数控铣加工工艺.docx
《数控铣加工工艺.docx》由会员分享,可在线阅读,更多相关《数控铣加工工艺.docx(11页珍藏版)》请在冰豆网上搜索。
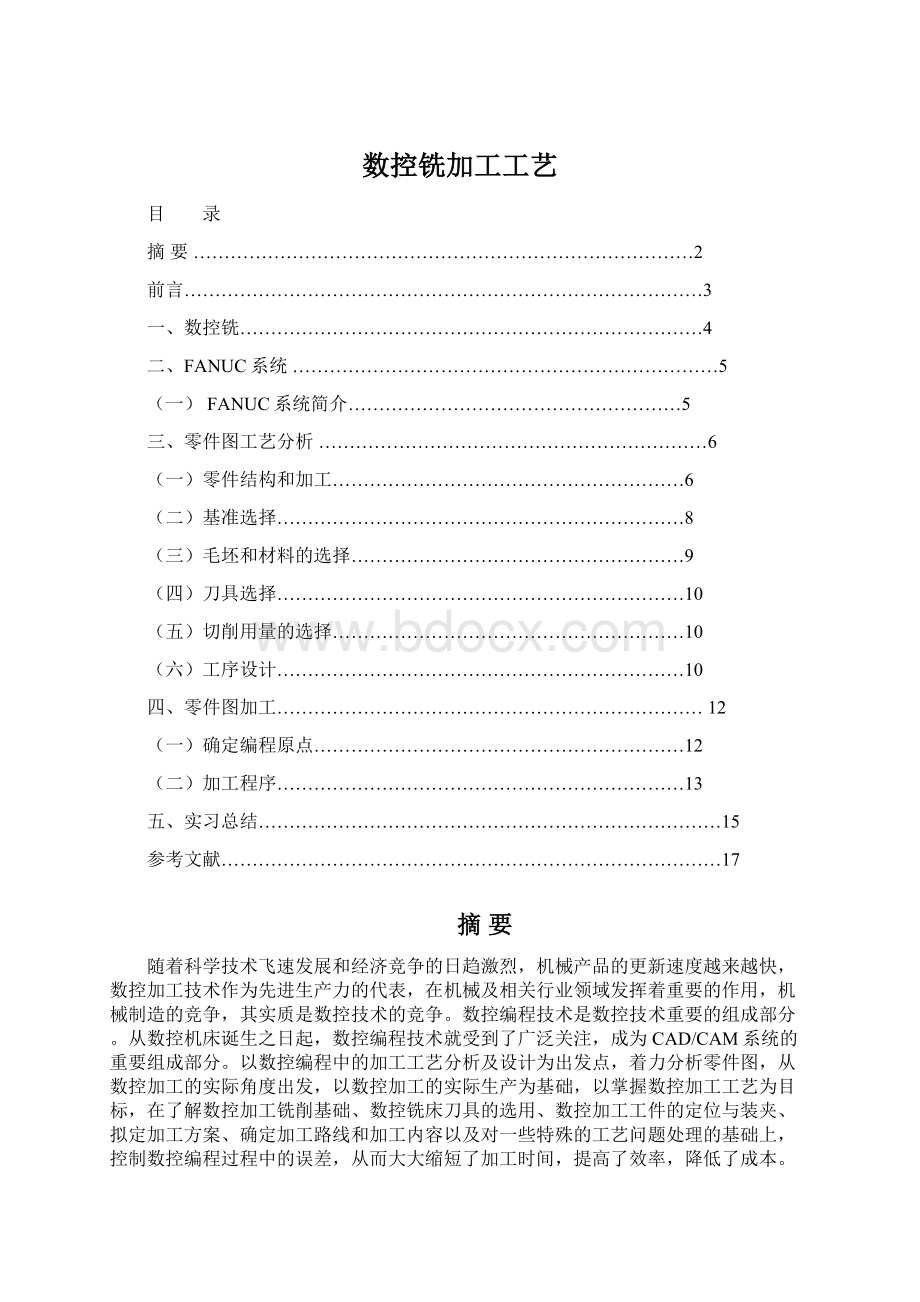
数控铣加工工艺
目 录
摘要………………………………………………………………………2
前言…………………………………………………………………………3
一、数控铣…………………………………………………………………4
二、FANUC系统……………………………………………………………5
(一)FANUC系统简介………………………………………………5
三、零件图工艺分析………………………………………………………6
(一)零件结构和加工…………………………………………………6
(二)基准选择…………………………………………………………8
(三)毛坯和材料的选择………………………………………………9
(四)刀具选择…………………………………………………………10
(五)切削用量的选择…………………………………………………10
(六)工序设计…………………………………………………………10
四、零件图加工……………………………………………………………12
(一)确定编程原点……………………………………………………12
(二)加工程序…………………………………………………………13
五、实习总结…………………………………………………………………15
参考文献………………………………………………………………………17
摘要
随着科学技术飞速发展和经济竞争的日趋激烈,机械产品的更新速度越来越快,数控加工技术作为先进生产力的代表,在机械及相关行业领域发挥着重要的作用,机械制造的竞争,其实质是数控技术的竞争。
数控编程技术是数控技术重要的组成部分。
从数控机床诞生之日起,数控编程技术就受到了广泛关注,成为CAD/CAM系统的重要组成部分。
以数控编程中的加工工艺分析及设计为出发点,着力分析零件图,从数控加工的实际角度出发,以数控加工的实际生产为基础,以掌握数控加工工艺为目标,在了解数控加工铣削基础、数控铣床刀具的选用、数控加工工件的定位与装夹、拟定加工方案、确定加工路线和加工内容以及对一些特殊的工艺问题处理的基础上,控制数控编程过程中的误差,从而大大缩短了加工时间,提高了效率,降低了成本。
本文主要研究了轮廓和孔的数控铣削工艺、工装以及在此基础上的数控铣床的程序编制。
侧重于设计该零件的数控加工夹具,主要设计内容有:
完成该零件的工艺规程(包括工艺简卡、工序卡和数控刀具卡)和主要工序的工装设计。
并绘制零件图。
用G代码编制该零件的数控加工程序。
关键词:
FANUC、数控加工、数控编程
前言
2015年3月份我来到了深圳市明星盛塑胶制品有限公司参加实习。
深圳市明星盛塑胶制品有限公司是一家是专业生产销售吹膜、PE袋子、OPP袋子,复合袋,铝箔袋,茶叶袋,咖啡袋,精美印刷,性价比行业第一。
手机防水袋、布丁袋、透明色、红色、绿色、蓝色、黑色各种颜色各种规格的加厚汽泡袋....等。
实习期间我主要从事印刷生产工作。
一、数控铣
数控铣或手动铣是用来加工棱柱形零件的机加工工艺。
有一个旋转的圆柱形刀头和多个出屑槽的铣刀通常称为端铣刀或立铣刀,可沿不同的轴运动,用来加工狭长空、沟槽、外轮廓等。
进行铣削加工的机床称为铣床,数控铣床通常是指数控加工中心。
铣削加工包括手动铣和数控铣,铣削加工在机加工车间进行。
数控铣床引是在一般铣床的基础上发展起来的,两者的加工工艺基本相同,结构也有些相似,但数控铣床是靠程序控制的自动加工机床,所以其结构也与普通铣床有很大区别
二、FANUC系统
(一)FANUC数控加工系统简介
FANUC公司创建于1956年,1959年首先推出了电液步进电机,在后来的若干年中逐步发展并完善了以硬件为主的开环数控系统。
进入70年代,微电子技术、功率电子技术,尤其是计算技术得到了飞速发展,FANUC公司毅然舍弃了使其发家的电液步进电机数控产品,一方面从GETTES公司引进直流伺服电机制造技术。
1976年FANUC公司研制成功数控系统5,随时后又与SIEMENS公司联合研制了具有先进水平的数控系统7,从这时起,FANUC公司逐步发展成为世界上最大的专业数控系统生产厂家,产品日新月异,年年翻新。
1979年研制出数控系统6,它是具备一般功能和部分高级功能的中档CNC系统,6M适合于铣床和加工中心;6T适合于车床。
与过去机型比较,使用了大容量磁泡存储器,专用于大规模集成电路,元件总数减少了30%。
它还备有用户自己制作的特有变量型子程序的用户宏程序。
1980年在系统6的基础上同时向抵挡和高档两个方向发展,研制了系统3和系统9。
系统3是在系统6的基础上简化而形成的,体积小,成本低,容易组成机电一体化系统,适用于小型、廉价的机床。
系统9是在系统6的基础上强化而形成的具备有高级性能的可变软件型CNC系统。
通过变换软件可适应任何不同用途,尤其适合于加工复杂而昂贵的航空部件、要求高度可靠的多轴联动重型数控机床。
1984年FANUC公司又推出新型系列产品数控10系统、11系统和12系统。
该系列产品在硬件方面做了较大改进,凡是能够集成的都作成大规模集成电路,其中包含了8000个门电路的专用大规模集成电路芯片有3种,其引出脚竟多达179个,另外的专用大规模集成电路芯片有4种,厚膜电路芯片22种;还有32位的高速处理器、4兆比特的磁泡存储器等,元件数比前期同类产品又减少30%。
由于该系列采用了光导纤维技术,使过去在数控装置与机床以及控制面板之间的几百根电缆大幅度减少,提高了抗干扰性和可靠性。
该系统在DNC方面能够实现主计算机与机床、工作台、机械手、搬运车等之间的各类数据的双向传送。
它的PLC装置使用了独特的无触点、无极性输出和大电流、高电压输出电路,能促使强电柜的半导体化。
此外PLC的编程不仅可以使用梯形图语言,还可以使用PASCAL语言,便于用户自己开发软件。
数控系统10、11、12还充实了专用宏功能、自动计划功能、自动刀具补偿功能、刀具寿命管理、彩色图形显示CRT等。
1985年FANUC公司又推出了数控系统0,它的目标是体积小、价格代,适用于机电一体化的小型机床,因此它与适用于中、大型的系统10、11、12一起组成了这一时期的全新系列产品。
在硬件组成以最少的元件数量发挥最高的效能为宗旨,采用了最新型高速高集成度处理器,共有专用大规模集成电路芯片6种,其中4种为低功耗CMOS专用大规模集成电路,专用的厚膜电路3种。
三轴控制系统的主控制电路包括输入、输出接口、PMC(ProgrammableMachineControl)和CRT电路等都在一块大型印制电路板上,与操作面板CRT组成一体。
系统0的主要特点有:
彩色图形显示、会话菜单式编程、专用宏功能、多种语言(汉、德、法)显示、目录返回功能等。
FANUC公司推出数控系统0以来,得到了各国用户的高度评价,成为世界范围内用户最多的数控系统之一。
三、零件图工艺分析
(一)零件结构和加工工艺要求分析
图3-1
零件的尺寸标注图图3-1所示,此零件的端面及外轮廓的粗糙度是3.2,加工过的端面粗糙度是6.3,矩形槽设置的极限偏差为0~+0.052mm,半圆形槽的极限偏差设置为0~+0.043mm,同一基准标注方法以同一基准引注尺寸或直接给出坐标尺寸,它适应数控铣床加工的特点,即便与编程,也便于保持设计工艺,测量基准与编程原点设置的一致性。
由于加工程序是以准确的坐标点来编制的,因此,构成零件轮廓的几何元素(点,线,面)的相互关系(如相切,相交,垂直和平行等)应明确,各种几何要素的条件要充分,应无引起矛盾的多余尺寸或影响工序安排的封闭尺寸,尺寸的标注应方便编程等。
保证零件的加工精度要特别注意:
过薄的底板的厚度公差,由于加工时产生的切削力及薄板的弹性变形易使切削面发生震动,薄板的厚度尺寸公差难以得到保证,薄棉粗糙度值也将增大。
对于面积较大的薄板,当厚度小于3mm时,应在工艺上充分重视。
零件的结构工艺性是指所设计的零件在满足使用要求的前提下制造的可行性和经济性。
良好的结构工艺性可使零件加工容易,节省工时和材料。
较差的结构工艺性,会使零件加工困难,浪费工时和材料,有时甚至会使零件无法加工。
(1)工件的内腔与外形应尽量采用统一的几何类型和尺寸,以减少刀具规格和换刀次数,方便编程和提高数控机床加工效率。
(2)工件内槽的圆角半径R不应过小。
圆角半径限制了刀具直径的大小,刀具直径与工件轮廓的深度之比又决定了刀具的刚度,如果刀具半径R<0.2H(H为工件轮廓的深度),则判定工件该部位加工工艺性差,如果R>0.2H时,则判定工件该部位的加工工艺性良好,工件的加工质量能得到保证。
(3)工件槽底的圆角半径r不宜过大。
铣刀端面刃与铣削平面的最大接触直径d=D-2r(D为铣削直径),当D一定时,r越大,铣刀的端面刃铣削平面的面积越小,加工平面的能力就越差,效率越低,工艺性越差。
当r大到一定程度时甚至必须用球头铣刀加工,这是应当避免的。
(4)应采用统一的基准定位
数控铣削加工中若没有统一的定位基准,则会产生因工件二次装夹而造成的加工后两个面上的轮廓,位置及尺寸不协调现象。
例如,有些零件需要在铣完一面后两次装夹铣另一面,由于数控铣削时不能使用通用铣床加工时常用的试切法来接切,这时最好采用统一基准定位,因此零件上应有合适的的孔作为定位基准。
如果没有基准孔。
则应专门设置工艺孔作为定位基准。
若无法制出工艺孔,也应用加工表面作为统一基准,以减少二次装夹产生的误差。
(5)该槽轮板的零件图工艺分析:
槽轮板是由平面,外轮廓以及孔系组成,几何元素之间关系描述清晰,完整,槽轮板侧面与矩形槽,半圆形槽内侧表面粗糙度值要求较小,为Ra3.2um。
该半圆形槽相对于中心线有对称度的要求,零件材料为45钢,切削加工性能较好,台阶面粗糙度值Ra3.6。
根据上述分析,槽轮板内,外轮廓及半圆型槽,矩形槽应分,粗,精加工两个阶段进行,以保证表面粗糙度值要求。
同时以零件的A和B定位,提高装夹刚度以满足垂直度和对称度的要求。
确定装夹方案,根据零件的结构特点,加工两个槽时,以A和B定位(必要时可设工艺孔),采用螺旋压板机构夹紧。
以A和B定位基准。
(二)基准的选择
粗基准选择应当满足以下要求:
(1)粗基准的选择应以加工表面为粗基准。
目的是为了保证加工面与不加工面的相互位置关系精度。
如果工件上表面上有好几个不需加工的表面,则应选择其中与加工表面的相互位置精度要求较高的表面作为粗基准。
以求壁厚均匀、外形对称、少装夹等。
(2)选择加工余量要求均匀的重要表面作为粗基准。
例如:
机床床身导轨面是其余量要求均匀的重要表面。
因而在加工时选择导轨面作为粗基准,加工床身的底面,再以底面作为精基准加工导轨面。
这样就能保证均匀地去掉较少的余量,使表层保留而细致的组织,以增加耐磨性。
(3)应选择加工余量最小的表面作为粗基准。
可以保证该面有足够的加工余量。
(4)应尽可能选择平整、光洁、面积足够大的表面作为粗基准,以保证定位准确夹紧可靠。
有浇口、冒口、飞边、毛刺的表面不宜选作粗基准,必要时需经初加工。
(5)粗基准应避免重复使用,因为粗基准的表面大多数是粗糙不规则的。
多次使用难以保证表面间的位置精度。
为了满足上述要求,基准选择以后钢板弹簧吊耳大外圆端面作为粗基准,先以后钢板弹簧吊耳大外圆端面互为基准加工出端面,再以端面定位加工出工艺孔。
在后续工序中除个别工序外均用端面和工艺孔定位加工其他孔与平面。
精基准的选择主要考虑基准重合的问题,当设计基准与工序基准不重合时,应当进行尺寸换算。
(三)毛坯和材料的选择
毛胚的设定,为了更快的加工出零件来,在选择毛胚的时候,应该尽量接近零件的基本尺寸,这样就可以节省加工时间和减少加工余量。
在这里选择毛胚是45钢,规格为:
长100mm宽为100mm高为25mm的长方体毛胚,示意图如下:
图3-2零件的正视图
此毛胚的未经过任何加工,表面的粗糙度比较差,要选择一个平面先进行面铣,再以这个平面作为基准平面。
现代机械加工的发展趋势之一,是通过毛胚精化使毛胚的形状和尺寸与零件接近,减少机械加工的劳动量,力求实现少、无切屑加工。
毛胚形状主要取决于毛胚种类、零形状和各种加工表面的总余量。
在本次的毕业设计零件中由于材料的限制,所以没有精化的零件毛胚。
(四)刀具选择
在本次的零件加工中所需要用到的刀具有立铣刀、中心钻、钻头等。
刀具的合理选用可以对零件的加工精度产生影响,为了让工件的精度达到要求,通过选择合理的刀具无疑是一种好方法。
为保证加工质量,工件在粗加工时切除金属较多,切削力、装夹力大,切削热量多,加工后应力要重新分布,由此而引起的工件变形较大,需要通过半精加工和精加工来纠正。
刀具的选择是数控加工工艺内容中重要内容之一,它不仅影响机床的加工效率,而且影响零件的加工质量。
所以在编程时,选择刀具通常是要考虑机床的加工能力、工序内容、零件的材料等。
为了减少加工时间,这里采用工序集中,一把刀具的加工内容尽量在一次性的加工完,这不仅可以提高生产效率,还可以减轻劳动强度。
(五)切削用量选择
切削用量包括主轴转速(切削速度)、切削深度或宽度、进给速度(进给量)等。
切削用量的大小对切削力、切削速率、刀具磨损、加工质量和加工成本均有显著影响。
对于不同的加工方法,需选择不同的切削用量,并应编入程序单内。
合理选择切削用量的原则是:
粗加工时,一般以提高生产率为主,但也考虑经济性和加工成本;半精加工或精加工时,应在保证加工质量的前提下,兼顾切削效率、经济性和加工成本。
具体数值应根据机床说明书、切削用量手册,并结合经验而定。
(六)工序设计
工序的划分:
根据数控机床的加工特点,加工工序的划分有以下几种方式:
(1)按装夹定位划分工序
(2)按所用刀具划分工序
(3)按粗、精加工划分工序
(4)按加工部位划分工序
粗铣,半精铣和精铣时使用同一加工程序,只需调整刀具参数,分三次调用相同的程序进行加工即可。
精加工时换直径20毫米和直径12毫米的精立铣刀。
粗铣圆柱外轮廓和凹圆弧粗铣圆柱外轮廓,留0.50mm的单边余量;粗铣4×直径30毫米凹圆弧,留0.50毫米的单边余量。
半精铣,精铣圆柱外轮廓和凹圆弧,安装直径20毫米精立铣刀对刀设定刀具参数,半精铣圆柱外轮廓和凹圆弧,留0.10毫米的单边余量。
实测工件尺寸,调整刀具参数,精铣圆柱外轮廓和凹圆弧至要求尺寸。
(5)铣半圆形槽
安装直径12毫米粗立铣刀并对刀,设定刀具,参数选择程序,粗铣各槽留0.50毫米单边余量。
安装直径12毫米精立铣刀并对刀,设定刀具参数,半精铣各槽留0.10单边余量。
实测工件尺寸,调整刀具参数,精铣各半圆形槽主要尺寸。
(6)铣矩形槽
安装直径为12毫米的键槽铣刀并对刀,设定刀具参数,选择程序,粗铣矩形槽,留0.50毫米单边余量。
安装直径为12毫米的精立铣刀并对刀,设定刀具参数,半精铣,矩形槽,留0.10毫米的单边余量。
实测矩形槽的尺寸,调整刀具参数,精铣矩形槽至要求尺寸。
(7)加工顺序的安排
数控铣削和加工中心,加工顺序的安排同样要遵循“基准先行,先粗后精,先主后次,先面后孔”的一般工艺原则。
在零件图样和实际零件上,总要依据一些一些指定的点、线、面来确定另外一些点、线、面的位置。
这些作为依据的点、线、面就是称为基准。
根据基准的功用的不同,它可分为设计基准和工艺基准两大类。
四、零件图加工
(一)确定编程原点
铣床上编程坐标原点的位置是任意的,他是编程人员在编制程序时根据零件的特点来选定的,为了变成方便,一般要根据工件形状和标注尺寸的基准以及计算最方便的原则来确定的工件上某一点为坐标原点,具体选择注意如下几点:
(1)编程坐标原点应选在零件图的尺寸基准上,这样便于坐标值的计算,并减少计算错误。
(2)编程坐标原点应尽量选在精度较高的精度表面,以提高被加工零件的加工精度。
(3)对称的零件,编程坐标原点应设在对称中心上;不对称的零件,编程坐标原点应设在外轮廓的某一角上。
(4)Z轴方向的零点一般设在工件表面。
(二)加工程序
N010G92X0Y0Z20
N020M06T01换直径18铣刀
N030G0G90X71.129Y1.286M03S800
N040G43H01Z5.1号刀,长度补偿
N050Z2.54
N060G1Z0.0F250.M08
N070G41X69.895Y3.46H011号刀,左偏刀具补偿
N080G3X64.5Y6.I-5.395J-4.46切入
N090G1X62.
N100X45.
N110G2X35.Y16.I0.0J10.R10圆弧
N120G1Y20.
N130G3X25.Y30.I-10.J0.0R10圆弧
N140G1X11.
N150X6.Y40.
N160Y60.
N170X11.Y70.
N180X25.
N190G3X35.Y80.I0.0J10.R10圆弧
N200G1Y84.
N210G2X45.Y94.I10.J0.0R10圆弧
N220G1X79.
N230G2X94.Y79.I0.0J-15.R15圆弧
N240G1Y21.
N250G2X79.Y6.I-15.J0.0R10圆弧
N260G1X59.5
N270G3X54.105Y3.46I0.0J-7.
N280G40G1X52.871Y1.286
N290G0Z5.M05
N300Z20
N310M06T02换直径22铣刀
N320X77.286Y52.371M03
N330G43H02Z5.2号刀,长度补偿
N340Z2.54
N350G1Z0.0F250.
N360G41X79.46Y53.605H022号刀,左偏刀具补偿
N370G3X82.Y59.I-4.46J5.395S600
N380G1Y61.5
N390Y73.
N400G3X70.Y85.I-12.J0.0R12圆弧
N410G1X54.
N420G3X42.Y73.I0.0J-12.R12圆弧
N430G1Y27.
N440G3X54.Y15.I12.J0.0R12圆弧
N450G1X70.
N460G3X82.Y27.I0.0J12.R12圆弧
N470G1Y64.
N480G3X79.46Y69.395I-7.J0.0退刀
N490G40G1X77.286Y70.629
N500G0Z5.
N510X78.557Y47.989
N520Z5.M05
N530Z20
N540M06T03换直径6铣刀
N550G43Z5H03M03S10003号刀,长度补偿
N560Z-2.46
N570G1Z-5.F250.
N580G41X79.222Y50.399H033号刀,左偏刀具补偿
N590G3X77.203Y56.01I-6.969J.662
N600G1X75.435Y57.778
N610X67.657Y65.556
N620G3X56.343I-5.657J-5.657R8圆弧
N630G1X46.444Y55.657
N640G3Y44.343I5.657J-5.657R8圆弧
N650G1X56.343Y34.444
N660G3X67.657I5.657J5.657R8圆弧
N670G1X83.213Y50.
N680X73.667Y59.546
N690G3X68.056Y61.565I-4.949J-4.95
N700G40G1X65.646Y60.9
N710G0Z5.
N720G00Z20
N730M05
N740X0Y0
N750M30