最新硅酸钠泡花碱的可研报告.docx
《最新硅酸钠泡花碱的可研报告.docx》由会员分享,可在线阅读,更多相关《最新硅酸钠泡花碱的可研报告.docx(24页珍藏版)》请在冰豆网上搜索。
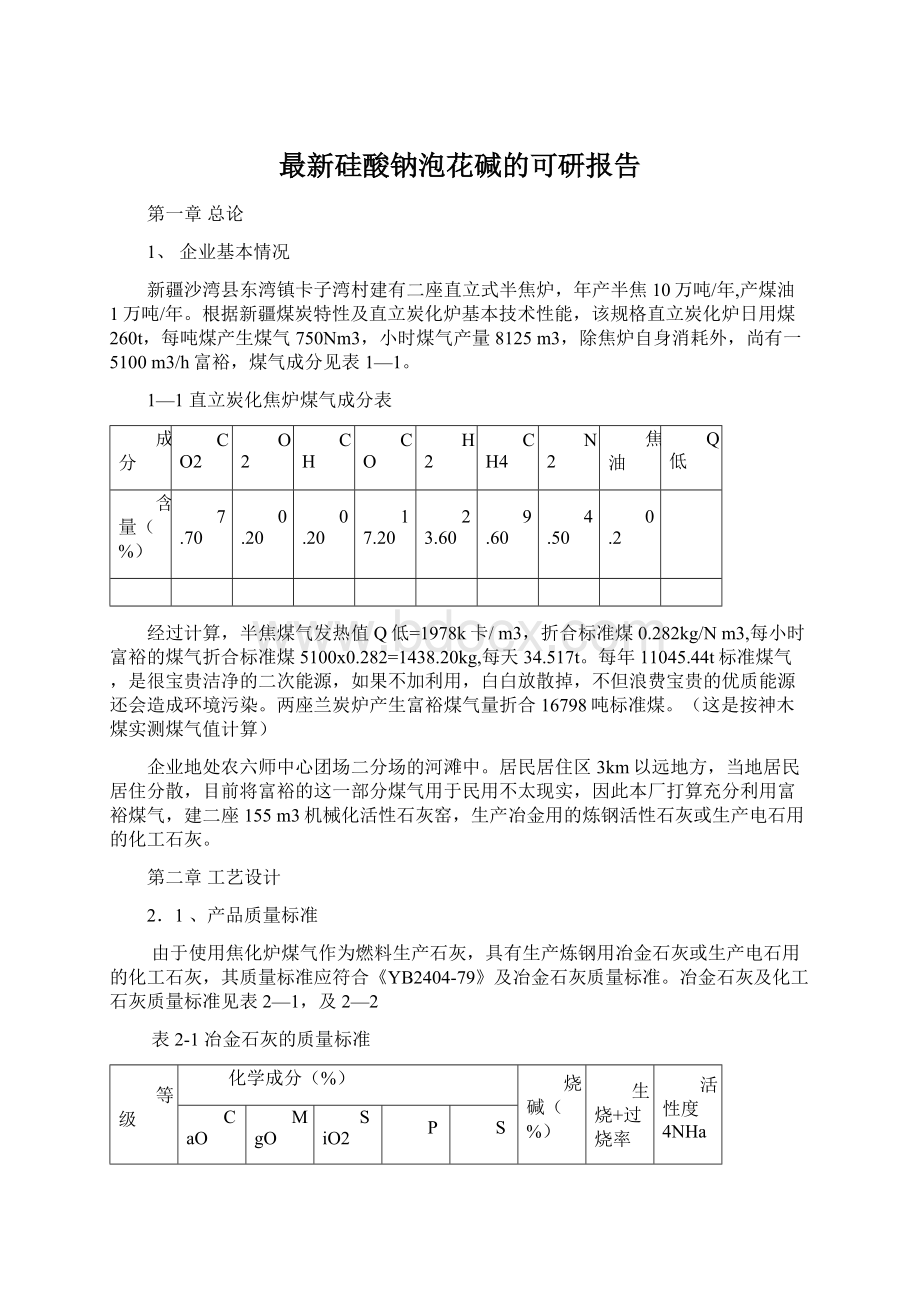
最新硅酸钠泡花碱的可研报告
第一章总论
1、企业基本情况
新疆沙湾县东湾镇卡子湾村建有二座直立式半焦炉,年产半焦10万吨/年,产煤油1万吨/年。
根据新疆煤炭特性及直立炭化炉基本技术性能,该规格直立炭化炉日用煤260t,每吨煤产生煤气750Nm3,小时煤气产量8125m3,除焦炉自身消耗外,尚有一5100m3/h富裕,煤气成分见表1—1。
1—1直立炭化焦炉煤气成分表
成分
CO2
O2
CH
CO
H2
CH4
N2
焦油
Q低
含量(%)
7.70
0.20
0.20
17.20
23.60
9.60
4.50
0.2
经过计算,半焦煤气发热值Q低=1978k卡/m3,折合标准煤0.282kg/Nm3,每小时富裕的煤气折合标准煤5100x0.282=1438.20kg,每天34.517t。
每年11045.44t标准煤气,是很宝贵洁净的二次能源,如果不加利用,白白放散掉,不但浪费宝贵的优质能源还会造成环境污染。
两座兰炭炉产生富裕煤气量折合16798吨标准煤。
(这是按神木煤实测煤气值计算)
企业地处农六师中心团场二分场的河滩中。
居民居住区3km以远地方,当地居民居住分散,目前将富裕的这一部分煤气用于民用不太现实,因此本厂打算充分利用富裕煤气,建二座155m3机械化活性石灰窑,生产冶金用的炼钢活性石灰或生产电石用的化工石灰。
第二章工艺设计
2.1、产品质量标准
由于使用焦化炉煤气作为燃料生产石灰,具有生产炼钢用冶金石灰或生产电石用的化工石灰,其质量标准应符合《YB2404-79》及冶金石灰质量标准。
冶金石灰及化工石灰质量标准见表2—1,及2—2
表2-1冶金石灰的质量标准
等级
化学成分(%)
烧碱(%)
生烧+过烧率(%)
活性度4NHa
40±1℃
10分钟
CaO
MgO
SiO2
P
S
优质
≥92
≤2
≤1
≤0.02
≤0.05
≤3
≤5
≥310ml
一级品
≥90
≤3
≤2
≤0.04
≤0.10
≤4
≤8
≥210ml
二级品
≥85
≤4
≤3
≤0.05
≤0.15
≤5
≤10
三级品
≥80
≤7
≤5
≤0.05
≤0.02
≤7
≤16
表2-2化工电石石灰的质量标准
成分
CaO
MgO
Fe2O3+Ae2O3
SiO2
P2O5
SO3
生过烧
含量
≥92
≤1
≤1
≤1
<0.008
<0.1
<6
石灰石粉度控制在20—100mm范围内
2.2原料及燃料
2.2.1原料
拟建石灰厂距石灰石矿25km左右,从矿内采出的石灰要在矿山进行破碎筛分。
粉度在20—100范围内,用汽车运回石灰石料场堆放。
2.2.2燃料
煅烧石灰采用焦炉煤气,煤气成分见表1-1.煤气低热值计算。
Q低=30.2CO+25.7H2+85.8CH4+142C2H4+55.3H2S
=30.2X17.2+25.7X23.6+85.8X9.6+142X0.2=1978千卡/m3
=8268KJ/m3
由焦炉来的煤气经过420X6mm煤气管道。
进入煤气加压站。
经加压后20000—21000Pa送至石灰车间,入窑压力为14000——16000Pa。
2.3工艺流程
2.3.1上料过程
合格程度的石灰石经汽车卸入受料槽。
再经原-1胶带机送人称量计(或人工推车、人工过磅)。
称量好的石灰石,放入料车提升机的1m3料车内;当料车升至窑顶时,窑顶料卸自动打开,料车内的石灰石随即倾入窑内,即完成一次上料过程。
整个上料过程均采用连锁控制。
2.3.2煅烧过程
进入炉内上部的石灰石随着石灰的排出而下降。
经上部预热带预热后,在900—1200℃的煅烧带煅烧。
石灰石中的主要成分碳酸钙受热分解,得到成品石灰。
成品石灰下移的过程中,经过窑下部冷却带,受到从窑底鼓入的冷风的冷却,燃烧过程结束。
窑内热量来自于从身侧已进入的煤气的燃烧。
进入窑内的空气分侧风(即一次风)和底风(即二次风),分别由各自独立的风机供给。
窑内各工作带均设有温度检测和气流压差检测,并设有料位探测装置。
2.3.3出灰过程
经冷却的成品石灰,经螺锥出灰机和星型出灰机排至链板输送机,送至斗式提升机至单层振动筛进行分级。
大于10mm的筛上物作为成品(冶金石灰或电石用石灰)进入灰仓储存;小于10mm的筛下物作为普通石灰进入普通灰仓,从而完成出灰过程。
为了保证进入灰仓的石灰质量,需石链板机尾捡选废品石灰(生烧、杂志等),将生烧部分返回原料。
2.4主要工艺设备及布置
2.4.1窑体
根据1号、2号窑的生产实践表明采用3.0米内径的竖窑,外径4.546m,有效高度为22.0m,有效容积为155m3。
上部和下部的窑内衬采用粘土质耐火砖,煅烧带采用高铝质耐火砖,外层为硅藻土隔热砖。
内衬与窑钢壳间采用高炉水渣填料。
2.4.2辅助设备
单独设置风机房,其内装3台风机,一、二次风分别由2台风机供给(2用1备)。
2.5主要生产技术指标
(1)年产量:
冶金灰:
34100t/a
普通灰:
2050t/a
全灰:
34150t/a
(2)年工作天数:
345天
(3)系数:
冶金灰0.6t/m3昼夜
全灰0.64t/m3昼夜
(4)综合合格率:
91%
(5)平均煤气耗量:
825标m3/t冶金灰
(6)石灰石粒度范围:
20—100mm
(7)石灰石消耗:
2.15t/t冶金灰
1X155m3白灰窑物料平衡见表2-3
表2-31X155m3白灰窑物料平衡图
序号
物料名称
工作班时
班X时
物料量
备注
年
昼夜
班
时
1
冶金石灰
3X8
32100
93
31.00
3.875
≥0mm
2
普通石灰
3X8
2050
5.94
1.98
0.2475
<0mm
3
检选欠烧
3X8
1020
2.745
0.99
0.124
返回原料堆场
4
储运损失
3X8
400
1.16
0.375
0.05
5
窑顶吹损
3X8
750
2.175
0.725
0.09
6
竖窑总出灰
3X8
36325
105.5
35.00
4.40
7
入窑石灰石
3X8
68240
168
66.00
8.25
序号
物料名称
工作班时
班X时
物料量
备注
年
昼夜
班
时
8
筛出石灰石
3X8
683
2.0
0.665
0.0835
9
进入原料堆场石灰石
3X8
68924
200
66.5
8
第三章竖窑热工参数
3.1竖窑结构参数
(1)内径3.0m
(2)外径4.546m
(3)全高29.1m
(4)有效高22.0m
其中预热带6.5m
煅烧带8.0m
冷却带7.5m
(5)高径比7:
33:
1
(6)烧咀2排,每排10个,上下排间距为2.0m
3.2竖窑热工参数(每座窑)
(1)石灰平均耗热5400KJ/kg灰
(2)煤气低发热值8268KJ/标m3
(3)平均煤气单耗:
冶金灰:
0.733标m3/kg灰
全灰:
0.65标m3/kg灰
(4)小时煤气耗量
平均:
3225标m3/h
最大:
4268标m3/h
(5)进窑煤气压力14000-18000Pa
(6)一次风量39-4500标m3/h
(7)二次风量2600-3000标m3/h
一、二次风比例6:
4
(8)一、二次风压力14000-15700Pa
(9)空气过剩系数1.1
(10)预热带温度400-1000℃
(11)煅烧带温度1000-1150℃
(12)冷却带温度1000-100℃
(13)窑顶压力0-500Pa
(14)窑顶烟气温度300-600℃
(15)烟气量13000-16500标m3/h
3.3.燃烧计算
3.3.1理论空气计算
每m3煤气理论干气量V千
V千=0.875K底/1000X1/4.18
=0.875X8268/1000X1/4.18
=1.731标m3/标m3气
(K低---煤气热值(KJ)
当鼓风温度为35℃时,V35:
V千=1.039,则在35℃时所需空气量V35为
V35=V千X1.039
=1.731X1.039
=1.80标m3/标m3气
3.3.2实际空气量计算
取空气过剩系数d=1.1,则实际空气量V实为
V实=1.8X1.1=1.98标m3/标m3气
小时鼓风量Q风为:
平均Q风均=3225X1.98=6386标m3/h
最大Q风大=4268X1.98=8450标m3/h
3.3.3烟气量计算
煤气燃烧所产生的烟气量V煤烟为:
V烟煤=0.725XX低/1000X1/4.18+10
=0.725X8268/1000X1/4.18+10
=1.434标m3/标m3气
1kg冶金灰啼生的CO2量VCO2为:
VCO2=1.947X1000/100X0.0224
=0.436标m3/kg
小时烟气量Q烟为:
平均Q烟为=1.434X3225+0.436X3875
=6314标m3/h
最大Q烟大=1.434X4268+0.436X133
=7922标m3/h
3.4竖窑切砖
窑内径3000mm,外径4546mm,内衬厚度761mm。
其中工作厚度466mm,标高13.5m以下和标高21.5m以上部分砌N-1粘土砖。
转的规格为TZ-3和TK-81;标高13.5m—21.5m部分砌LZ-65
高铝砖,以延长窑衬寿命。
砖的规格为TZ-3和TK-81。
保温层厚230mm,用GG-0.4硅藻土硅,规格为TZ-3和TK-81。
硅藻土砖与钢壳之间采用高炉渣填实,厚度为65mm。
窑顶采用耐热混凝土衬顶。
窑衬用材(一座炉)
(1)高铝砖90.0t
(2)粘土砖140t
(3)硅藻土砖30.0t
第四章总图运输
4.1、总图运输平面布置
两座石灰窑建在一个厂区,厂区土地比较富裕。
一座石灰窑占地50X50=2500m2,具体平面待到现场进行考察后再定。
场地排水采用自然排水。
4.2、工厂运输
每座石灰窑年运入石灰石8.0X104t,全部汽车运输,运出石灰3.5x104t,汽车外运。
所有气运全部组织社会车辆运输。
在场内需配置装载机一台,用于经受料槽转运石灰石。
第五章供配电
5.1电源及传动
一座石灰窑用电设备装机容量约400KW。
按满负荷考虑,由焦化厂统一考虑电源,用电设备全部是低压。
用电设备(380V和220V)年用电150X106KWh,各选一台S1—560/10,6KV/0.4Kv变压器。
在窑旁设一个低压配电室,配电室面积为4.5X6m,所有用电设备一律实行手动操作。
5.2、照明
各生产工段照明采用白炽灯,配电操作室采用茨光灯。
根据要求在有利位置设置安全电压照明插座。
5.3、防雷及接地
车间电气外线采用变压器中性点直接接入地运行方式,正常时外表面带的用电设备均采用保护接零方式。
窑炉及厂房需防雷
防雷接地与电气接地供用一套接地外线,其接地电阻值≤4Ω
第六章给水排水
6.1、给水
6.1.1、水源
供水在水源地由管道输送经计量后流入厂内贮水池,经水泵加压后送至厂内环状给水管网供给用户使用,
6.1.2、车间用水要求
表6-1车间用水要求见表
序号
用户名称
用水量(m3/h)
用水制度
水压(Pa)
水质
备注
最大
平均
1
窑顶冷却水箱
12
6
连续
0.34
工业水
2
矿石喷水
2.5
2.5
连续
0.2-0.3
工业水
3
地坪洒水
5
5
间断
0.2-0.3
工业水
4
操作室用水
1
1
间断
0.2-0.3
生活水
5
站房地坪用水
0.5
0.5
间断
0.2-0.3
生活水
6
其它用水
1
1
间断
0.2-0.3
生活水
小计
22
16
7
消防用水
27
0
合计
【答案】人工管理阶段,文件系统管理阶段,数据库系统管理阶段49
2.如果要在屏幕上直接看到查询结果,“查询去向”应该选择________。
16
ifc>max1
fori=1to6
A.SELECT产品名称,AVG(单价)FROM产品GROUPBY单价
max1=a
?
"maxtomin:
",max1,max2,min(a,b,c)6.1.3、给水系统
return6.1.3.1、石灰窑窑顶水箱直流给水系统
C.末记录的后面D.首记录的前面石灰窑窑顶水箱供水为直流给水系统,水量平均12m3/h。
窑顶冷却水箱标高为31.1m,为了保证水箱安全给水,每座窑设加压泵一台,选用IS-32-200A水泵,Q=12m3/h,H=39m,配用Y112-2电机,N=4kw,共计设水泵电机各两台,(其中一用一备),设置在窑前水泵房内。
窑前水泵房尺寸为:
LXBXH=4500X3500X4000mm;水泵吸水井尺寸为:
LXBXH=6000X2000X500mm.
窑顶冷却水箱供水,根据工艺要求,采用自动控制,当水箱水温超过80℃时,发出信号或警报,排水管上的气动薄膜阀开启放水,水泵自动启动供水;当水箱温度低于50℃时,水位达到正常高度时,水泵停止工作,自控部分见电器和计器专业说明。
为节约能源和水资源,窑顶冷却水箱用水为间接冷却用水,用后水,只是水温度升高至80℃左右,未受任何其他污染;可排入浴室,作为浴室补充水,不直接外排。
6.1.3.3、生活给水
C.将恢复所有被逻辑删除的记录D.只能恢复被物理删除的当前记录生活给水全部入焦化厂统一考虑,本设计不增加内容。
6.1.3.4、消防给水
管网水压0.3MPa,管网上设地上式消火栓。
火灾按一次考虑,消防总水量20L/s,内部消防水量15L/s,火灾延续时间按2小时计算,消防水容积144m3。
火灾时,消防车由厂内给水管网上消防栓或贮水池取水加压灭火。
6.2、排水
6.2.1、生产排水
窑顶冷却水箱的热水,排至浴室,做浴室补充水。
其他生产排水,就近排入室外排水管道。
单斗提升基地坑积水和车间内低洼处积水,本设计选用WQ-6型作业潜水电泵一台,Q=8.5m3.h,H=18m,P=1kw.定时把地坑内的积水抽至室外明沟。
6.2.2、生活排水
生活污水由焦化厂统一考虑。
仍就近排入室外下水道。
6.2.3、雨水
车间及场地的雨水排出由焦化厂统一考虑。
第七章通风除尘
7.1、概述
车间的通风除尘根据《建设项目环境保护设计规范(YB9066-1995)》《工业炉窑大气污染物排放标准(GB9078-1996)》等标准和规范进行设计。
达到车间内空气中粉尘的最高容许浓度6mg/m3和通风除尘系统排气筒的排放浓度不大于150mg/m3的目的。
设计所用气象条件按国家对新疆沙湾县的有关气象参数确定。
7.2、主要设计决定
7.2.1、竖窑烟净化系统
石灰竖窑烟净化,目前国内仍无十分可靠的方法。
本设计根据和舞阳钢铁厂等单位的生产实践,结合其他窑炉烟气处理经验,决定采用以下流程:
80—110℃
窑顶烟气—→机力空冷器——————横扁袋除尘
野风阀
器——→锅炉引风机。
实践证明,只要烟气能降低到合适的温度,采用袋式收尘器处理石灰竖窑烟气是成功的。
因此关键在于选择好烟气冷却在装置。
设计选用机力空冷器的目的在于,降低空冷器的重量、提高冷却能力,而且便于通过调节冷风量来达到控制烟气温度(80-110℃)的目的。
要尽量避免使用野风,以节生除尘器过滤面积和风机能耗,降低造价,设计不考虑用于防止烟气,结露而采用的加热措施,烟气结露情况在正常生产中应该很少出现,当其出现时,言气中含尘浓度不高,可采取短暂的直排方式以防除尘器虑袋粘堵。
每座竖窑设一个烟气净化系统、其主要设备是
(1)风机Y5-48No10C,风量25982m3/h,风压4450Pa,功率75kw.
(2)除尘器HBF—VⅢ/H型。
处理风量2880m3/h,反吹时过滤风速m/min。
除尘端阻力小于1300Pa,除尘效率大于99%,装机容量3.16kw,该除尘器结构紧凑。
维修工作量小、换袋极为方便,除尘器运行更为稳定可靠。
(3)机力空冷器为并联二通道式,冷却面积450m2,空冷用轴流风机4台,总重量14.8t
7.2.2、环境粉尘除尘系统
C—1系统,两台星形出灰机向链板输送机卸料时产生
大量粉尘,此处设置抽风罩抽尘。
本系统总处理风量1000m3/h,选4—79NO5A风机一台,功率15kw.选HBF—VI/I除尘器一台,过滤面积180m2。
C—2系统,本系统处理链板机卸料,电振机给料,斗提机(上、下)抽风等处粉尘。
处理风量10400m3/h。
风机除尘器选型同C—1。
C—3系统,本系统处理振动筛,胶带机受料,三个料仓抽风等处粉尘,处理风量9900m3/h,风机、除尘器选型C—1。
C—4系统,本系统处理三个料仓给汽车卸料所产生的粉尘。
因三个仓卸料不同时进行,故考虑用电蝶阀控制其抽风点。
系统总处理风量9600m3/h。
风机、除尘器选型同C—1。
C—1系统除尘器及风机设置在竖窑9.5m平台上,所收集的粉尘定期排至运行中的链板机上。
C—2—C—4的除尘器机设置在成品料仓顶层、他们所收集的粉尘定期子流至粉料料仓。
为防止C—1系统个别红粒料进入布袋除尘器而烧毁布袋、设计决定在布袋除尘器前设置粒颗沉降箱。
7.3车间通风及空调
(1)为排出竖窑机房的余热,风机房墙上安装2台T35NO4轴流风机排风。
(2)竖窑操作室和除尘操作室各安装一台LFD—6分体式空调器,制冷制热量均为700W.
(3)竖窑平台等处设置移动式轴流风机LF038NO6共4台,做人体降湿用。
第八章热力设施
8.1、竖窑鼓风
根据工艺专业的计算、每窑要求供风量为800—1000m3/h,按6:
4的比例分为一次、二次风分别送入窑内。
为便于这两次风的风压控制,设计决定这两次风自成系统,即每窑各用两台风机、两路风管单独供风。
由于一、二次风一个要求风量略高、风压略低,另一个要求风量略低、风压略高。
经校核计算,二者可用同种型号风机。
该风机为H10—13—11NO7.5A,风量4865—6980m3/h,全压14945—14131Pa,功率37kw,同时使用同型号风机2台,另选一台同型风机备用。
为减轻鼓风机房的噪音的影响,设计决定由土建对风机房做吸声墙等隔音设施,同时在一次风的风机进出口处装上ZH2-55-120消声器(2台)。
每台风机入口装可调电动蝶阀,由竖窑操作室根据炉况进行点动控制。
8.2蒸汽和压缩空气
8.2.1汽源及设计范围
蒸汽和压缩空气均由焦化厂现有的锅炉和压缩空气站供给。
本设计只考虑了车间内部的煤气管理的清用蒸汽管道和压缩空气管道。
8.2.2压缩空气
压缩空气的消耗量(见下表):
序号
用户名称
用户点个数
使用压力(Mpa)
消耗量(M3/min)
使用制度
备注
单个
合计
1
称量料斗气动闸
3
≥0.4
0.5
1.5
间断
伐
2
成品料仓气动闸
3
≥0.4
0.5
1.5
间断
平均小时开启次数为
伐
3次
3
废石料仓气动闸
1
≥0.4
0.5
0.5
间断
平均小时开放次数为
伐
2次
4
抓料吊车吹扫
1
≥0.4
0.8
0.8
间断
每周吹刷一次,每次
15分钟
小计
4.1
考虑同时使用系数0.8,综合消耗量
3.28
8.2.3蒸汽消耗量
本工程的蒸汽仅供煤气管道清扫,其消耗量为180kg/h,压力为0.6Mpa,用气制度为间断用汽;气源由已有焦化厂锅炉房提供。
第九章煤气加压站
1、概述
每座竖窑平均耗焦炉煤气为3225标m3/h,最大耗量为4268标m3/h,煤气入窑压力为14000~16000Pa。
2、煤气加压站
石灰车间内部增设煤气切断和排水设施,及入窑煤气压力和流量检测手段,选两台D100~1,2363/1,05668型加压机一台备用煤气管道¢426x6,从焦炉煤气总管送至煤气加压站,煤气经过加压后再送往石灰窑。
第一十章工业自动化
10.1、设计内容
本工程设计为一座155m3煤气燃烧竖窑之热工控制。
其设计内容包括以下系统的热工检测及自动控制;
(1)、一座155m3煤气燃烧石灰竖窑
(2)、三台离心式鼓风系统;
(3)、两台煤气加压机系统;
10.2、设计原则
(1)为防止6煤气进入操作室而引起事故发生,有关煤气压力测量和流量测量,均采用压力或差压变送器配相应二次仪表指示或记录,且将变送器装于现场。
(2)由于现有煤气热值波动较大,故本设计中煤气—空气配比自动调节,而采用了遥控操作,远方手动调节煤气与空气配比。
(3)对部分温度测点,采用巡回检测仪。
(4)对原料、成品、燃料设有必要的计量器,并累计、指示。
(5)为确保生产安全,设置必要报警的联锁系统。
10.4、仪表选择
(1)单元组合仪表均采用为DDZ—Ⅲ型电动单元仪表。
(2)各项煤气压力检测均采用微压力变压器一、二风压及窑顶压力测量,采用YSD—3型电感式微压变压器。
(3)温度就地指示,采用双金属温度计。
(4)测温一次部件采用普通热电阻或热电偶,流量测量节流装置采用标准孔板(无室)。
(5)指示仪表采用数字显示仪,记录仪表采用ER记录仪。
(6)进窑石灰石和成品石灰称量采用电子秤显示,机械累积或打印。
10.4、备注检测项目
10.4.1、竖窑、风机系统
(1)该系统检测控制项目包括烟气、预热带、煅烧带、冷却带温度检测;煤气、一、二次空气压力及流量检测。
(2)本系统煤气空气配比采用DFQ—1000型操作器配伺服放大和2AJW6电动蝶阀组成软手操作系统,可根据窑温手动操作进炉煤气、空气流量。
(3)窑顶水箱设有高低水温报警。
(4)进窑煤气设有低压发讯,并参与电器联锁,自动关闭煤气阀,同时打开放散阀。
(5)石灰石称量设有空、满料发讯,参与电器联锁。
10.4.2、除尘器系统
两除尘系统皆设有进除尘器烟气温度检测报警联锁。
通风机前温度检测,除尘器前后差压检测、记录及报警联锁。
10.4.3、仪表室及盘箱
(1)竖窑及风机系统之仪表设在操作平台,要求采光,防尘良好,层高4.5m,面积36m2,水磨实地面,油漆墙裙,内置三块柜式仪表盘,规格为2100X800X900。
面对竖窑一列安装。
(2)除尘系统采用两块柜式仪表盘,规格为2100X600X900。
第十一章土