常催机泵变频调速节能改造技术经济分析与评价最终版.docx
《常催机泵变频调速节能改造技术经济分析与评价最终版.docx》由会员分享,可在线阅读,更多相关《常催机泵变频调速节能改造技术经济分析与评价最终版.docx(8页珍藏版)》请在冰豆网上搜索。
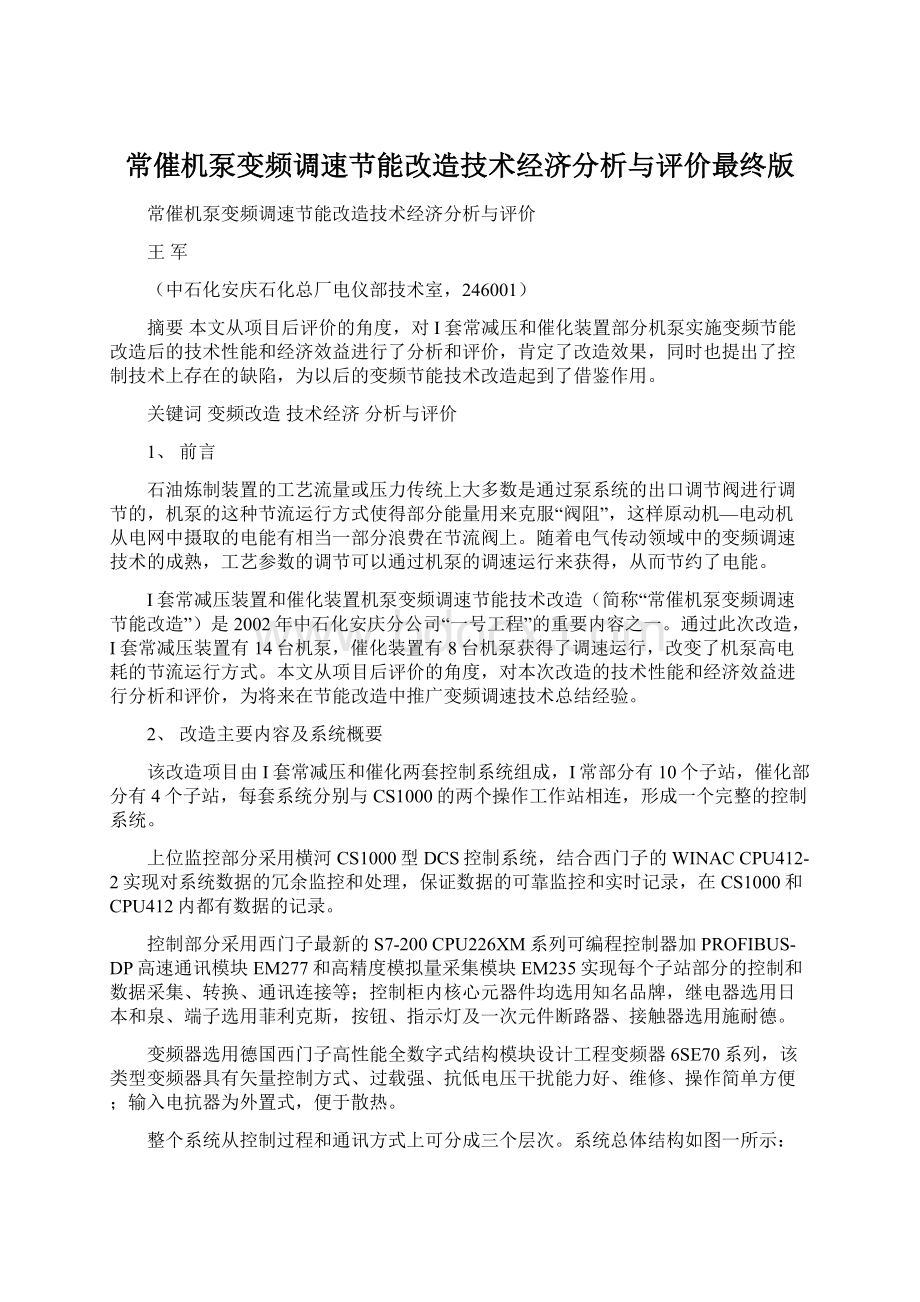
常催机泵变频调速节能改造技术经济分析与评价最终版
常催机泵变频调速节能改造技术经济分析与评价
王军
(中石化安庆石化总厂电仪部技术室,246001)
摘要本文从项目后评价的角度,对I套常减压和催化装置部分机泵实施变频节能改造后的技术性能和经济效益进行了分析和评价,肯定了改造效果,同时也提出了控制技术上存在的缺陷,为以后的变频节能技术改造起到了借鉴作用。
关键词变频改造技术经济分析与评价
1、前言
石油炼制装置的工艺流量或压力传统上大多数是通过泵系统的出口调节阀进行调节的,机泵的这种节流运行方式使得部分能量用来克服“阀阻”,这样原动机—电动机从电网中摄取的电能有相当一部分浪费在节流阀上。
随着电气传动领域中的变频调速技术的成熟,工艺参数的调节可以通过机泵的调速运行来获得,从而节约了电能。
I套常减压装置和催化装置机泵变频调速节能技术改造(简称“常催机泵变频调速节能改造”)是2002年中石化安庆分公司“一号工程”的重要内容之一。
通过此次改造,I套常减压装置有14台机泵,催化装置有8台机泵获得了调速运行,改变了机泵高电耗的节流运行方式。
本文从项目后评价的角度,对本次改造的技术性能和经济效益进行分析和评价,为将来在节能改造中推广变频调速技术总结经验。
2、改造主要内容及系统概要
该改造项目由I套常减压和催化两套控制系统组成,I常部分有10个子站,催化部分有4个子站,每套系统分别与CS1000的两个操作工作站相连,形成一个完整的控制系统。
上位监控部分采用横河CS1000型DCS控制系统,结合西门子的WINACCPU412-2实现对系统数据的冗余监控和处理,保证数据的可靠监控和实时记录,在CS1000和CPU412内都有数据的记录。
控制部分采用西门子最新的S7-200CPU226XM系列可编程控制器加PROFIBUS-DP高速通讯模块EM277和高精度模拟量采集模块EM235实现每个子站部分的控制和数据采集、转换、通讯连接等;控制柜内核心元器件均选用知名品牌,继电器选用日本和泉、端子选用菲利克斯,按钮、指示灯及一次元件断路器、接触器选用施耐德。
变频器选用德国西门子高性能全数字式结构模块设计工程变频器6SE70系列,该类型变频器具有矢量控制方式、过载强、抗低电压干扰能力好、维修、操作简单方便;输入电抗器为外置式,便于散热。
整个系统从控制过程和通讯方式上可分成三个层次。
系统总体结构如图一所示:
第一层:
现场控制和现场数据采集
这一层主要实现现场动作的完成和现场相应数据的采集过程,是整个控制系统的底层部分。
该层与上二层通过通讯相连组成了一个整体,又可独立运行。
第二层:
现场数据的传送和集中处理
这一层主要实现将现场数据分别通过切换柜上的14个PLC从站采集,将现场采集的数据分成I常10个站和催化4个站分别集中送入两块WINACSLOTPLC412-2DP内,集中处理,同时,上位机的操作也通过两块WINACSLOTPLC412-2DP传送到14个PLC站,再到现场。
第三层变频调速系统与CS1000的连接和CS1000系统的监控
这一层主要实现现场网络系统与CS1000监控系统的连接,CS1000系统的监控画面和菜单结构采用西门子WinAC技术实现与CS1000的连接。
总之,在此次变频改造中采用了多项先进控制技术,实现了与仪表DCS的有效连接,从而可以在CS1000的操作平台上同时实现实时监控变频调速系统的运行情况和生产工艺的流程状况。
3、技术性能及其评价
3.1、系统可维护性较好。
该系统在设计之初就考虑到系统的可维护性,通过软件设计配置了诊断查错程序,通过报警窗口等界面,帮助维护人员查找故障原因,缩短排除故障的时间。
3.2、系统可扩性较好。
该系统采用了PROFIBUS(ProcessFieldBus)现场总线,作为开放式通信系统工业标准,PROFIBUS现场总线公布了网络各层协议的所有规范,按照这些规范设计网络接口,不同厂家设备可以实现网络互连,因此基于PROFIBUS现场总线的系统其扩展性更方便。
3.3、通过设置“本地”和“远程”控制方式,提高了系统控制可靠性。
为了避免后台机监控失效,造成系统失控,在设计时就考虑了配置常规控制手段。
系统将后台监控定义为“远程”控制方式,将控制柜和现场操作柱上的操作定义为“本地”控制方式。
当远程控制失效时,可切换到“本地”控制方式,继续实施对系统的有效控制。
3.4、主回路采用了动态切换技术,节约了一次性投资。
在工艺上,机泵的设置常常采用一开一备的方式,对此,在机泵变频调速节能改造中,若各配置一台变频器,当然能够满足工艺安全性和可靠性的要求,但投资增加了一倍,而且变频器的利用率也不高。
而采用动态切换技术,只需配置一台变频器,便可实现“一拖二”功能,减少了投资,提高了变频器的利用率,也能满足一定可靠性要求。
对于工艺上单一机泵(无备机),通过采用动态切换技术,亦可以提高工艺可靠性。
动态切换技术是指一台变频器通过不停机切换可使二台互为备用的机泵分别实现调速运行,或不停机实现变频回路和工频回路之间的切换(参见图二)。
图二“一拖二”动态切换主回路
动态切换技术是通过PLC的用户程序结合工频接触器、变频接触器控制回路来实现的。
为了确保在切换过程中工频、变频不同时运行,控制回路以及用户程序中均通过接触器接点实现互锁。
在本地控制状态,动态切换的启动按钮(SB9或SB10)的动作值(1或0)通过PLC的输入触点(I0.6或I0.7)存于PLC的输入映象寄存器中。
对于远程控制状态,动态切换的控制通过数据通讯将其动作值存储于PLC内部位存储器(M)的标志位中。
在程序启动动态切换时,变频器自动上升到50Hz这一过程的实现,是利用变频器本身的二速运行功能,对变频器的二速参数设定为50Hz,其二速运行控制端子2DF置位后,变频器自动上升到50Hz运行,变频器输出触点(UPF,OCM)动作,频率到达继电器KA吸合。
用户程序在扫描到频率到达信号(I0.5=1)后,延时1S,变频器复位(R/M端子置位)停机。
该系统PLC控制回路如图三所示。
图三PLC控制回路
需要说明的是,当要动态切换到工频运行时,为了保证工艺的平稳运行,工艺操作人员可以通过DCS监控程序击活对调节阀的闭环控制,以调节工艺参数。
相反,当机泵投入到变频调速运行时,工艺操作人员亦可以通过DCS监控程序全开调节阀后封锁对调节阀的闭环控制。
该系统PLC用户程序是用梯形图设计的,梯形图简单易学易懂,便于维护。
有关动态切换的程序从用户程序或称为主程序(MAINPROGRAMER)中节录出来附后,并且为了便于理解,笔者对程序的每一步都进行了注释。
通过注释不难理解动态切换控制的实现过程。
动态切换技术充分发挥了变频器的使用效率,较之一台变频器控制一台机泵的方案,节省了一次性投资。
I套常减压装置的P108/1、2,P125/1、2,P104/1、2,P126/1、2,催化装置的P301/1、2,P302/1、2,P304/1、2,P308/1、2共计16台机泵通过“一拖二”控制方式实现了变频调速运行,减少了8台变频器的投资,虽然由于为了实现“一拖二”动态切换控制功能,在主回路和控制回路均增加了相应的投资,但相比之下,整个项目一次性投资仍然因此节约了近80万元。
动态切换技术虽然节约了投资,但有时会出现在切换过程中过流跳闸现象,造成工艺波动。
经过分析,造成配电空气开关有时跳闸的原因是:
在电机脱离变频器往工频切换的瞬间,电机处于发电状态,其定子绕组感应电动势为50Hz交流电势,与切换瞬间变频器的输出电压同相位。
如果变频器输出电压与工频输入电压相位同步,那么在切换瞬间电机投入到工频电网中就不会产生瞬时过电流。
但实际上两者常常出现相位差,使得与变频器输出电压同相位的电机感应电动势与工频电网之间存在着电压向量差,这个差值是随机的,最恶劣的情况是,相位
相差180度,这时电压差瞬时值可达2*1.414*220=622V,可以想见,在电机
投入工频电网的瞬间流过工频回路的电流会有多大,足以使空开瞬时跳闸。
这就解释了为什么在切换瞬间工频回路的配电空气开关有时会跳闸,而有时又不会跳闸的原因。
4、经济效益及其评价
通过此次改造,变频调速运行的机泵电耗较之改造前均有不同程度的下降,尤其I套常减压装置机泵改造后运行频率始终处在35Hz以下,节电效果显著,使得整个装置的电耗因此有了较大的下降。
2003年4月,I套常减压装置对装置增容改造(即所谓的“一号工程”)后的能耗进行了标定。
通过标定,得到如下数据:
表一全装置能耗
名称
消耗
标定
能耗
设计
能耗
2002年度能耗
单位
数量
每吨消耗
KgEO/t
KgEO/t
KgEO/t
电
KWh
67065.4
6.644
1.993
2.158
2.319
注:
此表摘自《I套常减压装置能耗测定总结》
从表一可见,在装置增容改造后部分机泵功率增大的情况下,装置电耗却较之2002年度下降了0.33KgEO/t。
在《I套常减压装置能耗测定总结》报告中分析认为,在装置增容后,电耗反而下降的主要原因,应归功于机泵的变频节能改造。
催化装置的8台机泵变频调速改造后,运行频率基本上在35Hz-42Hz区间波动,虽然有一定的节电效果,但相对于I常装置的机泵来讲,不甚理想。
究其原因,是改造前对催化装置不同工艺位置机泵的节电潜力论证不够充分,缺乏科学有效的论证方法。
机泵变频调速技术改造实现了机泵的调速运行,泵、阀门等泵系统中的元件磨损、冲击大大降低,无形中延长了使用寿命;其次,提高了装置工艺操作的自动化程度,降低了操作波动机率。
这是节电效益之外的无形效益。
5、结论
常催机泵变频调速节能技术改造采用了计算机分布式控制系统,实时监控,界面友好;现场总线开放,扩展性好;“本地”和“远程”冗余控制方式,提高了系统控制的可靠性。
总之,技术先进,提高了工艺操作的自动化程度。
从投资经济角度,采用简单投资回收期法做一个简单的保守的投资效益测算。
年节约电能:
0.33KgEO/t÷0.299KWh/KgEO*400万吨/年=441.5万KWh
年节约电费:
441.5万KWh*0.35元/KWh=154.5万元
(注:
我厂有自备电厂,0.35元/KWh是我厂内部电价。
)
简单投资回收期:
T=300万元/154.5万元=1.9(年)
在以上计算中,变频调速改造后节约的电能采用I常装置改造后较之2002年度下降的电耗0.33KgEO/t,实际上,因变频调速改造节约的电能应该高于此值。
如此保守计算,投资回收期仍不到两年。
可见,常催机泵变频调速节能技术改造投资回收期短,经济效益可观。
本次改造不足之处有二,供后续项目借鉴。
一是动态切换可靠性不高,其技术有待进一步改进。
解决这个问题的技术路线有:
选择带同步锁相功能的变频器,或者在工频回路中设置限流电抗器,以抑制切换大电流。
二是催化装置的机泵变频调速改造后节电效果不甚理想。
这告诫我们,在以后此类项目实施前,应制定科学有效的论证方法,选择最具节电潜力的机泵进行变频调速节能改造,以期获得最大投资效益。
参考文献:
1、余人杰,俞光昀,高祖纲.计算机控制技术.西安交通大学出版社,1989年1月.
2、唐济杨.现场总线(PROFIBUS)技术应用指南.中国现场总线(PROFIBUS)专业委员会,1998,11.