教材连铸坯低倍检验标准及在生产中的应用.docx
《教材连铸坯低倍检验标准及在生产中的应用.docx》由会员分享,可在线阅读,更多相关《教材连铸坯低倍检验标准及在生产中的应用.docx(17页珍藏版)》请在冰豆网上搜索。
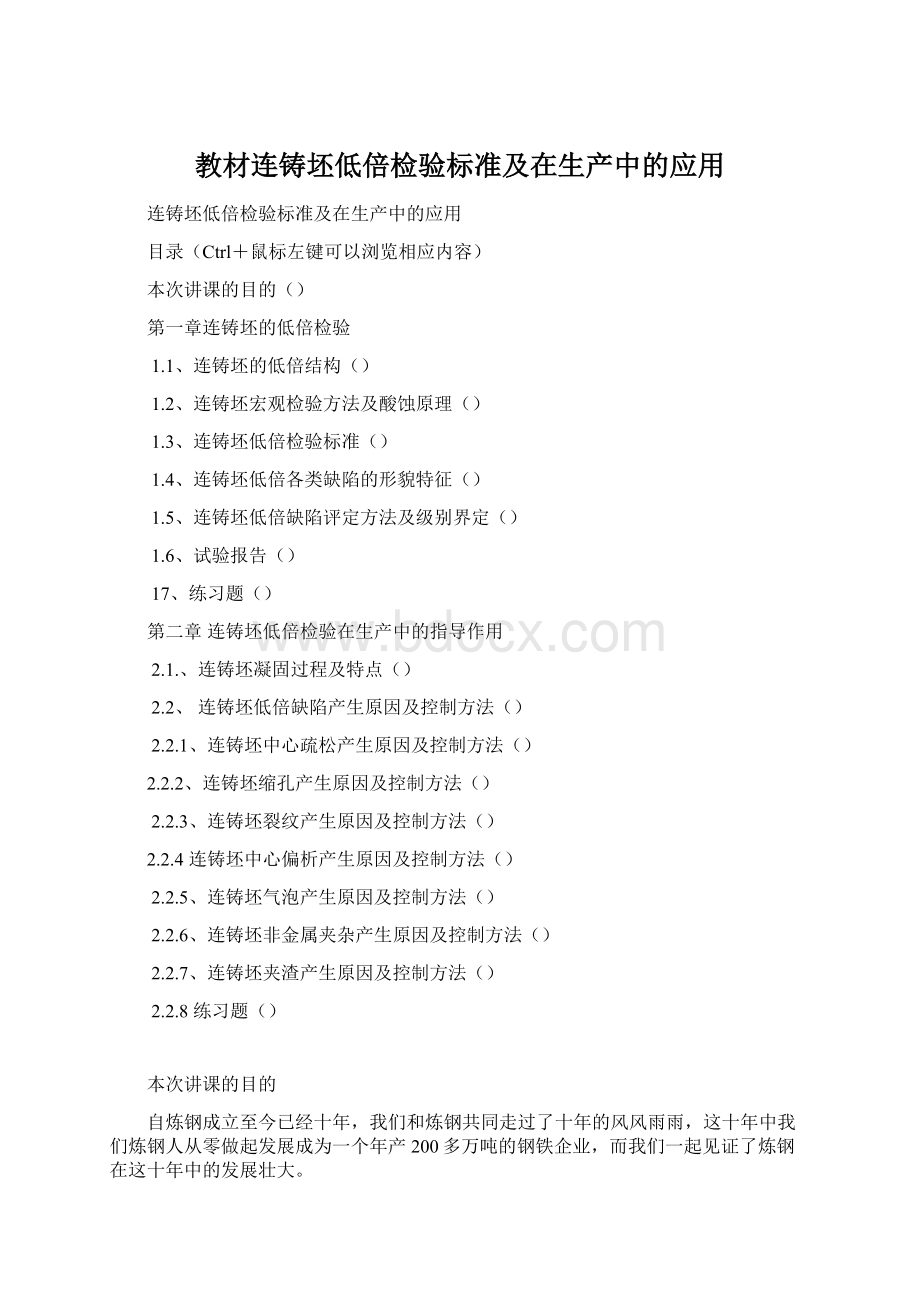
教材连铸坯低倍检验标准及在生产中的应用
连铸坯低倍检验标准及在生产中的应用
目录(Ctrl+鼠标左键可以浏览相应内容)
本次讲课的目的()
第一章连铸坯的低倍检验
1.1、连铸坯的低倍结构()
1.2、连铸坯宏观检验方法及酸蚀原理()
1.3、连铸坯低倍检验标准()
1.4、连铸坯低倍各类缺陷的形貌特征()
1.5、连铸坯低倍缺陷评定方法及级别界定()
1.6、试验报告()
17、练习题()
第二章连铸坯低倍检验在生产中的指导作用
2.1.、连铸坯凝固过程及特点()
2.2、连铸坯低倍缺陷产生原因及控制方法()
2.2.1、连铸坯中心疏松产生原因及控制方法()
2.2.2、连铸坯缩孔产生原因及控制方法()
2.2.3、连铸坯裂纹产生原因及控制方法()
2.2.4连铸坯中心偏析产生原因及控制方法()
2.2.5、连铸坯气泡产生原因及控制方法()
2.2.6、连铸坯非金属夹杂产生原因及控制方法()
2.2.7、连铸坯夹渣产生原因及控制方法()
2.2.8练习题()
本次讲课的目的
自炼钢成立至今已经十年,我们和炼钢共同走过了十年的风风雨雨,这十年中我们炼钢人从零做起发展成为一个年产200多万吨的钢铁企业,而我们一起见证了炼钢在这十年中的发展壮大。
在这十年坎坷中我们走出了一条由向规模要效益到由向质量要效益之路。
现在随着公司改革的不断深入和二次创业号召的提出,公司及厂部对我们的生产经营提出了要求更严、目标更高的要求;特别是现在随国家经济政策的调整及市场不断的发展变化,更要求我们在生产中不能仅仅停留在提高产品的外观质量这一低层次上,而是要以提高产品的内在质量,不断适应市场需求为最终目标。
产品质量的好坏除了生产中严格贯彻标准化操作及不折不扣的执行工艺纪律外,还需要对产品进行外观及内在质量检验,通过质量检验结果进一步对工艺进行改进、优化及完善,而铸坯低倍检验是一个快捷、经济的检验铸坯内在质量的检验方法。
通过本次授课希望大家能够基本掌握以下内容:
1、了解铸坯低倍检验方法及检验标准;
2、掌握铸坯低倍组织缺陷类型、缺陷产生原因及在生产中控制不良品的方法。
第一章连铸坯的低倍检验
1.1、连铸坯的低倍结构
一、连铸坯的凝固过程决定了铸坯的低倍组织
连铸坯的低倍组织结构是由铸坯的冷却凝固决定的:
连铸坯凝固可以看做是分阶段的连续凝固过程,凝固过程经历了三个阶段,即:
1、钢水遇到结晶器壁形成初生坯壳;
2、带液芯的铸坯在冷却中快速凝固;
3、带液芯的铸坯在冷却中稳定生长直至完全凝固。
正是以上凝固过程特点决定了铸坯组织结构。
二、铸坯的低倍结构
1、铸坯低倍结构定义:
从完全凝固的铸坯上取下一块横断面试样,经过磨光酸洗后用肉眼所观察到的组织叫低倍组织。
它是用肉眼或不大于十倍的放大镜检查金属表面、断口或宏观组织及其缺陷的方法。
2、连铸坯的低倍组织构成:
连铸坯的典型低倍组织是由三部分组成:
(1)、靠近表皮的细小等轴晶带,其特点是:
细小致密厚度小,其厚度一般为5~10mm。
(2)、其次是树枝晶带(柱状晶带),其特点是:
形状象树枝状其方向垂直于铸坯表面。
(3)、中间是粗大等轴晶。
铸坯的典型低倍组织见图:
(加工图片\典型低倍机构组织.jpg)
酸蚀低倍检验的作用
连铸是一个可以控制的传热过程,通过对凝固过程的检查和控制可以获得良好的铸坯质量。
从这个意义讲,了解连铸条件与最终产品缺陷之间的相互关系就可能预先判定产品的质量,这是实现计算机质量控制的基础。
酸蚀低倍检验的最终目的是得到一定工艺条件下所希望的铸坯质量,并根据检查结果适当调整工艺参数。
3、酸蚀低倍检验的作用主要有:
1)对铸坯质量进行监控,对为改善铸坯质量进行的工艺参数调整可行性进行判定。
2)开发试制新钢种时,根据不同的工艺条件(中包温度高低、拉速快慢、比水量大小等)切取铸坯样进行酸洗低倍检验进行分析,以验证、修订工艺控制参数。
3)根据低倍组织中反馈出来的各种具体缺陷种类、形状和位置,结合钢种凝固特点、凝固条件,对连铸工艺参数、浇铸操作和设备运行状况存在的问题做出判断,采取相应的措施,改善并提高铸坯质量。
4)为实现计算机质量控制做基础工作。
4、生产中对铸坯低倍结构的要求:
连铸坯的低倍组织对钢材的机械性能及加工性能都有很大影响:
除某些特殊用途要求柱状晶组织外绝大部分都希望得到等轴晶带大的组织,例如我厂对Qst32-3等钢种的等轴晶要求是≥40mm,因此提高铸坯等轴晶带是提高铸坯质量的一个重要任务,在生产中我们甚至可以通过铸坯低倍结构来分析冷却工艺制度缺陷及改进方案,由此可见铸坯低倍检验在生产中的重要性。
1.2、连铸坯宏观检验方法及酸蚀原理
一、连铸坯宏观检验方法
连铸坯宏观检验方法有:
酸蚀、硫印、塔形车削以及无损控伤等方法和断口分析等。
酸蚀宏观检验方法在以上方法中因为检验手段简单、费用较低所以得到应用较广。
二、酸洗检验低倍原理
钢中的许多缺陷如夹杂、偏析、疏松及气孔等因为尺寸较小,或由于塑性变形使其和钢基体相连,难以用肉眼辨认。
通过选用适当的腐蚀剂,由于缺陷和钢基体浸蚀程度的差别,可以使缺陷和钢基体产生选择浸蚀作用,从而使缺陷在试样上表现出来。
三、铸坯低倍浸蚀方法
低倍组织浸蚀方法分为热酸浸蚀法、冷酸浸蚀法和电解腐蚀法三种,我公司以冷酸浸蚀法检验低倍
冷酸浸蚀操作要点如下:
(1)根据材料种类选用合适的和一定配比的浸蚀液。
如:
1:
1的盐酸和氯化铜溶液
(2)试样检验面的光洁度应在
7以上,酸蚀前应将检验面擦净,去除油污。
(3)用擦蚀法时,将酸液慢慢倒在置地耐酸盆中的试样同上,然后用刷子将酸液刷匀,直至清晰显示出低倍组织和缺陷为止。
(4)浸蚀好后,用水冲掉酸液,并用碱水中和,然后用再热水冲洗,立即吹干。
1.3、连铸坯低倍检验标准
我公司铸坯低倍检验标准以YB/T266-1991为基础并结合我厂工艺装备水平及市场需求进行了更严格的细化,其标准适用于100-300mm的方坯和矩形坯。
以下是某厂铸坯低倍检验执行的标准:
除焊条芯用及软钢线材用坯外,方坯应进行低倍组织检查。
在其酸浸低倍试片上不得有肉眼可见的气泡、白点、裂缝、翻皮、夹杂、残余缩孔。
按GB1979进行评级的合格级别为:
低倍组织要求:
一般疏松≤3级、中心疏松≤3级、偏析≤3级
我公司根据我厂工艺装备水平及市场对不同钢种的加工要求制订了如下铸坯低倍检验标准:
连铸坯低倍检验标准
钢种
缩孔(mm)
中心裂纹(级)
中间裂纹(级)
中心疏松(级)
一般疏松(级)
皮下裂纹(级)
皮下气孔(级)
表面针孔
等轴晶
纵表面针孔
ML08ALSWRCH8ASWRCH6ASWRCH10A
≤3
≤15mm
0
≤2.0
≤2.0
≤1.0
≤10
SWRCH6A-KL
≤3
≤1.5
≤1.5
≤3.0
≤2.0
≤0.5
≥40
≤8
SWRCH15A-KL
≤3
≤1.0
≤2.0
≤0.5
≤2.0
≤0.5
≥70
≤8
SWRCH15ASWRCH18ASWRCH22A
≤2
0
0
≤2.5
≤2.0
≤3.0
≤0.5
≤10
ML35SWRCH35K
≤1
0
0
≤3.0
≤2.0
≤3.0
SCM435ML40Gr
0级
0
0
≤2.0
≤1.5
≤2.0
S20C
≤2
≤2.0
≤2.5
≤2.0
≤3.0
≤1.0
≤10
S45C45
≤3
0
≤1.0
≤2.5
≤2.0
≤3.0
≤1.0
≤10
60#65#70#
≤3
0
0
≤2.5
≤2.0
≤3.0
SWRH77B
≤2
0
0
≤2.5
≤1.5
≤2.5
30MnSiB
≤1
0
0
≤2.5
≤1.5
≤3.0
ER70S-6
≤3
≤1.0
0
≤1.5
≤2.5
≤2.0
H08A
≤4
≤1.5
0
≤2.0
≤3.0
0
≤2.5
≤60
Q195LY-3
≤4
≤1.5
0
≤2.5
≤3.0
≤1.0
≤2.0
≤40
LS
≤2
≤2.0
≤0.5
≤3.0
≤3.0
≤2.0
≤2.5
≤80
Qst32-3
≤3
≤1.5
≤1.5
≤3.0
≤2.0
≤0.5
≥40
≤8
1.4、连铸坯低倍各类缺陷的形貌特征
经过酸洗后的铸坯试样由于缺陷和钢基体分离,我们可以通过肉眼或10倍左右的放大镜进行观察。
铸坯低倍的缺陷种类及形貌特征如下;
1、中心疏松
在酸洗试样上集中在中心的空隙和暗点(加工图片\疏松.jpg)
2、缩孔
在酸洗试样的中心部位呈现不规则的空洞(加工图片\缩孔(中包温高).jpg)
3、皮下裂纹
在酸洗试样的边部细小等轴晶于树枝晶的交界处产生并沿树枝晶向内部扩展的裂纹(加工图片\皮下裂纹.jpg)
4、内部裂纹
(1)、中心裂纹
在酸洗试样中心出现的裂纹(加工图片\中心裂纹.jpg)
(2)、中间裂纹
在酸洗试样上裂纹在树枝晶区出现并沿树枝晶扩展(加工图片\中间裂纹(中包温高温高).jpg)应注意其与皮下裂纹的区别
5、中心偏析
在酸洗试样的中心部位呈现腐蚀较深的暗斑,有时在暗斑周围有灰白色带及疏松(加工图片\中心偏析.jpg)
5、铸坯的气孔
在酸洗试样皮下沿树枝晶方向呈现分散或簇状分布的细长裂缝或椭圆形气孔(加工图片\皮下气泡2.jpg)
6、非金属夹杂
在酸洗试样上呈现不同规则和不同颜色的非金属颗粒或非金属颗粒浸蚀剥落后留下的坑。
它们在酸浸试片上以镶嵌的形式存在,并保持其固有的各种颜色,常见的有灰白色、米黄色和暗灰色等。
有些低倍夹杂在制片时可能脱落,而表面为空洞。
空洞的特点区别于气泡是它的边缘不整齐,呈海绵状。
7、夹渣
在酸洗试样上呈现不同形状和不同颜色的块状或颗粒(加工图片\夹渣.jpg)
以上是常见铸坯低倍缺陷种类,另外还有如:
白亮带、翻皮及异金属夹杂等留有以后再探讨。
1.5、连铸坯低倍缺陷评定方法及级别界定
一、评级图片
冶金标准在评级标准图片中将需要评级的缺陷各分为四级不需要评级的缺陷只列一张图片,评级试样为边长(直径)100mm,疏松缺陷评级图(加工图片\中心疏松第一评级图.jpg、加工图片\中心疏松第二评级图.jpg)
其他缺陷评级图因篇幅原因这里不再累述。
二、评定方法
评定各级缺陷以肉眼可见为限,根据严重程度依据评级图进行比较分别评定。
当其严重程度介与相邻两级之间时可评半级。
在评定其他尺寸的连铸坯缺陷时可以根据缺各陷级评级图按比例进行放大或缩小。
1.6、试验报告
铸坯试样经过低倍检验后必须按标准进行试验报告填写,填写内容有:
1、委托单位。
2、检验牌号。
3、检验试样的冶炼炉号。
4、试样编号。
5、连铸坯规格。
6、检验结果:
缺陷类型、评定级别和应说明的情况等。
7、检验者、审核者及检验日期等
1.7、练习题
1、什么是铸坯的低倍组织?
铸坯的低倍组织有哪些构成?
其特点是什么?
2、铸坯的低倍组织缺陷有哪些?
3、简述铸坯低倍缺陷皮下裂纹、皮下气孔的形貌特征
4、生产中对铸坯低倍结构的要求是什么?
第二章连铸坯低倍检验在生产中的指导作用
2.1、连铸坯凝固过程及特点
一、连铸坯凝固的条件及钢水结晶过程
要了解连铸坯的凝固必须弄清以下几个概念:
〕
1、过热度:
钢水实际温度与液相线温度的差值
2、凝固温度:
钢由液体状态变成固体状态的温度为凝固温度。
3、过冷度:
钢液实际温度低于凝固温度的度数,它是钢水凝固必备的两个条件之一。
4、结晶核:
液体金属中存在的许多体积很小、近程有序排列的原子集团形成的胚胎晶核,它也是钢水凝固必备的两个条件之一。
钢水注入到结晶器后先从结晶器壁开始形成结晶核,这些结晶核相互连接发展逐渐形成凝固前沿。
由于钢水中各种元素在钢液与钢固体的溶解度不同,造成随凝固进行固相中钢水中元素析出,使固液界面处液相中溶解元素的浓度高于原来液相中的浓度,从而造成该处液相线温度的降低。
当液相钢水实际温度高于固液界面温度时热量从钢水传向凝固前沿。
但是当凝固前沿钢水温度低到液相线温度以下时该处液相已经处于过冷状态,这样凝固前沿发生晶体长大以消除局部过冷。
一旦凝固后又发生过冷和结晶长大,这就是凝固前沿发生的实际结晶生长
二、连铸坯的凝固过程
连铸坯铸坯的凝固过程是热量传递过程:
钢水进入结晶器边传热、边凝固、边运行。
在形成了一个液相穴很长的钢锭,而凝固是沿液相穴的固液界面在液固相温度区间把液体转变为固体把潜热释放出来的过程。
连铸坯凝固是分阶段的凝固过程:
1、钢水遇到结晶器壁形成初生坯壳;
2、带液芯的铸坯在冷却中快速凝固;
3、带液芯的铸坯在冷却中稳定生长直至完全凝固
在固液界面间刚凝固的晶体强度(1-3N/mm2)和塑性都非常小,当作用于凝固壳的热应力、鼓肚力、矫直力、摩擦力、机械力等外力超过所允许的外力值时,在固液界面就产生裂纹,这就形成了铸坯内部裂纹。
而已凝固的坯壳在二冷区接受强制冷却,由于铸坯线收缩,温度的不均匀性,坯壳鼓肚、导向段对弧形不准,固相变引起质点如(AlN)在晶界的沉淀等,容易使外壳受到外力和热负荷间歇式的突变,从而产生裂纹就是表面裂纹。
在凝固过程中中包注流对结晶器内钢水液相引起的流动和混合对铸坯凝固有重要影响:
液相上部为强制对流区,对流区高度取决于注流方式、浸入长水口类型和铸坯断面。
在液相线下部液体流动重要是坯壳、晶体下沉引起的自然对流,铸坯的鼓肚也会引起钢水的流动。
流动对铸坯结构、夹杂物上浮及溶质元素偏析有重要影响。
三、钢水凝固过程的收缩:
1、液态收缩:
由浇铸温度降到液相线温度的收缩。
2、凝固收缩:
液态钢水完全转变为固体的体积收缩它对铸坯的裂纹产生有很大影响。
对于钢一般为3-4%。
3、固态收缩:
钢坯由固相线温度冷却到室温的体积收缩一般为7-8%,它对铸坯的裂纹有重要影响
2.2、连铸坯低倍缺陷产生原因及控制方法
由以上学习我们可以知道铸坯凝固冷却及凝固过程的收缩是造成铸坯缺陷的重要原因,要得到良好的铸坯低倍组织就是缩小铸坯中的树枝晶区并扩大中心粗大等轴晶带。
在现实的生产中我们可以通过采取合理的工艺措施实现以上目的:
1、柱状晶带与粗大等轴晶带的相对大小由浇铸温度决定,控制钢水的过热度采用适宜的浇铸温度是得到粗大等轴晶带的措施之一,一般把中包钢水的过热度控制在20-30℃之间。
2、在结晶器内添加微型冷却剂如:
铁粉、小废钢等减少钢水过热度。
3、在二冷区采用弱冷适当减少水量
4、在结晶器中加入形核剂以增加结晶核来扩大等轴晶带
5、采用电磁搅拌把正在成长的树枝晶打碎从而扩大等轴晶带
2.2.1、连铸坯中心疏松产生原因及控制方法
一、铸坯疏松的定义
在铸坯的断面上存在的细小孔隙称为疏松。
分布于整个断面的孔隙称一般疏松;铸坯断面中心部位的疏松为中心疏松。
中心疏松伴有偏析、裂纹等缺陷轧制后不能完全焊合(加工图片\疏松.jpg)
二、中心疏松的产生原因及危害
中心疏松的产生是由于树枝晶过度生长碰到碰到一起造成“搭桥”现象,阻止桥上钢水向桥下钢液凝固收缩的补充,当桥下的钢水完全凝固因体积收缩后就留下许多孔隙。
若铸坯轧制时压缩比达到3-5时中心疏松可以焊合,但中心疏松引起的裂纹不能完全焊合,特别是其造成的中心偏析对产品的性能危害较大。
三、铸坯疏松的控制方法
根据钢种的需要控制合适的过热度和拉速,采用电磁搅拌和合理的二冷却制度可以促进树枝晶向等轴晶转化是减少疏松提高铸坯致密性的有效措施
2.2.2、连铸坯缩孔产生原因及控制方法
一、连铸坯缩孔的定义
在铸坯中心部位呈现的不规则的空洞
二、缩孔的产生
缩孔的产生是由于树枝晶过度生长碰到碰到一起造成“搭桥”现象,阻止桥上钢水向桥下钢液凝固收缩的补充,当桥下的钢水完全凝固因体积收缩形成空洞就形成缩孔。
(加工图片\缩孔(中包温高).jpg)
三、缩孔的控制方法
根据钢种的需要控制合适的过热度和拉速,采用电磁搅拌和二冷弱冷制度可以促进树枝晶向等轴晶转化是减少疏松提高铸坯致密性的有效措施
2.2.3、连铸坯裂纹产生原因及控制方法
目前连铸坯裂纹是影响我厂铸坯内在质量的关键因素,并且对轧钢工序造成较大影响。
一、连铸坯裂纹形态
连铸坯裂纹形态分为表面裂纹(加工图片\表面裂纹.jpg)、皮下裂纹(加工图片\皮下裂纹.jpg)内部裂纹有中间裂纹(加工图片\中间裂纹(中包温高温高).jpg)、中心裂纹(加工图片\中心裂纹.jpg)
线材表面裂纹及线材进一步加工过程中的。
在加热炉内铸坯的表面裂纹较深(≥1.5mm)会被氧化形成脱碳层,轧制过程中不能焊合形成线材缺陷造成裂纹。
皮下裂纹在轧制过程中会造成线材表面裂纹,严重的中间裂纹及中心裂纹在轧制过程中不能完全焊合会影响线材进一步的加工性能;裂纹造成的线材缺陷会导致线材加工时的:
拉拔断裂、墩裂等
二、 连铸坯裂纹的影响因素及控制措施:
连铸坯表面裂纹主要决定于钢水在结晶器的凝固过程,它是受结晶器传热、振动、润滑、钢水流动和液面稳定性所制约的,铸坯凝固过程坯壳形成裂纹, 铸坯内部裂纹的形成与铸坯鼓肚、表面回热和铸坯纸倍结构等因素有关。
从工艺设备和钢凝固特性来考虑影响裂纹形成的因素可分为:
1、连铸机设备状态方面有:
1) 结晶器冷却不均匀
2) 结晶器角部形状不当。
3) 结晶器锥度不合适。
4) 结晶器振动不良。
5) 二冷水分布不均匀(如喷淋管变形、喷咀堵塞等)特别是我厂3#、4#二冷水水质差,经常发生水嘴堵塞。
6) 支承辊对弧不准和变形。
2、工艺参数控制方面有:
1) 化学成份控制不良,含碳0.1-0.2%钢种发生包晶反应(如C、Mn/S)。
2) 钢水过热度高。
3) 结晶器液面波动太大。
液面自动检测发生故障及塞棒侵蚀严重
4) 保护渣性能不良。
5) 水口扩径拉速快。
6) 二次冷却水分配不良,铸坯表面温度回升过大。
7) 铸坯带液芯矫直。
8) 铸坯在脆性区(700~900℃)矫直。
3、钢的凝固特性方面有:
1) 凝固冷却过程的相变。
2) 铸坯凝固结构(柱状晶与等轴晶的比例)。
3) 凝固壳高温力学行为。
4) 凝固过程的偏析。
三、控制措施
铸坯裂纹的形成是传热、传质和应力相互作用的结果。
带液芯的高温铸坯在铸机内运行过程中,各种力的作用是产生裂纹的外因,而钢对裂纹的敏感性是产生裂纹的内因。
铸坯是否产生裂纹决定于钢高温力学性能、凝固冶金行为和铸机设备运行状态,如图5-23所示。
板坯中心裂纹是由于凝固末端铸坯鼓肚变形或中心偏析、中心凝固收缩产生的。
图5-23产生裂纹因素示意图
a控制铸机设备运行状态
钢的高温力学性能与铸坯裂纹有直接关系。
铸坯凝固过程固-液界面承受的应力(如热应力、鼓肚力、矫直力等)和由此产生的塑性变形超过允许的高温强度和临界应变值,则形成树枝晶间裂纹,柱状晶越发达,越有利于裂纹的扩展。
因此要减少铸坯发生裂纹的概率,就必
须使作用于铸坯上应力的总和最小,为此必须保证良好的铸机设备运行状态。
(1)确立铸机状况使用标准。
标准规定:
对弧误差<0.2mm;开口度偏差为0.2mm,最大<0.5mm;辊子磨损、弯曲变形≤0.5mm;辊子裂纹宽度<0.5mm。
(2)调整铸机传动段。
调整传动段上框架的垫片,并对扇形段弹簧的预紧力进行检查和调整,以模拟铸坯状况,避免发生鼓肚及异常压下中心裂纹。
(3)加强弯曲拉矫段的检查和维护。
辊道和框架在浇注过程中受较大的矫直力和钢水静压力的作用,容易产生位移或变形,因此对弯曲拉矫段进行特护特检,确保铸机可靠的精度值。
(4)连铸机流道质量主要包括扇形段开口度及对弧状况,在生产中,由于设备或工艺、技术方面的原因,可能会造成连铸机某处流道质量异常。
这样就可能导致以下情况:
一是造成该处铸坯产生一定程度的鼓肚,如果鼓肚发生在铸坯凝固末端附近区域,就可能造成该区域钢液不能正常补缩,即使得到补缩,也会在随后流道质量恢复正常时将残余钢液挤压出去;另一种情况则是凝固末端铸坯直接受到挤压,造成该区域钢液补缩不足。
这两种情况都会产生严重的中心偏析或中心裂纹。
b控制钢的凝固冶金行为
铸坯在凝固末期形成中心偏析、疏松和缩孔,如果此时钢水过热度过高,拉速与温度不匹配,辊子开口度扩大,就可能扩大为断续性的中心裂纹。
裂纹附近夹杂物较多,主要是硫化物沿晶界分布。
铸坯中心偏析有两种形成机理,“凝固桥”
理论是铸坯凝固过程中凝固桥的形成阻止液体补缩,形成中心缩孔和疏松,导致中心偏析;“鼓肚”理论是铸坯凝固过程中坯壳的鼓胀(如图5-24所示),造成树枝晶间富集溶质液体的流动,或者凝固末期由于铸坯收缩使凝固末端富集溶质液体流动导致中心偏析。
可见,凝固时树枝晶间富集溶质残余母液的流动是造成中心偏析的主要原因。
为减少中心疏松、缩孔和偏析,要抑制柱状晶生长,扩大中心等轴晶区和抑制液相穴末端富集溶质的残余钢液的流动。
(1)控制钢水过热度。
铸坯柱状晶发达,使材料呈各相异性,裂纹容易扩展,且易出现“搭桥”现象。
因此必须抑制柱状晶生长,扩大中心等轴晶区。
柱状晶和等轴晶区的大小决定于浇注温度,注温高,钢中气体、夹杂也高,铸坯收缩量大,相同冷却强度时坯壳薄、高温力学强度低。
另外,钢水温度高时拉速低,从而导致铸机夹辊弯曲、变形或损坏。
因此控制钢水过热度有利于减少板坯中心裂纹,理想的过热度是10~20℃。
图5-24铸坯凝固壳变形示意图
a—辊子对中不良的鼓肚;b—支撑辊间反复鼓肚
(2)控制钢水磷、硫、碳含量及锰硫比。
磷是裂纹敏感性元素,磷含量增加将显著增加磷在枝晶间的富集,枝晶间的偏析增加,容易产生裂纹;硫易形成低熔点FeS,分布在晶界,引起晶间脆性,成为裂纹扩展的路径。
而w(Mn)/w(S)高,有足够的锰与硫结合,生成MnS,以棒状形式分散在奥氏体基体中,而不易形成裂纹。
因此必须控制钢水中硫、磷含量并提高w(Mn)/w(S)。
一般要求钢水中硫、磷含量≤0.020%,w(Mn)/w(S)>30。
碳对钢种裂纹敏感性的影响也非常明显,碳含量高还会加剧磷的偏析。
碳含量应避开对裂纹敏感的包晶区范围(0.14%~0.18%)。
这是因为随着碳含量的增加,树枝状晶的显微偏析和因δ→γ的相变所造成的收缩加剧。
(3)控制和稳定拉速。
铸机的拉速高低及变化速率对铸坯的凝固壳厚度、凝固末端位置、凝固组织的构成和铸坯高温力学强度都有极大的影响。
拉速频繁变化,也会引起凝固末端位置的频繁变化,凝固末端附近凝固前沿“搭桥”的概率相应增加,最终诱发中心裂纹。
因此制定恒拉速考核奖励办法并全力推广“恒速浇铸”,保证了生产组织和工艺以及二冷供水的稳定,液相穴的变化小,有利于减少板坯中心裂纹。
(4)对铸机辊缝进行收缩。
对铸机辊缝进行收缩,形成一定的压下量,让枝晶间富集溶质的剩余液相仍保留在其原来的位置,不流到最后凝固的中心部位,减轻甚至消除中心偏析,明显降低了中心裂纹的发生率。
(5)优化冷却系统提高冷却效果。
铸坯质量对二冷水状况十分敏感,铸坯过冷将导致柱状晶发达,降低钢的高温强度;铸坯冷却不足,坯壳过薄易产生鼓肚。
铸