470万吨氧化铝溶出工段监理细则工艺管道.docx
《470万吨氧化铝溶出工段监理细则工艺管道.docx》由会员分享,可在线阅读,更多相关《470万吨氧化铝溶出工段监理细则工艺管道.docx(40页珍藏版)》请在冰豆网上搜索。
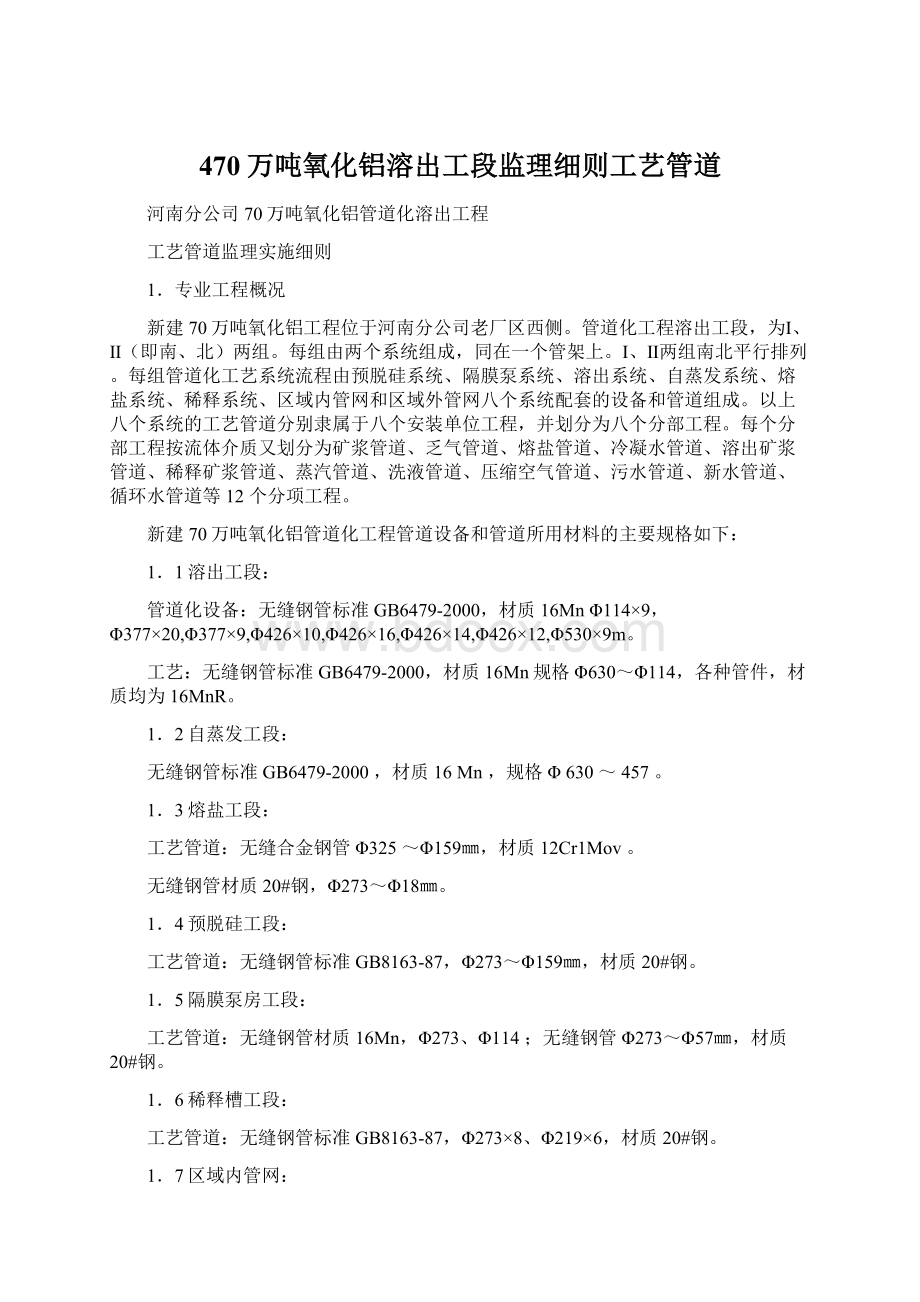
470万吨氧化铝溶出工段监理细则工艺管道
河南分公司70万吨氧化铝管道化溶出工程
工艺管道监理实施细则
1.专业工程概况
新建70万吨氧化铝工程位于河南分公司老厂区西侧。
管道化工程溶出工段,为Ⅰ、Ⅱ(即南、北)两组。
每组由两个系统组成,同在一个管架上。
Ⅰ、Ⅱ两组南北平行排列。
每组管道化工艺系统流程由预脱硅系统、隔膜泵系统、溶出系统、自蒸发系统、熔盐系统、稀释系统、区域内管网和区域外管网八个系统配套的设备和管道组成。
以上八个系统的工艺管道分别隶属于八个安装单位工程,并划分为八个分部工程。
每个分部工程按流体介质又划分为矿浆管道、乏气管道、熔盐管道、冷凝水管道、溶出矿浆管道、稀释矿浆管道、蒸汽管道、洗液管道、压缩空气管道、污水管道、新水管道、循环水管道等12个分项工程。
新建70万吨氧化铝管道化工程管道设备和管道所用材料的主要规格如下:
1.1溶出工段:
管道化设备:
无缝钢管标准GB6479-2000,材质16MnΦ114×9,Φ377×20,Φ377×9,Φ426×10,Φ426×16,Φ426×14,Φ426×12,Φ530×9m。
工艺:
无缝钢管标准GB6479-2000,材质16Mn规格Φ630~Φ114,各种管件,材质均为16MnR。
1.2自蒸发工段:
无缝钢管标准GB6479-2000,材质16Mn,规格Φ630~457。
1.3熔盐工段:
工艺管道:
无缝合金钢管Φ325~Φ159㎜,材质12Cr1Mov。
无缝钢管材质20#钢,Φ273~Φ18㎜。
1.4预脱硅工段:
工艺管道:
无缝钢管标准GB8163-87,Φ273~Φ159㎜,材质20#钢。
1.5隔膜泵房工段:
工艺管道:
无缝钢管材质16Mn,Φ273、Φ114;无缝钢管Φ273~Φ57㎜,材质20#钢。
1.6稀释槽工段:
工艺管道:
无缝钢管标准GB8163-87,Φ273×8、Φ219×6,材质20#钢。
1.7区域内管网:
工艺管道:
无缝钢管标准GB8163-87,Φ273×10~Φ157×3.5,材质20#钢,无缝钢管标准GB6479-2000,材质16Mn,规格Φ114×9、Φ325×8,焊接钢管Φ219×6~Φ57×3.5。
1.8区域外管网:
无缝钢管标准GB8163-87,材质20#钢,规格Φ273~Φ108。
2.编制依据
2.170万吨氧化铝工程监理规划;
2.2长铝设计院工艺图纸;
2.3《工业金属管道工程施工及验收规范》(GB50235-97);
2.4《现场设备、工业管道焊接工程施工及验收规范》(GB50236-98);
2.5《钢制压力容器焊接规程》(JB/T4709-2000);
2.6《管壳式换热器》(GB50319-2000/GB151-1999);
2.7《钢制压力容器》(GB150-1998);
2.8《电力建设施工及验收技术规范管道篇》(DL5031-94);
2.9《电力建设施工及验收技术规范火力发电厂焊接篇》(DL5007-92);
2.10《火力发电厂汽水管道零件及部件典型设计》;
2.11《压力容器无损检测》(JB4730-94);
2.12审批的施工组织设计和施工方案;
2.13《建设工程监理规范》。
3.监理工作程序
为保证管道化设备、工艺管道的安装工程质量、进度,严格按照施工规范和管道安装质量标准,遵照《建设监理规范》和监理委托合同,对70万吨氧化铝管道化工程的工程质量、工程进度和投资费用进行控制和协调。
根据本工程施工过程的工序,工艺流程,结合实际情况,制定质量工作控制流程如下图:
否
否
否
是
否
4.监理工作的要点及目标值
4.1.工程承包单位质量保证体系
4.1.1工程企业营业执照、施工资质证书。
(留复印件)
4.1.2工程承包单位必须持有的压力容器制造、安装许可证(留复印件)。
4.1.3焊接工艺评定、压力容器焊接焊工证、无损检测人员资格证。
(留复印件)
4.1.4施工组织设计和各专业施工技术措施。
4.1.5原材料进场质量检验报告。
4.1.6管式换热器的焊接、热处理和无损探伤记录。
4.1.7管式换热器内管焊缝硬度测试记录。
4.1.8管式换热器制作安装质量检查记录。
4.1.9工艺管道安装质量检查记录
4.2.原材料进场报验检查
4.2.1原材料进场检查报验制度:
承包单位在原材料进场后,应认真检查管子、管道组成件及管道支承件的材质、规格、型号、数量、外观质量应符合设计文件或规范的有关规定,必须具有制造厂家的质量证明文件,其质量不得低于国家现行标准的规定。
自检的主要内容:
外观检查、检测,其表面不得有裂纹、缩孔、夹渣、粘砂、折迭、漏焊、重皮等缺陷,加工表面应光滑,不允许有尖锐划痕,检查合格后填写自检记录,向监理单位进行材料报验,并填写材料报验申报表。
4.2.2选用GB6479标准的钢管时,其尺寸精度应选取高级,使用单位向钢管制造厂家订货时应注明该要求。
4.2.316Mn钢管的化学成分如下:
牌号
化学成分(%)
16Mn
C
Mn
Si
S
P
0.12~0.20
1.20~1.60
0.20~0.55
≯0.045
≯0.045
4.2.4合金钢管道及组成件应采用光谱分析或其它方法对材质进行复查,并应做标记。
4.2.5管材及管道组成件检查应符合下表:
序号
名称
材质
规格
允许偏差(㎜)
复查标准
外径
壁厚
1
钢管
16Mn
Φ114×9
±1
±1
光谱分析和硬度测试
2
钢管
16Mn
Φ377×20
±3
±2.3
光谱分析和硬度测试
3
钢管
16Mn
Φ377×9
±3
±1.1
光谱分析和硬度测试
4
钢管
16Mn
Φ426×10
±4
±1.1
光谱分析和硬度测试
5
钢管
16Mn
Φ426×16
±4
±2
光谱分析和硬度测试
6
钢管
16Mn
Φ426×14
±4
±1.75
光谱分析和硬度测试
7
钢管
16Mn
Φ426×12
±4
±1.5
光谱分析和硬度测试
8
钢管
16Mn
Φ426×10
±4
±1.1
光谱分析和硬度测试
9
钢管
16Mn
Φ530×9
±4
±1.1
光谱分析和硬度测试
10
钢管
16Mn
Φ219×6
±2.7
±0.75
光谱分析和硬度测试
11
钢管
16Mn
Φ219×12
±2.7
±1.8
光谱分析和硬度测试
12
钢管
16Mn
Φ273×11
±3
±1.65
光谱分析和硬度测试
13
钢管
16Mn
Φ325×9
±3.7
±1.35
光谱分析和硬度测试
14
钢管
16Mn
Φ630×9
±5
±1.35
光谱分析和硬度测试
15
钢管
16Mn
Φ114×4
±1
±0.5
光谱分析和硬度测试
16
钢管
16Mn
Φ159×4.5
±1.6
±0.5
光谱分析和硬度测试
17
钢管
16Mn
Φ57×3.5
±0.7
±0.4
光谱分析和硬度测试
18
弯管
16Mn
Φ114×9
最大外径与最小外径之差小于5.7㎜,着色探伤和硬度探伤。
19
钢管
12Cr1MoV
Φ273×8
±3
±1.65
光谱分析和硬度测试
20
钢管
12Cr1MoV
Φ219×7
±2.7
±0.25
光谱分析和硬度测试
21
钢管
12Cr1MoV
Φ325×9
±3.7
±1.35
光谱分析和硬度测试
22
钢管
12Cr1MoV
Φ159×6
±1.6
±0.5
光谱分析和硬度测试
23
法兰
12Cr1MoV
Φ300~Φ150
全部光谱分析和100%超声波探伤。
外观检查:
法兰密封面应光洁,不得有径向沟槽、气孔、裂纹、毛刺,凸面高度不得小于凹槽的深度。
24
大弯管
16MnR
Φ820~Φ630
100%X光射线探伤和光谱分析,Ⅱ级合格。
25
法兰
16MnR
Φ114~Φ377
全部光谱分析和100%超声波探伤。
外观检查:
法兰密封面应光洁,不得有径向沟槽、气孔、裂纹、毛刺,凸面高度不得小于凹槽的深度。
26
锥管
16MnR
全部光谱分析和硬度测试。
27
螺柱
35CrMoA
M45×3×350
硬度测试,抽检5%
28
螺柱
35CrMoA
M24×130
硬度测试,抽检5%
29
螺柱
35CrMoA
M27×140
硬度测试,抽检5%
30
螺柱
35CrMoA
M33×2×185
硬度测试,抽检5%
31
螺柱
35CrMoA
M33×2×165
硬度测试,抽检5%
32
螺柱
35CrMoA
M20×105
硬度测试,抽检5%
33
螺柱
35CrMoA
M45×3×245
硬度测试,抽检5%
34
螺柱
35CrMoA
M39×2×215
硬度测试,抽检5%
35
螺柱
35CrMoA
M33×2×170
硬度测试,抽检5%
36
螺柱
35CrMoA
M30×2×180
硬度测试,抽检5%
37
螺柱
35CrMoA
M30×2×140
硬度测试,抽检5%
38
螺柱
35CrMoA
M30×2×150
硬度测试,抽检5%
39
螺母
30CrMoA
M45×3
硬度测试,抽检5%
40
螺母
30CrMoA
M24
硬度测试,抽检5%
41
螺母
30CrMoA
M27
硬度测试,抽检5%
42
螺母
30CrMoA
M33×2
硬度测试,抽检5%
43
螺母
30CrMoA
M20
硬度测试,抽检5%
44
螺母
30CrMoA
M39×2
硬度测试,抽检5%
45
螺母
30CrMoA
M30×2
硬度测试,抽检5%
4.2.6螺柱、螺栓的硬度应比螺母稍高,螺纹应完整,无伤痕、毛刺等缺陷,螺栓与螺母应配合良好,无松动或卡涩现象。
4.2.7合金钢阀门的内件材质应进行抽查,采用光谱分析或其它方法对材质进行复查,每批(同制造厂、同规格、同型号、以下相同)抽查数量不得少于1个。
4.2.8输送设计压力大于1Mpa的阀门,应逐个进行壳体强度压力试验和密封试验。
不合格者,不得使用。
4.2.9阀门的壳体试验试验压力不得小于公称压力的1.5倍,试验时间不得少于5min,以壳体填料无渗漏为合格。
密封试验宜以公称压力进行,以阀瓣密封面无渗漏为合格。
安全阀应按设计文件规定的开启压力进行调试。
调压时压力应稳定,每个安全阀启闭试验不得少于3次。
试验后的阀门应及时填写试验记录。
4.2.10阀门检查见下表:
序号
名称
规格型号
壳体试验
压力MPa
密封试验
压力MPa
1
内螺纹暗杆楔式阀门
Z15W-10DN50
1.5
1.1
2
截止阀
JD42Y-16KDN200
2.4
1.8
3
截止阀
JD42Y-16KDN50
2.4
1.8
4
截止阀
JD42Y-100KDN100
15
11
5
截止阀
JD42Y-100KDN50
15
11
6
截止阀
JD42Y-100KDN80
15
11
7
气动截止阀
JD642Y-100KDN50
15
11
8
气动截止阀
JD642Y-100KDN65
15
11
9
截止阀
JD42Y-40KDN125
6
4.4
10
截止阀
JD42Y-40KDN50
6
4.4
11
气动截止阀
JD642Y-40KDN65
6
4.4
12
截止阀
JD42Y-16KDN150
2.4
1.8
13
气动截止阀
JD642Y-16KDN125
2.4
1.8
14
气动截止阀
JD642Y-40KDN80
6
4.4
15
气动截止阀
JD642Y-16KDN100
2.4
1.8
16
气动截止阀
JD642Y-100KDN40
15
11
17
气动截止阀
JD642Y-16KDN150
2.4
1.8
18
电动Y型截止阀
JY941-160DN200
24
18
19
电动角式调节阀
T944Y-160DN200/300
24
18
20
电动角式调节阀
T944Y-64DN250/400
96
70
21
手动终端阀
AZ560GY-1500LbDN200
2.4
1.8
22
截止阀
JD42Y-16KDN100
2.4
1.8
23
截止阀
JD4Y5GY-16KDN250
2.4
1.8
24
截止阀
JD44Y-100KDN100
15
11
25
截止阀
JD42Y-40KDN100
6.0
4.4
26
截止阀
JD44Y-40KDN100
6.0
4.4
安全阀(按照设计要求进行初调和终调)
1
安全阀
PN10.0/2.5MpaDN125/200
2
安全阀
PN4.0/2.5MpaDN200/250
3
安全阀
PN16.0/1.0MpaDN125/200
4
安全阀
PN6.4/2.5MpaDN150/250
5
安全阀
PN2.5/1.0MpaDN200/300
6
安全阀
PN2.5/1.0MpaDN200/250
7
安全阀
PN2.5/1.0MpaDN200/300
试验合格的阀门应及时排尽内部积水,并吹干。
4.2.11焊接材料
4.2.11.1焊条、焊丝等均应有制造厂的质量合格证,机械性能试验报告和化学成分分析报告等。
4.2.11.2氩弧焊用的氩气纯度不低于99.95%,并保持干燥。
4.2.11.3焊条、焊丝与母材必须相匹配。
4.2.11.4焊条选用型号J506、J507,按规定在350℃烘干1h,进行保温,随用随取。
专业监理工程师随时抽查焊条烘干记录。
焊丝必须去除油污、氧化物。
4.3.管道加工
4.3.1合金钢管宜采用机械方法切割。
当采用氧乙炔火焰切割时,必须保证尺寸正确和表面平整,并清除加工表面的氧化层。
4.3.2熔盐管道12Cr1MoV钢管切断前应移值原有标记。
4.3.2管子切口质量应符合下列规定:
4.3.2.1切口表面应平整、无裂纹、重皮、毛刺、凹凸、缩口、熔渣、氧化物、铁屑等,否则应将切口表面的氧化层除去。
4.3.2.2坡口角度及形式必须符合设计文件要求。
4.3.2.3切口端面倾斜偏差不应大于等于外径的1%,且不得超过3㎜。
其中:
Ф114钢管切口端面倾斜偏差<1㎜;
≤Ф200钢管切口端面倾斜偏差<2㎜;
>Ф200钢管切口端面倾斜偏差<3㎜。
4.4.弯管制作:
4.4.1弯管宜采用壁厚为正公差的管子制作。
当采用负公差的管子制作弯管时,管子弯曲半径与弯管前管子壁厚的关系是R≥6DN,R=9DN,弯管前管子壁厚1.06Tm=1.06×9=9.54㎜。
4.4.2Ф114合金钢管进行热弯时,应进行完全退火,正火加回火或回火处理。
名义
成分
管材
牌号
热处理温度
(℃)
加热速度
恒温时间
冷却速率
C-Mn
16Mn
600~650
当加热温度升至400℃时,加热速度不应大于569.4C/h。
15min。
在恒温期间内最高与最低温差应低于65℃。
恒温厚的冷却速度,且不得大于260℃/h,400℃以下可自然冷却。
4.4.3弯管质量应符合下列规定:
4.4.3.1不得有裂纹;
4.4.3.2不得存在过烧、分层等缺陷;
4.4.3.3不宜有皱纹。
4.4.4测量弯管任一截面上的最大外径与最小外径差,不应大于5.7㎜。
4.4.5高压钢管制作弯管后,应进行表面无损探伤。
4.4.6高压钢管弯管加工合格后,及时填写高压管件加工记录。
4.5.管道焊接的一般要求
4.5.1焊接技术人员应负责编制焊接作业指导书和焊接技术措施,指导焊接作业,参与焊接质量管理,处理焊接技术问题,整理焊接技术资料。
4.5.2无损探伤人员应由国家授权的专业考核机构考核合格的人员担任,并应按考核合格项目及权限,从事焊接检测和审核工作,无损探伤人员应根据焊接质检人员确定的受检部位进行检验,评定焊缝质量,签发检验报告,对外观不符合检验要求的焊缝应拒绝检验。
4.5.3焊工应持证上岗。
焊工应按规定的焊接作业指导书及焊接技术措施施焊,当遇到施工条件与焊接作业指导书及焊接技术措施的要求不符合时,应拒绝施焊,并及时填写施焊记录。
4.5.4焊接热处理人员应按规范、焊接作业指导书及设计文件中的有关规定进行焊接热处理工作。
4.5.5焊接时的风速不应超过下列规定:
当超过规定时,应有防风设施。
①手工电弧焊:
8m/s;
②氩弧焊、二氧化碳气体保护焊:
2m/s。
4.5.616Mn和12Cr1MoV管材焊接时,焊接电弧1m范围内的相对湿度不得大于90%。
4.5.7当焊件表面潮湿,覆盖有冰雪或在下雨、下雪、刮风期间,焊工及焊件无保护措施时,不应进行焊接。
4.5.8对不合格焊缝的返修,返修前应进行质量分析,当同一部位的返修次数超过两次时,应制订返修措施并经焊接技术负责人审批后方可进行返修。
4.6.焊接准备
4.6.1焊接坡口应保持平整,不得有裂纹、分层、夹杂等缺陷,形式和尺寸应符合设计文件规定。
详见下页表:
项次
厚度T(㎜)
坡口
名称
坡口形式
坡口尺寸
间隙C(㎜)
钝边P(㎜)
坡口角度α(°)
1
9
V型
坡口
0~2
1.0+0.5
65~75±2.5
2
9~26
V型
坡口
0~3
0~3
55~65±2.5
4.6.2坡口表面及两侧(以离坡口边缘的距离计焊条电弧焊各10㎜,气体保护焊各20㎜)应将水、铁锈、油污、积渣和其它有害杂质清理干净。
4.6.3焊前预热
4.6.3.1当焊件温度低于0℃时,所有焊缝应在始焊处100㎜范围的预热到150℃以上。
4.6.3.2焊前预热温度数据应及时填写在施焊记录表上,由监理工程师随时检查。
4.7管道焊接
4.7.1管道焊接时准备工作必须做充分。
4.7.2管道对口时一定应做到内壁齐平,如有错口,其错口值不大于0.5㎜。
4.7.3管子或管件对接焊缝组对时,外壁的错边量,应符合下表:
序号
焊件厚度(㎜)
错边量(㎜)
1
δ=9
<0.5
2
δ=10
<1
3
δ=12
<1.2
4
δ=14
<1.4
5
δ=16
<1.6
6
δ=20
<2
4.7.4对不同厚度焊件对口时,内壁尺寸不相等而外壁齐平时,可加工内壁15㎜长,15℃,倒角一周,其加工厚度应于薄壁的相同。
4.7.5定位焊缝应符合下列规定:
4.7.5.1焊接定位焊缝时,应采用与根部焊道相同的焊接材料和焊接工艺,并应由合格焊工施焊。
4.7.5.2定位焊缝的长度、厚度和间距,应能保证焊缝在正式焊接过程中不致开裂。
4.7.5.3在焊接根部焊道前,应对定位焊缝进行检查,当发现缺陷时应处理后方可施焊。
4.7.5.4与母材焊接工卡具其材质宜与母材相同或同一类别号。
拆除工卡具时,不应损伤母材,拆除后应将残留焊疤打磨修整至与母材表面齐平。
4.7.6严禁在坡口之外的母材表面引弧和试验电流,并应防止电弧擦伤母材。
4.7.7氩弧焊打底焊接时,焊缝内侧应充氩气或其它保护气体,或采取其它防止内侧焊缝金属被氧化的措施。
4.7.8焊接时应采取合理的施焊方法和施焊顺序,及时做好施焊记录。
4.7.9施焊过程中应保证起弧和收弧处的质量。
收弧时应将弧坑填满,多层焊的层间接头应错开。
4.7.10管子焊接时,应将两端管口堵死,防止管内的穿堂风。
4.7.11每条焊缝在施焊时应一次连续焊完,当因故中断焊接时,应采取保温缓冷或后热等防止产生裂纹的措施,再次焊接前应检查焊层表面,确认无裂纹后,预热到150~200℃时继续施焊。
4.7.12在焊接过程中,应控制层间温度,层间温度应不低于规定的预热温度下限。
必要时,在施焊过程中用氧乙炔火焰加热。
4.7.13外观检查质量标准:
见下表
序号
缺陷名称
质量分级(Ⅱ)
1
裂纹
不允许
2
表面夹渣
不允许
3
表面气孔
不允许
4
咬边
不允许
5
未焊透
不允许
6
根部收缩
δ=9≤0.38㎜
δ=10≤0.4㎜
δ=12≤0.44㎜
δ=14≤0.48㎜
δ=16≤0.5㎜
δ=20≤0.5㎜
7
角焊缝厚度不足
不允许
4.7.14焊缝应在焊完后立即去除渣皮、飞溅物,清理干净焊缝表面,然后进行焊缝外观检查。
4.7.15焊口组对时应禁止用强力对口,更不允许利用热膨胀法对口,以防引起附加应力。
4.7.16焊接现场应有防风、防雨、防雪、防寒等措施。
4.8.后热
4.8.1对冷裂纹敏感性较大的低合金钢和拘束度较大的焊件应采取后热措施。
4.8.2后热应在焊后立即进行。
4.8.3后热温度一般为200~350℃,保温时间一般不低于0.5h。
4.8.4若焊后立即进行热处理则可不做后热。
4.9.焊后热处理
4.9.1焊后热处理的加热范围,每侧不应小于焊缝宽度3倍,加热带以外部分应进行保温。
每侧加热范围见下表:
序号
管径
焊缝宽度(㎜)
每侧加热范围(㎜)
1
Φ114
6
20
2
Φ377
15
45
3
Φ426
20
60
4
Φ530
25
75
5
Φ273
8
24
6
Φ325
15
45
7
Φ219
8
24
8
Φ159
6
20
4.9.2焊前预热及焊后热处理过程中焊件内外壁温度应均匀。
4.9.3焊前预热及焊后热处理时,应测量和记录其温度,测温点的部位和数量应合理,测温仪表应经计量检定合格,记录报监理公司审核。
4.9.4焊前预热及焊后热处理应符合设计或焊接作业指导书的规定。
4.9.516Mn材质钢管焊后热处理温度在600~650℃。
4.9.6焊后热处理的加热速度,热处理温度下的恒温时间及冷却速度应符合下列规定:
4.9.6.1当温度升至400℃以上时,加热速率不应大于(205×25/δ)℃/h,见下表:
序号
壁厚
加热速率
1
δ=9
<166.7℃/h
2
δ=10
<150℃/h
3
δ=12
<125℃/h
4
δ=14
<107℃/h
5
δ=16
<93.7℃/h
6
δ=20
<75℃/h
4.9.7热处理后应及时在热影响区和焊缝做硬度测试,此硬度不宜大于母材硬度的125%。
4.9.8热处理后进行返修或硬度检查,超过规定要求的焊缝应重新进行热处理。
4.10无损探伤
4.10.1溶出工段