冷室压铸机打料培训教材.docx
《冷室压铸机打料培训教材.docx》由会员分享,可在线阅读,更多相关《冷室压铸机打料培训教材.docx(10页珍藏版)》请在冰豆网上搜索。
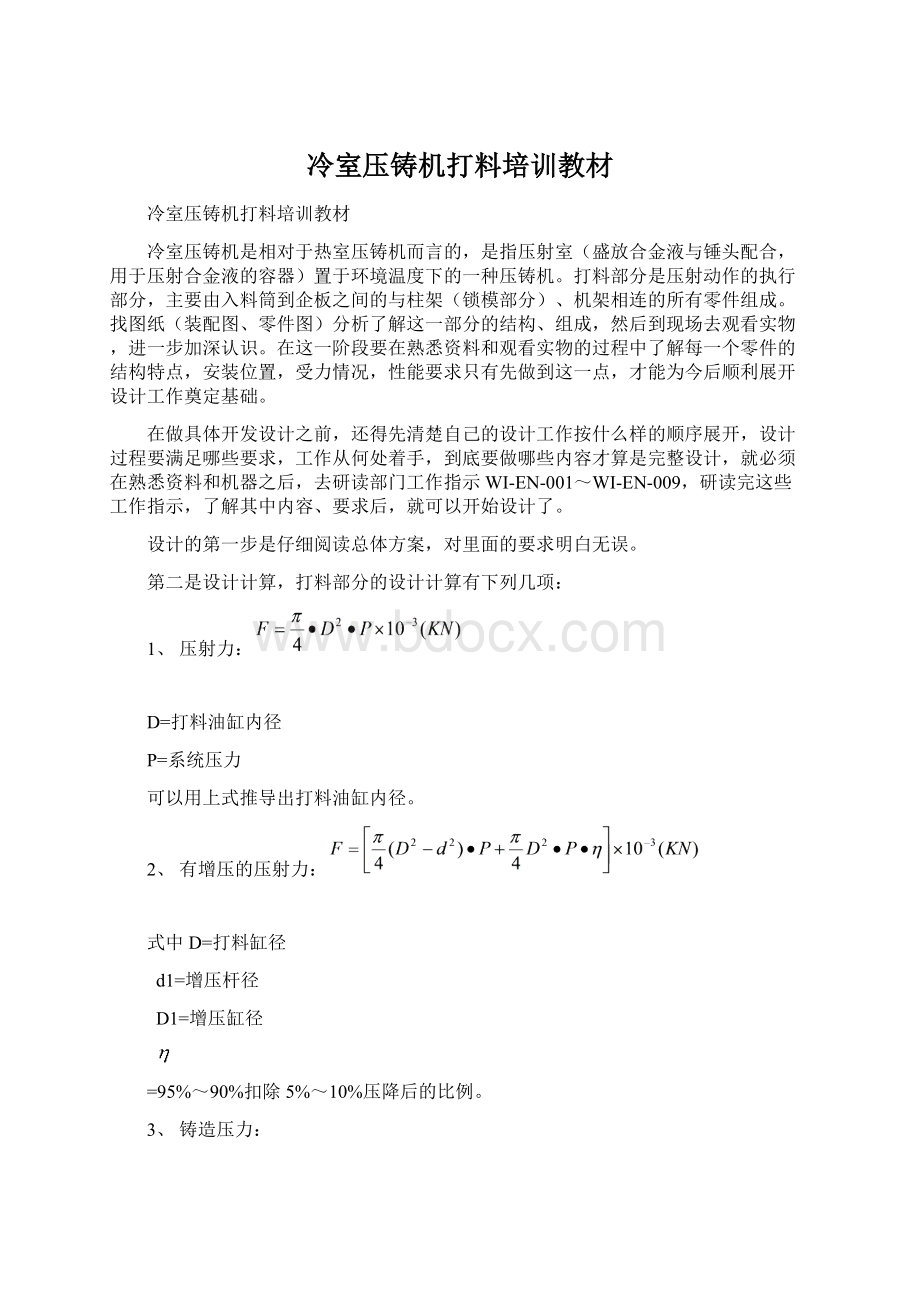
冷室压铸机打料培训教材
冷室压铸机打料培训教材
冷室压铸机是相对于热室压铸机而言的,是指压射室(盛放合金液与锤头配合,用于压射合金液的容器)置于环境温度下的一种压铸机。
打料部分是压射动作的执行部分,主要由入料筒到企板之间的与柱架(锁模部分)、机架相连的所有零件组成。
找图纸(装配图、零件图)分析了解这一部分的结构、组成,然后到现场去观看实物,进一步加深认识。
在这一阶段要在熟悉资料和观看实物的过程中了解每一个零件的结构特点,安装位置,受力情况,性能要求只有先做到这一点,才能为今后顺利展开设计工作奠定基础。
在做具体开发设计之前,还得先清楚自己的设计工作按什么样的顺序展开,设计过程要满足哪些要求,工作从何处着手,到底要做哪些内容才算是完整设计,就必须在熟悉资料和机器之后,去研读部门工作指示WI-EN-001~WI-EN-009,研读完这些工作指示,了解其中内容、要求后,就可以开始设计了。
设计的第一步是仔细阅读总体方案,对里面的要求明白无误。
第二是设计计算,打料部分的设计计算有下列几项:
1、压射力:
D=打料油缸内径
P=系统压力
可以用上式推导出打料油缸内径。
2、有增压的压射力:
式中D=打料缸径
d1=增压杆径
D1=增压缸径
=95%~90%扣除5%~10%压降后的比例。
3、铸造压力:
式中:
F=有增压的射料力
d=锤头直径
有几个锤头就要算几次。
4、铸造面积:
5、射料量计算:
式中:
d=锤头直径
L=射料行程
=合金密度
有几个锤头就要计算几次。
以上五个计算是打料部分固定的几个计算,在实际设计过程中还要经常用到各类计算,如各种零配件强度、校核计算等。
做完计算后,有许多零件的大小就可以初步确定,如:
缸筒选多大,某些零件的大小,固定螺丝的大小、个数等,有了这些就可以很快地将各零件的大小直接反映在方案图上。
在设计方案图时,除了要先进行必要的计算,另一方面要拿一个同系列同类型的现有机型打料部件图作参考,这样能提高作方案图的工作效率,同时也能避免出错。
做方案图时主要涉及零件尺寸的设计,零件尺寸都设计出来了,方案图也就出来了。
下面讲述各零件的设计方法,顺序以附图
(1)中的序号由小到大进行。
1、入料筒,安装位置见附图
(1)中的1,其中E是规格表中所述的压射室法兰直径,用于与模具配合,C是凸出头板高度,附图所示的是带升降的入料筒结构。
长度C+D+20-B
厚度=最大锤头直径时,最薄处单边厚度取20~35mm,如法兰直径与最大锤头直径相差很大时,单边厚度可略取厚些,这样切削量会小些。
配合部分的尺寸取整数。
其余选材和技术要求、精度要求见例图
(1)。
2、压射冲头:
也叫锤头,安装位置见附图
(1)中的2,其中20也是锤头伸进入料筒的长度。
锤头设计的注意事项有:
1)掏空后、前端壁厚不小于15,不大于20。
2)螺纹规格根据机器大小和与前后机型对比,尽量采用第一系列螺纹。
3)长度相对固定,1000T(含1000T)以下的长度为95,400T(含400T)以下的为90,1250T~1600T为120,2000T以下为150。
4)其余选材要求、结构同例图
(2)。
3、锤柄接头:
也叫锤柄,安装位置见附图
(1)中的3,它用来连接锤头和打料连接体,其设计要点有:
1)两端螺纹规格要相同,其余尺寸两头也相同。
2)中间大圆长度固定35,大圆直径D=最小锤头直径-2。
3)螺纹退刀槽处壁厚要合适,略小于大圆到定位圆的台肩宽。
4)选材和要求见例图(3)
4、打料连接体:
其装配位置见附图
(1)中的4,为一受拉、压及轴向冲击的杆件,设计要点:
1)要设计成中空用来运冷却水,也用来安装附图
(1)中的5,两头尺寸与锤柄和运水管座相配。
2)要安排冷却水进出接口,径向相差90°,轴向相距33,口径为1/4″。
3)长度根据附图
(1)中的D+30来确定杆部长度,(要减去锤柄长度和锤头部分长度。
外径D=锤柄大圆直径。
4)杆的尾部用定安排冷却水接管和安装定位用。
选材和要求见例图(4)
5、运水管组焊件:
由运水管和运水管座焊接而成,其总长的确定方法是:
管端距锤头前壁内侧10mm。
管座右端与打料连接体端面平齐。
装配位置见附图
(1)中的5,设计时,先定好总长和分别长度,再分别出各自的零件图。
样式见例图(5)
6、圆垫板:
装配位置见附图
(1)的6,其设计要点是:
1)外径与打料连接体大端外圆相同。
2)厚度比锤头伸入长度(20)大5、10、15,小机型取小值,大机型取大值。
3)厚度精度限制是将圆垫板装入后,连接件、打料连接体、圆垫板之间的轴向间隙在0.05~0.15之间。
其他选材和要求见例图(6)
7、连接件:
装配位置见附图
(1)中7,其设计要点是:
1)提供与打料连接体和打料活塞杆相配合的位置。
2)安排与连接板连接的螺孔,固定圆垫板的Φ9孔。
3)设计开槽,开槽方向和螺孔分布相对位置要明确。
4)活塞杆塞杆配合深度15、20、25、30、35,中间壁厚20、25、30,小机型取小值,大机型取大值。
5)装圆垫板的孔位直径比圆垫板大1。
选材和其他要求见例图(7)
8、连接板:
安装位置见附图
(1)中的8,作用是把打料活塞杆和连接件联接起来,同时与打料吉制连接,可带动连接杆起运动。
设计要点是:
1)厚度要遵循系列化的尺寸变化。
2)固定螺丝要匹配。
3)设开边环配合尺寸时要使连接板与连接件之间相隔0.2~0.3。
选材和其他要求见例图(8)
9、打料油缸底盖:
安装位置见附图
(1)中的9,主要用来作铜套的压盖。
设计要点:
1)零件上要安排尘封安装位。
2)固定螺丝的规格数量是以克服液压对铜套的推力。
3)与铜套的配合尺寸是以压紧铜套与缸盖的间隙要有0.1~0.2。
选材和其他要求见例图(9)
10、打料铜司:
装配位置见附图
(1)中的10,其用来支承活塞杆,设计要点是:
1)总长=1.5D,D为内径,也就是打料活塞杆杆径。
2)内孔上安排四条轴承带槽和两条油封槽,轴承带槽在两端,油槽中段,两油槽之间加一储油槽。
3)外圆上设计圆呤(O型密封圈)槽,靠大端壁厚处。
4)单边壁厚一般为15,内孔比杆大0.2,各槽的尺寸严格按标准件给定尺寸。
选材和其他要求见例图(10)
11、打料油缸盖:
也叫前缸盖,装配位置见附图
(1)中的11,设计要点是:
1)设计与铜司和油缸的配合尺寸,一般为H7。
2)设计油缸前腔压力油进出通道,根据液压部分的接口资料定。
3)定排各零件的联接孔。
选材和其他要求见例图(11)
12、打料吉制杆支承座:
安装位置见附图
(1)中的11,用来支承吉制杆。
设计要点:
1)吉制杆安装孔中心到底面高统一为30。
2)外形尺寸尽量与临近机型的通用。
3)安装编码器的座与不安装编码器的座,安装尺寸相同。
其他要求和样式见例图,例图(12)为可安装编码器的座。
13、打料吉制杆:
安装位置见附图
(1)中的13,作用是被近接制(感应开关)感应。
设计要点:
1)与吉制杆座配合部分直径为Φ
。
2)总长为与各零件的配合长度加上打料行程。
3)此杆分光杆和齿条杆两种,光杆适合感应开关,齿条杆适合编码器。
样式见例图(13)
14、打料缸套法兰
(1):
安装位置见附图
(1)中的14,它用来将前缸盖与缸套联接起来。
设计要点:
1)法兰的厚度和螺丝的大小个数要足以承受压射力,设计尺寸时要和前后机型作对比。
2)法兰的边缘不要超过前缸盖的外形,以免碰快排阀体。
要求和样式见例图(14)
15、打料缸套:
与打料缸套法兰
(2)焊在一起的叫打料缸套法兰组焊件,装配位置见附
(1)中的15。
设计要点:
1)内径以射料力换算得到,外径通过对比计算得到,同时考虑切槽和轴向工艺孔的影响。
2)外圆两头设计密封圈槽,与两头零件内孔配合精度定为g6。
3)与前缸盖配合长度比前缸盖配合深度大1,保证法兰
(1)装配时与前缸盖之间有1毫米间隙,配合长度一般为40、50、60、70。
4)长度上要满足打料行程、活塞长度、增压行程的要求,信号孔(缸壁上打的径向通孔)统一为Rc1/4,信号孔的位置处在打料活塞退到底和浮动活塞前进到头都盖不住的地方。
设计样式见例图(15)
16、打料活塞杆:
装配位置见附图
(1)中的16,由杆部和活塞部分组成。
设计要点:
1)杆部外径用f7精度,并镀铬,外径和内孔大小参照临近机型的尺寸,同时考虑回锤力的大小。
2)杆部前端与连接件相配,为装铜司方便,比杆部小2毫米。
3)在与连接件配合段的后边设计开边环定位槽,槽深以两者接触面压不大于1000bar为限,槽宽考虑系列化的尺寸。
并保证装配后连接板与连接件间有0.2~0.3的间隙。
4)活塞部分的长度一般为(0.6~0.8)D,(D为缸内径),上面安排四条耐磨环槽,一个油封槽,油封槽在中间。
各槽尺寸及外径按标准件要求尺寸给定。
5)内孔尾端要加堵头,堵头用螺纹旋进并烧焊,加焊接要求。
具体样式见例图(17)
17、导轨压板:
装配位置见附图
(1)中的17,主要用来压紧滑块座。
设计要点是:
1)其长度与企板上与相应凸台的长度相等,保证滑块在最高位和最低位时,外端仍有装一个螺丝的富余长度。
2)宽度和厚度及螺丝规格参考临近机型的尺寸,考虑系列化发展。
3)安装孔在宽度方向上要考虑力臂的合理分配,尽量往中靠。
设计样式见例图(17)
18、滑块座
(2):
具体装配位置见附图
(1)中的18,主要用来把缸套和油路系统联系起来。
设计要点:
1)在设计企板时就要考虑它的外形尺寸,一方面要与油路方面沟通,要能和油路板接得上,另一方面要把联接用的孔位布置下。
2)设计要紧凑避免外形过大影响企板尺寸。
与缸套的配合尺寸为H7。
3)长度一般比企板宽度大30左右,主要是为防止油路板上的阀碰到企板。
设计样式见例图(18)
19、企板:
装配位置见附图
(1)中的19,主要用来支撑打料系统和承受打料力的反作用力。
设计要点:
1)外形尺寸考虑系列化的尺寸变化加以控制。
2)多个打料位的企板开腔上下高度足够满足滑块座在不同位置上安装,上面间隙一般为10~15,下边位置一般留45以上间隙,以便接油管,上面间隙是指滑块座在最高打料位时上平面与开腔顶面间的距离,下面间隙道理相同。
3)滑块座与企板压紧后单边有效接触宽度为35~55,小机取小值,大机取大值,滑块座定位槽深一般为50~120,小机取小值,大机取大值。
侧向两者配合间隙为0.05~0.15。
4)企板要掏空,做成筋板式,筋板厚度和布局参考系列机型,并经强度验算。
5)大面加工余量要有7毫米以上,小面加工余量为5毫米。
根据具体位置和工艺特点安排。
选材及其他要求见例图(19)、(19A)
20、孔碟:
安装位置见附图
(1)中的20,主要用来对浮动活塞起限制作用,并能使浮动活塞复位,设计要点:
1)宽度一般为20~30,大径=打料缸内径-5~6mm。
2)保证强度的条件下,尽量加大均布孔的尺寸或个数以加大流通面积。
3)中孔与增压活塞杆配合。
见例图20
21、浮动活塞:
安装位置见附图
(1)中的21,它处在孔碟和套筒之间,主要与增压活塞杆配合起增压作用。
设计要点:
1)长度一般为(0.6~0.8)D,装配后与孔碟和套筒之间累计要有1mm间隙,外径以轴承带和油封与缸套配合。
2)内孔做成嗽叭型锥孔,小锥孔增压活塞杆锥面形成的最小圆台侧面积应不小于二速放油阀的通径,接触宽度3~4。
3)设计内孔时避免油槽底部壁厚太薄而破裂,一般不宜小于13mm。
选材及其他要求见例图(21)
22、套筒:
装配位置见附图
(1)中的22,它实际是与法兰轴承焊在一起,它的作用是保持浮动活塞的初始位置和避免液压油直接冲击浮动活塞。
设计要点:
1)大径比油路板相应位置孔径小1,内径与增压活塞杆之间的环隙保证有足够通径。
2)前端内孔设计成锥形,起导向作用。
3)长度要加限制,装配后保证前端不与缸套和浮动活塞发生干涉。
见例图(22)
23、增压活塞杆:
装配位置见附图
(1)中的23,它的作用其一是与浮动活塞配合在打料油缸中形成封闭腔起增压,其二是给打料活塞杆定位。
设计要点:
1)通过计算增压射料力的方法确定d1或直接根据总体方案确定。
2)与浮动活塞配合部分锥面的尺寸,需通过反复计算流通面积和闭合行程来确定,闭合行程要满足对建压时间的要求。
例图(23)锥面部分的大径大于要求的杆径,是为了加大通径的办法,常见的大径就是要求的杆径。
其他要求见例图(23)
24、法兰轴承:
装配位置见附图
(1)中的24,其作用一是支承增压活塞杆,二是为油路尾板提供定位基准,设计要点:
1)大径精度g6要求与中孔同轴。
2)固定螺丝有足够的安全系数承受系统压力,长度为1~1.2d1。
3)内外径都要密封,与油路板的配合精度为H7。
尺寸确定后给接口油路部分。
设计式样见例图(24)
25、增压活塞:
装配位置见附图
(1)中的25,与增压活塞杆连接用来传递增压力。
设计要点:
1)长度一般为90、100,直径由最大压射力换算而来或直接根据规格表要求定。
2)用螺纹和圆螺母与增压杆联接,要有足够的安装位。
见例图(25)
26、快排阀体:
安装位置见附图
(1)中的26,它由油路部分提供的资料接口(阀的型号规格)来确定尺寸,用来作压射时排油和回锤时进油用。
设计要点:
1)与油缸前盖的接触面要有密封,联接螺丝规格要合适。
2)安装用通过与内腔各孔不能互相干涉。
样式见例图(26)
27、回油管法兰组焊件:
安装位置见附图
(1)中的27,由四个法式零件和一根钢管组成,设计要点:
1)与快排阀体连接处要安排密封件。
2)钢管内径由最大空压射速度和管内流速不超过12米/秒,计算圆整得到,外径由内径加8~12后得到,管的长度要能在最低位置离机架底板200,在最高位能推进机架150。
3)靠近机架的三个法兰中,其一个焊在机架上,内孔比管外径一般大10~12毫米,压在中间的法兰要能够在水平方向滑动,间隙控制在0.1左右,法兰上要有防尘密封件及防飞料挡板。
设计样板见例图(27)
28、企板支承杆
(2):
装配位置见附图
(1)中的28,其作用主要是把压射系统和柱架部分联系起来,并承受最大压射力所形成的拉力和冲击,另外用来调校打料活塞杆和入料筒的同心度。
设计要点:
1)上下支承杆的装配位置要尽量使压射中心处于上下杆的中间部件,这样上下杆受力不会相差太大。
2)根据最大压射力乘1.3和极限压射位(最高、最低压射位)计算各杆所受的分力,然后用最大分力及弹性伸长量小于等于0.4mm,计算所需杆径。
考虑开料和加工余量取一个整数,即为最后各杆直径。
3)下杆为可调杆,两头采用正反旋螺纹,螺纹规格取最靠近杆径的第一或第二螺纹系列,螺距为2、3、4,小机选小值,大值选大值。
螺纹长度使螺母装配后与端面平齐(最好少一个牙)。
4)拉杆长度,以距头板、企板凸头平面1~2mm(取整)为准,凸台中的盲孔深一般为5~10mm。
5)两头螺丝后边要有退刀槽,宽40~60,台肩处圆弧过渡一般为R8~R10,槽底径=螺纹大径-螺距-2。
设计样式见例图(28)
29、支承杆座
(2):
装配位置见附图
(1)中的29,主要用来固定支承杆。
设计要点:
1)根据杆的受力大小选择合适的螺丝规格和个数,以此可确定外径。
2)以0.9~0.95倍的螺纹大径确定厚度。
设计样式见例图(29)
30、支承杆座:
安装位置见附图
(1)中的30,这是为方便调节而设计的,也起定位作用。
设计要点:
1)厚度一般为40~65。
定位止口长度为5毫米。
2)此零件只用于可调节杆的两头。
设计样式见例图(30)
31、企板支承杆:
安装位置见附图
(1)中的31,此杆主要起连接和定位作用。
设计要点:
1)压射系统其余零件全部确定好尺寸后,再确定这杆的总长,杆的两端面贴紧在头板,企板上的盲孔底面上。
2)杆的两端要求定位部分,比盲孔深长2毫米,杆径和下面两杆一般做成一样粗。
盲孔要有精度要求。
3)上杆的安装位设计时要考虑给汤手给汤时不发生干涉。
设计样式见例图(31)
32、企板厂型压板:
安装位置见附图
(1)中的32,主要用来限制企板左右位置和振动。
设计要点:
1)长度与企板厚相等。
2)侧面要求调节螺丝孔。
3)配合处高度方向上允许有微量间隙,一般为0.02~0.15,水平方向有1毫米间隙。
设计样式见例图(32)
33、连接板开边环:
装配位置见附图
(1)中的33,主要是用来把打料活塞杆与连接板、连接件联系起来。
设计要点:
1)宽度一般为15~35。
2)与活塞杆和连接板的垂直接触面一般为5~8mm。
设计样式见例图(33)
以上为打料部分主要零件的设计,当机器有2个或2个以上打料位置时,为便于装置在不同位置间上下移动,还必须有升降油缸作为动力来实现升降运动。
基本结构见附图
(2)。
设计要点:
1)油缸的大小要根据整个移动部分的重量、摩擦力、运动平稳性、可靠性来确定。
2)尽量安排固定在企板上,支撑位置要求处于重心位置。
3)油缸设计成单动作的,即顶出靠油压,退回靠自重。