产品结构设计准则壁厚篇.docx
《产品结构设计准则壁厚篇.docx》由会员分享,可在线阅读,更多相关《产品结构设计准则壁厚篇.docx(15页珍藏版)》请在冰豆网上搜索。
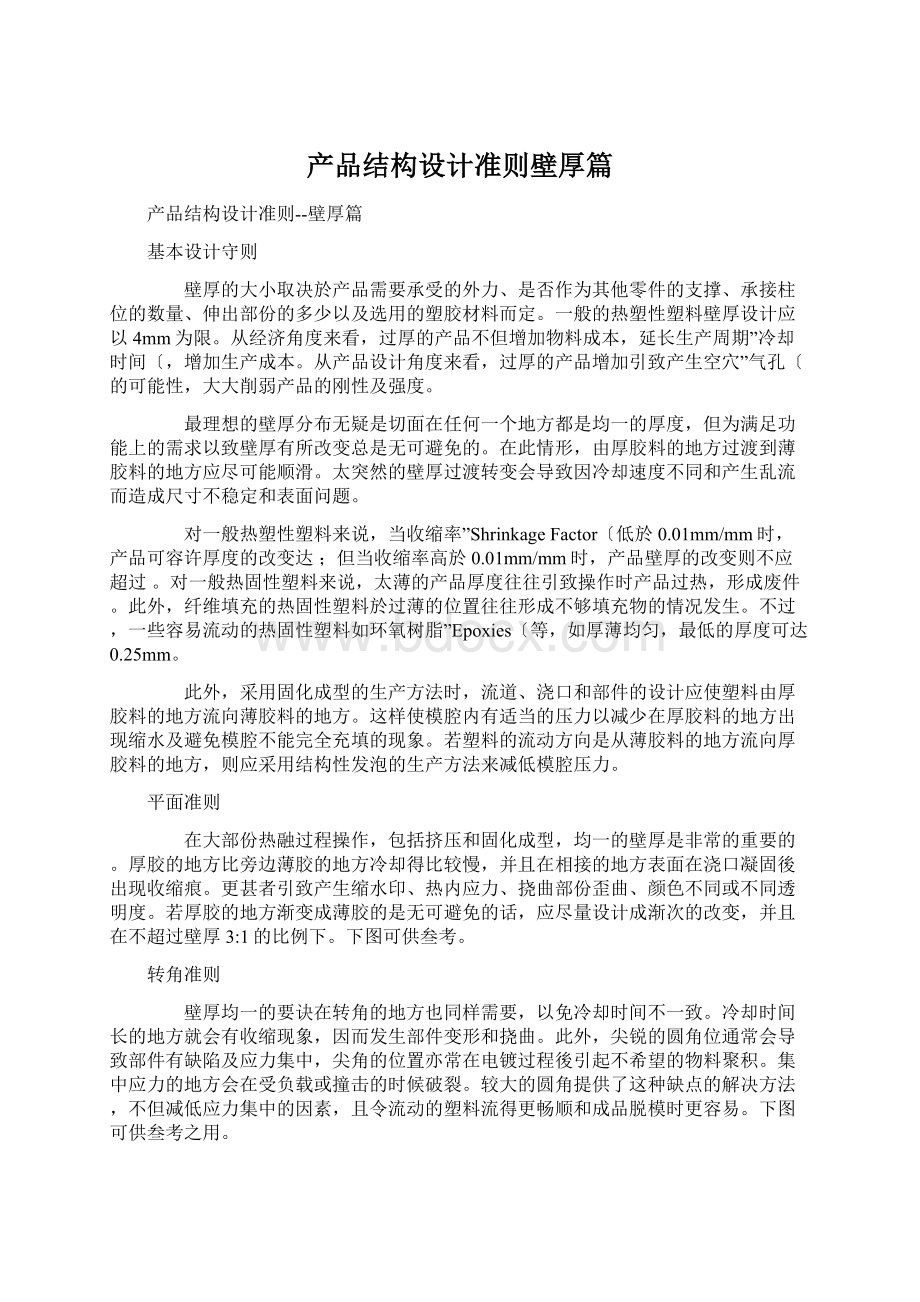
产品结构设计准则壁厚篇
产品结构设计准则--壁厚篇
基本设计守则
壁厚的大小取决於产品需要承受的外力、是否作为其他零件的支撑、承接柱位的数量、伸出部份的多少以及选用的塑胶材料而定。
一般的热塑性塑料壁厚设计应以4mm为限。
从经济角度来看,过厚的产品不但增加物料成本,延长生产周期”冷却时间〔,增加生产成本。
从产品设计角度来看,过厚的产品增加引致产生空穴”气孔〔的可能性,大大削弱产品的刚性及强度。
最理想的壁厚分布无疑是切面在任何一个地方都是均一的厚度,但为满足功能上的需求以致壁厚有所改变总是无可避免的。
在此情形,由厚胶料的地方过渡到薄胶料的地方应尽可能顺滑。
太突然的壁厚过渡转变会导致因冷却速度不同和产生乱流而造成尺寸不稳定和表面问题。
对一般热塑性塑料来说,当收缩率”ShrinkageFactor〔低於0.01mm/mm时,产品可容许厚度的改变达;但当收缩率高於0.01mm/mm时,产品壁厚的改变则不应超过。
对一般热固性塑料来说,太薄的产品厚度往往引致操作时产品过热,形成废件。
此外,纤维填充的热固性塑料於过薄的位置往往形成不够填充物的情况发生。
不过,一些容易流动的热固性塑料如环氧树脂”Epoxies〔等,如厚薄均匀,最低的厚度可达0.25mm。
此外,采用固化成型的生产方法时,流道、浇口和部件的设计应使塑料由厚胶料的地方流向薄胶料的地方。
这样使模腔内有适当的压力以减少在厚胶料的地方出现缩水及避免模腔不能完全充填的现象。
若塑料的流动方向是从薄胶料的地方流向厚胶料的地方,则应采用结构性发泡的生产方法来减低模腔压力。
平面准则
在大部份热融过程操作,包括挤压和固化成型,均一的壁厚是非常的重要的。
厚胶的地方比旁边薄胶的地方冷却得比较慢,并且在相接的地方表面在浇口凝固後出现收缩痕。
更甚者引致产生缩水印、热内应力、挠曲部份歪曲、颜色不同或不同透明度。
若厚胶的地方渐变成薄胶的是无可避免的话,应尽量设计成渐次的改变,并且在不超过壁厚3:
1的比例下。
下图可供叁考。
转角准则
壁厚均一的要诀在转角的地方也同样需要,以免冷却时间不一致。
冷却时间长的地方就会有收缩现象,因而发生部件变形和挠曲。
此外,尖锐的圆角位通常会导致部件有缺陷及应力集中,尖角的位置亦常在电镀过程後引起不希望的物料聚积。
集中应力的地方会在受负载或撞击的时候破裂。
较大的圆角提供了这种缺点的解决方法,不但减低应力集中的因素,且令流动的塑料流得更畅顺和成品脱模时更容易。
下图可供叁考之用。
转角位的设计准则亦适用於悬梁式扣位。
因这种扣紧方式是需要将悬梁臂弯曲嵌入,转角位置的设计图说明如果转角弧位R太小时会引致其应力集中系数(StressConcentrationFactor)过大,因此,产品弯曲时容易折断,弧位R太大的话则容易出现收缩纹和空洞。
因此,圆弧位和壁厚是有一定的比例。
一般介乎0.2至0.6之间,理想数值是在0.5左右。
壁厚限制
不同的塑胶物料有不同的流动性。
胶位过厚的地方会有收缩现象,胶位过薄的地方塑料不易流过。
以下是一些建议的胶料厚度可供叁考。
热塑性塑料的胶厚设计叁考表
热固性塑料的胶厚设计叁考img=
其实大部份厚胶的设计可从使用加强筋及改变横切面形状取缔之。
除了可减省物料以致减省生产成本外,取缔後的设计更可保留和原来设计相若的刚性、强度及功用。
下图的金属齿轮如改成使用塑胶物料,更改後的设计理应如图一般。
此塑胶齿轮设计相对原来金属的设计不但减省材料,消取因厚薄不均引致的内应力增加及齿冠部份收缩引致整体齿轮变形的情况发生。
不同材料的设计要点
ABS
a)壁厚
壁厚是产品设计最先被考虑,一般用於注塑成型的会在1.5mm(0.06in)至4.5mm(0.18in)。
壁厚比这范围小的用於塑料流程短和细小部件。
典型的壁厚约在2.5mm(0.1in)左右。
一般来说,部件愈大壁厚愈厚,这可增强部件强度和塑料充填。
壁厚在3.8mm(0.15in)至6.4mm(0.25in)范围是可使用结构性发泡。
b)圆角
建议的最小圆角半径是胶料厚度的25%,最适当的半径胶料厚比例在60%。
轻微的增加半径就能明显的减低应力。
PC
a)壁厚
壁厚大部份是由负载要求内应力几何形状外型塑料流量可注塑性和经济性来决定。
PC的建议最大壁厚为9.5mm(0.375in)。
若要效果好,则壁厚应不过3.1mm(0.125in)。
在一些需要将壁厚增加使强度加强时,肋骨和一些补强结构可提供相同结果。
PC大部份应用的最小壁厚在0.75mm(0.03in)左右,再薄一些的地方是要取决於部件的几何和大小。
短的塑料流程是可以达到0.3mm(0.012in)壁厚。
壁厚由厚的过渡到薄的地方是要尽量使其畅顺。
所有情况塑料是从最厚的地方进入模腔内,以避免缩水和内应力。
均一的壁厚是要很重要的。
不论在平面转角位也是要达到这种要求,可减少成型後的变型问题。
LCP
a)壁厚
由於液晶共聚物在高剪切情况下有高流动性,所以壁厚会比其它的塑料薄。
最薄可达0.4mm,一般厚度在1.5mm左右。
PS
a)壁厚
一般的设计胶料的厚度应不超过4mm,太厚的话会导致延长了生产周期。
因需要更长的冷却时间,且塑料收缩时有中空的现象,并减低部件的物理性质。
均一的壁厚在设计上是最理想的,但有需要将厚度转变时,就要将过渡区内的应力集中除去。
如收缩率在0.01以下则壁厚的转变可有的变化。
若收缩率在0.01以上则应只有的改变。
b)圆角
在设计上直角是要避免。
直角的地方有如一个节点,会引致应力集中使抗撞击强度降低。
圆角的半径应为壁厚的25%至75%,一般建议在50%左右。
PA
a)壁厚
尼龙的塑胶零件设计应采用结构所需要的最小厚度。
这种厚度可使材料得到最经济的使用。
壁厚尽量能一致以消除成型後变型。
若壁厚由厚过渡至薄胶料则需要采用渐次变薄的方式。
b)圆角
建议圆角R值最少0.5mm(0.02in),此一圆角一般佳可接受,在有可能的范围,尽量使用较大的R值。
因应力集中因素数值因为R/T之比例由0.1增至0.6而减少了50%,即由3减至1.5。
而最佳的圆角是为R/T在0.6之间。
PSU
a)壁厚
常用於大型和长流距的壁厚最小要在2.3mm(0.09in)。
细小的部件可以最小要有0.8mm(0.03in)而流距应不可超过76.2mm(3in)
PBT
a)壁厚
壁厚是产品成本的一个因素。
薄的壁厚要视乎每种塑料特性而定。
设计之前宜先了解所使用塑料的流动长度限制来决定壁厚。
负载要求时常是决定壁厚的,而其它的如内应力,部件几何形状,不均一化和外形等。
典型的壁厚介乎在0.76mm至3.2mm(0.03至0.125in)。
壁厚要求均一,若有厚薄胶料的地方,以比例3:
1的锥巴渐次由厚的地方过渡至薄的地方。
b)圆角
转角出现尖角所导致部件的破坏最常见的现象,增加圆角是加强塑胶部件结构的方法之一。
若将应力减少5%(由3减至1.5)则圆角与壁厚的比例由0.1增加至0.6。
而0.6是建议的最理想表现。
产品结构设计资料--禁用之塑料材质
.产品和制程上应该避免使用的东西
石棉、多氯联苯、多溴联苯、多氯二苯、氯乙烯单体、苯
2.制程及产品上需要管制的材质
铍及其化合物---含小于2%的铍的合金是可以被接受的。
镉及其化合物---当防生锈的扣件如果镀锌或其它加工都不适合的话,镀镉是可以被接受的。
取代品是镀锌,无电解镍,镀锡或用不锈钢产品。
铅及其化合物---铅使用在焊接剂的场合是可以接受的。
假如镀锡在PCB或者表面黏着镀锡则需要格外的管制。
为了减少铅蒸气的产生,焊锡设备应处以不超过800℉温度为极限。
镍及其化合物---在非持续接触的情况下使用应属可接受。
所有镀镍的应用应尽量避免使用在经常接触的零件表面,镀铬是常用取代镀镍的例如在按键或其它经常接触的零件。
水银及其化合物---如果使用在水银开关,水银电池及水银接点是可以接受的,但应尽量避免。
可以用结构或电子开关,非水银电池也很普遍。
铬及其化合物---铬分解产生的酸有剧毒,主要的危险是制造过程中暴露在铬化合物的环境中,如果零件在做铬酸盐表面处理时,有环境,卫生,安全单位严格管制,则应可接受。
锡的有机化合物---纯锡,含锡的焊剂以及锡合金是可以被使用的,在制程中是不可以含有有机锡产生。
硒及其化合物---硒如果使用在复制的仪器(如激光打印机)的磁鼓作为镀层之用是可以接受的。
所有使用过含有硒的仪器和设备,须由有执照的回收公司回收。
金它及其化合物---都含有剧毒。
砷及其化合物---可使用在半导体的制造。
四甲基氯化物---在产品上必须标注此溶剂对人体的健康有潜在的危险,替代品是氟氯碳化物溶剂。
氯化物溶剂---大部分氯化物溶剂都有强烈的毒性,氯化物溶剂应该尽量避免使用,除非是在制造或整修时之清洗或去脂的时候,而且找不到其它合适的替代品,替代品为水溶性的清洁剂或专用的溶剂。
甲醛------甲醛必须与盐酸溶液隔离,否则这两种化合物的气体会形成二氯甲基醚(致癌物质)。
当甲醛含有泡沫是表示尚未有反映是可以接受的,当树脂含有甲醛时要避免过高的温度和保持适当的通风。
乙二醇醚和醋酸盐---导致畸形,如用做抗光剂需有环境,卫生,安全单位严格管制。
四氟化碳---破坏臭氧层的主要原因,但四氟化碳聚脂是不受管制而且是可接受的材质。
3-1信息产品绿色环保
塑料外壳
外壳应该含有极少量的小零件,小零件应该使用同样的塑料材质几颜色塑料材质必须不可以含PVC或PVCD成份,在零件尚必须打上该材质的编号和记号。
如塑料材质因为要更稳定或配色或防火而需使用添加物,则禁止
1.含有镉,铬,汞,砷,铍,锑以有机的组成,每个小零件最多只能含有50mg/kg的PBB或PBBO。
2.含有铅,氯,溴化物的组成。
金属外壳结构
以使用SPCC及SECC为主要,铝合金则尽量减少使用,如果非使用铝为金属配件者,须与金属外壳容易拆卸为原则。
金属制外壳在制程上不可含有镉,铅,铬,汞
金属及塑料的组合件
如果可能的话,塑料件及金属件应该分开组装,金属件及铜合金应该避免黏合使用。
电子组件
1.PVC材质只使用在Cable的产品上面
2.非含有PCBV的电容器
3.不含水银的开关
4.零件间如果是非黏着性密接,废弃时候须拆卸及分类
5.不含铍成份的零件
包装
只有纸张、玻璃纸、纸板、聚乙烯和聚丙是被允许的。
塑料和纸板的组合是不好的一种包装方式。
包装材质应该打上能够回收的标志,黏贴胶布应该只能含有聚合丙烯及黏贴层。
该种胶布尽量少用因为无法回收。
印刷材料
为传递信息或促销用的印刷标签应该印刷在能回收使用的纸上,以及用氯漂白的纸上。
纸的加工方式必须载明在纸上,含有塑料成份的纸或纸板应拒绝使用。
产品结构设计资料--塑料材质
热硬化性塑料---在原料状态下是没有什么用,在某一温度下加热,经硬化作用,聚合作用或硫化作用后,热硬化塑料就会保持稳定而不能回到原料状态。
硫化作用后,热硬化塑料是所有塑料中最坚硬的。
热塑性塑料---象金属一样形成熔融凝固的循环。
常用有聚乙烯(PE)、聚苯乙烯(PS)、聚氯乙烯(PVDC)。
ABS:
成分聚合物
1.丙烯晴---耐油,耐热,耐化学和耐候性。
2.苯乙烯---光泽,硬固,优良电气特性和流动性。
3.丁二烯---韧性。
螺杆对原料有输送,压缩,熔融及计量等四种功能。
螺杆在旋转时使之慢慢后退的阻力为背压。
背压太低,产品易产生内部气泡,表面银线,背压太高,原料会过热,料斗下料处会结块,螺杆不能后退,成型周期延长及喷嘴溢料等。
压力的变动在一两模内就可知道结果,而温度的变动则需约10分钟的结果才算稳定。
2-1电镀
塑料电镀时,须先进行无电解电镀,塑料表面形成薄金属皮膜,形成导电物质后再进行电解电镀。
印刷
1.网版印刷:
适用于一般平面印刷
2.移印:
适用不规则,曲面的印刷文字
3.曲面印刷:
被印物体旋转而将文字与油墨印上
常用工程塑料
NORYL---PPO和HIPS合成,在240~300℃成型加工,须用70~90℃高模温。
ABS---在170~220下成型加工,模温40~60℃即可。
2-2ABS系列成品设计及模具加工
最佳的补强厚度t=70%成品工称肉厚(T),角隅圆角的外圆R=3/2*T,内圆R=T/2,T是成品工称肉厚。
喷嘴信道最小口径为6.35mm,长度宜尽量短,可变电阻器控制精度稍嫌不足,所以在喷嘴外壁应装设电偶作温度控制。
流道形状以圆形最佳,流动长度与流道口径关系。
流动长度(mm)流道直径(mm)
2509.5
75~2507.9
756.0
对防火级ABS材料应使用直溢口为最佳设计(流道直径最小7mm),边溢口及潜伏式溢口,建议其长度为0.762mm。
透气得设置是绝对必须的,每隔25~50mm开设一条透气沟,深度宜为0.05~0.064mm,以获得良好得透气效果及防止产生毛头。
冷却管口径应为11.1~14.3mm,每隔三个冷却管口径设一冷却管,距离模腔表面必须有1.5个冷却管口径尺寸。
一般模仁材料以采用P20或H13材质居多。
防火级材料尽量不要使用热浇道系统,因为内加热式的热浇道在电热管及树脂间会产生很大的剪切热,加热树脂温度过高将会造成严重的模垢,若要用就只能用外加热式,热嘴温度和树脂温度相近即可(约200℃)。
在任何时候热浇道须使用内部加热器或热探针。
为减少模垢的产生,螺杆压缩比宜取2:
1~2.5:
1,而L/D是20:
1(理想值是24:
1),可使用没有计量段的螺杆,使加热棒与熔融树脂温度差在5.5℃附近。
螺杆速度宜在40~55RPM。
模具保护剂可以中和防火级塑料及PVC树脂在成型过程所释放出的腐蚀气体,防止模垢的积成及腐蚀模具,有优良的脱模性,无须使用其它的脱模剂。
模垢去除剂主要用来清洗模垢,在有栅格的区域切勿过度喷洒以方破坏树脂导致无法脱模。
射出时理想的状况是成品重量约为射出单元一次为总排料量的80%,最少比例也应在50%以上。
熔融树脂温度在221~232℃时可得最佳物性,但不可超过243℃,以避免分解。
停机的排换料时须用模垢去除剂防止模具表面被腐蚀,然后在模具上喷一层良好的中性喷剂。
产品结构设计资料--金属材料
SPCC一般用钢板,表面需电镀或涂装处理
SECC镀锌钢板,表面已做烙酸盐处理及防指纹处理
SUS301弹性不锈钢
SUS304不锈钢
镀锌钢板表面的化学组成------基材(钢铁),镀锌层或镀镍锌合金层,烙酸盐层和有机化学薄膜层。
有机化学薄膜层能表面抗指纹和白锈,抗腐蚀及有较佳的烤漆性。
SECC的镀锌方法
热浸镀锌法:
连续镀锌法,成卷的钢板连续浸在溶解有锌的镀槽中;
板片镀锌法,剪切好的钢板浸在镀槽中,镀好后会有锌花。
电镀法:
电化学电镀,镀槽中有硫酸锌溶液,以锌为阳极,原材质钢板为阴极。
1-1产品种类介绍
1.品名介绍
材料规格后处理镀层厚度
SABC*D*E
SforSteel
A:
EG(ElectroGalvanizedSteel)电气镀锌钢板---电镀锌
一般通称JIS
镀纯锌EGSECC
(1)
铅和镍合金合金EGSECC
(2)
GI(GalvanizedSteel)溶融镀锌钢板------热浸镀锌
非合金化GI,LGSGCC(3)
铅和镍合金GA,ALLOYSGCC(4)
裸露处耐蚀性2>3>4>1
熔接性2>4>1>3
涂漆性4>2>1>3
加工性1>2>3>4
B:
所使用的底材
C(Coldrolled):
冷轧
H(Hotrolled):
热轧
C:
底材的种类
C:
一般用
D:
抽模用
E:
深抽用
H:
一般硬质用
D:
后处理
M:
无处理
C:
普通烙酸处理---耐蚀性良好,颜色白色化
D:
厚烙酸处理---耐蚀性更好,颜色黄色化
P:
磷酸处理---涂装性良好
U:
有机耐指纹树脂处理(普通烙酸处理)------耐蚀性良好,颜色白色化,耐指纹性很好
A:
有机耐指纹树脂处理(厚烙酸处理)---颜色黄色化,耐蚀性更好
FX:
无机耐指纹树脂处理---导电性
FS:
润滑性树脂处理---免用冲床油
E:
撇愫?
/P>
1-2物理特性
膜厚---含镀锌层,烙酸盐层及有机化学薄膜层,最小之膜厚需0.00356mm以上。
测试方法有磁性测试(ASTMB499),电量分析(ASTMB504),显微镜观察(ASTMB487)。
表面抗电阻---一般应该小于0.1欧姆/平方公分。
1-3
盐雾试验----试片尺寸100mmX150mmX1.2mm,试片需冲整捆或整叠铁材中取下,必须在镀烙酸盐后24小时,但不可超过72小时才可以用于测试,使用5%的盐水,用含盐的水汽充满箱子,试片垂直倒挂在箱子中48小时。
测试后试片的镀锌层不可全部流失,也不能看到底材或底材生锈,但是离切断层面6mm范围有生锈情况可以忽略。
1-4镀锌钢板的一般问题点
1.白锈---因结露或被水沾湿致迅速发生氢氧化锌为主要成分的白色粉末状的锈。
(会导致产品质量劣化)
2.红锈---因结露或被水沾湿致迅速发生氢氧化铁为主要成分的红茶色粉末状的锈。
3.烙酸不均匀---黄茶色的小岛形状或线形状的花纹,但耐蚀性没有问题。
4.替代腐蚀保护---在锌面割伤而,露出钢板基体表面的情况下,我们也不必担心镀锌钢板切边生锈问题。
1-5镀锌钢板之烤漆处理
1.前处理
由于锌是一种高活性金属,在烤漆前需要适当的化学转化处理如磷酸盐处理。
磷酸盐处理剂有两种,一种是处理铁的,一种是处理锌的。
2.脱脂
采用弱碱,有机溶剂及中性乳液或洗涤剂,避免用酸或强碱脱脂剂。
可用水膜试验(Waterlreakagetest)来确认,观察试验后的水是否受到污染,以及试品表面的水膜是否均匀。
3.烤漆
电镀锌钢片对漆的选择性比冷轧钢片为严。
使用水性底漆(Waterpromer)可以确保有较强的油漆附着性。
产品结构设计准则--公差(Tolerance)
基本设计守则
大部份的塑胶产品可以达到高精密配合的尺寸公差,而一些收缩率高及一些软性材料则比较难於控制。
因此在产品设计过程时是要考虑到产品的使用环境,塑胶材料,产品形状等来设定公差的严紧度。
除着顾客的要求愈来愈高,以往的可以配合起来的观念慢慢的要修正过来。
配合、精密和美观是要同时的能在产品上发挥出来。
公差的精密度高,产品质素相对提高,但随之而来的是增加了成本和因达到要求而花更多的时间。
故此公差的设定可以跟随不同塑料来作一标准,以下是几种由塑料供应商提供的塑料公差设计要点。
而设计的容许公差范围是可在美国SPI规格内找得到。
不同材料的设计要点
LCP
液晶共聚物成品容许公差随着设计的复杂程度和壁厚而定。
薄壁的部份经常可以在液晶共聚物的产品上可找得到。
而且液晶共聚物容许公差可是极小容许公差的50%。
LCP液晶高分子设计容许公差的指南
宝特龙(PET)的设计公差准则
POM精密公差的标准叁考表
产品结构设计准则--洞孔(Hole)
在塑胶件上开孔使其和其它部件相接合或增加产品功能上的组合是常用的手法,洞孔的大小及位置应尽量不会对产品的强度构成影响或增加生产的复杂性,以下是在设计洞孔时须要考虑的几个因素。
相连洞孔的距离或洞孔与相邻产品直边之间的距离不可少於洞孔的直径,如孔离边位或内壁边之要点图。
与此同时,洞孔的壁厚理应尽量大,否则穿孔位置容易产生断裂的情况。
要是洞孔内附有螺纹,设计上的要求即变得复杂,因为螺纹的位置容易形成应力集中的地方。
从经验所得,要使螺孔边缘的应力集中系数减低至一安全的水平,螺孔边缘与产品边缘的距离必须大於螺孔直径的三倍。
孔离边位或内壁边之要点
穿孔
从装配的角度来看,穿孔的应用远较盲孔为多,而且较盲孔容易生产。
从模具设计的角度来看,穿孔的设计在结构上亦较为优胜,因为用来穿孔成型的边钉的两端均可受到支撑。
穿孔的做法可以是靠单一边钉两端同时固定在模具上、或两枝边钉相接而各有一端固定在模具上。
一般来说,第一种方法被认为是较好的;应用第二种方法时,两条边钉的直径应稍有不同以避免因为两条边钉轴心稍有偏差而引致产品出现倒扣的情况,而且相接的两个端面必须磨平。
盲孔
盲孔是靠模具上的哥针形成,而哥针的设计只能单边支撑在模具上,因此很容易被溶融的塑料使其弯曲变形,形成盲孔出现椭圆的形状,所以哥针的长度不能过长。
一般来说,盲孔的深度只限於直径的两倍。
要是盲孔的直径只有或於1.5mm,盲孔的深度更不应大於直径的尺寸。
盲孔的设计要点
钻孔
大部份情况下,额外的钻孔工序应尽量被免,应尽量考虑设计孔穴可单从模具一次成型,减低生产成本。
但当需要成型的孔穴是长而窄时”即孔穴的长度比深度为大〔,因更换折断或弯曲的哥针构成的额外成本可能较辅助的後钻孔工序为高,此时,应考虑加上後钻孔工序。
钻孔工序应配合使用钻孔夹具加快生产及提高品质,亦可减少因断钻咀或经常番磨钻咀的额外成本及时间;另一做法是在塑胶成品上加上细而浅的定位孔以代替使用钻孔夹具。
侧孔
侧孔往往增加模具设计上的困难,特别是当侧孔的方向与开模的方向成一直角时,因为侧孔容易形成塑胶产品上的倒扣部份。
一般的方法是使用角针”AnglePin〔及活动侧模”SplitMould〔,或使用油压抽哥。
留意哥针在胶料填充时会否受压变形或折断,此情况常见於长而直径小的哥针上。
因模具的结构较为复杂,模具的制造成本比教高,此外,生产时间亦因模具必须抽走哥针才可脱模而相应增加。
其他设计考虑
有关孔穴在产品设计上的考虑,尚有下列各点:
1.多级”多个不同直径但相连的孔〔的孔可容许的深度比单一直径的孔长;此外,将模具件部份孔位偷空,亦可将孔的深度缩短,下图说明这两种方法的应用。
多级孔或将穿孔偷空的应用方法
2.侧孔若使用角针、活动侧模或油压抽哥必会使模具的结构复杂及增加成本,此问题可从增加侧孔壁位的角度,或以两级的孔取代原来的侧孔得以消除侧孔引致的倒扣,消除侧孔倒扣的方法图说明这两种方法的应用。
消除侧孔倒扣的方法
3.洞孔的边缘应预留最少0.4mm的直身位,设计一个完整的倒角或圆角於孔边在经济上或实践上都是不设实际的,可叁考洞孔边缘的设计图。
产品结构设计准则--入件(Moulded-inInserts)
基本设计守则
塑胶内的入件通常作为紧固件或支撑部份。
此外,当产品在设计上考虑便於返修、易於更换或重复使用等要求时,入件是常用的一种装配方式。
但无论是作为功能或装饰用途,入件的使用应尽量减少,因使用入件需要额外的工序配合,增加生产成本。
入件通