无损检测与热处理.docx
《无损检测与热处理.docx》由会员分享,可在线阅读,更多相关《无损检测与热处理.docx(22页珍藏版)》请在冰豆网上搜索。
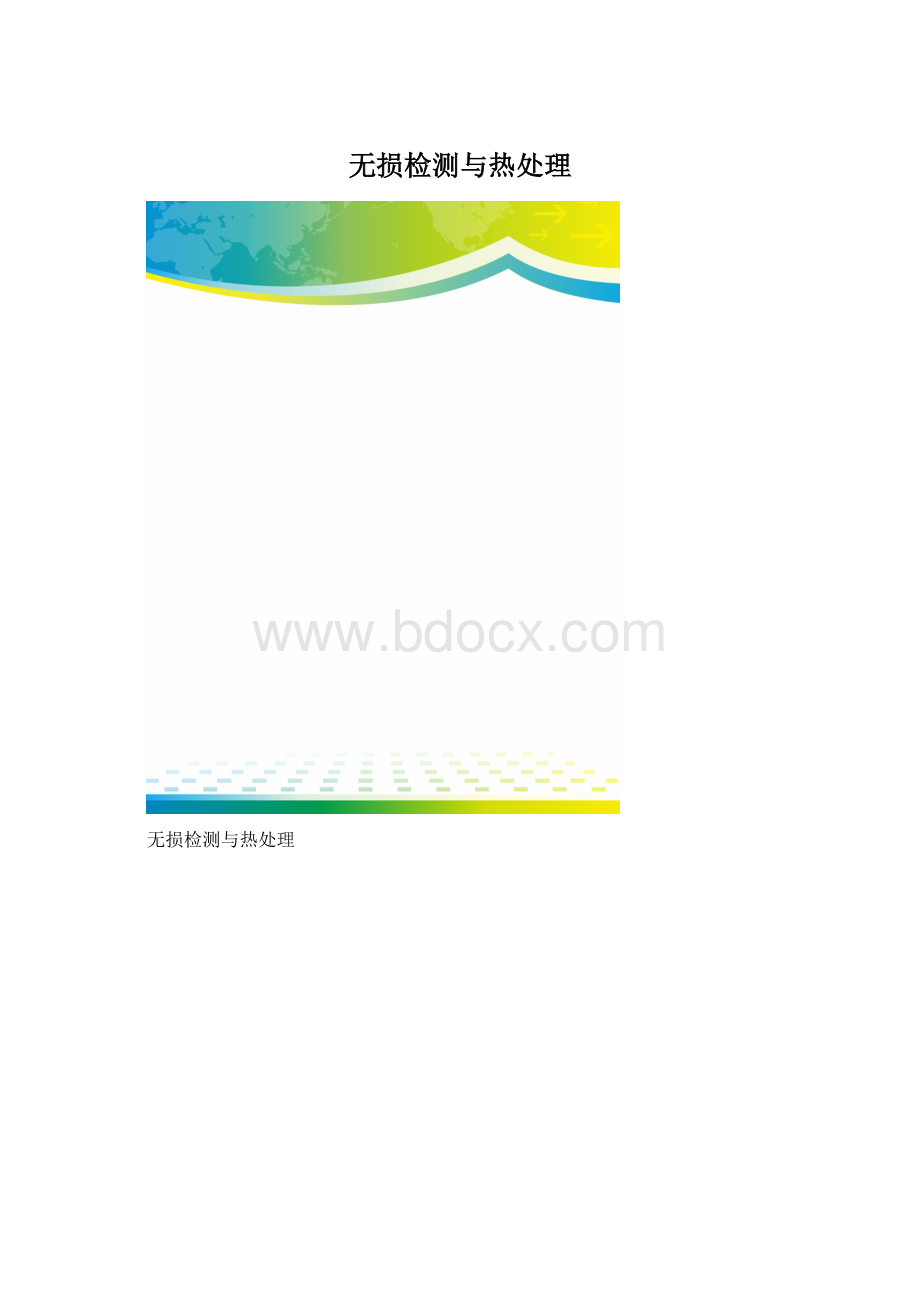
无损检测与热处理
无损检测与热处理
从事热处理生产应当维护好所用的淬火系统及淬火介质。
一般的管理工作包括:
防止介质受污染、保证冷却系统能正常工作、按要求控制好液温以及定期检测淬火介质的冷却特性等等。
而随着科技的不断发展,要求我们不断研究热处理的新工艺、新设备。
各种节能、高效、环保热处理新设备的应用是今后制造业发展的必然趋势。
前言
您每年是否需要10-20天停炉,抽出油槽中几吨甚至几十吨的淬火油进行清洗,人工铲除油槽底部的“淤泥”?
您是否会定期更换或补充淬火油以保证热处理效果?
您的产品表面是否出现污渍和黑斑,不易清洗?
或者在电镀前酸洗时间过长造成工件尺寸缩小或变形而报废?
您是否遇到工件淬火不稳定,强度不均匀,力学性能相差很大?
您的冷却系统是否因介质管道内堵塞造成油温超高冷却效率低下,甚至有时非计划停机?
或者冷却器泄漏水与油混和?
您是否发现淬火油粘度高,加热和冷却能耗大,增加热处理的生产成本?
……
最根本的问题
所有这些情况都与淬火油的污染物有必然联系,其典型种类有:
1.固体颗粒:
灰尘、金属颗粒、表面保护剂和氧化皮等伴随工件同时进入淬火油里。
2.水分:
通过潮气凝聚,冷却系统泄露进入,或是周围环境操作不当引起。
3.氧化物(树脂、积淀)因为淬火油频繁的高温,以上污染物都非常容易分解形成油泥积淀;同时油里被加热的大分子和少量的氧化物,很容易粘结在一起形成小颗粒贴附于淬火原件表面,导致清洗和加工困难。
图一:
油中污染物存在状态
最理想的解决方案
使用丹麦西西延森公司离线式精滤器HDU系列产品,它非常适合热处理系统及淬火油的维护。
其过滤精度为绝对精度3微米,名义精度0.8微米——这意味着98.7%的大于3微米的颗粒物和氧化物以及约50%大于0.8微米的所有微粒在一次过滤中会被去除。
新滤芯使用后滤芯
离线过滤的原理是指过滤单元配有一个循环泵,将油从油槽中吸出,经过过滤器元件再压回到油槽中-如此往复循环。
这创造了一个很理想的过滤条件,它可以24小时持续不断的运行,即低压力以使油槽中的油品持续保持必要的干净程度,延长其使用寿命。
CJC™离线精滤器易于安装,几乎没有维护费用。
而且24小时运转的电费也可以忽略不计。
CJC过滤器直接和淬火油箱连接
CJC™离线精滤器滤芯是由木质纤维成分制成,结构紧实致密,比表面积很大。
因此滤芯具有非常高的纳污量(4L/个),根据污染物密度的不同,单个滤芯纳污量甚至可达十几公斤,仅通过一次过滤,便可移除颗粒物、水分和油品降解产物等等。
因为滤芯的理化性质同时有吸收和吸附的作用,所以工作效率非常高,来自于不溶树脂,淤泥和漆类沉淀的降解产物和氧化产物进一步反应之前,就可以将它们全部去除。
漆类沉淀一旦形成于金属表面,便很难去除。
这类沉淀物非常粘且将进一步形成坚硬的污染物,在金属表面形成粗糙的“砂纸表面”,影响淬火工件表面质量,硬度不均衡,加速热处理系统其他零部件的损坏。
此外,漆类沉淀具有绝缘性,将降低热交换器的效率而且将造成伺服系统,比例阀和控制系统的阻塞。
最经济的效果
-阻止积碳、油泥和颗粒物的形成,提高零部件表面质量及其硬度。
过滤后
过滤前
-稳定淬火,保持油品污染在低水平,减少更换和清洗,使油品寿命延长3-5倍,节能降耗。
-避免因冷却系统(热交换机)故障造成非计划停机。
-降低油品自燃威胁(水的存在)。
锅炉厂
焊接热处理通用工艺
2008年3月10日
1总则
1.1为了保证锅炉焊接热处理质量,指导焊接热处理作业,特制定本工艺。
1.2本工艺适用于锅炉、压力容器、压力管道及在受压元件上焊接非受压元件的安装检修焊焊前预热、后热和焊后热处理工作。
1.3焊接热处理的安全技术、劳动保护应执行国家现行的方针、、法律和法规有关规定。
1.4焊接热处理除执行本工艺的规定外,还应符合国家有关标准规范的规定以及设计图纸的技术要求。
2编写依据
2.1《蒸汽锅炉安全技术监察规程》(劳部发[1996]276号)
2.2DL612—1996《电力工业锅炉压力容器监察规程》
2.3DL/T869—2004《火力发电厂焊接技术规程》
2.4DL/T752—2001《火力发电厂异种钢焊接技术规程》
2.5DL/T819—2002《火力发电厂焊接热处理技术规程》
2.6DL/T734—2000《火力发电厂锅炉汽包焊接修复技术导则》
2.7DL/T868—2004《焊接工艺评定规程》
2.8GB/T17394—1998《金属里氏硬度试验方法》
2.9GB/T16400—2003《绝热用硅酸铝棉及其制品》
3基本要求
3.1人员要求
焊接热处理人员资格:
a)焊接热处理操作人员应具备初中以上文件程度,经专业操作技术培训考核合格并取得资格证书;
b)接热处理技术人员应具备中专及以上文化程度,经专业培训并取得资格证书;
c)没有取得资格证书的人员只能从事辅助性的焊接热处理工作,不能单独作业或对焊接热处理结果进行评价。
热处理技术人员的职责:
a)熟悉相关规程,熟练掌握和严格执行DL/T819—2002《火力发电厂焊接热处理技术规程》;
b)负责编制焊接热处理方案、作业指导书等技术文件;
c)指导并监督热处理工的工作,收集、汇部、整理焊接热处理资料。
热处理工的职责:
a)执行DL/T819—2002《火力发电厂焊接热处理技术规程》,严格按照焊接热处理施工方案、作业指导书进行施工。
b)记录热处理操作过程并在热处理后进行自检。
3.2施工设备和材料要求
热处理设备
a)热处理施工前,热处理设备应经调试合格,设备应满足工艺的要求,参数调节灵活、方便,通用性好,运行稳定、可靠并满足安全要求;
b)热处理应采用自动温度控制箱,并配有自动打印记录仪,设备的温度精度应在±5℃以内,计算机温度控制系统的显示温度应以自动记录仪的温度显示为准进行调整,两者记录误差不大于0.5%;
c)焊接焊接热处理所用的计量器具必须经过校验,并在有效期内使用。
维修后的计量器具必须重新校验;
d)热处理应采用绳状或履带式远红外线加热器,在采用K型热电偶时,其连接线应采用补偿导线。
柔性陶瓷电阻加热器的技术要求应符合DL/T819—2002《火力发电厂焊接热处理技术规程》附录A的规定。
施工材料
a)采用氧—乙炔加热时,应采用瓶装气体。
b)热处理用保温材料应采用无硬碱超细玻璃或硅酸铝纤维毡,保温材料的性
能应满足工艺及环保的要求,产品质量应符合GB/T16400—2003《绝热用硅酸铝棉及其制品》的要求。
c)当用于不锈钢热处理保温时,其热处理材料中的氯离子含量不超过2510,且热电偶应采用不锈钢丝捆绑。
3.3技术准备
热处理施工前,应根据设计文件、标准、规范、工艺的要求,编制热处理施工技术方案或热处理技术措施。
热处理施工前,应向施工作业人员进行详细的施工技术交底。
3.4热处理作业条件
热处理作业人员已熟练掌握热处理的方法、程序和作业技术要求及质量控制标准,并已掌握热处理设备和测量仪表的操作要领。
焊接工作已完成。
焊缝外观质量符合质量标准,除铬钼耐热钢以外,焊缝已经过无损检测合格。
3.5热处理安全要求:
焊接热处理作业时应穿戴必要的劳动防护用品,防止烫伤、触电;
遵守施工和电和易燃易爆物品的安全规定,工作场所应旋转足够数量的灭火器材并设置高温、有电等警示牌;
采用电加热时,至少应有两人值班。
拆装热处理加热装置之前必须确认已切断电源,工作完毕应检查现场并确认无引起火灾的危险后方可离开。
4热处理
4.1热处理范围
下列焊接接头焊后应进行热处理:
a)壁厚>30mm的碳素钢管子与管件;
b)耐热钢管子与管件;
c)经焊接工艺评定需做热处理的焊件。
凡采用氩弧焊或低氢型焊条、焊前预热和焊后适当缓冷的下列部件可免作
焊后热处理。
a)壁厚≤10mm,管径≤108mm的15CrMo、12Cr2Mo钢管;
b)壁厚≤6mm,管径≤108mm的12CrlMoV钢管。
4.2热电偶及加热器安装
炉管焊后热处理时,热电偶及加热器应按热处理施工技术方案或热处理技术措施要求进行安装,热电偶及加热器的安装详见图1。
热电偶应安装在距焊缝边缘30mm的范畴内,热电偶端部与热处理管件的接触处应用砂轮机打磨露出金属光泽。
热电偶的安装应采用细铁丝(或细不锈钢丝)捆扎,为保证所测温度为管了加热的实际温度,在热电偶与加热器之间应垫小块保温玻璃布进行隔离。
4.3焊接热处理工艺
焊接热处理评定
.1焊接热处理工艺必须按照DL/T868—2004《焊接工艺评定规程》的规定,在相应原焊接工艺评定工作中进行评定;
.2实际采用的焊接热处理工艺应与评定的内容一致。
焊前预热
.1焊前预热的前提条件和预热参数按照焊接工艺评定的内容进行,常用材料的焊前预热的条件和预热温度见表1。
表1常用钢的预热温度
钢种
管材
板材
厚度/mm
预热温度/℃
厚度/mm
预热温度/℃
含碳量≤0.35%的碳素钢及其铸件
≥26
100~200
≥30
≥28
100~150
C-Mn(16Mn、16MnR)
≥15
150~200
Mn-V(15MnV、15MnVNR、18MnMoNbR)
0.5Cr~0.5Mo(12CrMo)
—
—
≥15
150~200
1Cr~0.5Mo(15McrMoZG20CrMo)
≥10
150~250
1.5Mn-0.5Mo-V(14MnMoV18MnMonbg)
—
—
1Cr~0.5Mo-V
—
200~300
—
—
1.5Cr~Mo-V(15CrlMolV)
2Cr~0.5Mo-VW(12Cr2MoWVB)
2.25Cr-1Mo(12Cr2Mo10CrMo910)
3Cr-1Mo-Vti(12Cr3MoVSiTiB)
≥6
250~350
9Cr-1Mo-V
—
250~300
—
—
12Cr-1Mo,9C-1Mo
350~400
—
—
1Cr5Mo
—
250℃
ZG15Cr1Mo1V
60℃~100℃(冷焊时)
100℃~150℃(热焊时)
ZG15Cr2Mo1
60℃~100℃(冷焊时)
150℃~200℃(热焊时)
ZG20CrMoV
250℃~300℃(热焊时)
注1:
(1)表中的温度为根据壁厚确定的最低预热温度。
当采用钨极氩弧焊打底时,可按下限温度降低50℃预热。
(2)壁厚大于或等于6mm的合金钢管子或,大板件在负温下焊接时,应比最低的预热温度高20℃~50℃。
壁厚小于6mm的低合金钢管子及壁厚大于15mm的碳素钢管子,在负温下焊接,也应适当预热。
(3)承压件与非承压件焊接时,应按承压件进行预热。
接管座与主管焊接进,应按主管进行预热。
注2:
对外径小于60mm,壁厚小于6mm的管子,采用氩弧焊时,预热温度为50℃~100℃
.2预热宽度从对口中心开始,每侧不小于焊件厚度的3倍,且不少于100mm。
.3特殊情况下的焊前预热要求:
a)在0℃及以下的低温环境下壁厚不小于6mm的耐热钢管子、管件和厚度不小于34mm的板件焊接时,预热温度可以按表1的规定值提高30℃~50℃;
b)在-10℃及以下低温下,壁厚小于6mm的耐热钢管子和壁厚大于15mm的碳素钢管子焊接时应适当预热,温度控制在50℃~70℃,可采和氧-乙炔加热;
c)异种钢焊接时,预热温度应按照焊接性能较差和合金含量较高的一侧选择;
d)接管座和主管焊接时,应以主管规定的预热温度为准;
e)非承压和承压件焊接时,预热温度应按承压件一侧选择。
.4施焊过程中,层间温度应不低于规定的预热温度的下限,且不高于400℃
.5当用绳形加热器进行加热时,坡口两侧布置的加热器应对称,加热器的缠绕圈数、缠绕密度应尽可能相同,缠绕方向应相反。
.6按要求应该预热的焊件返修和重新焊接时应重新预热。
后热
.1有冷裂纹倾向的焊件,当焊接工作停止后,若不能立即进行焊后热处理,应进行后热。
后热恒温度为300℃~400℃,保温时间为2h~4h,使焊年缓慢冷却。
.2对马氏体钢的焊接,如要进行后热,应在马氏体转变结束后进行。
焊后热处理工艺
.1当焊件符合DL/T869—2004《火力发电厂焊接技术规程》中5.4.2条、5.4.3条、5.4.4条和DL/T752—2001《火力发电厂异种钢焊接技术规程》的相关规定,或其他规程、焊接工艺文件有要求时,应进行热处理。
.2常用钢的焊后热处理温度和恒温时间见表2。
表2常用钢的焊后热处理温度和恒温时间
钢种
温度
C≤0.35(20、ZG25)
C-Mn(16Mn)
≤12.5
>12.5~25
>25~37.5
>37.5~50
>50~75
>75~100
>100~125
0.5Cr—0.5Mo(12CrMo)
600~650
—
—
1.5
2
2.25
2.5
2.75
1Cr-0.5Mo
(15CrMo、ZG20CrMo)
650~700
0.5
1
1.5
2
2.25
2.5
2.75
1Cr-0.5Mo-V
(12Cr1MoV)
(ZG20CrMoV
1.5Cr-1MoV
(ZG15Cr1Mo1V)
670~700
0.5
1
1.5
2
2.25
2.5
2.75
2.25Cr-1Mo
720~750
0.5
1
1.5
2
3
4
5
20Cr-0.5Mo-VW
(12Cr2MoWVTiB)
3Cr-1Mo-Vti
(12Cr3MoVSiTiB)
720~750
0.5
1
1.5
2
3
4
5
9Cr-1Mo-V
12Cr-1Mo
750~780
0.75
1.25
1.75
2.25
3.25
4.25
5.25
0.5
1
1.5
2
3
4
5
注:
接管与主管的焊件(管座)返修焊件,其恒温时间可按焊件的名义厚度δ'替代焊件厚度δ来确定,但应不小于30min。
焊件的名义厚度δ'可按下式计算。
h<5mm时,δ'=3h+5
h=5mm-10mm时,δ'=2h+10
h>10mm时,δ'=h+20
式中:
h——焊缝高度或返修焊厚度,mm。
.3焊后热处理的温度选择应按下属原则综合考虑。
a)不能超过Ac1,一般应在Ac1以下30℃~50℃;
b)对调质钢,应低于调质处理时的回火温度;
c)对异种钢,按合金含量低一侧钢材的Ac1选择。
.4焊后热处理、降温速度应符合以下规定:
a)热处理过程中的升温、降温速度应符合以下规定:
1)升温、降温速度一般可按250×25/壁厚℃/h计算,且不大于/h。
2)降温过程中温度在300℃以下可不控制。
b)热处理过程中升、降温速度的控制原则:
1)承压管道和受压元件,焊接热处理升降温度速度为6250/δ(单位为℃/h,δ为焊件厚度)且不大于300℃/h。
降温时,300℃以下可不控制;
2)对主管道与接管的焊接(如管座),应按主管的壁厚计算焊接热处理的升、降温速度;
3)对返修焊件的恒温时间按焊件的名义厚度计算,名义厚度如表3。
表3焊件名义厚度的计算
焊缝高度或返修焊厚度h/mm
焊件的名义厚度δ/mm
h<5mm
δ=3h+5
h=5mm~10mm
δ=2h+10
h>10mm
δ=h+20
.5异种钢焊接接头的焊后处理,应按两侧钢材及所用焊材综合考虑,热处理温度一般不超过合金钢低侧钢材的下临界点ACL。
.6热处理地,应保证内、外壁和焊缝两侧温度均匀,恒温加热范围内任意两侧点间温差应低于50℃。
厚度大于10mm时应采用感应加热或电阻加热。
.7热处理应采用自动温度记录仪进行测温,所用、热电偶及其附件,应按规定要求进行检定或校验。
.8进行热处理时,测温点应对称布置在焊缝中心两侧,且不得小于两点。
.9焊接接头热处理时应同步做好记录,热处理完毕后应做好标识。
4.4焊接热处理工艺措施
温度测量
.1根据加热方法可选择接触式和非接触式测定焊件温度,柔性陶瓷电阻加热和电炉加热一般采用接触式测温,火焰加热一般采用非接触测温。
.2热电偶测温时就根据处理温度和测温仪表的型号选择热电偶,宜选择防水型铠装热电偶。
.3热电偶的直径和长度应根据焊件的大小、加热宽度、固定方式选择。
.4热电偶的安装位置应以保证测温准确可靠、具有代表性为原则,且与焊件接触良好、固定牢固。
.5对于管道应按圆周均匀对称布置,且不少于两点。
水平管道的测温点应上下对称布置。
.6热电偶冷端温度不稳定时,必须使用补偿导线进行补偿,补偿导线与热电偶的型号、极性必须相匹配。
加热范围
.1对于承压管道及其返修焊件的加热,宜采用整圈加热的方法,加热宽度从焊缝中心算起,每侧不小于管子壁厚的3倍,且不小于60mm。
.2主管与接管的加热,宜采用环形加热的方法,加热宽度应不小于两者较大厚度的3倍。
加热器的安装
.1应将焊件的表面焊瘤、焊渣、飞溅清理干净,使加热器与焊件表面紧贴,必要时应用专用夹具,加热器的布置宽度至少应比要求的加热宽度每侧多出60mm。
.2对水平放置的直径大于273mm的管道或大型部件进行焊后热处理时,宜分区控制温度。
保温与温差控制
.1焊接热处理的保温宽度从焊缝隙坡口边缘算起,每侧不得小于管子壁厚5倍,且每侧应比加热器的安装宽度增加不少于100mm。
.2焊接热处理的保温厚度以40mm~60mm为宜。
对于水平管道,可以通过调整保温层厚度的方法来减少管道上下部分的温差。
.3焊接热处理恒温过程中,承压管道在加热范围内任意两点的温差应小于50℃,压力容器在加热范围内最大温差不宜大于65℃。
火焰加热工艺措施
.1用火焰加热进行热处理,应根据焊件的大小选择喷嘴型号与数量。
采用多个喷嘴时,应对称布置、均匀加热。
.2火焰焰心至工件的距离应在10mm以上,喷嘴的移动速度要稳定,不得在一个位置长期停留。
火焰加热时,应注意控制火焰的燃烧状况,防止金属的氧化或增碳。
.3火焰加热应以焊缝为中心,加热宽度为焊缝两侧各外延不少于50mm,火焰加热的恒温时间按每毫米焊件厚度保持1min计算。
.4加热完毕,应立即使用干燥的保温材料进行保温。
4.5质量检验
焊接热处理升温前应进行的核查:
a)加热及测温设备、器具是否符合工艺要求;
b)加热装置的布置、温度控制分区是否合理;
c)加热范围是否符合标准、规范和工艺的要求,保温层厚度、宽度是否合适;
d)温度测点的安装方法、位置和数量是否符合工艺的要求;
e)设定的加热温度、恒温时间、升降温速度等是否符合工艺要求;
f)是否符合现场安全的要求。
焊接热处理后自检的要求:
a)工艺参数在控制范围以内,并有自动记录曲线;
b)热电偶无损坏、无位移;
c)焊接热处理记录曲线与工艺卡吻合;
d)焊件表面无裂纹、无异常。
硬度检验要求
.1当热处理自动记录曲线与工艺卡不符或无自动记录曲线时,应做硬度检验,硬度检验结果应符合表4的要求。
表4焊后热处理的焊缝硬度检测合格值
合金总含量
硬度值(一般不超过母材布氏硬度值+100HBW)
<3%时
布氏硬度值≤270HBW
3%~10%
布氏硬度值≤300HBW
>10%
布氏硬度值≤350HBW
注:
非奥氏体异种钢热处理的硬度值以合金含量低侧母材的成分计算。
.2应对焊缝和母材进行硬度检验,当管道直径≥273mm时,检验部件不少于两处,检验部位应周向均匀分布。
.3采用里氏硬度计检验时,其检验方法和表示方法符合GB/T17394—1988《金属里氏硬度试验方法》的要求。
.4硬度检查结果超过规定范围时,应按班次加倍复查,当加倍复查仍有不合格者时,应将该班次进行100%的复查。
.5焊接热处理工程师应组织热处理技术人员对不合格接头分析原因并制定措施,对不合格接头重新热处理后应重新检验硬度。
5文件控制
5.1焊接热处理技术人员在热处理工作进行前应根据焊接工艺评定制定相应的热处理工艺卡,并报焊接热处理工程师审核。
5.2焊接热处理操作过程应进行记录,并按分项工程的热下理日期顺序进行统计,焊接热处理工程师审核。
5.3焊接热处理技术资料在工程竣工后与焊接技术资料一起移交。