生产全流程分析与改进CHECKLIST.docx
《生产全流程分析与改进CHECKLIST.docx》由会员分享,可在线阅读,更多相关《生产全流程分析与改进CHECKLIST.docx(28页珍藏版)》请在冰豆网上搜索。
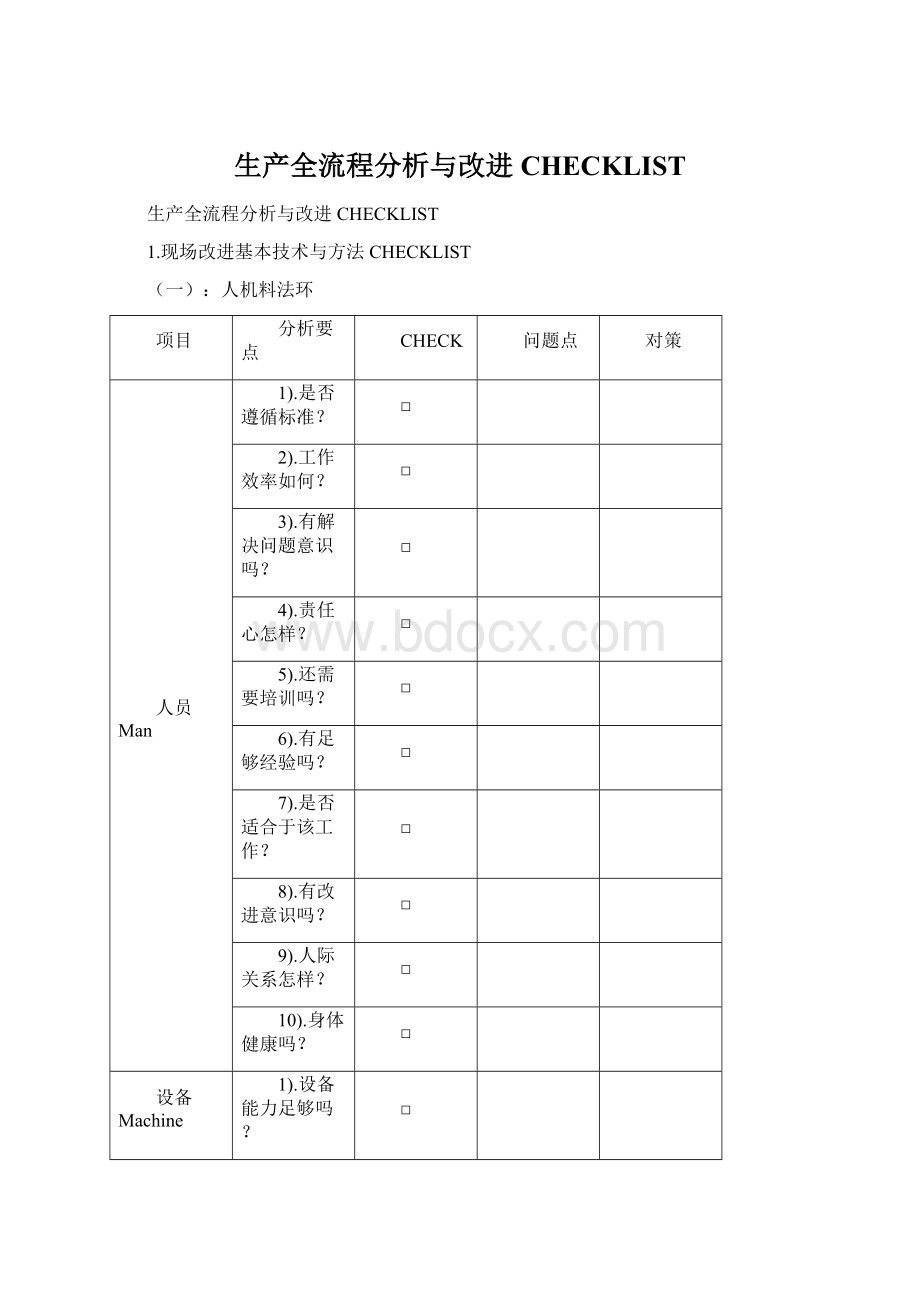
生产全流程分析与改进CHECKLIST
生产全流程分析与改进CHECKLIST
1.现场改进基本技术与方法CHECKLIST
(一):
人机料法环
项目
分析要点
CHECK
问题点
对策
人员Man
1).是否遵循标准?
□
2).工作效率如何?
□
3).有解决问题意识吗?
□
4).责任心怎样?
□
5).还需要培训吗?
□
6).有足够经验吗?
□
7).是否适合于该工作?
□
8).有改进意识吗?
□
9).人际关系怎样?
□
10).身体健康吗?
□
设备Machine
1).设备能力足够吗?
□
2).能按工艺要求加工吗?
□
3).是否正确润滑了?
□
4).保养情况如何?
□
5).是否经常出故障?
□
6).工作准确度如何?
□
7).设备布置正确吗?
□
8).噪音如何?
□
9).设备数量够吗?
□
10).运转是否正常?
□
材料Material
1).数量是否足够或太多?
□
2).是否符合质量要求?
□
3).标牌是否正确?
□
4).有杂质吗?
□
5).进货周期是否适当?
□
6).材料浪费情况如何?
□
7).材料运输有差错吗?
□
8).是否对加工过程足够注意?
□
9).材料设计是否正确?
□
10).质量标准合理吗?
□
方法Methode
1).工艺标准合理吗?
□
2).工艺标准提高了吗?
□
3).工作方法安全吗?
□
4).这方法能保证质量吗?
□
5).这种方法高效吗?
□
6).工序安排合理吗?
□
7).工艺卡是否正确?
□
8).前后工序衔接好吗?
□
环境environment
1).作业环境如光线、工作台、椅子等是否合适(舒适)
□
2).温度和湿度适宜吗?
□
3).通风和光照良好吗?
□
4).有无安全隐患。
□
(二):
5W2H
区分
5W2H
结果
Check
问题点
对策
参考对策
对象
WHAT
1.目前的情形如何?
□
排除不必要的部分工作
2.为何会如此?
□
3.是否还有其它的?
□
目的
WHY
1.为何是必要的?
□
2.为何会如此?
□
3.是否还有其他的事?
□
4.该如何去做?
□
场所
WHERE
1.在哪里发生?
□
合理的作业场所
2.为何会在该处发生?
□
3.别处不会再发生?
□
4.该在哪里做才好?
□
顺序
WHEN
1.什么时候发生的?
□
把顺序改变再重新组合
2.为何会在该时段发生?
□
3.别的时段不会发生吗?
□
4.何时来做才好?
□
人
WHO
1.究竟发生在谁的身上?
□
作业分工、工作分层
2.为何会发生在他身上?
□
3.可否有别人替代?
□
4.应该让谁来做才好?
□
方法
HOW
1.为何会变成那样子?
□
方法研究
2.有无其它的方法?
□
3.该如何来做?
□
经费
HOWMUCH
1.要花费多少?
□
选择经济的方法
2.为什么要花费那些钱?
□
3.如要改善的话,要花费多少?
□
4.会不会白白浪费掉?
□
(三):
消除浪费对策
Item
说明
结果
分析
Check
对策
生产
过多
之
浪费
在不必要的时候,将不必要的东西,生产不必要的量。
.阻碍物的流动
.不良的发生
.库存、在制品的增加
.资金周转率的降低
.材料、零组件的提前使用
.使计划无弹性
.过剩人员,过剩设备
□
.FullWork控制
.快速换模
.看板控制
.平准化生产
.少人化
.单件流动
.大批量生产
□
.大型高速机器
□
.无限制生产
□
等待
之
浪费
材料、作业、搬运、检查等的等待及宽裕
或监视作业。
.空间使用的浪费
.生产力降低
.搬运工时增加
.搬运设备增加
.不良的发生
.计划的不周全
□
.平准化生产
.自动仍化
.除错装置
.快速换模
.产品别配置
.产能不平衡
□
.上游制程的故障
□
.大批量生产
□
.机器配置不当
□
搬运
之
浪费
不必要的搬运、取放、换装等。
或过长的搬运及过低的活性系数。
.多余制程、多余作业
.人员、工时的增加
.效率降低
.不良增加
.Layout的不周全
□
.U-shape配置
.流程式生产
.多能工化
.立式作业
.活性系数的改善
.混载系统
.大批量生产
□
.单能工
□
.坐式作业
□
.低活性度
□
加工
之
浪费
本来不必要的加工作业。
.交货期的拉长
.迷失改善方向
.空间的浪费
.搬运、检查的增加
.周转资金的增加
.交货期的拉长
.迷失改善方向
.空间的浪费
.搬运、检查的增加
.制程顺序的检讨不足
□
.制程设计的重新检讨
.作业内容的重新检讨
.治具的改善
.标准化的推行
.VA/VE的推动
.作业内容的检讨不足
□
.治具的不周全
□
.标准化的不彻底
□
.材料的检讨不足
□
库存
之
浪费
指仓库及制程间之材料、半成品,零组件
等物料的停滞现象。
.周转资金的增加
.传统库存意识的影响
□
.库存意识的革新
.U-shape配置
.快速换摸
.平准化生产
.重视计画
.看板控制
.机器配置不当
□
.大批量生产
□
.计划的不周全
□
.预期生产
□
.自行生产
□
动作
之
浪费
不必要的动作,不产生附加价值的动作,过快或过慢的动作
.人员、工时的增加
.技术的私有化
.不安定的作业
.离岛式作业
□
.流程式生产的推行
.标准作业表
.U-shape配置
.动作经济原则的彻底活用
.老师傅风气
□
.机器配置不当
□
.教育、训练不足
□
不良
之
浪费
材料或加工不良的检查、抱怨、整修等。
.材料费的增加
.生产力降低
.检查人员、制程增加
.不良、顾客抱怨增加
.重视下游的捡查作业
□
.自働化、SOP
.除错装置
.全数检查
.品保制度的确立
.检查方法、基准的不周全
□
.品质过剩
□
.标准作业的不周全
□
2.现场改进流程CHECKLIST
1.全流程程序分析
分析要点:
工序关系,物流次序、瓶颈工序、关键工序(控制评审点)
关键方法:
ECRS四大原则、五个方面、程序分析、5W2H(结合使用)
1)ECRS原则
改善原则
目的
改善重点
Check
事例
排除
Eliminate
1.排除浪费;
2.排除不必要的作业。
(1)剔除所有可能的作业,步骤或动作(身体,足,手臂或眼)。
□
1.合理布置,减少搬运;
2.取消不必要的外观检查。
(2)剔除工作中的不规律性,使动作成为自发性,并使各种物品置放于固定地点。
□
(3)剔除以手作为持物工具的工作。
□
(4)剔除不方便或不正常的动作。
□
(5)剔除必须使用肌力才维持的姿势。
□
(6)剔除必须使用肌力的工作,而以力工具取代之。
□
(7)剔除必须克服动量的工作。
□
(8)剔除危险的工作。
□
(9)剔除所有不必要的闲置时间。
□
合并
Combine
1.配合作业;
2.同时进行;
3.合并作业。
(1)把必须突然改变方向的各小动作结合成一连续曲线动作。
□
1.一人多机作业;
2.一边加工一边检查。
(2)合并各种工具,使成为多用途。
□
(3)合并可能的作业。
□
(4)合并可能同时进行的动作。
□
重排Rearrange
1.改变次序;
2.改用其它的方法;
3.改用别的东西。
(1)使工作平均分配于两手,两手之同时动作最好呈对称性。
□
把检查工作移到前面,对来料质量进行控制。
(2)组作业时,应把工作平均分配于各成员。
□
(3)把工作安排成清晰的直线顺序。
□
简化
Simplify
1.连接更合理;
2.使之更简单;
3.去除多余的动作。
(1)使用最低级次的肌内工作。
□
使零件标准化,减少种类,批量生产有利于降低成本。
(2)减少视觉动作并降低必须注视的次数。
□
(3)保持在正常动作范围内工作。
□
(4)缩短动作距离。
□
(5)使手柄,操作杆,足踏板,按钮均在手足可及之处。
□
(6)在须要运用肌力时,应尽量利用工具或工作物的动量。
□
(7)使用最简单的动素组合来完成工作,
□
(8)减少每一动作的复杂性。
□
2)五个方面
方面
改进要点
存在问题点
操作分析
操作任务量化
搬运分析
运输路线要短
检验分析
检验设置合理
贮存分析
存储时间要少
等待分析
等待务必删除
3)程序分析
工序
作业内容
问题点描述
作业时间min
改善要点
符号
简化
取消
合并
重排
操作
运送
停放
检验
存储
○
≯
▓
□
▼
2.全流程操作分析
分析要点:
整理工序操作流程;消除工序操作中不经济、停滞现象;工序操作中作业进行优化,消除不经济现象
关键方法:
人机操作分析;联合操作分析;双手操作分析
1)人机操作分析
目的:
在机器的工作过程中,调查、了解在操作周期内,人与机的相互联系,以充分调动人与机的能量及平衡操作的分析。
要点:
•人力作业时序分布
•机器作业时序分布
•合理分布人机时序
•优化人机时序分布
•提高人机工作效率
2)联合操作分析
定义:
在生产现场,对常有两个或两个以上的操作员同时对一台机器(一项工作),进行工作,对其进行作业分析。
目的:
取消或減少空閒或等待時間,以達到縮短工期
要点:
•发掘空闲时间
•平衡人机工作
•减少工作周期
•合理分配人机
•提高设备效率
3)双手操作分析
定义:
调查、了解生产现场工人如何用双手进行实际操作的情况,称双手操作分析。
目的:
雙手動作規範、平穩,去除無效動作,改變不合理的物料、工具、設備位置。
要点:
•双手操作情况
•用6W方式提问
•有无优化动作
•实施简化合并
操作分析检讨点:
项目
检讨要点
Check
改进点
1.材料
1)在不影响品质之情况,可否用较廉价之材料为代用品?
□
2)当送至操作者时,是否规格一致,情况正常?
□
3)尺寸、重量、精度是否恰当而能经济地使用?
□
4)物料是否已尽量利用?
□
5)边料及不合格制品是否可加以利用?
□
6)在制程中材料、零件、半成品之存量能否减至最少?
□
2.物料搬运
1)搬运之次数可否减少?
□
2)运送之距离可否缩短?
□
3)材料之收发、运送,及储存是否用适当之容器?
容器是否清洁?
□
4)材料分送至操作者时有无延误?
□
5)可否应用输送带以减除工作之提送(搬运)?
□
6)材料之回送可否减少或剔除?
□
7)可否重排布置或合并操作以免除不必要之运送?
□
8)可否合并操作、检验或改变工作次序以免除不必要之运送?
□
3.工具、夹具及固定器
1)是否是适合此工作之最佳工具?
□
2)工具情况是否良好?
□
3)切削金属工具之削角是否正确?
是否有集中研磨工具之部门?
□
4)是否可变换工具或固定器,可使担任此道操作所需要的技术降低?
□
5)用工具、固定器时,工人双手是否皆做生产性工作?
□
6)可否采用滑运喂料、弹送、夹持工具?
□
7)可否因制程变更而使设计简化?
□
4.机器
□
A.准备工作:
1)操作者是否需自行准备其自己的机器?
□
2)是否可因生产批量之合适大小,而减少准备之次数?
□
3)蓝图、工具样板(量具)之供给有无耽搁?
□
4)试样之检验有无延误?
□
B.操作
1)此项操作能否剔除?
□
2)能否多种操作同时做?
□
3)机器之速度及进料速度能否增加?
□
4)能否改为自动进料?
□
5)此项操作能否分为二或更多较短的操作?
□
6)可否将二种或更多操作合并为一?
□
7)此操作之次序能否改变?
□
8)废料(废屑)及坏品量能否减少?
□
9)制成件能否预放于下道工序之位置?
□
10)干扰之次数可否减少或取消?
□
11)检验与操作可否合并?
□
12)机器情况是否良好?
□
5.操作者
1)操作者在智力及体力上是否适合做此操作?
□
2)是否可改变工具、夹具,或工作环境以免除工人不必要之疲劳?
□
3)此项操作之基本工资是否合适?
□
4)主管督导是否令人满意?
□
5)是否再加以教导可使工作者有更好的表现?
□
6.工作环境
1)灯光、温度及通风是否适合此项操作?
□
2)洗手间、更衣室、休息室、工作服(帽鞋等)等设备是否适当?
□
3)有无不必要之危险存在此操作之内?
□
4)有无使工人工作时可坐或可立之设置?
□
5)工作及休息时间之长短,是否已达最经济情形?
□
6)工厂中之工场整顿是否良好?
□
3.全流程动作分析
分析要点:
(1)了解操作者身体部位的动作顺序和方法;
(2)了解以两手为中心的人体各部位是否能尽可能同时动作,是否相互联系;
(3)明确各种动作的目的,动作过程中的必要动作和不必要动作;
(4)了解必要的作业动作中两手的平衡。
关键方法:
目视动作观察法(动素分析;双手操作分析);影像动作观察法
主要工具:
Rightanslefthandcharts(左右手分析法)/Simocharts;Processchart(流程图);Operationprocesschart(操作流程图)
1)动素分析
定义:
动素分析把动作分类归纳成18种基本的最小动作单位,可以分成以下三大类动素。
动素类型
动作内容
研究要点
Check
有效动素
伸手、握取、移物、定位、装配、拆卸、使用、放手、检查等9种
应该取消的不会很多;分析、改善的重点是如何缩短其时间
□
辅助动素
寻找、发现、选择、思考、预置等5种
此类动作将延缓第1
类动作实施,降低作业效率,除非用不可者外应尽量取消
□
无效动素
拿住、不可避免迟延、休息和可避免的耽搁等4种
一定要设法取消的动素
□
2)动作经济原则
定义:
动素分析把动作分类归纳成18种基本的最小动作单位,可以分成以下三大类动素。
动作经济原则
改进着眼点
改进目标
Check
减少动作数
避免不必要的动作,物料和工具的放置要便于使用,尽量减少动作数,或一次完成2个以上的动作。
(1)取消不必要的动作;
□
双手同时进行动作
同时使用双手动作,同时要改善作业现场和工装夹具以便于双手同时动作。
(1)双手同时开始同时完成动作
(2)双手对称、反向同时动作
□
缩短动作距离
1、动作方法;
2、作业现场布置
3、工夹具与机器
(1)便于用最适当的人体部位动作
(2)用最短的距离进行动作
(3)在不防碍作业的前提下尽量使作业区域狭窄
(4)利用重力和机械动力送进、取出物料;
(5)用人体最适当的部位操作机器
□
轻快动作
(1)使动作不受限制轻松进行
(2)利用重力及其他机械电磁力动作
(3)利用惯性力和反冲力动作
(4)连续圆滑地改变运动方向
□
3)巴恩斯22条原则
类别
动作经济原则
Check
问题点
对策
关于人体的运用
1、双手应同时开始并同时完成其动作。
□
2、除规定的休息时间外,双手不应同时空闲。
□
3、双臂的动作应该对称,反向并同时进行。
□
4、手的动作应以最低的等级而能得到满意的结果。
□
5、物体的运动量应尽可能地利用,但是如果需要肌力制止时,则应将其减至最小的程度。
□
6、连续的曲线运动,比方向突变的直线运动为佳。
□
7、弹道式的运动,较受限制后收控制的运动轻快自如。
□
8、动作应尽可能地运用轻快的自然节奏,因节奏能使动作流利及自发。
□
关于工作地布置
9、工具物料应放置在固定的地方。
□
10、工具物料及装置应布置在工作者前面近处。
□
11、零件物料的供给,应利用其重量坠送至工作者的手边。
□
12、下移应尽量利用重力实现。
□
13、工具物料应依最佳的工作顺序排列。
□
14、应有适当的照明,使视觉舒适。
□
15、工作台及座椅的高度,应保证工作者坐立适宜。
□
16、工作椅式样及高度,应能使工作者保持良好的姿势。
□
关于工具设备
17、尽量解除手的工作,而以夹具或脚踏工具代替。
□
18、可能时,应将两种工具合并使用。
□
19、工具物料应尽可能预放在工作位置上。
□
20、手指分别工作时,其各指负荷应按照其本能予以分配。
□
21、设计手柄时,应尽可能增大与手的接触面。
□
22、机器上的杠杆、十字杆及手轮的位置,应能使工作者极少变动姿势,且能最大地利用机械力。
□
动作改善要素
着眼点
Check
问题点
对策
1.基本原则
1)尽量减少操作中的各动作。
□
2)排列成最佳顺序。
□
3)有利时合并各动作。
□
4)尽可能简化各动作。
□
5)平衡双手的动作。
□
6)避免用手持物。
□
7)工作设备应合乎工作者的身材。
□
2.有无任何动作因下列的变更而予以剔除?
1)不必要。
□
2)变更动作的顺序。
□
3)变更工具及设备。
□
4)变更工作场所的布置。
□
5)合并所用工具。
□
6)改变所用材料。
□
7)改变产品设计。
□
8)使夹具动作迅速。
□
3.运送动作能否剔除?
1)因不必要。
□
2)因动作顺序的变改。
□
3)因工具约合并。
□
4)因工具或设备的改善。
□
5)因完成品的自动堕送。
□
4.手持的情形可否免除?
1)因不必要。
□
2)因采用夹具。
□
5.等待是否可减免?
1)因不必要。
□
2)因动作的变更。
□
3)因身体各部动作的平衡。
□
4)因同时以双手对称动作完成工作。
□
5)因双手交换的动作。
□
6.有无任何动作可以简化?
1)因用较好工具。
□
2)因变更杠杆机构。
□
3)因变更对象放置地点至适宜位置。
□
4)因采用较佳盛具。
□
5)因应用惯性力量
□
6)因减短视线距离。
□
7)因工作台高度之适当。
□
7.运送是否可以简化?
1)因变更布置减短距离。
□
2)因变更方向。
□
3)因使用不同肌肉。
□
4)因动作路线圆转不断(连续曲线)
□
8.夹持是否可改简易?
1)减短夹持时间。
□
2)使用身体有力部份,如用脚踏。
□