机械制造技术基础课程设计泵体设计说明书.docx
《机械制造技术基础课程设计泵体设计说明书.docx》由会员分享,可在线阅读,更多相关《机械制造技术基础课程设计泵体设计说明书.docx(24页珍藏版)》请在冰豆网上搜索。
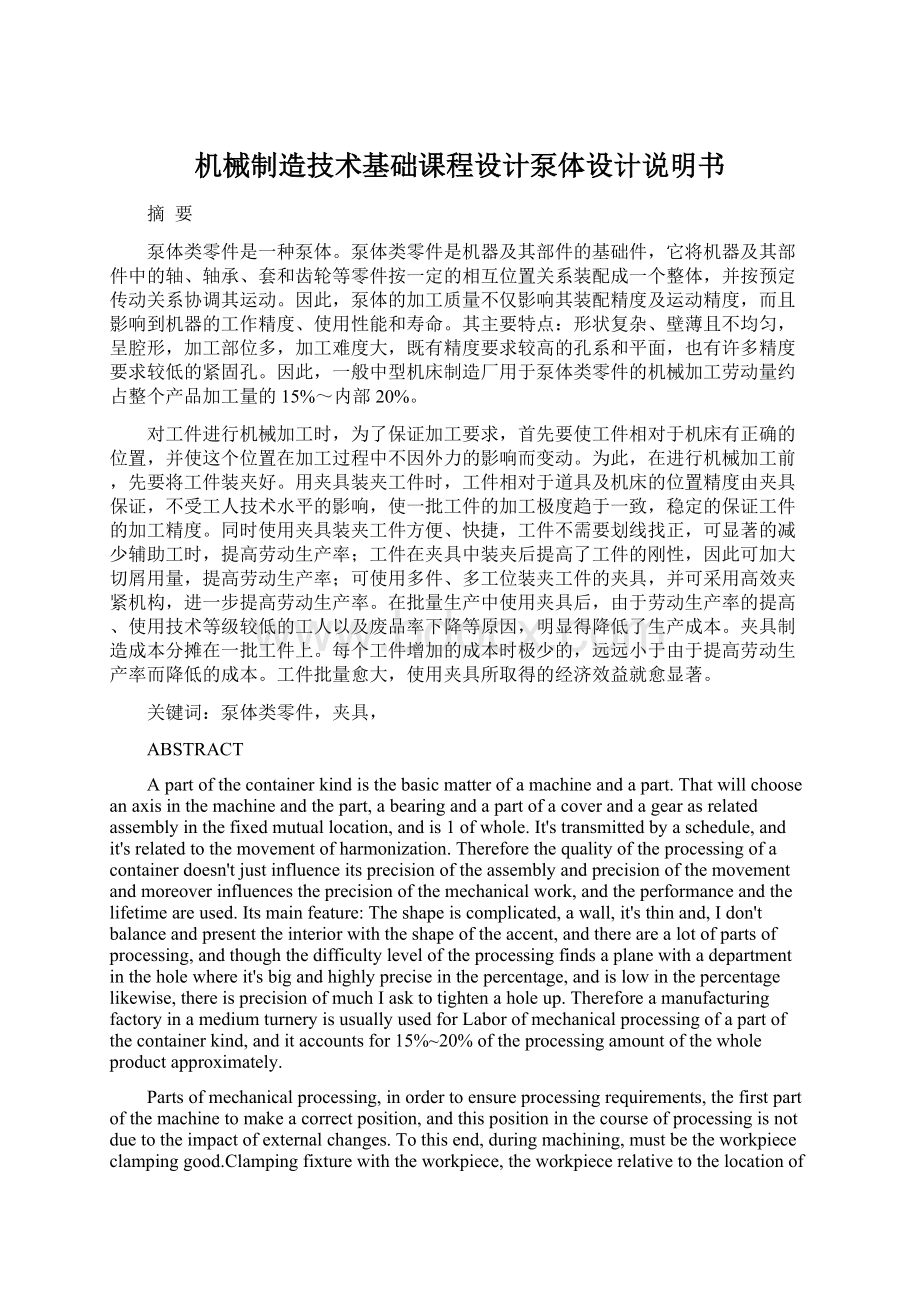
机械制造技术基础课程设计泵体设计说明书
摘要
泵体类零件是一种泵体。
泵体类零件是机器及其部件的基础件,它将机器及其部件中的轴、轴承、套和齿轮等零件按一定的相互位置关系装配成一个整体,并按预定传动关系协调其运动。
因此,泵体的加工质量不仅影响其装配精度及运动精度,而且影响到机器的工作精度、使用性能和寿命。
其主要特点:
形状复杂、壁薄且不均匀,呈腔形,加工部位多,加工难度大,既有精度要求较高的孔系和平面,也有许多精度要求较低的紧固孔。
因此,一般中型机床制造厂用于泵体类零件的机械加工劳动量约占整个产品加工量的15%~内部20%。
对工件进行机械加工时,为了保证加工要求,首先要使工件相对于机床有正确的位置,并使这个位置在加工过程中不因外力的影响而变动。
为此,在进行机械加工前,先要将工件装夹好。
用夹具装夹工件时,工件相对于道具及机床的位置精度由夹具保证,不受工人技术水平的影响,使一批工件的加工极度趋于一致,稳定的保证工件的加工精度。
同时使用夹具装夹工件方便、快捷,工件不需要划线找正,可显著的减少辅助工时,提高劳动生产率;工件在夹具中装夹后提高了工件的刚性,因此可加大切屑用量,提高劳动生产率;可使用多件、多工位装夹工件的夹具,并可采用高效夹紧机构,进一步提高劳动生产率。
在批量生产中使用夹具后,由于劳动生产率的提高、使用技术等级较低的工人以及废品率下降等原因,明显得降低了生产成本。
夹具制造成本分摊在一批工件上。
每个工件增加的成本时极少的,远远小于由于提高劳动生产率而降低的成本。
工件批量愈大,使用夹具所取得的经济效益就愈显著。
关键词:
泵体类零件,夹具,
ABSTRACT
Apartofthecontainerkindisthebasicmatterofamachineandapart.Thatwillchooseanaxisinthemachineandthepart,abearingandapartofacoverandagearasrelatedassemblyinthefixedmutuallocation,andis1ofwhole.It'stransmittedbyaschedule,andit'srelatedtothemovementofharmonization.Thereforethequalityoftheprocessingofacontainerdoesn'tjustinfluenceitsprecisionoftheassemblyandprecisionofthemovementandmoreoverinfluencestheprecisionofthemechanicalwork,andtheperformanceandthelifetimeareused.Itsmainfeature:
Theshapeiscomplicated,awall,it'sthinand,Idon'tbalanceandpresenttheinteriorwiththeshapeoftheaccent,andtherearealotofpartsofprocessing,andthoughthedifficultyleveloftheprocessingfindsaplanewithadepartmentintheholewhereit'sbigandhighlypreciseinthepercentage,andislowinthepercentagelikewise,thereisprecisionofmuchIasktotightenaholeup.ThereforeamanufacturingfactoryinamediumturneryisusuallyusedforLaborofmechanicalprocessingofapartofthecontainerkind,anditaccountsfor15%~20%oftheprocessingamountofthewholeproductapproximately.
Partsofmechanicalprocessing,inordertoensureprocessingrequirements,thefirstpartofthemachinetomakeacorrectposition,andthispositioninthecourseofprocessingisnotduetotheimpactofexternalchanges.Tothisend,duringmachining,mustbetheworkpiececlampinggood.Clampingfixturewiththeworkpiece,theworkpiecerelativetothelocationofpropsandprecisionmachinetoolsfromthefixturethatthetechnicallevelofworkersfromtheimpactofanumberofpartsoftheextremeprocessingline,astableguaranteetheaccuracyofprocessingtheworkpiece.Atthesametimetheuseoftheworkpiececlampingfixtureconvenient,fast,crossedtheworkpiecedoesnotneedtofindis,cansignificantlyreducethesupplementaryworkinghours,improvinglaborproductivity;Workpiecefixtureinthefixtureaftertheincreaseintherigidityoftheworkpiece,itcanincreasetheamountofchip,raisinglaborproductivity;canusepieces,multi-fixturepartsofthefixture,andefficientuseofclampinginstitutions,tofurtherimprovelaborproductivity.Intheuseofmassproductionafterthefixture,duetotheimprovementoflaborproductivity,theuseoftechnologyworkersinlowergradesandrejectratedroppedandotherreasons,obviouslyinthelowerproductioncosts.Fixturemanufacturingcostsassessedinanumberofpartson.Eachpartoftheincreaseinthecostofasmall,farlessthanduetoincreasedlaborproductivityandreducecosts.Workpiecelargerquantities,theuseoffixtureontheeconomicbenefitsachievedbythemarkedlyeffective.
Keywords:
Thefeatureofthepartofthecontainerkind,FixtureFeatures
第1章绪论
1.1泵体浅析
我国摩托车工业经过二十多年的飞跃发展,取得了长足的进步,已成为国民经济中的重要一环,尤其在1993年就以367.49万辆的产量首次超过摩托车王国——日本,成为世界头号摩托车生产大国,1997年则突破1000万辆大关,达1003.7万辆。
截止2005年,我国摩托车产量连续12年位居世界第一。
然而,我国虽是世界摩托车生产第一大国,但不是世界摩托车的强国。
我国摩托车的产品质量与欧、美、日等摩托车强国相比,特别是可靠性方面,仍有相当大的差距。
摩托车行业面临着开发能力低、产品同质化严重、中小排量技术欠缺、知识产权意识尚待提高等诸多问题。
目前我国摩托车主要集中在50mL、70mL、80mL、90mL、100mL、110mL、125mL、150mL等几款中小排量车型上,而250mL、350mL、400mL、750mL以上中高排量车型很少,有的甚至是空缺。
这说明我国摩托车生产技术水平只限于中、小排量低速车上,而且过于集中。
例如,某些型号的跨式车用发动机(如CG125款挺杆机型),全国竟然有256种型号与其外观相似,简单重复、千车一面、水平一般是我国摩托车品种的特点,真正有个性化且作为企业标记性的、有自主知识产权的产品寥寥可数,中、大排量及高速车的开发能力及成熟技术还没有真正掌握,大排量摩托车一直被进口车所垄断,这也是导致我国摩托车市场竞争过于激烈的一个重要原因。
泵体的性能
要求具有高的输出功率和良好的经济性。
(1)提高转速,性能 的主要手段。
(2)提高平均有效压力,提高扭矩。
(3)降低摩擦平均有效压力。
(4)其他提高性能的各项措施。
1.2崩体零件简介
1.2.1泵体类零件的功用及结构特点
泵体类是机器或部件的基础零件,它将机器或部件中的轴、套、齿轮等有关零件组装成一个整体,使它们之间保持正确的相互位置,并按照一定的传动关系协调地传递运动或动力。
因此,泵体的加工质量将直接影响机器或部件的精度、性能和寿命。
常见的泵体类零件有:
机床主轴箱、机床进给箱、变速泵体、减速泵体、发动机缸体和机座等。
根据泵体零件的结构形式不同,可分为整体式泵体,如图8-1a、b、d所示和分离式泵体,如图8-1c所示两大类。
前者是整体铸造、整体加工,加工较困难,但装配精度高;后者可分别制造,便于加工和装配,但增加了装配工作量。
泵体的结构形式虽然多种多样,但仍有共同的主要特点:
形状复杂、壁薄且不均匀,内部呈腔形,加工部位多,加工难度大,既有精度要求较高的孔系和平面,也有许多精度要求较低的紧固孔。
因此,一般中型机床制造厂用于泵体类零件的机械加工劳动量约占整个产品加工量的15%~20%。
1.2.2泵体零件加工工艺特点
泵体类零件的主要结构特点是:
有一对和数对要求严、加工难度大的轴承支承孔;有一个或数个基准面及一些支承面;结构一般比较复杂,壁薄且壁厚不均匀;有许多精度要求不高的紧固用孔。
泵体类零件的主要技术要求是对孔和平面的精度和表面粗糙度的要求;支撑孔的尺寸精度、几何形状精度和表面粗糙度;孔与孔的轴线之间的相互位置精度(平行度、垂直度);装配基准面与加工时的定位基准面的平面度和表面粗糙;各支承孔轴线和平面基准面的尺寸精度、平行度和垂直度。
这些技术要求是保证机器与设备的性能与精度的重要措施。
泵体加工工艺的原则:
1)“先面后孔”的原则。
先加工平面,后加工孔,是泵体零件加工的一般规律。
2)“粗精分开,先粗后精”。
由于泵体类零件结构复杂,主要表面的精度要求高,为减少或消除粗加工时产生的切屑力、夹紧力和切屑热对加工精度的影响,一般应尽可能把粗精加工分开,并分别在不同机床上进行。
至于要求不高的平面,则可将粗精两次进给安排在一个工序内完成,以缩短工艺过程,提高功效。
3)主要表面加工方法的选择。
泵体的主要加工表面为平面和轴承支承孔。
泵体平面的粗加工和半精加工,主要采用刨削和铣削。
铣削的生产率比刨削高,在成批和大量生产中,多采用铣削。
泵体平面的精加工多用磨削。
泵体上的轴承支承孔,一般采用钻--扩--粗铰--精铰或镗--半精镗--精镗的加工方案进行加工。
前者用于加工直径较小的孔,后者用于加工直径较大的孔。
第2章零件的分析
2.1零件的作用
题目所给定的零件是泵体。
泵体包围旋转的叶轮,并设有与叶轮垂直的液体入口和切线出口。
泵体在叶轮四周形成一个截面积逐步扩大的蜗牛形通道,故常称为蜗壳。
叶轮在壳内旋转的方向是顺着蜗壳形通道内逐渐扩大的方向(即按叶轮旋转的方向来说叶片是向后弯的),愈近出口,壳内接受的液体量越大,所以通道的截面积必须逐渐增大。
更为重要的是以高速从叶轮四周抛出的液体在通道内逐渐降低速度,使一大部分动能便转化为静压能,即提高了液体的压力,又减少了因流速过大而引起泵内部的能量损耗。
所以泵壳既作为泵的外壳汇集液体,它本身又是一个能量转换装置
2.2零件的工艺分析
在泵体上:
(1)上部的孔。
如图2.1.
(2)右侧设置孔。
如图2.2
(3)左侧设置安装通。
如图2.3
(4)泵体使用时不能太重,不能变形太大,丧失精度。
故泵机体使用HT200铸出中间部位设置加强筋。
图2.1
图2.2
图2.3
第3章零件的工艺规程设计
3.1选择零件的材料
由前面所讲的泵体上要安装多个功能各异的组件,故其形状比较复杂,而且难以加工。
合金是纯铝加入一些合金元素制成的,如铝—锰合金、铝—铜合金、铝—铜—镁系硬合金、铝—锌—镁—铜系超硬铝合金。
合金比纯铝具有更好的物理力学性能:
易加工、耐久性高、适用范围广、装饰效果好、花色丰富。
合金分为防锈铝、硬铝、超硬铝等种类,各种类均有各自的使用范围,并有各自的代号,以供使用者选用。
合金仍然保持了质轻的特点,但机械性能明显提高。
合金材料的应用有以下三个方面:
一是作为受力构件;二是作为门、窗、管、盖、壳等材料;三是作为装饰和绝热材料。
利用合金阳极氧化处理后可以进行着色的特点,制成各种装饰品。
合金板材、型材表面可以进行防腐、轧花、涂装、印刷等二次加工,制成各种装饰板材、型材,作为装饰材料。
成本低,而且使用一种加工工艺可以大量生产同样的零部件,这也是他的特点之一。
它的材料特性是轻、容易加工、以及在可耐强度方面不象碳素纤维有一个最大受力范围。
在制造一个比较大的零部件时可能会使用好几层碳素纤维,在超过受力能力时该零部件就会象酥饼一样变得一层一层的。
而合金在承受了一定的力量后,会慢慢变形再损坏。
还有就是合金容易加工和具有高度的散热性。
特别是车辆引擎部分特别适合使用铝合金材料。
此外,铝合金的加工工艺多种多样。
通用性较强。
合金铸造工艺性能,通常理解为在充满铸型、结晶和冷却过程中表现最为突出的那些性能的综合。
流动性、收缩性、气密性、铸造应力、吸气性。
这些特性取决于合金的成分,但也与铸造因素、合金加热温度、铸型的复杂程度、浇冒口系统、浇口形状等有关。
3.2确定毛坯的制造形式
根据生产批量,零件的力学性能,参考以下三种铸造方法,分别是离心铸造、熔模铸造、其制造方法的工艺特点如表3.2。
系列发动机它的生产批量大,故泵体毛坯宜用压铸方法铸造,且合金融化后,较其他铸造铝合金的流动性要好些,不易发生冷隔。
(填补不满铸模。
)
铸造方法
基本尺寸
形状复杂性
适用材料
生产方式
铸造孔的最小孔径
铸造最大深径比
铸造最小壁厚
尺寸公差等级CT
尺寸公差值
机械加工余量等级
加工余量值
浇注位置
经济合理性
砂型机器造型
630~1000
复杂
铸铁和有色金属
大批大量
30
10
5
8~10
2.8~6
6~8
7.0~5.0
顶,侧面
底面
合理
熔模铸造
630~1000
非常复杂
适于切削困难的材料
单件及成批生产
5~10
2
—
5~7
1.0~2.0
6~
8
7.0~5.0
顶,侧面
底面
不合理
金属型铸造
630~1000
复杂
铸铁和有色金属
小批到大量
10~20
8
4.5
7~9
2.0~4.0
6~8
7.0~5.0
顶,侧面
底面
不合理
(单位:
mm)
(资料来源:
《机械加工工艺手册》,3-3~3-20)
表3.2
3.3基准的选择
基准:
基准是用来确定生产对象上几何要素的几何关系所依据的那些点、线、面。
基准根据其功用的不同可分别为设计基准和工艺基准。
在工件工序图中,用来确定本工序加工表面位置的基准,加工表面与工序基准之间,一般有两次核对位置要求:
一是加工表面对工序基准的距离要求,即工序尺寸要求;另一次是加工表面对工序基准的形状位置要求,如平行度,垂直度等。
工件定位时,用以确定工件在夹具中位置的表面(或点,线)称为定位基准,定位基准的选择,一般应本着基准重合原则,尽可能选用工序基准作为定位基准,工件在定位时,每个工件的夹具中的位置是不确定的,一般是限制工件的六个自由度,分别是指:
沿三坐标轴的移动自由度,和绕三坐标轴转动的自由度。
基面的选择是工艺规程设计的重要工作之一,基面选择正确合理,可以使加工质量的到保证,减轻劳动强度,生产效率得到提高。
否则,会使加工困难,甚至造成加工零件报废。
[《机械制造技术基础》P110]
(1)粗基准的选择
粗基准选择原则:
选择粗基准,主要是选择第一道机械加工工序的定位基准,以便为后续工序提供精基准。
为了方便地加工出精基准,使精基准面获得所需加工精度,选择粗基准,以便于工件的准确定位。
选择粗基准的的出发点是:
一要考虑如何合理分配各加工表面的余量;二要考虑怎么样保证不加工表面与加工表面间的尺寸及相互位置要求,一般应按下列原则来选择:
1)若工件必须首先保证某重要表面的加工余量均匀,则应优先选择该表面为粗基准。
2)若工件每个表面都有加工要求,为了保证各表面都有足够的加工余量,应选择加工量最少的表面为粗基准。
3)若工件必须保证某个加工表面与加工表面之间的尺寸或位置要求,则应选择某个加工面为粗基准。
4)选择基准的表面应尽可能平整,没有铸造飞边,浇口,冒口或其他缺陷。
粗基准一般只允许使用一次。
基于上述的要求和考虑到安装装配面的精度要求和便于夹紧等实际情况,粗基准选用泵体内一个较大的非加工面在毛坯图上已经标出。
(2)精基准的选择
精基准选择原则:
选择精基准时,应从整个工艺过程来考虑如何保证工件的尺寸精度和位置精度,并要达到使用起来方便可靠。
一般应按下列原则来选择:
1)基准重合原则;应选择设计基准作为定位基准。
2)基准统一原则;应尽可能在多数工序中选用一组统一的定位基准来加工其他各表面,采用统一基准原则可以避免基准转换过程所产生的误差,并可使各工序所使用的夹具结构相同或相似,从而简化夹具的设计和制造。
3)自为基准原则;有些精加工或光整加工工序要求加工余量小而均匀,应选择加工表面本身来作为定位基准。
4)互为基准原则;对于相互位置精度要求高的表面,可以采用互为基准,反复加工的方法。
5)可靠,方便原则;应选择定位可靠,装夹方便的表面作为精基准。
本零件精基准选择泵体上一个最大平面,此平面专配时隔一纸垫在曲轴箱上。
此平面由于长、宽两方向是最大,用它做支靠,加工时安装稳定性好。
精基准放在工序最前面加工。
为了使零件在安装加工时角向位置准确,在泵体上选择相互距离较大的两个螺钉孔精加工为定位销孔,两销孔只作角向定位,零件使用时,它们仍是螺钉安装孔。
3.4制定工艺路线
(1)热处理工序的安排
加工工艺不安排热处理,因此铸件一般不另进行热处理,使用状态极为铸态。
(2)定位基准的选择
粗基准如果选择其他面,则由非加工面到加工面多个尺寸就不一定能保证准确度达到图纸要求。
精基准加工时支靠面不选择最大平面,因为加工时稳定性差一些,加工精度就受到了影响,角向定位也是这样。
(3)泵体的检验
泵体零件加工时,已加工好全部表面,此时安排检验,接着是该零件所属组件组合,这样安排较好。
精度检验的内容有:
表面几何形状精度、尺寸精度、各表面的相互位置精度。
所用量具有专用卡规、百分尺、游标卡尺、塞规、对表环、表架等。
通过对工件进行检验,不仅可以确定工件的加工质量是否能满足设计使用上的要求,而且可以发现影响加工质量关键所在,以使在误差分析的基础上采取有效措施,从而提高加工质量。
3.5加工工艺过程的分析
1)保证相互位置精度
全部加工分在几次安装中进行,先加工孔,后以孔为精基准最终加工其他表面。
泵体多道工序的加工都是以大孔、小孔以及平面组合定位,这种方法减少了工件的安装误差,能获得很高的相互位置精度,其结构简单,制造精度容易保证的主要是孔定位基准的夹具是心轴和定位销。
以孔定位其定心精度很高。
2)防止变形的工艺措施:
泵体在加工过程中,常由于夹紧力、切削力和切削热、热处理等因素的影响而产生变形,使加工精度降低,防止变形注意以下几点:
a)与减少切削力和切削热的影响。
粗、精加工应分开进行,使粗加工产生的变形在精加工中可以得到纠正,也可以采用辅助支撑,增加安装刚性,减少切削力影响。
b)减少夹紧力的影响,工艺上可采取一些措施。
可以分散应力,减少变形。
夹紧力不应集中于工件的某一点,使应力分布在比较大的面积上,以使工件单位面积上所受力较小,从而减少变形。
还可以采用夹紧工件的夹具。
第4章夹具设计
对工件进行机械加工时,为了保证加工要求,首先要使工件相对于机床有正确的位置,并使这个位置在加工过程中不因外力的影响而变动。
为此,在进行机械加工前,先要将工件装夹好。
用夹具装夹工件有下列优点:
1)能稳定的保证工件的加工精度用夹具装夹工件时,工件相对于道具及机床的位置精度由夹具保证,不受工人技术水平的影响,使一批工件的加工极度趋于一致。
2)能提高劳动生产率使用夹具装夹工件方便、快捷,工件不需要划线找正,可显著的减少辅助工时,提高劳动生产率;工件在夹具中装夹后提高了工件的刚性,因此可加大切屑用量,提高劳动生产率;可使用多件、多工位装夹工件的夹具,并可采用高效夹紧机构,进一步提高劳动生产率。
3)能扩大机床的使用范围
4)能降低成本在批量生产中使用夹具后,由于劳动生产率的提高、使用技术等级较低的工人以及废品率下降等原因,明显得降低了生产成本。
夹具制造成本分摊在一批工件上。
每个工件增加的成本时极少的,远远小于由于提高劳动生产率而降低的成本。
工件批量愈大,使用夹具所取得的经济效益就愈显著。
夹具上的各种装置和元件通过夹具体连接成一个整体。
因此,夹具体的形状及尺寸取决于夹具上各种装置的布置及夹具于机床的连接。
对于夹具体有以下几点要求:
1)有适当的精度和尺寸稳定性夹具体上的重要表面,应有适当的尺寸和形状精度,它们之间应有适当的位置精度。
2)有足够的强度和刚度加工过程中,夹具体要承受较大的切屑力和夹紧力。
为保证夹具体不产生不允许的变形和震动,夹具体应有足够的强度和刚度。
3)结构工艺性好夹具体应便于制造、装配和检验。
铸造夹具体上安装各种元件的表面应铸出凸台,以减少加工面积。
夹具体结构形式应便于工件的装卸。
4)排屑方便切屑多时,夹具体上应考虑排屑结构。
5)在机