导管钢围堰施工方案.docx
《导管钢围堰施工方案.docx》由会员分享,可在线阅读,更多相关《导管钢围堰施工方案.docx(16页珍藏版)》请在冰豆网上搜索。
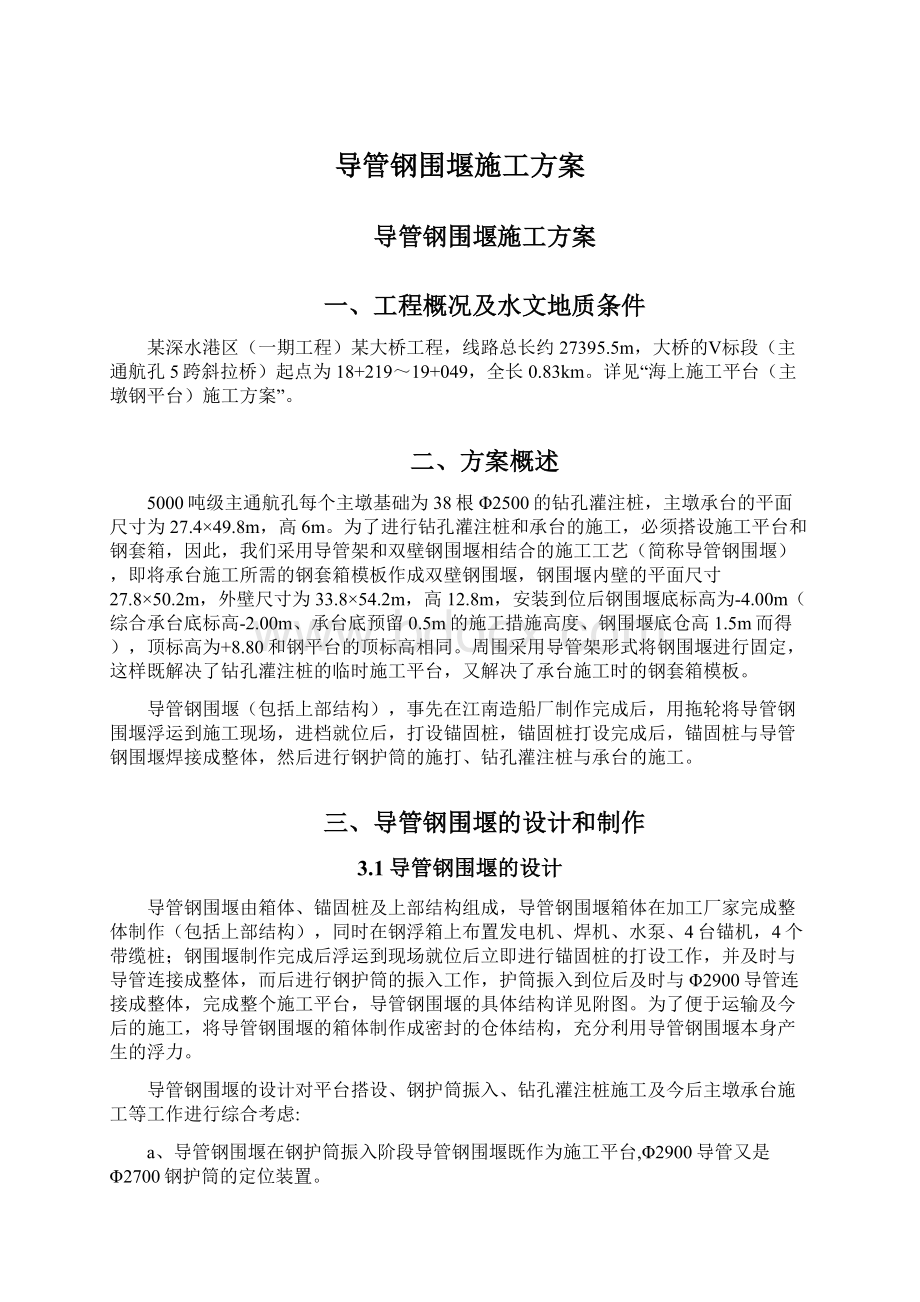
导管钢围堰施工方案
导管钢围堰施工方案
一、工程概况及水文地质条件
某深水港区(一期工程)某大桥工程,线路总长约27395.5m,大桥的Ⅴ标段(主通航孔5跨斜拉桥)起点为18+219~19+049,全长0.83km。
详见“海上施工平台(主墩钢平台)施工方案”。
二、方案概述
5000吨级主通航孔每个主墩基础为38根Φ2500的钻孔灌注桩,主墩承台的平面尺寸为27.4×49.8m,高6m。
为了进行钻孔灌注桩和承台的施工,必须搭设施工平台和钢套箱,因此,我们采用导管架和双壁钢围堰相结合的施工工艺(简称导管钢围堰),即将承台施工所需的钢套箱模板作成双壁钢围堰,钢围堰内壁的平面尺寸27.8×50.2m,外壁尺寸为33.8×54.2m,高12.8m,安装到位后钢围堰底标高为-4.00m(综合承台底标高-2.00m、承台底预留0.5m的施工措施高度、钢围堰底仓高1.5m而得),顶标高为+8.80和钢平台的顶标高相同。
周围采用导管架形式将钢围堰进行固定,这样既解决了钻孔灌注桩的临时施工平台,又解决了承台施工时的钢套箱模板。
导管钢围堰(包括上部结构),事先在江南造船厂制作完成后,用拖轮将导管钢围堰浮运到施工现场,进档就位后,打设锚固桩,锚固桩打设完成后,锚固桩与导管钢围堰焊接成整体,然后进行钢护筒的施打、钻孔灌注桩与承台的施工。
三、导管钢围堰的设计和制作
3.1导管钢围堰的设计
导管钢围堰由箱体、锚固桩及上部结构组成,导管钢围堰箱体在加工厂家完成整体制作(包括上部结构),同时在钢浮箱上布置发电机、焊机、水泵、4台锚机,4个带缆桩;钢围堰制作完成后浮运到现场就位后立即进行锚固桩的打设工作,并及时与导管连接成整体,而后进行钢护筒的振入工作,护筒振入到位后及时与Φ2900导管连接成整体,完成整个施工平台,导管钢围堰的具体结构详见附图。
为了便于运输及今后的施工,将导管钢围堰的箱体制作成密封的仓体结构,充分利用导管钢围堰本身产生的浮力。
导管钢围堰的设计对平台搭设、钢护筒振入、钻孔灌注桩施工及今后主墩承台施工等工作进行综合考虑:
a、导管钢围堰在钢护筒振入阶段导管钢围堰既作为施工平台,Φ2900导管又是Φ2700钢护筒的定位装置。
b、钻孔灌注桩施工时作为施工平台,在箱体内分隔成若干单元,作为今后钻孔灌注桩时的泥浆箱。
c、承台施工时作为主墩承台的模板及支撑结构。
导管钢围堰参照中国船级社《钢质海船入级与建造规范》(2001年版)设计、计算。
导管钢围堰定位后对以下工况进行计算。
工况1抛锚定位时浮箱自浮状态。
工况244根Φ1000钢管桩打入后强度计算(波浪按中浪取值)。
工况3钢护筒打入后强度计算(波浪按20年一遇5.57m浪高取值),上部
荷载4t/m2。
工况4承台砼浇筑后强度计算。
工况5体系转换后(未浇砼前)强度计算(波浪按5.57m浪高取值)上部
荷载0.2t/m2。
3.2导管钢围堰的制作
3.2.1制作场地的选择
导管钢围堰外形平面尺寸为54.24m(长)×42.4m(宽)×12.80(高)m,自重加甲板上设施共计约3000吨。
导管钢围堰的制作场地应考虑将来导管钢围堰的运输,因此选择在上海江南造船厂的船坞制作。
3.2.2总体制作方案
根据钢围堰的设计要求和结构特点,钢围堰在江南造船厂内1号船坞和3号船坞制造。
总体结构分为58个分段和若干散件,分段的划分如下表所示。
分段部位
分段号
分段数量
双层底
201-214
14个
艏艉
401-408
8个
舷侧
301P-308P,301S-308S
16个
甲板
101-114,115P-117P,115S-117S
20个
舷侧导管
L26
散装
舱壁
F15、F51、L12、圆弧板
散装
钢围堰制造采用零件拼装,分段组装,船坞总装的工艺流程。
板材下料后,首先在加工车间进行边缘加工、零件轧制、加工成型工作。
然后根据车间施工布置转移到生产平台,安排合理的施工工装设施,进行分段拼装、焊接及分段检验。
分段成型后转移到船坞,进行总段合拢。
钢围堰整体施工完成后,进行最终检验,包括尺寸验收、焊接检验和密性试验。
待检验合格后,出坞靠泊码头,安装附属设施。
最后由驳船拖运出海,运输至施工现场。
3.2.3放样、下料及加工
3.2.3.1放样
(1)按照施工设计图纸和施工工艺的要求,采用计算机进行放样,以确定各个零部件的精确尺寸,确定钢管相贯线结构。
(2)按放样尺寸,做出各种角度样板和下料样板。
(4)绘制零件草图、编制数控程序和编套料图,绘制钢管相贯线图,供下料用。
3.2.3.2下料
(1)平直构件可采用门式切割下料,不规则板采用数控或半自动切割下料。
(2)钢管相贯线采用相贯线切割机下料,也可采用样板手工下料。
3.2.3.3加工
(1)φ2900直缝管下料加工边缘,每节一个单元在三芯辊轮上进行卷制成型,注意保证圆弧曲率。
(2)相贯线采用相贯线切割机或手工火焰切割加工,需现场定尺的相贯线采用手工火焰切割。
(3)压筋板数切下料后,进行翼缘轧制。
3.2.4双层底分段制作
双层底分为14个分段,制作时可根据场地情况进行连体组装,一般可采用201-207作为一组,208-214作为另一组,分段之间采用搭焊方式临时固定,做到一个连体分段组之间无余量制作。
首先制作平面胎架,以舱底板为基准进行正造。
骨材及桁材先焊于舱板上,以平面板单元形式进行分段组装,以提高装焊效率。
φ2900导管需进行拼板成管形,导管长度方向以原材料宽度为基准尺寸进行划分,一般定2600mm宽度为一节。
每节最多允许拼两条纵缝,注意节与节连接时纵缝应错开至少300mm。
双层底分段制作完成后,分拆各个分段进行编号,划出对合线,注意不同组的分段应留有分段余量。
运送至船坞或堆场,准备进行总装。
3.2.5艏艉分段制作
艏(艉)分段由于高度较高,宜于采用侧卧式制造。
每段共有4个分段组成,可安排生产场地两个一组或四个一组进行连体制造。
以F2(F64)水密舱为基准面铺设水平胎架,划出钢围堰纵中中心线。
各个水密舱板、实肋板的骨材可在组装车间装焊形成板单元,分段组装均以板单元形式供货安装,对于φ1100导管及其连接板可以散件形式,在分段组装时提供。
分段成型后注意应保留对合线,留出分段余量,待总装定位使用。
3.2.6舷侧分段制作
舷侧分段结构与艏艉分段类似。
应注意舷侧分段与舷侧导管之间有穿管连接。
制作时要保证分段中心线的定位。
穿管位置及腹板位置可在分段制作时划出,留待总装时再开孔安装穿管。
3.2.7舷侧导管分段制作
舷侧导管与导管架结构较为相似,制作时可以L26为胎架基准面进行单榀管结构拼装,注意保证中心线位置。
根据场地起重能力及总装吊运要求,可将导管结构分为4个分段,分段之间的连接管以散件提供,留待总装定位。
注意散件两段相贯节点留有余量,现场用手工方式开出。
3.2.8甲板分段制作
上甲板共有20个分段组成,考虑到高度高结构软,采用反造法制造。
下部导管可只留1500mm,余下长度到船坞进行散装。
与双层底分段制作方法类似,各个分段之间以搭焊方式连接进行连体组装。
一般按101-107、108-114、115S-117S、115P-117P分为四组制造。
首先制作平面胎架,以上甲板为基准面首先定位,安装甲板纵横骨架。
定位φ1100、φ2900导管,注意导管定位应加斜撑撑住,防止歪斜。
分段完成后进行划对合线、标记工作,注意保留分段余量,运送至堆场或船坞进行总装。
3.2.9船坞总装
根据钢围堰形体及硬档位置排放座墩,调整座墩高度保持同一水平。
从艉到艏先安放双层底分段,切割分段余量后检验、焊接。
安装双层底人孔盖、扶梯等附属设施。
再顺序吊装尾部分段、两侧舷侧分段及首部分段。
将F15、F51、L12、圆弧板、导管等散件吊装到位,定位检验及焊接。
继续吊装两侧舷侧导管分段,散件固定安装。
最后吊装上甲板分段,检验后焊接。
安装甲板人孔盖、扶梯等附属设施,完成结构制造。
四、导管钢围堰的施工工艺
根据现场施工进度,导管钢围堰的施工顺序为:
先进行PM335墩钢平台的钢围堰施工,然后进行PM336墩钢围堰施工。
4.1导管钢围堰的运输
导管钢围堰在船坞制作完成后,利用导管钢围堰本身的浮力拖运(钢围堰内不加水),用拖轮吊拖到施工现场,拖运前必须取得海事部门同意。
根据计算,钢围堰在浮运时吃水深度1.96m。
由于导管钢围堰尺寸较大,根据钢围堰设计要求可在中浪状态下拖运,为了保证运输安全,应选择在海况较好的天气进行导管钢围堰的拖运工作。
经计算导管钢围堰自浮工况下的吃水深度在1.96m左右,在1.5m/s水流作用下,长边(54.0m)迎流时的水流力约为15t,短边(33.8m)迎流时的水流力约为9t。
经计算,钢围堰在浮运状态时稳性衡准数Kf=31,符合要求(稳定计算详见附页)。
4.2导管钢围堰的定位、安装
导管架钢围堰的定位、安装需浮吊协助。
安装流程:
4.2.1导管架钢围堰的临时系泊
钢浮箱由拖轮拖到现场后由拖轮协助将钢围堰临时系泊在350t浮吊边上。
若气象条件较差无法进行下一步工作则先将钢围堰单独锚泊,待天气好转后再系泊到浮吊边上。
4.2.2导管架钢围堰拖运及就位
a、限位装置的安装
为了能使钢围堰精确定位,事先在钢围堰两端的导管架平台侧面安装限位装置,安装位置在导管架第二层水平支撑(+2.312),两侧限位装置安装好后留有54.90m的空档,详见附图。
b、钢围堰的初定位
钢围堰初定位利用350t浮吊及“建基1502”工作船进行。
导管钢围堰拖运时机选在落潮期间,当流速小于1.0m/s时进行钢围堰的浮运作业。
通过绞动350t浮吊上的锚机,将钢围堰缓慢地推移到已安装好导管架平台的中间,并将围堰上的锚机抛锚。
绞动钢围堰上的锚机使钢围堰两角上的钢管桩分别紧贴1#、2#导管架平台上的限位装置,同时马上将3#、4#导管架平台上的限位装置推出50cm并将两个角限位翻下进行焊接,将钢围堰的平面位置固定,竖直方向则可随着潮水的涨落而上下移动。
限位装置根据导管架实测平面位差,由工厂预制后现场安装。
限位装置设在导管架第二层水平支撑位置(标高+2.312m),由型钢和橡胶护舷组成。
其中西侧限位架即1#2#导管架上的限位架在进档架安装好,东侧限位架的护舷在进档前可以自由伸缩,进档时留有60cm的间隙,以保证围堰进档。
进档后,将护舷推出50cm,使围堰与护舷留10cm间隙后焊接固定。
限位装置与围堰每边条均留有10cm的间隙,即围堰外包尺寸为33.8×54.2m,限位装置内净尺寸为34×54.4m。
详见附图。
C、注水下沉
钢围堰水平初定位完成后,用锚机临时系泊,然后进行注水下沉。
打开钢围堰的进水阀门(进水量400-800立方/小时),使各进水仓进水,待钢围堰达到平衡时关闭进水阀门,继续用水泵往各进水仓加水,将钢围堰下沉3.7米后,使钢围堰浮在水中(此时钢围堰吃水5.86m,顶标高在平均高潮位+1.86时达到设计标高+8.80,需加水5757t,围堰内各进水仓的水深为5.03m)。
钢围堰在拖航前,在围堰四角及围堰内舱均画吃水标志线,注水时观察好各舱的吃水深度,保证围堰注水后水平,必要时用水泵调整舱内水位,控制四角高差不大于5cm(平潮时)。
4.3锚固桩的施工
锚固桩采用Φ1000、壁厚20mm,长度为47m的钢管桩。
结构详见附图。
4.3.1钢管桩的制作、装船及运输
钢管桩由专业制作单位制作,长度均可一次性加工成47m,制作好的整根钢管桩在码头装船运至现场。
4.3.2钢管桩的施打
导管钢围堰注水下沉就位后,利用350t浮吊马上进行插桩、打桩,350t浮吊插桩时机选择流速小于1.5m/s时进行。
全部钢管桩插桩、打桩工作由350t浮吊完成。
钢管桩施打先打一侧,然后浮吊移到另一侧施打。
钢管施打时,应尽量保证桩身垂直度,并用调整舱内水位的方法控制围堰垂直度。
插桩宜在落潮时进行,以使即使浮箱有倾斜,桩身与围堰基本呈同一角度。
在进行钢管桩施工时,应由外向内逐渐插桩,施打时亦应由外向内打到设计标高。
4.3.3沉桩控制
画桩:
用油漆在桩上每一米位置画上刻度线,桩顶最后一米每10厘米画线,以便记录最后贯入度。
钢管桩整根制作、整根吊装和打设,钢管桩顶标高为+9.30m,标高控制按±0~±50mm范围控制。
4.3.4钢围堰标高调整并与桩连接
钢管桩施打后,应用水准仪在+8.8m处画出标志,并以标志为基准在钢管桩上焊接限位牛腿。
限位牛腿是钢管桩与围堰焊接时的标高限位措施。
每根钢管桩上设计2只牛腿,牛腿抗浮能力为56t/只。
限位牛腿应在两个相邻高平潮间完成焊接工作。
限位牛腿焊接后,可在高平潮进行钢管桩与围堰的连接。
当高平潮时,围堰会随着潮位的上涨而顶住钢管桩上的限位牛腿,同时将钢围堰和限位装置间的间隙,钢管桩与钢围堰间的间隙用钢板或钢楔填实,即进行钢管桩与围堰的连接,详见附图。
焊接应在高平潮时完成10个钢管桩的焊接,然后随着潮位的下落,用水泵在13#舱内抽水,并打开9#~17#舱(13#舱除外)的阀门,使海水内外连通,并继续进行围堰与桩的连接,待全部焊接完成后,打开13#舱阀门。
4.4导管钢围堰与导管架平台的连接
锚固桩打设完成并与导管钢围堰连接完成后,进行导管钢围堰与导管架平台的连接及上部结构的安装工作。
4.5钢护筒施工
钢护筒用厚16mm的钢板卷制而成,直径为2700mm,总长43m。
钢护筒顶部和底部各1m范围用14mm厚钢板作加强箍(详见附图)。
设计底标高为-33.70m,顶标高为+9.30m,入土约23米,竖向承载力为260t(考虑安全系数为2)。
土层
摩阻力KPa
厚度(m)
面积(m^2)
承载力(KN)
3.1
10
4.82
40.88
408.85
4.1
15
8.78
74.47
1117.12
5.1
35
6.83
81.43
2027.69
6
65
1.75
14.84
964.86
7.11
75
1.02
8.65
648.90
合计
23.200
5167.42
5167.42KN合527.29吨
钢护筒的防腐要求按照设计要求进行,钢护筒焊接要求必须符合二级焊缝的要求,制作完成后进行超声波探伤检测。
钢护筒运至施工现场后,质监人员须对钢护筒的直径、圆度和焊接质量进行验收,验收合格后方可进行施工。
用350t浮吊进行钢护筒的起吊和施打,护筒的施工应选在平流阶段进行,减少水流对护筒埋设的垂直度的影响。
护筒施打前,根据导管钢围堰实际偏差在Φ2900导管内设限位装置以保证护筒位置及垂直度。
钢护筒打设采用350t浮吊靠钢围堰一侧全部打完的办法(最远时利用辅钩
2,此时吊臂仰角55°、回转半径49.3m、扬程54.8m、吊重45.87t),每根护筒打设完成后,立即进行护筒与导管钢围堰的连接。
钢护筒插桩结束后,可解除钢围堰上的锚机。
钢护筒与围堰的连接完成后,钢围堰内舱阀门可根据施工需要打开或关闭。
4.6钻孔灌注桩施工
钻孔灌注桩施工方案另报。
钻孔桩施工时,9#~17#舱室可作为泥浆沉淀池。
允许泥浆储放高度为4m,但应以浮箱中心对称储放。
4.7堵漏、抽水及体系转换
4.7.1堵漏
抽水前,在进行导管与钢护筒之间的堵漏工作,堵漏工作由潜水员水下作业。
Φ2700护筒与Φ2900导管之间的堵漏采用哈夫式抱箍与不分散细石膨胀混凝土相结合的施工工艺。
具体方案另报。
4.7.2抽水
用水泵抽除围堰内水(泥浆),沉渣则用人工清理后外运。
4.7.3体系转换
Φ2700护筒与Φ2900导管之间的堵漏工作完成后,在Φ2900导管底部圆周上割开八个30cm宽,高60cm的焊接孔,凿除导管与钢护筒之间的堵漏砼,用连接板与钢护筒和底板焊接,再用钢板使连接板与导管焊接,详见附图。
完成体系转换后,即可按附图进行导管、钢护筒的割除,并凿除钻孔桩上部砼,进行承台施工。
4.8垫层与承台施工
1、体系转换完成后,在导管钢围堰箱内底板以上铺设35cm厚的砂层(标高为-2.50~-2.15),然后浇筑15cm厚的C10混凝土(标高为-2.15~-2.00),但须根据封堵效果而定。
2、承台施工:
承台施工方案另报。
五、项目组织机构
六、质量保证措施
6.1质量控制目标
导管钢围堰加工平面尺寸控制精度±10mm。
导管钢围堰就位平面位置偏差按150mm控制。
沉桩过程中,桩尖按标高控制贯入度校核,锚固桩标高误差±0~±50mm。
钢平台横向承重主梁必须连续布置,节点按固端处理。
钢平台所有的焊缝应满足设计要求,表面严禁有裂缝、夹碴、焊瘤、烧穿、弧坑、针状气孔和熔合性飞溅等缺陷。
6.2质量保证体系
严格按照ISO-9001体系文件及相关文件,实现质量目标。
测量放线应有放样和复核验收二道工序,内业计算亦由二人计算后校对复核。
工地专门设立质量管理小组,工地质量员负责对每个工序进行质量检查。
工程材料必须要有数量、质量、规格及材料检验报告(质量合格证书及产品合格证书)。
建立工地质量检查网络,制定质量检查制度,建立计量网络,定期对计量器具进行校验。
6.3质量保证措施
6.3.1测量控制点的建立及复测
1、导管钢围堰两侧导管架安装形成后,在每个导管架平台上设置两个测量控制点。
2、测量控制点位置设置醒目的标志,严禁任何物体碰撞控制点。
3、定期对测量控制点进行复核,每次的复核结果报技术部门备案。
4、测量控制点受碰撞后必须马上进行复核。
6.3.2导管钢围堰制作及安装
导管钢围堰加工平面尺寸控制精度±10mm。
导管钢围堰焊接用的焊条、焊剂、焊丝等焊接材料在施工前,按其说明书进行烘焙和存放。
导管钢围堰在加工时必须精确放样,由于在今后钢护筒振入施工时,φ2700钢护筒插入钢围堰φ2900导管内,因此在导管钢围堰加工制作时必须保证精度。
由于管钢围堰是承重结构,而且箱体又是密封的仓体,因此在加工制作时必须确保电焊质量,所有的焊缝均应符合设计要求,在各部件隐蔽前必须经加工方质量工程师认可并取得委托方驻厂代表同意。
导管钢围堰安装就位偏差应控制在150mm内。
6.3.3钢管、钢护筒运输和堆放
堆放形式和层数应安全可靠,避免产生纵向和局部压曲变形。
运输过程中必须绑扎牢靠,确保运输安全。
管节在起吊、运输和堆放过程中,应尽量避免由于碰撞、摩擦等原因造成管节变形和损伤。
6.3.4沉桩施工控制
钢管桩(钢护筒)起吊前应复核长度,壁厚、直径是否与图纸一致。
沉入过程中若发生突然下沉,桩身倾斜应立即停打并通知工程部,研究处理办法。
七、安全保证措施
7.1安全管理和保证体系
工程项目经理部实行项目经理负责制,对项目工程的安全负全面责任。
项目经理是本项目的安全生产第一责任人,全面负责本项目的安全生产工作。
项目部建立安全生产管理机构,配备足够的安全管理人员,全面负责本项目的安全生产管理工作,确保安全管理目标的实现。
7.2施工前的安全管理措施
1、所有海上施工船舶都应有气象和海洋环境图和船舶抛锚方位图。
大中型机具设备包括船舶要有安全操作规程。
所有水上施工人员应佩带好安全帽和救生衣。
特殊工种必须持证上岗,并有安全员巡视检查。
2、项目部和施工船只每天收听当地气象台颁布的气象、海浪预报,及时掌握和了解施工水域海况,提前采取各种应急措施。
3、各类船舶的海上施工通讯保障措施、避风措施、、消防措施、防污染措施以及管线保护措施详见“海上施工平台(主墩钢平台)施工方案”。
4、导管架钢围堰制作、运输、安装安全保证措施
导管架钢围堰制作时应采取可靠措施保证导管架构件的稳定。
运输过程中,导管架应用钢丝绳与船体绑扎牢固,并事先应获得海事、安全部门认可。
启航前,与港监交管中心加强联系,确实掌握航道内的有关气象资料及其他船舶航行信息。
控制船位、船速,用安全航速航行,并做好应急准备。
到达指定锚地抛锚之后,应按规定发出锚泊声号。
5、打桩安全保证措施
施工时专人负责,操作、指挥人员持证上岗。
每天工作前,对吊机及夹具、索具进行安全检查,确保安全施工。
吊机操作、指挥,应严格按安全规程执行,分工明确、精力集中、信号明确,不得随便离开岗位。
吊桩作业应指派专人统一指挥,参加吊桩的起重工要掌握作业安全要求,其他人员要有明确分工。
沉桩前须检查各项准备工作、起重设备和施工机具,并在正式施工前进行试运转。
起桩时,要检查吊点是否牢固,索具、卸扣使用是否正确,围绳是否牵紧,正确无误后才能继续作业。
起吊时,速度要均匀,构件要平衡,回转要慢,下落时需慢速轻放,禁止忽快忽慢和突然制动,做到密切配合,动作协调。
所有现场工作人员必须正确佩戴安全帽,指挥、操作时,不得吸烟。
严禁在六级以上大风、暴雨、雷电、大雾天气施工作业。
八、文明施工保证措施
建立、健全安全生产责任制,分部分项工程有安全与技术交底,特殊作业工种必须持证上岗,“七牌二图”与安全标牌齐全。
施工船只和平台上的发电设备和配电装置完整无损,安全可靠,电线电缆布置合理,相对固定,有可靠的接地接零。
起重吊机和各类卷扬机就位合理,吊索器具配备合理,有上岗操作牌。
建立项目部和班组专、兼职防火责任人,严格动火作业审批制度。
项目部分片建立义务消防队,配置消防器材。
作业区域道路布置合理,保持畅通,工程材料和施工材料堆放整齐。
施工驳船四周配置安全围栏,机动船只加强“管、用、养、修”等综合管理。
大、中、小型机动设备加强维护保养,落实专人操作,保持外观整洁,按时填写运行记录。
健全施工“五有”设施,食堂卫生符合《食堂卫生法》要求,针对工程特点设有临时保健室,制定职工宿舍卫生整洁规范。
九、劳动力计划
序
岗位名称
数量
备注
1
测量工
8
2
电焊工
20
3
起重工
15
4
潜水员
2
5
其他辅助人员
20
6
管理人员
15
7
总计
80
十、主要机械设备计划表
序号
名称
数量
规格
备注
1
浮吊
1艘
350t
施打φ1000钢管桩和φ2700钢护筒
2
履带吊
4台
50~100t
限位装置施工
3
工程驳船
1艘
1500t
钢围堰定位
4
拖轮
2艘
3200KW
钢围堰运输
5
拖轮
1艘
980KW
钢围堰运输
6
潜水泵
12台
50m3/h
钢围堰起浮抽水
7
锚机
4台
20t
钢围堰锚泊
8
锚
4个
5t
钢围堰锚泊
9
锚艇
1艘
协助抛锚
10
运输驳船
4
艘
1000t
运输钢管桩、钢护筒
11
交通艇
艘
80t
12
全站仪
10
13
水准仪
2台
NA2
14
经纬仪
3台
J2
15
电焊机
20
交流
钢围堰、钢平台搭设
16
潜水设备
1套