模具制造实训.docx
《模具制造实训.docx》由会员分享,可在线阅读,更多相关《模具制造实训.docx(16页珍藏版)》请在冰豆网上搜索。
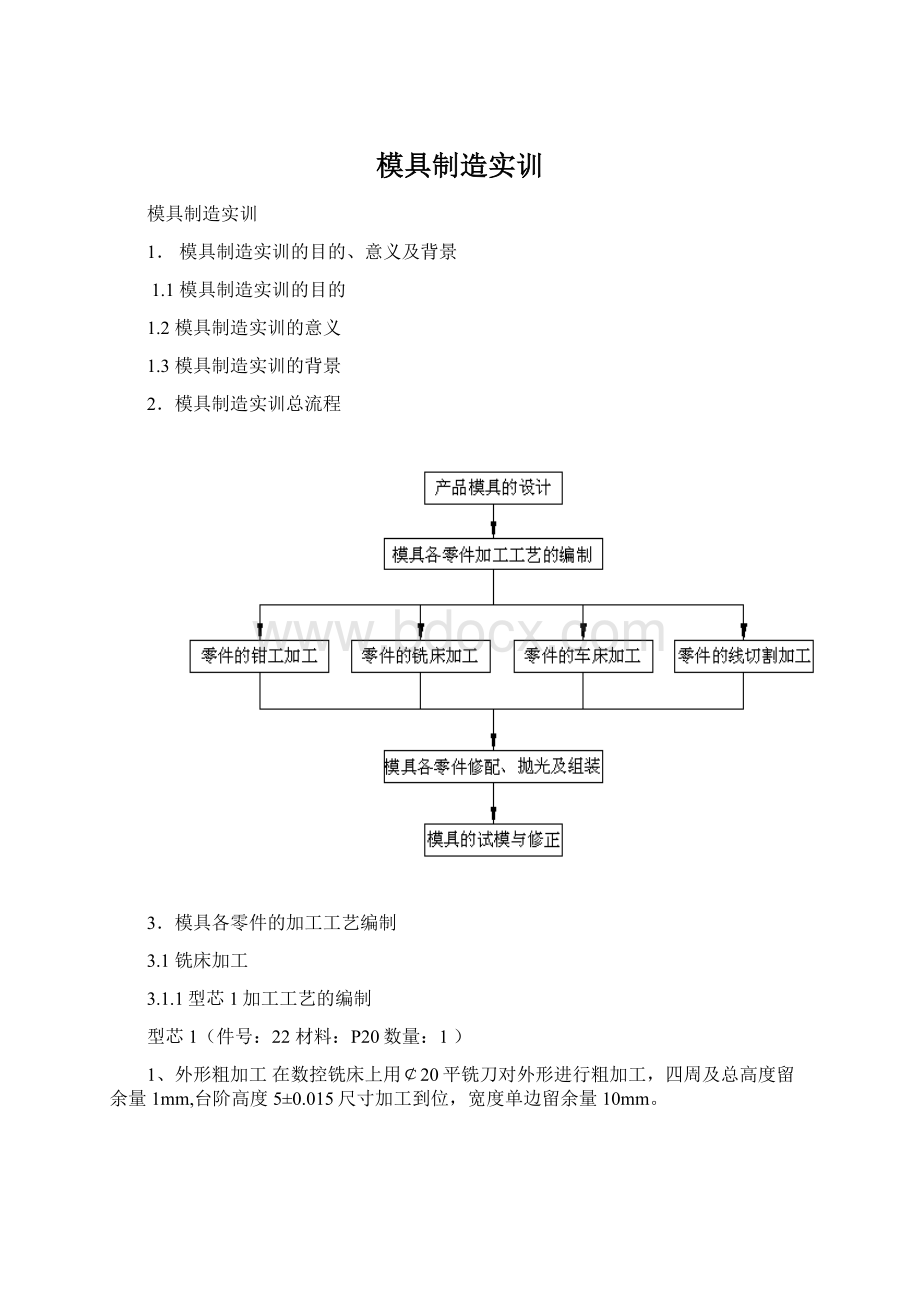
模具制造实训
模具制造实训
1.模具制造实训的目的、意义及背景
1.1模具制造实训的目的
1.2模具制造实训的意义
1.3模具制造实训的背景
2.模具制造实训总流程
3.模具各零件的加工工艺编制
3.1铣床加工
3.1.1型芯1加工工艺的编制
型芯1(件号:
22材料:
P20数量:
1)
1、外形粗加工在数控铣床上用¢20平铣刀对外形进行粗加工,四周及总高度留余量1mm,台阶高度5±0.015尺寸加工到位,宽度单边留余量10mm。
2、冷却水孔加工划线并用样冲定位,在台钻床上用¢8钻头进行钻孔加工,用压缩空气和钢针将冷却水孔内铁屑除净,用¢8×6的紫铜闷头按图示进行闷死,形成一进一出的冷却循环回路。
3、外形精加工在数控铣床上用¢10平铣刀对外形进行精加工,按给定尺寸的上偏差制作,最后将台阶宽度加工到72mm。
4、钳工镶配对型芯1—型芯固定板和推件板进行抛磨镶配,对成型部分进行抛磨。
3.1.2型腔1加工工艺的编制
型腔1(件号:
24材料:
P20数量:
1)
1、外形及成型腔粗加工在数控铣床上用¢20球形铣刀对外形及成型腔进行粗加工,四周及总高度留余量1mm。
用¢20平铣刀对外形台阶进行加工,高度5±0.015尺寸到位,宽度单边留余量10mm。
2、冷却水孔加工划线并用样冲定位,在台钻床上用¢6钻头进行钻孔加工,用压缩空气和钢针将冷却水孔内铁屑除净,用¢6×6的紫铜闷头按图示进行闷死,形成一进一出的冷却循环回路。
进、出口二端用¢11.6钻头扩孔,深度10mm,用G1/4″丝锥进行螺纹加工。
3、外形及成型腔精加工在数控铣床上用¢4球形铣刀对外形进行精加工,按给定尺寸的上偏差制作,将外形台阶宽度加工到128mm。
对成型腔用紫铜作电极对底面R2进行脉冲精加工。
4、钳工镶配对型腔—型腔孔进行抛磨镶配,对成型腔进行抛磨。
3.1.3型芯2加工工艺的编制
型芯2(件号:
21材料:
P20数量:
1)
1、外形粗加工在数控铣床上用¢20平铣刀对外形进行粗加工,四周及总高度留余量1mm,台阶高度5±0.015尺寸加工到位,宽度单边留余量10mm。
2、冷却水孔加工划线并用样冲定位,在台钻床上用¢8钻头进行钻孔加工,用压缩空气和钢针将冷却水孔内铁屑除净,用¢8×6的紫铜闷头按图示进行闷死,形成一进一出的冷却循环回路。
3、外形精加工在数控铣床上用¢10平铣刀对外形进行精加工,按给定尺寸的上偏差制作,最后将台阶宽度加工到72mm。
4、钳工镶配对型芯2—型芯固定板进行抛磨镶配,对成型部分进行抛磨。
3.1.4型腔2加工工艺的编制
型腔2(件号:
23材料:
P20数量:
1)
1、外形及成型腔粗加工在数控铣床上用¢20球形铣刀对外形及成型腔进行粗加工,四周及总高度留余量1mm。
用¢20平铣刀对外形台阶进行加工,高度5±0.015尺寸加工到位,宽度单边留余量10mm。
2、冷却水孔加工划线并用样冲定位,在台钻上用¢6钻头进行钻孔加工,用压缩空气和钢针将冷却水孔内铁屑除净,用¢6×6的紫铜闷头按图示进行闷死,形成一进一出的冷却循环回路。
进、出口二端用¢11.6钻头扩孔,深度10mm,用G1/4″丝锥进行螺纹加工。
3、外形及成型腔精加工在数控铣床上用¢4球形铣刀对外形进行精加工,按给定尺寸的上偏差制作,将外形台阶宽度加工到128mm。
对成型腔用紫铜作电极对底面R2进行脉冲精加工,用¢4平铣刀对成型腔台阶进行精加工,高度1.5mm尺寸到位.
4、钳工镶配对型腔—型腔孔进行抛磨镶配,对成型腔进行抛磨。
3.1.5推杆固定板加工工艺的编制
推杆固定板(件号:
13材料:
45数量:
1)
1、螺纹孔加工划线并用洋冲中心定位,在台钻床上用¢6.8钻头进行通孔加工,用M8丝锥进行螺纹孔加工。
2、支撑柱孔加工在横臂钻床上与件12—推板配作。
3.1.6定模座板加工工艺的编制
定模座板的加工(件号:
02材料:
45数量:
1)
1、浇口套孔加工在数控铣床上用¢20平铣刀对¢42进行通孔加工到所需尺寸。
2、定位圈孔加工在数控铣床上用¢20平铣刀对¢150孔进行加工,按给定尺寸的上偏差进行制作,深度为5mm。
3、螺纹孔加工在数控铣床上用中心钻进行定位并预钻1mm深度。
用¢5钻头进行孔加工,深度为12mm,用M6的丝锥进行螺纹孔加工,深度为8mm。
3.1.7动模座板加工工艺的编制
动模座板(件号:
08材料:
45数量:
1)
1、顶出孔加工在数控铣床上用¢20铣刀对¢70进行通孔加工,尺寸到位
2、支撑柱孔加工在数控铣床上用¢20铣刀对¢20孔进行通孔加工,用¢20铰刀对¢20孔进行铰孔。
3.1.8支撑板加工工艺的编制
支撑板(件号:
06材料:
45数量:
1)
1、冷却水管孔加工划线并用洋冲中心定位,在台钻床上用¢8钻头进行孔加工,深度15mm。
划线并用洋冲中心定位,在台钻床上用¢8钻头进行孔加工,深度75mm。
在台钻床上用¢11.6钻头扩孔,深度10mm,用G1/4″丝锥进行螺纹加工。
2、密封圈槽加工用中心钻坐标定位,在数控铣床上用¢3铣刀进行密封圈槽加工,深度2mm。
3.2车床加工
3.2.1支撑柱加工工艺的编制
支撑柱(件号:
11材料:
45数量:
2)
1、粗加工在数控车床上将坯料一端夹持在车床主轴上车削¢30,按给定尺寸的下偏差制作,长度大于105mm并进行端部倒角。
2、精加工在数控车床上将半坯料180°翻身装夹车削¢20,按给定尺寸的下偏差制作并控制长度¢30×90,用切断车刀将工件切至105mm并端部倒角。
3.2.2拉料杆加工工艺的编制
拉料杆(件号:
20材料:
45数量:
1)
1、粗加工将坯料一端夹持在数控车床主轴上车削¢8,尺寸到位。
2、精加工在数控车床上将半坯料180°翻身装夹在车床主轴上,另一端用尾架中心顶住车削¢4,按给定尺寸的下偏差制作并至长度大于50,然后换切断车刀对SR1.5×¢2尺寸进行加工并最后切断至长度45mm。
3.3线切割加工
3.3.1型腔固定板加工工艺的编制
型腔固定板(件号:
03材料:
45数量:
1)
1、型腔孔加工划线并用洋冲中心定位,在台钻上用¢10钻头进行穿孔加工。
在数控线切割机床上用线切割进行型腔孔加工,按给定尺寸的下偏差制作。
2、型腔孔台阶加工在数控铣床上用¢4平铣刀对型腔孔台阶进行加工,深度5mm。
3、冷却水管穿孔加工划线并用洋冲中心定位,在台钻床上用¢14钻头进行通孔加工。
4、浇口套孔加工划线并用洋冲中心定位,在台钻床上用¢11.9钻头进行通孔加工,用¢12铰刀进行铰孔。
5、钳工镶配对型腔孔—型腔进行抛磨镶配。
3.3.2型芯固定板加工工艺的编制
型芯固定板(件号:
05材料:
45数量:
1)
1、型芯孔加工划线并用洋冲中心定位,在台钻床上用¢10钻头进行穿孔加工。
在数控线切割机床上用线切割进行型芯孔加工,按给定尺寸的下偏差制作。
在数控铣床用¢4铣刀对型芯孔台阶进行加工,深度5±0.015mm。
2、拉料杆孔加工与件4—推件板配作定位后,用大于¢4.2钻头进行通孔加工,然后在台钻上用¢9平孔钻进行扩孔,深度3mm。
3、钳工镶配对型芯孔—型芯进行抛磨镶配。
3.3.3推板加工工艺的编制
推板(件号:
12材料:
45数量:
1)
1、螺钉孔加工划线并用洋冲中心定位,在台钻上用¢9钻头进行通孔加工,用¢14平孔钻进行沉孔加工,深度10mm。
2、支撑柱孔加工划线并用洋冲中心定位,在横臂钻床上用¢30钻头进行通孔加工(与件13—推杆固定板配作)。
3.3.4推件板加工工艺的编制
推件板(件号:
04材料:
45数量:
1)
1、型芯孔加工划线并用洋冲中心定位,在台钻床上用¢10钻头进行穿孔加工。
在数控线切割机床上用线切割进行型芯孔加工,按给定尺寸的下偏差制作。
在数控铣床上用¢4铣刀对型芯孔反面进行10°斜面加工,深度10mm。
2、浇注系统加工在数控铣床用R3球形刀对分浇道进行加工,用R1.5球形刀对浇口进行加工。
3、拉料杆孔加工用中心钻坐标法定位,在数控铣床用¢4铣刀进行通孔加工,然后用¢4铰刀进行铰孔(与件5—型芯固定板配作)。
4、钳工镶配对型芯孔—型芯进行抛磨镶配。
4.模具各零件的加工
4.1铣床加工
4.1.1型芯1的加工
加工工件名称:
型芯1
毛坯材料:
P20
毛坯尺寸:
46×76×82
辅助时间2小时:
装夹:
次数3、单次时间3~5min;装刀:
次数4,单次时间8~10min;对刀:
次数4,单次时间3~4min;传程序:
CF卡
加工时间12小时:
用时:
14小时,加工器械:
万能铣床X6325D、数控铣床GSVM6540L2,夹具:
台虎钳,刀具:
YT14,φ20平铣刀,φ16平铣刀,φ5键槽铣刀,φ4球头铣刀,量具:
游标卡尺。
加工工序:
型芯1
铣削毛坯两侧,使毛坯尺寸加工至42×72×82
4.1.1.1装夹工件在摇臂铣床上,注意基准方向,使用护口板保护工件单边,防止工件受损。
4.1.1.2对加工表面进行对刀。
对刀要求只需削去工件表面很少一层,能确定刀具与工件接触就可,使用刀具YT14,摇杆调整机床高度(每格为0.05mm,一次最多进给10格),速度档位:
左一。
4.1.1.3按照预计加工次数,在最后2次加工前使用游标卡尺,对工件进行尺寸测量以确保加工精度。
4.1.1.4工件换面加工,装夹时使用垫块。
4.1.1.5检查刀具情况,发现严重磨损或是崩刃时马上换刀,换刀时注意拧紧螺钉。
4.1.1.6对刀加工至图纸要求,完成后测量尺寸。
4.1.1.7重新装夹工件,使用护口板。
4.1.1.8铣削工件两侧凸台,松开机床前后控制开关调整至合理范围(约6mm~10mm),开机对刀,对刀要求同上。
4.1.1.9测量对刀后台阶的尺寸,按照实际测得尺寸调整机床前后位置,最终使台阶尺寸保持在5.5mm。
4.1.1.10固定机床前后位置开始进行Z方向加工,加工至图纸要求尺寸,完成后测量尺寸。
4.1.1.11重新装夹工件换面加工凸台,完成后测量尺寸。
铣削工件顶面,使工件至加工图纸要求
4.1.1.12装夹工件,对刀,输入原先预设的程序,使用φ20平头铣刀加工工件顶面,使其加工至81.3mm,机床回零,测量尺寸。
4.1.1.13换刀,重新对Z方向进行对刀,使用φ16平铣刀,加工出凸台,机床回零,测量尺寸。
4.1.1.14换刀,重新对Z方向进行对刀,使用φ5键槽铣刀进行精加工,机床回零,测量尺寸。
4.1.1.15换刀,重新对Z方向进行对刀,使用φ4球铣刀加工工件顶面圆角,机床回零,测量尺寸。
4.1.1.16使用垫块重新装夹工件,对刀,使用φ4球铣刀加工工件侧边圆角,机床回零,测量尺寸。
4.1.1.17使用垫块重新装夹工件,对刀,使用φ4球铣刀加工工件另侧边圆角,机床回零,测量尺寸。
4.1.1.18完成加工
4.1.2型腔1的加工
加工工件名称:
型腔1
毛坯材料:
P20
毛坯尺寸:
132×94×52
辅助时间2小时:
装夹:
次数3、单次时间3~5min;装刀:
次数4,单次时间8~10min;对刀:
次数4,单次时间3~4min;传程序:
CF卡
加工时间12小时:
用时:
14小时,加工器械:
万能铣床X6325D、数控铣床GSVM6540L2,夹具:
台虎钳,刀具:
YT14,φ20平铣刀,φ16平铣刀,φ4键槽铣刀,φ6球头铣刀,φ4球头铣刀,量具:
游标卡尺。
加工工序:
型腔2
铣削毛坯两侧,使毛坯尺寸加工至128×90×50
4.1.2.1装夹工件在摇臂铣床上,注意基准方向,使用护口板保护工件单边,防止工件受损。
4.1.2.2对加工表面进行对刀。
对刀要求只需削去工件表面很少一层,能确定刀具与工件接触就可,使用刀具YT14,摇杆调整机床高度(每格为0.05mm,一次最多进给10格),速度档位:
左一。
4.1.2.3按照预计加工次数,在最后2次加工前使用游标卡尺,对工件进行尺寸测量以确保加工精度。
4.1.2.4工件换面加工,装夹时使用垫块。
4.1.2.5检查刀具情况,发现严重磨损或是崩刃时马上换刀,换刀时注意拧紧螺钉。
4.1.2.6对刀加工至图纸要求,完成后测量尺寸。
4.1.2.7重新装夹工件,使用护口板。
4.1.2.8铣削工件两侧凸台,松开机床前后控制开关调整至合理范围(约6mm~10mm),开机对刀,对刀要求同上。
4.1.2.9测量对刀后台阶的尺寸,按照实际测得尺寸调整机床前后位置,最终使台阶尺寸保持在5.5mm。
4.1.2.10固定机床前后位置开始进行Z方向加工,加工至图纸要求尺寸,完成后测量尺寸。
4.1.2.11重新装夹工件换面加工型腔,完成后测量尺寸。
铣削工件型腔,使工件至加工图纸要求
4.1.2.12装夹工件,对刀,输入原先预设的程序,使用φ20平头铣刀加工型腔,使其加工至尺寸,留有余量,机床回零,测量尺寸。
4.1.2.13换刀,重新对Z方向进行对刀,使用φ6球铣刀,加工型腔,机床回零,测量尺寸。
4.1.2.14使用垫块重新装夹工件,对刀,使用φ4球铣刀加工工件侧边圆角,机床回零,测量尺寸。
4.1.2.15使用垫块重新装夹工件,对刀,使用φ4球铣刀加工工件另侧边圆角,机床回零,测量尺寸。
4.1.2.16用电极对型腔进行点火花加工,达到型腔尺寸。
4.1.2.17完成加工
4.1.3型芯2的加工
加工工件名称:
型芯2
毛坯材料:
P20
毛坯尺寸:
43×76×78
辅助时间2小时:
装夹:
次数2、单次时间3~5min;装刀:
次数4,单次时间8~10min;对刀:
次数4,单次时间3~4min;传程序:
CF卡
加工时间8小时:
用时:
10小时,加工器械:
万能铣床X6325D、数控铣床GSVM6540L2,夹具:
台虎钳,刀具:
YT14,φ20平铣刀,φ16平铣刀,φ4球头铣刀,量具:
游标卡尺。
加工工序:
型芯2
铣削毛坯两侧,使毛坯尺寸加工至39×72×76.5
4.1.3.1装夹工件在摇臂铣床上,注意基准方向,使用护口板保护工件单边,防止工件受损。
4.1.3.2对加工表面进行对刀。
对刀要求只需削去工件表面很少一层,能确定刀具与工件接触就可,使用刀具YT14,摇杆调整机床高度(每格为0.05mm,一次最多进给10格),速度档位:
左一。
4.1.3.3按照预计加工次数,在最后2次加工前使用游标卡尺,对工件进行尺寸测量以确保加工精度。
4.1.3.4工件换面加工,装夹时使用垫块。
4.1.3.5检查刀具情况,发现严重磨损或是崩刃时马上换刀,换刀时注意拧紧螺钉。
4.1.3.6对刀加工至图纸要求,完成后测量尺寸。
4.1.3.7重新装夹工件,使用护口板。
4.1.3.8铣削工件两侧凸台,松开机床前后控制开关调整至合理范围(约6mm~10mm),开机对刀,对刀要求同上。
4.1.3.9测量对刀后台阶的尺寸,按照实际测得尺寸调整机床前后位置,最终使台阶尺寸保持在5.5mm。
4.1.3.10固定机床前后位置开始进行Z方向加工,加工至图纸要求尺寸,完成后测量尺寸。
4.1.3.11重新装夹工件换面加工顶面,完成后测量尺寸。
铣削工件顶面,使工件至加工图纸要求
4.1.3.12装夹工件,对刀,输入原先预设的程序,使用φ20平头铣刀加工工件顶面,使其加工至76.5mm,机床回零,测量尺寸。
4.1.3.13换刀,重新对Z方向进行对刀,使用φ4球铣刀加工工件顶面圆角,机床回零,测量尺寸。
4.1.3.14使用垫块重新装夹工件,对刀,使用φ4球铣刀加工工件侧边圆角,机床回零,测量尺寸。
4.1.3.15使用垫块重新装夹工件,对刀,使用φ4球铣刀加工工件另侧边圆角,机床回零,测量尺寸。
4.1.3.16完成加工
4.1.4型腔2的加工
加工工件名称:
型腔2
毛坯材料:
P20
毛坯尺寸:
132×94×52
辅助时间2小时:
装夹:
次数3、单次时间3~5min;装刀:
次数4,单次时间8~10min;对刀:
次数4,单次时间3~4min;传程序:
CF卡
加工时间14小时:
用时:
16小时,加工器械:
万能铣床X6325D、数控铣床GSVM6540L2,夹具:
台虎钳,刀具:
YT14,φ20平铣刀,φ16平铣刀,φ4键槽铣刀,φ6球头铣刀,φ4球头铣刀,量具:
游标卡尺。
加工工序:
型腔2
铣削毛坯两侧,使毛坯尺寸加工至128×90×50
4.1.4.1装夹工件在摇臂铣床上,注意基准方向,使用护口板保护工件单边,防止工件受损。
4.1.4.2对加工表面进行对刀。
对刀要求只需削去工件表面很少一层,能确定刀具与工件接触就可,使用刀具YT14,摇杆调整机床高度(每格为0.05mm,一次最多进给10格),速度档位:
左一。
4.1.4.3按照预计加工次数,在最后2次加工前使用游标卡尺,对工件进行尺寸测量以确保加工精度。
4.1.4.4工件换面加工,装夹时使用垫块。
4.1.4.5检查刀具情况,发现严重磨损或是崩刃时马上换刀,换刀时注意拧紧螺钉。
4.1.4.6对刀加工至图纸要求,完成后测量尺寸。
4.1.4.7重新装夹工件,使用护口板。
4.1.4.8铣削工件两侧凸台,松开机床前后控制开关调整至合理范围(约6mm~10mm),开机对刀,对刀要求同上。
4.1.4.9测量对刀后台阶的尺寸,按照实际测得尺寸调整机床前后位置,最终使台阶尺寸保持在5.5mm。
4.1.4.10固定机床前后位置开始进行Z方向加工,加工至图纸要求尺寸,完成后测量尺寸。
4.1.4.11重新装夹工件换面加工型腔,完成后测量尺寸。
铣削工件型腔,使工件至加工图纸要求
4.1.4.12装夹工件,对刀,输入原先预设的程序,使用φ20平头铣刀加工型腔,使其加工至尺寸,留有余量,机床回零,测量尺寸。
4.1.4.13换刀,重新对Z方向进行对刀,使用φ6球铣刀,加工型腔,机床回零,测量尺寸。
4.1.4.14换刀,重新对Z方向进行对刀,使用φ4键槽铣刀进行台阶精加工,机床回零,测量尺寸。
4.1.4.15使用垫块重新装夹工件,对刀,使用φ4球铣刀加工工件侧边圆角,机床回零,测量尺寸。
4.1.4.16使用垫块重新装夹工件,对刀,使用φ4球铣刀加工工件另侧边圆角,机床回零,测量尺寸。
4.1.4.17用电极对型腔进行点火花加工,达到型腔尺寸。
4.1.4.18完成加工
4.1.5支撑板的加工
加工工件名称:
支撑板
毛坯材料:
#45
毛坯尺寸:
300×200×30
辅助时间0.5小时:
装夹:
次数1、单次时间3~5min;装刀:
次数1,单次时间8~10min;对刀:
次数1,单次时间3~4min;传程序:
CF卡
加工时间5小时:
用时:
5.5小时,加工器械:
数控铣床GSVM6540L2,夹具:
台虎钳,刀具:
φ3键槽铣刀,量具:
游标卡尺。
加工工序:
钻孔
4.1.5.1划线,定位孔中心
4.1.5.2样冲打中心点
4.1.5.3上钻床夹紧
4.1.5.4安装刀具,钻刀Φ8mm深孔钻
4.1.5.5开启机床检查刀具是否装正
4.1.5.6对中心
4.1.5.7开始钻孔(注意事项:
钻头下到一定程度,要及时抬刀,以免铁屑不能及时排出,钻头卡死。
)
4.1.5.8换钻头,钻刀Φ10mm
4.1.5.9开启机床检查刀具是否装正
4.1.5.10对中心
4.1.5.11开始扩孔
4.1.5.12攻螺纹
铣密封环槽
4.1.5.14换刀,Φ3mm平头铣刀
4.1.5.15装夹工件(注意事项:
不能压紧工件)
4.1.5.16打表(注意事项:
公差在2丝内即可)
4.1.5.17压紧
4.1.5.18对刀
4.1.5.19载入程序
4.1.5.20开始加工,进给速度10,给进量0.2
4.1.6定模座板的加工
加工工件名称:
定模座板
毛坯材料:
#45
毛坯尺寸:
300×200×25
辅助时间0.5小时:
装夹:
次数1、单次时间3~5min;装刀:
次数1,单次时间8~10min;对刀:
次数1,单次时间3~4min;传程序:
CF卡
加工时间3.5小时:
用时:
4小时,加工器械:
数控铣床GSVM6540L2,夹具:
台虎钳,刀具:
φ20平铣刀,量具:
游标卡尺。
加工工序:
钻孔
4.1.6.1划线,定位孔中心
4.1.6.2样冲打中心点
4.1.6.3上钻床夹紧
4.1.6.4安装刀具,钻刀Φ8mm深孔钻
4.1.6.5开启机床检查刀具是否装正
4.1.6.6对中心
4.1.6.7开始钻孔(注意事项:
钻头下到一定程度,要及时抬刀,以免铁屑不能及时排出,钻头卡死。
)
铣定位圈
4.1.6.8换刀,Φ20mm平头铣刀
4.1.6.9装夹工件(注意事项:
不能压紧工件)
4.1.6.10打表(注意事项:
公差在2丝内即可)
4.1.6.11压紧
4.1.6.12对刀
4.1.6.13载入程序
4.1.6.14开始加工,进给速度10,给进量1mm
线切割加工
4.1.6.15放置工件
打表将型腔固定板放正。
注意事项:
1打表前把板固定住,用橡胶榔头修正板。
不要夹得太松。
4.1.6.16穿丝
注意事项:
钼丝要保证穿在导轮上。
4.1.6.17调节丝的垂直,开始运丝,把丝接触工件,看是否上下都有火花。
4.1.6.18对中心。
自动对中心,对完后观察是否和划的线一致(穿丝孔没有打在划线的中心),不一致手动调节。
4.1.6.19载入程序
4.1.6.20开始加工
当切到一半左右时用吸铁石吸住切下的部分,要保证工件切完后仍吸在工件上,不能但是吸铁石不能离丝太近,磁性会影响丝的动作。
4.1.6.21加工完成
4.1.5推杆固定板的加工
4.2车床加工
4.2.1支撑柱的加工
4.2.2拉料杆的加工
4.3线切割加工
4.3.1定模座板的加工
4.3.2型腔固定板的加工
4.3.3推件板的加工
4.3.4型芯固定板的加工
4.3.5动模座板的加工
4.3.6推板的加工
4.3.7推件板的加工
5.模具各零件的修配、抛光与组装
5.1模具各零件的修配
5.1.1型芯1与型芯固定板的修配
5.1.2型芯2与型芯固定板的修配
5.1.3型腔1与型腔固定板的修配
5.1.4型腔2与型腔固定板的修配
5.2模具零件的抛光
5.2.1型芯1的抛光
5.2.2型芯2的抛光
5.2.3型腔1的抛光
5.2.4型腔2的抛光
5.3模具的组装
5.3.1XXXXXXXXX
5.3.2XXXXXXXXX
5.3.3XXXXXXXXX
5.3.4XXXXXXXXX
6.模具的试模与修正
6.1模具的吊装
6.2模具的试模
6.2.1注射压力
6.2.2保压时间
6.2.3冷却时间
6.2.4XXXXXXX
6.2.5XXXXXXX
6.3模具的修正
6.3.1XXXXXXXXX
6.3.2XXXXXXXXX
6.3.3XXXXXXXXX