冲压件检验标准.docx
《冲压件检验标准.docx》由会员分享,可在线阅读,更多相关《冲压件检验标准.docx(10页珍藏版)》请在冰豆网上搜索。
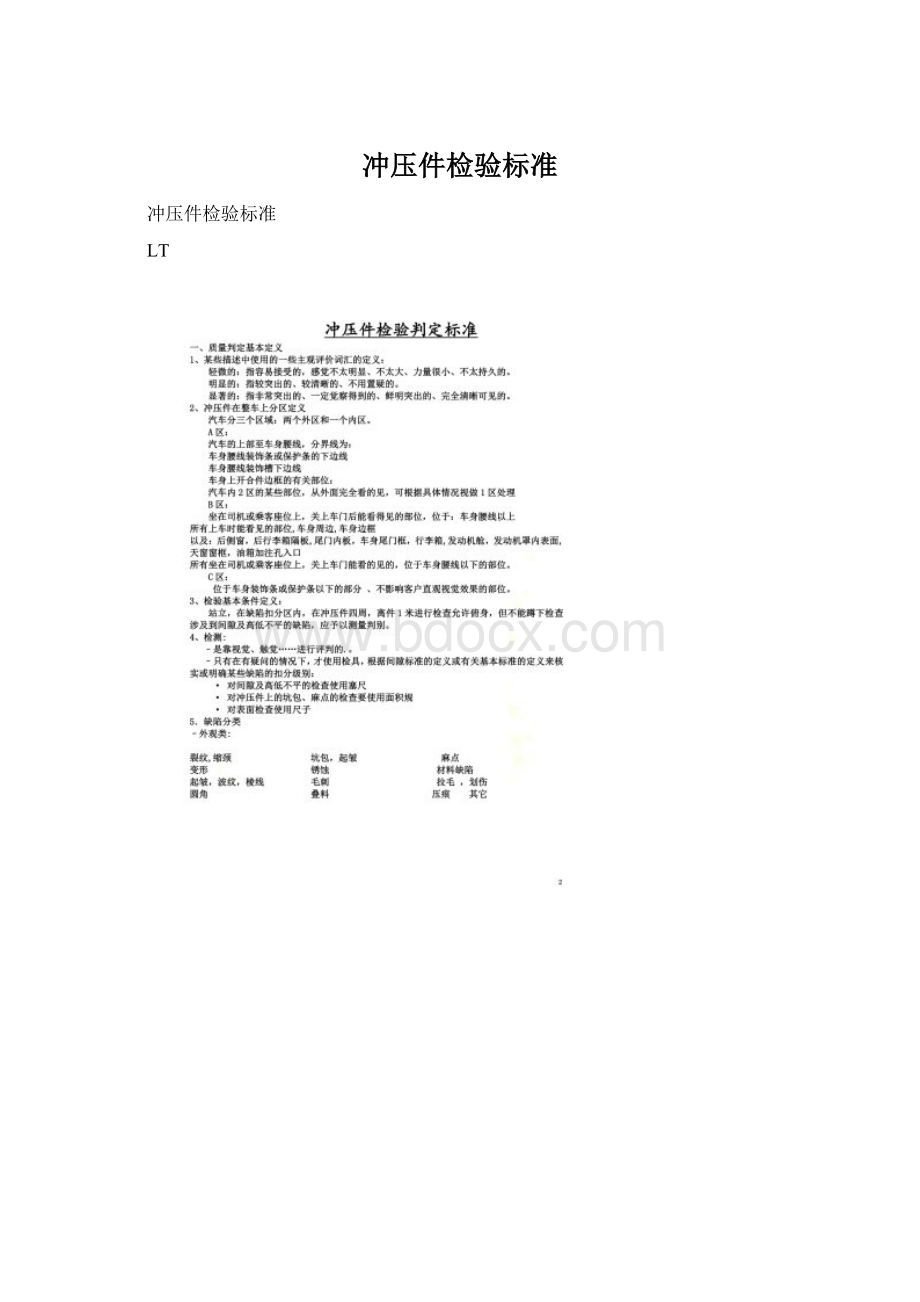
冲压件检验标准
冲压件检验标准
LT
坑包高度≥1mm
返工
返工
返工
放行
放行
麻点
零件2/3面积上能看到麻点或小凸包。
报废
返工
报废
返工
放行
零件表面用油石磨件之前用手感觉明显的麻点或麻点群。
返工
放行
返工
放行
放行
锈蚀
锈蚀厚度≥料厚的40%
报废
表面质量受锈蚀影响但可通过打磨修复。
返工
返工
返工
返工
返工
材料缺陷
料厚明显不符合要求,表面有明显的桔皮滑移线、镀锌层疏松、
锌皮脱落长度≥300mm宽度≥5mm
报废
轻微的材料缺陷、磨件后可见的材料缺陷
返工
放行
返工
放行
放行
起皱/波纹/棱线
棱线、弧线度明显地不清晰、不光顺;肉眼就能看出的严重皱折、
棱线错位,严重影响焊接及装配。
报废
棱线、弧度不够清晰光顺;非一区内用肉眼可见的皱纹、波纹、
棱线错位、在要求严格的部位还包括磨件后的可见波纹等缺陷。
返工
放行
返工
放行
放行
毛刺
装配面上的粗毛刺(大于料厚的45%)有危险性的粗毛刺。
返工
拉毛
拉毛深度≥料厚的20%或宽度≥2mm、长度≥5mm
返工
返工
返工
返工
放行
压痕
压痕深度≥料厚的40%
报废
返工
报废
返工
返工
料厚的10%<压痕深度<料厚的40%
返工
返工
返工
返工
放行
划伤
未经专业训练的人一眼就能看出的划伤,深度≥料厚的50%
报废
返工
报废
返工
返工
指甲触及有感觉
返工
返工
返工
放行
放行
圆角
圆角半径不均匀,未达到要求,明显地不清晰、不光顺;
报废
报废
报废
报废
报废
圆角半径不够均匀,不够清晰光顺;配合间隙较之原状态
相差2mm以上
返工
返工
返工
返工
返工
叠料
板料重叠宽度≥8mm
报废
报废
返工
返工
返工
其它
能引起严重功能障碍的缺陷。
报废
对使用有明显影响的缺陷。
返工
6、尺寸要求:
冲压件按其功能分为三类,A类是外表面件,其要求最高,其次是B类,主要是结构件。
最后是C类,例如支架之类。
冲压件放于合格的检具上,特殊要求的尺寸和公差按产品图纸要求,其它按照“冲压件的未注允许公差表”执行。
补充:
冲压件的未注允许公差表
一般位置精度:
(A类件:
±0.5,B类件:
±1.0,C类件:
±1.5)
一般孔:
中心位置精度:
±0.5
直径轮廓:
(塞规测量)+0.5,-0.0;(最大值/最小值之间的差值,游标卡尺测量)0.15
孔距(孔与孔):
±0.5
工具孔:
直径:
+0.2,-0.0基准到基准:
±0.2
阶梯(搭接):
深度(高度差):
+0.3,-0.0位置精度:
±1.0
配合面精度:
(B类面:
±0.7,C类面:
±1.0)
翻边宽度:
+1.0,-0.5
一般曲率半径:
±0.5
角度:
±2度
安装孔:
直径轮廓(塞规测量):
±0.5孔距(孔与孔,塑料件装配用):
±0.5
孔距(孔与孔,金属件装配用):
±0.3
一致性
同一批中的五个样品的所有的检点的六个标准值不得超过1.0毫米。
其平均值的移动较之前一批不得大于±0.3毫米。
对称性
左右手对称件的所有的尺寸差值应在±0.5毫米范围内,所有的位置差应在±0.75毫米内。
如特殊要求和情况需要,可以把冲压件放于合格的检具上用三座标测量冲压件型面尺寸:
测量要素尺寸要求按产品图纸和“冲压件的未注允许公差表”执行。
一般检测原则为:
检测任意一点与数模的空间公差在±0.2mm以内;装配、定位和基准孔的公差控制在0.10mm。
冲压件放于合格的检具上,型面公差±0.5mm,基准孔孔位公差±0.20mm,轮廓尺寸公差±0.5~2mm。
具体数值以冲压件等级不同而变化。
外覆盖件的检查
一、检验方法:
1、触摸检查
●用干净的纱布将外覆盖件的表面擦干净。
●检验人员需戴上触摸手套沿着零件纵向紧贴零件表面触摸,这种检验方法取决于检验员的经验,必要时可用油石打磨被探知的可疑区域并加以验证,但这种方法不失为一种行之有效的快速检验方法。
2、油石打磨
●用干净的纱布将外覆盖件的表面擦干净。
●打磨用油石(20×13×100mm或更大)
●有园弧的地方和难以接触到的地方用相对较小的油石打磨(例如:
8×100mm的半园形油石)
●油石粒度的选择取决于表面状况(如粗糙度,镀锌等)。
建议用细粒度的油石。
油石打磨的方向基本上沿纵向进行,并且很好地贴合零件的表面,部分特殊的地方还可以补充横向的打磨。
3、涂油检查(Highlightoil)
●用干净的纱布将外覆盖件的表面擦干净。
●用干净的刷子沿着同一个方向均匀地涂油至零件的整个外表面。
把涂完油的零件放在Highlight下检查,建议把零件竖在车身位置上。
用此法可很容易地发现零件上的微小的麻点、瘪塘、波纹。
二、常见的缺陷及标准
1、碎裂
检查方法:
目视。
标准;对于外覆盖件任何碎裂的零件都是不可接受的。
2、拉伤、晶粒粗大、暗伤
检查方法:
目视
标准:
对于外覆件任何导致零件潜在碎裂的拉伤、晶粒粗大、暗伤都是不可接收的,尤其是四门、两盖的咬边翻边部位。
3、瘪塘
检查方法:
目视、油石打磨、触摸、涂油
标准:
A类缺陷:
是用户不能接收的缺陷,没有经过培训的用户也能注意
这类瘪塘发现后必须立即对冲压件进行冻结。
B类缺陷:
是一种使人感到不愉快的缺陷,它是在冲压件外表面上摸得着和看得见的可确定的瘪塘。
C类缺陷:
是需要修正的缺陷,这些瘪塘绝大多数处于模棱两可的情况下,只有在油石打磨后才看得出。
4、波浪
检查方法:
目视、油石打磨、触摸、涂油
标准:
A类缺陷:
是用户不能接收的缺陷,没有经过培训的用户也能注意
这类瘪塘发现后必须立即对冲压件进行冻结。
B类缺陷:
是一种使人感到不愉快的缺陷,它是在冲压件外表面上摸得着和看得见的可确定的波浪。
C类缺陷:
是需要修正的缺陷,这些波浪多数处于模棱两可的情况下,只有在油石打磨后才看得出。
5、翻边、切边不平整及短缺
检查方法:
目视、触摸
标准:
对于外覆盖件任何翻边、切边的不平整及短缺,影响了咬边质量及焊接搭边不平整、短缺,从而影响焊接质量都是不可接受的。
6、毛刺:
(切边、冲孔)
检查方法:
目视
标准:
毛刺的长度要求小于板料厚度的10%。
任何影响焊接搭边贴合程度的毛刺是不可接受的。
任何容易导致人身伤害的毛刺是不可接受的。
任何影响零件定位及装配的冲孔毛刺是不可接受的。
7、拉毛及划伤:
检查方法:
目视
标准:
外覆盖的外表面不允许存在拉毛及划伤,外覆盖件的内表面不允许存在影响外表面质量
的划伤。
内覆盖件表面不允许存在潜在的导致零件拉裂的严重划伤。
8、回弹:
检查方法:
放在检具上检查
标准:
冲压件不允许存在严重的回弹从而导致零件间的尺寸匹配和焊接变形。
9、漏冲孔
检查方法:
目视检查并用水溶性记号笔作计数标记
标准:
零件上任何孔的漏冲将影响零件的的定位与装配,是不可接受的。
10.起皱
检查方法:
目视
标准:
外覆盖件不允许存在任何顾客容易察觉的起皱,内覆盖件不允许存在严重的起皱从而导致材料重迭。
11、麻点群、麻点、压痕
检查方法:
目视、油石打磨、触摸、涂油
标准:
A类缺陷:
麻点集中,超过整个面积2/3都分布有麻点。
B类缺陷:
麻点可看到、可摸到。
C类缺陷:
打磨后可见单独分布的麻点,在1区要求麻点间距离为300mm或更大。
12、打磨缺陷、打磨印
检查方法:
目视、油石打磨
标准:
A类缺陷:
打磨穿了,在外表面上明显可见,所有顾客都立即可见。
B类缺陷:
能看到、摸到,在有争议的地方打磨后也能证明。
C类缺陷:
用油石打磨后能看出。
13、材料缺陷
检查方法:
目视
标准:
材料强度不符合要求,轧钢板留下的痕迹、重叠、桔皮、有条纹、镀锌表面疏松、镀锌层剥落。
14、油花纹
检查方法:
目视
标准:
外覆盖件经油石打磨后不允许存在明显得印痕。