本科毕业设计论文《烧结钕铁硼磁性材料电镀前处理工艺探究》.docx
《本科毕业设计论文《烧结钕铁硼磁性材料电镀前处理工艺探究》.docx》由会员分享,可在线阅读,更多相关《本科毕业设计论文《烧结钕铁硼磁性材料电镀前处理工艺探究》.docx(25页珍藏版)》请在冰豆网上搜索。
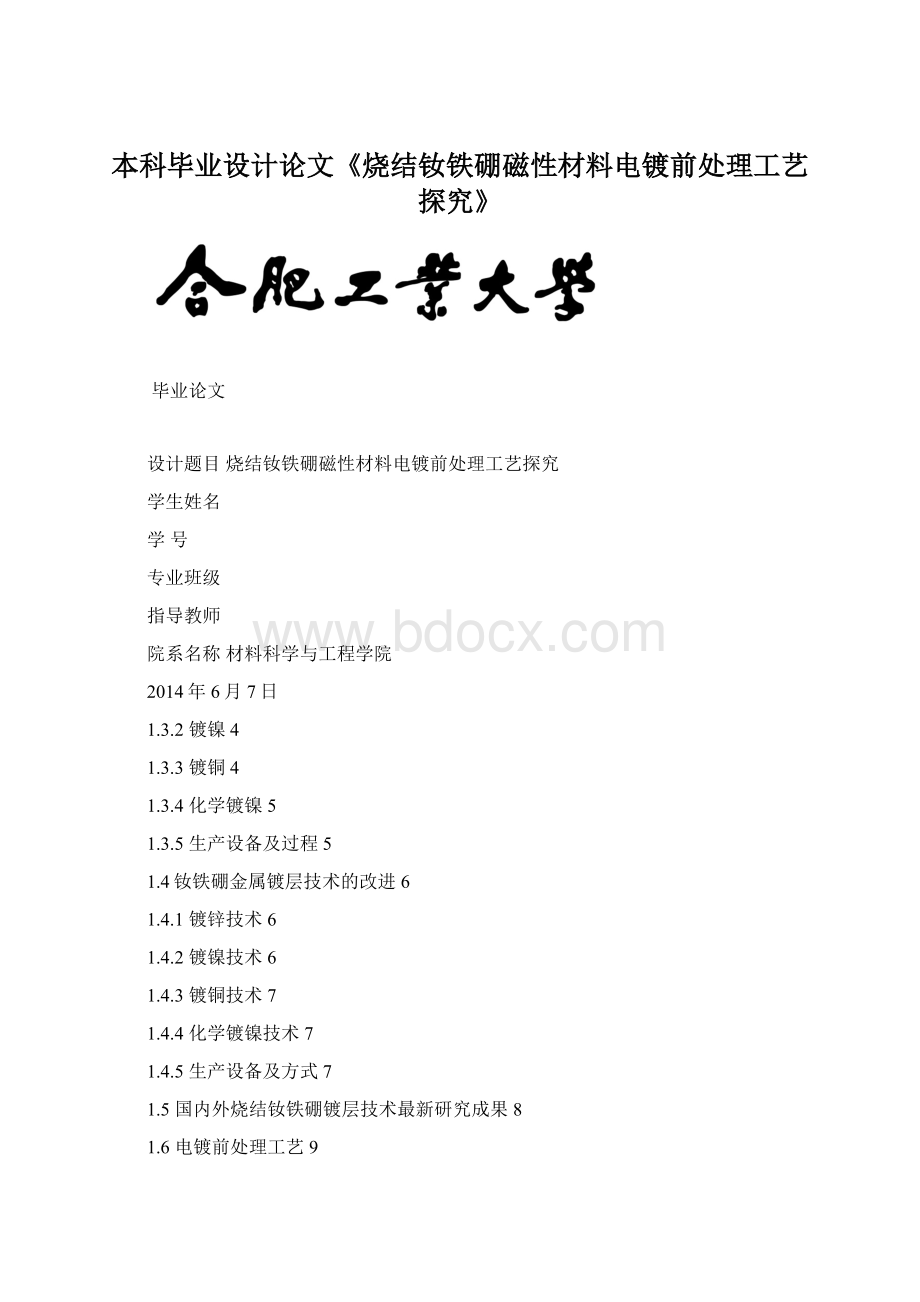
本科毕业设计论文《烧结钕铁硼磁性材料电镀前处理工艺探究》
毕业论文
设计题目烧结钕铁硼磁性材料电镀前处理工艺探究
学生姓名
学号
专业班级
指导教师
院系名称材料科学与工程学院
2014年6月7日
1.3.2镀镍4
1.3.3镀铜4
1.3.4化学镀镍5
1.3.5生产设备及过程5
1.4钕铁硼金属镀层技术的改进6
1.4.1镀锌技术6
1.4.2镀镍技术6
1.4.3镀铜技术7
1.4.4化学镀镍技术7
1.4.5生产设备及方式7
1.5国内外烧结钕铁硼镀层技术最新研究成果8
1.6电镀前处理工艺9
1.6.1烘烤除油9
1.6.2封孔9
1.6.3倒角10
1.6.4化学除油10
1.6.5酸洗11
1.6.6喷砂12
1.7课题来源及研究内容13
2.1.2不同的前处理工艺流程14
2.1.4试验分析16
2.2酸洗时间试验17
2.2.1试验材料17
2.2.2试验方法17
2.2.3试验结果与讨论17
3烧结钕铁硼材料镀镍层退镀试验19
3.1退镀方法的筛选19
3.2退镀试验材料及方法19
3.3试验过程20
3.3.1配方药品的选定20
3.3.2试剂浓度的确定21
3.4电镜分析表面形貌24
4结论与展望24
4.1结论24
4.2展望25
致谢26
参考文献27
烧结钕铁硼磁性材料电镀前处理工艺探究
摘要:
对烧结钕铁硼磁性材料的不同前处理流程和工艺规范进行比对试验,比较不同前处理工艺的镀层结合力和耐蚀性,用电子扫描电镜分析样品酸洗后的表面结构和腐蚀形态。
同时研究了烧结钕铁硼磁性材料镍镀层退镀溶液中试剂的种类和浓度对退除效果的影响,并对退除后的样品进行电镜扫描分析。
研究结果表明,采用40ml/L硝酸、0.5g/L硫脲酸洗30s后效果最佳,经过前处理的样品可直接电镀;以间硝基苯磺酸钠为氧化剂、EDTA为络合剂、柠檬酸钠为辅助络合剂、硫氰化钾为催化剂、氟化钾为缓蚀剂的退镀配方,并确定了配方中各成分的最佳含量。
上述配方退速快、对基体腐蚀小,退镀后可直接重新电镀,适合钕铁硼磁体镍镀层的退除。
关键词:
烧结钕铁硼,磁性材料,电镀前处理,退镀
PretreatmentofElectroplatingonSinteredNdFeBMagneticMaterials
Abstract:
CompareexperimentsonthedifferentpretreatmentsandprepareprocessesofsinteredNdFeBmagneticmaterialswereconducted.Theadhesionandcorrosionresistanceofdifferentpretreatmentprocesseswerecompared.ThesurfacemicrostructureandcorrosionstatusafteracidpicklingwereinvestigatedbySEM.Also,theeffectofsolutionsandtheirconcentrationonthedeplatingofnickelwerestudied.Theresultsindicatethatthespecimencanbedirectlyelectroplatingafter30sofpretreatmentwiththesolutionof40ml/LHNO3and0.5g/LCN2H4S.Optimizeddeplatingsolution,sodiumm-nitrobenzenesulfonateasoxidant,EDTAascomplexingagent,C6H5Na3O7.2H2Oasauxiliarycomplexingagent,KSCNascatalystandKFascorrosioninhibitor,aredetermined.Fasterdeplatingandlessmatrixcorrosionareachievedwiththeaforementionedsolution.Thedeplatedspecimencanbere-plated.
Keywords:
SinteredNdFeB,Magneticmaterials,Pretreatmentofplating,Deplating
1绪论
1.1简介
第三代永磁体钕铁硼自20世纪80年代问世以来,以性价比高、资源储备丰富的优势而备受人们的青睐。
该材料符合现代科学技术向集成化、轻量化及智能化发展的趋势,并有力的促进现代科学技术与信息产业发展。
目前,该材料已在计算机、网络信息、航空航天、通讯、交通、家电、保健等高新技术领域得到广泛应用。
但是当前烧结钕铁硼永磁体在推广应用中还存在一定的问题,即耐腐蚀性差。
烧结钕铁硼磁性材料主要成分为铁Fe(质量分数约为65%)、稀土金属Re(含钕Nd、镝Dy、铽Tb、镨Pr等,总质量分数约为33%)及硼B(质量分数约为1%)。
由于材料中的富钕相和主相之间电位差很大,材料的表面被腐蚀后易发生电化学反应,进一步腐蚀基体,导致材料的磁性能大大降低[1]。
并且,钕铁硼磁体采用粉末冶金工艺生产,材料的实际密度达不到理论密度,内部存在很多微小孔隙,直接暴露在空气中会吸收氧使稀土元素氧化,破坏合金组织。
表层被腐蚀后,由于微小孔洞的存在,腐蚀将会由外到内快速进行,使磁性能严重衰减直至完全丧失,因此钕铁硼磁体表面必须进行严格的表面处理。
目前钕铁硼表面防护多采用电镀、化学镀、电泳及喷涂等工艺,其中电镀工艺因为技术成熟而被广泛应用[2]。
1.2钕铁硼的腐蚀机理
钕铁硼磁体主要由Nd2Fe14B相、富Nd相、富B相三相组成。
相互接触的各相电位不同,在潮湿环境下会发生电化学反应,形成腐蚀原电池,造成晶间腐蚀[3]。
研究结果表明,钕铁硼磁体的腐蚀通常发生在三种环境中:
长时间高温环境、湿暖环境和电化学环境[4]。
1.高温环境:
钕铁硼材料在低于150℃的干燥环境中氧化速度很慢,但温度高于150℃时,即使环境干燥,富钕相也会发生如下反应:
4Nd+3O2→2Nd2O3。
Nd2Fe14B相分解生成Fe和Nd2O3,Fe进一步发生氧化,生成Fe2O3等产物使磁性能下降。
2.湿暖环境:
在湿暖环境下(温度30~50℃,湿度50%~75%),钕铁硼磁体表层晶界处的富Nd相首先会与环境中的水蒸气发生反应,反应生成的H渗入晶界中,与富Nd相进一步发生反应生成NdH3,造成晶界的腐蚀,而NdH3的生成会增大晶界体积,形成晶界应力,进而破坏晶界,使晶界断裂造成磁体粉化。
3.电化学环境:
在电化学环境中,钕铁硼磁体中相互接触的各相之间存在很大的电位差,形成了微电池。
富Nd相和富B相优先发生腐蚀,致使材料在腐蚀介质中表现为晶间腐蚀,使其耐蚀性降低。
1.3钕铁硼磁体金属镀层工艺
目前钕铁硼磁体金属镀层主要采用镀锌、镍铜镍及镍铜化学镍三大工艺组合,其他如镀金、镀银及镀黑镍等,一般在上述工艺基础上另加施镀[5]。
1.3.1镀锌
和普通钢件不同,由于材料中的钕的电负性很高,钕铁硼磁体镀锌不能对基体起到明显的阳极保护作用,因此镀层致密度对耐蚀性影响很大。
目前采用的一般是酸性氯化钾镀锌工艺,该工艺直接在钕铁硼表面施镀,易出现镀层结合力不高、零件易发生腐蚀以及镀液容易受到污染等问题[6]。
这些问题可以通过加快零件表面金属沉积来解决。
沉积越快,零件表面就越不易被氧化。
目前大多采取以下措施:
①使用阴极电流密度上限高的镀液;②采用小容积细长型滚筒;③带电入槽、工序间不间断操作等。
2007年应欧盟RolS指令要求,淘汰传统的铬酸盐钝化工艺,钕铁硼磁体镀锌钝化采用新型的三价铬钝化工艺,目前形成了以蓝白和彩色为主的三价铬钝化膜体系[7]。
然而采用氯化钾镀锌和三价铬钝化组合工艺后,发现三价铬钝化膜耐蚀能力远远低于铬酸盐。
其原因是:
三价铬钝化膜薄,容易受到镀液中的杂质干扰,只有在纯度较高的锌层表面才能形成连续覆盖的膜层。
而氯化钾镀锌层中有机杂质的含量较高,不利于在镀锌件表面形成完全覆盖的钝化膜,所以使三价铬钝化膜的耐蚀能力下降。
烧结钕铁硼磁体镀锌效果图如图1.1所示。
1.3.3镀铜
钕铁硼磁体镀铜是指在底镍与表层镍之间的中间镀铜层,用来减少表层镍的厚度,优点是:
①用铜代替部分镍,可减小磁体磁性能损失;②铜的孔隙率比镍低,能提高镀层的耐蚀性;③降低了电镀成本;④对体积较小的产品(即比表面积大)镍层的磁屏蔽作用更加明显,用铜取代部分镍可以提高产品的磁性能。
从电镀效果来说,镀铜采用氰化镀铜工艺比较好,溶液成分稳定,抗污染能力也很强,并且镀层亮度均匀、应力小,各方面的性能均衡稳定。
但氰化物剧毒,国家对其使用有严格的管理和限制,现在仅有少数厂家仍然使用该工艺。
钕铁硼电镀大多采用半光亮镍打底,采用半光亮镍打底时,酸性镀铜的结合力低[9],所以在现有钕铁硼电镀镍铜镍工艺中,滚镀铜一般不采用这种工艺。
目前钕铁硼镀铜85%以上使用焦磷酸盐镀铜工艺,另外还有近年发展起来的柠檬酸盐镀铜工艺。
多年的生产实践表明,在准确操作的前提下,采用这两种工艺生产,基本能够满足钕铁硼件镀铜的要求[10]。
但这两种工艺仍然存在不足之处:
①焦磷酸盐存在的问题:
a.镀液黏度大,生产过程中易被带出,只适合用于手动线,自动线则不适合使用;b.溶液稳定性差,工艺参数难以控制;c.无法准确判断焦磷酸根和铜离子的比例关系是否正常;d.焦磷酸盐镀铜中需要的光亮剂生产厂家少,光亮剂制造技术不成熟,与镍相比,镀铜光亮剂的添加量更不易掌控。
综上所述,焦磷酸盐镀铜工艺难以实现超前控制,只能在出现镀层质量问题后依靠经验恢复调整。
②柠檬酸盐存在的问题:
该工艺也存在分析溶液成分困难、难以控制等难题,但更主要的问题是,处理措施不当会使工件表面发暗,影响产品质量。
③以上两种工艺存在的共同问题:
焦磷酸根和柠檬酸根都是铜离子的弱络合剂,这两种工艺都对底镍层质量要求高,否则会发生铜置换现象进而影响镀层结合力。
生产中焦磷酸铜溶液稳定性稍差,若钕铁硼基体受到镀液腐蚀,产物将会污染溶液。
采用以上两种工艺生产,一般均要求底镍层平均不低于4~5μm。
然而底镍层过厚增加了总镍层厚度,对小体积产品的磁屏蔽作用明显,磁体磁性能会大幅衰减。
1.3.4化学镀镍
钕铁硼磁体电镀锌、镍基本能够满足镀层耐蚀性的一般要求(中性盐雾试验72h),如果要求更高(如96h以上),就只能增加镀层厚度,但镀层厚度过大会影响磁体磁性能。
化学镀镍可以解决这个问题[11]。
钕铁硼磁体化学镀镍主要采用磷含量高的酸性化学镀镍、磷合金工艺,优点有:
①镀层耐蚀性较高,镀层薄,避免了镍层过厚对磁体磁性能的影响;②高磷化学镍层不导磁,有利于保持磁体磁性能;③钕铁硼镀件磁体深孔、沟槽较多,电镀镍难以取得较好的防护效果,而化学镀镍可实现薄镀层、低磁屏蔽和高防腐性,是钕铁硼磁体表面处理的优良选择。
但是,化学镀也存在明显的缺陷:
其成本比电镀高得多、镀液稳定性差、施镀时有氢析出引起钕铁硼材料吸氢和氢脆、镀层有空洞等。
烧结钕铁硼磁体化学镀镍效果图如图1.3所示。
图1.1烧结钕铁硼磁体镀锌效果图图1.2烧结钕铁硼磁体镀镍效果图
图1.3烧结钕铁硼磁体化学镀镍效果图图1.4钕铁硼材料滚镀自动线
1.4钕铁硼金属镀层技术的改进
目前的钕铁硼金属镀层生产技术,基本满足了大多数产品的要求,但其中一些工艺仍然存在不足,使磁体表面品质难以保持稳定,并且增加了生产成本,因此现有电镀工艺有待进一步的改善[15]。
1.4.1镀锌技术
对于三价铬钝化膜耐蚀性差的问题,若纯锌电镀层工艺不能直接在钕铁硼基体上施镀,可先用氯化钾镀锌打底,然后再镀纯锌层[16]。
另外,提高钕铁硼镀锌层的耐蚀性还可以通过以下方式:
1.采用碱性镀锌层。
碱性镀锌层致密度高,有机杂质夹附少,有利于生成三价铬钝化膜;2.采用锌镍合金镀层。
锌镍合金镀层耐蚀性很好,可做为钕铁硼镀锌的高档镀层。
1.4.2镀镍技术
钕铁硼在简单盐镀液中易受腐蚀污染镀液,可以通过处理镀液中的铁离子来解决这个问题:
1.定期处理镀液,这会增加处理溶液的费用,造成部分溶液流失;2.采用药剂与镀液中的铁离子形成螯合物,这样可延长溶液处理周期,保持生产质量稳定。
底镍层厚会加大对磁体的磁屏蔽作用,底镍层薄可减小其影响,会使钕铁硼基体容易被后续镀铜液腐蚀。
可以采取以下措施:
尽量选用对磁体腐蚀性小的镀铜工艺,镀铜液对基体腐蚀小,可降低底镍层厚度的要求。
表层镍较厚影响磁体磁性能,但表层镍太薄又会降低镀层耐蚀性。
比较好的方案是:
1.首先保持镀铜层为7~9μm;2.然后使用不导磁的高磷化学镍,8~10μm。
这样既能提高镀层耐腐蚀能力,又能减小对磁体磁性能的影响。
1.4.3镀铜技术
镀铜的关键问题是镀铜液对磁体腐蚀严重,且腐蚀产物污染镀铜液。
针对钕铁硼的特殊性,开发新型无氰碱性镀铜工艺,寻找更加稳定的络合剂,是解决问题的关键。
新型无氰碱铜工艺采用络合能力强的络合剂,与钕铁硼基体不产生置换反应。
同时新型无氰碱性镀铜工艺还一下优点:
1.镀液中P(Cu)为7~8g/L,溶液波美度22左右,黏度低,溶液稳定性好,适合自动线连续生产;2.无需添加光亮剂,镀层自光亮度满足要求,生产参数更加容易控制;3.溶液成分易控制,测试方便;4.深镀能力好,铜镀层纯度高、应力低。
生产实践证明,新型无氰碱性镀铜工艺是一种很适合在钕铁硼表面处理生产中采用的镀铜工艺[17]。
1.4.4化学镀镍技术
针对钕铁硼的特殊性,开发低温、高稳定和适合滚镀生产的化学镀镍工艺,是钕铁硼化学镀镍改进的方向[18]。
一套可行性较高的化学镀镍流程如下:
预镀镍2μm→电镀铜4μm→化学镀镍1μm→化学镀镍铜磷合金10~15μm。
该工艺可获得满足96h中性盐雾试验要求的钕铁硼化学镀镍层,并且1.对磁体磁性能影响小;2.溶液操作温度低,约60℃,溶液使用寿命长;3.无滚筒及氟塑料加热器被金属化现象,适合连续生产;4.可以自行配制镍补加液,成本低;5.镀层不含铅、镉,满足RolS指令要求。
1.4.5生产设备及方式
钕铁硼滚镀自动线生产问题较多,现仅就各镀液交叉污染问题提出以下几项改善措施[19]。
1.实现充分水洗。
自动线生产应实现充分水洗,转换镀液时采用两级回收、四级逆流漂洗。
清洗水需精密过滤,纯水效果更佳。
2.选择更适合自动线生产的工艺,解决镍、铜溶液交叉污染问题。
例如,预镀镍采用低浓度工艺,降低黏度,利于水洗环节的清洗效果;镀铜采用新型无氰碱性镀铜工艺,铜离子浓度低,有利于水洗。
3.各镀种强化电解净化环节,通过净化装置消除生产中难以避免的交叉污染,实现溶液的自我维护。
钕铁硼半自动滚镀生产线较适合钕铁硼零件滚镀生产。
钕铁硼各镀种单独成线(如镀锌线、镀底镍线、镀铜线、镀亮镍线等),滚筒运送采用半自动行车。
这种形式兼顾了手动线和自动线的优点劳动生产效率提高,灵活性强,可实现钕铁硼滚镀镀件高质高产。
1.5国内外烧结钕铁硼镀层技术最新研究成果
赵晴等[20]讨论了钕铁硼永磁体表面镀镍工艺,分别对半光亮镍/光亮镍、中性预镀镍/半光亮镍/光亮镍两种体系进行了探究。
结果表明,镀镍层与孔隙率、耐蚀性均有关系,中性预镀镍的性能更好。
MaCB等[21]探讨了温度、电流密度、镀液pH和亚磷酸含量等对电沉积Ni-P微观组织结构的影响。
研究结果表明,通过优化工艺条件得到的Ni-P非晶态合金,在约180h、3.0%NaCl盐雾试验后仍不出现腐蚀点。
张蕾等[22]用新工艺对钕铁硼材料进行表面处理后进行了性能测试,测试表明该工艺极大地提高了钕铁硼耐蚀能力,同时降低了磁性能损失。
李建等[23]采用不同浇铸工艺和破碎工艺制备了三种烧结钕铁硼磁体,对三种磁体及其电镀镍后的防腐性能进行了比较。
研究结果表明,采用速凝薄带配合氢气破碎工艺制备的镀镍磁体防腐性能最佳。
SongZL等[24]利用复合电沉积方法制备了Ni-Al2O3复合镀层,在3.5%NaCl溶液中进行长达288h浸泡实验,证明了复合镀层对永磁体具有优异的腐蚀保护性能。
王昕等[25]研究了不同前处理工艺对烧结型钕铁硼电镀锌层性能的影响,通过对镀层孔隙率、耐蚀性等性能的测试,得到了光亮、孔隙率低、耐蚀性强的镀层。
杨培燕等[26]将超声波技术引入到化学镀中,用于钕铁硼永磁材料的表面防护,利用孔隙率测试、扫描电子显微镜、电化学测试及盐雾试验等检测方法,对镀孔的孔隙率、结合力以及镀层的耐腐蚀性能进行了分析。
研究结果表明,将超声波技术与二次化学镀相结合,应用于永磁材料的表面化学镀Ni-P合金上,能有效地提高镀层的结合力和抗腐蚀能力。
ZhangTS等[27]研究了钕铁硼磁体表面的化学镀镍的工艺,研究表明化学镀镍得到的非晶态Ni-P合金镀层具有高耐蚀性、低的磁屏蔽性,可以作为钕铁硼永磁体的理想涂层之一。
严密等[28]采用超声波化学镀方法,研究了在频率为40kHz超声波条件下化学镀Ni-P合金对钕铁硼磁体抗腐蚀性能的影响。
研究表明,与无超声场下的化学镀Ni-P合金镀层相比,超声条件下化学镀Ni-P合金组织更加细致,有更加优良的耐腐蚀性。
应华根等[29]采用在烧结型钕铁硼永磁体表面化学镀Ni-Cu-P合金镀层的方法来提高磁体的耐腐蚀性能。
腐蚀结果表明,Ni-Cu-P三元合金镀层耐中性盐雾试验的时间为268h,能为磁体提供良好的腐蚀保护。
但是,化学镀也存在明显的缺陷:
其成本比电镀高得多、镀液稳定性差、易引起永磁材料吸氢和氢脆、镀层有空洞等。
1.6电镀前处理工艺
钕铁硼材料中Nd含量高,材料的化学性质极为活泼,在潮湿的空气中极易氧化,与酸发生强烈的反应。
钕铁硼材料的晶界处存在富Nd相,易发生晶间腐蚀,产生大量Nd的氧化物和氢化物使材料粉化。
并且,钕铁硼永磁材料是通过粉末冶金烧结成型,结构疏松,孔隙率高,表面状况较差。
如不采取适当的电镀前处理措施解决以上缺陷,将会使镀层与钕铁硼基体间结合力下降,严重影响镀层的防护能力和使用寿命。
以下介绍几种前处理工艺。
1.6.1烘烤除油
置于200℃左右的烘箱中烘烤1h,使油脂炭化成灰烬。
烧结型Nd-Fe-B永磁体通过粉末冶金方法成型,结构疏松,存在大量孔隙。
其中往往吸附有油脂,用常规除油方法难以除去,较好的方法是将试件置于烘箱中,在200℃左右烘烤1h,除去磁体中的油脂,减小电镀时对镀层的影响。
1.6.2封孔
钕铁硼基体结构疏松、孔隙多,钕铁硼基体在除油、除锈及电镀过程中腐蚀性溶液易渗入孔隙内,使镀层在储存、使用过程中基体与镀层的结合力面逐渐腐蚀粉化,造成镀层脱落。
因此需要通过封孔处理解决基体表面的孔隙问题。
选择的3种封孔工艺[5]为:
1.沸水封孔工艺:
将零件放入沸腾的水(蒸馏水或去离子水)中煮3~5min,通过毛细作用将水吸入孔隙内,使孔隙内部的氧化物通过水合作用生成水合氧化物,增大氧化物体积,封闭孔隙;
2.浸硬脂酸锌工艺:
将硬脂酸锌加热至135℃左右,在其为熔融状态时将试样放入,20~25min后取出冷却,此时孔隙内部被凝固的硬脂酸锌封闭;
3.不封孔:
与其他两种封孔工艺相比较,以考察封孔的效果。
表1.1封孔工艺对镀层外观、性能的影响
工艺
沸水封孔
硬脂酸锌封孔
无封孔
外观
鼓泡数量较少
基本无鼓泡
鼓泡数量多
孔隙率(/cm2)
5
<4
>8
耐蚀性(全浸入)
6小时后有锈迹
10小时无锈迹
3小时有锈迹
结合力
局部起皮
无起皮
起皮脱落严重
从表1.1中可知,采用沸水封孔虽然可以降低基体表面的孔隙率,但效果并不明显;而浸硬脂酸锌工艺获得的镀层孔隙率低、结合力好。
1.6.3倒角
在电镀前进行倒角可以去除产品的尖角,避免电镀时因为滚筒滚动产品表面被尖角划伤。
并且去除尖角后,镀液中的金属在圆滑的边缘部位更容易沉积形成完全覆盖的镀层。
①倒角机的分类:
1.滚动倒角机:
适用于单重G<2g的常规产品,或单重G<7.5g的深孔产品。
最大装载量(产品+磨料)为80kg,其中磨料至少为25kg。
2.震动倒角机:
适用于单重G(1.2g80L的最大装载量为80kg,磨料>30kg;150L的最大装载量为250kg,磨料>100kg。
②磨料的分类:
1.球状(氧化铝):
用于震动倒角(不可用于滚动倒角)。
2.斜三角(氧化铝):
用于R角小的滚动倒角或单重G<3g产品的震动倒角。
3.斜柱状(碳化硅):
震动倒角时可与球状磨料混用(不可用于滚动倒角)。
4.斜三角(碳化硅):
用于R角大的产品滚动倒角或有尖角产品的震动倒角。
③倒角操作:
检查确认倒角机中没有其他物品后开启电源,接着按生产单要求放入适量磨料并加入缓蚀剂溶液,设置震动(滚动)频率,然后放入需要加工的产品,设定倒角时间。
初始频率为30Hz,4~6小时后开始升高频率,每隔2小时提高频率2Hz,在预先设定的倒角时间结束3小时前测定R角,若R角不满足要求则适当增加倒角时间。
易产生的缺陷是产品缺角,通过设置合理的震动(滚动)频率及倒角时间可以减少缺角。
1.6.4化学除油
去除钕铁硼基体表面的油污,不宜选用电化学除油[33]。
因为,阳极除油磁体可能会使阳极溶解;阴极除油,因磁体疏松多孔,大量的析氢导致后续镀层产生鼓泡而影响镀层的质量,所以最好用化学除油。
由于钕铁硼磁体非常活泼,所以化学除油碱性不宜太强,pH值最好控制在10以下。
表1.2和表1.3比较了几种化学除油工艺。
从表1.3可知,1号工艺除油液中加入乳化剂能使镀件表面完全浸润,不但能提高除油效率,还降低了强碱对基体组织的腐蚀,能够获得良好的镀层;2号工艺虽然在一定程度上降低了强碱对基体的腐蚀,但是除油效率低,影响了镀层的表面外观和耐蚀性;3号工艺除油时间过长,会导致基体氧化,使镀层表面出现黄色斑点。
因此综合比较后发现1号工艺最佳。
除油后用热水清洗干净。
另外,还可以使用超声波除油,超声波的空化作用可彻底清除钕铁硼微孔中的油污和酸碱等物质[34]。
在实际操作时,一般用塑料网盛少许零件进行人工晃动清洗,完成了超声除油、酸洗及水洗等步骤后再装入滚筒电镀。
此操作清理彻底、效果好,缺点是工人劳动强度稍大。
表1.2不同的化学除油工艺
编号
1
2
3
工艺规范
OP-102.5ml/L
Na2CO325g/L
Na3PO415g/L
Na2SiO310g/L
温度80℃
时间3min
丙酮
Na2CO312g/L
Na3PO470g/L
洗涤剂0.5g/L
温度65℃
时间5min
表1.3化学除油工艺对镀层外观、性能的影响
工艺
1
2
3
除油效果
除油速度快、彻底镀件表面全浸润
速度慢,除油不彻底
除油慢、彻底镀件表面浸润
镀层外观
镀层完整均匀
局部有盲点
有黄色斑点
孔隙率(/cm2)
<4
空隙较多
7
结合力
无起皮、脱落现象
起皮脱落严重
无起皮、脱落现象
1.6.5酸洗
酸洗工艺过程易产生电镀废品,导致这些产品报废的原因是酸洗时间控制不当导致的产品尺寸超差,以及酸洗时间过长基体表