79
2.05
Ti
1.40
1.05
7.49
4.51
1.41
0.97
1.28
0.78
Cr
4.68
3.22
5.24
3.35
29.81
16.54
5.28
3.36
3.83
2.17
Fe
1.75
1.04
Co
8.78
6.33
8.08
4.55
3.0
1.47
8.39
4.71
6.64
3.31
Ni
56.03
34.19
45.76
25.87
13.68
6.73
44.89
25.28
46.82
23.46
总
100
100
100
100
100
100
100
100
100
100
100
100
表3-4图3-11中所示分叉裂纹简短的能谱分析
元素
含量
O
Al
W
Ti
Cr
Co
Ni
Wt%
12.49
5.21
10.73
1.80
5.38
9.35
55.04
At%
34.39
8.52
2.57
1.66
4.56
6.99
41.31
3.3故障分析结论
综上所述,高压涡轮叶片叶尖裂纹形成与发展是环境和热应力复合作用的结果。
叶片表层材料发展衰变和形成局部蚀坑,这些腐蚀坑再热循环过程中起缺口效应,容易形成微裂纹,是潜在的裂纹源。
裂纹形成后,形成了燃气内侵蚀通道,形成氧化物和碳化物等腐蚀产物,这些氧化物和碳化物像钉子一样深入到金属内部,形成“钉扎效应”,再循环应变下,裂纹内淤塞的腐蚀产物起着楔子的作用,在裂纹尖端处造成附加应力,促进裂纹扩展;在裂纹扩展过程中,热腐蚀导致裂纹面氧化增宽;材料晶界腐蚀为分叉裂纹提供核心,并在热应力作用下扩展。
主裂纹的扩展是先开裂后腐蚀,分叉裂纹是先腐蚀后开裂。
3.4叶片纵向裂纹故障的修理方法
针对高压涡轮叶片叶尖裂纹故障,目前所能采取的方法,可以用激光显微焊修复。
(1)激光显微焊接修复叶片裂纹要注意如下原则:
1.由于叶片叶尖存在氧化腐蚀、组织衰变,要彻底消除裂纹,就要消除腐蚀层和组织衰变层,但又不能使基材损伤过