乌克兰G0R精炼转炉技术综述.docx
《乌克兰G0R精炼转炉技术综述.docx》由会员分享,可在线阅读,更多相关《乌克兰G0R精炼转炉技术综述.docx(14页珍藏版)》请在冰豆网上搜索。
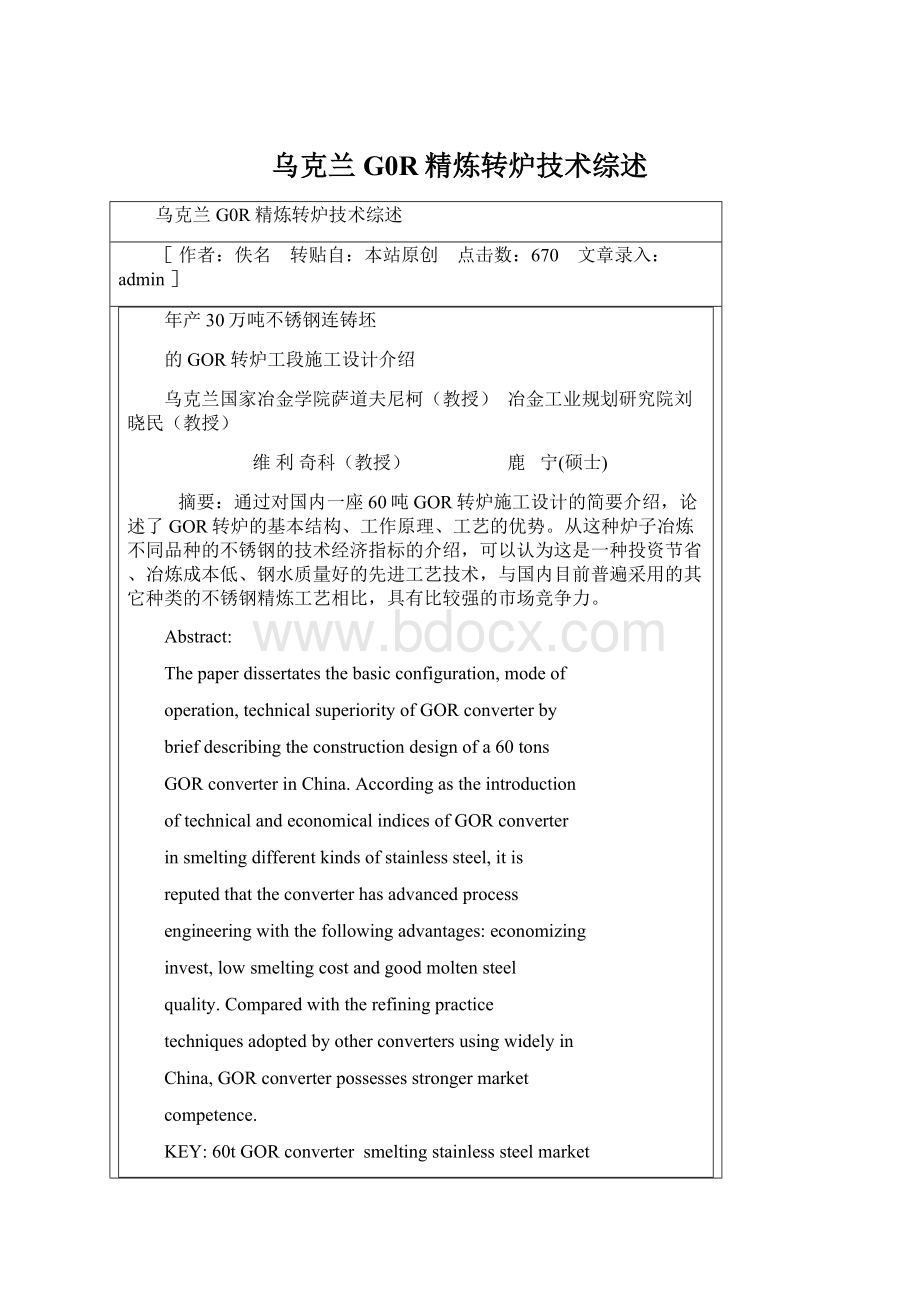
乌克兰G0R精炼转炉技术综述
乌克兰G0R精炼转炉技术综述
[作者:
佚名 转贴自:
本站原创 点击数:
670 文章录入:
admin]
年产30万吨不锈钢连铸坯
的GOR转炉工段施工设计介绍
乌克兰国家冶金学院萨道夫尼柯(教授) 冶金工业规划研究院刘晓民(教授)
维利奇科(教授) 鹿 宁(硕士)
摘要:
通过对国内一座60吨GOR转炉施工设计的简要介绍,论述了GOR转炉的基本结构、工作原理、工艺的优势。
从这种炉子冶炼不同品种的不锈钢的技术经济指标的介绍,可以认为这是一种投资节省、冶炼成本低、钢水质量好的先进工艺技术,与国内目前普遍采用的其它种类的不锈钢精炼工艺相比,具有比较强的市场竞争力。
Abstract:
Thepaperdissertatesthebasicconfiguration,modeof
operation,technicalsuperiorityofGORconverterby
briefdescribingtheconstructiondesignofa60tons
GORconverterinChina.Accordingastheintroduction
oftechnicalandeconomicalindicesofGORconverter
insmeltingdifferentkindsofstainlesssteel,itis
reputedthattheconverterhasadvancedprocess
engineeringwiththefollowingadvantages:
economizing
invest,lowsmeltingcostandgoodmoltensteel
quality.Comparedwiththerefiningpractice
techniquesadoptedbyotherconvertersusingwidelyin
China,GORconverterpossessesstrongermarket
competence.
KEY:
60tGORconverter smeltingstainlesssteelmarket
competence.
国内一家不锈钢公司经过考察和对比,确定建设一座60吨GOR转炉作为30万吨/年不锈钢炼钢车间的精炼炉。
这个车间采用一座60吨电炉---一座60吨GOR转炉二步法冶炼ASTMA276-92标准规定的201(1Cr17Mn6Ni5N)、304(0Cr18Ni9)等不锈钢钢种,钢水经一套国产的板坯连铸机浇铸成板坯。
该公司委托冶金工业规划研究院和乌克兰钛设计院承担精炼工段的设计、试车指导、生产20炉合格的不锈钢(成份和温度合格率达到100%)任务。
GOR精炼转炉技术是前苏联的第聂伯尔冶金学院和钢铁研究院合作开发的一种不锈钢冶炼工艺,在前苏联境内建设有1吨、5吨、10吨和60吨的GOR转炉不锈钢冶炼车间,目前乌克兰全国的不锈钢钢材都是利用这种炉子生产的钢坯轧制的。
这种工艺是前苏联的专利技术,乌克兰独立后,被批准为乌克兰的专利技术。
这次设计参考了扎波罗什特钢厂60吨GOR转炉15年的生产经验。
但是中国冶炼不锈钢的原材料构成与乌克兰有很大差异,并且计算机技术的发展使这种工艺更容易实现冶炼过程的自动化控制,设计中进行了多项改进。
GOR转炉是多种能源介质复合吹炼的底吹转炉,其供气管路可以向熔池吹入可调成份的氧气、氮气、氩气、天然气(或其它炭氢化合物)的混合气体。
这种工艺具有如下一些优点:
―――冶炼周期为40-60分钟,高的生产率使这种工艺能做到以一当二,从而可以降低投资。
―――工艺过程具有高的灵活性:
可以用废钢和高炭铁合金、也可以用100%的不锈废钢(不另加合金)来冶炼不锈钢。
―――根据成品钢中炭含量要求不同,氩气消耗6-13.5立方米/吨。
―――这种工艺不但可以冶炼任何一种国际标准的不锈钢,还适用冶炼高级合金钢、低合金钢和炭素钢。
―――GOR转炉可以很容易的实现合理的温度制度和造渣制度,包括5吨的小转炉也没有发生热量不足的困难。
―――特殊的出钢口设置可以准确的控制炉渣进入钢包的数量,有利于钛等容易氧化的合金元素的合金化,也有利于对成品钢水进行调质。
――在通过吹入氮气准确的控制含氮钢中的氮含量(达到溶解度及以下),精确度为±0.01%(质量)。
――炉令高,降低了耐火材料消耗。
――在最低氧化性条件下实现深度脱气,降低铅、锡等有色金属含量。
――容易实现工艺过程再现,方便的实现工艺过程自动控制。
1.施工设计的主要内容:
GOR转炉不锈钢生产工段,包括GOR转炉、散料上料系统、能源介质供应系统、工艺过程自控系统及主要工艺设备(钢包渣包车、倒转钢包、浇铸钢包、千斤顶小车、伸缩提升小车)。
2.主要技术决定
2.1生产钢种、原材料消耗
不锈钢(钢水)年产量30万吨。
冶炼钢种:
钢号
C%
Si%
Mn%
P%
S%
Ni%
Cr%
N2%
Cu%
304
0.03~0.08
0.30~0.70
1.6~2.0
≤0.045
≤0.030
8.0~8.8
17.0~18.0
0.01~0.03
205
0.08~0.11
0.2~0.5
17.0~18.0
≤0.045
≤0.030
1.5~2.0
17.0~18.0
0.32~0.45
2.5~2.8
201
0.08~0.12
≤0.75
6.5~7.5
≤0.045
≤0.030
4.0~4.5
16.5~17.5
0.2~0.25
J4
0.08~0.12
0.2~0.5
11.0~12.0
≤0.045
≤0.030
0.8~1.2
13.0~14.0
0.3~0.45
2.5~2.8
供应初炼钢水(在50t电弧炉中熔化的高合金融熔金属),由国内的设计院完成。
对初炼钢水的要求:
——化学成份:
[P] <0.03%;
[C] 不限制(实际为2.2%);
[Si]、[Mn] 、[Cr]、[Ni]按不同钢种在操作规程中给出。
[S] 0.045%以下。
——温度无特殊要求,但要保证全部初炼钢水都能兑入转炉。
——在倒转钢包中应保证电炉炉渣量为最小。
初炼钢水在称重、取样测定化学成份及测温后,进入GOR转炉工段。
GOR转炉方法采用的能源介质:
氧 气 压力1.0~1.2MPa,耗量(最大)7500m3/h
氩 气 压力1.0~1.2MPa,耗量(最大)3600m3/h
氮 气 压力1.0~1.2MPa,耗量(最大)3600m3/h
天然气 压力0.5~0.6MPa,耗量(最大)1000m3/h
冶炼周期(从兑初炼钢水到兑初炼钢水)最长不超过60分钟。
主要原材料及能源介质的综合单耗(含电炉冶炼)因钢种不同而有差异:
表2.1-1
名 称
单位
304
205
201
J4
原 材 料
1.炭素废钢
kg
646.0
522.0
642.0
687.0
2.高炭铬铁(炭8%)
kg
297.0
297.0
289.0
229.0
3.金属镍
kg
85.0
18.0
43.0
10.0
4.金属锰
kg
16.0
196.0
77.0
130.0
5.硅铁ØC-75
kg
13-25.0
13-25.0
13-25.0
13-25.0
6.金属铝
kg
1.0
1.0
1.0
1.0
7.金属铜
kg
—
26.0
—
26.0
金属料合计
kg
1070.0
1085.0
1077.0
1108.0
能 源
1.氧气(初始炭不同)
m3
30-50
30-50
15~30
25-45
2.氩气
m3
当[C]=0.06~0.12%
m3
6~8
—
2~3
—
当[C]≤0.03%
m3
10.0~13.5
3.氮气
m3
—
9~10
8~9
5~7
4.天然气
m3
4~6
4~6
2~4
3~5
精炼过程中从转炉逸出的含尘烟气的成份、温度及尘粒的粒度构成在初步设计中已经给出,烟气需要经除尘后排放。
精炼过程形成的炉渣量为70~100kg/t钢,化学成份也已经在初步设计中给出。
2.2配置方面的决定
GOR转炉工段的有关设备全部布置在主厂房内36×54米的区域内,转炉有独立的基础,转炉倾动轴线标高+8.600m,转炉的主要工作平台标高+7.500m,转炉四周有密封挡板。
高位料仓带有溜槽用于将料装入转炉,其标高为+14.800m。
用大倾角皮带机将料运至高位料仓。
在主工作平台下面,布置能源介质供应系统。
千斤顶小车用于更换炉底。
伸缩提升机用于修炉。
在炉前布置工艺过程控制室(包括主控台室、PLC室、检测仪表室、电气室、MCC—电机控制中心室)。
2.3工艺过程的描述
GOR转炉精炼设备—工艺流程图附于本文的后面。
冶炼工艺过程均为自动化,由主操纵台进行控制。
设有现场操纵台,但只有主操纵台发出允许指令后才能进行操纵。
工艺过程的组织如下:
不锈钢的冶炼,是通过电弧炉—GOR转炉双联法来实现的。
50t电弧炉只用于熔化初炼钢水并加温到必要的温度。
使用容量为60t的倒转钢包转运,在钢包内取样、称重、测温,然后,用吊车转运至GOR转炉工段。
测温结果、初炼钢水重量以及快速化学分析的成份均传至GOR转炉主操纵台。
GOR转炉通过安装在转炉底部的三个套管式喷嘴向转炉内吹入某种气体或是多种气体的混合气体。
用于底吹的气体有氧气、氩气、氮气、天然气(或其它炭氢化合物)。
向转炉底部供气通过转炉的空心耳轴来实现,分别由喷嘴的中心管及环缝管向炉内喷入不同种类的气体或者不同比例的混合气体。
通过计算机控制供应能源介质的阀门组,使向GOR转炉供气实现自动化。
在主操纵台将初炼钢水温度、质量及其化学成份等信息输入到工艺过程自控系统的数据库中,计算机自动计算精炼过程参数。
用桥式吊车将初炼钢水兑入GOR转炉。
在兑入初炼钢水之前,向GOR转炉加入必要数量的石灰及冷料(铁合金、废钢等)。
向GOR转炉加入的散料(造渣剂、还原剂、合金料)存放在散料上料系统的料仓之中。
将散料装入料仓通过吊车及活底料斗来实现。
为了检测高架料仓中物料的料位,在料仓中装有雷达料位仪。
从这个系统加入炉内的原料种类和数量输入到工艺过程自控系统,参与精炼过程参数的的进一步计算。
精炼过程分三个阶段进行:
第一阶段吹氧,由天然气保护;第二阶段吹入氧、氩混合气体;第三阶段向转炉熔池吹入纯氩。
根据钢种不同,选定特定的自动化程序自动控制冶炼过程。
在第一阶段结束时和在出钢之前取样送化验室分析。
化验分析的结果和钢水温度的信息进入工艺过程自控系统的PLC,必要时对计算程序进行修正。
在GOR转炉精炼过程中,要加入脱氧剂及合金化材料,这一作业也是通过“散料供应系统”来实现的,散料供应系统可以实现在冶炼过程中连续的向炉内加料。
GOR转炉工艺过程的控制(供气制度、散料上料等)由主操纵台来实现,是全部自动化的。
在精炼结束时,确认快速化学分析的结果与目标钢种的成份相符、温度合格后,将钢水出到浇铸钢包内。
出钢作业完成后进行出渣作业。
为了加速修炉工作,将炉底和炉帽做成可更换的形式。
为了实现修炉工作机械化,设计了专用设备:
千斤顶小车和伸缩提升机。
根据不同冶炼钢种,制定详细的工艺操作规程,还制定了安全生产技术要求,这些都必须认真执行。
3.检测仪表及自动化
3.1工艺过程自控系统的任务及目的
工艺过程自控系统用于对GOR转炉生产不锈钢的冶炼过程进行自动控制。
建立本系统的目的是:
——通过自动控制吹炼,保证所生产的钢符合设定目标,保证工艺过程的再现性;
——能源介质的单耗及合金料单耗最经济;
——保证工艺人员及时得到冶炼过程的实时信息以及主要设备状态的信息;
——建立熔炼记录的数据库以备长期保存和分析工艺信息。
工艺过程自控系统的设计,考虑了投产后可以根据市场需要方便的增加其它钢种冶炼控制程序。
3.2主要技术决定
3.2.1自动化功能
选择了GOR转炉工艺过程自控系统的两级功能结构。
下一级(控制器及检测仪表系统),按照操作人员提出的任务控制冶炼过程,检测工艺参数和设备工作状态,将信息传送到上一级。
上一级(操作站)对下一级传送来的信息进行加工,并以表格或模拟图等形式反映在显示屏上,形成工艺参数状态及偏差的通千,发出调整工艺过程的建议,将信息转达到下一级,打印报告文件,或建设磁盘文件。
GOR转炉工艺自控系统包括:
(1)“吹炼”分系统—-检测和控制吹炼制度;
(2)“合金化”分系统—-检测和控制造渣及合金化;
(3)“设备检测”分系统—-检测工艺设备及自控设备的工作状态;
(4)“接口”分系统――组织人—机接口;
(5)“文件”分系统—-组织熔炼记录及信息存档。
“吹炼”分系统的任务:
——检测能源介质参数及供气管路状况;
——根据冶炼钢种、初炼钢水及金属料的总重量,以及融熔金属的状态,按炉进行吹炼程序计算;
——根据所做的计算及倒炉时取样分析的结果,对吹炼融熔金属进行自动控制。
“合金化”分系统的任务:
——检测散料及合金称量和上料路径上的机械状态;检测供给转炉或供至钢包的材料种类及数量;
——计算每炉的造渣料、脱氧剂和合金化材料所需数量;
——自动控制向转炉或向浇铸钢包供应造渣料、还原和合金化材料的称量及加料作业。
“设备检测”分系统的任务:
——检测电气设备的状态是否完好;
——检测自动化设备的完好性(控制器,系统内部通讯);
——工艺参数在显示屏以模拟图的方式显示,操作人员输入指令,对指令进行加工;
——生成工艺过程及事故方面的报告。
“文件”分系统的任务:
——生成生产过程的熔炼记录;
——生成并服务于熔炼记录的存档。
系统内部信息通讯联系通过局部网来实现。
或以传递速度能保证GOR转炉工艺自控系统功能的、顺序多个接口为基础。
3.2.2数学保证
GOR转炉工艺自控系统的数学保证以下列原则为基础:
——广泛采用对所用信息进行防干扰的数学方法,如过滤、平滑、可信度分析、误差及逻辑检验等等;
——采用统一的检测与控制的算法;
——在控制的算法中采用能对工艺过程中变化着的条件适应的适配模型方法。
3.2.3信息保证
GOR转炉工艺自控系统的信息保证包括有:
——安装在控制的工艺对象上的传感器发出的输入信号、来自操纵台控制板手及按钮的输入信号、进入可编程序逻辑控制器输入组件的信号;
——从操纵人员来的控制指令及数据,作为输入信号;
——从可编程序逻辑控制器输出组件来的,向执行机构发出的输出信号;
——输出文件。
3.2.4软件保证
GOR转炉工艺自控系统的软件包括系统(基础)软件和应用软件。
可编程序控制器的系统软件保证,包括:
控制器操作系统,系统功能及功能模块的存储,采用STEP7系统作为可编程序控制器的编程系统。
工作站的软件系统包括Windows2000的操作系统及SCADA-WINCC系统。
在编制设计文件过程中,建立应用软件。
为了更好的培训中国的专家,应用软件的编制在工厂进行。
3.2.5技术保证
在上一级工艺自控系统考虑两个工作站,一个工程师站。
他们之间相互联系,同时用局部网与可编程序控制器PLC联系(采用GndustrialEthernet)。
转炉操纵台上备有两台18英寸的LCD显示器。
在下一级工艺自控系统有两个SIMATICS7-400的可编程序逻辑控制器,“吹炼”分系统及“合金化”分系统实现从自控系统装置及传感器收集信息、数据,并进行初步加工,以及对设备控制。
PLC可编程序控制器“吹炼“分系统与操作屏的联系,以及与转炉状态传感器之间的联系是以PROFIBUS-DP网为基础来实现的。
测量氧、氩、氮气及天然气的温度采用铂电阻温度计,美国RosemountInc公司产品。
测量压力及流量采用美国RosemountInc公司的传感器。
实现GOR转炉精炼过程自动控制的必要条件之一,就是要能在很大的范围内、精确的测量和调节吹炼气体的流量。
要求保证流量变化范围为1:
10,精度为0.5%。
为了保证随机对流量进行温度和压力影响值的调整,采用绝对大气压的传感器测量气体压力。
为了保证调整的高精确度,采用美国FISHE公司的调节阀。
考虑正常生产状态和事故状态的要求,确定阀门的常开或常闭。
在主操纵台设有能源介质的事故控制器,通过这个控制器,可以将所有截断阀的控制转换为远程控制制度,并可在此通过操作控制台上的旋转开关改变截止阀的状态。
此外,还可以通过手控连锁和手动开关,控制向底吹喷咀中心管和边缘环缝的供氩流量。
4.能源供应
4.1对能源介质的要求
用GOR法生产不锈钢时,通过一套自动控制程序精确控制能源介质供应,它是基于调整及检测氧、氩、氮、天然气耗量来实现的。
控制能源供应的阀门站装备有流量计、截止阀、调节阀。
此外还需要干燥的压缩空气,Q=60m3/h,P=0.4~0.6MPa,用于控制能源介质传送系统调节阀和切断阀。
控制散料上料系统料仓气动闸阀的压缩空气,Q=2.0m3/h。
氧气
对氧气的物理化学指标要求为:
——体积纯度不低于99.5%;
在T=20℃,P=101.3kPa,水蒸汽的(质量)浓度不大于0.07g/m3。
供气系统保证按工艺过程需要,可在很大的范围内对氧气消耗量进行检测和调控,系统设有测量用的流量孔板,截断阀及调节阀。
氩气
纯净气态氩应具有下列物理化学指标:
——体积纯度不低于99.96%;
——氧气含量不大于0.005%;
——氮气含量不大于0.04%;
——CO、CO2、CnHm的含量不大于0.005%;
——T=+20℃,P=101.3kPa时,水蒸汽的(质量)浓度不大于0.03g/m3。
氮气
气态氮应具有下列物理化学指标:
——体积纯度不低于99.6%;
——氧气含量不大于0.4%;
——T=+20℃,P=101.3kPa时,水蒸汽(质量)浓度不大于0.07g/m3。
天然气
天然气在吹氧脱碳阶段,作为一种保护气体。
采用的天然气热值Q=7900~8000kcal/m3(≈34MJ/m3)。
压缩空气
企业的空压站应带有空气干燥装置。
干燥的压缩空气用于检测仪表的控制系统以及调节阀门。
4.2对能源介质供应系统的要求
控制能源介质供应的阀门站布置在车间内,用网格栏栅进行空间范围的完全隔离。
能源介质传感器的房间布置在阀门站旁。
对GOR转炉能源介质管线的要求如下:
—--在供气管线上装设有测量用的流量孔板,截止阀和调节阀。
——所有管路中均考虑切断阀。
——每种能源介质的管道均设有逆止阀。
——在供气联管通向GOR转炉时,设置火焰阻断管。
——在向转炉供氮气、氩气、天然气的管道上,设置带有切断阀和放散阀的吹扫管。
5.结语:
年产30万吨不锈钢的工程正在紧张的进行土建施工,主要工艺设备已经制造完成,很快将进入设备安装,预计2006年初投产。
采用这样一种多种气体复合吹炼的底吹转炉作为不锈钢的精炼炉,希望能够收到投资节省、冶炼成本低、钢水质量好、容易开发多种不锈钢品种和其它合金钢品种的效果,在激烈的市场竞争中凭借先进工艺的优势取胜。
Energiron---新一代直接还原技术
来源:
文章发表时间:
2006-11-28
与炼钢车间结合在一起,Energiron直接还原技术优化了运营成本、产品质量、工厂操作以及减轻对环境的影响。
达涅利和得兴HYL技术联合体所展现的Energiron工艺代表了全球钢铁市场该领域的顶尖技术,它结合了两个公司在生产高质量、先进的DRI和HBI设备方面的知识和经验。
联合体的目标是为DRI生产商提供可靠的而且技术先进的直接还原设备,以生产高质量和性能稳定的DRI,例如,全面控制DRI的金属化程度和高碳含量,以适应长途运输和电炉的高功率。
这个战略性技术联合体以新的Energiron为商标呈现给世界,使三个公司各自的技术和诀窍融合在一起,进行气体直接还原铁厂的设计和建设。
新型Enegiron技术的突出特点是金属产品的高性能含量,及将直接还原厂和炼钢厂结合在一起,达到节能和降低成本的目的。
此工艺能广泛适应于各种铁矿石,包括高硫矿,并能使用多种还原气体,例如,天然气、发生炉煤气和焦炉煤气。
这个新联合体的第一个成就是与阿联酋迪拜Genera资产公司(GHC)签订的交钥匙工程,提供一个年产140万t长材的联合钢铁厂。
2006年7月末,美国明尼苏达钢铁公司宣布了与达涅利和HYL技术公司签订一排他性协议,协议要求将新的Energiron直接还原厂和炼钢设备安装近于(美国)明尼苏达Nashwauk的联合矿山和炼钢厂。
年产175tDRI的Energiron厂和年产150t的板坯连铸机皆属于交钥匙工程。
炼钢厂将包括电炉、钢包炉、真空脱气炉和板坯连铸机,并将采用达涅利的专利技术。
预计2007年初开始建设,2009年底投入工业化生产。
Energiron技术有如下显著特点:
该工艺对原料适应性强;
DRI质量控制(高碳);电炉直接热装DRI;高效率,降低生产成本。
工艺灵活性含有还原介质CO和H2的任何气体几乎都可用做炉补充煤气,而无需对还原煤气回路进行任何大的改动,例如:
来自蒸汽重整炉的重整煤气;来自煤/碳氢气化合物气化煤气;来自其它炼铁工艺的净化煤气;焦炉煤气;自身重整煤气。
在Energiron技术流程中,CO2和水被从烟气中分离出来,再用于还原炉,并能从外管线气源补充新的还原气。
Energiron技术的设计是通过利用干净的高还原性煤气来开发其工艺。
Energiron工艺可灵活调整产品质量
由于渗碳条件的改进,Energiron工艺能获得1%~4%含碳量水平。
高碳DRI比普通的传统直接还原工艺所获得低碳DRI具有更高的稳定性。
高碳DRI的稳定性源于高的碳化铁含量,它能抑制金属铁与氧化成分(空气-水)接触后发生再氧化。
Energiron高碳DRI储藏和运输安全,无需惰性气体保护和压块,从而省去压块(HBI)环节,并降低了运输成本。
这种产品能直接用于毗邻的电炉或运输到其他地方。
在墨西哥的Hylsa公司,用Energiron工