刀具合理几何参数的选择.docx
《刀具合理几何参数的选择.docx》由会员分享,可在线阅读,更多相关《刀具合理几何参数的选择.docx(10页珍藏版)》请在冰豆网上搜索。
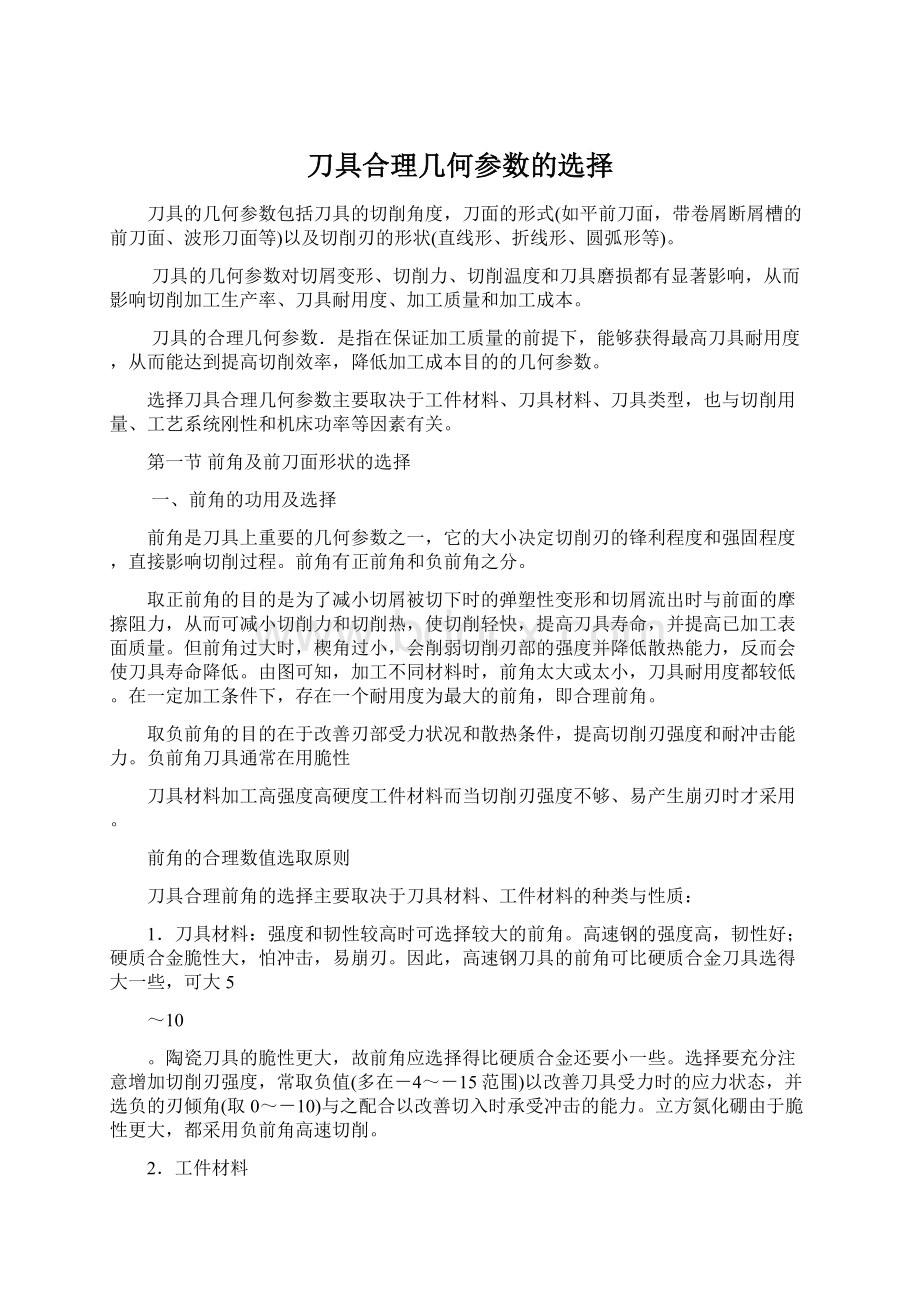
刀具合理几何参数的选择
刀具的几何参数包括刀具的切削角度,刀面的形式(如平前刀面,带卷屑断屑槽的前刀面、波形刀面等)以及切削刃的形状(直线形、折线形、圆弧形等)。
刀具的几何参数对切屑变形、切削力、切削温度和刀具磨损都有显著影响,从而影响切削加工生产率、刀具耐用度、加工质量和加工成本。
刀具的合理几何参数.是指在保证加工质量的前提下,能够获得最高刀具耐用度,从而能达到提高切削效率,降低加工成本目的的几何参数。
选择刀具合理几何参数主要取决于工件材料、刀具材料、刀具类型,也与切削用量、工艺系统刚性和机床功率等因素有关。
第一节前角及前刀面形状的选择
一、前角的功用及选择
前角是刀具上重要的几何参数之一,它的大小决定切削刃的锋利程度和强固程度,直接影响切削过程。
前角有正前角和负前角之分。
取正前角的目的是为了减小切屑被切下时的弹塑性变形和切屑流出时与前面的摩擦阻力,从而可减小切削力和切削热,使切削轻快,提高刀具寿命,并提高已加工表面质量。
但前角过大时,楔角过小,会削弱切削刃部的强度并降低散热能力,反而会使刀具寿命降低。
由图可知,加工不同材料时,前角太大或太小,刀具耐用度都较低。
在一定加工条件下,存在一个耐用度为最大的前角,即合理前角。
取负前角的目的在于改善刃部受力状况和散热条件,提高切削刃强度和耐冲击能力。
负前角刀具通常在用脆性
刀具材料加工高强度高硬度工件材料而当切削刃强度不够、易产生崩刃时才采用。
前角的合理数值选取原则
刀具合理前角的选择主要取决于刀具材料、工件材料的种类与性质:
1.刀具材料:
强度和韧性较高时可选择较大的前角。
高速钢的强度高,韧性好;硬质合金脆性大,怕冲击,易崩刃。
因此,高速钢刀具的前角可比硬质合金刀具选得大一些,可大5
~10
。
陶瓷刀具的脆性更大,故前角应选择得比硬质合金还要小一些。
选择要充分注意增加切削刃强度,常取负值(多在-4~-15范围)以改善刀具受力时的应力状态,并选负的刃倾角(取0~-10)与之配合以改善切入时承受冲击的能力。
立方氮化硼由于脆性更大,都采用负前角高速切削。
2.工件材料
1)加工塑性材料时,切屑呈带状,沿刀具前面流出时和前面接触长度较长,摩擦较大,为减小变形和摩擦,一般都采用正前角。
工件材料塑性愈大,强度和硬度愈低时,前角应选得愈大。
如加工铝及铝合金取o=
25
~35
,加工低碳钢常取o=20
~25
。
当工件材料强度较大、硬度较高时,前角宜取小值,如正火高碳钢取o=10
~l5
。
当加工高强度钢时,为增强切削刃,才取负前角。
2)加工脆性材料(如灰铸铁)时,塑性变形小,切屑呈崩碎状,刀屑接触长度短,摩擦不大,切削力集中在切削刃附近且产生冲击,容易造成崩刃。
所选前角应比加工塑性材料时小一些,以提高切削刃强度和散热能力。
如加工灰铸铁取o=5
~15。
前角数值随脆性材料强度和硬度的增大而逐渐减小。
在加工淬火钢、冷硬铸铁等高硬度难加工材料时,宜取负前角。
实验证明,用正前角硬质合金车刀加工高硬度淬火钢时,切削刃几乎一开始切削就会发生崩刃。
3.具体加工条件:
粗加工时或断续切削时,切削力和冲击较大,为使切削刃有足够强度,宜取较小前角;精加工时,切削刃强度要求较低,为使刀具刀刃锋利,降低切削力,以减小工件变形和减小表面粗糙度值,宜取较大前角。
在工艺系统刚性较差或机床马达功率不足时,宜取较大前角;在自动机床上加工时,为使刀具稳定,宜取小一些的前角。
4.其他参数的选择:
前角的合理数值不是孤立的,还和刀面形状及刃区参数以及其他角度有关,特别是和刃倾角有密切关系。
例如:
带负倒棱的刀具允许采用较大前角;大前角刀具常与负刃倾角相匹配来保证切削刃强度和抗冲击能力。
许多先进刀具就是在针对某种加工条件,善于灵活运用这些原则而产生的。
下表是一般情况下硬质合金车刀合理前角的经验数值,可供选用时参考。
二、刃区参数及前面形状的选择
1.刃区参数
刃区剖面型式有锋刃型、倒棱型和钝圆切削刃型三种。
1)锋刃:
指刃磨前面和后面直接形成的切削刃。
但它也并不是绝对锐利的,而在刃磨后自然形成一个切削刃钝圆半径rn.其数值取决于刀具材料、刃磨工艺和楔角的大小。
并且在切削过程中随着磨损而有增大的趋势,刀面表面粗糙度值越大,增大的速度也越大。
优点:
与倒棱切削刃和钝圆切削刃相比,锋刃的钝圆半径很小,切削刃比较锋利。
适合作精加工和超精加工的切削刃,如超精铣削或超精镗削,以及精加工和半精加工轻金属及其合金。
缺点:
锋刃的强度和抗冲击性能较差,产生微小裂纹导致崩刃的可能性也较大。
因此,对于精细切削和微量切削的刀具锋刃,都要求仔细刃磨和研磨,以获得小的切削刃钝圆半径,消除微小裂纹,提高刃口质量;采用锋刃切削时,一般应采用较小的进给量(O.05~0.lmm/r以下),以避免崩刃并减缓刃区裂纹的出现。
2)倒棱:
倒棱就是沿切削刃研磨出很窄的负前角棱面(又称第一前面),是增强刀刃强度的有效措施。
当负倒棱面宽度和棱面前角选取合理时,在切削过程中,棱面上将形成滞留金属三角区。
在复杂应力状态下可能转化为积屑瘤,使切屑层同工件的分离面发生在刃前三角区的峰部,如图所示。
这时,切屑仍沿着正前角的前面流出,切削力增大不明显,却使切削刃加强并受到三角区滞留金属的保护,刀具寿命明显提高。
另一原因是使切削合力的方向发生变化。
实验结果看出,当倒棱宽度b一定时,刀具总切削力的方向与后面的夹角随负倒棱前角01的增大而增大,从而在一定程度上改变了刀片的受力状况,减小了对切削刃产生弯曲应力的比例分量。
它对脆性刀具材料提高冲击能力是极为有利的。
倒棱参数的选取:
主要取决于进给量、刀具材料和工件材料。
a)进给量:
无论刃区取何参数,随进给量的增加,刀具寿命就下降,但下降的程度随参数值而异。
对应于某个进给量值,总有一个使刀具寿命最高的倒棱参数值。
一般讲,精加工时01要小些;粗加工时,进给量大,01要大些。
用硬质合金刀具加工钢时,负倒棱宽度b1一般不宜超过进给量。
这时,切削力与锋刃相比增大较小,b1大于f时,切削力将有明显增大趋势。
当负倒棱宽度大于一定数值时,切屑流出时只和负倒棱部分接触,随即卷曲而去,根本不和具有正前角的前面接触,这时,负倒棱实际上即变成负前角的前面。
b)刀具材料:
用硬质合金车刀车削碳钢、合金钢时,一般可取b(0.3~0.8)f,01=-10~-15。
对WC基硬质合金刀片,b取小值;高速钢刀具强度和韧性较好,一般不磨负倒棱,必要时可研磨出零度或小前角正倒棱。
c)工件材料:
加工低碳钢、不锈钢、灰铸铁时,可取b≤0.5f,01=-5~-10;当加工有硬皮的锻件和铸钢件时,在机床功率和刚度足够的条件下,倒棱负前角可减小到-30,当冲击严重时,负倒棱宽度可取b=(1.5~2)f,但这时切削力增大较多。
3)钝圆切削刃:
是在负倒棱的基型上进一步修磨而成,或直接通过刀片钝化处理而成。
特点:
钝圆半径比锋刃增大了一定数值,它不但在提高切削刃强度方面获得和负倒棱同样的效果,而且比负倒棱更有利于消除刃区微小裂纹,使刀具获得最佳寿命。
同时,在切削过程中对已加工表面还有一定的熨压和消振作用,有利于提高已加工表面质量。
经刃口钝化处理的可转位刀片和硬质合金涂层刀片就是采用了钝圆切削刃,已获得广泛应用。
钝圆切削刃的钝圆半径rn根据刀具材料、工件材料和切削条件三个方面选择。
可制成轻型,(rn约为0.025~0.05mm)、中型(rn约为0.05~0.1mm)和重型(rn约为0.1~0.15mm)三种。
刀具材料的强度和韧性影响钝圆切削刃钝圆半径的最佳数值。
高速钢刀具一般取正前角锋刃或轻型钝圆切削刃。
陶瓷刀片一般要求负倒棱且带有重型钝圆切削刃,而WC基硬质合金刀片一般多采用中型钝圆切削刃。
TiC基硬质合金的钝圆切削刃参数则介于两者之间选择。
工件材料的切削加工性也影响切削刃钝圆半径的合理数值,切削可加工性较好的有色金属,如铜、铝合金时,刀具刃区常采用轻型钝圆切削刃或锋刃。
切削灰铸铁、球墨铸铁、可锻铸铁时,由于其多孔性及其分布不均匀而产生冲击,刀具刃区通常采用中型钝圆切削刃。
切削普通钢材时,其刃区参数可根据含碳量确定。
切削低碳钢和大多数不锈钢的刀具可采用轻型钝圆切削刃,而切削高硬度合金时,刀具刃区需要中型乃至重型钝圆切削刃。
在切削加工条件中,进给量和切削刃钝圆半径rn也有一定关系,当用WC基硬质合金切削钢材时,一般可取rn≤f/3,而用Tic基硬质合金刀片和涂层刀片时,则可取rn≤f/l.5。
rn过小时,切削刃容易产生裂纹和崩碎,但rn过大时,也会使切削刃严重挤压切削层而降低刀具寿命,并增大已加工表面冷硬程度,甚至引起振动。
2.前刀面形状
前刀面形状分平面型和断屑前面型两大类。
在切削过程中金属材料受到变形,如变形程度超过了材料的断裂应变,则切屑将自行折断。
但多数情况下,只靠切削过程中的变形还不能使切屑折断,必须采用断屑器使切屑得到附加的二次变形。
在加工塑性材料时,为使切屑卷成螺旋形或折断成C形,使之易于排出和清理,常在前刀面上制成卷断屑槽。
卷断屑槽可作成直线圆弧型、直线型和全圆弧型三种。
直线圆弧型和直线型断屑槽适用于切削碳素钢、合金结构钢、工具钢等,0=5~15。
直线圆弧型的槽底圆弧半径Rn和直线型的槽底角(180-)较小时,切屑卷曲半径较小,切屑变形大,易于折断,但此时切屑易堵塞在槽内,会增大切削力,甚至造成崩刃。
一般取Rn=(0.4~0.7)Wn,(180-)=110~130。
全圆弧型适用于切削紫铜、不锈钢等高塑性材料,0可增大至25~30。
目前机夹可转位硬质合金刀片压制有各种形状及尺寸的断屑槽,可供不同切削情况下选用。
第二节后角及后刀面形状的选择
一、后角的功用及合理后角
后角的作用主要是:
减小后面与过渡表面和已加工表面之间的摩擦;影响楔角0的大小,从而可配合前角调整切削刃的锋利程度和强度。
对刀具耐用度和加工表面质量有很大影响。
适当增大后角可提高刀具耐用度.这是因为;
✧增大后角时能减小已加工表面弹性恢复层△h与后面的摩擦面积,从而减小后面摩擦与磨损。
✧后角增大,楔角则减小,刀刃钝圆半径可以减小,切削刃锋利,刀刃易切入工件,可减小工件表面的弹性恢复。
✧在一定的后刀面磨损量VB下,后角较大时,所允许磨去的金属体积较大。
但后角过大时,将使楔角且过小,削弱切削刃强度,减小散热体积而使刀具耐用度降低。
所以,在一定条件下,后角也有一个对应于最高刀具寿命的合理数值。
合理后角的选择主要取决于切削层公称厚度hD(或进给量f)的大小。
✧当hD(或进给量f)很小时(精加工),磨损主要发生在后刀面上,为减小磨损和增加切削刃的锋利程度,宜取较大的后角。
✧当切削厚度很大时,前刀面上月牙洼磨损显著.这时取较小后角可以增强切削刃和加大散热体积。
例如高速钢立铣刀,由于每齿进给量很小,后角取到16,而圆片铣刀当每齿进给量为0.01mm时,后角取30。
车刀后角的变动范围比前角要小。
粗车时,因hD较大,为保证切削刃强度取较小后角(4~8);而精车时,hD较小.为保证已加工表面质量,取较大后角8~12。
切断刀的进给量较小,且考虑进给运动对工作后角的影响.宜取较大后角10~12。
刀具合理后角还与一些切削条件有关:
✧工件材料的强度、硬度较高时,为加强切削刃,宜取较小后角(0=5~7)。
工件材料塑性较大,加工硬化严重时,为减小后刀面摩擦,应取较大后角(10~12)。
✧工艺系统刚性较差时,为避免振动,应适当减小后角。
✧对于尺寸精度要求较高的刀具,宜取较小的后角。
因为当径向磨损量NB为定值时,较小的后角所允许磨损掉的刀具材料体积较多,故刀具耐用度较高。
✧合理后角的选择还应考虑切削刃的运动轨迹。
例如切断刀愈接近工件中心,工作后角愈小,因此切断刀的后角应比外圆车刀大一些。
在车削大螺距右旋螺纹时,左刀刃的后角应比右刀刃的后角大一些。
车刀的副后角一般取其等于主后角。
切断刀及切槽刀的副后角,由于受其结构强度的限制,只能取得很小,0‘=1~2。
二、后面形状及选择
为减少刃磨后面的劳动量,提高刃磨质量,常把后面作成双重后面,b1取l~3mm。
1.刃带:
沿主切削刃或副切削刃磨出后角为零的窄棱面。
对定尺寸刀具沿后面(如拉刀)或副后面(如铰刀、浮动镗刀、立铣刀等)磨出刃带的目的是:
为了在制造刃磨刀具时便于控制和保持其尺寸精度,同时在切削时也可起到支承、导向、稳定切削过程和消振(产生摩擦阻尼)的作用。
此外,刃带对已加工表面还会产生所谓“熨压”作用,从而能有效降低已加工表面粗糙度值。
刃带宽度一般在0.05~O.3mm范围内.超过一定值后会增大摩擦,导致擦伤已加工表面,甚至引起振动。
2.消振棱:
沿着后面磨出负后角倒棱面,倒棱角01=-5~-10,倒棱面宽b1=0.1~0.3mm。
它可以增加后刀面与加工表面的接触面积,在切削时能产生同振动位移方向相反的摩擦阻力,不仅可以减小振动,也可对工件表面起一定的熨压作用,从而提高加工表面质量。
这是车削细长轴和镗孔时常采取的消振措施之一。
第三节主、副偏角及刀尖形状的选择
一、主偏角对切削加工的影响
1.对刀具耐用度影响很大。
随着主偏角减小,刀具耐用度提高。
这是因为:
(1)当背吃刀量ap和进给量f相同时,主偏角的变化将改变切削层形状,使切削层参数发生变化,从而影响切削刃上的负荷。
当主偏角Kr减小时,由于切削层公称宽度bD(=ap/sinKr)增加,切削层公称厚度hD(=fsinKr)减小,使作用在主切削刃单位长度上的负荷减轻。
(2)主偏角减小,则刀尖角r增大,使刀尖强度提高,散热体积增大。
(3)主偏角较小的刀具在切入时,最先与工件接触处是远离刀尖的地方,因而可减少因切入冲击造成的刀尖损坏。
2.影响切削分力比值及切削层单位面积切削力
当Kr减小时,由于hD减小,变形系数增大,使切削层单位面积切削力有所增大;在ap和f相同时,使切削功率有所增加。
但更主要的是会使背向力Fp增大,容易引起工艺系统振动。
当工艺系统刚度不足时,会使刀具寿命降低。
3.影响已加工表面质量
减小Kr进可以使工件表面残留面积高度减小,从而使已加工表面粗糙度值减小。
4.影响断屑效果、排屑方向
增大Kr会使hD增厚,bD减小,有利于切屑折断,有利于孔加工刀具使切屑沿轴向顺利流出。
二、合理主偏角的选择原则
由上述分析可知,无论增大还是减小主偏角,都产生相互矛盾的影响。
因此,在一定的切削条件下,主偏角也有一个合理数值,其主要选择原则为:
1.粗加工时,硬质合金车刀一般选用较大的主偏角(Kr=60~75),以利于减少振动、断屑和采用较大的切削深度。
2.加工硬度高的材料,如冷硬铸铁和淬硬钢时,在系统刚性好,切削深度不大时.取较小的主偏角(Kr=10~30),以利于提高刀具耐用度。
3.工艺系统刚性较好时,取较小的主偏角可提高刀具耐用度;刚性不足,加车削细长轴时,应取大的主偏角,可取Kr=90~93,以减小背向力ap,减少振动。
4.需要从中间切入及仿形加工的车刀,应取较大主偏角;车阶梯轴则需用Kr=90的偏刀;要用一把刀加工外圆、端面和倒角时可取Kr=45。
三、副偏角的功用及选择
1.副偏角Kr的作用:
减小副切削刃及副后面与已加工表面之间的摩擦。
副偏角Kr的大小主要影响刀具耐用度和已加工表面粗糙度。
1)Kr对刀具耐用度的影响:
由图可知,副偏角太小或太大刀具耐用度都不高,其存在着一个合理值。
这是因为副偏角过小会增加参加切削工作的刀刃长度,增大副后刀面与已加工表面间的摩擦,同时也易引起振动;而副偏角过大致使刀尖强度降低和散热条件恶化,结果会使刀具耐用度降低。
2)Kr对加工表面质量的影响:
在副偏角较小时,加工表面粗糙度值较小。
这是因为减小副偏角可减小残留面积高度,降低理论表面粗糙度值。
2.合理副偏角的选择原则
(1)一般刀具的副偏角,在工艺系统刚性较好,不产生振动的情况下,可选取较小的数值,如取Kr=5~10。
(2)精加工刀具的副偏角应取得更小一点,必要时,可磨出一段Kr=0的修光刃,车刀的修光刃长度取为b=(1.2~1.3)f,硬质合金端铣刀的b=(4~6)f。
(3)切断刀和切槽刀由于结构强度的限制,只能取很小的副偏角,Kr=1~3。
四、刀尖形状及尺寸选择
刀尖是切削刃上工作条件最恶劣、构造最薄弱的部位,刀尖处强度差,散热条件不好,故切削温度高、易磨损。
所以,强化刀尖可显著提高刀具耐用度。
同时刀尖部分的形状对已加工表面的粗糙度值也有很大的影响。
若采用减小主、副偏角的办法增强刀尖,常会使背向力Fp增大,引起振动。
若在主、副刃之间磨出倒角刀尖,即具有直线切削刃的刀尖,既可使刀尖角r加大,增强了刀尖,又可不使背向力增加许多。
刀尖处的过渡刃有:
1.圆弧形过渡刃
圆弧形过渡刃不仅可提高刀具耐用度,还可大大减小已加工表面粗糙度值,常在精加工车刀上采用。
刀尖圆弧半径对硬质合金和陶瓷车刀一般可取r=0.5~1.5mm,对高速钢车刀可取r=1~3mm。
适当增大r可减小刀具的磨损和破损;但r太大时,由于背向力Fp增大会引起振动。
2.直线形过渡刀
粗加工时,切削深度较大,为减小背向力Fp和振动,并使硬质合金刀片能得到充分利用,通常采用较大的主偏角。
但这时刀尖强度变差,散热条件恶化。
为解决这个矛盾,常常在刀尖处磨出直线过渡刃。
过渡刃偏角一般取为Kr≈1/2Kr,过渡刃长度b=0.5~2mm或b=(1/4~1/5)ap。
切断刀的b≈1/4B。
第四节斜角切削及刃倾角的选择
一、斜角切削的概念
1.直角切削:
刀具切削刃垂直合成切削运动方向的切削。
切削刃垂直主运动速度方向,或刃倾角s=0的切削。
2.斜角切削:
切削刃与合成切削运动方向不垂直的切削。
切削刃不垂直主运动速度方向或刃倾角s≠0的切削。
当只有一个切削刃进行的切削,称为自由切削。
在金属切削加工中,斜角切削是最普遍的。
二、刃倾角的功用
1.控制切屑流出方向。
如图是外圆车刀刃倾角s对排屑方向的影响。
可见,在精车时,希望取正刃倾角(+s).以使切屑流向待加工表面,防止缠绕和划伤已加工表面。
2.影响刀头强度及断续切削时切削刃上受冲击的位置。
如图是一把Kr=90刨刀的加工情况。
当s=0时,切削工作刃全长与工件同时接触,冲击较大。
当s为正值时,刀尖首先接触工件.容易崩尖。
当s为负值时,离刀尖较远的切削刃首先接触工件,保护了刀尖。
同时,切削面积在切入时由小变大,切出时由大变小,故切削过程比较平稳。
因此,在粗加工或冲击较大的加工中,常采用负刃倾角的刀具.负刃倾角车刀的强度较高,散热条件也较好。
3.影响切削刃的锋利程度。
当s0的斜角切削时,由于切屑在前刀面上流向的改变,使实际前角增大;同时,刃倾角增大还可减小刀刃的钝圆半径,使切削刃变得锋利。
如切下极薄切屑的精车刀、精刨刀多采用45~75的大刃倾角。
4.影响切削分力的大小。
当负刃倾角绝对值增大时,背向力Fp显著增大,将导致工件变形及引起振动。
刃倾角对刀具耐用度的影响如图所示。
在不同的加工条件下,也存在着一个合理数值。
三、合理刃倾角的选择原则
1.加工一般钢料和灰铸铁,粗车取s=0~5,精车时取s=0~+5;有冲击负荷时,s=-5~-15;当冲击特别大时,可取s=-30~-45。
2.加工高强度钢、高锰钢、淬硬钢时,可取s=-5~-15或负数的绝对值更大一些。
3.工艺系统刚性不足时,尽量不采用负刃倾角。
最后应该指出,刀具各角度之间是互相联系互相影响的。
孤立地选择某一角度并不能得到所希望的合理值。
例如:
改变前角将使刀具的合理后角发生变化,如图所示。
在加工硬度较高的材料时,为增加刀刃强度,一般取较小的后角。
但在加工特别硬的材料,如淬硬钢时,通常采用负前角,这时楔角已较大,如适当增加后角,不仅使切削刃易于切入工件,而且还可提高刀具耐用度。
刀具前角和刃倾角的选择也常常是互相影响的。
强力切削时,切削面积大,切削力也大,为强化刀刃,前角适宜取小一些。
但此时如采用太小前角会导致切屑变形太大。
可以采用较大前角,而同时采用负的刃倾角及负倒棱来强固刀刃;采用过渡刃来强化刀尖,从而达到满意的效果。
由此可见,任何一个刀具合理几何参数,都应该在多因素的相互联系中确定。
WelcomeTo
Download!
!
!
欢迎您的下载,资料仅供参考!