中型煤制合成氨尿素厂生产技术现状水污染治理现状及存在问题.docx
《中型煤制合成氨尿素厂生产技术现状水污染治理现状及存在问题.docx》由会员分享,可在线阅读,更多相关《中型煤制合成氨尿素厂生产技术现状水污染治理现状及存在问题.docx(14页珍藏版)》请在冰豆网上搜索。
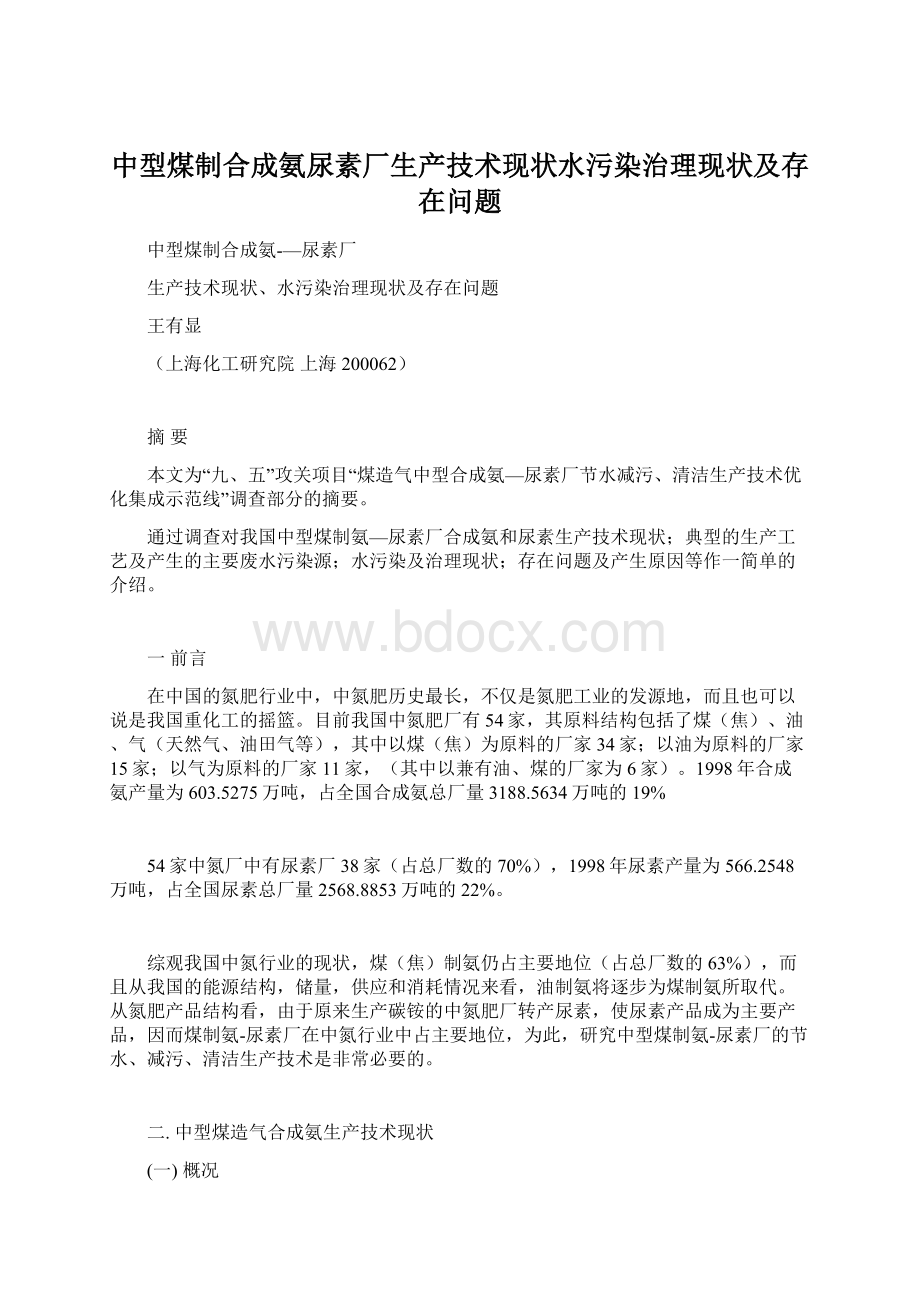
中型煤制合成氨尿素厂生产技术现状水污染治理现状及存在问题
中型煤制合成氨-—尿素厂
生产技术现状、水污染治理现状及存在问题
王有显
(上海化工研究院上海200062)
摘要
本文为“九、五”攻关项目“煤造气中型合成氨—尿素厂节水减污、清洁生产技术优化集成示范线”调查部分的摘要。
通过调查对我国中型煤制氨—尿素厂合成氨和尿素生产技术现状;典型的生产工艺及产生的主要废水污染源;水污染及治理现状;存在问题及产生原因等作一简单的介绍。
一前言
在中国的氮肥行业中,中氮肥历史最长,不仅是氮肥工业的发源地,而且也可以说是我国重化工的摇篮。
目前我国中氮肥厂有54家,其原料结构包括了煤(焦)、油、气(天然气、油田气等),其中以煤(焦)为原料的厂家34家;以油为原料的厂家15家;以气为原料的厂家11家,(其中以兼有油、煤的厂家为6家)。
1998年合成氨产量为603.5275万吨,占全国合成氨总厂量3188.5634万吨的19%
54家中氮厂中有尿素厂38家(占总厂数的70%),1998年尿素产量为566.2548万吨,占全国尿素总厂量2568.8853万吨的22%。
综观我国中氮行业的现状,煤(焦)制氨仍占主要地位(占总厂数的63%),而且从我国的能源结构,储量,供应和消耗情况来看,油制氨将逐步为煤制氨所取代。
从氮肥产品结构看,由于原来生产碳铵的中氮肥厂转产尿素,使尿素产品成为主要产品,因而煤制氨-尿素厂在中氮行业中占主要地位,为此,研究中型煤制氨-尿素厂的节水、减污、清洁生产技术是非常必要的。
二.中型煤造气合成氨生产技术现状
(一)概况
正如前述,我国以煤炭为原料的中型合成氨厂有34家,其工艺流程基本相同。
大致可分为:
原料气的制备;原料气的净化;气体压缩和氨合成四大部分,只是在使用的具体技术上有不同的差异,现简述如下:
1.原料气的制备
目前我国煤焦制氨采用的气化技术主要有下面两种。
(1)固定床间歇气化。
目前我国34家中型煤焦制氨厂均采用该技术,典型的炉型为UGI炉。
其直径一般为2.74米、3米和3.6米,由于产量不同而台数各异。
(2)水煤浆加压气化。
该法为引进德士古气化技术,首家使用该技术的是山东鲁南化肥厂第二氮肥厂,93年联动试车,94年3月通过国家的审核。
其它还有解放军化肥厂二期工程鲁奇法褐煤加压气化技术,该技术为国家科委重点科研项目。
1974年投产,但该法仍存在一些问题,而且污染较为严重,目前准备与捷克合作对鲁奇炉褐煤气化、净化及污染治理进行合作。
2.原料气的净化
在制得的原料气中,除有用成分氢和氮外,还有不同数量的H2S、有机硫化物、CO2、CO等。
为此必须将原料气进行净化。
现将我国煤焦制氨厂的各种净化工艺统计分述如下:
(1)硫化物的脱除
据统计34家厂中采用的脱硫技术如表2-1所示
表2-1脱硫技术及使用厂家数
脱硫技术名称
使用厂数
比例%
ADA
29
61.8
栲胶
6
17.6
GV
1
2.9
MSQ
3
8.8
PDS
2
6.0
活性碳
1
2.9
合计
34
100
从表2-1可见,各厂使用的脱硫技术绝大部分都不是以NH3作为碱源,这就大大地降低了由于脱硫所引起的NH3-N的污染。
(2)CO2的脱除
原料气中CO2的脱除方法有:
物理吸收法;化学吸收法;物理-化学吸收法等。
据所收集的29个厂的数据统计,这些厂所使用的脱碳技术如表2-2所示
表2-2脱碳技术及使用厂数
脱碳技术名称
使用厂数
比例%
加压水洗法
12
41.4
苯菲尔法
3
10.3
氨基乙酸法
4
13.8
热钾碱法
5
17.3
丙烯碳酸酯法
2
6.9
二乙醇胺法
2
6.9
环丁砜法
1
3.4
合计
29
100
从表2-2中可见,加压水洗脱碳占主要优势,其压力在1.77~2.94MPa之间。
(3)CO的脱除
脱除CO的技术主要有铜洗、甲烷化和液氮洗等技术。
据统计34家厂采用的脱CO技术如表2-3所示。
表2-3脱CO技术及使用厂数
脱CO技术名称
使用厂数
比例%
铜洗
29
85.3
液氮洗
1
2.9
甲烷化
4
11.8
合计
34
100
从表2-3可见,有85.3%的厂使用铜洗流程,由于铜洗流程有大量稀氨水排放,这成为合成氨厂氨氮的主要排放源。
(4)CO变换
CO变换技术有常压变换、中温变换、低温变换和中变串低变等到技术。
3.气体的压缩
原料气的净化和氨的合成都必须在加压和高温中进行。
必须使用如原料气压缩机、循环压缩机和氨压缩机等进行压缩。
压缩机的类型很多,但在合成氨生产过程中一般常用的都是往复式压缩机。
如氢氮压缩机大多采用H22和3D22等系列。
4.氨合成
氨合成从压力来分有高压法、中压法和低压法三种,我国目前煤焦制氨的34家合成氨厂均采用中压法,其合成压力除大化化肥厂为26MPa外,其它均为31.4MPa。
合成塔的直径一般为Ф800~Ф1000mm,但大多为Ф1000mm。
只有大化化肥厂采用德国Krnp公司Ф1300mm的合成塔。
至于合成塔的台数主要根据各厂的实际情况来定。
(二)典型工艺流程及概述
1.以煤焦为原料的固定床制气合成氨工艺流程及概述(略)
2.以煤为原料德士古炉制气(水煤浆加压气化)合成氨工艺流程及概述(略)
(三)我国合成氨生产技术主要的废水污染源
原料气的制备、原料气的净化、气体压缩和氨合成四大部分构成了合成氨生产主要的技术。
1.原料气制备技术所产生的水污染
合成氨原料气的制备对煤(焦)而言,是以煤或焦与气化剂(如空气、蒸汽、氧气等)进行一系列非均相化学反应,生成以CO、H2、CO2和CH4等为基本组分的各种煤气。
然而煤中除含有C外,还含有S、O、N等元素,为此煤气中还含有H2S、HCN以及未反应的煤屑。
由于从造气炉出来的煤气除含有上述的气体和杂质外,气体温度也较高,所以必须经过降温、洗涤才能进入下一个工序。
这是任何一种制气方法都不能避免。
而洗涤剂和降温介质一般为水。
故此就产生了一股温度高、色度深、含有大量煤屑及氰化物的污水。
由于这些化合物中氰化物的浓度高,并有剧毒故一般称这股废水为造气含氰废水。
不同的制气工艺,产生不同的造气含氰废水。
现将我国目前煤制气中氮厂所采用的UGI炉固定床间歇气化、德士古水煤浆气化(鲁南)和鲁奇Lurgi褐煤加压气化(解放军化肥厂)有关排水量和污染物的组成列于表2-4。
表2-4煤制气不同工艺造气废水排放量和组成
制气
工艺
排水量
(t/tNH3)
水温
(℃)
pH
S.S
(mg/l)
CN-
(mg/l)
phen.
(mg/l)
S=
(mg/l)
NH3-N
(mg/l)
CODcr
(mg/l)
UGI
30—70
50—60
7—8
50—500
10—30
0.01—0.05
0.1—30
40—470
20—360
Texaco
0.8
60
8.9
150
30
200
900
Lurgi
5
50
7—9
25
250—300
30
700
600
从表2-4可见:
UGI炉常压固定床间歇气化由于炉温低(700—800℃)、气化强度低,单炉生产能力相应也低,因而吨氨能耗高、废水排放量大,分别为Texaco和Lurgi法的38—88倍和5—14倍,而且污染物排放的绝对量最大,对水环境污染严重。
我国目前煤制气氨厂中除鲁南、解化二期工程分别采用Texaco和Lurgi法外,全部采用UGI炉常压固定床气化法。
目前中氮肥厂的发展方针是节能、增产改造。
为此采用UGI法比较合适,其依托条件较多,投资少。
因而无论是在中氮合成氨改造的“818”(8万吨/年合成氨、18万吨/年尿素)方案,还是在部分新建的“1830”(18万吨/年合成氨、30万吨/年尿素)方案中均采用此法。
常压固定床间歇气化是我国煤制氨的特有技术,为此造气含氰废水也就成了我国煤制氨行业的特有污染。
2.原料气的净化技术所产生的水污染
合成氨原料气的净化主要包括硫化物的脱除;CO2的脱除;CO的脱除和CO的变换。
硫化物的脱除从表2-1中可见:
在目前常用的方法中绝大多数不以氨作为碱源,故排除了氨氮对水环境的污染。
CO的脱除污染严重的是铜洗流程。
铜洗液再生产生了含有NH3、CO和CO2的铜洗再生气。
铜洗再生气经水洗涤产生铜洗稀氨水,其浓度视所采用的洗涤技术不同而不同。
一般在1—3%左右。
中氮肥厂每小时约产生10吨废水。
这股废水除含有氨外,还含有CO2,所以采用一般的提浓方法都由于容易生成碳铵引起管道堵塞而无法处理。
为此要么采用铜洗再生氨直接放空;要么就是铜洗稀氨水排放。
这不但浪费了宝贵的资源,也引起了大气或水环境的严重污染。
然而我们从表2-3可见:
目前34家煤制氨厂脱CO技术有85%的厂采用铜洗流程。
综上所述,我国煤制氨的中氮肥厂,目前所采用的生产技术其主要的水污染源为煤造气含氰废水和铜洗稀氨水。
三.中型尿素生产技术现状
(一)概述
制造尿素的方法有50余种,但实现工业化的只有氰氨化钙(石灰氮)法和氨与CO2直接合成法两种。
合成氨生产为氨与CO2直接合成尿素技术提供了氨和CO2,因原料获得方便,产品浓度高,现在广泛采用此法生产尿素。
我国尿素生产主要采用水溶液全循环法。
水溶液全循环法是将未反应的氨和CO2用水吸收生成甲胺或碳酸铵水溶液循环返回系统。
我国在煤焦制氨-尿素厂26家中有22家均采用水溶液全循环法。
采用Ф1400mm的尿素合成塔,Ф9000—16000mm的自然通风造粒塔。
80年代末,北京化工实验厂、洛阳氮肥厂、宣化化肥厂和原平化肥厂引进了意大利氨汽提技术,规模为13.2万t尿素/a,并配有尿素解析、废液深度水解装置,使我国中型合成氨厂、尿素生产技术和环保治理技术达到了较先进的水平。
三明化工厂第二尿素车间采用CO2汽提法尿素生产工艺。
(二)典型工艺流程及概述
1水溶液全循环法尿素工艺流程及概述(略)
2氨汽提法尿素工艺流程及概述(略)
3CO2汽提法尿素工艺流程及概述(略)
(三)我国尿素生产技术主要的废水污染源
氨和二氧化碳生产尿素的方法,由于原料易得,产品纯度高,所以目前在世界各国均采用此法生产尿素。
工业上由NH3与CO2直接合成尿素分下列四个步骤进行:
(1)NH3与CO2的原料供应及净化
(2)NH3与CO2合成尿素
(3)尿素熔融液与未反应成尿素物质的分离和回收。
(4)尿素溶液的加工。
一般说来,上述四个步骤中,第一步和第二步除工艺条件稍有差别外,在设备构造和操作原则上几乎差不多。
第四步尿素溶液加工,实际上是尿素溶液浓缩结晶,造粒生产尿素颗粒成品或液态尿素的过程。
造粒塔排放的粉尘和NH3会对大气环境造成污染,但对水环境不会有很大的影响。
第三个步骤差异较大,在合成尿素工艺流程分类时,是按第三步来分,大致分为不循环法;部分循环法;半循环法和全循环法。
即将NH3与CO2在尿素合成系统中循环使用。
气提法是全循环法的发展。
在简化流程,热能回收,延长运转周期和减少费用等方面较水溶液全循环法优越。
目前我国中氮尿素厂,尿素生产方法以水溶液全循环法为主,并引进了氨气提和CO2气提法。
这三种方法的产污系数见表3-1。
表3-1不同尿素生产工艺废水和污染物的产污系数
生产工艺
污染物
CO2气提法*1
水溶液全循环法
氨气提法*2
QH2O(t/tUr)
0.88
2.78
0.72
NH3-N(kg/tUr)
7.82
5.26
24.7
Ur(kg/tUr)
12.68
1.96
2.60
CODcr(kg/tUr)
0.17
1.63
0.07
*1包括大型尿素厂*2按北京化工实验厂数据计算
在尿素生产过程中,生成一克分子的尿素就要副产一克分子的水,也就是说生产一吨尿素就会产300公斤的水,其废水的主要污染源为尿素解吸液,其它为地面冲洗水,废水中NH3-N和Ur的来源,除尿素解吸液外,还来自高压液氨泵等设备和装置的跑、冒、滴、漏。
据从水溶液全循环法的11万吨/a尿素厂物料衡算,其泄漏损失为28.93kg/tUr。
从表3-1可见:
从废水的排放,气提法优于水溶液全循环法,为此目前新建的“1830”工程,尿素生产工艺均采用氨气提法,但我国26家煤制氨-尿素厂中有22家采用水溶液全循环法。
综上所述,我国中型煤制氨-尿素厂,目前所采用的生产技术,其主要水污染源为以尿素解吸液为主含NH3-N和Ur的废水,其主要污染物为NH3-N和Ur。
四.煤制氨-尿素厂水污染及治理现状
(一)水污染现状
据近年来调查,有关中型氮肥厂和煤制氨-尿素厂废水排放情况如表4-1,4-2,4-3。
表4-1中型氮肥厂给排水情况
年份
氨产量
(万吨/年)
吨氨用水量
(吨)
吨氨排水量
(吨)
循环率
(%)
万元产值新鲜水用量(吨/万元)
1985年
367.5
761.01
217.94
67.09
4543.67
1990年
464.5
616.09
154.24
76.65
1950.48
表4-2中型氮肥厂主要污染物排放情况
年份
排水量
(万吨/年)
悬浮物
(吨/年)
氰化物
(吨/年)
氨氮
(吨/年)
1985年
309,441.71
592,563.9
2,878.87
230,999.95
1990年
225,746.28
287,146.6
509.72
65,095.20
表4-31990—1998年中型煤制氨-尿素厂水污染物排放汇总
污染物
QH2O
(t/tNH3)
PH
S.S
(mg/l)
CN-
(mg/l)
S2-
(mg/l)
CODcr
(mg/l)
NH3-N
(mg/l)
范围
28-230
6-9
50-200
0.03-2.60
0.1-1.5
50-150
18-300
平均值
115
6-9
108
0.56
0.60
112
89
从表4-1,4-2可见,中型氮肥厂的水污染状况,随着时间的推移有所改善,随氨产量的递增,污染物的年排放量减少。
特别是氰化物和氨氮降低的幅度更大。
氰化物在80年前的年排放量为1.08万吨,到1990年仅为509.72吨,下降了95.28%;氨氮1985年排放量为23.1万吨,到1990年下降到6.51万吨,降低了371.8%。
这是由于中氮行业对环境保护工作重视的结果。
然而从整体来说污染状况虽有所改善,但与国家标准GB13458-92《合成氨工业水污染排放标准》比较(见表4-4)中型煤制氨-尿素厂达标厂数不多,特别是双达标的厂数更少。
为此中型煤制氨-尿素厂的水污染现状仍是比较严重的。
4-4中型煤制氨厂水污染物排放标准与部分厂达标情况
GB13458-92《合成氨工业水污染物排放标准》中型厂,煤头.二级
排水量
t/tNH3
PH
S.S
CN-
S2-
CODcr
NH3-N
mg/l
kg/tNH3
mg/l
kg/tNH3
mg/l
kg/tNH3
mg/l
kg/tNH3
mg/l
kg/tNH3
80
6-9
100
8.00
0.5
0.04
1.0
0.08
200
16.00
80
6.40
达标厂数
9
28
7
6
15
12
17
15
17
14
14
7
统计厂数
28
28
18
23
21
17
28
(二)治理现状
氮肥工业的“三废”治理始于70年代中叶,经过了20多年的努力,开发了一批结合我国国情的治理技术,使氮肥工业的水污染得到了有效的控制,成绩是喜人的。
1.合成氨工业给排水状况有了很大的改善
随着对我国水资源利用和环保意识的提高,一水多用,循环利用势在必然,中型厂的水循环率逐渐提高,如表4-1所示,至1990年止,中氮的平均水循环率已达到76.63%,吨氨排水量从1957年的1098吨,下降到154吨,下降了86%,大大节约了宝贵的水资源。
从表4-4中型煤制氨厂吨氨排水量平均为115吨,说明又迈进了一步。
2.排水中的氰化物基本上得到了控制
由于氰化物的毒性在70年代已引起了氮肥环保工作者的关注,用了20多年的时间开发了一批结合我国国情的造气含氰废水的治理技术,使氰化物基本上得到了有效控制,目前采用的方法主要有:
冷却型塔式生物滤池法;生物滤池法;冷却塔(凉水塔)法;内电解法等。
据我们对26家中型煤制氨厂调查,采用冷却型塔式生物滤池法的为14家;冷却塔法10家;内电解法1家;生物滤池1家,这些方法各有特点,我们将作专门论述。
但都能有效控制水中氰化物的排放。
3.重视氨流失和含氨废水的治理
正如前述,我国氮肥行业氨流失相当严重,1985年氨氮排放量为23.1万吨,相当于合成氨28.1万吨,亦即是使每年要从废水中排放一个大型厂的氨产量。
这个调查数据引起了有关领导部门的重视,为此对氨流失和氨氮废水的治理马上提到议事日程上来,首先从排放标准入手,控制氨氮的排放,因此大力开展从工艺改革到氨氮治理技术的研究,经过20多年的努力开发了一批结合我国国情的治理技术。
(1)合成放空气,氨罐弛放气稀氨水的回收。
采用蒸馏技术回收氨。
目前大部分厂均采用该项技术,避免了由于稀氨水无销路,排入环境,造成环境污染。
(2)铜洗稀氨水回收。
这部分稀氨水在80年代末,90年代初大多采用蒸馏法回收,但由于含有CO2,在蒸馏过程中不仅NH3被蒸出,而CO2也同样被蒸出,在冷凝时,容易生成碳酸铵,使管道堵塞,为此,这部分稀氨水不能很好地被回收利用,在无法出售时,只有排放,长期困绕着采用铜洗流程的工厂。
最近由上海化工研究院与南化公司氮肥厂开发的《含碳氨水回收集成分离技术》,通过优化分离设计将解吸、精馏、防结晶措施结合在一起,比较好的解决了结晶堵塞的问题,可将含NH3约1.7%,CO21.3%的铜洗稀氨水提浓到NH318%以上。
目前已在中、小氮肥厂推广使用,如南化氮肥厂、宣化化肥厂等。
(3)以预蒸馏代替预分离减少尿素装置稀氮水的排放,此项措施可使流程达到全循环的目的,消除外送废氨水,使每吨尿素氨耗一般可降低32-35公斤。
(4)改造尿素解吸塔,提高解吸能力,增加氨的回收量。
并使解吸废液中含NH3浓度大大降低。
(5)引进尿素解吸液高温深度水解技术。
80年代中期云天化、泸天化、沧化和辽化引进了意大利斯纳姆普罗吉蒂公司尿素解吸液高温深度水解技术,其NH3和尿素的处理效率达到99.9%,处理后废水中含NH3和Ur在1-2mg/l左右,很好地解决了尿素解吸液中NH3和Ur的回收问题。
近年来利用世行贷款的四个中型煤制氨-碳铵厂(北京化工实验厂、宣化化肥厂、洛阳化肥厂和原平化肥厂)在扩建和转产尿素时,也采用该技术,处理效果十分理想,其后陆续扩建成的河池氮肥厂、鄂西化肥厂以及近年来兴建的“1830”工程尿素解吸液也采用该技术进行处理,彻底解决了尿素工厂排放的NH3-N污染。
(三)存在问题及产生原因
1.存在问题
(1)水的循环率仍然很低,吨氨排水量大
近年来中型氮肥厂的水循环率不断提高,如表4-1所示,然而与大型厂的水循环率>96%比较,差距仍然很大,大型厂的吨氨排水量一般在8-10吨左右,只为中型厂的6-8%。
另据54家中型氮肥厂中的48家统计有循环水系统的只有42家,另有6家仍用直流水,特别是一些丰水地区,吨氨排水量更大。
(2)造气含氰废水中的氰化物虽然得到有效的控制,仍存在二次污染。
在目前所采用的造成气含氰废水的治理技术中,对于排水中的氰化物确实起到了有效控制,但由于当时仍未有关于氰化物的大气排放标准,因此忽视了污染物从水中转移到大气的这个事实。
对照GB16297-1996《大气污染物综合排放标准》,现有处理工艺排气中HCN无论是排放浓度还是排放速率都是超标的。
而且如采用横流式的生物滤塔其高度低于标准要求的25米。
然而,值得注意的是,在使用冷却型塔式生物滤池法的厂中,有些厂由于生化操作不好,如挂膜不好,填料堵塞,碳源不足等,而不再进行生化处理,实际上生物滤池只作为冷却塔(凉水塔)使用,影响了脱氰的效果。
(3)造气废水氰化物沿途挥发严重
煤造气废水,从造气车间煤气洗涤塔出水,通过排水沟进入沉淀池,在进入处理装置前,由于水温较高,一般在50-60℃,PH在7-8,所以沿途流失比较严重,这种流失大部分是以HCN的形式挥发到大气中,其流失率一般为20-40%,但这受水温、气温、气象条件的影响较大。
(4)铜洗稀氨水仍是NH3-N的主要污染源
在肥料紧缺时期,从铜洗排出的低浓度稀氨水,通常再加入一些氨,配制成18%的碳化氨水出售,并且经常脱销,但随着化肥向高浓度发展的趋向,氨水几乎已经无人问津了,加上在一段较长的时间内,没有适用的回收技术,为了维持生产只能排放,甚至有个别厂为了避免铜洗稀氨水的产生,而将铜洗再生气未经洗涤,直接放空,不但污染了大气环境,还造成了资源的极大浪费。
(5)尿素解吸液的处理仍未得到彻底的解决
大多数厂虽然通过以预蒸馏代替预分离;改造解吸塔等措施使解吸液中的NH3浓度大大降低,但往往仍受到生产管理、操作、设备负荷等的制约,使解吸液中NH3浓度增高。
目前虽然已经引进了高温深度水解技术,但普及面仍然不广。
2.产生原因
(1)政策和思想观念方面的原因
在我国的氮肥工业中,中氮肥困难最多,当然这有主观原因,也有客观原因,因而限制了它的优势发挥。
与大氮和小氮相比,中氮肥计划经济观念较深,市场经济观念较淡泊,因此很难适应市场的变化和冲击。
与小氮肥相比,小氮肥有比较开放的政策,能够进行较大规模的技术改造以及进行了“三废”治理,比较明显的是两水闭路循环的国家专项拔款,就使小氮肥的造气含氰废水得到了治理,吨氨排水量下降到30吨左右。
与大氮相比,中氮设备陈旧,工