钣金检验通用标准.docx
《钣金检验通用标准.docx》由会员分享,可在线阅读,更多相关《钣金检验通用标准.docx(17页珍藏版)》请在冰豆网上搜索。
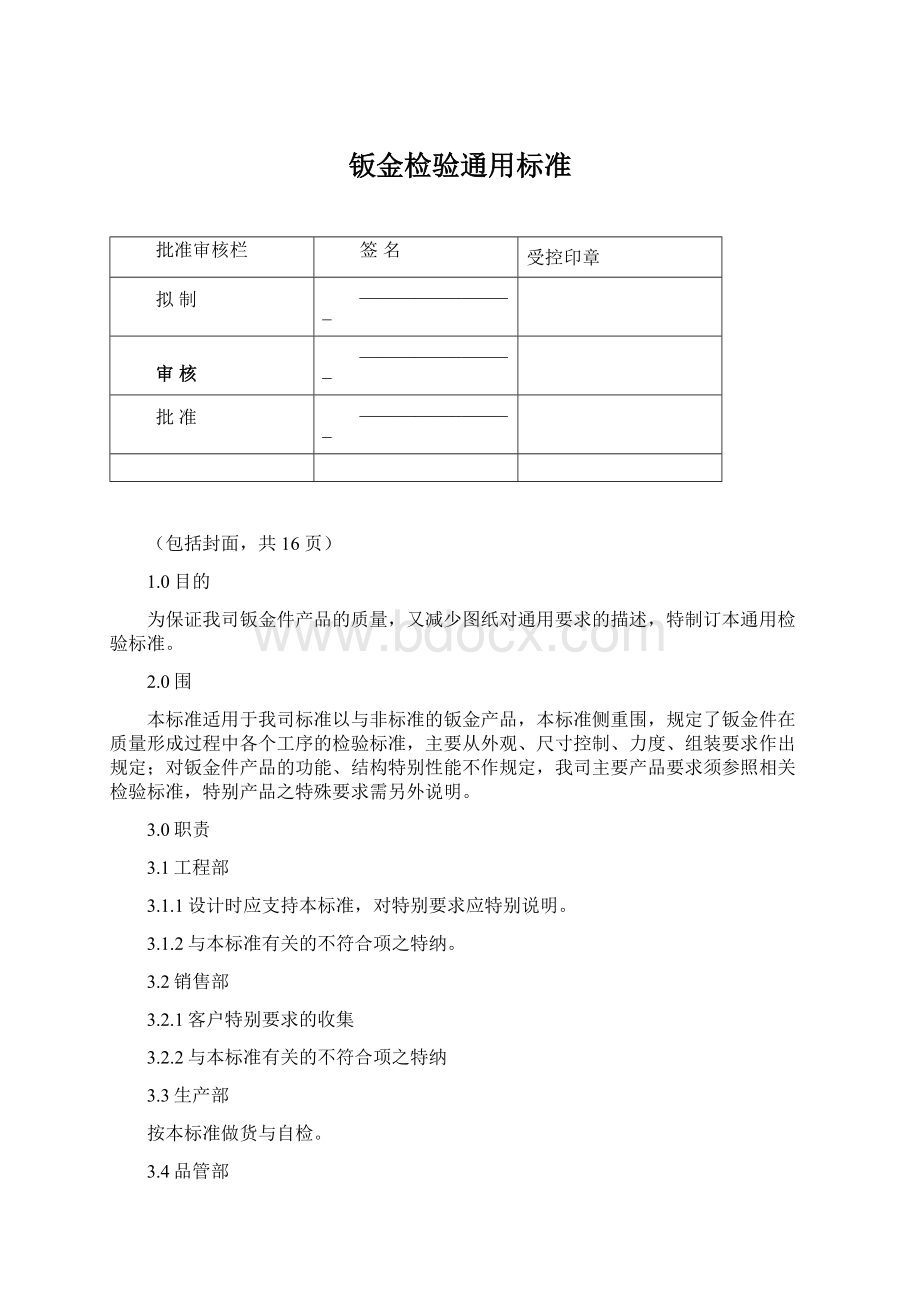
钣金检验通用标准
批准审核栏
签名
受控印章
拟制
_________________
审核
_________________
批准
_________________
(包括封面,共16页)
1.0目的
为保证我司钣金件产品的质量,又减少图纸对通用要求的描述,特制订本通用检验标准。
2.0围
本标准适用于我司标准以与非标准的钣金产品,本标准侧重围,规定了钣金件在质量形成过程中各个工序的检验标准,主要从外观、尺寸控制、力度、组装要求作出规定;对钣金件产品的功能、结构特别性能不作规定,我司主要产品要求须参照相关检验标准,特别产品之特殊要求需另外说明。
3.0职责
3.1工程部
3.1.1设计时应支持本标准,对特别要求应特别说明。
3.1.2与本标准有关的不符合项之特纳。
3.2销售部
3.2.1客户特别要求的收集
3.2.2与本标准有关的不符合项之特纳
3.3生产部
按本标准做货与自检。
3.4品管部
按本标准检验。
4.0作业容
4.1剪床开料
4.1.1外观保证
4.1.1.1剪床开料必须用经IQC检验合格之板材,大料平直度、外表面状态必须符合IQC检验标准。
4.1.1.2未经确认不得采用已生锈之SECC和SPCC板料,以与表面严重划伤之SUS板料。
4.1.1.3对胶沙不锈钢应注意开料之纹向要求,不可在不确定情况下作出纹向任意开料,并严格保护表面,以避免刮伤。
4.1.1.4剪床开料之批锋应小于料厚之3%,手摸应无明显刮手现象。
4.1.2尺寸控制
4.1.2.1为保证钣金成形尺寸,减少过程累积误差对工件尺寸的影响,剪床开料尺寸允差按下表检验:
尺寸围
0-200
200-500
500-1000
>1000
允许偏差
±0.15
±0.3
±0.5
±0.8
4.1.2.2对一开几过多的开料件,如单一方向开料数量超过六件(一般应为偶数),应先将料对开,然后再开成单件,以减少误差累积。
4.1.2.3对长度超过1500-2500之开料切边直线度应小于0.3mm/m,宽度大小端误差小于0.5mm。
4.1.2.4开料件之长短边90。
角度允差±3´。
4.2CNC冲孔
4.2.1外观保证
4.2.1.1CNC冲孔应先检查板材是否有划伤,对经剪床放行而有少许划伤之板料,冲孔时应将划伤面尽量放于批锋面,以减少对外观的影响。
4.2.1.2CNC冲孔应留意批锋在工件成形后的位置影响,应尽量保证批锋在工件成形后的面方向:
(对重要表面,工程绘图应将外表面放在正视方向,以方便编程)对重要表面又分左右之工件,CNC冲孔需在冲孔时分左右(即正反),以保证成形后批锋都朝面。
4.2.1.3对胶沙不锈钢,CNC冲孔应保证批锋位于胶沙之反面。
(工程绘图,应留意将外表面放在胶沙面且于图之正视方向,并作出相应之标注,如在打弯图上标明胶沙面位置)。
4.2.1.4冲孔应保证最小的模具接合缝以与批锋高度,直边接合缝不可出现大于0.1~0.15之阶梯现象。
孔边批锋高度一般应小于料厚的3%,最大不可超过0.1mm(对T≦3mm厚板材言)
4.2.1.5为保证折弯后钣金件的拼角外观以与折弯尺寸,CNC冲应留意工艺孔不可漏冲。
一般T=0.8或1.0板,工艺孔取Φ2.0;T=1.0/1.5/2.0板,工艺孔取Φ2.6;T=3.0板,工艺孔取Φ3.2。
4.2.2尺寸保证
4.2.2.1孔距
4.2.2.1.1对有孔距尺寸要求的关联孔,冲孔时一般宜于一次装夹中完成,以保证孔距精度;(工程施工图对开料尺寸应留意,如工件孔距有精度关联,需能保证CNC冲孔在一次装夹中将工件关联孔整组打出)。
4.2.2.1.2孔距公差按机床正常保证精度控制,可按下表校验,对异常情形之孔距偏差需与设计者确认。
尺寸围
0-200
200-500
500-1000
>1000
允许偏差Δ
±0.1
±0.2
±0.3
±0.5
注:
基于上述允差围,工程施工图在对螺丝固定孔的大小尺寸设计中,应兼顾螺纹孔侧之孔距公差与固定孔侧之孔距公差,即应保证固定孔与螺丝之单边间隙尺寸≧4Δ,对孔距最终由折弯或焊接保证的如无特别要求,固定孔一般宜将误差方向做成长孔。
4.2.2.2孔大小尺寸
4.2.2.2.1由模具一次成形之孔大小尺寸一般按基孔制作正公差控制,但根据我司产品的特点和以往模具制造参数,从成本考虑允许负差,但不可超过相应的正公差值。
4.2.2.2.2以基孔制为检验标准的孔大小允差按下表:
孔尺寸
(冲头对角线)
0-12.7
50.8-100
允差
+0.2
+0.3
+0.4
+0.5
4.2.2.2.3由模具连续冲裁成形之孔大小尺寸规定按基孔制作正公差控制,其允差按下表检验:
尺寸围
0-200
200-500
500-1000
>1000
允许偏差
+0.2
+0.3
+0.5
+0.8
(注:
此类孔亦包含未封闭之缺口,角度口、切角)
4.2.2.3外形尺寸
4.2.2.3.1本“外形尺寸”一般指由模具连续冲裁成形保证之尺寸,一般规定按正负公差控制,其允差按下表:
尺寸围
0-200
200-500
500-1000
>1000
允差
±0.2
±0.3
±0.5
±0.8
4.2.2.3.2对控制台外盖面板类工件,其允许偏差应加严控制,尺寸围300~800,允差±0.15,故加工时应一次装夹冲出。
4.3剪角和包角
4.3.1剪角尺寸的大小影响钣金件成形后边角之拼缝大小,对成形后边角位无焊接打磨要求的,则直接影响钣金件的外观,故对剪角尺寸的大小应作出控制。
4.3.2剪角尺寸公差按孔的方式作出正公差取值控制,其允差按下表:
尺寸围
0-50
50-100
100-200
200-300
允差
+0.2
+0.3
+0.4
+0.5
4.3.3由于剪角对外观的影响,为保证良好的成形外观,现将钣金件成形包角,设计常见种类示意如下,供加工时检查参考:
A.
90。
V曲邻边互不包。
设计接缝Δ=0,常用于料厚1.5以上,角位外部烧焊打磨R场合。
B.90。
V曲邻边一边包另一边。
设计接缝Δ=0.2~0.3,常用于外部不加焊或角点焊不打磨场合,A面外观重要性大于B面。
C.
90。
U曲(双V曲)邻边互不包,斜角拼缝。
设计接缝Δ1=0.2~0.3,Δ2=0,常用于料厚1.5以上,角位外部焊接打磨R场合。
D.90。
U(双V曲)邻边一边包另一边,斜角拼缝
设计接缝Δ1=0.2~0.3,Δ2=0,常用于角位不加焊,斜角点焊加固场合,A面外观重要性大于B面。
此形式常用于转门和盖的拼角。
E.90。
U曲(双V曲)邻边一边包另一边,直角拼缝
设计接缝Δ=0.2~0.3,A面外观重要性大于B面。
此形式常用于电视墙层板等的拼角。
F.以上接缝值Δ,加工后允许再加上相应的剪角允差。
对外观缝隙严的配件需用CNC或模具一次冲出切角与外形。
4.3.4对施工图中个别单件(批量工件除外)未作标注的90。
V曲或U曲剪角尺寸,可分别按上述之B和D方式处理,并采用长边包短边方式切角。
4.4冲压等辅助工艺规
4.4.1压铆
4.4.1.1钣金件常用之压铆件有冲压螺丝、冲压丝母柱、压铆螺母(即花时那),压铆应保证稳固不能松动,结合表面平整,无明显凹陷和凸起现象,压铆件与工件表面垂直不能歪斜,压铆件与板材接合端不能出现断裂现象。
4.4.1.2压铆件的方向性应与图纸方向一致,规格型号与图纸与BOM一致。
4.4.1.3对需外发氧化与铬化的铝材工件、其压铆件应于氧化或铬化后才压。
4.4.1.4为保证各压铆件的稳固性和配合性,需按PEM标准检查对应的板厚、适宜板材与底孔尺寸。
下面分别列出常用压铆件之对应表,供设计与制作检验作参考。
A.冲压螺丝
规格
长度
最小板厚
底孔+0.08
M3
8~18
1.0
Φ3
M4
8~25
1.0
Φ4
M5
10~25
1.0
Φ5
M6
10~35
1.6
Φ6
常用类型
材质
适宜板材
FH
碳钢
铝板、钢板
FHS
300系列不锈钢
铝板、钢板
FH4
400系列不锈钢
不锈钢板
B.冲压螺丝
规格
长度
最小板厚
底孔+0.08
M3
6~25
1.0
Φ4.2
3.5M3
6~25
1.0
Φ5.4
M4
6~25
1.3
Φ7.2
M5
6~35
1.3
Φ7.2
常用类型
材质
适宜板材硬度
BSO
加硬钢
≤80HRB
BSON
不加硬钢
≤60HRB
BSOS
不锈钢
≤70HRB
C.
压铆螺母(即花时那)
规格
系列号
最小板厚
底孔+0.08
M3
0
0.8~1.0
Φ4.2
1
1.0
2
1.4
M4
0
0.8~1.0
Φ5.4
1
1.0
2
1.4
M6
0
1.2
Φ8.73
常用类型
材质
适宜板材硬度
S
王牌钢
≤80HRB
CLS
不锈钢
≤70HRB
4.4.2抽孔攻牙
4.4.2.1抽孔攻牙应按图纸的方向要求,不可反向。
4.4.2.2常用的螺纹孔对应板材与抽孔前底孔如下表,加工时应作检查。
螺孔规格
板材厚
底孔
M3
0.8/1.0/1.2
Φ1.6
M4
0.8/1.0/1.2
Φ2.1
M5
1.0/1.2
Φ2.6
M6
1.0/1.2
Φ2.6
4.4.3沉孔
4.4.3.1圆头螺丝沉孔应保证其方向与图纸一致,不可反向。
4.4.3.2我司常用圆头螺丝沉孔对应板材与底孔规格如下:
螺丝规格
板材厚
底孔
冲后扩孔
M3
0.8
CNC冲点
不用
M3
1.0/1.2
Φ2.3
不用
M4
1.0/1.2
Φ3.0
不用
M6
0.8/1.0/1.2
Φ2.6
扩Φ6.3
4.4.3.3我司常用平头十字螺丝沉孔对应板材与底孔规格如下表,沉孔时不可将底孔扩大,以避免螺丝锁不紧现象,沉孔角度为90。
。
螺丝规格
最小板材厚
底孔
M3
小平头
1.0
Φ3.0
常规
1.2
Φ3.5
M4
1.5
Φ4.2
M5
2.0
Φ5.5
M6
3.0
Φ6.6
4.4.4攻螺纹
4.4.4.1于板材上直接攻螺纹仅适宜于铁与不锈钢板,铝板上一般宜打压铆螺母,厚铝板镶钢丝牙套,攻牙最小应保证1.5-2圈螺纹或更多。
牙孔应无积屑、坏牙、断牙、变形等现象。
4.4.4.2为保证螺纹联接力度,现将各螺孔规格对应板材最小厚度以与底孔尺寸规定如下:
螺丝规格
底孔
最小板厚
小于最小板厚措施
M3x0.5
Φ2.6
1.2
抽孔攻牙或压铆螺母
M4x0.7
Φ3.2
1.2
抽孔攻牙或压铆螺母
M5x0.8
Φ4.2
1.5
压铆螺母
M6x1.0
Φ5
压铆螺母或碰焊丝母
对重要联接或经常拆装位之螺纹,在最小板厚时亦宜按小于最小板厚措施处理。
4.4.5打百叶
4.4.5.1冲百叶应注意其方向与开口与图纸方向一致,不可弄反,百叶开口角位应无影响外观的撕裂口。
4.4.5.2百叶冲压后工件不能有影响尺寸与外观的明显扭曲、凹陷等变形现象。
4.5折弯
4.5.1外观保证
4.5.1.1折弯应将冲裁之批锋放在工件的面(面一般指与折弯刀接触的面,对有正反向折弯的,需根据工件具体情况判断)。
对胶沙或镜面不锈钢应保证将胶沙或镜面放于工件的外表面。
4.5.1.2对胶沙或镜面不锈钢外观折弯件,应避免出现刀槽口压痕(故加工时,刀槽应贴皱纹胶纸保护)。
4.5.1.3分布折弯角附近的孔一般不能出现折弯爆裂,孔边于折弯后不能拉过R位,特别情形不影响外观另定。
4.5.1.4折弯后应保证转门之类外观件之拼角缝隙均匀,其缝隙值Δ≤设计缝隙值+剪角误差+折弯误差=0.5~0.7。
4.5.2折弯外形尺寸的控制
4.5.2.1对折弯尺寸的控制,主要可将重点放在“关键尺寸”的控制上,为保证“关键尺寸”,允许对“非关键尺寸“作出适当调整。
4.5.2.2关键尺寸:
指影响产品的装配配合,外观缝隙,产品尺寸精度的一类尺寸;非关键尺寸:
指不影响以上要求的一类尺寸。
根据我司产品的特点,下面列出典型工件的需保证“关键尺寸”,(下面所有图中以“A”表示“关键尺寸”)。
A.
控制台、电视墙类框架关键尺寸如下图:
主体框架穿插于主框架条的付框架条
通常为保证焊装穿插,B尺寸允许比图纸尺寸少0.2~0.3。
(注:
严格意义上工程图纸需将B尺寸考虑进间隙标注,考虑到既往习惯与生产、工程共识,允许图纸按B=A-2t作理论尺寸标注,由折弯工序按穿插配合修正,故折弯需对B=A-2t的框架尺寸作配合控制)。
B.外盖件之长、宽尺寸:
如面板尺寸影响控制台、电视墙的前视外观效果;门之长、宽尺寸关系到门缝间隙外观效果;控台顶盖长、宽尺寸影响到顶部缝隙外观效果。
其关键尺寸如下图:
影响到顶部缝隙外观效果。
其关键尺寸如下图:
C.标准角关键尺寸如下:
D.机柜立柱类关键尺寸如下:
E.标准角关键尺寸如下:
F.机柜立柱类关键尺寸如下:
G.其它类工件可根据具体情况判断。
4.5.2.3对关键尺寸的控制按下表:
尺寸围
0~50
50~150
150~300
300~550
550~1000
1000~2500
允许偏差
±0.15
±0.2
±0.3
±0.4
±0.5
±0.7
4.5.2.4在保证关健尺寸前提下,将毛坯误差适当累积到非关键尺寸上,原则上应以不影响装配、外观以与产品规格尺寸为准,可根据具体情况对待。
4.5.2.5对于长工件折弯的直线度允差按下表:
长度围
1000~1500
1500~2000
2000~2500
允差
0.4
0.6
0.8
4.5.2.6折弯角角度误差以保证折弯后整体尺寸为原则,一般不另作规定,特别要求以图纸为准。
4.5.2.7为避免不必要误差,除图中有注明刀槽号的按图要求外,其余都以下表为对应原则。
板材厚度
刀槽号
折弯系数
最短V曲边尺寸
0.8
V8
1.5
6.6mm
1.0
V8
1.8
6.7mm
1.2
V12
2.2
6.5mm
1.5
V12
2.8
7.5mm
2.0
V12
3.5
8.5mm
3.0
V20
5.5
15mm
注:
a.表中折弯系数对应板材SECC、SPCC和SUS,如为AL板,相应减少0.3mm。
b.表中最短V曲边尺寸为折弯长度较短时(一般在200mm以)之尺寸,如长度较长时,需相应加大1~2mm。
常用板材要求用小刀槽折弯,以减少外R值,以下表为对应原则:
板材厚度
刀槽号
折弯系数
最短V曲边尺寸
1.2
V8
2.0
6.8mm
1.5
V8
2.5
7.0mm
4.5.2.9因图形打印尺寸比例在输出时对尺寸标注点清晰度影响,故施工图对打弯尺寸的标注一般都以外壁尺寸为标注原则(含R位),如下图示:
但对某些阶梯形打弯尺寸标注打弯时应特别留意。
如下图示,应留意如C=A+B则为按“图一”形式标注。
如C=A+B-T(T指材料厚度),则为按“图二”形式标注,(工程施工图在此标准推出后对图形输出清晰度不高情形下,一般应标注A、B、C三尺寸为校验参考)
4.5.2.10对非90。
折弯尺寸标注以下面图示为原则,折弯时以此为检验依据。
4.5.3.11对利用模具冲压与折弯成形的钣金件尺寸检验如下。
线性尺寸的未注公差按下表检验:
尺寸围
0.5~3
3~6
6~30
30~120
120~400
400~1000
1000~2000
2000~3000
允差
±0.1
±0.2
±0.3
±0.4
±0.5
±0.8
±1.2
±2
角度未注公差按下表检验:
短边尺寸围
≤10
>10~25
>25~63
<63~160
>160
角度允差
±1。
15´
±1。
±45´
±30´
±15´
4.6焊接
钣金件的焊接需从外观、尺寸和力度保证三个方面作出检验控制,以保证产品的质量。
4.6.1外观检验
4.6.1.1焊接应根据钣金件的材质、板厚与焊接位置选用合适的焊接方法,对T≤2.0薄板组件应尽量采用TIG、MIG或MAG焊接,以保证良好外观和减少焊接变形。
注:
TIG焊——钨极气体保护电弧焊(含钨极氩弧焊)。
MIG焊——熔化极惰性气体保护焊(含熔化极氩弧焊)。
MAG焊——熔化极非惰性气体保护焊(含CO2气体保护焊)
4.6.1.2钣金件的焊接在保证力度的前提下,焊点、焊缝应尽量置于对外观无影响的位置,且焊点布局应尽量匀称、大小适中,不能出现表面烧穿,擦伤之缺陷。
4.6.1.3焊接后工件表面应无明显的凹凸变形和影响产品外观又不可纠正的扭曲变形。
凹凸变形以平面度允差:
≦1.0mm/500x500。
4.6.1.4布于外观表面上的碰焊点应分布均匀,间距一般为150mm左右,且碰焊嘴于外表之压痕应尽量少,前提是保证牢固。
(注:
工程在设计时应尽量将加骨、碰焊码之材料厚度同面材厚度接近,不可相差悬殊)。
4.6.1.5布于主要外观表面与拼角位的焊缝应满焊,并能方便地打磨处理,不能作打磨处理的次要外观表面与拼角位的焊缝与焊点一定要平顺均匀,大小适中。
4.6.1.6对外表面为胶沙不锈钢的钣金箱体之焊接,应尽量避免于产品外观之正反面烧焊,而将焊点布于折边与拼角位,对不作喷涂处理之不锈钢其上所焊接之螺丝或丝母,也应为不锈钢、避免生锈与腐蚀影响外观与使用。
4.6.2焊接尺寸控制
4.6.2.1组焊必需于焊接前对拼装外尺寸进行检查,核查无误后才可焊接固定,避免前期错误的延续。
4.6.2.2钣金组焊件外形尺寸的控制,适用于拼焊类箱体、柜体、框架类部件,其外形尺寸的控制按周边尺寸和对角线检验控制,分别如下:
周边尺寸
100~400
400~1000
1000~1500
1500~2500
允许偏差
±0.4
±0.5
±0.7
±1
对角线尺寸
300~600
600~1000
1000~1500
1500~2500
允许偏差
±0.5
±0.8
±1.0
±1.5
对组焊件中有孔距要求的,焊接应留意检验,并尽量消除前工序如打弯误差对孔距的影响。
4.6.3力度保证
4.6.3.1焊接应牢固、可靠,适应各构件的力度要求,不能出现假焊、虚焊、焊点松脱裂纹,需作外表磨平处理的焊缝应有供焊透之坡口或间隙,不可磨平之后出现断裂纹现象。
4.6.3.2碰焊点应牢固,不可松脱,对重要工件应作出拉力测试,如铝质工件之机箱等。
4.6.3.3对控制台大于800mm高的转门和电视墙、机柜前后门之四角拼缝以与加骨两端与门边接合位均应作点焊联接,以保证门之力度。
(注:
设计留意尺寸大于600mm宽的门应考虑是否设计成对开门,以从设计上保证门之力度。
)
4.6.3.4对电视墙层板类大受力托盆之四角拼缝与其加骨两端与托盆边接合位均应作点焊加固,以保证拖盆之承载力度。
4.6.3.5特别力度要求按工程图纸或客户之技术要求检验。
4.7打磨
4.7.1打磨主要用于外观的保证以与避免装配时焊点凸起顶位干涉,具体如下:
A.外观表面、角位之焊点凸起磨平、修R位。
B.不锈钢表面处理:
抛光、发线。
C.铝板氧化前擦纹。
D.边角位去批锋、锐角。
4.7.2打磨对线条的处理要流畅,不能出现缺损和线条不追通现象,R位处理要自然与产品外观协调一致。
对外观平面的打磨要平顺,不能出现凹陷打磨过量现象。
4.7.3对外表面为胶沙不锈钢的钣金箱体的打磨,应尽量避免全身打磨,只作边角位局部打磨和发线追通处理。
镜面不锈钢一定不可打磨原身镜面,只可作边角位局部处理。
此点焊接和设计亦需配合,必要时可采用胶粘方式代替焊接。
4.7.4特别要求按工程图纸或客户之技术要求检验。
4.7.5其余按生产打磨工序自检要求。
4.8构制组装
4.8.1构制必须将产品的装配件进行必要的试装,以检验产品的尺寸正确性、结构正确性、使用符合性。
4.8.2必须对产品外观之缝隙、活动件灵活性、产品装配成形后的扭摆度进行必要的调整修配。
4.8.3对产品的维护、方便性进行检验评定。
4.8.4根据各项产品检验与技术条件进行必要的检验,特别要求按工程图纸之技术要求。
4.8.5其余按工序自检要求。
4.9配木检验
因我司钣金产品与配木有着重要关联,故在此对配木的通用检验标准亦作以下规定。
4.9.1外表面之防火胶板、木纹皮等不能有明显的刮伤、划痕,加工时应作保证。
4.9.2木台板之外形尺寸,应于装配时配作,对铁架整体喷粉之台体,应适当预留喷涂后长度增加之余量,方便保证最后之总装外观间隙与配合。
4.9.3各成形板件外观边角不能有缺损,塌角与毛批,木纹皮台板边位一般应加3-5mm实木边。
4.9.4木线边、手枕边应与本体结合牢固,粘接板面不能有起泡和压不牢之现象。
4.9.5有纹向要求之表面应留意纹向的对应,不可乱纹影响整体外观。
4.9.6经PU油喷涂之木手枕与防火胶板之接缝高低应手摸不明显。
4.9.7对木纹皮或实木手枕的表面处理效果应与要求一致,色差符合有关检验要求。
4.9.8尺寸按工程图纸以与整体装配效果配合检验。
4.9.9特别要求按工程图纸检验,其余按工序自检要求检验。
4.10表面喷涂
按《最终表面处理验收标准》检验。
4.11包装
4.11.1包装需对产品作出适当的必要的保护,避免损坏产品。
4.11.2必须按BOM点检配件数量,并按要求作组装、半组装与散装,且组装与半组装的大件货品需校核可否进入安装现场之通道。
4.11.3对BOM中不能组装的螺丝应按配件用途作出标识并分别包装,以方便现场安装以与客人自已安装。
4.11.4《BOM》中出现的单面胶边、海棉胶边,应按所属配件作出粘贴。
我司常见的用于开口面板之单面胶边粘贴要求示如下:
A.开口为利口的面板
B.开口为折边的面板
4.11.5特别要求按工程图纸与资料要求,控制台、电视墙、机柜等主要产品,按各产品之专用设计与检验标准才可包装。
5.0注意事项
5.1上述4.0项之“作业容”,为根据我司产品的通用工艺流程制订,实际制作中可根据各工件的具体流程选用其中检验项目。
对产品要求高于此标准容的需按相关资料要求。
5.2该标准“作业容”中的某些项目,亦可作为工程设计标准在设计时采用,做货时亦作检验标准检验。
6.0相关文件
《图纸》
《BOM》
《控制台产品设计与检验产品标准》
《电视墙