论文大体框架.docx
《论文大体框架.docx》由会员分享,可在线阅读,更多相关《论文大体框架.docx(14页珍藏版)》请在冰豆网上搜索。
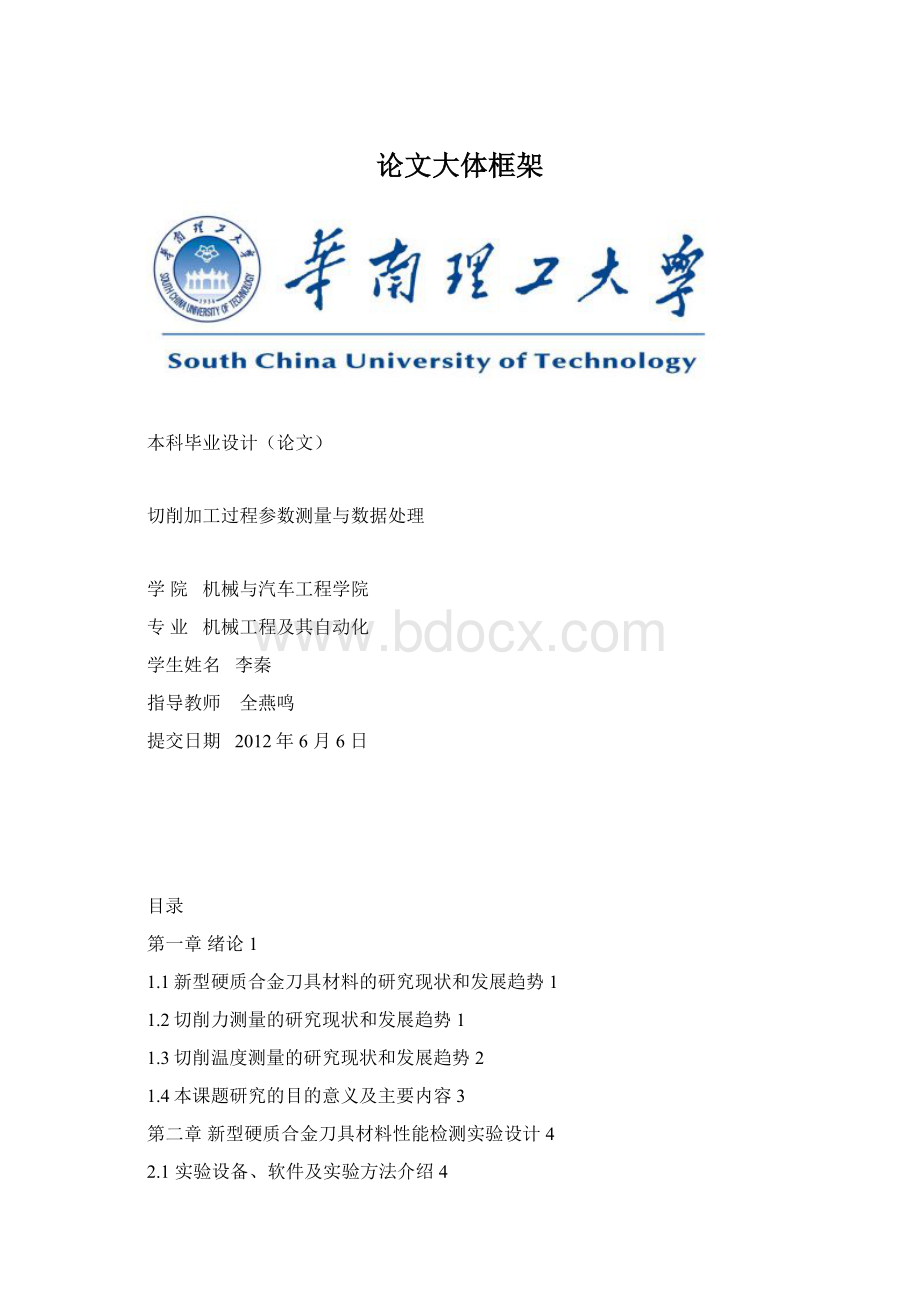
论文大体框架
本科毕业设计(论文)
切削加工过程参数测量与数据处理
学院机械与汽车工程学院
专业机械工程及其自动化
学生姓名李秦
指导教师全燕鸣
提交日期2012年6月6日
目录
第一章绪论1
1.1新型硬质合金刀具材料的研究现状和发展趋势1
1.2切削力测量的研究现状和发展趋势1
1.3切削温度测量的研究现状和发展趋势2
1.4本课题研究的目的意义及主要内容3
第二章新型硬质合金刀具材料性能检测实验设计4
2.1实验设备、软件及实验方法介绍4
2.1.1实验设备介绍4
2.1.2实验原理及方法介绍4
2.2实验方案设计12
2.2.1正交试验介绍12
2.2.2正交试验设计12
2.3本章小结13
第三章数据采集及处理分析14
3.1数据采集14
3.2数据处理和分析14
3.3本章小结14
第四章刀具优化设计14
4.1原有刀具介绍及分析14
4.2刀具优化设计14
4.3本章小结14
结论14
参考文献14
第一章绪论
1.1新型硬质合金刀具材料的研究现状和发展趋势
硬质合金由难熔金属化合物(如WC、TiC)和金属粘结剂Co经粉末冶金法制成,含钴量的多少决定了硬质合金的韧性大小,但钴会降低硬质合金的熔点,影响刀具耐热性能,此外钴的成本高、可用量越来越少,而且对环境会造成污染,不符合绿色制造和环保的要求。
新型的无钴少钴硬质合金将成为材料科学工程发展的一个新方向。
研究现状介绍请阅读附件文献并做简单介绍
1.2切削力测量的研究现状和发展趋势
切削测力仪从五十年代发展到七十年代,其测量方法(如机械式液压式和电气式)基本上由应变式和压电式所代替。
1963年德国阿亨工业大学首先研制成功采用三向压电石英力传感器的三向车削测力仪。
此外瑞士苏黎士联邦工业大学对压电测力仪进行了基础理论的的研究,并与瑞士Kistler公司协作研制成功具有优良性能的压电石英传感器系列和车削、钻削、铣削测力仪及多分量测力平台,电荷放大器等等,从而完成了压电测试系统所需要成套设备,开辟了压电测试的新局面。
1970年意大利在《机床设计与研究》(MTDR)发表三向压电晶体式车削测力仪。
英国门切斯特大学1971年研制成二向压电晶体式平面磨削测力仪。
上世纪八十年代,切削力的测量已由原来的测静态力发展到测动态力,瑞士的Kistler公司及国外其它研究部门和厂商研制的切削测力仪当时已经达到了实用水平[5]。
进入二十世纪八十年代,许多学者利用比较成熟的压电切削测力仪进行实验和研究工作,使用量日趋扩大,将采集的动态切削力信号进行各种处理,如利用动态数据建立统计预测和分析刀具破损情况,美国利用动态切削力信号建立时间序列模型,对机械加工中表面光洁度、刀具磨损进行在线控制,另外还可以建立动态数据系统,通过求得切削加工中的传递函数来评价机械加工系统的动态稳定性,同时相关分析和谱分析在机械行业数据处理中也得到广泛应[5]。
切削力数据采集系统由测力仪、电荷放大器、数据采集卡、计算机系统等组成。
目前利用labview编写程序虚拟机(VI)来替代传统控制电路是目前研究的主流技术方向。
与传统仪器相比,虚拟仪器在智能化程度、处理能力、性能价格比、可操作性等方面都具有明显的技术优势。
利用虚拟仪器技术在线采集和处理多种切削参数,并对切削过程监控,具有很大的优越性。
VI已经是当今计算机辅助测控领域中的一项重要技术[6]。
目前,切削力测力系统研究仍然方兴未艾,大量研究结果表明,切削状态的每个微小变化都能通过切削力的变化反应出来,检测切削力是目前国内外研究与应用最多的监控方法之一。
此种方法具有力信号比较容易采集、响应快、灵敏度高、便于在线实时测量等优点。
缺点是测力仪在使用时或多或少要改变机床的原有部件,影响机床的整体特性,特别是对高精度数控机床影响更大。
现代切削加工正在向高速强力切削、精密超精密加工方向发展,机床的振动频率也会远远高于系统的固有频率,
这对切削力测量系统提出了新的要求,针对这些要求,切削力测量技术将会朝着:
开发新的弹性元件并优化结构;应用集成电路和微电子技术,使数据采集系统集成化,提高数据采集的速度与精度;完善数据处理分析软件的功能,将虚拟仪器技术引入切削力测试系统;建立专家系统[3][4]这三个大方向发展。
1.3切削温度测量的研究现状和发展趋势
切削热是切削过程的重要物理现象.切削热产生的切削温度是影响刀具耐用度的重要因素[1]。
Oxley等人指出:
切削温度还是决定切削金属变形区几何形状和切削力大小的重要因素.切削热影响积屑瘤大小和已加工表面质量,特别是在精加工和超精加工时,切削温度对加工精度的影响更加突出.因此,国内外从事金属切削研究的工作者,在切削温度的理论计算和实验技术方面,进行了大量的研究工作,已发展了许多测试技术.这些技术包括人工热电偶法,工件-刀具组成的自然热电偶法、热敏漆涂层法、高速钢金相组织变化法及红外照像法等[7]。
近年来,采用这些方法进行的切削温度测量方面的研究工作如下:
G.S.utter采用基于可见光范围的传感技术的加强CCD相机,以及一种正交切削实验装置测量正交切削过程中切削区域温度,以分析不同切削速度以及切削厚度对切削温度的影响。
D.O'Sullivan采用嵌入式人工热电偶方法以及红外热像法分别测量了硬质合金刀具车削6082-T6铝合金时的工件温度以及刀具温度分布情况。
G.Suttera设置了一个正交切削试验装置,用于测量切削过程中切屑和刀具侧面的温度场。
陈明等人应用红外热像仪测温系统对高速铣削过程中切削温度的动态变化规律进行试验研究,给出了铝合金高速铣削过程中存在的临界切削速度关键数据及切削温度随切削速度的变化。
通过在YG6硬质合金车刀刀片的前、后刀面上上嵌入标准热电偶的方法,分析了在不同切削参数以及冷却方法(干式切削、压缩空气、乳化液浇注以及最小量润滑方式)条件下车削复合材料时刀具的前、后刀面的温度变化情况。
周泽华等人对G.Loewen,M.C.Shaw的热源法进行了推广分析并对切削过程的温度场进行了解析求解[8]。
在进行切削过程测量温度时,由于加工现场切屑和切削液飞溅、刀具或工件旋转、刀具和切屑及工件互相遮挡等因素使得现场实施困难,对切削过程的瞬态切削温度的实验测量目前仍是一个难题。
1.4本课题研究的目的意义及主要内容
本次论文是基于针对我材料学院新研发的硬质合金材料的切削性能的实验数据分析报告和改良刀具的设计说明。
实验包括切削力和切削温度实验数据的采集,测量切削力和切削温度,以及刀具磨损度。
通过以上实验数据研究切削机理、优化切削用量和刀几何参数。
通过力和温度的变化来监控切削过程,反映刀具磨损或破损、切削用量合理性。
最终,得出新材料刀具的部分切削加工性能,并完善刀具和切削参数。
本文的主要内容包括:
1)参与新型硬质合金(可转位刀片)刀具切削试验,协助进行刀具改良设计。
2)熟悉切削力、切削温度和切削热的在线试验装置、测量仪器和数据采集系统,协助进行切削实验装置设计、加工。
3)实施切削实验,完成至少三种条件下的试验数据采集。
4)分析试验数据,据此提出刀具设计和切削实验参数改进意见,重复实验。
5)提交刀具设计图和切削试验装置设计图,完成毕业论文。
第二章新型硬质合金刀具材料性能检测实验设计
2.1实验设备、软件及实验方法介绍
2.1.1实验设备介绍
本实验室用的数控机床是大连化成机电设备有限公司生产的CKA6150i型系列数控车床。
该机床具有较高的经济性及实用性。
由于机床采用独立主轴结构,前后轴承采用日本NSK精密轴承,使得机床具有高速、高精度的特点。
相关性能参数如下:
床身上最大工件回转直径(500mm)
最大加工长度(680、930mm)
主轴中心高(250mm)
主传动主传动(FANUC交流主轴伺服电机,无级调速)
主电动机(双速电机)(11/15kW)
最大进给速度6m/min、
主轴转速范围(30~3000r/min)
(介绍测力仪温度采集卡、显微镜等设备)
2.1.2实验原理及方法介绍
本实验主要通过测量新型硬质合金刀片切削不锈钢材料过程中的力和温度来分析新型硬质合金刀片的性能。
2.1.2.1实验过程中的切削力
(一)切削力的来源、合力及其分力
切削力是工件材料抵抗刀具切削所产生的阻力,它是影响工艺系统强度、刚性和加工工件质量的重要因素。
切削力也是设计机床、刀具、夹具和计算切削动力消耗的主要依据。
在自动化生产和精密加工中,也常利用切削力来检测和监控刀具磨损、加工表面质量;
刀具在切削工件时,存在切屑与工件内部弹性塑性变形的抗力;切屑与工件对刀具产生的摩擦阻力;两者作用在刀具上的合力为F。
合力F作用在切削刃上工作空间某方向,如图2-1-1所示,由于大小与方向都不易确定,因此,为了便与测量、计算和反映实际作用的需要,可将合力F分解为三个分力:
切削力Fa(主切削力Fz)—在主运动方向上的分力;
切削力Fp(主切削力Fy)—在垂直于假定工作面上分力;
图号和名称
切削力Fa(主切削力Fx)—在进给运动方向上的分力。
背向力Fp与进给力Ff也是推力FD的分力,推理是在基面上且垂直于主切削刃的合力。
合力F、推力Fp与各分力之间的关系:
(公式要标明引用参考文献,并在公示后面标注序号)
此式表明,主偏角κr大小影响各分力间的比例。
(二)各分力的作用和测量切削力的方法
为了实际应用,Fr可分解为相互垂直的Fx(国标为Ff)、Fy(国标为Fp)和Fz(国标为Fc)三个分力。
在车削时:
上图的图号和标题要重新编排,不能直接出现在图中
Fz(Fc)——主切削力或切向力。
它切于过渡表面并与基面垂直。
Fz是计算车刀强度,设计机床零件,确定机床功率所必需的。
Fx(Ff)——进给抗力、轴向力或走刀力。
它是处于基面内并与工件轴线平行与走刀方向相反的力。
Fx是设计进给(走刀)机构,计算车刀进给功率所必需的。
Fy(Fp)——切深抗力、或背向力、径向力、吃刀力。
它是处于基面内并与工件轴线垂直的力。
Fy用来确定与工件加工精度有关的工件挠度,计算机床零件和车刀强度。
它与工件在切削过程中产生的振动有关。
切削过程中的切削力信号需要由测力仪来采集。
测力仪的主要工作元件是测力传感器,目前常用的测力仪是电阻应变式和压电晶体式。
压电式晶体测力仪如图所示为压电晶体传感器,它是由3组石英晶体组成(每组2片),并被密封在不锈钢体壳中,在两片石英晶体中间装有金属电极和因触电喝凉的导线。
各组石英晶体分别受Fc、Fp和Ff力作用产生压电效应,是两片变形的晶体相对表面上产生负电荷,电荷量多少和受力大小成正比。
电荷由电极经过导线输入电荷放大仪在经过光线示波器记录。
图31326为压电晶体测力仪(方孔为装刀孔)。
测力仪被固定在两底板间、经精确水平调整的4个压电晶体传感器,串联后可分别测量3个切削分力。
目前利用计算机数据处理可更简便得到切削力数值。
将电荷放大以输出的电信号,通过A/D转换器获得的数字信号输入计算机,再由已编制的程序进行数据处理,最后经打印、绘图显示出三项切削力数据和变化规律图形。
上图的图号和标题要重新编排,不能直接出现在图中
目前,压电晶体测力仪价格昂贵,但是由于其测力精度比较八角环电阻式测力仪要高,在动态受理情况下能测的切削力微小变化,因此在科研单位中使用的比较多。
(三)影响切削力的因素
凡影响一切削过程变形和摩擦的因素都影响切削力,其中主要包括有:
切削用量,工件材料和刀具几何参数等三个方面。
下面介绍其中主要因素对切削力的影响规律。
涉及到本次试验要研究的方面会详细一些。
1、工件材料
(1)硬度或强度提高,剪切屈服强度τs增大,切削力增大。
(2)塑性或韧性提高,切屑不易折断,切屑与前刀面摩擦增大,切削力增大。
2、切削用量
(1)背吃刀量(切削深度)ap、进给量ƒ增大,切削层面积增大,变形抗力和摩擦力增大,切削力增大。
由于背吃刀量ap对切削力的影响比进给量对切削力的影响大(通常XFz=1,YFz=0.75-0.9),所以在实践中,当需切除一定量的金属层时,为了提高生产率,采用大进给切削比大切深切削较省力又省功率。
(2)切削速度vc
1)加工塑性金属时,切削速度Vc对切削力的影响规律如同对切削变形影响一样,它们都是通过积屑瘤与摩擦的作用造成的。
2)切削脆性金属时,因为变形和摩擦均较小,故切削速度Vc改变时切削力变化不大。
3、刀具几何角度
(1)前角γo:
前角增大,变形减小,切削力减小。
(2)主偏角κr:
主偏角κr在30°-60°范围内增大,由切削厚度hD的影响起主要作用,使主切削力Fz减小;主偏角κr在60°-90°范围内增大,刀尖处圆弧和副前角的影响更为突出,故主切削力Fz增大。
一般地,κr=60°-75°,所以主偏角κr增大,主切削力Fz增大。
实践应用,从切削力观点分析,切削时不宜选用过大的负刃倾角λs。
特别是在工艺系统刚度较差的情况下,往往因负刃倾角λs增大了切深抗力Fy的作用而产生振动。
4、其他因素影响
刀尖圆弧半径增大,切削变形、摩擦增大,切削力增大。
5、刀具磨损
刀具的切削刃及后刀面产生磨损后,会使切削时摩擦和挤压加剧,因此使得切削力Fc和Fp增大。
这一项是这次切削实验刀具性能的理论基础,同时可以对理论作验证。
6、切削液
合理的选用切削液,会产生良好的冷却和润滑作用,能减小刀具与工件间的摩擦和粘结,因此会使切削力减小。
高效的切削液比干切削能减小
2.1.2.2实验过程中的切削热和切削温度
(一)切削温度的来源
切削热是切削过程中必须考虑的一个重要的物理因素,因为切削温度能够改变前刀面上的摩擦系数,改变工件材料的性能,影响已加工表面质量的提高。
所以,国内外研究金属切削方面的人员在切削温度的理论计算和实验技术方面,都进行了大量的研究工作。
切削时所消耗的能量,除了1—2%用以形成新表面和以晶格扭曲等形式形成潜藏能外,有98—99%转换为热能。
由于很少一部分的能量转换成潜藏能,我们可以近似地认为切削时消耗的能量全部转换为热能。
在前面我们已经知道,被切削的金属在刀具的作用下会发生塑性变形,这是切削热的一个重要来源。
除了切削作用,摩擦也是产生大量热量的原因,像切屑与前刀面、工件与后刀面之间都会发生摩擦。
因此,切削时共有三个发热区域:
剪切面、切屑与前刀面接触区、后刀面和切削表面的接触区。
如图2-6所示,箭头表示的是热传导的方向,在剪切面区域发生了强烈的塑性变形,有最大的热量传导到切屑和工件,是引起切屑和工件的温度
升高主要原因,这些热量是由于金属发生塑性变形产生的,是第一个发热区域;后刀面与切削表面的接触区也有较大的热量传导,工件已加工表面因为这部分热量而有明显的温度提升,这部分热量的产生时由于刀具后刀面与切
削表面摩擦所产生的,是第二个发热区域;切削与前刀面接触区是第三个发热区,相比较前两个发热区域,这个区域的热传递要小得多,且只在刀具与切屑之间传导,对工件没有影响。
上图的图号和名称
(二)切削温度测定原理
1.切削温度测定原理
在生产中,切削热对切削过程的影响是通过切削温度起作用的。
切削温度是指切削过程中切削区域中切削区域的平均温度。
切削温度的确定以及切削温度在切屑—工件—刀具中分布可利用热传导和温度场的理论计算确定,但较为简便和常用的是利用实验方法来测定。
2.温度测量方法
测量切削温度的方法很多,例如有热电偶法、热辐射法、远红外
上图的图号和名称
法和热敏涂红色法等。
热电偶法用得较多,它的测温装置简单、测完方便。
这次试验选用的是人工热电偶法:
见图2—3,利用人工热电偶法可以测定刀具和工件上的定点温度值。
在刀具和工件被测点上钻出的小孔,在空中插入一对标准热电偶丝(镍鉻—镍铝或铂—铂铑等),两热电偶丝一端焊接点置于刀具或工件小孔底的被测点处,另一端分别接入毫伏计两极,通过毫伏计测的冷热端的电势差。
空中热电偶丝之间和孔壁均保持绝缘。
3.切削温度分布
图2-5微侧的得到的刀具、工件和切屑中温度分布;图2-7为刀具前刀面上的温度分布。
从图中看出温度分布规律为:
上图的图号和标题要重新编排,不能直接出现在图中
1)刀—屑接触面间摩擦大,热量不易传散,股温度值最高;
2)切削区域的最高温度点在前面上进切削刃处;
3)切屑带走热量最多,切屑上平均温度高于刀具和工件上的平均温度,因切削剪切面上塑性变形严重,其上各点剪切变形功大致相同。
个点温度值也较接近。
工件切削层中最高温度在近切削刃处,它的平均温度较刀具上最高温度点底2~3倍。
2.2实验方案设计
本实验用新型硬质合金刀具和普通硬质合金刀具YG8对不锈钢进行车削,并实时检测记录切削力及切削温度数据,对比分析新型硬质合金刀片相对普通硬质合金刀片的切削性能等。
2.2.1正交试验介绍
介绍正交试验的特点及数据分析方法
2.2.2正交试验设计
本实验分别对新型硬质合金刀具和普通硬质合金刀具YG8采用三因素三水平的L9(34)正交试验。
1)三个因素分别为切削深度ap,进给量f,切削速度vc
2)各因素的水平取:
ap=0.2、0.5、1.0mm
f=0.02、0.05、0.1mm/r
vc=50、100、150m/min
3)试验指标:
切削力和切削温度
一般认为切削三要素对切削力的影响是独立作用的,正交试验表头设计见表2-1(该表编号请依本章顺序修改)。
表2-1正交试验表头设计
因素水平
A
背吃刀量(mm)
B
进给量(mm)
C
切削速度(m/min)
1
0.2
0.02
50
2
0.5
0.05
100
3
1.0
0.1
150
2.3本章小结
第三章数据采集及处理分析
3.1数据采集
包括测力和测温具体的实验操作,标定方法,原始数据的采集等
3.2数据处理和分析
包括力和温度的数据处理分析
3.3本章小结
第四章刀具优化设计
4.1原有刀具介绍及分析
4.2刀具优化设计
4.3本章小结
结论
参考文献