6汽油调和过程集散控制系统中的监控部分设计.docx
《6汽油调和过程集散控制系统中的监控部分设计.docx》由会员分享,可在线阅读,更多相关《6汽油调和过程集散控制系统中的监控部分设计.docx(21页珍藏版)》请在冰豆网上搜索。
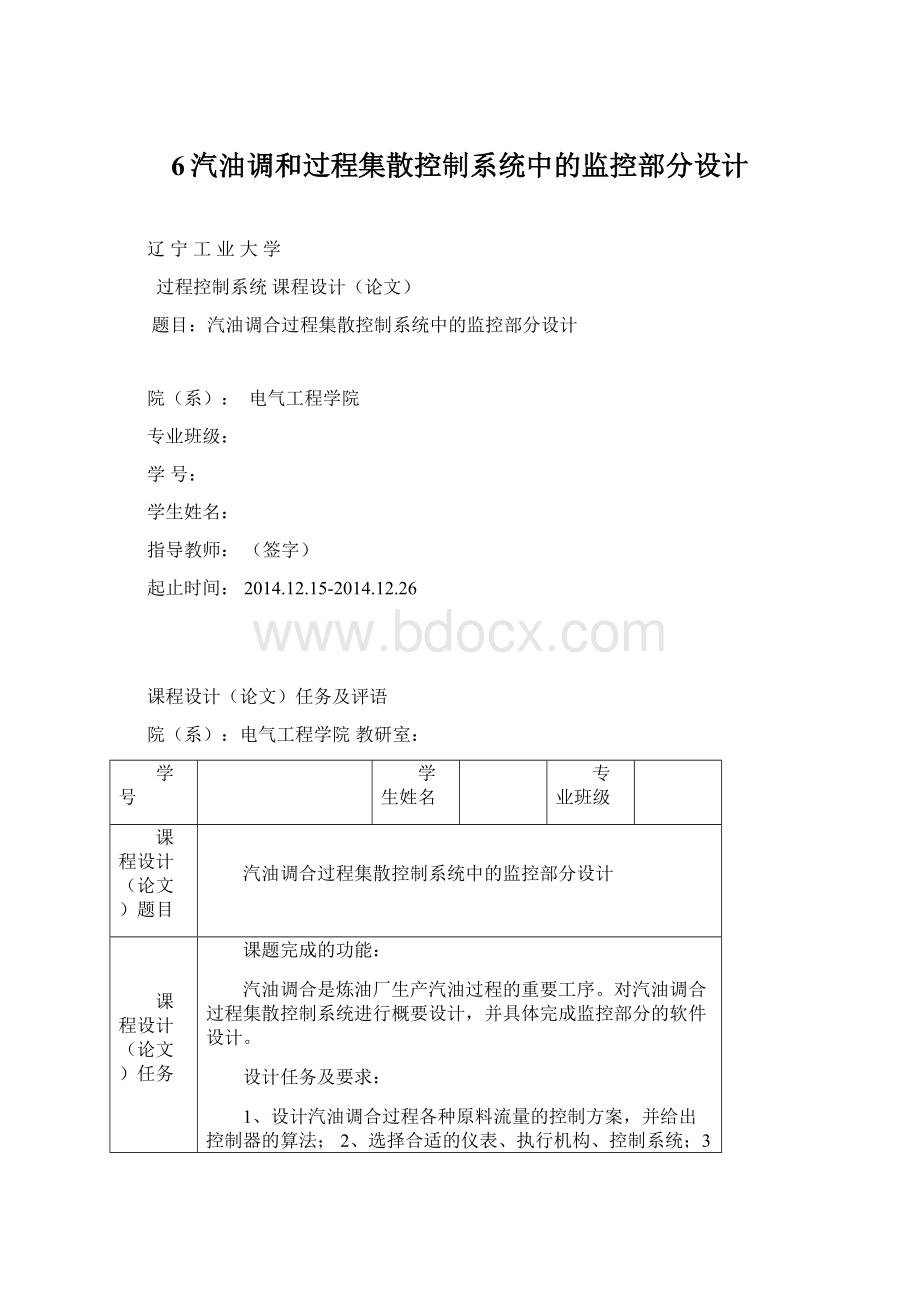
6汽油调和过程集散控制系统中的监控部分设计
辽宁工业大学
过程控制系统课程设计(论文)
题目:
汽油调合过程集散控制系统中的监控部分设计
院(系):
电气工程学院
专业班级:
学号:
学生姓名:
指导教师:
(签字)
起止时间:
2014.12.15-2014.12.26
课程设计(论文)任务及评语
院(系):
电气工程学院教研室:
学号
学生姓名
专业班级
课程设计(论文)题目
汽油调合过程集散控制系统中的监控部分设计
课程设计(论文)任务
课题完成的功能:
汽油调合是炼油厂生产汽油过程的重要工序。
对汽油调合过程集散控制系统进行概要设计,并具体完成监控部分的软件设计。
设计任务及要求:
1、设计汽油调合过程各种原料流量的控制方案,并给出控制器的算法;2、选择合适的仪表、执行机构、控制系统;3、控制系统要求采用浙大中控JX-300XP系统;4、完成监控软件的开发,包括分组画面、一览画面、趋势画面、总貌画面。
技术参数:
1、各种原料的流量范围为0-150t/h;
2、交流电动机的额定功率35Kw,额定电压380V,额定电流15A,额定转速1450rpm。
进度
计划
1、熟悉课程设计题目,查找及收集相关书籍、资料(2天);2、设计系统的结构原理图(1天);
3、仪表、控制系统等设备的选型(1天);4、控制方案设计及实现(4天);5、撰写课设论文(1.5天);
6、设计结果考核(0.5天);
指导教师评语及成绩
平时:
论文质量:
答辩:
总成绩:
指导教师签字:
年月日
注:
成绩:
平时20%论文质量60%答辩20%以百分制计算
摘要
本文旨在设计一个汽油调合过程集散控制系统中的监控部分。
将汽油调合与集散控制监控相结合的设计内容。
本课题采用了浙大中控JX-300XPDCS为控制系统,采用PID控制算法,通过采用8路MicroMotion高精度质量流量计和北京英贤公司的在线近红外分析仪NIR26000完成整个控制过程,同时使用管道调合来完成汽油调合。
最后由浙大中控系统的SCkey组态控制编辑器开发监控画面的设计。
本设计针对监控画面设计开发包括分组画面、一览画面、趋势画面、总貌画面,有效地提高了油品调合的自动化程度,反映了现场情况,可以取得了很好的效果。
关键词:
汽油调合;PID控制算法;近红外线分析仪;监控画面
目录
第1章绪论1
第2章汽油调合集散控制设计的方案4
2.1调合工艺流程4
2.2系统组成总体结构5
2.3汽油调合的PID控制与控制方式6
2.4常规调合控制8
第3章硬件设计及选型9
3.1调合检测系统选型9
3.2硬件控制执行系统选型9
第4章软件设计13
4.1系统硬件组态设计13
4.2系统画面组态开发17
第5章课程设计总结20
参考文献21
第1章绪论
汽油调合是炼油厂将生产的多种汽油组分,按照某种比例配方和添加剂均匀混合得到符合质量标准的汽油产品的过程,是汽油成品出厂的最后一道工序,也是保证汽油质量指标满足环保和使用要求的重要手段。
尽管炼油行业发展快速,无论是生产技术和生产规模都有了长足的进步,包括应用DCS,采用各种不同层次、深度的局部优化和先进控制技术(APC)以及全厂一体化的管理控制信息系统等,使得整个生产控制和管理具有较高的水平。
但由于汽油调合与炼制过程工艺相比相对简单,加上过去对高标号汽油的需求不大和环保的质量指标要求不严格,因此,汽油调合生产普遍没有引起炼油厂的足够重视,调合的控制系统相对简单和技术落后。
随着清洁汽油燃料生产的要求越来越严格,炼油行业正面临严峻的压力和挑战:
一是进口燃油增多,竟争激烈,炼油厂利润空间变小;二是环保压力增大,汽车排放指标不断提高;三是国内轿车的数量迅速增加对高标号汽油的需求量越来越大,而高品质汽油必须经过调合才能达到相应的使用性能指标。
同时,汽油调合方法主要有罐调合和管道调合两种。
罐调合的优点是工艺流程简单,最大缺点是调合周期长、所需罐容大、能耗高和一次调合合格率低。
而且由于调合配比比较保守、检测手段落后,致多项质量指标难以同时得到满足,辛烷值指标过剩较严重,降低炼油企业的经济效益。
管道调合是一种较为先进的调合方式,可以克服罐调合的缺点,减少重调次数,节省资源,但实施费用相对昂贵,汽油质量分析和优化软件的推广应用还存在较大难度。
随着国家对汽油质量指标和环保指标的不断提高,对汽油调合的工艺要求有了进一步的提升,炼油企业和相关研究单位开始重视汽油调合以及优化控制技术。
所以,本次设计为了生产更多符合环保和使用要求的高品质汽油,降低汽油生产成本,提高竞争力,越来越多的炼油厂开始重视汽油调合自动控制,并把它作为增加经济效益的关键所在
最初的工业过程控制是通过单元组合仪表采用原始分散控制,各控制回路相互独立,其优点是某一控制回路出现故障时,不影响其它回路的正常工作,缺点是硬件过多,自动化程度不高,难以实现整个系统的最优控制。
随后出现集中控制,它是通过计算机将控制回路的运算、控制及显示等功能集于一身,其优点是硬件成本较低,便于信息的采集和分析,易实现系统的最优控制,缺点是危险集中,局部出现故障会影响整体。
鉴于以上原因,
人们开始研究集中分散控制,随着控制技术、计算机技术、通信技术、图像显示技术的发展,70年代中期吸收原始分散控制和集中控制两者优点,克服其缺点的集中分散控制系统诞生了。
集散控制系统发展的三个阶段:
初始阶段,1975年美国霍尼韦尔公司第1套TDC-2000集散控制系统问世不久,世界各国仪表制造商就相继推出了自己的集散控制系统,即第1代集散控制系统,比较著名的有:
霍尼韦尔公司的TDC-2000;FOXBORO公司的SPECTRUM;FISHER公司的PROVOX;横河公司的CENTUM;西门子公司的TELEPERM等。
这些产品虽只是集散控制系统的雏形,但已经拥有集散控制系统的基本结构:
分散过程控制装置,操作管理装置和通讯系统。
并已具备了集散控制系统的基本特点:
集中管理,分散控制。
发展阶段:
随着控制技术、计算机技术、半导体技术、网络技术和软件技术等的飞速发展,集散控制系统进入第2代。
主要产品有:
霍尼韦尔公司的TDC-3000;TAYLOR公司的MOD300;西屋公司的WDPF,横河公司的CENTUM-XL,ABB公司的MASTER等。
第2代集散控制系统的主要特点是系统功能的扩大和增强以及通信范围和数据传送速率的大幅提高。
它采用横块化、标准化设计,数据通信向标准化靠拢,控制功能更加完善,具有很强的适应性和可扩充性。
成熟阶段:
1987年美国FOXBORO公司推出的1/AS系统标志着集散控制系统进入了第3代。
主要产品有:
霍尼韦尔公司带有UCN网的TDC-3000;横河公司带有SV-NET网的CEN-TUM-XL,BALLEY公司的INFO-90等。
第3代集散控制系统的主要改变是在局域网络方面。
它通过采用MAP等协议,使各不同制造商的产品可以相互连接、相互通信和进行数据交换,同时,第3方应用软件可方便应用,也为用户提供了更广阔的应用空间集散控制系统的特点:
分级递阶控制。
集散控制系统是分级递阶控制系统,它的规模越大,系统重直和水平分级的范围也越广。
最简单的集散控制系统至少在垂直方向分为操作管理级和过程控制级,水平方向各过程控制级之间相互协调,向垂直方向送数据,接受指令,各水平级间也进行数据交换。
分散控制是集散控制系统的一个重要特点。
分散的含义不单是分散控制,还包括人员地域的分散、功能分散、设备分散、负荷分散、危险分散。
目的是危险分散,提高设备使用率。
功能齐全,可完成简单回路调节、复杂多变量模型优化控制,可执行PID控制算法、前馈-反馈复合调节、史密斯预估、预测控制、自适应控制等各种运算,可进行反馈控制,也可进行间断顺序控制、批量控制、逻辑控制、数据采集,可实现监控、显示、打印、输出、报警、历史趋势贮存等各种操作要求。
易操作性。
集散控制系统根据对宜人学的研究,结合系统组态、结构方向的知识,为操作工提供了一个非常好的操作环境。
为操作员提供的数据、状态等信息易于辨认,报警或事件发生的信息能引起操作员的注意,长时间工作不易疲劳,操作方便、快捷。
安全可靠性高。
为了提高系统的可靠性,确保生产持续运行,集散控制系统在重要设备和对全系统有影响的公共设备上采用了后备冗余装置,并引入容错技术。
硬件上包括操作站、控制站、通讯线路等都采用双重化配置,使得在某一个单元发生故障的情况下,仍然保持系统的完整性,即使全局性通信或管理失效,局部站仍能维持工作。
从软件上采用分段与模块化设计,积木式结构,采用程序卷回或指令复执的容错设计,使系统安全稳定。
采用局部网络通信技术和标准化通信协议。
已经采用的国际通信标准有IEEE802、PROWAY和MAP等,这些协议的标准化是集散系统成为开放系统的根本。
集散控制系统的开放使各不同制造厂的应用软件有了可移植性,系统间可以进行数据通信,为用户提供广阔的应用场所。
信息存储容量大,显示信息量大,有极强的管理能力,可实现生产过程自动化,工厂自动化、实验室自动化、办公室自动化等目标。
适用于化工生产控制,有良好的性能价格比,不但其硬件适应化工控制,而且软件的适应性也稳定,随着系统开放第三方的应用软件也可方便应用。
第2章汽油调合集散控制设计的方案
调合工艺流程
汽油产品调节器合是把两种或两种以上基础组份油或各种添加剂按比例均匀混合而成为一种新产品的过程。
如汽油、柴油、润滑油等的调合以及原油调合。
目前调合工艺主要有两种方式:
即罐式搅拌混合调配或管道自动调合。
罐式搅拌混合调配是把待混合的各组份油、添加剂等按所规定的调合比例分别送入调合罐内,再用泵循环、电动搅拌或风搅拌等方法将它们均匀混合成为产品。
这种方法不仅要占用大量的中间组份油罐、调合罐,而且调合时间长,油品损耗多,能源消耗大,最重要的是质量不能得到保证。
此外,成品油久存也会使其质量劣化。
管道自动调合是采用控制仪表或专用控制系统控制各个被调组份的流量,或采用先进的在线成份分析仪表控制调合成品的质量指标,各组份油在管线中并经静态混合器混流均匀达到自动调合的目的。
这种方法能够连续生产,调合时间短,物料损失少,节省能源,调节比例精确,是当各炼油厂普遍采用的方法,同时采用浙大中控进行控制完成汽油在线调合监控设计。
根据此炼油装置的工艺技术路线和国内外汽油调合优化的成功方案,调合工艺采用2个静态混合器(调合头)的管道调合技术,装置既能调合来自炼油装备引入的组分汽油(静态)。
参与调合的组分油有蜡催汽油、重催汽油、重整汽油、脱苯汽油、芳烃抽余油、MTBE(甲基叔丁基醚)和精制油等,生产高标号汽油常用MMT(甲基环戊二烯三羰基锰)作添加剂。
组分油和添加剂经过管道调合装置分别调合出93号、97号和98号汽油。
每一路调合管道设高精度的质量流量计作瞬时流量和累积流量的测量,在线NIR分析仪对组分油和调合后的汽油性质进行检测,检测的主要指标包括辛烷值(RON,MON)、密度、蒸汽压、烯烃含量、芳烃含量、苯含量和氧含量等。
工艺简要流程如图2.1所示
图2.1工艺流程图
系统组成总体结构
汽油在线调合系统包括在线调合控制系统、DCS、近红外分析仪、现场总线、调合头等,主要功能根据手动输入的组分配方案以及现场采集到的油品分析数据等信息完成调合步骤,使得调合好的汽油满足要求,质量过剩最小,罐区罐存的合理分配及罐区生产的自动化,产生最大可能的效益。
调合时所需要完成的泵、阀等的启动和停止动作由DCS系统根据调合服务器的给定自动完成,调合服务器与DCS系统通过开放的OPC接口实现数据传输通讯方式给DCS数据传输。
系统构成如图2.2所示。
图2.2汽油调合系统结构图
汽油调合的PID控制与控制方式
在闭环控制系统中,控制器是系统的核心,其控制算法决定了系统的控制特性和控制效果。
本实验采用模拟PID控制。
PID控制是指将被控量的检测信号(及传感器测
实际值)与被控变量的目标信号(即设定值)进行比较,以判断是否已经达到预定的控制目标。
如果未达到,则根据两者的差值进行调整,直到达到预定的控制目标为止。
PID控制是利用PI控制和PD控制的有点组合而成的控制,是P、I和D三个运算的总和。
在过程控制中,按偏差的比例(P)、积分(I)和微分(D)进行控制的PID控制器(亦称PID调节器)是应用最为广泛的一种自动控制器。
它具有原理简单,易于实现,适用面广,控制参数相互独立,参数的选定比较简单等优点;而且在理论上可以证明,对于过程控制的典型对象──“一阶滞后+纯滞后”与“二阶滞后+纯滞后”的控制对象,PID控制器是一种最优控制。
PID调节规律是连续系统动态品质校正的一种有效方法,它的参数整定方式简便,结构改变灵活控制器的参数整定。
PID控制算法有三种:
增量算法,位置算法,速度算法。
从应用利弊上来看,采用增量算法和速度算法时,手自动切换都很方便,它们可从手动时的
出发,直接计算出再投入自动运行时应采取的乘凉
或变化速度
,同时,这两类算法不会引起积分饱和现象。
增量算法:
(4.1)
(4.2)
速度算法:
增量输出与采样周期之比:
(4.3)
其中,
(4.4)
本实验采用的是PI控制,增量算法:
(4.5)
(4.6)
比例(P)、积分(I)、微分(D)控制算法各有作用:
比例,反应系统的基本(当前)偏差
,系数大,可以加快调节,减小
差,但过大的比例使系统稳定性下降,甚至造成系统不稳定;
积分,反应系统的累计偏差,使系统消除稳态误差,提高无差度,因为有误差,积分调节就进行,直至无误差;
微分,反映系统偏差信号的变化率
,具有预见性,能预见偏差变化的趋势,产生超前的控制作用,在偏差还没有形成之前,已被微分调节作用消除,因此可以改善系统的动态性能。
但是微分对噪声干扰有放大作用,加强微分对系统抗干扰不利。
积分和微分都不能单独起作用,必须与比例控制配合。
调合系统需要采用PID控制算法,使流量泵在交流电机的作用下运作,传输组分油进入管道,由调节阀控制流量大小,在经过流量计测出当前管道内的流量,并且通过PID控制算法得到但是流量计的反馈同时控制调节阀的开度从而改变管道内的流量,即如下图2.3、图2.4所示。
图2.3管道调合
图2.4流量控制回路
由此流量控制回路参与分别运转各组分油的管道调合内,集散控制中的PID算法分别控制各个管道支路的执行器,即调节阀的流量开度,分别显示在各条管道支路的流量计上,通过反馈回路再次控制PID影响调节阀。
常规调合控制
常规调合控制是汽油调合优化的底层控制,采用浙大中控系统的SCkey组态控制编辑器进行编辑组基于DCS的汽油调合优化控制系统的设计和实现组态。
在调合优化软件未投用时,DCS根据操作员输入的调合经验配方进行流量和压力PID自动控制,调合优化软件投用后,DCS接受来自优化程序的流量给定值设定进行控制,使各组分油按照配方比例进行调合。
常规调合控制的另一个任务就是实现调合的开停工控制,调合正常完成和异常终止都要对装置的泵和阀门的起、停进行逻辑联锁控制,确保装置能调合出合格的汽油产品和安全可靠运行。
常规调合控制过程中,在线NIR分析数据只作显示,不参与闭环控制。
第3章硬件设计及选型
调合检测系统选型
此次设计对优化系统较重要的8路组分流量测量采用MicroMotion高精度质量流量计。
汽油质量检测采用北京英贤公司的在线近红外分析仪NIR26000。
本系统流量变送器采用电磁流量计TI046D。
在电磁仪表中,流动介质相当于运动的导体。
与流速成比例的感应电压用两个测量电极检出并传送出放大器。
流体体积根据管道的直径进行计算,恒定磁场由交变极性的开关直流电流产生。
在线近红外分析仪:
基本原理是物质分子在近红外线的照射下会发生振动能级的跳跃,并发生衍射,对衍射光波进行快速扫描能得到各种光谱,与标准谱图库进行比较就能得出各种物质的比例并计算出相应的值。
每个近红外分析仪能带十六个探头。
每路探头都能测多个参数。
硬件控制执行系统选型
执行器位于控制回路的最终端,因此,又称为最终元件。
执行器直接与被控介质接触,在高低温、高压、腐蚀性、粉尘和爆炸性环境运行时,执行器的选择尤为重要。
执行器的选择:
调节阀的流量特性是流过阀门的流体的相对流量与阀门的相对开度间的关系,相对开度是调节阀某一开度行程与全开行程之比。
执行器是由执行过程和调节阀组陈的,而执行机构与正反两种作用,调节阀也有正反两种作用,因而组装成的气动调节阀有气关气开两种形式。
无压力信号时阀全开,随着压力信号增大,阀门逐渐关小的气动调节阀为气关式;反之,无压力信号时阀全关,随着压力信号增大,阀门逐渐开大的气动调节阀为气开式。
图3.1调节阀的类型示意图
汽油调合控制的管道调合保证流量的控制所以采用气开阀类型,本系统选用Valtek公司推出的STARPAC型智能调节阀,与上位机的控制系统的连接用4-20mA模拟信号,采用数字通信方式进行组态、校准、数据检索与故障诊断等信息传输。
汽油调合优化控制系统由四部分组成:
DCS,现场仪表,调合优化软件,在线NIR分析仪。
DCS采用浙大中控公司的JX-300XP系统作为调合自动控制的底层控制。
现场仪表采用通用、稳定可靠的仪表和阀门,
浙大中控JX-300XPDCS的硬件主要由操作站和控制站组成,其中操作站包括工程师站和操作员站,控制站包括主控制卡、数据转发卡和I/O卡件。
其控制系统有三层网络:
(1)信息管理网也称为以太网,用于工程级的信息传送和管理,实现全场综合管理的信息通道。
(2)过程控制网用于连接工程师站、操作员站和控制站。
(3)控制总线(SBUS网络)SUBS-S1用于连接数据转发卡和I/O卡件;SBUS-S2用于连接主控制卡和数据转发卡。
输入输出卡件是分散过程控制装置的控制器与模拟仪表(含带HART通信的模拟仪表)之间的桥梁,它将由模拟仪表输入的模拟信号转换为数字信号送到控制器,也将控制器输出的数字信号转换为模拟信号送到新厂安装的模拟执行器。
输入输出卡件根据信号的不同分为模拟量输入卡件、模拟量输出卡件、数字量输入卡件、数字量输出卡件和脉冲量输入卡件等。
模拟信号可分为电流信号和电压信号,开关信号可分为直流和交流,电压的等级也可分为多种类型。
XP258为电源卡件,将24V转换成5V为卡件供电。
主控制卡是系统的大脑主要进行I/O处理、控制运算、上下网络通信控制和诊断等功能。
数据转发卡主要是连接主控制卡和I/O卡件并管理本机笼的I/O卡件。
控制管道流量泵的执行器为额定功率35Kw,额定电压380V,额定电流15A,额定转速1450rpm的交流电动机以及阀门执行器等。
DCS由1套AW51应用操作站处理机、2套WP51操作站处理机(其中1套兼作OPC服务器)、1对XP243X冗余主控制卡和相应的数据转发卡以及FBM现场总线I/O模块组成,采用冗余的通信网络节点总线(Nodebus)和现场总线(Fiedbus)结构。
系统配置的非冗余检测AI18点,冗余AO8点,温度RTD输入8点,干触点DI16点,DO8点以及Modbus通信接口1个,I/O分配如下表3.1.
表3.1I/O分配表
信号类型
点数
备用点
卡件型号
卡件数目
配套
段子板
段子板
数目
模拟量信号
电流信号
18
6
XP313
4
XP520
2
模拟量
输出
8
0
XP322
2
XP520
1
开关量信号
开关量输入信号
16
0
XP363(B)
2
XP520
1
开关量输出信号
8
8
XP362(B)
2
XP520
1
总计
50
14
10
5
该汽油调合的集散控制系统采用浙大中控公司的JX-300XP集散控制系统,系统中用到了两块电源模块XP258-2(互为冗余),主控制卡两块XP243X(互为冗余),数据装发卡两块XP233(互为冗余)。
电流信号输入卡件选择XP313卡件,模拟量输出模块采用XP322,数字量输出用XP362(B)卡件,把这些卡件安装在一个机笼内,完成集散控制系统的硬件连接,如下图机笼所示。
SCI-1(2-0)
00
01
02
03
04
05
06
07
08
09
10
11
12
13
14
15
冗余
冗余
X
P
2
4
3
X
X
P
2
4
3
X
X
P
2
3
3
X
P
2
3
3
X
P
3
1
3
X
P
3
1
3
X
P
3
1
3
X
P
3
1
3
X
P
3
2
2
X
P
3
2
2
X
P
2
5
8
-2
X
P
2
5
8
-2
图3.2机笼1图
SCI-1(2-2)
00
01
02
03
04
05
06
07
08
09
10
11
12
13
14
15
冗余
冗余
X
P
2
5
8
-1
X
P
2
5
8
-1
X
P
2
3
3
X
P
2
3
3
X
P
3
6
3
(B)
X
P
3
6
3
(B)
X
P
3
6
2
(B)
X
P
3
6
2
(B)
图3.3机笼2图
在线NIR分析仪是调合控制的核心设备,有10个流路,每个调合头5个流路,1个流路分析8个油品的性质,采用Modbus串行通信和DCS通信,通信速率为9600B/s,8位数据位,2位停止位,无校验位。
每流路1.5min可得出分析数据并传送给DCS,并配有数据分析和模型管理的计算机。
DCS工程师站和操作站计算机的软件平台采用WindowsXP操作系统。
优化系统计算机的软件平台采用Windows2000操作系统。
汽油调合控制系统的配置如图3.4所示。
图3.4汽油调合控制系统配置
第4章软件设计
系统硬件组态设计
系统的硬件组态包括对主控制卡、I/O卡件、各个I/O点以及操作站的组态,其组态步骤如下图所示:
图4.1主控制卡的组态
图4.2操作站的组态
图4.3数据转发卡的组态
图4.4I/O卡件的组态
(1)
图4.5I/O卡件的组态
(2)
图4.6XP313卡件中I/O点的组态
(1)
图4.7XP313卡件中I/O点的组态
(2)
系统画面组态开发
集散控制系统的操作功能主要通过操作站实现。
从易操作性分析操作功能的实施,其判别准则是如何获得所需信息,既经过多少项操作步骤能达到所需信息的画面,及如何对过程实施操作。
系统的画面组态包括系统的总貌画面、趋势画面、分组画面和一览画面,其组态过程如下图所示。
图4.8总貌画面开发
图4.9分组画面开发
图4.10一览画面开发
图4.11趋势画面开发